落料凹模设计.docx
《落料凹模设计.docx》由会员分享,可在线阅读,更多相关《落料凹模设计.docx(17页珍藏版)》请在冰豆网上搜索。
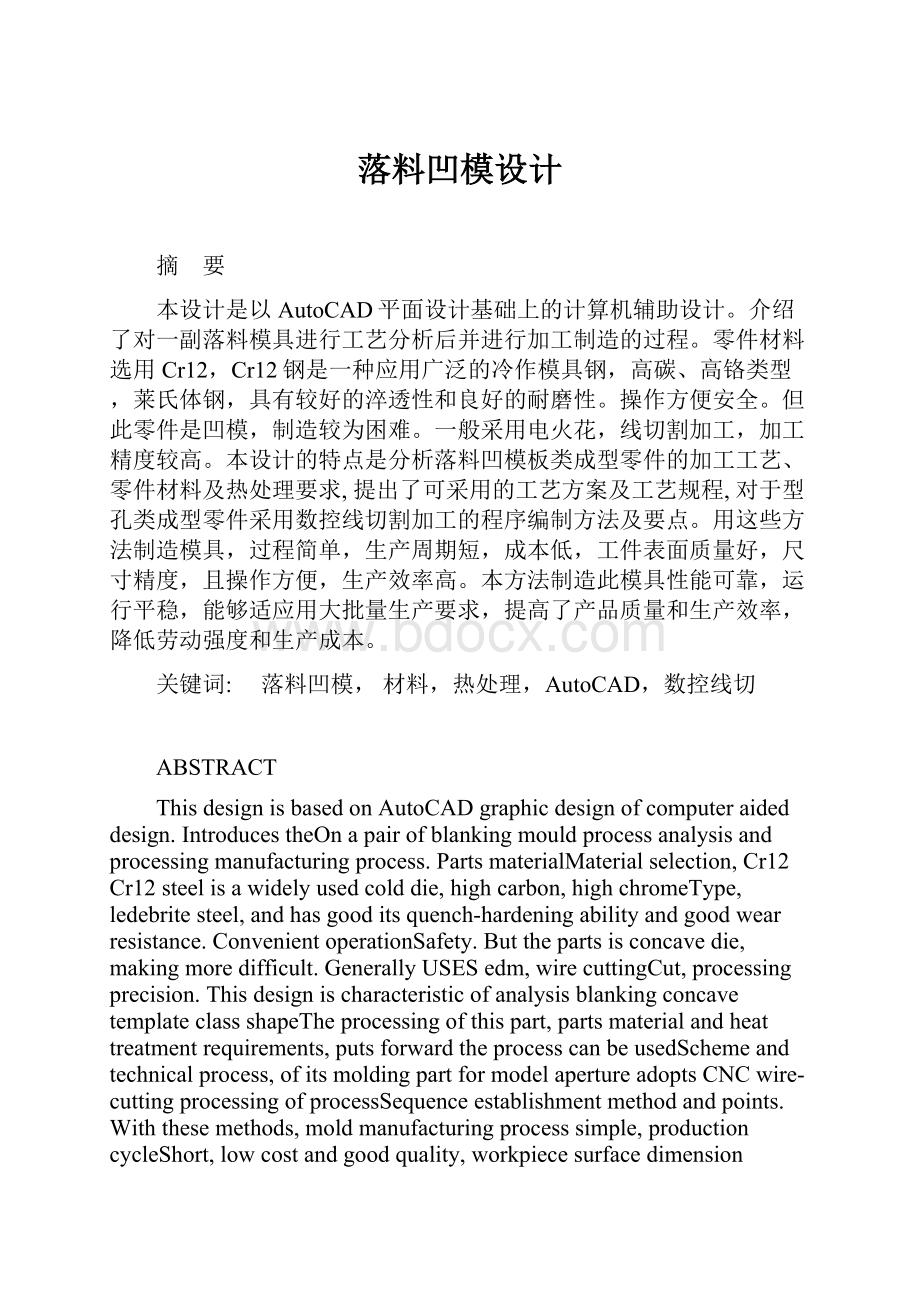
落料凹模设计
摘 要
本设计是以AutoCAD平面设计基础上的计算机辅助设计。
介绍了对一副落料模具进行工艺分析后并进行加工制造的过程。
零件材料选用Cr12,Cr12钢是一种应用广泛的冷作模具钢,高碳、高铬类型,莱氏体钢,具有较好的淬透性和良好的耐磨性。
操作方便安全。
但此零件是凹模,制造较为困难。
一般采用电火花,线切割加工,加工精度较高。
本设计的特点是分析落料凹模板类成型零件的加工工艺、零件材料及热处理要求,提出了可采用的工艺方案及工艺规程,对于型孔类成型零件采用数控线切割加工的程序编制方法及要点。
用这些方法制造模具,过程简单,生产周期短,成本低,工件表面质量好,尺寸精度,且操作方便,生产效率高。
本方法制造此模具性能可靠,运行平稳,能够适应用大批量生产要求,提高了产品质量和生产效率,降低劳动强度和生产成本。
关键词:
落料凹模,材料,热处理,AutoCAD,数控线切
ABSTRACT
ThisdesignisbasedonAutoCADgraphicdesignofcomputeraideddesign.IntroducestheOnapairofblankingmouldprocessanalysisandprocessingmanufacturingprocess.PartsmaterialMaterialselection,Cr12Cr12steelisawidelyusedcolddie,highcarbon,highchromeType,ledebritesteel,andhasgooditsquench-hardeningabilityandgoodwearresistance.ConvenientoperationSafety.Butthepartsisconcavedie,makingmoredifficult.GenerallyUSESedm,wirecuttingCut,processingprecision.ThisdesignischaracteristicofanalysisblankingconcavetemplateclassshapeTheprocessingofthispart,partsmaterialandheattreatmentrequirements,putsforwardtheprocesscanbeusedSchemeandtechnicalprocess,ofitsmoldingpartformodelapertureadoptsCNCwire-cuttingprocessingofprocessSequenceestablishmentmethodandpoints.Withthesemethods,moldmanufacturingprocesssimple,productioncycleShort,lowcostandgoodquality,workpiecesurfacedimensionaccuracy,andconvenientoperation,theproductionefficiencyRateishigh.Thismethodmakesthemoldreliableperformance,smoothoperation,andcanadapttouselargeQuantityproductionrequirements,improvetheproductqualityandproductionefficiencyandreducelaborintensityandproductioncost.
Keywords:
Blankingconcavedie,Materials;Heattreatment,AutoCAD,CNCwirecutting
目录
第1章绪论…………………………………………………………6
1.1模具工业的的概况…………………………………………………6
1.2落料模的发展方向………………………………………………………6
1.3模具的发展与现状………………………………………………………7
1.4模具CAD/CAE/CAM技术…………………………………………………8
1.5课题的的主要特点及意义………………………………………………10
第2章落料凹模工艺分析………………………………………12
2.1零件工艺性分析………………………………………………………13
2.2拟定工艺方案……………………………………………………………15
2.3工艺过程的制定…………………………………………………………15
第3章加工程序的编制…………………………………………17
第4章工艺评价………………………………………………20
结束语…………………………………………………………21
致谢…………………………………………………………23
参考文献……………………………………………………………………25
第1章绪论
1.1模具工业的的概况
模具工业是国民经济的基础工业,受到政府和企业界的高度重视,发达国家“模具工业是进入富裕社会的源动力”之说,可见其重视的程度。
当今,“模具就是经济效益”的观念,已被越来越多的人所接受。
模具技术水平在很大程度上决定于人才的整体水平,而模具技术水平的高低,又决定着产品的质量、效益和新产品的开发能力,因此模具技术已成为衡量一个国家产品制造水平高低的重要标志。
在现代工业生产中,模具已经成为生产各种工业产品不可缺少的重要工艺装备,随着我国工业的不断发展,模具的重要性更是不可替代。
提高模具制造工艺水平,保证模具质量、降低生产成本以及先进模具制造技术的开发应用是模具制造业思考的重要课题。
1.2落料模的发展方向
落料模是在板材上冲裁制件或毛坯的冲模。
随着市场的发展,新材料及多样化成型方式今后必然会不断发展因此对模具的要求也一定会越来越高。
为了满足市场的需要,未来的模具无论是品种、结构、性能还是加工技术都必将会有较快发展,而且这种发展必须跟上时代发展步伐。
展望未来,下列几方面发展趋势预计会在行业中得到较快应用和推广。
当然,这是需要开拓、创新和做出艰苦努力的。
超大型、超精密、长寿命、高效模具将得到发展;模加高精度具设计、加工及各种管理将向数字化、信息化方向发展,CAD/CAM/CAE/CAPP等将向智能化集成化和网络化方向发展;更加高速、更加智能化的各种模具加工设备将进一步得到发展和推广应用;更高性能及满足特殊用途的各种模具新材料将会不断发展,随之而来的也会产生一种特殊的和更为先进的加工方法;各种模具表面处理技术、涂覆、修补、研磨和抛光等新工艺也会不断得到发展;逆向工程、并行工程、复合加工乃至虚拟技术将得到发展。
科学技术发展的进程表明,机械工业是科学技术物化为生产力的重要载体,而模具设计与制造在机械行业占有举足轻重的地位。
目前,电子、汽车、电机、电器、仪器、仪表、家电、通讯和军工等产品中,60%-80%的零部件,都要依靠模具成型。
用模具成型的制件所表现出来的高精度、高复杂性、高一致性、高生产率和低消耗,是其他加工制造方法所无法比拟。
模具在很大程度上决定着产品的质量、效益和开发能力总体来说中国的模具行业现只达到世界20世纪80年代中期的先进水平,也就是说差距还很大,所以很有发展前途,且模具是很基础的行业,用途非常广。
专家认为,我国模具行业日趋大型化,而且精度将越来越高。
10年前,精密模具的精度一般为5μm,现在已达2-3μm。
不久,1μm精度的模具将上市。
随着零件微型化及精度要求的提高,有些模具的加工精度公差就要求在1μm以下,这就要求发展超精加工。
需要大家的努力了。
1.3模具的发展与现状
模具是工业生产中的基础工艺装备,是一种高附加值的高技术密集型产品,也是高新技术产业的重要领域,其技术水平的高低已成为衡量一个国家制造水平的重要标志。
随着国民经济总量和工业产品技术的不断发展,各行各业对模具的需求量越来越大,技术要求也越来越高。
目前我国模具工业的发展步伐日益加快,“十一五期间”产品发展重点主要应表现在[2]:
(1)汽车覆盖件模;
(2)精密冲模;
(3)大型及精密塑料模;
(4)主要模具标准件;
(5)其它高技术含量的模具。
目前我国模具年生产总量虽然已位居世界第三,其中,冲压模占模具总量的40%以上[2],但在整个模具设计制造水平和标准化程度上,与德国、美国、日本等发达国家相比还存在相当大的差距。
以大型覆盖件冲模为代表,我国已能生产部分轿车覆盖件模具。
轿车覆盖件模具设计和制造难度大,质量和精度要求高,代表覆盖件模具的水平。
在设计制造方法、手段上已基本达到了国际水平,模具结构功能方面也接近国际水平,在轿车模具国产化进程中前进了一大步。
但在制造质量、精度、制造周期和成本方面,以国外相比还存在一定的差距。
标志冲模技术先进水平的多工位级进模和多功能模具,是我国重点发展的精密模具品种,在制造精度、使用寿命、模具结构和功能上,与国外多工位级进模和多功能模具相比,存在一定差距[2-3]。
1.4模具CAD/CAE/CAM技术
冲压技术的进步首先通过模具技术的进步来体现出来。
对冲模技术性能的研究已经成为发展冲压成形技术的中心和关键。
20世纪60年代初期,国外飞机、汽车制造公司开始研究计算机在模具设计与制造中的应用。
通过以计算机为主要技术手段,以数学模型为中心,采用人机互相结合、各尽所长的方式,把模具的设计、分析、计算、制造、检验、生产过程连成一个有机整体,使模具技术进入到综合应用计算机进行设计、制造的新阶段。
模具的高精度、高寿命、高效率成为模具技术进步的特征。
模具CAD/CAE/CAM是改造传统模具生产方式的关键技术,是一项高科技、高效益的系统工程。
它以计算机软件的形式,为企业提供一种有效的辅助工具,使工程技术人员借助于计算机对产品性能、模具结构、成形工艺、数控加工及生产管理进行设计和优化[4]。
模具CAD/CAE/CAM技术能显著缩短模具设计与制造周期,降低生产成本和提高产品质量已成为模具界的共识。
模具CAD/CAE/CAM在近20年中经历了从简单到复杂,从试点到普及的过程。
进入本世纪以来,模具CAD/CAE/CAM技术发展速度更快,应用范围更广。
在级进模CAD/CAE/CAM发展应用方面,本世纪初,美国UGS公司与我国华中科技大学合作在UG-II(现为NX)软件平台上开发出基于三维几何模型的级进模CAD/CAM软件NX-PDW。
该软件包括工程初始化、工艺预定义、毛坯展开、毛坯排样、废料设计、条料排样、压力计算和模具结构设计等模块。
具有特征识别与重构、全三维结构关联等显著特色,已在2003年作为商品化产品投入市场。
与此同时,新加波、马来西亚、印度及我国台湾、香港有关机构和公司也在开发和试用新一代级进模CAD/CAM系统。
我国从上世纪90年代开始,华中科技大学、上海交通大学、西安交通大学和北京机电研究院等相继开展了级进模CAD/CAM系统的研究和开发。
如华中科技大学模具技术国家重点实验室在AutoCAD软件平台上开发出基于特征的级进模CAD/CAM系统HMJC,包括板金零件特征造型、基于特征的冲压工艺设计、模具结构设计、标准件及典型结构建库工具和线切割自动编程5个模块。
上海交通大学为瑞士法因托(Finetool)精冲公司开发成功精密冲裁级进模CAC/CAM系统。
西安交通大学开发出多工位弯曲级进模CAD系统等。
近年来,国内一些软件公司也竞相加入了级进模CAD/CAM系统的开发行列,如深圳雅明软件制作室开发的级进模系统CmCAD、富士康公司开发的用于单冲模与复合模的CAD系统Fox-CAD等[4]。
展望国内外模具CAD/CAE/CAM技术的发展,本世纪的科学技术正处于日新月异的变革之中,通过与计算机技术的紧密结合,人工智能技术、并行工程、面向装配、参数化特征建模以及关联设计等一系列与模具工业相关的技术发展之快,学科领域交叉之广前所未见。
今后10年新一代模具CAD/CAE/CAM系统必然是当今最好的设计理念、最新的成形理论和最高水平的制造方法相结合的产物,其特点将反映在专业化、网络化、集成化、智能化四个方面。
主要表现在[4]:
(1)模具CAD/CAM的专业化程度不断提高;
(2)基于网络的CAD/CAE/CAM一体化系统结构初见端倪;
(3)模具CAD/CAE/CAM的智能化引人注目;
(4)与先进制造技术的结合日益紧密。
1.5课题的主要特点及意义
该课题主要针对落料凹模的制作工艺进行分析,提出了该零件采用数控线切割加工程序编制方案;本设计的特点是根据零件的形状、尺寸精度要求分析落料凹模板类成型零件的加工工艺、零件材料及热处理要求,提出了可采用的工艺方案及工艺规程,对于型孔类成型零件采用数控线切割加工的程序编制方法及要点。
用这些方法制造模具,过程简单,生产周期短,成本低,工件表面质量好,尺寸精度,且操作方便,生产效率高。
本方法制造此模具性能可靠,运行平稳,能够适应用大批量生产要求,提高了产品质量和生产效率,降低劳动强度和生产成本。
在保证工件的尺寸和形状位置精度要求的同时,提高了材料的利用率和劳动生产率。
本课题涉及的知识面广,综合性较强,在巩固大学所学知识的同时,对于提高设计者的创新能力、协调能力,开阔设计思路等方面为作者提供了一个良好的平台。
此毕业设计不但让我巩固了大学三年所学的知识,拓展了本人的视野,更重要的是它让我学会要做事的恒心、处理问题的虚心,而且让我更加了解了模具这个行业的一些基本情况。
第二章落料凹模工艺分析
如图
(1)所示零件为一落料凹模。
零件材料为Cr12、要
求热处理后硬度为60~64HRC,其它技术要求见图。
图1 凹模
2.1 零件工艺性分析
2.2.1 结构分析:
由图
(1)可知该零件为典型的型孔板类零件,其外形尺寸
为120mm×80mm×17mm,成型部分为不规则型孔,由线段
和凸、凹圆弧组成,其下端加工有漏料孔,另有安装及定位孔
4,4-8,4-8.5,均为通孔。
从模具制造工艺的角度来分析,该成型零件可按单型孔
板类零件来加工。
2.1.2 模具材料及热处理分析:
模具材料是模具的制造基础,合理选择材料,正确实施热
处理工艺是保证模具寿命,提高模具质量和使用效能的关键
技术。
选择模具材料应考虑其使用性能要求和工艺性能要求。
该零件为落料凹模,选择合金钢Cr12作为模具材料,其主要化学成分(%)碳C:
2.00~2.30硅Si:
≤0.40锰Mn:
≤0.40硫S:
≤0.030磷P:
≤0.030铬Cr:
11.50~13.00镍Ni:
允许残余含量≤0.25铜Cu:
允许残余含量≤0.30钴Co:
≤1.00[1],cr12是一种合金钢。
淬火硬度高,韧性尚可,抗腐蚀性能也不错。
因为其综合性能优良、价格低廉,所以最常被作为冷作模具用钢(用做冷作模具的刃板和模型)和工具用钢。
Cr12钢是一种应用广泛的冷作模具钢,高碳、高铬类型莱氏体钢,具有较好的淬透性和良好的耐磨性。
由于钢中碳质量分数最高可达2.30%,从而钢变得硬而脆,所以冲压韧性较差,几乎不能承受较大的冲击荷载,易脆裂,而且易形成不均匀的共晶碳化物。
综合以上分析,得出的特性如下:
真空脱气精炼处理钢质纯净。
球化退火软化处理,切削加工性能良好。
强化元素钒,钼特殊加入,耐磨性极其优异。
因
Cr12钢具有较好的淬透性,淬火变形小,耐磨性,热硬性,强韧性均优于碳素工具纲,主要用于制造要求变型小,形状较复杂的轻载冲载模等。
Cr12纲具有良好的锻造性能,锻造温度范围为1150~1100℃,锻后空冷到650~700℃转入热灰中缓冷。
但该钢碳化物偏析较严重,锻后缓冷易形成网状碳化物,故锻造时需要反复锻粗拔长。
Cr12钢锻后应进行等温球化退火,加热温度790~830℃,等温温度700~720℃,退火后硬度为,269~217HBCr12n钢具有良好的淬透性,采用950℃加热淬火时,在获得较高硬度(63HRC)的同时,还可以获得最高的抗弯强度和韧性。
另外,如采用等温淬火对提高CrWMn钢的强韧性有显著效果,对于易断裂的模具可采用等温淬火。
Cr12钢要获得硬度大于60HRC,回火温度应不超过550~650℃。
2.1.3 零件毛坯形式选择:
根据该零件结构、材料及使用性能要求确定毛坯为锻件,
锻造时采用多向镦拔法,锻件残余网状碳化物,带状碳化物及
碳化物偏析三项≤2级。
锻后进行等温球化退火。
2.1.4 精度要求分析:
该零件为成型零件,有较高的加工精度要求。
选择加工工
艺及方法时应充分考虑这方面的要求,进而保证零件的使用
质量及使用寿命。
(1)尺寸精度:
主要是成型部分尺寸精度及定位孔的尺寸
精度要求较高。
(2)形位精度:
上下外表面有平行度要求,相临外表面有
垂直度要求,成型部分应保证形状精度。
(3)表面粗糙度:
成形部位Ra0.4,重要定位面为Ra0.8。
其它部位为Ra1.6~Ra3.2。
2.2 拟定工艺方案
对复杂型面凹模制造工艺应根据凹模形状、尺寸、技术要
求并结合本单位设备情况等具体条件来进行制定。
该落料模
零件可考虑采用以下两种加工方案:
(1)下料→锻造→退火→铣(刨)六面→平磨→钳(画线,
做各孔)→钳工压印→精铣内形→钳修至成品尺寸→淬火→
回火→平磨→钳研抛光。
(2)下料→锻造→退火→铣(刨)六面→平磨→划线→钳
工(做各孔及钻中心工艺孔)→铣漏料孔→淬火→回火→平磨
→数控线切割→钳工研磨。
第一种方案为传统的加工方法做,先用仿形刨或精密铣
床等设备将凸模加工出来,用凸模在凹模坯上压印,然后借助
精铣和钳工研配的方法来加工凹模。
第二种方案采用电火花线切割设备加工。
淬火前划线铣
出漏料孔,淬火后电火花线切割成形部分;若凸模设计为直通
式结构,也可使用同一线切割程序加工,这样可保证凸、凹模
形状及配合间隙。
2.3 工艺过程的制定
本文采用数控线切割加工方案来制定具体的工艺过程,
主要工艺如下:
序号工序名称工序主要内容
1下料 锯床下料56×105mm
2锻造 锻六方125×85×23
3热处理退火HBS≤230
4立铣 铣六方120.6×80.6×18.6
5平磨 磨六面对90°
6钳 倒角去毛刺,划线,做各孔
7工具铣钻线切割穿丝孔,铣漏料孔
8热处理淬火,回火,60~64HRC
9平磨 磨上、下面及基准面,对90°
10线切割找正,切割型孔留研磨量0.01~0.02mm
11钳 研磨型孔
第三章 加工程序编制
(1)设电极丝直径为0.15mm,单边放电间隙为
0.01mm。
(2)建立图2所示编程坐标系,按平均尺寸计算凹模刃口
轮廊交点及圆心坐标见下表。
图2 凹模型孔及平均尺寸
凹模刃口轮廊交点及圆心坐标
交点
及圆心XY交点及圆心XY
A 3.4270 9.4157F-50.025-16.0125
B-14.697516.0125G-14.6975-16.0125
C-50.02516.0125H3.4270-9.4157
D-50.0259.7949O00
E-50.025-9.7949O1-600
偏移量D=r+=(0.152+0.01)mm=0.085mm
穿丝孔在O点,按O→A→B→C→D→E→F→G→H→A
的顺序切割,程序如下:
G92X0Y0
G41D85(插入间隙补偿,此程序段应放在切入线之前)
G01X3427Y9416
G01X—14698Y16013
G01X—50025Y16013
G01X—50025Y9795
G02X—50025Y—9795I—9975J—9795
G01X—50025Y-16013
G01X-14698Y-16013
G01X3427Y-9416
G03X3427Y9416I-3427J9416
G40(G40应放在退出线之前,取消间隙补偿)
G01X0Y0(切出段)
第四章工艺评价
数控线切割加工无论在技术方面还是经济方面都具有许多特点。
如数控线切割加工的生产效率高,且操作方便,易于实现机械化与自动化;加工时由模具保证了制造零件的尺寸与形状精度,且一般不破坏零件材料的表面质量,模具的寿命一般较长,所以加工件的质量稳定,互换性好,具有“一模一样”的特征;数控线切割加工可加工出尺寸范围较大、形状较复杂的零件,而且一般没有切屑碎生成,材料的消耗较少,,因而是一种省料,节能,可缩短制造周期的加工方法,数控线切割加工的成本较低。
该零件的生产属于大批量的生产,这时采用其他方法制作该零件不能得到较好的效果。
但数控线切割加工时所使用的模具,制造的精度高,技术要求高,是技术密集产品。
所以只有在零件生产批量较大的情况下数控线切割加工的优点才能充分体现,从而获得较好的经济效益。
若凸模设计为直通式结构,也可使用同一线切割程序加工,这样可保证凸、凹模形状及配合间隙。
此加工法有节约原材料、节约能源、较高的生产效率,以及保证较高的加工精度等特点,在国民经济中越来越重要。
模具技术成为衡量一个国家制造水平的重要依据之一。
在模具加工行业,类似这样的零件很多,但是不同零件的技术要求、结构、材料及使用性能可能存在差异。
因此,我们在考虑零件的加工工艺时,应该具体问题具体分析,并结合工厂的实际情况选择一种合适的工艺方案,在保证零件加工质量及使用性能的前提下尽可能地降低生产成本,缩短制造周期,力争更好的经济效益。
结束语
这次的毕业设计是大学三年中的最后一个环节,是对三年的学习生活中所学的知识一个汇总和概括,使我们每个人都能总合运用所学的知识进行设计。
就我个人而言,通过这次毕业设计,使我学习到了许多知识,对模具的设计与制造有了极为深刻的认识,是一次由理论向实践的飞跃,让我感慨颇深,主要体会有以下几点:
1、扎实的基础课,专业课是模具设计的基础。
由于以前所学的课程难免有些理解不深,遗忘等,而本次设计又或多或少的用到了这些知识,从而迫使我再次回顾以前的课程,并加深了对这些课程的理解,如机械制图中的各种线型的特点应用,材料力学中的应力校核,热处理中各种材料与热处理性能,公差配合与测量技术中公差的正确选用,模具的加工与制造技术。
塑料模具的设计与制造步骤,模具材料的正确选用等。
2、理论与实践相结合的重要性以前的学习中,基本上是纯理论的学习,虽然有金工实习、毕业实习等实践的体味,但却停留在表面上,没有进行过真正的设计,从而使理论与实践严重脱节,在作设计的过程中,我才真正感觉到眼高手低的含义,同时也“窥一斑而知全豹