混凝土外观质量控制空港.docx
《混凝土外观质量控制空港.docx》由会员分享,可在线阅读,更多相关《混凝土外观质量控制空港.docx(8页珍藏版)》请在冰豆网上搜索。
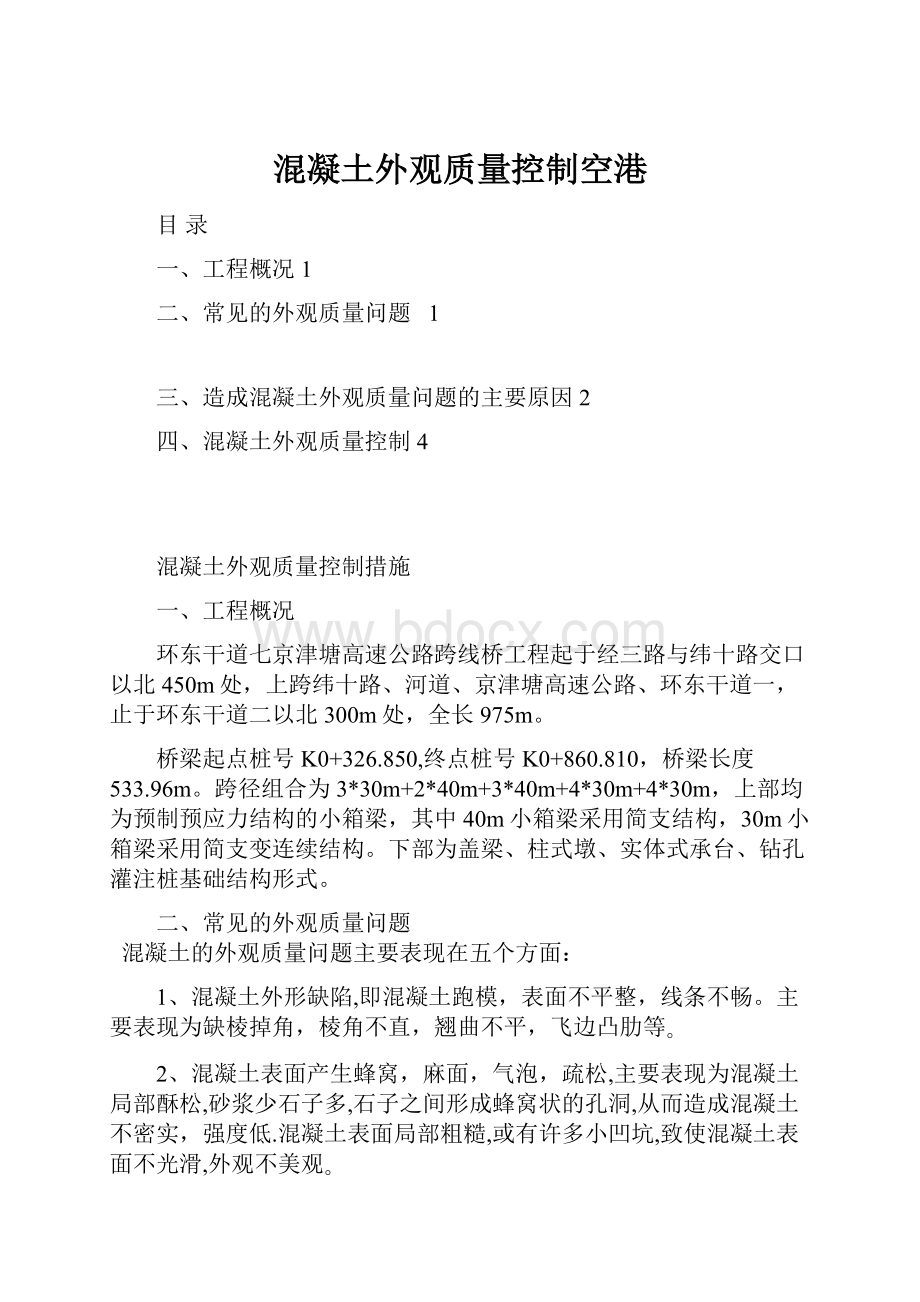
混凝土外观质量控制空港
目录
一、工程概况1
二、常见的外观质量问题1
三、造成混凝土外观质量问题的主要原因2
四、混凝土外观质量控制4
混凝土外观质量控制措施
一、工程概况
环东干道七京津塘高速公路跨线桥工程起于经三路与纬十路交口以北450m处,上跨纬十路、河道、京津塘高速公路、环东干道一,止于环东干道二以北300m处,全长975m。
桥梁起点桩号K0+326.850,终点桩号K0+860.810,桥梁长度533.96m。
跨径组合为3*30m+2*40m+3*40m+4*30m+4*30m,上部均为预制预应力结构的小箱梁,其中40m小箱梁采用简支结构,30m小箱梁采用简支变连续结构。
下部为盖梁、柱式墩、实体式承台、钻孔灌注桩基础结构形式。
二、常见的外观质量问题
混凝土的外观质量问题主要表现在五个方面:
1、混凝土外形缺陷,即混凝土跑模,表面不平整,线条不畅。
主要表现为缺棱掉角,棱角不直,翘曲不平,飞边凸肋等。
2、混凝土表面产生蜂窝,麻面,气泡,疏松,主要表现为混凝土局部酥松,砂浆少石子多,石子之间形成蜂窝状的孔洞,从而造成混凝土不密实,强度低.混凝土表面局部粗糙,或有许多小凹坑,致使混凝土表面不光滑,外观不美观。
3、露筋,构件内钢筋未被混凝土包裹而外露,从而影响钢筋与混凝土的握裹,使应力不能有效传递,局部钢筋无混凝土保护层而很快造成结构不安全。
4、施工缝处混凝土结合不好,有缝隙或夹有杂物形成缝隙夹层,造成结构物整体性不好。
5、混凝土表面骨料显露,颜色不均匀及有砂痕产生。
三、造成混凝土外观质量问题的主要原因
1、模板方面的原因
(1)模板缝口加工粗糙,模板缝口加工精度不够,拼装后存在渗漏的缝隙,缝隙比较小,水泥浆虽跑不出去,但水泥浆中的水分会渗出,使得缝隙处的水泥较多,导致缝口处混凝土表面发黑;缝隙比较大,水泥浆会从缝隙中跑出,导致缝口处出现砂线,甚至出现蜂窝,空洞。相邻模板拼装后缝口板面不平整,混凝土表面会出现错台。高墩柱模板在拼缝处加工精度或拼装精度不够,在模板拼缝处易出现“套箍”现象。
(2)模板板面不平,不洁,模板表面不平整,周转次数过多,保管不善,模板会有不同程度的变形或磨损,混凝土表面的平整度和光洁度差,钢模板表面的锈清除不彻底,混凝土表面会有锈斑,有时模板表面的红锈已除去,但表面仍有黑锈,混凝土的表面会有黑斑。模板表面涂油过早,表面沾上尘土或昆虫等杂物,影响混凝土表面的光洁度。脱模剂用废机油,混凝土表面会发黑。模板表面涂油过多或油的粘度过大,混凝土表面气泡较多。
(3)模板装拆不慎,模板支立不牢固,经振捣和混凝土倾落冲击后,模板发生跑模和变形,混凝土表面线形不顺,甚至有明显的“胀肚”现象,盖梁模板和墩柱结合不紧密,混凝土中的水泥浆会漏出而污染立柱。模板拆除过早,混凝土表面的光泽不好,会有脱皮斑点。拆除模板时模板边角或支架材料碰撞混凝土,会损坏混凝土的边角或在表面留下划痕。
2、混凝土配料方面的原因
水泥用量较多,混凝土表面光泽较好,水泥用量过多时,混凝土表面易产生龟裂。水泥用量过少,或者砂子用量过多,或者石子粒径过小,混凝土表面有磨砂感,缺乏自然光泽。水泥库存时间过短,混凝土表面会产生龟裂。水的用量过多,混凝土坍落度过大,混凝土表面会有较多的气泡。原材料色差较大,混凝土的色差较大。
3、混凝土拌和方面的原因
混凝土配料计量不准,搅拌不均匀,混凝土在运输过程中出现分层离析,或水分损失较多,用于接茬的混凝土坍落度相差较大,混凝土易出现色差。混凝土中掺加氯化钙,混凝土表面会形成暗色条纹。掺加减水剂的混凝土搅拌不匀,易出现色差。减水剂用量过大,混凝土离析、泌水现象严重,处量不好,混凝土表面色差较大。
4、混凝土浇筑方面的原因
混凝土浇筑是工程建设中的重要环节之一,浇筑质量的好坏将直接影响到工程整体质量。从实验中看,振捣方法不当和浇筑工艺不妥都会直接影响到混凝土的外观质量。
5、钢筋显隐现象
在混凝土的浇筑过程中,振捣棒触碰钢筋或模板等现象会使钢筋受到较大的振动或扰动,使得钢筋周围的混凝土离析、泌水,或者钢筋的保护层偏小,混凝土的表面会显露钢筋的轮廓,但不是露筋,这种现象称为钢筋显隐,钢筋的显隐使得混凝土表面形成色差。
四、混凝土外观质量控制
1、模板制作安装质量控制
模板外观应达到下列要求
(1)侧板无翘曲、变形,表面平整无凹凸,无褶皱;
(2)焊缝饱满、牢靠,无夹渣、漏焊、焊瘤、结疤等焊接质量存在;
(3)阴阳接头要严格按图纸施工,加工精确,结合紧密。
(4)模板两块间接缝处平直、光滑且拼接后严密,顺直。
对于模板局部表面不平整处,采用砂轮机对其进行打磨,打磨后的表面与周围模板表面相接平顺过渡,确保模板表面光滑和平整度的要求。
局部产生变形时,采取切实可行的措施对模板进行调整,修整后的模板应符合要求。
制造加工完成后,并经检查合格的模板,涂刷防锈剂,置于存放场地,应遮盖。
模板在使用前进行整修除锈,然后用脱模剂自上而下均匀涂刷两遍以上,达到摸之有油、视之无油的程度。
2、砼浇筑工艺质量控制
坍落度
砼拌合物是砼成形结构的原材料,而砼拌合物的成形可塑性的最终反映是坍落度,对砼外观质量的控制,最重要的是砼坍落度控制,要求砼拆模后对砼外露面的色泽感观一致,则要求砼坍落度一致,所以,恰当控制反映砼和易性指标的坍落度就很有必要。
拌合物含水量少,易克服砼气泡。
一般情况都采用12-16cm坍落度的拌合物;但有外观质量要求的砼,坍落度较通常一般采用的坍落度略减少1-2cm,使砼拌合物稠一点粘一点,振捣效果好一些,有利于砼外观质量。
为此,需将通常的泵送砼12-16cm,调整为11-14cm,施工时,要求砼搅拌运送对砼坍落度波动严格按照上下限限差控制,以求砼的塑性稳定。
砼浇筑与振捣
强调浇与振并重,必须克服重视振捣、轻视浇铺的习惯现象。
浇铺无序或振捣无方,都是砼产生各种不均匀弊端的根源。
唯一克服的办法是注意把握浇与振的“火候”,要求振捣要密切注意浇铺状况,什么状况不能振,什么状况可以振,以及振多长时间,多少遍数,都依据浇铺具体情况而定。
把握火候,是确保砼建立密实质量的措施。
即对砼不要早振,也不要迟振;不要欠振,也不要过振。
砼的浇振方法:
⑴段分层、限时接茬
砼的浇筑,无论是按从一端开始向另一端,或从中不开始向两端对称的,呈斜面层次,全断面而推进的浇筑方法,还是按从下向上一层层的,呈水平层次浇筑方法,都必须分段、分层次地进行浇筑作业。
如下图示:
4812
3711
2610
159
第三层
第二层
第三段
第二段
第一段
第一层
斜面层次
101112
789
456
123
第三层
第二层
第一段
第二段
第三段
第一层
水平层次
所谓分段,是指砼浇筑筑进程的划分,确定分段长度的原则:
在砼未初凝的可重塑时间内,完成砼的分层拼茬和分段接茬,确保砼供料跟得上;根据砼浇筑时气温条件,防止砼浇捣面上水分挥发过多造成接茬不良。
若发生砼拌合物表面失水而未初凝的“假凝”现象时,可先用振捣棒震动,使其液化后在接茬浇筑。
所谓分层,是指砼灌筑过程中,按断面处自下而上分次进行的砼虚铺厚度,40-50cm一层为宜(约为振动棒作用半径的1.25倍),每层砼挨次、连续进行等厚铺浇。
结构模板有限角倒坡时,砼铺至内侧倒坡以下5cm,把坡顶留出,便于排气泡。
砼分段分层的后段与前段或上下层之间的浇筑(接茬)间隔时间,在常温气候条件下,限为2个半小时为宜。
虽然水泥初凝时间不早于45min,终凝时间不迟于10小时,但砼拌合物(不掺缓凝剂时)的初凝时间一般为4小时左右,因为当水泥初凝时砼失去塑性,终凝时砼开始产生强度,如果振捣,砼表面不会留下接茬痕迹。
如果超过了3个小时或4个小时;当砼已经接近初凝,或砼是水过多上下层间插捣困难,即使勉强振捣,砼中水泥(砂)浆的塑性差异过大,难于均匀分布,结果形成色差带或冷缝式色差;如果当下层砼已经失去塑性而达到完全初凝状态时砼接茬,则必然造成冷缝。
⑵浇前振后、切莫早振:
砼振实过程,是砼拌合物在所浇部位上进行;一是液化;二是振动;三是振实。
为达到砼均匀密实性,振捣确有许多讲究,首先是前面浇后面振的配合步骤,切忌早振。
所谓早振,有两种情况:
一是指本层砼厚度未铺足或本层浇铺不到位或两侧模之间未全范围铺满(横向未到边,纵向不连贯),即砼拌合物层次不清、顺序零乱,往往出现中间高、两边低,或一边高、一边低的堆积和低洼现象。
此时,如果依然随浇就急于振捣,则称为早振。
二是对本层砼浇铺段前沿临空部分,不等下段砼浇铺衔接,就过早振捣,也称早振。
特别是箱梁、T型梁和盖梁以及防撞护栏等砼浇筑,无论采用斜面层次还水平层次方法浇筑,要切实注意对每层砼振捣作业时,始终保持“浇”与“振”前后沿一段至少相当于振捣棒作用半径二倍的范围内的砼,不要急于振捣,待下一段浇铺接茬后在振。
早振的结果是:
①砼拌合物有流动现象,砂浆与骨料分离或水泥砂浆泛出向低处漫溢;②再浇砼时,随砼浇注量增加,砼液化面上升,则富水泥浆上浮,紧靠侧模面,形成色差带;③倘若振捣时过振,会出现水纹似的云状或磷状色斑。
所谓“过振”,是振动延时过长,砼易产生离析、泌水。
离析状态较重的,砼骨料分离,显露砂石;轻的出现泌水、砂线、砂斑。
⑶快插慢提,振速控制:
当振捣棒的棒头直径和振捣时间或上提速度来定:
一是模板内看的见的砼,以现象观察为准,砼振实特征表现为:
砼已无显著沉落、表面呈现平坦,砼已不冒气泡、砼开始泛浆。
二是对能见度低或阴角部分,以快插慢提的速度为准,一般塑性砼采用通常的插入式振捣棒,整个过程的累计振捣时间为25秒左右,即按本层砼厚度做振捣动作;①“快插”,用1-2秒时间尽快插入后上下抽动2-3次,以助砼沉落稳定;②“振捣”,振捣棒于插点不提动,用10秒左右时间振捣;③“慢提”,振捣棒往上提时慢速提动约用15秒时间(即按每次3-5cm速度上提,每提一次停1-2秒时间),振实并排气。
振捣棒提的快了,砼中的气泡排除不好。
振捣作业注意事项:
操作注意:
①振动棒差点间距,最大不超过振捣棒作用半径1.5倍。
中型振动棒通常控制40cm等间距移动,便可防止漏振现象发生。
如前后2根振动棒工作,其互相距离,一般为3-5m。
②要离开模板拼缝20cm左右,因拼缝处是容易渗水漏浆的薄弱环节。
③振捣棒作为砼的振捣工具,且莫用于振赶砼流动,防止砂浆散失而失去均匀性。
亦不得将振捣棒卧下来(呈水平状态)振捣,否则表面泛浆严重,导致产生层次(带状)色差。
④掌握振捣时间或速度,还与拌合物坍落度大小有关,如拌合物较稀时,相应缩短振捣时间,减少抽动次数,防止过振,如当砼坍落度7cm时震动25秒,则5cm时应为30秒,9cm时应为20秒。