鼠标下壳.docx
《鼠标下壳.docx》由会员分享,可在线阅读,更多相关《鼠标下壳.docx(16页珍藏版)》请在冰豆网上搜索。
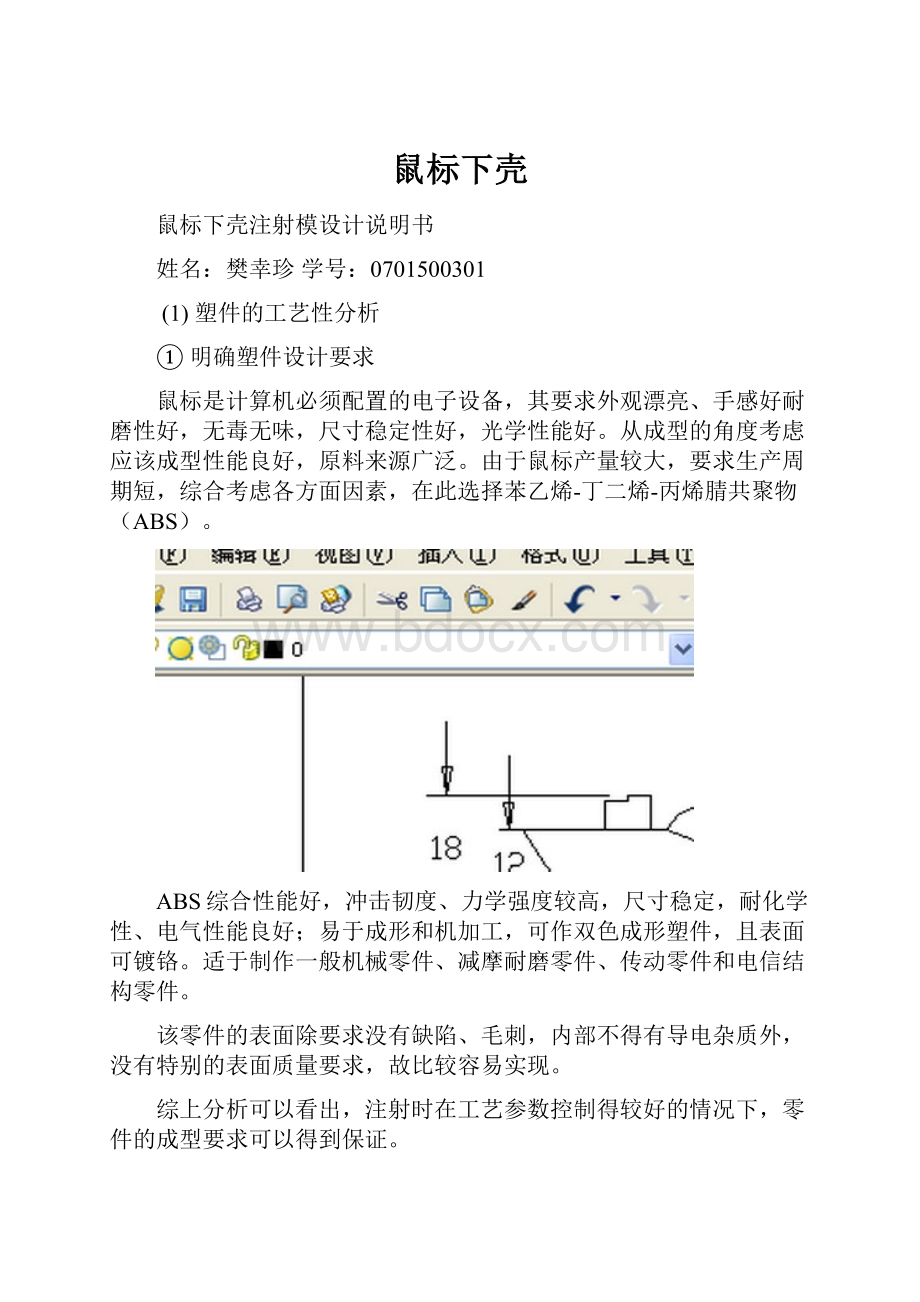
鼠标下壳
鼠标下壳注射模设计说明书
姓名:
樊幸珍学号:
0701500301
(1)塑件的工艺性分析
①明确塑件设计要求
鼠标是计算机必须配置的电子设备,其要求外观漂亮、手感好耐磨性好,无毒无味,尺寸稳定性好,光学性能好。
从成型的角度考虑应该成型性能良好,原料来源广泛。
由于鼠标产量较大,要求生产周期短,综合考虑各方面因素,在此选择苯乙烯-丁二烯-丙烯腈共聚物(ABS)。
ABS综合性能好,冲击韧度、力学强度较高,尺寸稳定,耐化学性、电气性能良好;易于成形和机加工,可作双色成形塑件,且表面可镀铬。
适于制作一般机械零件、减摩耐磨零件、传动零件和电信结构零件。
该零件的表面除要求没有缺陷、毛刺,内部不得有导电杂质外,没有特别的表面质量要求,故比较容易实现。
综上分析可以看出,注射时在工艺参数控制得较好的情况下,零件的成型要求可以得到保证。
②明确塑件的生产批量
由于该塑件要进行长期大批量生产,为了提高生产效率,降低塑件的生产成本,塑件的质量控制要求的尺寸精度,性能和表面粗糙度较高低,采用一模两腔生产模具可保证塑件的表面的粗糙度和质量,以缩短生产周期,提高生产效率,降低成本,能达到制件的最佳的技术经济性。
③查阅相关手册,记录塑料的相关参数
1)塑件材料苯乙烯-丁二烯-丙烯腈共聚物的加工特性:
(1)无定型塑料,其品种很多,应按品种确定成形方法及成形条件;
(2)吸湿性请,含水量应小于0.3%,必须充分干燥,要求表面光泽的塑件应要求长时间预热干燥;
(3)流动性中等,溢边料0.04mm左右;
(4)料温对物性影响较大;
(5)要注意浇注系统,选择好进料口位置、形式。
推动力过大或机械加工时塑件表面呈现白色痕迹。
脱模斜度宜取2度以上。
2)塑件ABS材料的物理性能、热性能
密度g/cm3
1.02~1.16
质量体积cm3/g
0.86~0.98
吸水率24h
0.2~0.4
熔点℃
130~160
熔融指数g/10min
200℃
维卡针入度℃
71~122
热变形温度℃
83~108
线膨胀系数10-5℃
7.0
比热容J/(kg·K)
1470
热导率W/(m·K)
0.263
3)塑件材料的成形条件
注塑成型机类型
螺杆式
密度g/cm3
1.03~1.07
计算收缩率%
0.3~0.8
预热
温度℃
80~85
时间h
2~3
料筒温度℃
后段
150~170
中段
165~180
前段
180~200
模具温度℃
50~80
注塑压力MPa
60~100
成形时间s
注塑时间
20~90
高压时间
0~5
冷却时间
20~120
总周期
50~220
螺杆转速r/min
30
后处理
方法
红外线灯、烘箱
温度℃
70
时间h
2~4
(2)模具总体设计
①塑件在模具中的方位的确定;
型腔的布置和浇口的开设部位应力求对称,以防模具承受偏载而产生溢料现象,并且型腔的排列宜紧凑,以节约钢材,减轻模具的质量。
这里采用一模两腔,对称布置,结构紧凑。
②分型面的选择;
分型面是分开模具,取出制品的面。
分型面是决定模具结构形式的重要应素,它与模具的整体结构和模具的制造工艺有密切的关系,并且直接影响到塑料熔体的流动充填特性及塑件的脱模,注射模具有一个分型面和多个分型面的模具。
结合相关零件的特点,选择零件的最大端即零件的低面为分型面,这样,在开模时容易取出零件。
下图为分型面示意图,红色线框为分型面。
③浇注系统的选择;
1、主流道的设计参考教材《塑料成型工艺与模具设计》主流的部分尺寸:
查教材《塑料成型工艺与模具设计》常用热塑性塑料注射机型号和主要技术规格XS-ZY-125:
喷嘴球半径=ф12㎜;主流道小端直径=5㎜。
浇口套与定位圈的配合采用H7/m6;浇口套与定位圈的配合H9/f8。
1)分流道截面的选择与确定
根据分流道截面流道的表面积比(指流道的表面积与体积比称之为表面积比),能使塑料熔体的温度下降小、阻力小、流道效率高,以及加工容易和顺利脱模为原则,故选择分流道截面为圆形。
2)分流道的大小与计算
分流道是主流道与浇口之间的进料通道。
在多型腔模具中分流到必不可少。
在分流道设计时应考虑尽量减小在流道内的压力损失和尽可能避免熔体温度的降低,同时还要考虑减小流道的容积。
该制品的分流道直径根据制品重量和壁厚由参考文献中的查得
=5
。
2、侧浇口的设计
本模具采用一模两腔,采用侧浇口。
侧浇口又称边缘浇口,其截面为矩形,应用范围广泛。
1)其一般开在分型面上,取厚h=0.5~2mm,宽B=0.8~2.4mm(也可取塑件厚的1/3~2/3),。
2)侧浇口的尺寸推荐值
深度h=0.5~2mm,取1mm;宽度B=0.8~2.4mm,取1.5mm;浇口长度长L=0.7~2mm,取1mm。
3)侧浇口位置的选择
根据浇口的位置对塑件有直接的影响,位置选择应尽量避免注塑缺陷的出现以及缩短成型周期为前提和原则,故侧浇口设在鼠标尾部边缘。
④成型零件的总体结构;
成型零件分为整体式和组合式。
这里我们采用组合式。
组合式能简化模具制造工艺、提高模具质量、保证塑件精度要求、节省优质钢材、方便热处理。
鼠标凸模有两组小型芯,组合方式如下图示意。
型芯是用来形成制品的内表面。
它分为以下三种形式:
(1)组合式主型芯
(2)圆柱形型芯
(3)异形型芯结构
(4)镶拼型芯结构
结合制品内部结构,对以上的形式进行比较,组合式型芯的优点是节省优质模具钢材、便于机加工和热处理。
可以用轴肩连接,也可采用螺钉固定。
圆柱形型芯制造方便,采用反嵌法。
异形非圆形的型芯在固定时大都采用反嵌法,对于复杂的型芯,为了便于加工,可采用镶拼型芯使机加工和热处理工艺大为简化,但要注意镶拼结构的合理性。
最终选定第一种方式,组合式型芯。
它的固定形式是用轴肩连接。
⑤排气方式选择;
要保证注射成型过程的顺利进行,不发生被压缩气体产生的高温,引起塑件的局部炭化烧焦,或使塑件产生气泡,或使塑件熔接不良引起强度下降,甚至充模不满等缺陷必须重视模具的排气系统设计。
本模型排气主要是通过分型面间隙、推杆和推杆孔的配合间隙自然排气排出,而不必再开设专门的排气槽。
⑥顶出机构的结构;
按照推出机构设计的原则:
1)不影响塑件质量。
应使成型制件不变形,不变白,不卡住、迅速可靠地脱模、推出痕迹应不影响外观质量;2)结构优化、运行可靠、机构尽可能简单、零件制造方便、配换容易;3)尽量设计在动模一侧。
脱模机构通常包括四种:
推杆推出机构、推管推出机构、推件板推出机构、推块推出机构、联合推出机构及其他特殊推出机构。
本制品为薄壁的容器塑件,故采用推杆推出机构。
其中推杆推出机构具有脱模力大而均匀,运动平稳,无明显的推出痕迹等特点,且不必另设复位机构,在合模过程中推杆依靠弹簧力的作用回到初始位置。
本制品为薄壁容器器件,故采用推杆推出机构,其推出效果如下图所示。
⑦浇注系统凝料的脱出方式。
分型时主流道凝料从定模拉出,整个浇注系统和塑件通过浇口连接在一起,推出塑件和冷料穴中的凝料时,浇注系统即随塑件一起脱出。
(3)模具设计的有关计算
①成形零件工作尺寸的计算,
该成型零件工作尺寸计算时均采用平均尺寸、平均收缩率、平均制造公差和平均磨损量来进行计算。
在计算成型零件型腔和型芯的尺寸时,塑件和成型零件的尺寸均按单向极限制,如果塑件的公差时双向分布的,则应按这个要求加以换算。
而孔中心矩尺寸则按公差带对称分布的原则进行计算。
由参考文献可知聚丙烯材料的成型收缩率为S=0.3%~0.8%,故平均收缩率S
=(0.3+0.8)%/2=0.55%,查表9.4-5取模具制造公差
。
1)型芯的径向尺寸计算
型芯的径向尺寸计算公式:
式中
型芯径向名义尺寸(最大尺寸);
制品的名义尺寸(最小尺寸),其它同上。
②型腔壁厚的确定;
在确定注射机工作范围与模具相关尺寸的关系时需要解决所设计模具的厚度能否满足所选注射机上模具高度的安装要求这个问题。
模具厚度Hm太大,将会造成模具锁模力不足而锁不紧;模具厚度Hm太小,将会造成模具在注射机上压不紧。
注射机由于结构限制,一般都给出了其允许的最大模具厚度Hmax和最小模具厚度Hmin。
Hmin≤Hm≤Hmax其中,由XS-ZY-125型注射机技术参数得知,Hmax=300mm、Hmin=200mm,及Hm的范围为:
200~300mm。
③模具加热、冷却系统的确定
由于ABS黏度和流动性一般,塑料成型时的模具温度为50~80摄氏度,故模具不需要专门设置加热装置,只要设置冷却冷却系统以确保合理的模温即可,但注塑前要对模具进行预热,使模具温度达到80度左右再注塑。
因ABS对温度较敏感需考虑设冷却系统,利用铜管镶入模具冷却孔内串联冷却。
常用的冷却方法有水冷却、空气冷却和油冷却,本设计采用水冷却,经济实惠。
(4)预选注射机
①计算塑件的体积和质量
对于规则的图形可以通过相关的体积公式来实现,而对于一些复杂或不规则的实体图形我们可以通过相关软件(如UG、PRO/E)来实现体积计算。
对于该制品来说属于不规则实体,因此,不能通过体积公式来计算体积,必须要借助相关软件来实现体积计算。
这里,借助了PRO/E来实现体积计算。
鼠标下壳的体积为V=15532㎜
=15.532cm
。
一模两腔,则总体积为4V=62.128cm
对于一次注射体积还要加上浇注系统中凝料的体积。
根据设计手册可查得ABS的密度为
=1.1g/cm
,故塑件的质
②计算确定注射机的相关参数
注塑机的最大注射量是指柱塞或螺杆在作一次最大注射行程时,注射装置所能达到的最大注出量。
为了保证正常的注射成型,选择注射机时,注塑机的最大注塑量应大于制品的质量或体积(包括流道及浇口凝料和飞边),通常注塑机的实际注塑量最好在最大注塑量的80﹪。
根据:
0.8M
≥M
+M
式中:
M
——注塑机的最大注塑量,g;
M
——塑件的质量,g,该零件M
=68.3408g
M
——浇注系统质量,g,该零件M
=1.1*7.1=7.81g。
故M
≥
=
锁模力是指注射过程中注射机能够提供的防止模具打开的最大锁紧力,计算公式:
其中,S——塑件与浇注系统在分型面上的总投影面积
P——最大注射压力是指注射过程中位于柱塞或螺杆前端的熔融塑料的压力
K——压力损失系数。
一般取值范围为1/4~1/2
Pa——有效注射压力
③结合注射压力的要求初步确定注射机的型号
初选符合上述要求的几种规格的注射机已备挑选。
最大注射量在98g以上,锁模力在44kN以上的机型有:
XS-ZY-125、SZY-300、XS-ZY-500、XS-ZY-1000、XS-ZY-4000。
④记录注射机与设计模具有关的技术参数
所以选用卧式XS-ZY-125。
型号国产注射机,其主要技术参数如下:
螺杆(柱塞)直径(毫米)
Φ42
喷嘴
球半径(毫米)
12
孔直径(毫米)
Φ4
注射容量(厘米或克)
125
定位孔直径(毫米)
Φ100
注射压力
1190
顶出
中心孔径(毫米)
两侧
孔径(毫米)
Ø22
孔距(毫米)
230
锁模力(kN)
900
模具厚度(毫米)
最大
300
最小
200
最大注射面积(厘米)
320
模板厚度(毫米)
300
(5)模具的具体设计
1)模架的选择
根据《塑料注射模中小型模架》(GB/T12556.1-1990),中小型模架分A1、A2、A3、A4四种基本型模架结构
这里,选用的模架为A2型,模板尺寸为250
400mm,导柱正装的中小型模架。
2)导向与定位机构设计
注射模的导向机构用于动定模之间的开合模导向和脱模机构的运动导向。
定位机构分模外定位和模内定位。
模内定位是通过定位圈使模具易于在注射机上安装以及模具的浇口套能与注射机喷嘴精确定位。
而模内定位则通过锥面定位机构用于动、定模之间的精密对中定位。
导柱导向机构是利用导柱和导套之间的配合来保证模具的对合精度。
导向结构的设计内容包括:
导柱和导套的机构设计;导柱和导套的配合;导柱和导套的数量和布置等。
导柱是与安装在另一半上的导套相配合,用以确定动、定模的相对位置,保证模具运动导向精确的圆柱形零件。
本模具采用如图的导向结构。
(6)注射机参数的校核
①最大注射量的校核;
0.8M
≥M
+M
式中:
M
——注塑机的最大注塑量,g;
M
——塑件的体积,g,该零件M
=68.3408g
M
——浇注系统体积,g,该零件M
=7.81g。
故M
≥
=
此处选定的注塑机注塑量为125g,所以满足要求。
②锁模力的校核;
锁模力是指注射机的锁模装置对模具所施加的最大夹紧力。
当高压的塑料溶体充满模具型腔时,沿锁模方向会产生一个很大的作用力,此力总是力图使模具沿分型面胀开。
为此,注射机的额定锁模力必须大于型腔内塑料熔体压力与塑件及浇注系统在分型面上的投影面积之和(即注射面积)的乘积。
一般,闭模时要从模外加大于型腔内压力一倍以上的锁模力。
F
>P
A(3-1-3)
式中:
P
——熔融型料在型腔内的压力(60MP~1000MP);
A——塑件和浇注系统在分型面上的投影面之和,经计算为80
;
F
——注塑机的额定锁模力,KN。
故F
>P
A=60×8000=480KN
此处选定的注塑机为900KN,满足要求。
③模具与注射机安装部分及运动部分的相关尺寸校核。
1)模具闭合高度校核
本模具的闭合高度为
,XS-ZY-125型注射机所允许模具的最小闭合厚度为
,最大厚度为
,即模具满足
的安装条件。
2)开模行程校核
注射机的开模行程应满足分开模具取出塑件的需要。
所选注塑机为XS-ZY-125型,其最大行程与模具厚度无关,故注塑机的开模行程应满足下式
(5~10)
式中
——注塑机最大开模行程,
。
H
——推出距离,
;
H
——包括浇注系统在内的塑件高度,
;
因为S=300
H
+H
+(5~10)=50+40+10=100
故开模行程满足要求。
(7)模具结构总装图
模具装配时要求相邻装配单元之间的配合与联接均需要按装配工艺确定的装配基准进行定位与固定,以保证其间的配合精度和位置精度,从而保证型芯与型腔间能精密均匀的配合和定位,开合运动与推出脱模机构都能够实现运动的精确性。
具体的工艺要求:
(1)通过装配与调整,使装配尺寸链的精度能够完全满足密封性的要求;
(2)装配完成的模具其塑料注射完全满足规定的要求;
(3)寿命期限可以达到预先规定的数值和水平等。
具体装配后,其装配图的三维图和爆炸效果图如下图所示。