250T氧气顶吹转炉主体设备设计及支撑机构设计详解.docx
《250T氧气顶吹转炉主体设备设计及支撑机构设计详解.docx》由会员分享,可在线阅读,更多相关《250T氧气顶吹转炉主体设备设计及支撑机构设计详解.docx(52页珍藏版)》请在冰豆网上搜索。
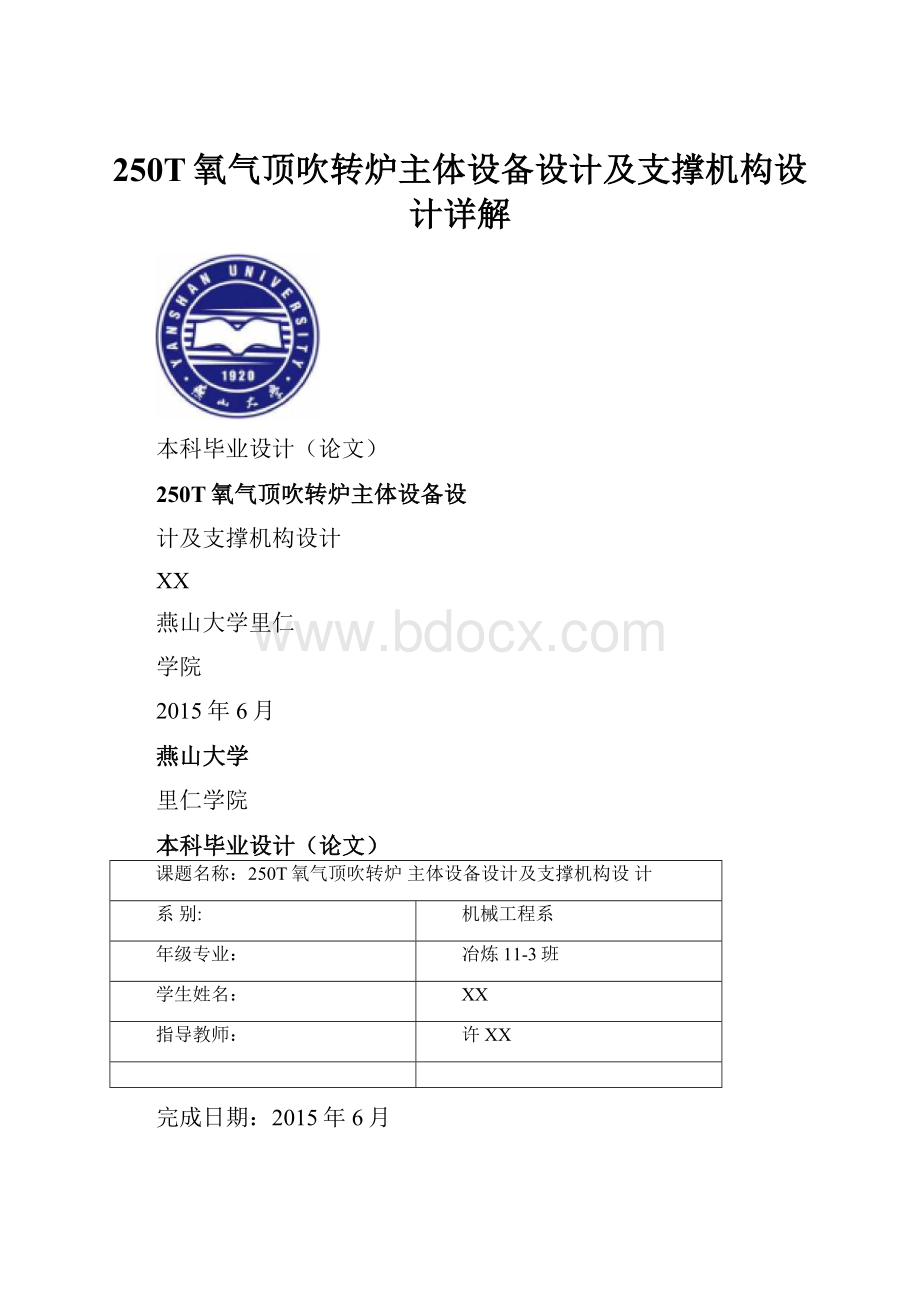
250T氧气顶吹转炉主体设备设计及支撑机构设计详解
本科毕业设计(论文)
250T氧气顶吹转炉主体设备设
计及支撑机构设计
XX
燕山大学里仁
学院
2015年6月
燕山大学
里仁学院
本科毕业设计(论文)
课题名称:
250T氧气顶吹转炉主体设备设计及支撑机构设计
系别:
机械工程系
年级专业:
冶炼11-3班
学生姓名:
XX
指导教师:
许XX
完成日期:
2015年6月
燕山大学里仁学院毕业设计(论文)任务书
学院:
里仁学院系级教学单位:
机械工程系
学号
xxxxx
学生姓名
XX
专业班级
冶炼11-3
课题
题目
250T氧气顶吹转炉主体设备设计及支撑机构设计
来源
模拟
主要内容
1)转炉炉型设计;
2)炉液倾动力矩计算;
3)总装图;
4)炉体与支撑机构设计。
基本要求
1)用计算机完成炉型设计及倾动力矩和转动惯量计算;
2)总装图和零件图必须满足国标要求;
3)总图纸量不少于6个A1,至少2张A1手工图;
4)设计说明书不少于2万字,摘要不少于300字,且汉英对照
5)翻译相关外文资料不少于5000汉字,参考文献不少于15篇;
参考资料
1)转炉连铸工艺设计与程序,贾凌云,冶金工业出版社;
2)宝钢参考资料;
3)谭牧田著《氧气顶吹转炉》。
周次
1周
2—3周
4—7周
8—13周
14—17周
应
宀完成的内容
收集资料炉型设计
倾动力矩及转动惯量计算炉型校核
总体方案制定
完成总装图
炉体与托圈联接结构设计
托圈结构设计
完善设计
撰写设计说明书
准备答辩
指导教师:
系级教单位审批:
摘要
氧气顶吹转炉主体设备是实现炼钢工艺操作的主体设备,它由炉体、炉体支撑系统、炉体倾动机构以及炉体与托圈联接装置等组成。
本次设计针对250T氧气顶吹转炉主体设备和支撑机构进行。
炉体采用A型炉(即锥球型),活炉帽死炉底结构;托圈采用整体式托圈结构,其断面形状选择矩形断面;炉体倾动力矩的计算利用Solidworks
软件绘制实体从而得到炉体、炉液的重心和重量,结合计算公式进行计算;为保证转炉在倾动过程中的安全性,最佳耳轴位置的确定利用全正力矩原则进行;炉体支撑系统选用耳轴与耳轴轴承座的支承方式;倾动机构选用带有
扭力杆式缓冲装置的四点才啮合全悬挂式倾动机构;炉体与托圈联接装置采
用活节螺栓与止动托座配合的连接结构。
同时对250T氧气顶吹转炉的主体设备和支撑装置中的各个部分进行工作原理的分析和结构设计。
并且针对其工作状况和受力情况等进行理论分析和校核。
关键字氧气顶吹转炉主体设备;倾动机构;支撑装置
Abstract
Themainequipmentinoxygentop-blownconverterIstherealizationofthemainequipmentinbofsteelmakingprocessthebodyoftheequipmentoperation,anditissupportedbyfurnace,furnacesystem,furnacetiltingmechanism,aswellaslinkageandcoil,furnacelining,etc.Thedesignforthemainequipmentin250toxygentop-blownconverterandtiltingmechanism.
FurnaceadopttypeAfurnace(namelyconeballtype),livehatdiehearthfurnacestructure;Supportingringwiththeringstructure,thecrosssectionshapeselectrectanglecrosssection;FurnacetiltingtorquecalculationusingSolidworkssoftwarerenderingentitiestogetthecenterofgravityandweightofthefurnace,furnace,combinedwiththeformulatocalculate;Inordertoensurethesafetyintheprocessofconverterintilting,besttrunnionpositionusingtheprincipleofpositivemoment;Furnacebodysupportsystemselectsthetrunnionandtrunnionbearingsupportingway;Tiltingmechanismwithtorsionbarusedbufferdeviceonlyfourmeshingfullsuspensiontypetiltingmechanism;Furnacebodyandsupportingringconnectiondeviceadoptseyeletboltandretainingbracketwiththeconnectionofthestructure.
Atthesametimefor250toxygentop-blownconverteroftheindividualpartsofthebodyoftheequipmentandtheconnectingdevicefortheanalysisoftheworkingprincipleandstructuredesign.Andforitsworkingconditionandstressdistributionofthetheoryanalysisandchecking.
KeywordThemainequipmentinoxygentop-blownconverter;Tiltingmechanism;supportdevice
摘要错误!
未定义书签。
Abstract错误!
未定义书签。
第1章绪论8
1.1氧气顶吹转炉主体概述8
1.2250T氧气顶吹转炉主体设备设计总体说明9
第2章转炉炉型的设计10
2.1设计参数10
2.2根据原始数据对转炉炉型进行选择及计算11
2.3对转炉主体进行计算12
2.4250T转炉炉型设计过程12
第3章水冷炉口的设计17
3.1水冷炉口的结构说明17
3.2水冷炉口的设计与计算17
第4章托圈的设计.19
4.1托圈部件整体说明19
4.2托圈断面形状的选择20
4.3托圈基本尺寸参数的确定21
4.4托圈制造的技术要求和材料22
第5章倾动力矩的计算23
5.1倾动力矩简述23
5.2空炉重量及重心位置计算24
5.2.1计算思想24
522新炉空炉重量及重心位置24
523老炉空炉重量及重心位置25
5.2.4新老炉钢液的重心位置的确定26
5.3倾动力矩的计算27
5.3.1.转炉倾动力矩的计算步骤:
27
5.3.2•转炉倾动力矩的计算数据28
第6章倾动机构的设计35
6.1倾动方案的确定35
6.2电动机的选择36
6.3一级减速器的选择38
6.4二次减速器的设计38
第7章耳轴的设计45
7.1耳轴概述45
7.2耳轴的设计46
第8章炉体与托圈连接结构的设计47
8.1活节螺栓连接的设计47
8.2连接装置的设计原理48
结束语50
参考文献51
致谢53
第1章绪论
钢铁行业是衡量整个行业发展的标准,对任何一个国家来说,钢铁产量
对其经济的发展有着重大意义。
随着第二次行业革命的发展和现代科学技术的提高,对高质量钢的需求不断增加,炼钢工艺和技术不断的进步,因此对于炼钢设备来说也得到了很大的提升空间。
过去钢铁行业在一个很长的时间内,以普通的平炉炼钢为首。
从1952年氧气顶吹转炉出现以后,使炼钢行业发生了蜕变,使得全球的钢产量得到了迅速的提高。
氧气顶吹转炉炼钢又称L-D炼钢法,上个世纪50年代在奥地利的其所属的林次(Linz)和道纳维次CDonawitz)两钢厂中由Voest-Alpine联合公司试验成功并在投入行业生产,氧气顶吹转炉的别称为L-D炼钢炉,其中的L
和D分别是林茨和道纳维茨的开头字母。
氧气顶吹转炉炼钢出现后,在全球得到了快速的发展,各国炉钢的产量也得到了迅速的提升,上世纪60年
代末的产钢量为20300万吨。
其中,L-D转炉炼钢占全球总量的37.5%。
L-D转炉炼钢能够有这样的结果,其原因主要在与传统炼钢方法相比,它具有一系列的优势。
包括有:
(1)产量高
(2)质量高,性能好(3)原材料消耗少,热效率高,钢的成本低(4)对原材料的适应性强(5)基础设施投资少,建设效率高(6)对于实现自动化有着重要作用,并能和其他炼钢工艺能很好的结合。
进入七十年代后,L-D转炉炼钢法已逐渐取代当时世界上其他的传统炼钢方法,而
且L-D转炉炼钢法的技术逐渐成熟。
1.1氧气顶吹转炉主体概述
LD炼钢炉是实现炼钢工艺操作的主体设备,它由转炉主体、转炉主体支撑装置和转炉主体倾动机构等组成。
转炉主体的作用是盛装铁水并进行有氧吹炼,它通过托圈和耳轴支撑在其支座上,利用倾动装置可以0.1〜1.5转/分的速度随耳轴、托圈在正负360°内转动,以满足装炼钢,出渣,维修等的需要。
倾动系统是由电动机、减速机、扭力杆系统和制动保护器等组成。
1.2250T氧气顶吹转炉主体设备设计总体说明
本次设计内容包括转炉主体以及托圈连接机构。
在本设计中,转炉炉型采用A型,采用死炉底活炉帽的结构形式。
这种结构不但简单,并且相比传动的炼钢炉来说质量轻。
最重要的是制造简单,具有较高可靠性,并符合经济指标。
水冷炉口采用铸铁埋管式水冷炉口,这个结构是不易被烧透而导致钢水的泄漏,从而能达到延长炉体寿命的效果,缺点是不容易在泄漏后进行焊接修补,并使多。
为了保证水冷炉口和炉体之间连接强度,应采的形式是用n形卡板焊接而成。
本设计采用隔热板和挡渣板来保护炉体,使其受到较少的热辐射和腐蚀。
由于炉渣安息角45-50度,所以取各板倾斜角度50度,以利于炉渣下滑。
转炉主体支承系统分为两部分,主动侧支承系统直接固定在地面上,从动侧支承装置设计为铰链式轴承支座结构,以适应托圈和耳轴的热膨胀。
转炉主体采用二支点方式支承在托圈上,其支承装置采用球面带销螺栓将转炉主体和托圈连接在一起。
整个连接装置由两部分组成:
一部分
是托圈上三个球面带销活节螺栓与炉壳上部连接支承法兰组成的倾动承载部分,承受转炉主体在垂直位置和倾动过程中的转炉主体载荷;另一部
分是安装在两耳轴部位的托圈上下的两组止动托座,在转炉主体倾动到水平位置时将载荷传递给托圈。
连接设备可以满足性能要求的连接设备,且结构简单,制造、安装容易,维护方便,是一种简单可靠并且值得推广的设备。
第2章转炉炉型的设计
2.1设计参数
工艺参数
平均出钢量:
250吨
供氧强度:
3・5标米3/吨.分
供氧压力:
10公斤力/厘米
吹氧时间:
17分钟
2.2根据原始数据对转炉炉型进行选择及计算
a—筒球型;b—锥球型;c—截锥型
图2—1转炉常用炉型示意图
(a)筒球型炉型:
该炉型由圆筒型的炉身、球缺型的炉底和截锥型的炉
帽组成。
其特点是结构简单、砌砖较容易,反应比较充分,适合中型转炉。
(b)锥球型炉型:
该炉型由倒置截锥体、球缺体组成的炉底和圆筒型的炉身以及截锥型的炉帽组成。
其特点是容量大,反应面积大、反应充分,适用于吹炼高磷铁水,但炉底砌砖比较复杂,适合大型转炉。
(c)截锥型炉型:
该炉型由倒置的截锥体炉底、圆筒型的炉身和截锥型的炉帽组成。
其特点是形状简单,炉底砌砖方便,但反应不太充分,适合小型转炉。
2.3对转炉转炉主体进行计算(炉衬、炉壳厚度、炉帽、炉
身、炉底尺寸);
设定炉型参数
*(V/T,h/d,d1/d,d3/d,r/d,a1,T1,T2,T3)
2.4250T转炉炉型设计过程
本次设计中,转炉炉型采用A型,炉帽为截锥形,炉身为圆筒形,炉底为球缺形。
(1)熔池直径计算
供氧强度为:
3.5标米3/吨.分
G=1.1Go=1.125°=275G为金属装容量
Dr=(0.66_0.05)G0'4Dr为熔池表面直径
Dr=(0.66_0.05)2750'4=5.77-6.71m取Dr为5.8m
氧枪出口直径计算
Q0v0q0G/60=1.4293.52501.1/60=22.9公斤/秒;
单孔枪头出口直径
dchD
13.8
Pg
■0-285亠
Q。
-0.285
二15.38cm
Pg为氧气工作压力,一般取10公斤力/厘米2
而大型转炉采用三孔枪头:
氧枪枪头出口面积:
二22
Fchs~3—dchs185.83cm
4
氧枪出口氧流速度:
氧枪理论工作高度
氧气与钢液相遇直径:
d^DR-0.64m
9
h0=dHdchD=1.54m
2xtana
(4)理论熔池直径:
Hr=5.3dchDW°c=1931mm
(5)理论氧气穿透深度
取K=1.893,则de=111mm
其中dc氧枪枪头喉口直径d
采用三孔枪头其中hehu=(0・25-°.4)hR=。
48~°.774m
取hehu=500mrn,符合最大范围。
代入方程两侧满足平衡条件。
(6)炉底、炉帽、炉口、出钢口等尺寸的确定
250T氧气顶吹转炉的炉型选取A型,取球缺半径
R=(0.8-0.9)Dr=4.64~5.22m
取R=5.2m
设球缺高h=884mm
其球缺部分体
2h3
泊h2(R)=12.04m3
3
铁水体积
3
则V=236.5m
炉身尺寸确定
取转炉工作容积与炉容量之比V/T=0.86
3
炉身体积sb/「%v翳舱詔55.°亦炉身高4R,取hsh=5.9m
则实际体积V=VmaVq《=223.77亦
炉衬尺寸的确定
根据具体的设计要求和工艺要求的需要,选取炉衬厚度如下表所示:
工作层
填充层
永久层
钢板
炉身部分
(mm)
900
60
148
85
炉底部分(mm)
700
60
450
85
材料
焦油白云石
焦油镁砂
镁砂
15MnVg
密度(吨/立方米)
2.85
2.6
2.8
7.85
炉壳外径的确定:
Dk=Dr2“22
式中r为炉衬厚度,:
2为炉壳钢板厚度
下面确定炉壳钢板的厚度:
转炉炉壳部分材料选择的一般准则是:
要有良好的韧性和弹性,有良好的工艺性能,较高的抗疲劳强度;另外根据经济指标来选择材料以符合成本的经济性。
目前炼钢转炉发展和设计的趋势是使炉壳各部分的厚度相同,这能使制造工艺的简化以及降低边界效应有很大的意义。
根据转炉设计的安全性原则和经验,取钢板厚度为85mm材料为抗高温抗腐蚀的碳素钢和抗疲劳强度咼的低合金钢。
因此,Dk=8.07亦
水冷炉口高取350毫米,则炉壳高H厂11.259m,Hz/Dk=1372符合要求。
第3章水冷炉口的设计
3.1水冷炉口的结构说明
水冷炉口基本有两种结构形式,即水箱式和铸铁埋管式。
水箱式水冷炉口为钢板焊接,它冷却强度大,工作效果好,易于制造,并且漏水时,可以补焊,维修方便。
铸铁埋管式水冷炉口,往返曲折的钢管埋铸在铸铁炉口中,另外还有蛇形,螺旋曲型的钢管埋铸在铸铁中的结构。
铸铁埋管式水冷炉口比水箱式水冷炉口不易烧穿漏水,使用寿命长,但
是漏水不易焊接,且制造繁琐。
水冷炉口地寿命,根据国内实践,钢板焊接的水箱式水冷炉口大致需要半年左右更换一次,而铸铁埋管式是半年到一年的时间更换一次。
水冷炉口与炉壳的连接形式,在我国多采用“n”型卡板焊接的形式。
为了拆卸方便,曾采用过螺栓连接,但由于炉口与炉壳变形不一样,拆卸后再装配时,螺栓孔不易对正。
有的在使用过程中讲螺钉拉断,也有的由于炉口喷溅讲螺钉粘接,更换时仍需用火焰切割。
实践表明,螺钉连接不如“n”型卡板适用可靠。
本次设计采用埋管式水冷炉口,材料选用球墨铸铁QT40-10L水冷炉口与炉壳的连接采用“n”型卡板16块厚度为30毫米的钢板进行连接。
3.2水冷炉口的设计与计算
炉口承受炉气高温作用,其吸热强度q可按下列数据考虑:
大型转炉1105T.2105千卡「米2•时
中型转炉8104-9104千卡「米2•时
小型转炉6104-7104千卡「米2•时
受热面积可以按炉口内侧面积和顶面面积之和计算。
(1)炉口冷却水用量的计算
式中z---水冷炉口材料的辐射黑度
此次设计中,水冷炉口材料选用球墨铸铁,取0.90。
q---水冷炉口的吸热强度。
此次设计中,250吨LD炼钢转炉为大型转炉,故q取1.1105千卡/米2♦时。
F---水冷炉口的传热面积。
此次设计中,水冷炉口高150mmR1=「5口R2=2.592m
2
炉口内侧面积F1=2-:
时=23.141.70.1=1.6022米
顶面面积:
F2(R;-R2)3.1416(2.59252-1.72)=12.0356米2
所以,受热面积F二F2=13.6378米2
根据安全原则考虑,水冷炉口受热不仅是由内侧和顶面带来的热量,在外侧和下定面均有热传导和热辐射,因此应在计算时乘以一个安全系数Ko
在此次设计中K取值为1.4.
Stch----冷却水进温度,此次设计中,tj=30C,
由以上分析,炉口冷却水用量'
5
Q=0.91.11013.6378=6.75105公斤/时
tch_tj50-30
14KQ
36*105…、
Q――水冷炉口需要的水量。
进水管直径的计算铸铁埋管式水冷炉口,进、出水管直径取值为一致。
式中,
由以上的计算,Q=6.75x10000公斤/时
K――安全系数。
由以上的计算,K=1.3
'――冷却水流速
y
——冷却水比重
水的比重:
二1吨/米3
取水压:
4公斤力/厘米2时
v=3米/秒
由以上分析,进、出水管直径
14KQ
1”1.3*6.75*104‘pi米.pi毫米
36*105
・5
136*103.1416*3*1
查取有关手册取低压流体输送焊接管(GB3091-82取4in管,内径
100mm可以满足要求。
第4章托圈的设计
4.1托圈部件整体说明
托圈是转炉的重要承载和传动部件,工作过程中,除承受炉体、钢液及炉体附件的静载荷和传递倾动力矩外,还承受频繁启、制动产生的动负荷,以及来自炉体、钢水罐、渣罐、烟罩及喷溅物等的热辐射、热传导所产生的热负荷。
因此,托圈应具有足够的强度和刚度。
本次设计采用整体托圈结构。
托圈是一个整体的钢板焊接的箱形结构,有四个部分,即由驱动侧耳轴座、从动侧耳轴座、出钢侧托圈瓣、装料侧托圈瓣焊接成一个整体托圈的。
托圈耳轴座和耳轴铸成一体,为了减少托圈内外腹板与耳轴座联接处,因为刚度的急剧变化而引起的应力集中,所以将耳轴轴承座与内外腹板连接部位做成叉型过渡形式,并且和腹板与腹板焊接处的尺寸相同,向着缓慢的增厚到耳轴附近处。
同样,由于连接板刚度急剧变化,并且为了减少应力集中引起的连接板刚度,因此距离焊缝的地方加上隔离板。
隔离板焊在耳轴两侧各一块儿,其焊接位置在托圈中间。
为了增加腹板的刚度和强度,在两耳轴同一侧的两块
隔板之间应该焊有八块筋板。
为了增强托圈的刚度以及炉壳与托圈的冷却效果,应当在每两块加强筋中间焊接上穿通内外腹板的圆管。
为了减少钢水和炉渣带来的的辐射热对托圈的作用,在出钢口附近的托圈外腹板上应有楔形块儿块和螺钉来联接挡板。
另外,由于托圈各部位受热不均,因此会导致高于机械载荷应力的热应力出现。
该托圈采用了水冷措施,从水冷炉口,炉顶钢板,渣裙排出的冷却水,进排水集水箱由驱动侧耳轴座上部进入托圈,再由靠近从动侧耳轴座的
外腹板上部的排水管引出。
托圈通水冷却可使托圈各部位温度趋于均匀,降
低温度梯度。
托圈和炉体连接方式,在托圈上利用吊耳,吊耳成120。
均匀
分配来实现炉体和托圈之间的连接。
两耳轴侧的人孔用十焊接横隔板的对接焊缝和腹板上下盖板与耳轴座连接处的内焊缝。
4.2托圈断面形状的选择
托圈的断面结构大致有两种结构,其中包括开口和闭口侧面两种形式。
闭口断面多为矩形,开口断面有C形和反C形两种。
反C形开口断面是指开口向着炉体的断面。
托圈断面的几种结构形式,如下图所示
1
1厂1
■r
1
_i__
-Cij-
jj!
l
厂—
b
c
raw托圈断面形状
现在,托圈断面通常会采用矩形断面结构,其中a所示。
在这种托圈断面中,切应力以均匀环流的方式分布在托圈上。
同时开口断面的抗扭刚度比矩形断面结构的要小很多。
尤其是大型转炉托圈的矩形封闭断面结构的热应力可以通入冷却水来降低。
综上所述,在本次设计250TLD转炉采用矩形断面托圈,为了降低托圈热应力还采取了如下措施:
(1)采用隔热保护板,挡渣板。
(2)采用防护板。
(3)在托圈上下盖板之间和内腹板表面安装水冷装置。
4.3托圈基本尺寸参数的确定
托圈的基本尺寸参数包括:
托圈外径、内径,断面尺寸。
托圈的基本尺寸参数的确定:
托圈内经:
Dn=Dl+2A
托圈外径:
Dw=Dn+2B=Dl+2A+2B
其中Dl---炉壳外径
A---炉壳与托圈之间的间隔
b---托圈断面宽度
其中间隙a=0.03Dl,目前国内间隔值小于此值。
本次设计中DL=8.186m,故A=245mm
Dn=Dl2二8677mm
托圈断面尺寸:
端面高度H、端面宽度B、盖板和腹板厚度2。
由于托圈工作时,受弯扭复合作用,转炉多数时间处于正吹位置。
因此,断面采用立着的矩形断面。
断面高度比H/B=2.5~3.5大型转炉为了配置紧凑,选用较大比值,本设计采用H/B=3。
断面高度