2钢铁企业能耗指标管理.docx
《2钢铁企业能耗指标管理.docx》由会员分享,可在线阅读,更多相关《2钢铁企业能耗指标管理.docx(18页珍藏版)》请在冰豆网上搜索。
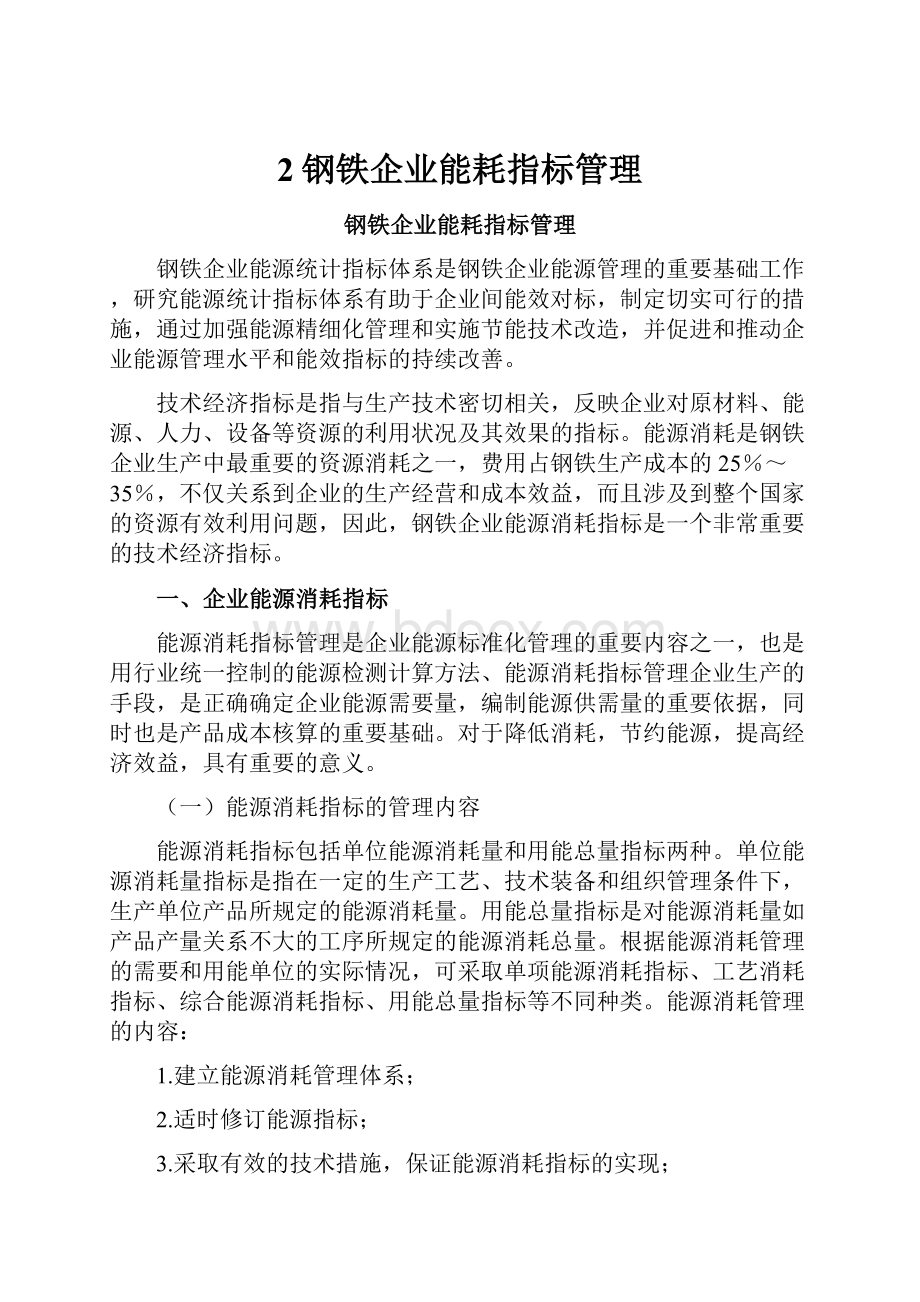
2钢铁企业能耗指标管理
钢铁企业能耗指标管理
钢铁企业能源统计指标体系是钢铁企业能源管理的重要基础工作,研究能源统计指标体系有助于企业间能效对标,制定切实可行的措施,通过加强能源精细化管理和实施节能技术改造,并促进和推动企业能源管理水平和能效指标的持续改善。
技术经济指标是指与生产技术密切相关,反映企业对原材料、能源、人力、设备等资源的利用状况及其效果的指标。
能源消耗是钢铁企业生产中最重要的资源消耗之一,费用占钢铁生产成本的25%~35%,不仅关系到企业的生产经营和成本效益,而且涉及到整个国家的资源有效利用问题,因此,钢铁企业能源消耗指标是一个非常重要的技术经济指标。
一、企业能源消耗指标
能源消耗指标管理是企业能源标准化管理的重要内容之一,也是用行业统一控制的能源检测计算方法、能源消耗指标管理企业生产的手段,是正确确定企业能源需要量,编制能源供需量的重要依据,同时也是产品成本核算的重要基础。
对于降低消耗,节约能源,提高经济效益,具有重要的意义。
(一)能源消耗指标的管理内容
能源消耗指标包括单位能源消耗量和用能总量指标两种。
单位能源消耗量指标是指在一定的生产工艺、技术装备和组织管理条件下,生产单位产品所规定的能源消耗量。
用能总量指标是对能源消耗量如产品产量关系不大的工序所规定的能源消耗总量。
根据能源消耗管理的需要和用能单位的实际情况,可采取单项能源消耗指标、工艺消耗指标、综合能源消耗指标、用能总量指标等不同种类。
能源消耗管理的内容:
1.建立能源消耗管理体系;
2.适时修订能源指标;
3.采取有效的技术措施,保证能源消耗指标的实现;
4.考核分析能源消耗指标完成情况,总结经验,提出改进措施。
(二)能源消耗指标管理的作用
能源消耗指标是编制能源供需计划的重要依据。
企业实行了先进合理的能源消耗指标管理,才能正确计算企业能源需要量,编制出准确的、科学的能源供需计划,预算企业能源成本。
能源消耗指标是科学地组织能源供应的重要基础。
企业制定先进合理的能源消耗指标,才能严格地按质、按量、按时组织能源供应计划,做好各项能源的平衡计划,并对消耗情况实施控制,从而保证生产的正常进行。
能源消耗指标是监督和促进企业内部开展节能工作的有力工具。
企业为了使其能源消耗指标经常保持在先进合理的水平上,就必须不断提高用能技术水平和能源管理水平。
能源消耗指标是企业加强经济核算和节能奖惩的依据。
(三)能源消耗指标的制定及制定方法
1.能源消耗指标制定的原则
“定质”与“定量”相统一的原则。
能源消耗指标的制订应该包括“定质”与“定量”两个方面。
定质,是确定所需要能源的品种、规格和质量要求,定量,是确定能源消耗的数量。
先进性和合理性相统一原则。
能源消耗指标必须反映生产过程中的技术水平和生产组织管理水平。
能源消耗指标的先进性,是指在满足工艺需要的前提下,充分考虑所能实现的各项节能措施效果,使制定的能源消耗指标能够比已达到的实际水平先进。
能源消耗指标合理性,是指指标必须是切合实际可行的、有科学依据的,是经过努力可以达到的。
因此,用能单位按照本单位能源消耗的历史最好水平和现行的生产工艺状况,核定能源消耗指标。
能源消耗指标的制订必须遵循从实际出发,深入生产第一线,进行调查研究,了解情况,掌握资料,实际测算,适当的科学分析,精确的核算等原则;制定的能源消耗指标应迅速及时,走在生产之前,对生产起指导和促进作用;依靠长期的指标资料积累和经常了解分析生产情况,使能源消耗指标准确;钢铁企业按照可计量性、工艺要求性以及便于核算考核性制定能源消耗指标;能源消耗指标制定既具有先进性,又要切实可行,对能源消耗尚未达到行业平均水平的,其指标要从严核定,以利于调动一切积极因素。
2.能源消耗指标制定的依据
(1)国家和地方有关能源消耗限额标准;
(2)近三年能源消耗计量统计资料和历史最好水平资料;
(3)近三年生产技术经济指标,如产量、品种、质量等;
(4)年度生产计划、技术经济指标;
(5)所耗能源的品种、品质、规格;
(6)生产技术及工艺的发展趋势,实施节能技改的情况;
(7)国内外同类产品单位能耗先进水平。
3.能源消耗指标制定的方法
制定能源消耗指标的主要方法有:
技术计算、实际测定和统计分析三种。
钢铁企业目前基本上是用统计分析法辅以技术计算法、实际测定法来确定指标,统计分析法与实际接近,涵盖环境和计量偏差影响因素,便于管理与考核。
为了提高能源消耗指标的准确性和可靠性,应以技术计算法和实际测定法制定能源消耗指标。
技术计算法。
技术计算法是根据产品设计、工艺过程、管理水平等各方面因素,通过精确计算,并考虑达到的先进能耗指标水平和采用节能技术措施等因素后制定能源消耗指标的一种方法。
实际测定法。
实际测定法是根据现场能源消耗的条件,通过能源消耗测定,用实际计算方法确定能源消耗指标。
实际测定法也可以通过对现有设备(工序)进行能量平衡测试,计算出该工序或设备的某种能源实际数量,再结合设备改造,改进操作和其他节能措施的实施,最后确定该设备(工序)的能源消耗指标。
统计分析法。
统计分析法是指在分析研究资料,并全面考虑有关工艺技术、操作技术水平、能源供应质量等因素的基础上制定出来的能源消耗指标。
(四)能源消耗指标的修订
由于影响能源消耗指标的各种因素是在不断变化的,因此能源消耗指标必须定期修改或临时修改,一般单项指标每年修改一次,遇到下述情况时,可做必要的临时修改:
1.能源消耗执行过程中,发现能源消耗指标脱离实际或计算错误时;
2.产品结构、用能设备和生产工艺有重大改变时;
3.提高生产或改进操作时;
4.能源品种、规格、质量等发生重大改变时。
由于能源消耗规律的作用,要求能源消耗指标具有相对稳定性。
因此,能源消耗指标一经确定,不宜经常改动,只做定期(如一年)修订,以便于贯彻执行。
(五)能源消耗指标的执行与考核
能源消耗指标考核是指标管理的又一重要环节,将制定的能源消耗指标与执行消耗指标的实际结果经常进行比较,找出偏差,并分析研究产生偏差的原因,以便及时贯彻执行。
1.考核的目的与意义
(1)通过生产实践的检验,考核制定的能源消耗指标是否合理。
(2)通过能源消耗指标的考核,与历史最好水平,与国内外先进水平对标,找出差距,努力改进。
(3)通过能源消耗考核,积累完整的历史资料,为指导生产和有效地进行能源管理提供科学依据。
2.考核方式
由于能源消耗指标管理采取分级管理制,所以能源消耗指标的考核应与能源消耗指标的制定、贯彻执行相一致,进行分级考核。
即由公司对厂部,厂部对车间,车间对班组考核,或按工艺流程实行“一条龙”考核。
随着能源消耗指标的细化,考核工作也将越来越细。
3.考核内容
能源消耗指标考核的主要内容和深度大体上分以下三级:
(1)考核到单项产品的单项能耗
(2)考核到单项产品的综合能耗
(3)考核到单项工艺的单项能耗和综合能耗
应当指出,国家《“十二五”节能减排综合性工作方案》把“合理控制能源消费总量”提升到很高的高度,把合理控制能源消费总量作为转变经济发展方式的重要着力点。
能源总量控制将对各地的经济增长速度产生重大影响,将比节能指标更加严厉。
这也标志着政府从“十一五”单纯的能耗强度控制转变到强度和总量双控制、绝对指标和相对指标想结合的考核方式。
这不仅要靠企业内部管理、节能措施等节能手段,还要靠淘汰落后,工艺改进等措施控制能源消费量。
二、企业节能量
节约能源的目的在于充分有效地发挥现有能源的作用,使相同的能源消耗,生产出更多符合市场和用户需求的产品,也就是以最少的能源消费取得更大的经济效益。
能源节约量的计算就是反映能源在使用过程中的节约和浪费情况,研究提高能源利用率的有效途径。
(一)节能量概念与计算
1.节能量的概念
节能量是指报告期内实际能源消耗量与某个基准值总量之间的相对差值。
因此,节能量是个相对的量,随着选择作为对比用的基准量不同,其数值亦不相同。
节能量有两类,一类是与自身比较的节能量,如与上年同期相比的节能量,它反映了企业在能量利用水平上的提高与进步,是一种实际节能量;一类是与他人相比较的节能量,如与标准能耗指标相比或与标杆企业指标对比的节能量,反映了企业的实际用能水平,是一种名义节能量。
钢铁企业节能量是指在一定时期内,通过加强生产经营管理,提高生产技术水平、调整生产结构、进行节能技术改造等措施,所节约的能源数量,综合反映企业直接节能和间接节能的总成果,是考核企业节能工作的重要指标。
企业节能量可分为产品节能量、产值节能量、技术节能量、产品结构节能量和单项能源节能量等。
计算时,根据不同的目的和要求,采用不同的比较基准。
2.节能量的计算
(1)综合节能量
吨钢综合能耗节能量=(报告期吨钢综合能耗-基期吨钢综合能耗)×报告期钢产量
(2)单位产品能耗节能量
某种产品单位能耗节能量=(报告期该种产品单位能耗-基期该种产品单位能耗)×报告期该种产品产量
(3)技术措施节能量
指企业在生产同样数量和质量的产品或提供同样的工作量的条件下,采用某项节能技术措施后所减少的能源消费量。
它是评价描述技术项目节能效果的指标。
计算公式:
技术措施节能量=[
-
]×采取技术措施后的产品产量
采取技术措施前的能源消费量是指企业在技术改造措施项目开工之前一种或几种能源综合的实际消费量。
技术措施后的能源消费量是指企业在进行了某项技术改造措施后而实际消费的一种或几种综合能源数量。
(4)提高产品质量的节能量。
指企业生产同样数量的产品,在提高产品质量的情况下,而减少的能源消费量。
计算公式:
提高产品质量的节能量=(报告期生产定额能耗量-基期生产定额能耗量)×报告期比基期减少的废品量
(5)降低损失的节能量。
指企业在报告期,由于实际损失率比计划规定的损失率低,所节约的能源数量。
计算公式:
降低损失的节能量=(实际损失率-计划规定的损失率)×报告期能源消耗量
(6)提高能源利用率的节能量。
是指企业报告期内的能源利用率高于基期的能源利用率,所节约的能源数量。
计算公式:
提高利用率的节能量=(
-
)×报告期能源消耗量
(7)产品结构节能量。
指假定在企业单位综合能源消费量不变的情况下,由于企业产品生产结构变化而少用(或超用)的能源数量。
计算公式:
结构节能=Σ[(报告期某产品产量占全部产量-基期某产品产量占全部产量的比重)×基期该产品单位综合能源消费量]×报告期全部产品产量
(8)单一能源品种节约量。
指根据单位产品产量单项能耗计算的节能量,反映企业某一种能源(如煤、油、电等)的节约量。
如单位产品节煤量计算公式:
单位产品产量节煤量=(报告期某单位产品产量煤炭消耗量-基期某单位产品产量煤炭消耗量)×报告期该产品产量
单位产品产量节电量、节油量计算公式类似。
(二)节能率、年平均节能率计算
节能率指在一定时间范围内单位产出能耗的降低速率。
反应能源节约成都的综合性指标。
计算公式为:
节能率(%)=
=
对钢铁联合企业可采用吨钢综合能耗来计算,公式如下:
节能率(%)=
节能率一般按年计算,如果研究一个时期内的节能程度的一般水平,可计算年平均节能率。
对钢铁联合企业来说其计算公式为:
年平均节能率(%)=
式中:
N—报告期年号-基期年号(间隔年数)
以上公式所得结果负数表示节能,正数表示超耗。
例:
某钢铁联合企业“十五”期间产量、能耗情况如表3.5所示,试计算其节能量、节能率及年平均节能率。
节能量计算:
2002年节能量=(0.809-0.891)×538.03=-44.12万吨标准煤
同样计算2001年、2003年、2004年、2005年的节能量分别是41.54万吨标准煤、16.97万吨标准煤、20.08万吨标准煤、25.08万吨标准煤。
节能率计算:
或
“十五”期间年平均节能率
表3.5某钢铁联合企业“十五”期间产量、能耗情况
年份
指标
2001年
2002年
2003年
2004年
2005年
钢产量(万吨)
477.43
538.03
606.21
803.04
964.58
吨钢综合能耗(tce/t)
0.891
0.809
0.781
0.756
0.730
节能量(万吨)
-41.54
-44.12
-16.97
-20.08
-25.08
节能率(%)
-8.90
-9.20
-3.46
-3.20
-3.44
五年平均节能率(%)
-4.86
三、能源统计分析
能源统计分析,就是依据能源统计资料,在深入实际调查研究的基础上,运用统计分析的基本原则和方法,定量分析与定性分析相结合,对能源系统流程运动的内在联系及其发展变化规律、能源供需平衡状况、能源消费构成、能源流转、能源加工深度、能源储存、能源使用效益、能源综合利用等方面,进行分析、研究、判断和推理,找出规律性,系统、鲜明、生动地反映客观实际,提出切实可行的建议。
钢铁企业能源统计分析是通过钢铁企业特有的统计报表形式,并对其进行分析、研究、判断和推理。
能源统计分析的目的在于掌握能源消费现状,弄清影响能耗升降的各种因素,查找能源浪费的主要环节,提出改进措施以便会同企业内相关部门组织实施。
为企业优化生产方式,节能降耗和降低生产成本提供技术支持,为领导决策提供依据。
(一)能源统计分析的基本原则
1.要坚持实事求是的原则,真实反映客观情况。
能源统计分析必须要建立在客观事实的基础上,按照唯物辩证法的科学原理观察问题,全面正确认识其经济现象的内在联系及其发展变化的规律。
要以科学发展观的理念,与时俱进的眼光,研究企业经济发展的主要矛盾和矛盾的主要方面,透过现象反映本质。
在观察情况反映问题时,必须进行认真核实,有根有据,全面真实反映情况,颂扬成绩、揭露问题,报喜也报忧。
2.要以党和国家的方针政策为依据进行分析。
能源统计分析要以国家确定的能源方针“开发与节约并重,近期把节能工作放在优先地位”为重点,以“节能就是资源”新观点,以节能降耗,提高能源经济效益,加快经济发展方式转变为中心,调查研究能源流程过程中的经济效益状况,挖掘节能潜力,揭露能源系统流程过程中的损失浪费现象,提出合理有效利用能源的途径。
3.坚持理论联系实际的方法。
能源统计分析要对所掌握的感性材料进行深入分析研究,增强分析的鲜明性和科学性,实现数字与情况的有效对接、材料与观点的有机统一,使分析的结论切合实际。
4.主题鲜明、论点明确、判断准确、推理符合逻辑。
能源统计分析主题的选择要对路、适时,具有鲜明性、时效性;论点要明确,避免含糊不清,模棱两可;判断要准确,有充分依据,避免主观、片面,随意定性;推理要符合客观事物的内在联系,避免不符合逻辑的推理。
(二)能源统计分析的主要特点
1.从量的分析入手,对能源技术经济现象进行定量研究。
能源统计涉及能源生产、利用的技术和工艺,能源统计分析是以统计、核算资料为主要依据,进行的定量分析。
2.综合性、相关性和系统性。
对钢铁企业来说,能源统计分析着眼于企业外购能源供应、品质对企业可持续发展影响,着眼于二次能源对企业经济运行的综合平衡状况,以及能源对系统流程的总体特征和系统各环节的相关性、能源系统结构及其运行的合理化,因此,在进行能源统计分析时,必须采用大量相关的经济指标进行对比,分析它们之间的内在联系和相互制约的关系,具有很强的综合性和系统性。
3.多样性和灵活性。
能源统计分析既可分析企业总体经济问题,也可分析企业局部或单体设备经济问题;既可就某一个问题进行专题分析,也可将有关问题联系起来进行综合分析;既可分析过去,也可预测未来。
(三)钢铁企业能耗分析主要内容
钢铁企业能耗分析应充分考虑产品结构、工艺流程、装备水平、技术操作等,综合地研究寻求降低能耗途径,还要通过对能源载能体的综合平衡、分析以及经济约束、环境约束和政策约束,寻求最大限度的能源节约。
钢铁企业能耗分析主要内容大致包括:
1.装备水平、工艺先进性、产品结构、钢比系数、能源消费结构、原料结构。
2.企业产品的能耗,吨钢综合能耗、工序能耗及单项能耗(如煤耗、电耗、汽耗、水耗等)。
3.企业节能量和节能率。
4.企业能源利用率(或企业能量利用率)。
5.企业能源加工转换,投入产出分析。
6.各工序、炉窑、耗能设备对标情况。
7.企业各节能工程项目的投资效果。
8.能耗升高和降低的原因。
9.节能潜力及下阶段的节能目标、措施。
钢铁企业能耗分析定期进行,每季度编制能源平衡表时,必须进行全面的能耗分析。
能源消耗是企业一项综合性指标,它涉及企业管理的各个方面。
能耗分析的结果应及时地反馈到计划、生产、设备、物资供应、计量、技术等部门。
根据反馈信息,生产设备部门要考虑改进生产组织方式,组织能源平衡及设备的经济运行,充分合理利用能源;物质采购部门应按定额供应燃料;计量部门要完善计量;技术部门对热工部门定期检测,发现问题,提出改进意见;随着生产条件和环境的改善,计划、技术、设备机动部门,应根据具体情况,组织修订能源消耗指标,保证定额的先进性。
(四)钢铁企业能源统计分析主要方法
能源统计分析方法包括对比分析法、结构分析法,因素分析法以及平衡分析法等。
由于钢铁生产的特殊性,东北大学蔡九菊教授根据钢铁生产自身特点,引入了e-p分析法。
运用这些基本的分析方法,针对企业能源运行的不同侧面和企业管理的不同需求,提供分析报告。
对比分析法。
将互相联系的指标结合起来进行对比分析,发现问题,解决问题。
如工序能耗完成情况分析,该分析可通过企业报告期能源消耗情况与基期比较、历史最好水平比较或与同行业其他企业、国外企业比较,主要的分析是通过对单耗指标完成情况所进行的分析。
在对比分析时,要认真检查相关指标的内容、口径、计算方法、计量单位是否一致,要具有可比性。
结构分析法。
是把事物的总体分解为各个组成部分,通过计算结构的相对指标来研究总体内部的各因素的构成及其变化趋势。
它是以总体总量作为比较标准,求各部分占总量的比重,以百分数表示。
对消费总量、节能量等进行结构性分析十分重要。
比如,炼铁工序能耗占总能耗的比例,可反应和分析影响能耗的主要方面和次要方面,从而抓住重点。
因素分析法。
因素分析法的基本特点是假定其它因素数量相同,从而测定其中一个因素的影响方向和程度。
如果有三个因素,则假定其中两个因素不变,测定另一个因素的影响。
指数体系是因素分析法的基本根据,若干因素指数的乘积应等于总变动指数,若干因素影响差额的总和应等于实际发生的总差额。
如对影响能源节约量的各种因素进行剖析,首先剖析由于采取新技术、提高产品质量、提高能源利用率,加强管理等措施降低工序能耗的直接节能的影响程度。
再来剖析由于调整产品结构、原材料消耗升降等因素,对能源(间接节能)的影响程度。
e-p分析法实际采用的也是此方法。
企业能源平衡分析。
企业能源平衡表反映了企业各种能源的来踪去迹以及各种能源的消费构成、加工转换的投入和产出、损失等,体现出企业能量的平衡关系。
通过企业能源平衡表分析,就是对企业用能情况全面、系统地分析,以便明确企业能源利用程度。
(五)能耗分析及应用
吨钢综合能耗是钢铁联合企业一个综合性技术经济指标,它的高低综合反映了一个企业装备水平、生产组织、技术应用等方面水平。
吨钢综合能耗表达式:
吨钢综合能耗=企业耗能总量/钢产量,kgce/t=(P1e1+P2e2…+Pnen)/钢产量;
式中:
P1,P2,…Pn分别为统计期内各工序实物产量;
e1,e2…en分别为统计期内对应实物产量的工序的工序能耗。
可进一步转化为:
吨钢综合能耗=p1e1+p2e2…+pnen
式中:
p1,p2,…pn分别为统计期内各工序实物产量与钢产量之比。
铁钢比=统计期内生铁产量/钢产量
钢铁企业吨钢综合能耗e-p分析。
在研究钢铁企业能源消耗时,同时分析钢比系数和工序能耗这两类因素的方法,称作e-p分析法。
吨钢综合能耗分析时,可同时应用到能耗分析方法中的各种方法,因此,能耗分析应用主要通过吨钢综合能耗的分析说明。
钢铁生产流程的特点是,上道工序往往是下道工序的主要原材料,每道工序所消耗的,除主要原料外,还有其他各种各样的原材料,如耐火材料、石灰、铁合金、脱氧剂等等,其中许多是钢铁企业内部生产的产品。
每道工序不仅要注意节能,而且注意降耗。
“节能”是节约本工序所消耗的能源,“降耗”是指降低本工序所消耗的各种原材料。
前者是降低本工序产品的直接能耗,后者是降低本工序产品的间接能耗,直接能耗与间接能耗之和,才是全能耗。
因此,只有既节能又降耗,才能收到良好的节能效果。
为了分析统计期间吨钢能耗的变化、影响因素以及节能潜力,可将吨钢能耗的变化量写为:
式中,
是统计期间吨钢能耗的改变量;
,
分别为统计期末第i工序的能耗;
,
分别为统计期始末第i工序的钢比系数。
上式中右侧第一项是因工序能耗变化(即工序节能)获得的节能量,称直接节能;第二项是因钢比系数变化(即结构节能)获得的节能量,称为间接节能量。
可见,统计期内吨钢能耗的变化时,同时分析钢比系数和工序能耗这两类因素变化对吨钢能耗的影响。
通过基期(同比、环比、历史最好水平、行业先进水平等)与报告期的能源平衡表,利用吨钢综合能耗e-p分析与统计指数分析法可从数量上全面地对吨钢能耗剖析。
工序能耗影响吨钢能耗(直接节能)=Σ(报告期某产品工序能耗-基期某产品工序能耗)×基期该产品钢比系数
钢比系数影响吨钢能耗(间接节能)=Σ(报告期某产品钢比系数-基期某产品钢比系数)×报告期该产品工序能耗
动力及其它影响吨钢能耗(直接节能)
=Σ(
)
报告期与基期吨钢能耗增减量=工序能耗影响吨钢能耗(直接节能)+钢比系数影响吨钢能耗(间接节能)+动力及其他影响吨钢能耗
能耗分析及应用案例:
某钢铁联合企业基期钢产量1337.54万吨、平衡表计算吨钢综合能耗完成733kgce/t;报告期钢产量1402.75万吨、平衡表计算吨钢综合能耗完成718kgce/t,报告期与基期相比,吨钢能耗降低15kgce/t,基期、报告期数据均来源于能源平衡表,分析其影响因素,具体见表3.6。
吨钢综合能耗影响因素计算:
1.工序能耗影响吨钢能耗(直接节能)
工序能耗影响综合能耗=
烧结工序能耗影响吨钢能耗=(60.57-61.61)×1.5997=-1.68kgce/t;
同样计算炼焦、炼铁、炼钢、轧钢影响吨钢能耗分别是-1.64kgce/t、+3.30kgce/t、2.51kgce/t、+0.40kgce/t;
工序能耗累计影响吨钢能耗=(-1.64)+(-1.68)+3.30+(-2.51)+0.40=-2.12kgce/t
2.钢比系数影响吨钢能耗(间接节能)
钢比系数影响综合能耗=
烧结矿钢比影响吨钢能耗=(1.5997-1.6188)×60.61=-1.17kgce/t;
同样计算炼焦、炼铁、轧钢影响吨钢能耗分别是-2.70kgce/t、-6.35kgce/t、0.23kgce/t;
钢比系数累计影响吨钢能耗=(-2.70)+(-1.17)+(-6.35)+0.23=-10.00kgce/t;
高炉煤气放散损失影响吨钢能耗=
;
同样计算焦炉煤气、氧气影响吨钢能耗-0.07kgce/t、+0.01kgce/t。
3.放散损失影响吨钢能耗=0.13+(-0.07)+0.01=0.07kgce/t;
4.同样计算动力转换及其它影响吨钢能耗分别为-0.37kgce/t、-3.03kgce/t;
累计影响吨钢综合能耗=(-2.12)+(-10.00)+0.07+(-0.37)+(-3.03)=15kgce/t
表3.6综合能耗影响因素
指标名称
单位
基期
报告期
增减量(±)
综合能耗影响因素±kgc