品管管理基础知识培训资料范文.docx
《品管管理基础知识培训资料范文.docx》由会员分享,可在线阅读,更多相关《品管管理基础知识培训资料范文.docx(32页珍藏版)》请在冰豆网上搜索。
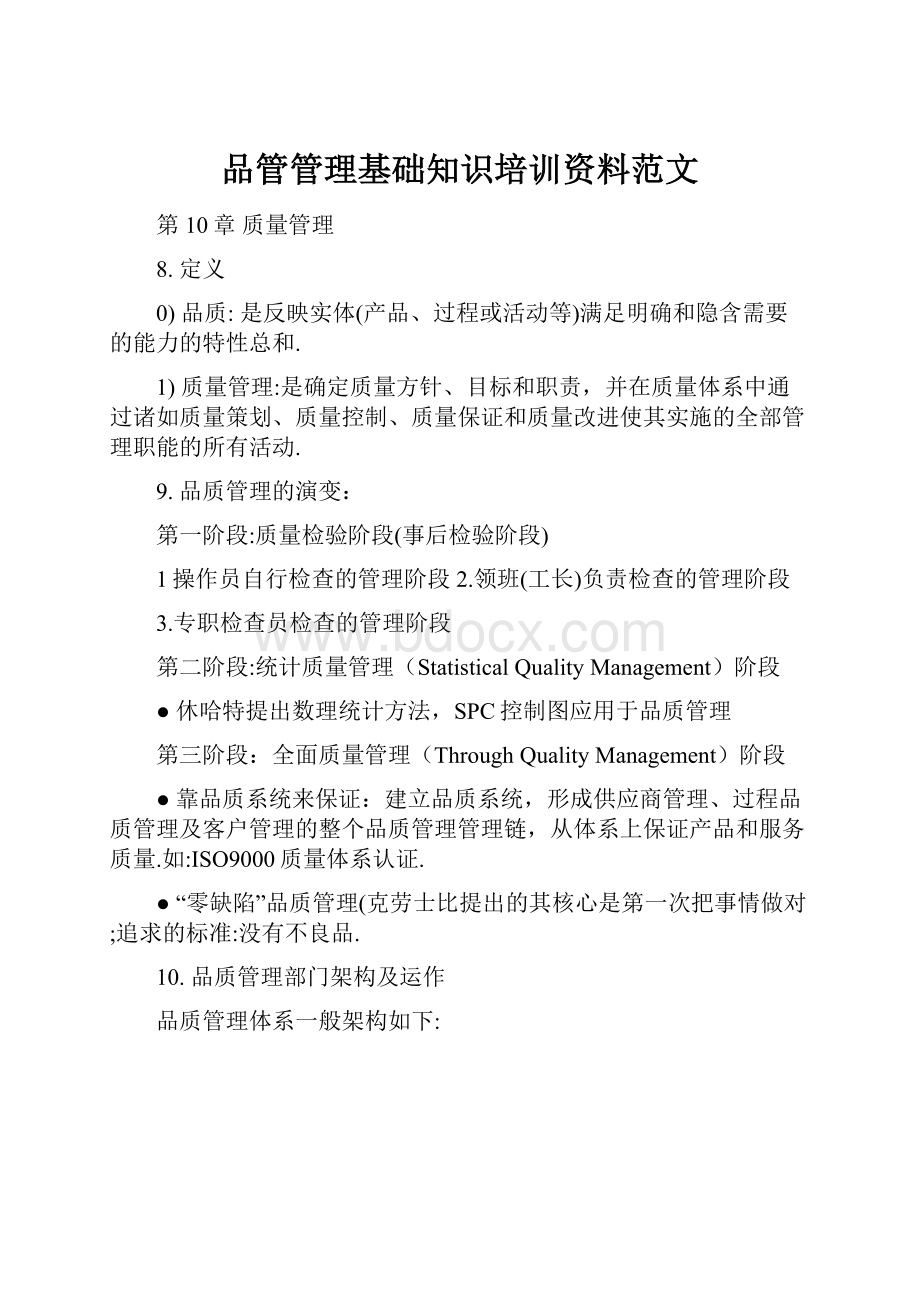
品管管理基础知识培训资料范文
第10章质量管理
8.定义
0)品质:
是反映实体(产品、过程或活动等)满足明确和隐含需要的能力的特性总和.
1)质量管理:
是确定质量方针、目标和职责,并在质量体系中通过诸如质量策划、质量控制、质量保证和质量改进使其实施的全部管理职能的所有活动.
9.品质管理的演变:
第一阶段:
质量检验阶段(事后检验阶段)
1操作员自行检查的管理阶段2.领班(工长)负责检查的管理阶段
3.专职检查员检查的管理阶段
第二阶段:
统计质量管理(StatisticalQualityManagement)阶段
●休哈特提出数理统计方法,SPC控制图应用于品质管理
第三阶段:
全面质量管理(ThroughQualityManagement)阶段
●靠品质系统来保证:
建立品质系统,形成供应商管理、过程品质管理及客户管理的整个品质管理管理链,从体系上保证产品和服务质量.如:
ISO9000质量体系认证.
●“零缺陷”品质管理(克劳士比提出的其核心是第一次把事情做对;追求的标准:
没有不良品.
10.品质管理部门架构及运作
品质管理体系一般架构如下:
L
图中各缩写词涵如下:
QC:
Qualitycontrol品质控制
QA:
QualityAssurance品质保证
QE:
QualityEngineering品质工程
IQC:
IncomingQualityControl来料品质控制
LQC:
LineQualityControl生产线品质控制
IPQC:
InProcessQualityControl制程品质控制
FQC:
FinalQualityControl最终品质控制
OQC:
OutgoingQualityControl出货品质控制
SQA:
Source(Supplier)QualityAssurance供应商品质保证
DCC:
DocumentControlCenter文件控制中心
PQA:
ProcessQualityAssurance制程品质保证
FQA:
FinalQualityAssurance最终品质保证
DAS:
DefectsAnalysisSystem缺陷分析系统
FA:
FailureAnalysis坏品分析
CPI:
ContinuousProcessImprovement连续工序改善
CS:
CustomerService客户服务
Training培训
0)供应商品质保证(SQA):
是通过在供应商处设立专人进行抽样检验,并定期对供应商进行审核、评价,从源头实施品质保证的一种方法.
主要职责:
0.对从来料品质控制(IQC)/生产及其它渠道所获取的信息进行分析、综合,将结果反馈给供应商,并要求改善.
1.根据派驻检查员提供的品质情报对供应商品质进行跟踪.
2.定期对供应商进行审核、及时发现品质隐患
3.不定期给供应商导入先进的品质管理手法及检验手段,推动其品质保证能力的提升
4.根据本公司生产反馈的状况、派驻人员检验结果、对投诉的反应速度及态度对供应商进行排序,为供应商取舍提供依据.
供应商管理的主要方法:
3.驻检验员
4.定期审核,审核项目包括:
0>品质:
包括管理职责;文件控制;质量计划;追溯性;检查与测试;工序控制/统计控制;计量;纠正/预防行动;搬运,存贮,包装,交付;培训;客户方面;品质成本;连续过程改善.根据以上内容作“供应商品质保证体系评价表”
1>生产支持:
包括物料管理;反应能力;生产性仪器设备布局;能力;变化点控制;设备、工具、治具设计、设备工具保养维修程序.
2>技术能力及新产品导入.包括技术能力、工序能力
3>一般事务:
包括组织和管理;公司目标;生产和市场能力等
5.定期对供应商排序:
排序准则:
1>SQA批合格率不得低于95%
2>IQC批合格率不得低于95%
3>部品抽入后的品质问题要求总的工序直通合格率不低于85%
4>回复纠正行动报告(CAR)的态度和速度要及时响应,对问题作令人信服的分析,并有纠正预防措施
5>交货期履行情况,能积极履行合约,并对廷期交货作合理说明
6>审核结果分数至少在60分以上
7>与本公司人员的在各项事务中配合是否良好
6.帮助供应商导入新的体系和方法
对供应商的评鉴,通常采用5R法:
RightQuality(适质)、RightPrice(适价)、RightQuantity(适量)、RightTime(适时)、RightPlace(适地)
2)来料品质控制(IQC):
又称验收检验,是管制不让不良原物料进入物料仓库的控制点。
根据供应商的品质信赖度及物料的数量、单价、体积等,分为全检;抽检;免检。
①检验项目大致可区分为:
1.外观检验,2.尺寸、结构性检验,3.电气特性检验,4.化学特性检验,5.物理特性检验,6.机械物性检验
各种产品依据要求项目,列入检验
②抽样检验一般使用随机抽样。
③验收条件:
15>一般采用规准型;也可与供应商协商后使用选别型.
16>允收水准(AQL:
AcceptQualityLevel)须协商,一般订在0.5~1.0%(或依特定产品而定)
17>采用MIL-STD-105D检验水准Ⅱ.
④物料检验一般流程图:
3)制程品质控制(IPQC)、生产线品质控制(LQC)与制程品质保证(PQA)
制程品质管制是品质管理的核心,是指来料管制(放入物料仓库存)以后到成品管制以前,这中间的生产品质控制活动,又称中间检验.
0制程品质检验的目的:
在生产中,防止大量不良产生;不让制程不良品流入下个工序.
1IPQC职责:
a>(首件/流程/作业方法)确认;
b>CSP(Criticalsamplingplan),对关键工序定时抽检.对于(以前曾有异常、不良较高的产品;不稳定的机器;新量产的机种;新人员操作)要作重点控制.
c>巡视生产线并反馈发现的品质隐患及品质问题;
d>SPC(统计控制图)制作、跟进;每日检验应有相应的检验记录,并将品质状况回馈给生产部.
2检验后产品处理:
检验合格批交下工序(成品回仓);不合格批须进行适当处置,处置结果一般为:
a.特采回用,挑选使用;b.返工/返修;C.让步接收;d.报废.
4)出货品质控制(OQC)、最终品质控制(FQC)与最终品质保证(FQA)
出货检验也就是成品管制,根据出货批数量,对照抽样标准规定的样本数,以随机抽样从总体中抽取样本,并按产品图面检验项目进行检验。
对于检验合格产品加盖PASS印,并作《出货成绩书》付在出货产品上;对与检验不合格的开《返工通知书》退生产部返工,并跟进返工结果.对生产部返工的产品批要进行加严抽样,再次对图面要求检验项目进行检验,并要求生产部采取纠正措施行动.
5)品质工程(QE)与不良改善
客户投诉处理:
a>客户投诉处理部门一般为QE部,或CS部,参与部门为技术部、生产部、品质部.
b>客户投诉处理原则:
快速反应;弄清事实;精确分析;纠防结合.
C>客户投诉处理的一般流程(见下图)
③纠正预防措施的实施:
其目的是为消除实际和潜在的不良原因,防止不良再发生.
现场改善的程序:
0.把握问题点探讨影响问题的原因
1.调查影响较大的原因
2.提出改善对策
3.对策实施
4.效果确认
5.效果维持
11.如何推动品管圈?
组成品管圈的步骤:
1)组成品管圈(5~7人),选圈长.圈长要具一定的领导能力及专业能力.
2)命圈名.
3)掌握部门内的问题点.(包括效率、成本、品质、服务、浪费等)。
4)决定主题.(应选取首要问题并有能力改善的课题)
5)制定目标.目标应是在了解现状的基础上制定,并把5W2H做法带进来.
What(万尺)《什么》:
做什么,即主题项目及目标值(数据)
Who(后)《谁》:
谁来做,即圈员应分工,各有所司.
Where(唯尔)《什么地方》:
何处进行,即进行的场所及配合部门
When(问)《在…什么的时候》:
何时.即订出阶段做法及预定进度.
HowToDo(哈噢来嘚):
如何做,即进行方法加以规划设计
How(哈噢)〈数量价值〉much(麻此)《大量的》:
成本如何,即大约需花多少成本
订目标要掌握目标管理的Smart(思马埃哦此)原则:
Specific(思败谁被K)〈细节〉:
目标要详细明确,就是主题明确.
Measurable(唛瑞的暴)〈可测量的〉:
目标要可衡量的,就是要以数据作目标.
Attainable(阿臣可暴)〈可到达的〉:
目标经努力是可以达到的,就是不要订做不到的目标.
Relevant(软伯润此)〈相关的〉:
订立的目标是团体与个人都需要的.
Timetable(插恩贼暴)《时间表》三:
目标达成、衡量是有时程的.
6)订立达成目标的工作计划.
7)掌握改善主题的重点.
8)探讨原因.
9)提出对策.(包括改善项目、发生原因、对策措施、责任者、预定完成时间)
10)对策实施。
11)效果确认。
12)效果维持.
13)总结与发表.
12.如何做好品质管理?
1)重视制度,实施标准化
2)重视执行.
品质管理涵盖4个步骤:
1.制定品质标准2.检验与标准是否一致3.采取矫正措施并追踪效果4.修订新标准
3)重视分析:
应用统计分析手法
4)重视不断的改善
品质管理在于三个层次:
1.品质开发.2.品质维持.3.品质突破
5)重视教育培训
6)改善循环与维持循环
戴明PDCA循环的四个阶段:
计划(Plan)、执行(Do)、检查(Check)、评价和处理(Action)
7)制定企业[品质月]活动
8)推行5S活动
9)高层主管的重视
第11章全面质量管理(TQM)的工作程序
一.全面质量管理(TotalQualityManagement)的指导思想:
7.从系统和全局出发的指导思想
8.为用户服务的指导思想
9.以预防为主的指导思想
10.用事实和数据说话的指导思想
11.不断改进的指导思想
12.以人为主贯彻群众路线的指导思想
13.质量和经济统一的思想
14.突出质量的经营管理思想
二.全面质量管理的工作程序
全面质量管理程序具体分为8个步骤:
第1步:
调查研究,分析现状,找出存在的质量问题
第2步:
根据存在的问题,分析产生问题的影响因素,并逐个加以分析
第3步:
找出主要影响因素,从主要影响因素着手解决质量问题
第4步:
针对主要因素,制定详尽具体的计划和措施
以上4步为P阶段的具体化
第5步:
按照计划执行.即为D阶段.
第6步:
根据计划要求,检查执行结果.即C阶段.
第7步:
根据检查结果进行总结,把成功的经验总结出来并对原有的制度、标准修正
第8步:
提出本次尚未解决的问题,并将其转为下一次P、D、C、A循环中去
三.质量螺旋曲线及质量环
质量形成过程是有一个产生、形成、实现、使用和衰亡的过程。
产品质量从市场调查研究开始,到形成,实现后交付使用,在使用中又产生新想法,构成动力再开始新的质量过程,呈螺旋上升趋势,朱兰称之为“质量螺旋”(见下图3-1)
质量环包括12个环节(见上图3-2)
第12章质量管理常用统计方法
2.抽样方法
4.随机抽样:
指总体中每一个个体都有同等可能的机会被抽到作为样本.如抽签、用随机数表
5.分层抽样:
是先将总体按照研究内容密切有关的主要因素分类和分层,然后在各层中按照随机原则抽取样本
6.系统抽样:
又叫机械随机抽样,它是在时间和空间上按一定间隔从总体中抽取样本的一种方法
0.抽样检验
9.抽样检验标准:
0.美、英、加联合制定MIL-STD-105D标准
1.美国制定ANSI/ASQCZ1.4标准
2.我国GB2828标准
2.抽样检查中的符号及其含义:
N:
批量n:
样本大小AC:
允收Re:
拒收
P:
批质量AQL:
合格质量水平Pa:
批合格概率ASN:
平均样本大小
IL:
检查水平LR:
界限数
3.规准型抽样检验:
依据消费者和生产者双方均可接受的OC曲线,来决定抽检方式.
允收水准(AcceptableQualityLevel):
对生产者,考虑了现有设备、物料、管理及操作后,认为某种程度下的不良率,消费者应可以接受,而消费者(接收者)也认为可以接受的不良率.
规定检查水平:
一般检查水平有3种:
Ⅰ、Ⅱ、Ⅲ
特殊检查水平有4种:
S-1、S-2、S-3、S-4
抽检步骤:
0.决定品质基准:
即检查项目及判定规格
1.决定品质允收水准AQL
2.决定检验水准,通常使用Ⅱ级
3.群体批(LOT)R的构成,尽可能接近同一条件下的产品
4.求样本代字(见下表)
f.决定抽样方式,使用一次抽样还是多次抽样.
g.决定检查严格度.(参见严格度调整图)
h.查出抽检方式
①由表1样品代码表查出样本的代字的行.
②由表2/3/4查出指定的AQL的列.
③由样本代字的行与AQL值的列交会点,查出合格判定个数及不合格判个数.
i.由样本代字查出抽取样本数n.
j.抽取样本.(抽取的样本要有代表性,能代表群体的品质),样本抽取方法普遍使用随机抽样
k.测量样本,并判定群体批是允收(AC)还是拒收(Re)
四.品质管理应用手法(QC七大手法)
2)层别法:
即将复杂的资料加以有系统有目的的分门别类的归纳及统计.
分类:
材料
U.S.A
China
Japan
India
人员
张三
95%
98%
94%
92%
李四
96%
95%
95%
94%
王五
95%
96%
93%
93%
小二
93%
95%
94%
94%
●时间的层别
●作业员的层别
●机械、设备的层别
●作业条件的层别
●原材料的层别
●地区的层别
结果显示:
张三使用China的材料良品率最高,为98%
3)柏拉图:
1897年,意大利学者柏拉托分析社会经济结构,发现大多数财富掌握在极少数人手里,称为“柏拉法则”.美国质量专家朱兰博士将其应用到品管上,创出了“VitalFew,TrivialMany”(重要的少数,瑣細的多数)的名词,称为“柏拉图原理”。
定义:
是根据收集的数据,以不良原因、不良状况发生的现象,有系统地加以项目(层别)分类,计算出各项目所产生的数据,(如不良率、损失金额)及所占的比例,再依照大小顺序排列,再加上累积的图形.(见下图2-1)
柏拉图分析的步骤:
(0)将要处置的事,以状况(现象)或原因加以层别.
(1)纵轴虽可以表示件数,但最好以金额表示比较强列.
(2)决定搜集资料的期间,自何时至何时,作为柏拉图资料的依据,期间尽可能定期.
(3)各项目依照合计之大小顺位自左至右排列在横轴上.
(4)绘上柱状图.
(5)连接累积曲线.
层别统计表
顺序
不良类型
不良数
占不良比率
累积比率
1
外跳
100
57.1%
57.1%
2
内跳
30
17.1%
74.3%
3
外观
20
11.4%
85.7%
4
来料
10
5.7%
91.4%
5
其它
15
8.6%
100.0%
合计
175
100.0%
图2-1
柏拉图的用途:
11.作为降低不良的依据
12.决定改善的攻击目标
13.确认改善效果
14.用于发现现场的重要问题点
15.用于整理报告和记录
16.可作不同条件的评价
4)特性要因图:
又叫鱼骨图因果图,它是1952年日本品管权威学者石川馨博士发明,又称“石川图”。
是将造成某项结果的众多原因,以系统的方式图解之,亦即以图来表达结果(特性)与原因(要因)之间的关系.(见下图)
图3-1
特性要因图的使用步骤:
(0)集合与此问题相关人员的、有经验的人员,最好为4~10人
(1)由集合人员就影响问题的要因发言,发言内容记入图上,不可对他人意见提出批评和质询(脑力激荡法)
(2)从4M1E(人Man、机Machine、物料Materiel、方法Method、环境Environment)等方面搜集20~30个原因
5W1H法:
(什么问题What、什么地点Where、什么时间When、什么人Who、原因何在Why、如何解决How)
(3)就影响最大的原因大家轮流发言,经大家磋商后,认为影响较大的矛盾圈上红圈,认为最重要的可以再圈上两圈、三圈
(4)重新画一张要因图,未上圈的予去除,圈数最多的列为优先处理
0)散布图:
是用来表示一组成对的数据之间是否有相关性。
散布图的绘制程序:
(14)收集数据(至少30组以上)2.找出数据中的最大值与最小值
(15)准备座标纸,划出纵轴、横轴的刻度,计算组距
(16)将各组对应数标示在座标上4.须填上资料的收集地点、时间、测定方法、制作者等项目
散布图类型见下图:
(8)强正相关:
X增大,Y也隨之增大,称为強正相关.
Y
X
(b)弱正相关:
X增大,Y也隨之增大,但增大的幅度不显著.
Y
X
(0)强负相关:
X增大時,Y反而減小,称为强负相关.
Y
X
(d)弱负相关:
X增大時,Y反而減小,但幅度并不显著.
Y
X
(e)不相关:
X与Y之间毫无任何关系.
Y……...
……….
……….
X
(f)非线性关相关:
X開始增大时,Y也隨之增大,但达到某一值后,当X增大時,Y卻減小.
Y
X
散布图判读注意事项:
0.注意有无异常点
1.看是否有层别必要
2.是否为假相关
3.勿依据技术、经验作直觉的判断
4.数据太少,易发生误判
5)查检表(checksheet):
就是备忘条,将要进行查看的工作项目一项一项地整理出来,然后定期或定时检查
制作程序如下:
0)制作表格,决定记录形式
1)将点检项目列出
2)查核
3)异常事故处理
查检表类型:
A.点检用查核表:
主要功用是为要确认作业实施、机械设备的实施情形,或为預防发生不良或事故,确保安全時使用.這种点检表可以防止遗漏或疏忽造成缺失的产生.(见表5-1)
把非作不可、非檢查不可的工作或項目,按點檢順序列出,逐一點檢並記錄之.
B.记录用查核表(计数用):
主要功用在於根据收集之数据以调查不良項目、不良主因、工程分布、缺点位置等情形.必要時,对收集的数据要予以层別.(见表5-2)
日期
1
2
3
4
5
6
…
31
项目
工作场地
机器保养
工具使用
人员服装
查检者
……..
……..
异常处理
修整项目
次数
外圆跳动不良
||||||||||||
内圆跳动不良
|||||||||
外观不良
|||||||||||||
磨削不完全
||||
碰伤
|||||
轴向划伤
|||
其它
||||||
表5-1表5-2
0)直方图:
又称柱状图,可将杂乱无章之资料,解析出其规则性.
1..直方图制作之步骤:
(14)收集数据,并记录于纸上.
(15)定组数:
总资料数与组数的关系如下表所示;
(16)找出最大值(L)及最小值(S),并计算全距(R)=L-S
(17)定组距(C):
R/组数=组距,通常是2.5或10的倍数
(18)定组界:
最小一组的下组界=S-测量值的最小位数(一般是1或0.1)*0.5
最小一组的上组界=最小一组的下组界+组距
最小二组的下组界=最小的上组界
依此类推.
(19)决定组的中心点:
(上组界+下组界)/2=组的中心点
(20)制作次数分布表:
依照数值大小记入各组的组界内,然后计算各组出现
的次数.
(21)制作直方图:
横轴表示测量值的变化,纵轴表示次数.
(22)填上次数、规格、平均值、数据来源、日期
例1):
测量50根铝管长度的数据
N=50
规格:
=310±8mm,测量50个长度数据如左下表6-1:
1
308
317
306
314
308
2
315
306
312
311
307
3
305
310
309
305
304
4
310
316
307
303
318
5
309
312
307
305
317
6
312
315
305
316
309
7
313
307
317
315
320
8
311
308
310
311
314
9
304
311
309
309
310
10
309
312
316
312
318
行最大
315
317
319
314
320
行最小
304
306
302
303
304
L=320
S=302
1.将其分成7组
2.全距R=L-S=320-302=18
3.组距C=18/7=2.57,取C=3
4.第一组下界=S-(S个位数*0.5
)=302-(2*0.5)=302-1=301
5.第一组上界=301+C=304
6.第二组依次类推
7.画次数分配表,见下(见表6-2)
8.画直方图(见图6-3)
表6-1
组
组界
中心值
划记
次数
1
301~304
302.5
||||
4
2
304~307
305.5
||||||||||
10
3
307~310
308.5
|||||||||||||
13
4
310~313
311.5
|||||||||
9
5
313~316
314.5
||||||||
8
6
316~319
317.5
|||||
5
7
319~322
320.5
|
1
表6-2图6-3
1.直方图的分布形状:
A.常态分布:
如(图A对称形、图2平坦形、图3尖峰形),左右对称,显示制程大致稳定、正常.
B.偏态分布:
如(图4左陡壁形、图5右陡壁形),应有人为因素.
C.双峰分布:
如(图6双峰形、图7孤岛形),制程可能有两种不同的组合.
D.不正常分布:
如(图8折齿形),可能检查测定人员对测定值的处理有偏差.
3.图形与规格比较
成常态分布,且均落于规格界限之内(准确度、精确度均可)
平均值偏低,部分比例正超过下限(准确度差)
平均值偏高,部分超过上限(准确度差)
产品变异大,品质不匀,精密度差,应改善变异或放宽规格.
产品变异太小,可能品质过剩.
1)管制图(Controlchart):