采煤机检修工艺.docx
《采煤机检修工艺.docx》由会员分享,可在线阅读,更多相关《采煤机检修工艺.docx(14页珍藏版)》请在冰豆网上搜索。
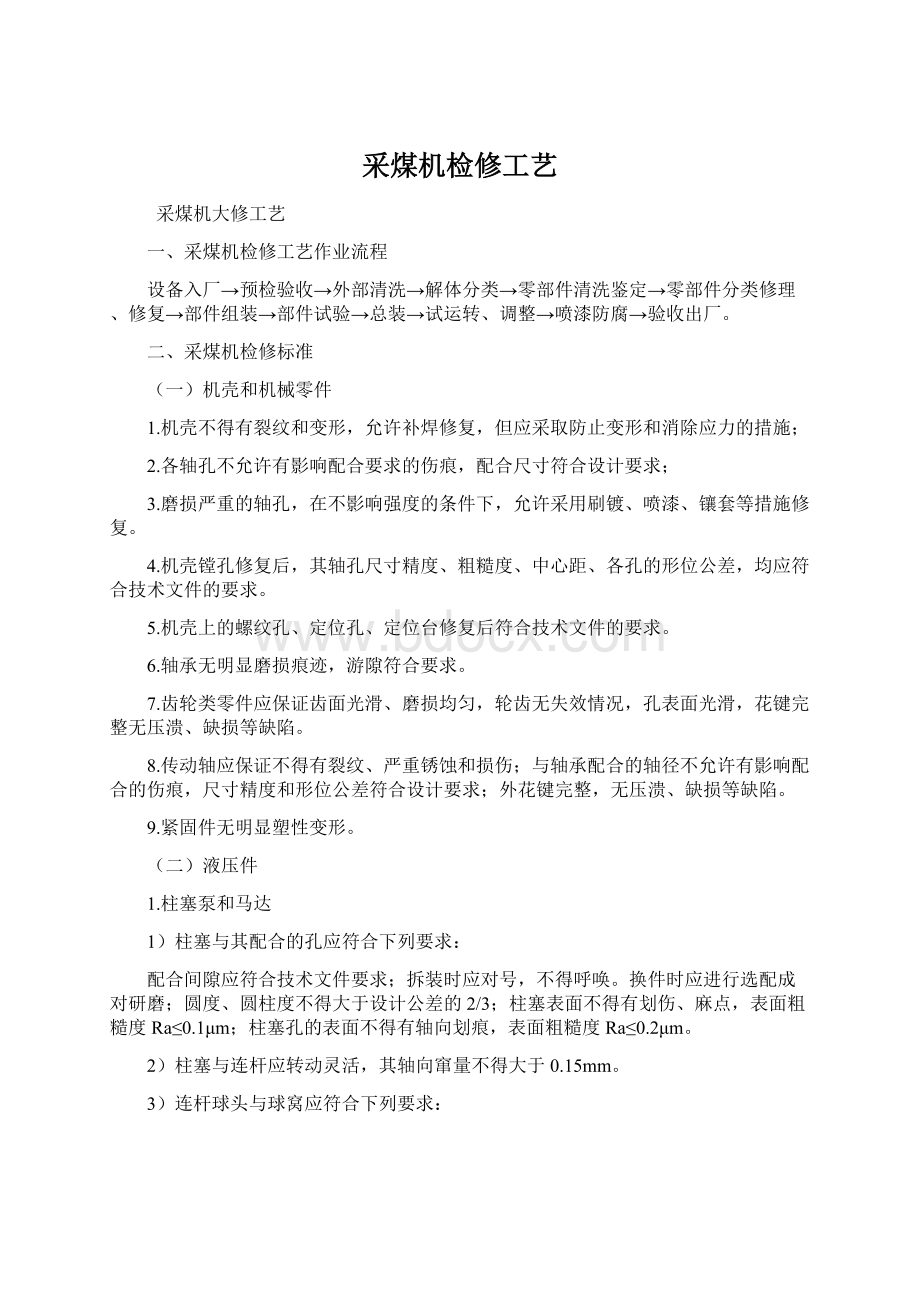
采煤机检修工艺
采煤机大修工艺
一、采煤机检修工艺作业流程
设备入厂→预检验收→外部清洗→解体分类→零部件清洗鉴定→零部件分类修理、修复→部件组装→部件试验→总装→试运转、调整→喷漆防腐→验收出厂。
二、采煤机检修标准
(一)机壳和机械零件
1.机壳不得有裂纹和变形,允许补焊修复,但应采取防止变形和消除应力的措施;
2.各轴孔不允许有影响配合要求的伤痕,配合尺寸符合设计要求;
3.磨损严重的轴孔,在不影响强度的条件下,允许采用刷镀、喷漆、镶套等措施修复。
4.机壳镗孔修复后,其轴孔尺寸精度、粗糙度、中心距、各孔的形位公差,均应符合技术文件的要求。
5.机壳上的螺纹孔、定位孔、定位台修复后符合技术文件的要求。
6.轴承无明显磨损痕迹,游隙符合要求。
7.齿轮类零件应保证齿面光滑、磨损均匀,轮齿无失效情况,孔表面光滑,花键完整无压溃、缺损等缺陷。
8.传动轴应保证不得有裂纹、严重锈蚀和损伤;与轴承配合的轴径不允许有影响配合的伤痕,尺寸精度和形位公差符合设计要求;外花键完整,无压溃、缺损等缺陷。
9.紧固件无明显塑性变形。
(二)液压件
1.柱塞泵和马达
1)柱塞与其配合的孔应符合下列要求:
配合间隙应符合技术文件要求;拆装时应对号,不得呼唤。
换件时应进行选配成对研磨;圆度、圆柱度不得大于设计公差的2/3;柱塞表面不得有划伤、麻点,表面粗糙度Ra≤0.1μm;柱塞孔的表面不得有轴向划痕,表面粗糙度Ra≤0.2μm。
2)柱塞与连杆应转动灵活,其轴向窜量不得大于0.15mm。
3)连杆球头与球窝应符合下列要求:
连杆球头表面不得有划伤,麻点,表面粗糙度Ra≤0.1μm;球窝表面不得有划痕,表面粗糙度Ra≤0.2μm;球头与球窝的接触面积与配合间隙应符合生产厂家技术文件要求,修磨或更换零件必须成对研磨。
4)转子与配油盘(盖)的配合面不得有划痕,修磨量不得大于表面硬化层厚度的50%,研磨必须成对进行。
5)径向柱塞泵、马达的曲轨表面不得有划伤、剥落现象,表面粗糙度Ra≤0.4μm。
6)斜盘轴向柱塞泵的滑履与斜盘滑动表面不得有划伤,表面粗糙度Ra≤0.1μm。
7)柱塞复位弹簧不得有断裂、疲劳和锈痕等缺陷。
8)其余各主要工作部分的配合间隙、接触密封均应符合生产厂家技术文件要求。
9)各种液压泵液压马达检修后,须经检验合格后,方可装机使用。
10)液压泵若由于密封件损坏,达不到性能要求时,可更换密封件,检修后进行性能测试,压力应达到原液压泵指标,流量不低于系统设计要求。
液压泵主要零件损坏的应整体更换。
2.阀类
1)各种阀体均不得带有磁性,配合面不得有毛刺、划伤、锈斑和点蚀等缺陷。
2)各种阀的配合表面可以研配直到符合要求。
3)滑阀的配合面、密封面的表面粗糙度不得大于0.1,其它阀配合面的表面粗糙度不得大于0.4.
4)阀杆和阀孔的配合间隙为0.01~0.03mm。
磨损后间隙的增大量不得超过原设计要求1/3。
5)电磁阀的换向稳定性应符合下列要求:
在液压系统额定压力下,换向与复位必须迅速、灵活、可靠,不得有外泄漏和卡阻现象;当电压降至额定电压的85%时,电磁阀应能正常动作。
6)各种阀类元件损坏应更换,主要元件损坏应更换新件,各种阀修复后应能满足液压系统要求。
7)阀体上各种孔道表面、阀芯表面以及其他镀层表面不得剥落或出现锈蚀。
8)阀用弹簧不得有锈蚀、腐蚀半点,弹性符合设计要求,否则应更换。
9)方向控制阀检修后,应保证其动作灵活,做1.5倍额定耐压试验5min,不得渗漏。
10)压力表、温度计损坏应更换。
未损坏应对齐进行校核,保证正确可靠工作。
11)油箱应彻底清洗干净,并加入要求牌号液压油。
压力表、温度计、油位计、空气滤清器应完好。
每周或在污物阻塞报警指示时更换过滤网。
(三)行走驱动装置
1.各零件应认真清洗,不得有锈斑,机壳不得有任何污物。
2.伺服机构调零必须准确。
3.试验前应按规定注入经过滤的油液,并排干净管路中的空气。
4.各种安全保护装置必须齐全、灵敏、可靠,并按规定值调定,不得甩掉任何一种保护装置。
(四)截割传动装置和滚筒
1.滚筒应转动灵活,不得有裂纹和开焊,不得损坏喷嘴螺纹。
滚筒端面齿座,径向齿座应完整无缺,其孔磨损不得超过1mm,补焊齿座角度应符合技术文件要求。
更换齿座时应首先保证与原设计的几何位置相同,然后采用预热或保护焊等工艺,保证焊接强度,且齿座应具有互换性。
2.截齿座严重磨损影响其强度或孔变形过大,影响使用时应更换。
在更换过程中不得损坏切割体的其他部位。
3.螺旋叶片的磨损不超过原厚度的1/3,否则要进行补焊。
4.喷雾配水装置中易损件、密封件应更换,两金属零件密封面磨损应全部更换。
5.截割电动机扭矩轴应灵活,手把固定应可靠,当一根轴损坏时应将两根轴都更换。
6.截割电动机限矩器应检查磨损程度,当磨损指示器的表面与端盘齐平时应及时更换输出装置。
(五)附属装置
1.密封件(油封、浮动油封、0形密封圈、防尘圈、油缸用密封圈等)应全部进行更换。
2.连接件、紧固件无明敁塑性变形,否则应进行更换。
3.底托架、挡煤板无裂纹、严重变形或开焊现象。
底托架的平面度不得大于5mm
4.滑靴磨损量不得超过10mm,销轴磨损量不得超过1mm。
5.行走轮、导向滑靴无严重磨损或变形,否则应更换。
有链牵引的采煤机,导链器不得变形,不得有卡阻现象;牵引链紧装置应齐全可靠。
6.采煤机的冷却喷雾系统符合技术文件要求,不得有变形。
外喷雾装置齐全,在额定压力1.5倍下进行试验,不得有漏水现象。
7.防滑装置应对靠,制动力矩符合技术文件要求。
8.机身护板整形、配齐。
9.进行耐压和动作试验,不得出现漏液。
(六)部件试验
1.泵、马达
1)跑合试验:
在最大排暈、空载压力工况下启动,达到公称转速后运转2min以上,开始测量排量,其值应在公称排量95%〜110%的围。
然后逐渐加载分级跑合。
2)超载试验:
在公称转速、最大排量下,逐渐加载至最高输出压力或额定压力的125%,运转1min以上,不得有异常现象。
3)在进行上述各项试验时,观察外泄漏、噪声、振动及温升,不得有异常现象。
2.行走驱动装置
1)试验准备:
按要求注油排气,接通电源,接上冷却水,水温不低于10℃。
2)空运转试验:
以最大工作牵引速度正反向各空载运转20min,再以最大调动牵引速度正反向各空载运转10min,观察运转情况和各部温升情况。
要求操作灵活、运转平稳、无异常响声或强烈振动,各部分温升正常,定位可靠,零位准确;所有油管接头和各密封处无渗漏现象,测定的空载最大牵引速度(输出轴转速)应符合设计要求。
3)热平衡试验:
在最大工作牵引速度和最大工作牵引力下连续加载运转,直到各测温点(检验部门根据热源位置确定)均达到热平衡(每小时温升不超过IK时视为热平衡)。
正反向各试验一次。
测录各测温点的热平衡温度和环境温度。
要求液压系统油池热平衡油温不大于75℃,温升不大于50K;齿轮传动油池热平衡油温不大于100℃,温升不大于75K;其他各测温点(如电动机、变压器、电力电子器件等)的极限温度指标按设计要求或有关规定。
具有四象限运行牵引特性的采煤机,在最大工作牵引速度和最大工作牵引力下连续运转,直到各测温点均达到热平衡(每小时温升不超过1K时视为热平衡)时,热平衡温度的要求同上。
4)牵引特性试验:
牵引速度给定在最大工作牵引速度位置,缓慢加载,直到牵引速度降到零或接近于零,然后缓慢减载直到完全卸载,测录出在最大工作牵引速度下的最大工作牵引力值;牵引速度给定在最大调动牵引速度位置,试验方法同上,测录出在最大调动牵引速度下的最大调动牵引力值(牵引特性无恒功率区段的不进行);牵引速度给定在1/5最大工作牵引速度位置,试验方法同上,测录出在1/5最大工作牵引速度下的最大工作牵引力值。
反向以完全相同的方法试验,并观察运行稳定性。
具有四象限运行牵引特性的采煤机牵引速度给定在最大工作牵引速度位置,调整试验台的加载装置为原动机工况,缓慢增加制动力,直到制动力额定值。
以上工况各重复试验两次,且试验时各测温点均保持在热平衡温度。
要求在最大工作牵引速度下的最大工作牵引力值应符合额定值;在最大调动牵引速度下的最大调动牵引力值应符合额定值;在1/5最大工作牵引速度下的最大工作牵引力应符合额定值。
误差不得大于±5%并运行稳定。
具有四象限运行牵引特性的采煤机在最大工作牵引速度下的最大制动力应符合额定值,误差不得大于±5%,并运行稳定。
5)运转过程中,应无异常噪声和撞击声,无渗漏现象。
试验结束后,检查齿面接触情况,应无点蚀、剥落或胶合等现象。
6)试验后,放油清洗油池,更换滤油器。
3.截割传动装置
1)试验准备:
截割传动组装注油后,接通电源,按设计要求的水量接上冷却水,冷却水温度不低于10℃。
2)轻载跑合试验:
以截割(主)电动机额定功率的25%运转120min,应运转平稳,无异常响声或强烈振动,各部分温升正常,各密封处无渗漏现象。
跑合后,放油清洗油池。
3)温升试验:
重新加油,摇臂置于近水平位置,以截割(主)电动机额定功率的50%运转60min、75%运转60min和100%运转30min以后,测录各减速箱油温和环境温度,最髙油温不得大于100℃,最高温升不得大于75K。
运转过程中,应无异常噪声和撞击声,无渗漏现象。
试验后检查齿面接触情况,应无点蚀、剥落或胶合现象。
(七)整机试验
1.试验准备:
采煤机整机安装在配套刮板输送机中部槽上,行走部驱动装置输出轴空转,按设计要求供电、供冷却水(水温不低于10℃),各油池按规定的油质和油量加油。
2.空载跑合试验:
依次启动各电动机(供少量冷却水),牵引速度给定在最大工作牵引速度位置,两摇臂分别处于最高和最低位置,空运转30min;速度给定在反向最大工作牵引速度位置,两摇臂的最髙和最低位置交换后,再运转30min。
运转过程中测录各电动机的输人功率、滚简转速、破碎滚筒转速和正反向最大工作牵引速度各三次;观察各部分运转和温升情况,以及所有管路系统和各接合面的密封情况。
要求空载跑合时滚筒转速、破碎滚筒转速、最大牵引速度值位符合原设计要求;各电动机空载功率接近原采煤机出厂检验报告值;各部分运转平稳,无异常噪声、无异常振动和异常温升;各密封处均应密封良好,不得有渗漏现象。
3.操作系统试验:
依次操作采煤机(包括无线电随机控制和巷道控制)的所有机械、电气、液压操作手把、按钮、旋钮各五次。
观察各受控部位的动作准确性和可靠性(包括预告信号和延时启动)及各显示器(显示屏、表、光柱等)的显示。
要求操作手把、按钮、旋钮操作灵活,各受控部位动作准确,不得有任何误动作;预告信号和延时启动时间均应符合设计要求;显示淸楚,显示值符合原设计要求。
4.空运转噪声测定:
依次启动各电动机(供少量冷却水),牵引速度给定在最大工作牵引速度位置,将声级计分别放置在采煤机中部和机身两端水平距离1m处,测录三处的空运转噪声值。
5.摇臂调高系统试验:
启动摇臂调髙系统电动机,滚筒不转动。
操作调高手把,使摇臂在最髙位置和最低位置之间往复摆动三次,观察运行情况;将摇臂停在最髙位置,测录最大截割髙度,将摇臂停在最低位置,测录下切深度(可在没有滚筒的情况下进行);将摇臂由最低位置升至最高位置,测录上升全行程所需时间;将摇臂由最高位置降至最低位置,测录下降全行程所需时间;摇臂处于最低位置或最高位置时,继续操作调髙手把直至安全阀开启动作,测录安全阀开启压力;将摇臂置于近水平位置,16h后测录滚筒中心的下降量。
左右摇臂均需分别完成以上试验。
要求左右摇臂升降均匀,无抖动现象;最大截割高度和下切深度应符合原设计要求;升降全行程所需时间应符合原设计要求;安全阀开启压力应符合原设计要求;摇臂置于近水平位置,16h后滚筒中心下降量不得大于25mm。
6.破碎滚简升降系统试验:
启动破碎滚筒升降系统电动机,破碎滚筒不转动。
操作破碎滚筒升降手把,使破碎滚筒上下升降三次,观察运行情况,将破碎滚筒停在最高位置,测录破碎滚筒底端距输送机中部槽中板的垂直距离;将破碎滚筒停在最低位置,测录破碎滚筒底端距输送机中部槽中板的垂直距离;将破碎滚筒置于最高位置,16h后测录破碎滚筒中心的下降量。
要求破碎滚筒升降平稳,无抖动现象;破碎滚筒在最高位置和最低位置时滚筒底端距输送机中部槽中板的垂直距离应符合原设计要求;破碎滚筒置于最髙位置,16h后滚筒中心下降量不得大于15mm。
7.空载行走试验:
行走部的行走轮(或主链轮)与行走轨(或牵引链)啮合,采煤机依次以1/5最大工作牵引速度和1/2最大工作牵引速度在直线铺设的输送机中部槽上往返行走各三次,观察运行情况。
空载行走应运行平稳,无卡滞现象。
三、主要检修容为:
1.对采煤机的牵引箱、左右截割部、摇臂滚筒、行走机构、底托架等上井冲洗、分解、清洗、检查、修理或更换。
2.对油缸分解、清洗、检查、修理,对镀层有锈蚀、划痕或碰伤超过标准的应重新电镀,更换全部密封件并做打压试验。
3.各种阀类全部分解、清洗,更换损坏的零部件,更换全部密封。
按规定做打压试验,逐条检查各高压胶管,更换不合格的高压胶管,更换全部密封件。
4.做好检修试验记录。
四、检修工艺流程图见附表
五、各主要检修工序工艺规程
(一)冲洗采煤机
1.采煤机进入厂房,打扫采煤机上的浮矸、浮煤等,以减少冲洗工作量;
2.用天车将采煤机吊至冲洗室,用高压水(压力达到30MPA)冲洗采煤机上的矸石、煤尘以及其它杂物等;
3.清理地上的煤泥,并冲洗干净。
(二)采煤机解体
1.截割部拆卸
1)采用专用工具拆卸截齿。
2)拆卸截割滚筒。
先用行车先将其拉好,下面用枕木支好。
拆卸滚筒压盖螺钉并拆下压盖,拆卸滚筒与驱动方盘的连接螺栓,用行车慢慢拉出滚筒。
3)拆卸摇臂。
将摇臂降至地面或用木头支撑,拆卸护罩,拆卸水管和油管,并堵口以防止污物进入。
拆掉电机引线及接线盒。
将螺栓拧入销轴涨套中心使涨套松开,取下销轴。
完成拆卸。
4)拆卸截割部的减速箱、电机。
先将摇臂与减速箱的连接锥销拆掉,拆掉电机的花键输出轴的弹性转矩轴,脱开减速箱与电机的连接。
5)拆卸减速箱各端盖,依次拆卸各轴、齿轮、轴承,清洗后做好标记按顺序分类存放。
2.牵引部拆卸
1)排放牵引箱的润滑油。
2)用工具将牵引部表面的紧固螺栓拆掉,将盖板拆掉。
3)用顶丝旋入销轴,将销轴拔出。
起吊采煤机,将导向滑靴和链轮沿着销排滑动,直到其脱离惰轮,拆掉导向滑靴和链轮组。
4)利用天车将采煤机抬高,直到其脱离溜槽,然后将其支撑固定。
将螺栓从卡片中取出。
将上部连接销向外拔大约25mm,可以取掉卡片。
将连接销从机腿中拔出,将机腿挪开。
将滑靴和机腿分离开来,拔掉螺栓,取出销子,拆掉机腿和支撑滑靴。
5)拆调高油缸和液压制动器时,除拆卸连接长螺钉、销轴和紧固螺栓外,应特别注意其与齿轮泵及各种安全阀、换向阀、电磁阀的连接管路,以免损伤管路;对液压制动器,先拆下其与缸体固定的6颗螺栓,方能拆卸。
6)拆下调高泵、拆下调高电机。
7)拆牵引部减速箱的固定螺栓,将减速箱的连接轴花键拿掉后,可将其卸载;之后卸掉牵引电机。
8)将牵引部与电控箱的螺柱拆掉,再拆掉行走箱;
3.拆电控箱及中间架
1)先将中间框架靠煤壁侧的管线通道拆掉,再将拖缆架、连接板、电缆夹板的连接销拔出,紧固螺栓拆掉,再将其的电缆、油管、水管拆掉,以免对其造成破坏;
2)拆卸变频箱和电气控制系统时,因其没有独立的设计箱,又是采煤机的核心部分,故拆卸时必须要小心,不能碰伤撞坏。
(三) 左右摇臂检修:
1.摇臂壳体的修复:
1)测量与轴承外圈、轴、轴承座、密封盖配合的孔尺寸,当超过极限尺寸0.02mm—0.05mm时,采用刷镀或涂镀处理,当超过极限尺寸在0.05mm以上时,采用补焊机加工进行修复。
2) 检查各配合面,平面度超过0.05mm或划痕长度大于配合面宽度的2/3或深度超过0.3~0.5mm时采用补焊机加工修复。
3) 壳体上非加工面有裂纹、损伤、变形时,采用补焊打磨修复。
4)壳体上连接螺纹孔、轴承座固定螺纹孔超差时进行补焊机加工修复;
5)壳体的水腔渗水时,重新进行焊接,并进行打压保压测试达要求;
2.销轴检修
配合的轴径磨损量0.02mm—0.05mm时,采用刷镀或涂镀处理; 磨损严重的进行更换。
3.轴承座检修
1)检查与轴承外圈相配合的孔径,超过极限尺寸0.02mm—0.05mm在围时采用刷镀或涂镀处理,当超过极限尺寸在0.05mm以上时采用补焊机加工进行修复。
2)轴承座上的台孔变形、损坏时采用补焊机加工修复。
3)轴承座上的工艺拆装螺纹孔变形、损坏时采用补焊机加工修复。
4)轴承座上的固定螺纹孔超差、变形、损坏时采用补焊机加工修复。
4.行星架修复
1)测量重要配合尺寸,与轴承圈、销轴、密封相配合的尺寸超过极限尺寸0.02mm时,采用刷镀或涂镀处理,当超过极限尺寸在0.05mm以上时采用补焊机加工进行修复。
2)检查固定用螺纹孔,超差、有断丝时采用“钻孔—补焊—钻孔—攻丝"工艺进行修复。
5.驱动方盘修复
1)驱动方盘的四方头尺寸超出极限尺寸在0.05mm以上时采用补焊机加工进行修复。
2) 固定螺纹孔超差时采用“扩孔—补焊—钻孔—攻丝"工艺进行修复。
6.分水块修复
1)与轴承、密封相配合的尺寸,超过极限尺寸0.02mm时,采用刷镀或涂镀处理,当超过极限尺寸在0.05mm以上时采用补焊机加工进行修复。
2)分水接口螺纹、固定螺纹孔超差、损坏、变形时采用补焊机加工修复。
3)台孔、非配合的表面损坏、变形时采用补焊机加工修复。
7.截割滚筒修复
1)驱动方孔尺寸超过极限尺寸0.1 5mm以上时采用补焊机加工进行修复。
2)各齿座的孔径超过极限尺寸0.02mm时需更换齿座。
3)螺旋叶上的耐磨块磨损后用耐磨焊条补焊打磨修复或直接更换。
8.护板修复
1)变形时采用火焰加热进行校正。
2)通孔、台孔上变形、损坏时采用补焊机加工修复。
9.截割部组装
1)组装摇臂行星轮组件。
将轴承装入行星轮中,安装行星轮到行星架,装入行星轮销轴,安装销轴的止退卡圈。
2)截割摇臂低速区安装。
将摇臂水平放置,并安装各惰轮; 再将摇臂垂直放置并支承平稳; 装入行星部大轴承; 将行星部装入箱体;安装齿圈;安装轴承杯,并调整锥轴承的轴向间隙;安装浮动密封;安装驱动盘;安装分水阀;插入中心水管;安装齿轮组件;安装轴承压盖。
3)高速区安装。
将轴承外圈安装到摇臂轴承孔中; 将轴承圈安装到齿轮上; 吊起齿轮,将其装入摇臂壳体。
将轴承压盖安装到位,并用螺栓联接,紧固到要求力矩。
4)截割电机的安装。
用天车将截割电机吊起,并安装O型密封;在电机与摇臂壳体接触部位涂抹润滑脂;将电机垂直装入摇臂壳体;安装紧固螺栓,并紧到要求力矩;装入扭矩轴,并将电机的密封盖安装到位。
5)安装摇臂连接板。
清理打磨摇臂、连接板的接触表面;安装定位销;将连接板吊起,安装到摇臂上; 安装M30联接螺栓,并用倍增器紧到要求力矩。
(三)牵引部检修
1. 牵引部壳体修复
1)配轴承、导向滑靴相配的孔超过极限尺寸0.02mm时,采用刷镀或涂镀处理,当超过极限尺寸在0.05mm以上时采用补焊机加工进行修复。
2)测量与轴承杯相配合的孔,超过极限尺寸0.05mm以上时采用补焊机加工进行修复。
3)4个定位销孔超过极限尺寸大于0.02mm时,采用补焊机或加套加工进行修复。
4)轴承杯及轴承压盖的固定螺栓超差时采用补焊机加工修复。
5)起吊用的螺纹孔损坏、变形、开裂时采用补焊机加工修复。
6)结合面平面度超过0.05mm或结合面上的划痕长度大于结合面宽度的2/3或深度超过0.3~0.5mm时采用补焊机加工修复。
2.轴承杯修复
1)与轴承相配的孔超过极限尺寸0.02mm时,采用刷镀或涂镀处理,当超过极限尺寸在0.05mm以上时采用补焊机加工进行修复;
2)与密封相配的孔超过极限尺寸0.05mm以上时采用补焊机加工进行修复。
3)与壳体相配的外径尺寸、与密封圈相配的孔径尺寸超过极限尺寸0.15mm 采用补焊机加工修复。
4)螺纹孔超差时采用补焊机加工修复。
5)台孔变形、有焊渣时采用机加工修复。
6)结合面平面度超过0.05mm或结合面上的划痕长度大于结合面宽度的2/3或深度超过0.3~0.5mm时采用补焊机加工修复。
3.距离套、轴承压圈检修
1)结合面平面度超过0.05mm或结合面上的划痕长度大于结合面宽度的2/3或深度超过0.3~0.5mm时采用补焊机加工修复。
2)与密封相配的孔超过极限尺寸0.05mm以上时采用补焊机加工进行修复。
4.导向滑靴检修
1)与牵引块的铰接孔超过极限尺寸0.05mm以上时采用补焊机加工进行修复。
2)螺纹孔超差、变形、损坏时采用补焊修复。
3)用标准块进行止口尺寸磨损检测,磨损严重尺寸超出最大允许值时,采用补焊修复。
4)其它非配合表面磨损或变形后采用补焊修复。
5.支承滑靴检修
1)与机脚的铰接孔超过极限尺寸0.05mm以上时采用补焊机加工进行修复。
2)底部支承面磨损不严重或局部磨损后补焊修复,整体磨损严重时更换底部焊件,然后进行机加工到图纸要求尺寸。
3)对滑靴底部磨损量严重部位采用数控等离子耐磨熔覆工艺,进行耐磨强化。
如果磨损导致尺寸减小太多,可先用普通焊条堆焊打底,再进行熔覆。
6.机腿检修
1)与油缸相配的孔、与机身铰接的前端小孔超过极限尺寸0.02mm时,采用刷镀或涂镀处理,当超过极限尺寸在0.05mm以上时采用补焊机加工进行修复。
2)与机身铰接的后部两大孔、与支承滑靴铰接的孔超过极限尺寸0.05mm以上时采用补焊机加工进行修复。
3)螺纹孔变形、开裂、损坏时,采用焊接机加工修复。
7.连接耳修复
1)公差小于等于0.05mm的配合尺寸(油缸铰接孔、定位销孔),超过极限尺寸0.02mm时,采用刷镀或涂镀处理,当超过极限尺寸在0.05mm以上时采用补焊机加工进行修复。
2) 公差为大于0.05mm的孔径尺寸(与摇臂的铰接孔)超过极限尺寸0.05mm以上时采用补焊机加工进行修复。
3)螺纹孔超差时采用补焊机加工修复。
4)台孔变形、损坏、有焊渣时采用机加工修复。
5)结合面平面度超过0.05mm或结合面上的划痕长度大于结合面宽度的2/3或深度超过0.3~0.5mm时采用补焊机加工修复。
8.牵引部组装
1)煤壁侧齿轮箱体的组装。
依次将各齿轮的轴承外圈分别装入轴承孔,圈装到各轴上;依次装入各齿轮;安装轴承压盖,用螺栓联接,坚固到要求力矩。
2)采空侧齿轮箱的组装。
将齿轮所用轴承的圈安装到齿轮轴上,外圈装入箱体的孔; 将齿轮安装到位;将齿轮轴承杯安装到位,用螺栓联接,紧固到要求力矩;安装齿轮圈;装入太阳轴;将行星架组件吊起,安装到位。
3)牵引块的组装。
清理打磨牵引箱壳体及轴承杯; 将轴承圈装到传动轮上,外圈装到箱体及轴承杯的孔;安装传动轮的Y型密封;将传动轮吊起装到箱体;安装轴承杯,安装联接螺栓,紧固到要求力矩; 调整锥轴承的轴向间隙;安装轴承压盖;安装链轮组件。
(四)整机组装
1.电控箱、左右牵引箱联接。
将电控箱安全平稳地放置在组装平台上;清理打磨三体间的接触平面,之后在平面上涂抹润滑脂;安装四个定位销;将左牵引箱平稳吊起与电控箱对接,支承平稳,安装联接螺栓,并用力矩倍增器将其紧固到规定力矩。
右牵引箱联接过程同。
2.安装机腿及支撑滑靴,将机腿推入到左右牵引箱下部;用千斤顶及撬杠调整其高度直到与牵引箱的铰接孔对正;穿入铰接销; 安装止退卡片;将支承滑靴同样推入到机腿下部,使其铰接孔对正;穿入铰接销;安装止退卡片。
3.安装牵引块。
安装牵