钢的热处理课程设计热工课设.docx
《钢的热处理课程设计热工课设.docx》由会员分享,可在线阅读,更多相关《钢的热处理课程设计热工课设.docx(30页珍藏版)》请在冰豆网上搜索。
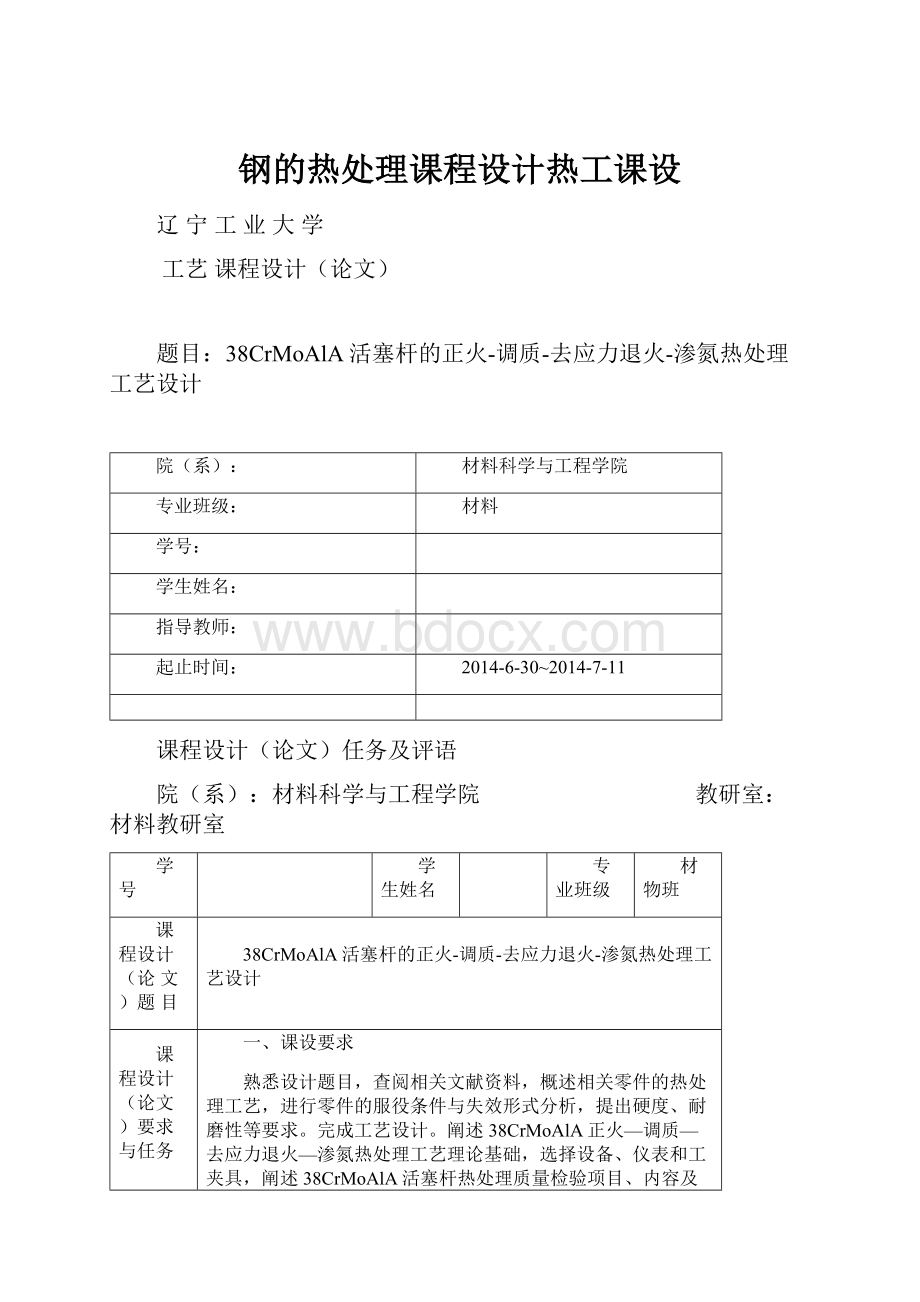
钢的热处理课程设计热工课设
辽宁工业大学
工艺课程设计(论文)
题目:
38CrMoAlA活塞杆的正火-调质-去应力退火-渗氮热处理工艺设计
院(系):
材料科学与工程学院
专业班级:
材料
学号:
学生姓名:
指导教师:
起止时间:
2014-6-30~2014-7-11
课程设计(论文)任务及评语
院(系):
材料科学与工程学院 教研室:
材料教研室
学号
学生姓名
专业班级
材物班
课程设计(论文)题目
38CrMoAlA活塞杆的正火-调质-去应力退火-渗氮热处理工艺设计
课程设计(论文)要求与任务
一、课设要求
熟悉设计题目,查阅相关文献资料,概述相关零件的热处理工艺,进行零件的服役条件与失效形式分析,提出硬度、耐磨性等要求。
完成工艺设计。
阐述38CrMoAlA正火—调质—去应力退火—渗氮热处理工艺理论基础,选择设备、仪表和工夹具,阐述38CrMoAlA活塞杆热处理质量检验项目、内容及要求;阐明38CrMoAl3A活塞杆热处理常见缺陷的预防及补救方法;给出所用参考文献。
二、课设任务
1.活塞杆材料的选择(要求在满足工件使用性能的前提下,兼顾经济性和工艺性,合理选择材料);
2.给出38CrMoAlA的C曲线;
3.给出38CrMoAlA活塞杆冷热加工工艺流程图;
4.制定38CrMoAlA活塞杆正火—调质—去应力退火—渗氮热处理工艺。
三、设计说明书要求
设计说明书包括三部分:
1)概述;2)工艺设计;3)热处理工艺卡;4)参考文献。
设计说明书结构见《工艺设计模板》。
工作计划
集中学习0.5天,资料查阅与学习,讨论1.5天,设计7天:
1)概述0.5天,2)服役条件与性能要求0.5天,3)失效形式、材料的选择0.5天,4)结构形状与热处理工艺性0.5天,5)冷热加工工序安排0.5天,6)工艺流程图0.5天,7)热处理工艺设计2天,8)工艺的理论基础、原则0.5天,9)设计工夹具0.5天,10)可能出现的问题分析及防止措施0.5天,11)热处理质量分析0.5天,设计验收1天。
指导教师评语及成绩
成绩:
学生签字:
指导教师签字:
年月日
目录
138CrMoAlA钢活塞杆热处理工艺概述1
238CrMoAlA活塞杆的热处理工艺设计2
2.1活塞杆的服役条件、失效形式2
2.2活塞杆技术要求及零件示意图2
2.3活塞杆的材料选择3
2.4活塞杆38CrMoAlA的C曲线3
2.5活塞杆的加工工艺流程图4
2.638CrMoAlA活塞杆的正火-调质-去应力退火-渗氮热处理工艺5
2.738CrMoAlA钢的正火-调质-去应力退火-渗氮热处理工艺理论7
2.838CrMoAlA钢活塞杆热处理的设备、仪表和工夹具选择13
2.9活塞杆的热处理质量检验项目、内容及要求16
2.10活塞杆的热处理常见缺陷的预防及补救方法17
3热处理工艺卡19
3.1活塞杆正火工艺卡19
3.2活塞杆调质工艺卡20
3.3活塞杆去应力退火工艺卡21
3.4活塞杆渗氮工艺卡22
4参考文献23
138CrMoAlA钢活塞杆热处理工艺概述
活塞杆是支持活塞做功的连接部件,大部分应用在油缸、气缸运动执行部件中,是一个运动频繁、技术要求高的运动部件。
活塞杆在正常使用中,承受交变载荷作用,有密封装置往复摩擦其表面,所以该处要求硬度高又耐磨。
而经过渗氮后的38CrMoAlA钢具有极高的硬度,而心部则有良好的综合力学性能,并增加其表面耐磨性和抗蚀能力。
调质热处理后获得回火索氏体,提高心部力学性能,同时减小渗氮时氮化物分布的不均匀性。
对于活塞杆,选用38CrMoAl钢调质后渗氮,更易满足其较高的硬度、渗氮层深度要求。
38CrMoAlA钢热处理工艺为正火—调质—去应力退火—渗氮,通过不同的热处理工艺分析,更加明确在执行热处理工艺过程中所需要注意的问题。
能够正确确定加热温度、时间,保温时间,冷却方式,其目的就是通过正确的热处理工艺,使金属材料的潜在能力得到充分的发挥。
正火的主要目的是消除锻造缺陷,消除活塞杆内部过大的应力,增加活塞杆的韧性,改善材料的切削性,并为最终热处理做好组织准备。
调质的主要目的是得到强度、塑性都比较好的综合机械性能。
退火的目的是为了降低钢的硬度,提高其塑性,细化晶粒,均匀内部组织及成分,消除钢中的残余内应力,提高切削加工性能,为最终热处理做好准备。
而且经过氮化处理的38CrMoAl钢具有极高的硬度、耐磨性、疲劳强度、抗腐蚀性、红硬性以及抗咬合性。
在设计正火—调质—去应力退火—渗氮热处理工艺中,本设计借鉴了《热处理工程师手册》,《热处理手册》,《实用热处理手册》,《机械加工工艺方案设计及案例》《热处理工艺与实践》,《热处理使用技术》等。
根据工艺设计的理论基础设定了完整的热处理工艺流程,使热处理的活塞杆表面具有极高的硬度、耐磨性、疲劳强度、抗蚀性、红硬性以及抗咬合性,从而满足活塞杆的质量要求。
238CrMoAlA活塞杆的热处理工艺设计
2.1活塞杆的服役条件、失效形式
2.1.1服役条件
活塞杆是支持活塞做功的连接部件,大部分应用在油缸、气缸运动执行部件中,是一个运动频繁、技术要求高的运动部件。
在正常使用中,承受交变载荷作用,有密封装置往复摩擦其表面,所以该处要求硬度高又耐磨。
2.1.2失效形式
活塞杆在工作时,承受高频率的返复拉压应力,易产生疲劳断裂;外表面与密封材料四氟乙烯进行快速多次摩擦,一旦磨损严重,会引起介质泄漏;其使用在含H2S成分的气体介质中,易遭受腐蚀。
因此,要求活塞杆具有耐腐蚀性、有较好的基体强度及外表面的耐磨损性能。
2.2活塞杆技术要求及零件示意图
2.2.1技术要求
活塞杆加工要求高,其加工质量的好坏直接影响整个产品的寿命和可靠性。
其表面粗糙度要求为Ra0.4~0.8μm,对同轴度、耐磨性要求严格。
活塞杆结构比较简单,但长径比很大,属于细长轴类零件,刚性较差,为了保证加工精度,在车削时要粗车、精车分开,而且粗、精车一律使用跟刀架,以减少加工时工件的变形。
在加工两端螺纹时要使用中心架。
在选择定位基准时,为了保证零件同轴度公差及各部分的相互位置精度,所有的加工工序均采用两中心孔定位,符合基准统一原则。
硬度要求:
经调质处理和表面渗氮后,心部硬度为28~32HRC,表面渗氮层深度0.2~0.3mm,表面硬度为62~65HRC。
渗氮处理时,螺纹部分等应采取保护措施进行保护。
[4]
2.2.2零件示意图
图1活塞杆零件示意图
2.3活塞杆的材料选择
活塞杆,不论是液压的还是气压的,经常运动,需要润滑良好,不易生锈,根据活塞杆的服役条件、失效形式及性能要求选择符合条件的材料,一般可以选用60Mn、40Cr、38CrMoAlA钢等,这些钢都具有高的硬度和耐磨性,同时具有高的耐腐蚀性。
但热处理变形大,精度要求较高时,制造出的活塞杆刚性不够,受到切削力时容易扭曲变形。
60Mn热处理工艺为调质、球化退火、感应淬火和低温时效耐磨性好,精加工后表面粗糙度可达到0.02~0.04μm,但其整体淬火活塞杆承受冲击能力差。
40Cr调质或正火、淬火、低温时效耐磨性好,生产成本低,能承受一定冲击,活塞杆的负荷较小,比较容易生锈。
38CrMoAlA钢是应用最广的渗氮钢。
该钢经渗氮处理后,可获得很高的硬度,而心部则有良好的综合力学性能,并增加其表面耐磨性和抗蚀能力,具有良好的淬透性。
加入Mo后,抑制了材料的第二类回火脆性,心部具有一定的强韧性,因而广泛用于主轴、螺杆、活塞杆等需高硬度、高耐磨而又冲击不大的零件。
渗氮前先进行调质热处理,获得回火索氏体,提高心部力学性能,同时减小渗氮时氮化物分布的不均匀性。
对于活塞杆,选用38CrMoAlA钢调质后渗氮,更易满足其较高的硬度、渗氮层深度要求。
由活塞杆的服役条件、失效形式等综合比较,考虑到活塞杆的综合精度,采用38CrMoAlA材料,使活塞杆既有一定的韧性,又具有较好的耐磨性、较高的强度及耐腐蚀性。
经过调质和表面氮化处理后,钢表面可获得最高氮化层硬度,达到900~1000HV。
[7.8]
2.4活塞杆38CrMoAlA的C曲线
影响C曲线的因素主要有以下几点:
1)含碳量随着奥氏体中含碳量的增加,奥氏体的稳定性增大,C曲线的位置向右移,这是一般规律。
2)合金元素除Co以外的几乎所有合金元素溶入奥氏体后,都增加奥氏体的稳定,使C曲线不同程度的右移。
某些合金元素当达到一定含量时,还改变C曲线的形状。
3)加热温度和保温时间随加热温度提高和保温时间延长,奥氏体晶粒长大,晶界面积减少,奥氏体成分更加均匀。
这些都不利于过冷奥氏体的转变,从而提高了奥氏体的稳定性,使C曲线右移。
[9]
通过查找《热处理手册》获得38CrMoAlA钢的成分如表1所示,C曲线如图2所示:
表138CrMoAlA钢的化学成分(GB/T1299—2000)W/%
C
Si
Mn
Cr
Mo
Al
0.379
0.42
0.42
1.38
0.23
0.82
图238CrMoAlA钢C曲线
通过查《实用热处理手册》得到38CrMoAlA钢的临界点及热处理工艺参数如表2所示:
表238CrMoAlA钢的临界点及热处理工艺参数
Ac1
Ac3
正火温度
淬火温度
淬火介质
淬火硬度
回火温度
760℃
885℃
930~970℃
920~940℃
油或水
≥52HRC
620~650℃
2.5活塞杆的加工工艺流程图
图3活塞杆加工工艺流程图
2.638CrMoAlA活塞杆的正火-调质-去应力退火-渗氮热处理工艺
2.6.1正火工艺曲线
一般均安排在毛坯生产之后,切削加工之前,或粗加工之后,半精加工之前。
其主要目的是消除锻造缺陷,消除活塞杆内部过大的应力,增加活塞杆的韧性,改善材料的切削性,并为最终热处理做好组织准备。
正火加热温度范围为930~970℃,保温2h后空冷[2]。
38CrMoAlA钢活塞杆的正火工艺曲线如图4所示:
图438CrMoAl钢正火工艺曲线
2.6.2调质工艺曲线
调质通常指淬火+高温回火,以获得回火索氏体的热处理工艺。
方法也就是先淬火,淬火温度:
亚共析钢为Ac3+30~50℃;过共析钢为Ac1+30~50℃;合金钢可比碳钢稍稍提高一点,为920~940℃,保温2h后油淬。
活塞杆要求具有较高的硬度和疲劳强度,心部硬度为HRC35~40。
所以本设计的回火温度为620~650℃,保温0.5~1h后空冷。
调质的主要目的是得到强度、塑性都比较好的综合机械性能。
[3]38CrMoAlA钢活塞杆的调质的工艺曲线如图5所示:
图538CrMoAl钢的调质的工艺曲线
2.6.3去应力退火工艺曲线
去应力退火是将工件加热到Ac1以下的适当温度,保温一定时间后逐渐缓慢冷却的工艺方法。
其目的是为了去除由于机械加工、变形加工、铸造、锻造、热处理以及焊接后等产生的残余应力。
38CrMoAlA钢活塞杆的去应力退火工艺曲线如图6:
图6去应力退火工艺曲线
2.6.4渗氮工艺曲线
渗氮的目的是为了提高工件的硬度、耐磨性及疲劳寿命,提高工件在腐蚀介质环境的耐蚀性。
渗入钢中的氮与钢中的合金元素结合形成各种合金氮化物,特别是氮化铝、氮化铬。
这些氮化物具有很高的硬度、热稳定性和很高的弥散度,因而可使渗氮后的钢件得到高的表面硬度、耐磨性、疲劳强度、抗咬合性、抗大气和过热蒸汽腐蚀能力、抗回火软化能力,并降低缺口敏感性。
与渗碳工艺相比,渗氮温度比较低,因而畸变小,渗氮有多种方法,本设计采用的是气体渗氮,渗氮温度480~560℃。
38CrMoAlA钢活塞杆的渗氮工艺曲线如图7所示:
图738CrMoAl钢渗氮热处理曲线
2.738CrMoAlA钢的正火-调质-去应力退火-渗氮热处理工艺理论
2.7.1活塞杆正火工艺理论原理
1.正火的目的
正火的主要目的是消除锻造缺陷,消除活塞杆内部过大的应力,增加活塞杆的韧性,改善材料的切削性,并为最终热处理做好组织准备。
2.正火加热温度
通常对于亚共析钢正火的加热温度通常为Ac3+30~50℃。
而对于中碳合金钢的正火温度正火温度通常为Ac3+50~100℃,38CrMoAlA是中碳低合金结构钢,正火温度应为Ac3+50~100℃。
因为有少量合金元素,较难加热,所以温度在此基础上要稍有提高,由38CrMoAlA钢的C曲线可知38CrMoAlA钢的Ac3为885℃,所以正火加热温度范围为930~970℃。
加热温度过低先共析铁素体未能全部溶解而达不到细化晶粒的作用,加热温度过高会造成晶粒粗化恶化钢的力学性能。
[3.9]
3.正火加热保温时间
保温时间,这个问题比较复杂,一般由试验确定,但也有个经验公式:
t=αKD
(1)
t—保温时间(min);
α—加热系数(min/mm);
K—反映工件装炉时的修正系数,通常在1.0~1.3范围内选取;
D—工件的有效厚度(mm);
工件有效厚度的计算原则是:
薄板工件的厚度即为其有效厚度,长的圆棒料直径为其有效厚度,正方体工件的边长为其有效厚度,长方体工件的高和宽小者为其有效厚度,带锥度的圆柱形工件的有效厚度是距小端2L/3(L为工件的长度)处的直径,带有通孔的工件,其壁厚为有效厚度。
一般情况下,碳钢可以按工件有效厚度每25mm/h来计算保温时间,合金钢可以按工件的有效厚度每20mm/h来计算保温时间,活塞杆的有效厚度为25mm,所以加热时间应为1.25h,可适当延长加热时间到2h。
[3.8]
2.7.2调质工艺原理
1.调质的目的
调质的目的是使工件得到所需的强度、硬度及力学性能,从而提高使用寿命。
调质件大都在比较大的动载荷作用下工作,它们承受着拉伸、压缩、弯曲、扭转或剪切的作用,有的表面还具有摩擦,要求有一定的耐磨性等等。
总之,零件处在各种复合应力下工作。
这类零件主要为各种机器和机构的结构件,如轴类、连杆、螺栓、齿轮等,在汽车和拖拉机等制造工业中用得很普遍。
尤其是对于重型机器制造中的大型部件,调质处理用得更多。
在机械产品中的调质件,因其受力条件不同,对其所要求的性能也就不完全一样。
一般说来,各种调质件都应具有优良的综合力学性能,即高强度和高韧性的适当配合,以保证零件长期顺利工作。
2.38CrMoAlA钢的调质工艺
经氮化后的工件要求表面有高硬度,并具有一定深度的氮化层,有时它本身是最后一道热处理工序,对工件的要求是氮化前有均匀而有细致的组织(即回火索氏体),以保证工件心部有较高的强度和良好的韧性,不允许存在游离的铁素体,表面不能有脱碳层,氮化前的表面粗糙度应小于Ra1.6μm,从而提高其综合力学性能,为氮化做好必要的组织准备,因此必须进行调质处理(淬火+高温回火)。
正确选择淬火和回火温度是工件调质是否合格的关键。
(1)淬火
把钢加热到临界点Ac1或Ac3以上一定温度,保温一定时间,然后以大于临界淬火速度的速度冷却,使过冷奥氏体转变为马氏体或贝氏体组织的热处理工艺称为淬火。
[9]
1)淬火方式、冷却介质的确定
淬火方法的分类是以冷却方式的不同划分的,常用的淬火工艺方法有:
单介质淬火、双介质淬火、分级淬火和等温淬火。
由于活塞杆的形状简单、尺寸较小,本设计选择单介质淬火,即将加热奥氏体化后的钢件放入单一淬火介质中,连续冷却到室温的操作方法。
其特点是操作简单,易于实现自动控制,但水中淬火变形与开裂倾向大;油中淬火冷却速度小,淬透直径小,大件无法淬透。
只适用于形状简单、尺寸较小碳钢和合金钢工件。
为了防止变形和开裂,要选择在油中淬火[3]。
2)淬火加热温度的确定
加热温度,亚共析钢淬火加热温度为Ac3+30~50℃,一般在空气炉加热比在盐浴中加热高10~30℃,采用油、硝盐淬火介质时,淬火加热温度应比水淬提高20℃左右。
共析钢、过共析钢淬火加热温度为Ac1+30~50℃,一般合金钢淬火加热温度为Ac1或Ac3+30~50℃。
本设计中38CrMoAlA钢是合金结构钢,含碳量为0.35~0.42%,因此在调质过程中淬火加热温度为Ac3+30~50℃,即920~940℃。
[3]
3)淬火保温时间的确定
保温时间,加热与保温时间由零件入炉到达指定工艺温度所需升温时间(t1),透热时间(t2)及组织转变所需时间(t3)组成。
其中组织转变在升温到>Ac1时便发生,因之与透热时间有交叉。
t1+t2有设备功率、加热介质及工件尺寸、装炉数量等因素决定,t3则与刚才的成分、组织及热处理技术要求等有关。
普通碳钢及低合金钢在透热后保温5~15min即可满足组织转变要求,合金结构钢透热后应保温15~25min。
计算加热时间一般由工件“有效厚度”乘以加热系数,与正火的加热时间的确定相同。
所以本设计调质时的淬火时间为2h。
[3]
4)淬火加热速度的确定
对于形状复杂,要求变形小,或用合金钢制造的大型铸锻件,必须控制加热速度以保证减少淬火畸变及开裂倾向,一般以30~70℃/h限速升温到600~700℃,在均温一段时间后再以50~100℃/h速度升温。
形状简单的中、低碳钢,直径小于400mm的中碳合金结构钢可直接到温入炉加热。
[3]
(2)高温回火
淬火后在500~650℃温度回火为高温回火,已获得回火索氏体组织,使渗氮件心部有较高的综合力学性能。
1)回火温度的确定
常用回火温度与硬度有关。
活塞杆要求具有较高的硬度和疲劳强度,心部硬度为HRC35~40。
所以本设计的回火温度为620~650℃。
[3]
2)回火时间的确定
从工件入炉后炉温升至回火温度时间开始计算回火时间一般为0.5~1h,可参考经验公式加以确定:
tn(min)=Kn+An×D[1]
(2)
式中tn——回火时间(min);
An——回火系数;
Kn——回火时间基数;
D——工件有效厚度(mm),
表3Kn及An推荐值[1]
回火条件
300℃以下
300~450℃
450℃以上
箱式电炉
盐浴炉
箱式电炉
盐浴炉
箱式电炉
盐浴炉
Kn/min
120
120
20
15
10
3
An/(min/mm)
1
0.4
1
0.4
1
0.4
本设计的回火温度为620~650℃使用箱式电炉回火,工件的有效厚度为25mm,所以回火时间tn=10+1*25=35min,可适当延长,为0.5~1h。
2.7.3去应力退火工艺原理
去应力退火是为了去除工件内的由于机械加工、变形加工、铸造、锻造、热处理以及焊接后等产生的残余应力,而无需发生显微组织的转变,将工件加热到Ac1以下适当的温度,保持一定时间后缓慢冷却的工艺方法。
钢铁材料加热温度一般是500~650℃。
由于车削零件时不可避免地会产生内应力,在氮化时它会增加零件的变形,因此对于形状复杂的重要零件在磨削前要进行稳定化处理,即去应力退火,才能保证零件氮化后的变形量符合工艺的要求。
去应力退火的加热温度由《热处理工程师手册》可查为Ac1-100~200℃,38CrMoAlA钢的Ac1为760℃,所以退火加热温度为560~660℃,保温10~12h,随后缓慢冷却(炉冷至200℃出炉)。
为了防止变形和开裂,加热速度应控制在100~200℃∕h应当指出氮化前经过较直的工件,为防止其氮化过程中发生变形,必须进行去应力处理。
[1.8]
2.7.4渗氮工艺原理
1.渗氮的目的
钢件得到高的表面硬度、耐磨性、疲劳强度、抗咬合性、抗大气和过热蒸汽腐蚀能力、抗回火软化能力,并降低缺口敏感性。
与渗碳工艺相比,渗氮温度比较低,因而畸变小,可用于精度要求高、又有耐磨要求的零件,但由于渗氮层较薄,不适于承受重载的耐磨零件。
2.渗氮方式的选择
渗氮的方法有气体渗氮、液体渗氮、离子渗氮、气体氮碳共渗、液体氮碳共渗等,各种渗氮方法的特点如表4所示:
表4各种渗氮方法的特点[7]
渗氮方法
优点
缺点
气体渗氮
500~550℃渗氮,变形小;渗氮可控;设备简单,操作容易;适用于大批量生产,特别适用于复杂、渗层深的零件
渗氮时间长,生产效率低
液体渗氮
570~580℃渗氮,渗速快,效率高;适用于薄层渗氮
有公害,废液处理费用高
离子渗氮
520~570℃渗氮,渗速快,效率高;节约渗剂,节约能源,无公害;适用于均匀大量生产单一零件
设备投资费用高;温度不均匀,且不好测量
气体氮碳共渗
550~600℃渗氮,渗速较快,适用于较轻载荷零件;用于小批量零件和工模具
心部硬度较低
液体氮碳共渗
530~570℃渗氮,渗速较快,适用于较轻载荷零件大批量生产
心部硬度较低
综合比较选择气体渗氮,温度较低且变形小,操作简单。
气体渗氮渗氮剂为氨气。
3.活塞杆的气体渗氮工艺
气体渗氮一般以提高金属的耐磨性为主要目的,因此需要获得高的表面硬度。
它适用于38CrMoAlA等渗氮钢。
渗氮后工件表面硬度可达850~1200HV。
气体渗氮可采用一般渗氮法(即等温渗氮)或多段(二段、三段)渗氮法。
前者是在整个渗氮过程中渗氮温度和氨气分解率保持不变。
温度一般在480~520℃之间,氨气分解率为15~30%,保温时间近80小时。
这种工艺适用于渗层浅、畸变要求严、硬度要求高的零件,但处理时间过长。
多段渗氮是在整个渗氮过程中按不同阶段分别采用不同温度、不同氨分解率、不同时间进行渗氮和扩散。
整个渗氮时间可以缩短到近50小时,能获得较深的渗层,但这样渗氮温度较高,畸变较大。
(1)渗氮工艺参数
1)渗氮温度渗氮温度是一个重要的工艺参数。
渗氮温度越高,扩散越快,获得的渗氮层便越深。
但是渗氮温度高至550~600℃以上时,合金氮化物会发生强烈聚集长大引起弥散度减小,表面硬度显著降低。
过低的渗氮温度将使氮原子扩散减慢,为达到一定的渗氮深度需延长时间,同时导致工件表面不能吸收足够活性氮原子,硬度不高,渗层过浅,故渗氮温度不应低于480℃。
应综合考虑温度对工件表面硬度、变形量、心部性能的影响,渗氮温度一般在480~560℃左右。
2)渗氮时间渗氮时间的长短与渗氮温度和渗层厚度有关,同时还与渗氮钢的成分的等因素有关。
渗氮时间的长短与渗氮温度的关系是渗氮温度越高获得相同渗层所需时间越短;反之,所需时间越长。
在氮化温度一定时,主要取决于所要求的氮化层深度。
随着氮化时间的延长,氮化层深度的增加先快后慢,但过长的氮化时间对提高层深效果不明显。
渗氮时间是一个多因素的工艺参数,一般要通过生产实践才能得到正确的工艺参数。
3)氨分解率表示在一定温度下,分解的氮和氢的混合气体占整个炉气的体积百分比,氨分解率的高低直接影响着工件表面吸氮的速度。
实验表明,当分解率在15~40%左右时,钢件吸收氮的速度最快。
但当温度较高时,很难维持这样低的分解率。
[7]
(2)渗氮前的生产准备
1)去污处理。
零件装炉前要用汽油或酒精进行脱脂、去污处理,零件表面不允许有锈蚀及脏污。
2)防渗处理。
对零件非渗氮部分,可用电镀或涂料法进行防渗氮处理。
3)渗氮件的表面质量应良好,不允许有脱碳层存在,因此,零件在预先热处理前应留有足够的加工余量,以便在渗氮前的机加工能将脱碳层全部去除,以保证渗氮层的质量。
4)装炉前检查设备和渗氮夹具、电系统、管道、氨分解测定仪等应保证正常使用;渗氮夹具不允许有赃物或氧化皮,如有应清除。
5)随炉试样。
随炉的试样应与渗氮零件通材料并经过同样的预先处理。
(3)渗氮工艺
常用的气体渗氮有等温渗氮有等温渗氮、二