年产300万吨中厚板轧钢车间设计.docx
《年产300万吨中厚板轧钢车间设计.docx》由会员分享,可在线阅读,更多相关《年产300万吨中厚板轧钢车间设计.docx(57页珍藏版)》请在冰豆网上搜索。
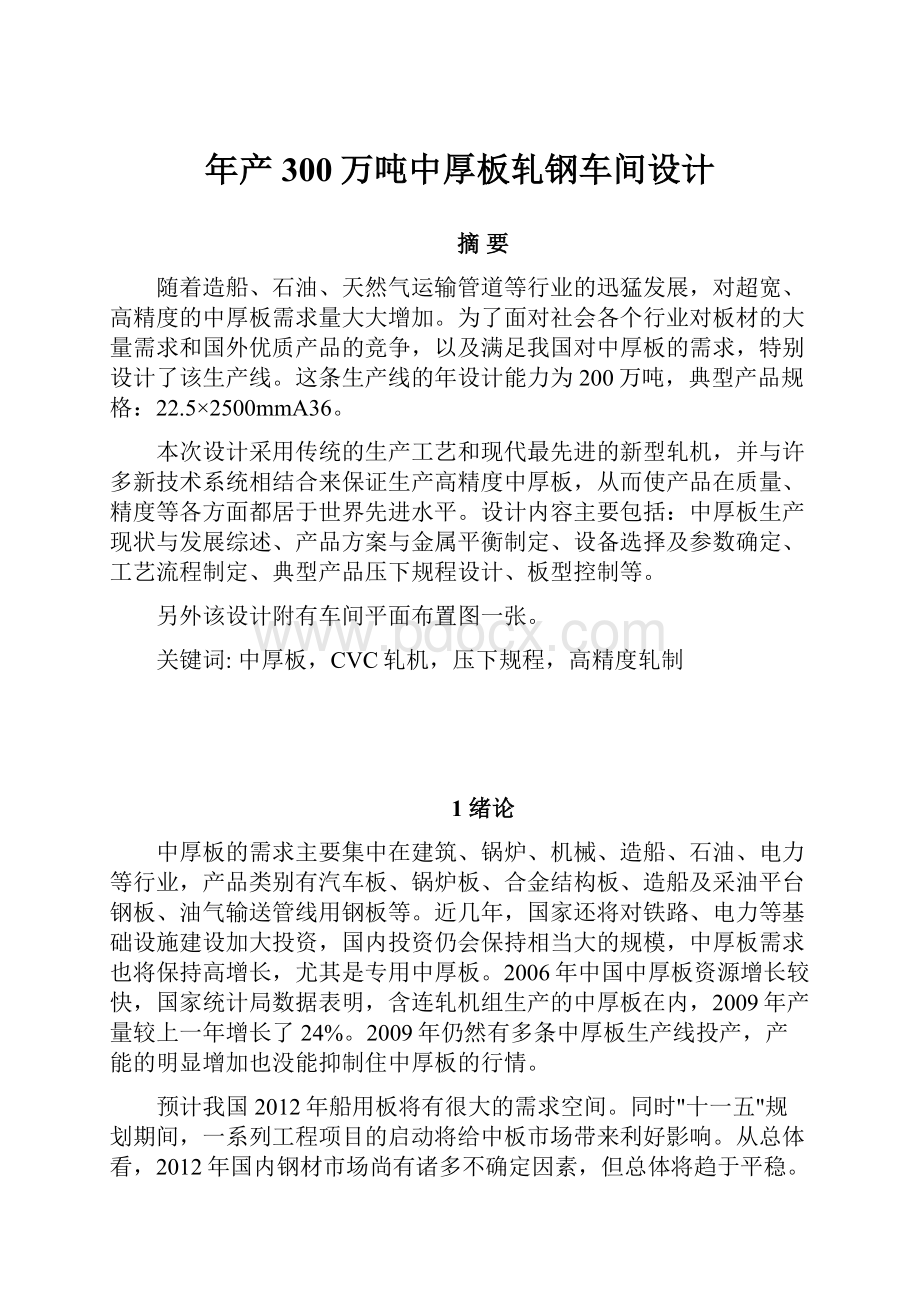
年产300万吨中厚板轧钢车间设计
摘要
随着造船、石油、天然气运输管道等行业的迅猛发展,对超宽、高精度的中厚板需求量大大增加。
为了面对社会各个行业对板材的大量需求和国外优质产品的竞争,以及满足我国对中厚板的需求,特别设计了该生产线。
这条生产线的年设计能力为200万吨,典型产品规格:
22.5×2500mmA36。
本次设计采用传统的生产工艺和现代最先进的新型轧机,并与许多新技术系统相结合来保证生产高精度中厚板,从而使产品在质量、精度等各方面都居于世界先进水平。
设计内容主要包括:
中厚板生产现状与发展综述、产品方案与金属平衡制定、设备选择及参数确定、工艺流程制定、典型产品压下规程设计、板型控制等。
另外该设计附有车间平面布置图一张。
关键词:
中厚板,CVC轧机,压下规程,高精度轧制
1绪论
中厚板的需求主要集中在建筑、锅炉、机械、造船、石油、电力等行业,产品类别有汽车板、锅炉板、合金结构板、造船及采油平台钢板、油气输送管线用钢板等。
近几年,国家还将对铁路、电力等基础设施建设加大投资,国内投资仍会保持相当大的规模,中厚板需求也将保持高增长,尤其是专用中厚板。
2006年中国中厚板资源增长较快,国家统计局数据表明,含连轧机组生产的中厚板在内,2009年产量较上一年增长了24%。
2009年仍然有多条中厚板生产线投产,产能的明显增加也没能抑制住中厚板的行情。
预计我国2012年船用板将有很大的需求空间。
同时"十一五"规划期间,一系列工程项目的启动将给中板市场带来利好影响。
从总体看,2012年国内钢材市场尚有诸多不确定因素,但总体将趋于平稳。
稳定,将是2012年国内钢市的主旋律。
预测12年我国的钢材静观消费将达到5亿吨。
在现代社会的国民生产中,钢铁生产占据着很重要的地位。
钢铁材料的用途十分广泛,不论农业、工业、还是国防;也不论是原材料工业、矿山、煤炭、水电、石油、化工、还是铁路、交通、机械、建材及其他部门,都需要有质量优良,品种齐全,数量足够的钢铁。
在钢铁产品当中,中厚板是重要种类之一,目前全球中厚板年产量约为1.2亿吨,占世界钢材总产量的14.8%左右。
我国的生产能力约为3500万吨,约占当年全国钢材的总产量的14%左右。
1.1国内中厚板生产的发展历史
我国第一套中厚板轧机是在1936年鞍山钢铁公司建成的2300mm三棍劳特式轧机。
近几年来,在全国中厚板轧机改造的同时新建轧机的工作也比较顺利。
宝钢和沙钢的两套5500mm厚板轧机正在加紧施工,舞钢、济钢及邯钢等厂完善厚板精整设备。
经过50年的建设和生产,我国已形成了较强的中厚板生产能力。
但是,与国外先进的中厚钢板生产相比,归纳起来还有以下5条主要的差距:
1)厚板连铸比低。
目前只存百分之十几,大部分以初轧坯和小钢锭为原料,日本的厚板连铸比已达92%以上。
2)轧机性能差。
轧机规格尺寸小,轧机性能低、宽厚板轧机少,还缺少5m左右的特宽厚板轧机。
,
3)钢板质量差,品种不全。
主要是缺少炉外精炼,钢质差。
4)工艺落后,操作与管理水平差,消耗高。
与日本相比,金属消耗大l0%,燃耗多两倍。
5)自动化水平低,辅助设备陈旧。
1.2中厚钢板生产的发展趋势
中厚板轧机是轧钢设备中的主力轧机之一,代表一个国家钢铁工业发展的水平,世界上每个工业先进的国家都拥有若干套。
各国的中厚板轧机和生产技术都各有其特色,钢板质量和各项经济指标也达到了较高的水平。
总的说,目前日本的厚板轧机性能和生产技术在世界上居于领先地位。
归纳起来,中厚钢板生产的发展趋势有以下6个方面。
(1)轧制技术普遍提高
中厚板轧制技术的发展是比较快的,不论是新建的,还是改造的,轧机性能也都普遍提高了。
首先是轧机的刚度系数已提高至800kN/mm以上,辊身单位长度的轧制力由10kN/mm提高至15~20kN/mm,轧制速度由4m/s提高至7.5m/s,主电动机功率也大大加大。
液压AGC、计算机以及测温、测压、测厚、测宽、测长及测板形等自动化检测手段已广泛采用,轧制钢板的最大长度已由30m提高至60m,生产钢板最大宽度已达到5350mm。
钢板尺寸的偏差也缩小了,厚度最小偏差已达±0.055mm,宽度最小偏差达士3mm,长度的最小偏差为8mm以下,镰刀弯也减至5mm/m以下。
切废量已减至很小,总切边量只有50mm以下,切头尾长不到200mm,使成材率达到95%以上。
热装炉时,燃耗已降至0.6GJ/t以下。
(2)厚板连铸比不断提高
目前,世界上大多数中厚板轧机用的原料都以连铸板坯为主,厚板连铸比逐年有明显地提高,日本厚板连铸比已达92%以上,大部分厂均已做到全连铸生产。
(3)轧机越建越大
世界上中厚板轧机越建越大。
新建轧机的尺寸(辊面宽度)都在5m左右,世界上5m以上轧机有5套,其中5500mm级轧机有2套,而淘汰的都是4m以下的,因此,中厚板轧机的尺寸普遍加大。
(4)控轧控冷相结合
控轧控冷可细化晶粒,提高强度和韧性,降低合金元素含量和碳当量,提高可焊性,改善钢板性能,降低生产成本,节约贵重的合金元素。
控轧终轧温度为740~780℃,控冷速度为9℃/s,冷至550℃,抗拉强度可提高20~50MPa,屈服强度可增高20~30MPa,而韧性的变化很小。
碳当量可由0.37%降至0.28%,各种性能均能满足UOE焊管的要求。
(5)板形动态系统控制
为了提高钢板的精度和成材率,板形控制己成为厚板轧机一项不可缺少的新技术。
板形控制的最终目标是生产出切头尾和切边少、矩形或近似矩形的平直钢板。
广泛采用液压AGC、横向板形控制及计算机控制,实现了自动化板形动态系统控制的要求。
(6)精整现代化
厚板精整线一般由热矫直机、步进式或盘辊式冷床。
表面检查修磨装置、超声波探伤仪、双边剪或圆盘剪、定尺剪、打印机、收集装置及冷矫直机等设备所组成,一条现代化精整线一年可处理钢板200万t以上。
1.3本设计目的与内容
本次设计着眼于调整我国中厚板产品,增强产品的市场竞争力,增强企业效益,而设计一座年产200万吨5500mm中厚板车间。
内容主要包括:
产品分析、主要设备选择、压下规程设计、板型控制、辅助设备选择等等
2产品大纲与金属平衡
2.1产品大纲
产品大纲是设计任务书中的主要内容之一,是进行车间设计时制订产品生产工艺过程、确定轧机组成和选择各项设备的主要依据。
2.1.1产品大纲
本设计综合考虑以上各点,制定产品大纲如下:
1产量及钢种:
300万吨/年
2规格:
(1)坯料规格:
200mm~300mm•1500mm~2300mm•3000mm~5200mm
表2.15500mm宽厚板生产线产品大纲
序号
产品品种
代表钢号
年产量(吨)
比例
1
管线板
X52—X80、X100
400000
20%
2
造船钢板
A,B,D,E,AH32~AH40,DH32~DH40,EH系列,FH系列
700000
35%
3
结构钢板
普通结构板
A36,A28,A529,S355JR,SS400,SS490,S235JR,S275JR
36,50,SM490
A572,A573,SN400A、B、C
SHY685,HT--590
500000
25%
桥梁板
建筑结构板
高强结构板
4
锅炉钢板
05G,20G
80000
4%
5
容器钢板
16Mn,16MnNiR
160000
8%
6
其他
耐大气腐蚀板
SMA400A、B、C
SPA-H
160000
8%
工程机械用板
S10C~S58C
耐磨板
相当于HARD0×500
磨具钢板
A681—P20
(2)成品规格
厚度:
5mm~150mm
宽度:
2000mm~4900mm
长度:
最大50m
重量:
最大板重22t(暂时)二期最大单重54t
3产品执行标准:
按GB,DIN,JIS,API等执行。
2.1.2技术要求
1尺寸、外形、重量
(1)钢板的尺寸
钢板厚度5~40mm。
厚度间隔应符合GB709—65热轧中厚钢板品种的规定。
厚度5~40mm的钢板最大长度和宽度应符合GB709—65规定。
宽度为50mm的倍数的任何尺寸,但不得小于600mm。
长度为50mm的倍数的任何尺寸,但不得小于1200mm。
(2)钢板的厚度允许偏差
钢板厚度允许偏差应符合GB709—65的规定。
(3)钢板的长度和宽度允许偏差
长度和宽度允许偏差应符合GB709—65的规定。
(4)钢板的不平度:
钢板的不平度,每米不得大于10mm。
(5)钢板的切斜度
钢板应切成直角,切割偏斜及锯齿形不得使钢板长度及宽度小于公称尺寸。
并需保证定货公称尺寸的最小矩形。
钢板长度不大于6m的,切割偏斜不得超过10mm。
钢板长度大于6m的,切割偏斜不得超过15mm。
2技术要求
(1)牌号和化学成分
成品钢板化学成分的允计偏差应符合GB222—84的《钢的化学分析用试样取样法及成品化学成分允许偏差》的规定。
表2.2钢的牌号和熔炼成分应符合下表规定
钢号
化学成分,%
C
Si
Mn
V
Mo
Nb
P
S
不大于
20g
0.16~0.24
0.15~0.30
0.35~0.65
0.035
22g
0.19~0.26
0.17~0.37
0.70~0.90
12Mng
<=0.16
0.20~0.60
1.10~1.50
16Mng
0.12~0.20
0.20~0.60
1.20~1.60
15MnVg
0.10~0.18
0.20~0.60
1.20~1.60
0.04~0.12
14MnMoVg
0.10~0.18
0.20~0.50
1.20~1.60
0.05~0.15
0.40~0.65
18MnMoNbg
0.17~0.23
0.17~0.37
1.35~1.65
0.45~0.65
0.025~0.050
(2)冶炼方法
钢由平炉、氧气顶吹转炉或电炉冶炼,经供需双方协议也可用其他方法冶炼。
(3)交货状态
钢板以热轧或热处理状态交货。
如需方要求热处理状态交货、应在合同中注明。
14MnMovg、18MnMoNbg钢板不经热处理时,应以样坯热处理状态交货的热处理制度填写在质量证明书里。
对于厚度21mm~40mm的钢板,必须进行断口检验。
判定方法如下:
在钢板断口上金属组织应均匀,不得有气泡、裂缝和夹杂,一个断口上允许有长度和不大于30mm的发纹,单任一条发纹长度不应大于15mm。
(4)表面缺陷
钢板不得有气泡、裂缝、夹杂、折叠和分层。
上述缺陷允许清除,但其清除深度从钢板实际尺寸算起,不得超过厚度的负偏差,并应保证有缺陷处厚度不低于允许的最小尺寸。
其他表面缺陷允许存在,但其深度从钢板实际尺寸算起,不得超过厚度的负偏差,并应保证有缺陷处厚度不低于允许的最小尺寸。
钢板的波浪度和瓢曲度,每米不得大于15mm。
2.2.金属平衡
轧钢生产中主要原料机动力消耗有:
金属、燃料、电力、轧辊、水、油、压缩空气、氧气、蒸气和耐火材料等。
由于生产条件不同,或者由于技术操作水平和生产管理水平不同,不同车间上述消耗指标会有很大的差异;就是同一车间在不同时期,各种指标也可能因某种原因而发生变化。
因此,要经常掌握和研究各类产品的各种消耗指标,才能了解和改进生产。
金属消耗是轧钢生产中最重要的消耗,通常它占产品成本的一半以上,因此,降低金属消耗对节约金属、降低产品成本有重要意义。
金属消耗指标通常以金属消耗系数表示,它的含义是生产一吨合格钢材需要的钢锭或钢坯量。
其计算公式为10:
(2-1)
式中:
K——金属消耗系数;
W——投入坯料重量(吨);
Q——合格产品重量(吨)。
金属消耗一般由下列的金属损耗所组成:
1)烧损;2)切头、切尾、切边造成的损失;3)情理表面损耗(包括酸洗损耗);4)轧废;5)由于加热、精整造成的缺陷以及钢号混乱所造成的损失等。
.
表2.3金属消耗
金属消耗
所占比率
烧损
1%
切损
1%
清理表面损失
0.5%
轧废
0.5%
生产轧制成品的金属平衡如表2.4所示。
表2.4金属平衡表
序号
产品品种
年产量(吨)
烧损
切损
清理表面损失
轧废
原料
1
管线板
400000
4000
4000
2000
2000
4120000
2
造船钢板
750000
7500
7500
3750
3750
772500
3
结构钢板
500000
5000
5000
2500
2500
515000
4
锅炉钢板
80000
8000
8000
4000
4000
104000
5
容器钢板
160000
16000
16000
8000
8000
208000
6
其他
160000
16000
16000
8000
8000
208000
3设备选择及参数确定
轧钢机是完成金属轧制变形的主要设备,代表着车间的技术水平,是区别于其他车间类型的关键。
因此,轧钢车间主要设备选择就是指轧机的选择。
轧机选择的是否合理对车间生产具有非常重要的影响。
轧机选择的主要依据是:
车间生产的钢材的钢种,产品品种和规格,生产规模的大小以及由此而确定的产品生产工艺过程。
对轧钢车间工艺设计而言,轧钢机选择的主要内容是:
确定轧钢机的结构形式,确定其主要技术参数,选用轧机的架数以及布置方式。
在选择轧钢机时一般要考虑下列各项原则:
1)在满足产品方案的前提下,使轧机布置合理,既要满足当前生产又要考虑未来的生产发展。
2).有较高的生产效率和设备利用系数。
3).能获得质量良好产品的同时还要尽可能多地轧制多品种。
4).有利于轧机机械化,自动化的实现,有助于改善劳动条件。
5).轧机结构型式先进合理,操作简单,维修方便。
6).有良好的综合技术经济指标。
3.1宽厚板轧机选择
生产中厚板的轧机型式很多。
按机架结构分类,可分为二辊式、三辊劳特式、四辊式、复合式及万能式几种。
按机架布置分类,可分单机架.并列式和顺列式双机架等几种。
有些中板车间设置带炉卷的可逆热轧钢板,使得能够生产较薄中板产品等。
3.1.1新型轧机
宽厚板轧机主要有:
HC轧机、CVC轧机、PC轧机。
现在介绍如下[5]:
1)HC轧机(HighCrownControlMill)
HC轧机为高性能板形控制轧机的简称,是日立公司研制的一种新型六辊轧机,它是在普通四辊轧机的基础上增加两个可轴向移动的中间辊,其出发点是为了改善或消除四辊轧机中工作辊和支撑辊之间有害的接触部分。
HC轧机利用轧辊轴向串动装置,就能适应带钢宽度变化的要求,使辊身接触长度作相应的改变。
HC轧机的主要特点:
(1)具有大的刚度稳定性。
(2)HC轧机具有很好的控制性。
(3)HC轧机由于上述特点因而可以显著提高带钢的平直度,可以减少板、带钢边部变薄,减少切边损失。
(4)压下量由于不受板形限制而可适当提高。
2)CVC(ContinuouslyVariableCrown)轧机
CVC轧机是SMS公司在HCW轧机的基础上于1982年研制成功的。
近年来广为采用的CVC轧机是德国技术和其他国家专利的结合物,它被世界各国认为是一个能对辊型进行连续调整的理想设备。
CVC辊和弯辊装置配合使用可调辊缝达600微米.CVC精轧机组的配置一般是,前几个机架采用CVC辊主要控制凸度,后几个机架采用CVC辊主要控制平直度。
CVC的基本原理是将工作辊辊身沿轴线方向一半削成凸辊型,另一半削成凹辊型,整个辊身成S型或花瓶式轧辊,并将上下工作辊对称布置,通过轴向对称分别移动上下工作辊,以改变所组成的孔型,从而控制带钢的横断面形状而达到所要求的板形。
CVC轧机有很多优点:
板凸度控制能力强,轧机结构简单,易改造,能实现自由轧制,操作方便,投资较少。
CVC轧机的缺点是:
轧辊形状复杂,特殊,磨削要求精度高,而且困难,必须配备专门的磨床;无边部减薄功能,带钢易出现蛇形现象.。
此外随着轧辊窜动,热辊型及磨损辊型亦将窜动。
3)PC(PairedCrossedMill)轧机
PC轧机为轧辊成对交叉轧机,其工作原理是相互平行的上工作辊,上支承轴中心线与相互平行的下工作辊,下支承辊轴中心线的交叉成一定角度,这一角度等同于工作辊凸度.通过改变这一交叉角度就能改变轧辊辊缝形状,从而达到控制带钢凸度和平直度的目的.
PC轧机能很好解决轧辊磨损和能耗的问题,PC轧机比单辊交叉所承受的轴向力要小,在PC轧机结构上设计有能够承受轴向力的止推装置来克服轴向力,此止推装置安装在工作辊操作侧轴端。
PC轧机的轧辊轴线交叉角一般为0.5—1.5度,等效工作辊凸度Cr由下式表示:
Cr=ζb2tan2θ/2DW=ζb2θ/2DW
其中:
Cr——等效工作辊凸度,mm
ζ——影响系数
b——轧制板带的宽度,mm
θ——交叉角
DW——工作辊直径,mm
由上式可知,交叉轧辊等效的轧辊凸度Cr与带钢宽度b成正比,轧件越宽,控制效果越好。
当轧件宽度b一定时,板凸度的控制范围与轧辊交叉角度成正比。
因此,通过根据轧制条件设定适合的交叉角,可以得到任意的目标带钢凸度。
PC轧机的优点:
(1)良好的板型与凸度控制能力;
(2)单一的轧辊原始辊型。
(3)压下率大;
(4)轧制计划的自由性。
PC轧机的缺点:
轧机结构复杂,轴向力大(达到轧制力的8%~10%)将使轴承寿命缩短,使维护工作量加大,并增加了轧制力的测量的滞后性,操作与控制复杂,投资成本增加。
3.1.2轧机选择
本次设计经过综合对比和实际考察并结合设计目的和产品大纲要求,主要从控制板型(板凸度,平直度等),建厂投资等方面考虑,而最终选用双机架轧机,粗轧机为四辊可逆轧机,精轧机为CVC轧机。
其具体的数据如下:
粗轧:
类型:
四辊可逆轧机
最大轧制力:
105000KN
扭转力矩:
2×10000MN•m
工作辊:
Φ1240~1140mm,辊身长度5500mm.
支撑辊:
Φ24000~2200mm,辊身长度:
5400mm
轧机速度(在最大轧辊直径下):
0~±3.35/7.3m/s
轧机模数:
9000KN/mm
主电机功率:
2•10000kW
主电机额定转矩:
2×1910KNm
最大辊径开口度:
1100mm
轧制线标高:
+840mm
板型控制方式:
工作辊弯辊
辊缝控制:
HGC+EGC
精轧:
类型:
四辊可逆轧机
最大轧制力:
100000KN
扭转力矩:
2×10000MN•m
工作辊:
Φ1120~1020mm,辊身长度5300mm.
支撑辊:
Φ23000~2100mm,辊身长度:
4950mm
轧机速度(在最大轧辊直径下):
0~±3.35/7.3m/s
轧机模数:
8400KN/mm
主电机功率:
2•10000kW
主电机额定转矩:
2×1910KNm
最大辊径开口度:
550mm
轧制线标高:
+830mm
板型控制方式:
工作辊弯辊+CVC
辊缝控制:
HGC+EGC
3.2辅助设备选择
辅助设备选择一般要遵循下列原则:
1)满足产品生产工艺要求;
2)有较高的工作效率,保证轧机获得较短的轧制节奏时间而有较高的产量;
3)设备结构的型式要先进合理,动作灵活机构紧凑,操作维修容易,备品备件标准化,制造、更换方便;
4)辅助设备的生产能力一般要大于轧机生产能力,以保证轧机生产能力得到发挥。
通常辅助设备能力可按大于轧机能力20%考虑;
5)设备设计经济合理,体积小,重量轻,以减少设备总重量和节省车间投资。
辅助设备选择的主要内容是根据生产的要求确定他们的型式、能力和数量。
本设计仅对加热设备、切断设备、矫直设备、冷却设备、起重运输设备和热处理设备的选则简述如下。
3.2.1加热设备选择
加热是热轧生产个的一个重要工序。
而钢料的加热质量的保证和加热炉产量的大小,完全依赖于所选则的加热设备和它的热工制度。
出此,对加热设备的选择也应给于足够的重视。
3.2.2炉型确定
在轧钢生产中,用作加热工序的加热设备基本上可以分为两类:
均热炉和各种形式的连续式加热炉。
连续式加热炉的主要类型有推钢式连续加热炉、环形炉、链式炉、辊底式炉以及步进式炉等。
其中推钢式连续加热炉是轧钢车间最常见的加热设备。
但是,由于步进式加热炉加热钢料温度均匀,加热质最良好等原因已日益得到发展和广泛应用。
确定连续式加热炉炉型要考虑的因素很多,主要的有:
加热的钢种、坯料断面尺寸大小及形状、坯料温度以及炉子的产量要求、加热要求达到的质量等。
但其中根据生产需要的加热质量和产量要求以及与此相关的温度制度是确定加热炉炉型的主要依据。
综上,本设计选用步进式加热炉。
因为步进式加热炉有以下特点:
1)钢料入炉不是依靠推钢机送进,而是利用步进机构将料送入炉内,取消了实炉底,不用打渣,钢料表面也不会划伤。
2)步进送料,因不发生拱钢现象,加热炉长度不受推钢比的限制。
3)钢料在炉内间隔排放,可以实现多面加热,使坯料加热温度均匀,无推钢式炉那样的黑印。
为保证轧件尺寸和组织性能均匀提供了条件。
4)可以利用步进机构使钢科之间距离得以调整,适应加热炉产量的变化。
并使加热时间不变,以减少钢料的氧化和脱碳。
5)可以将炉内钢料全部出空,有利于处理求故,也便于加热不同钢种。
6)因靠步进机构将钢料送入炉内,因此加热坯料形状一般可不受限制。
3.2.3产量计算
按下式计算:
(3-1)
式中:
Q——加热炉小时产量(吨/时);计算得250吨/小时
L——加热炉有效长度(米);本设计取55m;
n——加热炉内装料的排数;本设计为n=1;
G——每根钢料的重量(吨);本设计取为3.16吨;
b——加热钢料断面宽度(米);本设计取为1.6m;
T——加热时间(小时)。
T=CB;这里取40min。
3.2.4炉子尺寸确定
1.炉子宽度主要根据坯料长度确定。
但要考虑装出料的方便和保证坯料端部加热质量。
单排料时B=l+2c(3-2)
双排料时B=2l+3c(3-3)
式中:
l——来料最大长度;
C——料间或料与炉墙间的间隙距离。
一般为0.15~0.3米。
2.炉子长度主要根据要求的加热炉产量决定。
本设计加热炉的选择:
炉型:
步进式加热炉
数量:
2
炉子尺寸:
B•L=11.6m•55m
每座炉子产量:
450吨/小时
3.3斜刃剪的选择
3.3.1斜刃剪的形式
斜刃剪作用是主要用于横向、纵向剪切板材。
主要形式有[5]:
1)上切式斜刃剪:
主要特点是下刀片固定不动,上刀片向下运动剪切轧件。
其结构简单,制造方便,故应用较为广泛。
2)下切式斜刃剪:
这种剪切机通常是上刀片固定不动,由下刀片向上运动剪切轧件。
在下切式斜刃剪中液压驱动得到了广泛应用。
3)滚切式(斜刀片)剪切机:
与普通斜刃剪相比,滚切式(斜刀片)剪切机上刀片是弧形的,弧形上刀刃在平直的下刀刃上滚动剪切。
此时,在整个剪切范围内刀片重叠量不变,被剪切板材几乎不弯曲。
而在普通斜刀片剪切机上剪切厚度较大的板材时,由于刀片行程大,易使板材产生横向弯曲,在剪切侧边时半边也不齐,影响板材的剪切质量和产量。
另外,这种剪切机的开口度比斜刀片剪切机大一些,但其总行程却小30%~40%