石油化工工艺过程防爆安全技术标准版本.docx
《石油化工工艺过程防爆安全技术标准版本.docx》由会员分享,可在线阅读,更多相关《石油化工工艺过程防爆安全技术标准版本.docx(8页珍藏版)》请在冰豆网上搜索。
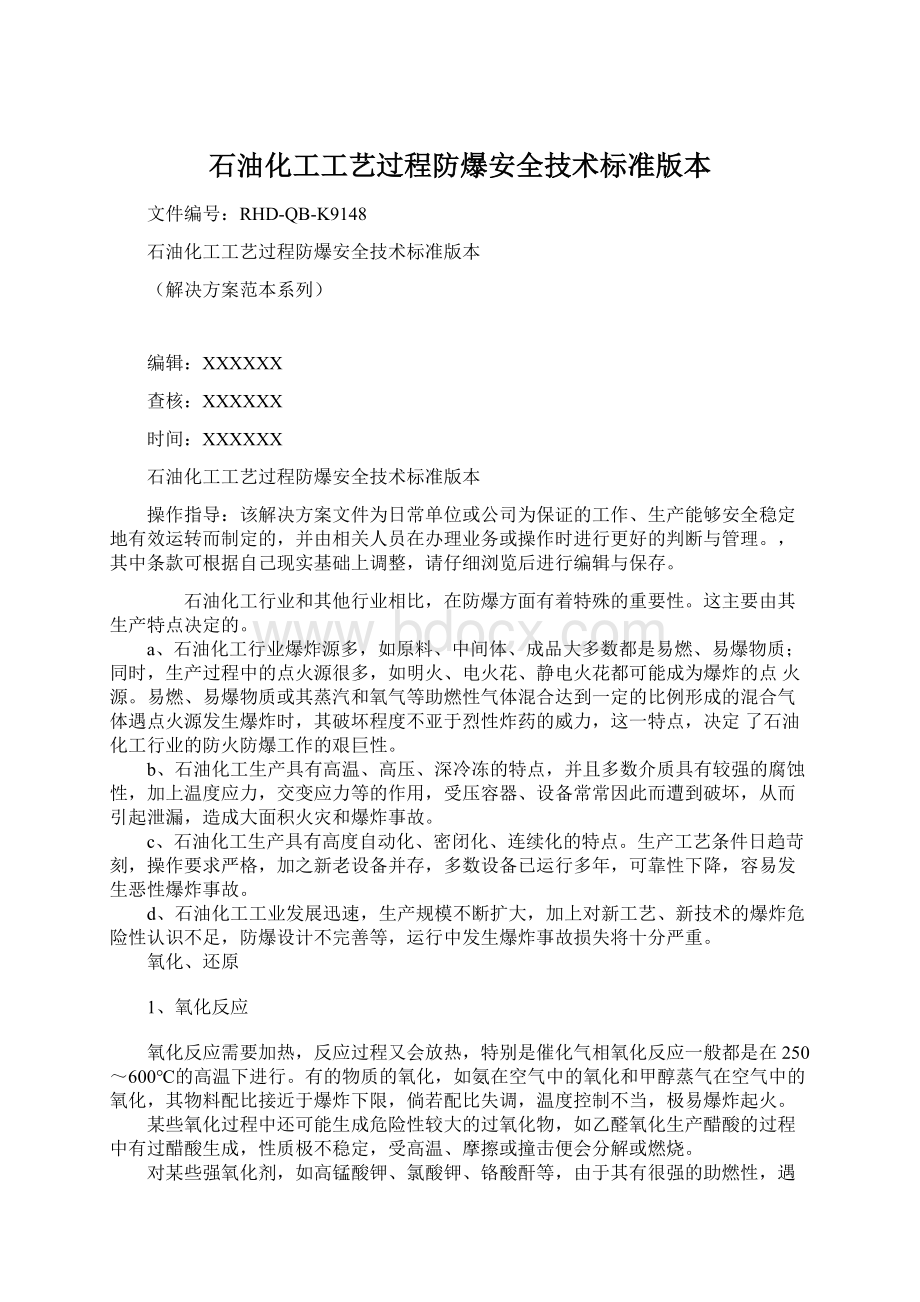
石油化工工艺过程防爆安全技术标准版本
文件编号:
RHD-QB-K9148
石油化工工艺过程防爆安全技术标准版本
(解决方案范本系列)
编辑:
XXXXXX
查核:
XXXXXX
时间:
XXXXXX
石油化工工艺过程防爆安全技术标准版本
操作指导:
该解决方案文件为日常单位或公司为保证的工作、生产能够安全稳定地有效运转而制定的,并由相关人员在办理业务或操作时进行更好的判断与管理。
,其中条款可根据自己现实基础上调整,请仔细浏览后进行编辑与保存。
石油化工行业和其他行业相比,在防爆方面有着特殊的重要性。
这主要由其生产特点决定的。
a、石油化工行业爆炸源多,如原料、中间体、成品大多数都是易燃、易爆物质;同时,生产过程中的点火源很多,如明火、电火花、静电火花都可能成为爆炸的点火源。
易燃、易爆物质或其蒸汽和氧气等助燃性气体混合达到一定的比例形成的混合气体遇点火源发生爆炸时,其破坏程度不亚于烈性炸药的威力,这一特点,决定了石油化工行业的防火防爆工作的艰巨性。
b、石油化工生产具有高温、高压、深冷冻的特点,并且多数介质具有较强的腐蚀性,加上温度应力,交变应力等的作用,受压容器、设备常常因此而遭到破坏,从而引起泄漏,造成大面积火灾和爆炸事故。
c、石油化工生产具有高度自动化、密闭化、连续化的特点。
生产工艺条件日趋苛刻,操作要求严格,加之新老设备并存,多数设备已运行多年,可靠性下降,容易发生恶性爆炸事故。
d、石油化工工业发展迅速,生产规模不断扩大,加上对新工艺、新技术的爆炸危险性认识不足,防爆设计不完善等,运行中发生爆炸事故损失将十分严重。
氧化、还原
1、氧化反应
氧化反应需要加热,反应过程又会放热,特别是催化气相氧化反应一般都是在250~600℃的高温下进行。
有的物质的氧化,如氨在空气中的氧化和甲醇蒸气在空气中的氧化,其物料配比接近于爆炸下限,倘若配比失调,温度控制不当,极易爆炸起火。
某些氧化过程中还可能生成危险性较大的过氧化物,如乙醛氧化生产醋酸的过程中有过醋酸生成,性质极不稳定,受高温、摩擦或撞击便会分解或燃烧。
对某些强氧化剂,如高锰酸钾、氯酸钾、铬酸酐等,由于其有很强的助燃性,遇高温或受撞击、摩擦以及与有机物、酸类接触,皆能引起燃烧或爆炸。
氧化过程中,在以空气为氧化剂时,反应物料的配比(反应可燃气体和空气的混合比例)应控制在爆炸极限范围之外,空气进入反应器之前,应经过气体净化装置,清除空气中的灰尘、水汽、油污以及可使催化剂活性降低或中毒的杂质以保持催化剂的活性,减少着火和爆炸的危险。
在催化氧化过程中,对于放热反应,应控制适宜的温度、流量,防止超温超压和混合气处于爆炸极限范围。
为了防止接触器在万一发生爆炸或燃烧时危及人身和设备安全,在反应器前后管道上应安装阻火器,阻止火焰蔓延,防止回火,使燃烧不致影响其他系统。
为了防止接触器发生爆炸,应有泄压装置。
应尽可能采用自动控制或调节,以及警报联锁装置。
使用硝酸、高锰酸钾等氧化剂时,要严格控制加料速度,防止多加、错加。
固体氧化剂应该粉碎后使用,最好呈溶液状态使用。
反应中要不间断地搅拌。
使用氧化剂氧化无机物,如使用氯酸钾生产铁蓝颜料时,应控制产品烘干温度不超过燃点,在烘干之前用清水洗涤产品,将氧化剂彻底除净,防止未起反应的氯酸钾引起已烘干的物料起火。
有些有机化合物的氧化,特别是在高温下的氧化反应,在设备及管道内可能产生焦状物,应及时清除以防自燃。
氧化反应系统宜设置氮气或水蒸气灭火装置。
2、还原反应
还原反应有的比较安全,但是有几种还原反应危险性较大,如初生态氢还原和催化加氢还原等均较危险。
无论是利用初生态氢还原,还是用触媒把氢气活化后还原,都有氢气存在,氢气的爆炸极限为4%~75%。
特别是催化加氢,大都在加热加压条件下进行,如果操作失误或因设备缺陷有氢气泄漏,与空气形成爆炸气体混合物,遇上火源即能爆炸。
操作过程中要严格控制温度、压力和流量;车间内的电气设备必须符合该爆炸危险区域内的防爆要求,且不宜在车间顶部敷设电线及安装电线接线箱;厂房通风要好,采用轻质屋顶,设置天窗或风帽,使氢气及时逸出;反应中产生的氢气可用排气管导出车间屋顶,经过阻火器向外排放;加压反应的设备要配备安全阀,反应中产生压力的设备要装设爆破板;还可以安装氢气检测和报警装置。
雷内镍吸潮后在空气中有自燃危险,即使没有火源存在,也能使氢气和空气的混合物发生爆炸、燃烧。
因此,用它们来催化氢气进行还原反应时,必须先用氮气置换反应器内的全部空气,经过测定证实含氧量降低到符合要求后,方可通入氢气。
反应结束后,应先用氮气把反应器内的氢气置换干净,方能打开孔盖出料,以免外界空气与反应器内的氢气相混,在雷内镍触媒作用下发生燃烧、爆炸。
雷内镍活化后应当储存于酒精中。
钯炭回收时要用酒精及清水充分洗涤,过滤抽真空时不得抽得太干,以免氧化着火。
用保险粉(Na2S2O4)做还原剂时,要注意保险粉遇水发热,在潮湿空气中能分解析出硫,硫蒸气受热有自燃的危险。
保险粉本身受热到190℃也有分解爆炸的危险,应妥善储藏,防止受潮;用水溶解时,要控制温度,可以在开动搅拌的情况下将保险粉分批加入冷水中,待溶解后,再与有机物接触进行反应。
还原剂硼氢化钾(钠)是一种遇火燃烧物质,在潮湿空气中能自燃,遇水和酸即分解放出大量氢气,同时产生高热,可使氢气燃烧而引起爆炸事故,应储于密闭容器中,置于干燥处,防水防潮并远离火源。
在工艺过程中,调节酸、碱度时要特别注意,防止加酸过快、过多。
使用氢化锂铝作还原剂时,要特别注意安全问题,因为这种催化剂危险性很大,遇空气和水都能燃烧,必须在氮气保护下使用,平时浸没于煤油中储存。
上述还原剂遇氧化剂会猛烈发生反应,产生大量热量,也有发生燃烧爆炸的危险。
还原反应的中间体,特别是硝基化合物还原反应的中间体具有一定的火灾危险。
例如,邻硝基苯甲醚还原为邻氨基苯甲醚的过程中,产生氧化偶氮苯甲醚,该中间体受热到150℃能自燃。
苯胺在生产中如果反应条件控制不好,可以生成爆炸危险性很大的环已胺。
采用危险性小,还原效率高的新型还原剂,对安全生产有很大的意义。
例如采用硫化钠代替铁粉还原,可以避免氢气产生,同时还解决了铁泥堆积的问题。
电解
电解在工业生产中有广泛的应用,食盐溶液电解是化学工业中最典型的电解反应例子之一。
食盐电解中的安全问题,主要是氯气中毒和腐蚀、碱灼伤、氢气爆炸以及高温、潮湿和触电危险等。
现就防爆问题叙述如下:
在正常操作中,应随时向电解槽的阳极室内添加盐水,使盐水始终保持在规定液面。
否则,如盐水液面过低,氢气有可能通过阴极网渗入到阴极室内与氯气混合。
要防止个别电解槽氢气出口堵塞,引起阴极室压力升高,造成氯气含氢量过高。
氯气内含氯量达5%以上,则随时可能在光照或受热情况下发生爆炸。
在生产中,单槽氯含氢浓度一般控制在2.0%以下,总管氯含氢浓度控制在0.4%以下,都应严格控制。
如果电解槽的隔膜吸附质量差;石棉绒质量不好;在安装电解槽时碰坏隔膜,造成隔膜局部脱落或者在送电前注入的盐水量过大将隔膜冲坏;以及阴极室中的压力等于或超过阳极室的压力时都可能使氢气进入阳极室,引起氯含氢量高。
此时应该对电解槽进行全面检查。
盐水有杂质,特别是铁杂质,致使产生第二阴极而放出氢气;氢气压力过大,没有及时调整;隔膜质量不好,有脱落之处;盐水液面过低,隔膜露出;槽内阴阳极放电而烧毁隔膜;以及氢气系统不严密而逸出氢气等,都可能引起电解槽爆炸或着火事故。
引起氢气或氢气与氯气的混合物燃烧或爆炸的着火源可能是槽体接地产生的电火花;断电器因结盐、结碱漏电及氢气管道系统漏电产生电位差而发生放电火花;排放碱液管道对地绝缘不好而发生放电火花;电解槽内部构件间由于较大的电位差或两极之间的距离缩小而发生放电火花;雷击排空管引起氢气燃烧;以及其他点火源等。
水银电解槽若盐水中含有铁、钙、镁等杂质时,能分解钠汞齐,产生氢气而引起爆炸。
若解汞室的清水温度过低,钠汞齐来不及在解汞室还原完,就可能在电解槽继续解汞而生成大量氢气,这也是水银电解发生爆炸的原因之一。
因此,加入的水温应能保持解汞室的温度接近于95℃,解汞后汞中含钠量宜低于0.01%,一般每班应作一次含钠量分析。
由于盐水中带入铵盐,在适宜的条件下(pH值<4.5时),铵盐和氯作用产生三氯化氮,这是一种爆炸性物质。
三氯化氮和许多有机物质接触或加热至90℃以上,以及被撞击时,即以剧烈爆炸的形式分解。
因此在盐水配制系统要严格控制无机铵含量。
突然停电或其他原因突然停车时,高压阀门不能立即关闭,以避免电解槽中氯气倒流而发生爆炸。
电解槽食盐水入口处和碱液出口处应考虑采取电气绝缘措施,以免漏电产生火花。
氢气系统与电解槽的阴极箱之间亦应有良好的电气绝缘。
整个氢气系统应良好接地,并设置必要的水封或阻火器等安全装置。
电解食盐厂房应有足够的防爆泄压面积,并有良好的通风条件,应安装防雷设施,保护氢气排空管的避雷针应高出管顶3m以上。
电解过程由于有氢气存在,有起火爆炸危险。
电解槽应安置在自然通风良好的单层建筑物内。
聚合
由于聚合物的单体大多是易燃易爆物质,聚合反应多在高压下进行,本身又是放热过程,如果反应条件控制不当,很容易引起事故。
例如高压聚乙烯反应一般在13~30MPa压力下进行,反应过程流体的流速很快,停留于聚合装置中的时间仅为10s到数分钟,温度保持在150~300℃。
在该温度和高压下,乙烯是不稳定的,能分解成碳、甲烷、氢气等。
一旦发生裂解,所产生的热量,可以使裂解过程进一步加速直到爆炸。
国内外都曾发生过聚合反应器温度异常升高,分离器超压而发生火灾;压缩机爆炸以及反应器管路中安全阀喷火而后发生爆炸等事故。
因此,严格地控制反应条件是十分重要的。
在高压聚乙烯生产中,主要危险因素有:
a.该过程处在高压下,所以当设备和管道的密封有极小损坏时,即会导致气体大量喷出到车间中,并和空气形成爆炸性气体混合物。
b.该过程为放热和热动力不稳定过程。
乙烯聚合反应产生的热效应为96.3kJ/mol,所以当热量来不及导出时,会引起乙烯爆炸性分解。
c.乙烯可能在设备和管道中聚合,使温度上升到危险程度,导致乙烯分解和聚合产品堵塞设备。
d.如果违反压力条件和规定的混合气体流量比,在设备中乙烯和氧气可能形成易爆混合物。
e.乙烯分解时产生的分解细粒状炭黑有可能堵塞反应器和管道,从而使过程难以正常进行,以致不得不停产进行设备清理。
由上述危险因素可见,必须对工艺流程的所有工序进行温度、压力和物料流速的严格自动控制和调节。
尤其应该准确地控制乙烯中氧的限制含量,因为当氧含量超过允许量时,反应速度将迅速加快,反应热来不及导出,以致使过程反应强度显著提高,最终使过程由乙烯爆炸性分解为甲烷和碳而结束。
此外,当过量供氧时,还会形成爆炸性混合物。
高压聚乙烯的聚合反应在开始阶段或聚合反应进行阶段都会发生暴聚反应,所以设计时必须充分考虑到这一点。
可以添加反应抑制剂或加装安全阀来防止。
在紧急停车时,聚合物可能固化,停车再开车时,要检查管内是否堵塞。
高压部分应有两重、三重防护措施;要求远距离操作;由压缩机出来的油严禁混入反应系统,因为油中含有空气,进入聚合系统能形成爆炸性混合物。
氯乙烯聚合是属于连锁聚合反应,连锁反应的过程可分为3个阶段,即链的开始、链的增长、链的终止。
聚合反应中链的引发阶段是吸热过程,所以需加热。
在链的增长阶段又放热,需要将釜内的热量及时导走,将反应温度控制在规定值。
这两个过程要分别向夹套通入加热蒸汽和冷却水。
温度控制多采用串级调节系统。
为了及时导走热量必须有可靠的搅拌装置。
由于氯乙烯聚合是采用分批间歇方式进行的,反应主要依靠调节聚合温度,因此聚合釜的温度自动控制十分重要。