罩壳注塑模设计.docx
《罩壳注塑模设计.docx》由会员分享,可在线阅读,更多相关《罩壳注塑模设计.docx(20页珍藏版)》请在冰豆网上搜索。
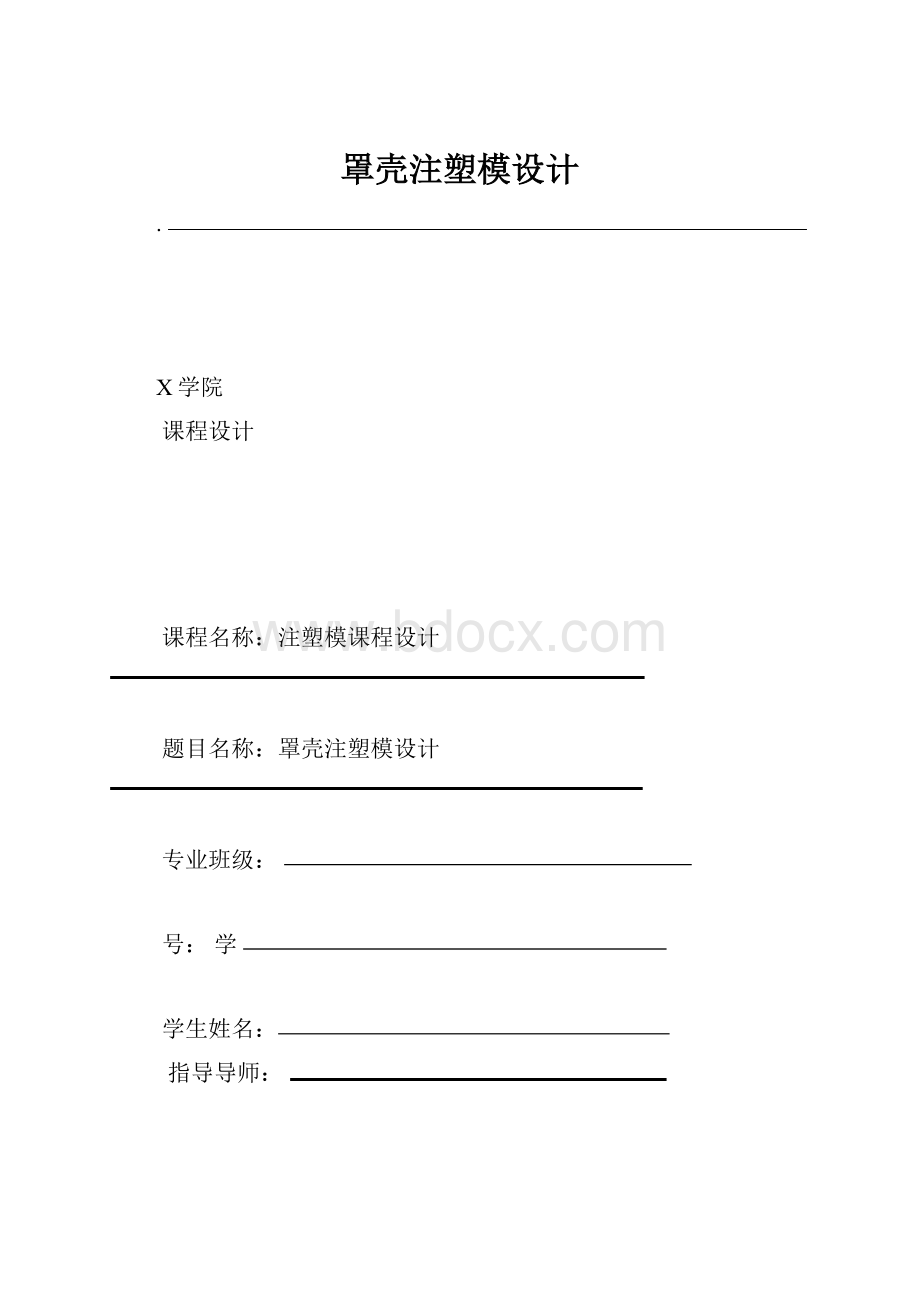
罩壳注塑模设计
.
X学院
课程设计
课程名称:
注塑模课程设计
题目名称:
罩壳注塑模设计
专业班级:
号:
学
学生姓名:
指导导师:
;.
.
设计题目…………………………………………………………………………2
一:
塑件的工艺性分析……………………………………………………………3
1、塑件的原材料分析……………………………………………………………3
2、塑件的结构工艺性分析………………………………………………………4
3、塑件的尺寸精度分析…………………………………………………………4
4、塑件表面质量分析…………………………………………………………4
二:
成型设备选择与校核………………………………………………………4
1、注塑机的初选…………………………………………………………………4
2、注塑机的校核与终选…………………………………………………………5
3、塑件模塑成型工艺参数的确定………………………………………………6
三:
注射模的结构设计…………………………………………………………6
1、分型面的选择…………………………………………………………………7
2、型腔数目的确定及型腔的排列……………………………………………8
3、注系统的设计…………………………………………………………………8
4、型芯、型腔结构的确定………………………………………………………9
四:
成型零件尺寸计算…………………………………………………………10
五:
冷却系统的设计……………………………………………………………10
1、冷却直径和位置……………………………………………………………10
2、冷却介质……………………………………………………………………11
六、模架的尺寸………………………………………………………………11
七.排气系统的设计……………………………………………………………12
八:
导向与定位结构的设计……………………………………………………12
九:
推件方式的选择……………………………………………………………12
十:
模具的工作原理及特点……………………………………………………13
1、工作原理……………………………………………………………………14
2、结构特点……………………………………………………………………14
设计小结…………………………………………………………………………15
参考文献…………………………………………………………………………15
;.
.
一.塑件的工艺性分析
塑件的工艺性分析包括:
塑件的原材料分析、塑件的尺寸精度分析、塑件表面质量和塑件的工艺性分析,其具体分析如下:
1、塑件的原材料分析
塑件材料该塑件为塑料罩壳,壁厚为3mm,塑件外型尺寸不大,选用PP塑料,塑件精度要求为MT5级。
性能:
密度小,强度、刚性、硬度、耐热性均优于HDPE,可在100℃左右使用。
具有优良的耐腐蚀性,良好的高频绝热性,不受温度影响,但低温变脆,不耐磨,易老化。
成型特性:
结晶型塑料,吸湿性小,可能发生熔体破裂,长期与热金属接触易发生1)分解;
流动性极好,溢边值0.03mm左右;2)冷却速度快,浇注系统及冷却系统的散热性适度;3)成型收缩范围大,收缩率大,已发生缩孔,凹痕、变形,取向性强4)注意控制成型温度,料温低时取向性明显,尤其低温高压时明显,模5)具温度低于50℃以下塑件无光泽,易产生熔接痕、流痕;90℃以上时已发生翘曲、变形;
塑件应壁厚均匀,避免缺口,尖角,以防止应力集中6)物理、热性能、力学性能、电气性能
2、塑件的结构工艺性分析
⑴从图纸上分析,该塑件的外形为回转体,壁厚均匀,都为3.2mm,且符合最小壁厚要求.
⑵塑件型腔较大,有尺寸相等的孔,它们均符合最小孔径要求.
3、塑件的尺寸精度分析
塑件的型腔尺寸:
;.
.
塑件表面质量分析:
、34、该塑件为工业用罩盖塑料,对其表面质量没有什么高的要求,粗糙度可取Ra3.2um,塑件内部也不需要较高的表面粗糙度要求,所以内外表面的粗糙度都3取Ra3.2um.
二、成型设备的选择及校核
1、注塑机的初选
1.1计算塑件的体积
根据制件的三维模型,利用三维软件直接求得塑件的体积为:
V=33;=10.32cm1032mm
1.2计算塑件的质量
30.9g/cm=查手册得密度为:
?
塑件的质量为:
M=V×?
=9.288g
1.3选用注射机
3,初步选取螺杆式注塑成型机XS—1.288cm根据总体积V=ZY—60
注塑成型机XS—ZY—60主要参数如下表所示
;.
.
3250mm最小模具厚度250理论注射量cm
130MPa定位孔的直径20注射压力?
125mm深
SR18mm1800kN喷嘴球半径锁模力
?
350mm4mm最大模具厚度喷嘴孔半径
350mm移模行程
、注塑机的终选2注射量的校核2.1
W≥由公式:
0.8W注公3);W——注塑机的公称注塑量(cm公——每模的塑料体积量,是所有型腔的塑料加上浇注系统塑料的总和W注3);(cm
3远小于注塑机的理论注如前所述,塑件及浇注系统的总体积为1032mm
3,故满足要求。
250cm
模具闭合高度的校核2.2
Hmax﹤H闭﹤公式:
Hmin
而注塑成型机的最大模具厚260mm,闭=如装配图可知模具的闭合高度HHmaxH闭﹤最小模具厚度Hmin=250mm,满足Hmin﹤度Hmax=350mm,
安装要求。
模具安装部分的校核2.3
,故能满足安装要求。
×250mm模具的外形尺寸为300mm
,满足安装要求。
?
100模具定位圈的直径?
=注塑机定位孔的直径
满足要求。
SR1=SR+(1-2)=20浇口套的球面半径为
满足要求。
R+9(1-2)=4+1=5浇口套小端直径R1=
模具开模行程的校核2.4
H≤公式:
H=H1+H2模注(mm)——模具的开模行程H模(mm)——注塑成型机移模行程H注)H1——制件的推出距离(mm
)H2——包括流道凝料在内的制品的高度(mm
,满足要求。
=350mm=代入数据得:
H≤H注模锁模力的校核2.5
KAPmF≥公式:
;(kN)F——注射机的额定压力
(cm)A——制件和流道在分型面上的投影面积之和
15MPa——型腔的平均压力Pm(Mpa);这里取
;~——安全系数,通常取KK=1.11.2
;.
.
将数据代入公式得:
15X2826*2=93.258KNKAPm=1.1×
,满足要求。
F=1800KN>93.258KN
注射压力的校核2.6
P0K′公式:
Pmax≥
;(Mpa)Pmax——注射机的额定注射压力
;(Mpa)P0——注射成形时的所需调用的注射压力
′——安全系数K
将数据代入公式得:
满足要求。
130Mpa≤Pmax=′P0=1.3×80=104MPaK
完全符合本模具的使用要求—250选取螺杆式注塑成型机XS—ZY结论:
3、塑件模塑成型工艺参数的确定
LDPE可根据实际情况作适当调整试模时,注射成型工艺参数见下表,规格工艺参数规格
工艺参数注射时间2-6预热和干燥成型时间/s温度t/℃:
80-100
15-60高压时间
时间/h:
1-2
后段冷却时间15-60160-180料筒温度t/℃
180-200中段总周期35-130
200-220
前段48
)n/(螺杆转速140-160喷嘴温度t/℃方法红外线灯烘后处理箱40-65模具温度t/℃温度t/℃70
70-100
注射压力2-4
p/Mpa
/h
时间三、注射模的结构设计
分型面的选择、模具型腔数目的确定及型腔的排:
注射模结构设计主要包括列、浇注系统设计、型芯、型腔结构的确定、推件方式、侧抽芯机构的设计、.
模具结构零件设计等内容、分型面的选择1
只要求外径没有,,该塑件为工业用圆盖塑料对其表面质量没有什么高的要求考虑不影响塑根据分型面的选择原则在选择分型面时明显的斑点及熔接痕.,,;.
.
件的外观以及成型后能够顺利取出制件,有以下方案:
由分型面选择原则,
2、型腔数目的确定及型腔的排列
由于该塑件采用一模二件成型,所以,型腔布置在模具的中间.这样也有利于浇注系统的排列和模具的平衡.
3、浇注系统的设计
(1)主流道设计
a、主流道尺寸
主流道是指浇注系统中从注射机喷嘴与模具接触处开始到分流道为止的塑料熔体的流动通道,是熔体最先流经模具的部分,它的形状与尺寸对塑料熔体的流动速度和充模时间有较大的影响,因此,必须使熔体的温度降和压力损失最小。
根据手册查得XS-ZY-60型注射机喷嘴的有关尺寸:
喷嘴球半径:
R=18mm0喷嘴孔直径:
d=Ф4mm0定位孔的直径:
Ф100mm
主流道通常设计在浇口套中,为了让主流道凝料能顺利从浇口套中拔出,主流.
,内壁表面粗糙度Ra小于2~60.4um,小端直径道设计成圆锥形,其锥角为。
,a=43~6mm。
现取锥角一般取注射机喷嘴直径大0.5~1mm,小端直径Dd小端直径比喷嘴直径大1mm套一般采用碳素工具钢材料制造,热处理淬火硬度50~55HRC。
由于小端的前面是球面,其深度为3~5mm,这里取3mm,注射机喷嘴的球面在该位置与模具接触并且贴合,因此要求主流道球面半径比喷嘴球面半径大1~2mm。
浇口套与模板间配合采用H7/m6。
主流道是一端与注射机喷嘴相接触,另一端与分流道相连的一段带有锥度的流动通道。
主流道小端尺寸为5mm。
主流道的长度由定模座板和定模板厚度确定,一般L不超过60mm。
b、主流道衬套的形式
;.
.
主流道小端入口处与注射机喷嘴反复接触,属易损件,对材料要求较严,因而模具主流道部分常设计成可拆卸更换的主流道衬套形式,以便有效的选用优质钢材单独进行加工和热处理。
常用浇口套分为浇口套、定位圈整体式和浇口套与定位圈单独分开两种(下图为后者),由于注射机的喷嘴球半径为18mm,所以浇口套的为R22mm。
根据模具主流道与喷嘴的关系:
R=R+(1~2)mm0D=d+(0.5~1)mm
0取主流道的球面半径R=20mm
主流道的小端直径d=Ф5mm设计如图
c、主流道衬套的固定
因为采用的为分开式,所以用定位圈配合固定在模具的面板上。
定位圈的外径为Φ125mm,内径Φ35.5mm。
具体固定形式如下图所示:
;.
.
(2)分流道的设计
分流道的形状及尺寸与塑件的体积、壁厚、形状的复杂程度、注射速率等因素有关.该塑件的体积比较大但形状并不复杂,且壁厚均匀,可以考虑采用多点进料的方式,缩短分流道的长度,有利于塑件的成型和外观质量的保证.从便于加工的方面考虑,采用截面形状为半圆形的分流道.查有关的手册,选择R=2mm.由于分流道中与模具接触的外层塑料迅速冷却,只有中心部位的塑料熔体的流动状态较为理想,因面分流道的内表面粗糙度Ra并不要求很低,一般取1.6μm左右既可,这样表面稍不光滑,有助于塑料熔体的外层冷却皮层固定,从而与中心部位的熔体之间产生一定的速度差,以保证熔体流动时具有适宜的剪切速率和剪切热。
(3)浇口设计
a.浇口形式的选择
由于该塑件外观质量要求不高,浇口的位置和大小还是要不能太影响塑件的外观,同时,也应该尽量使模具结构简单.根据对塑件结构的分析及已确定的分型面的位置,选择侧浇口
主要用于圆筒形制品或中间有孔的制品,它可使进料均匀,在整个圆周上进料的流速大致相同,空气容易顺序排出,同时避免了侧浇口的型芯对面的熔接痕,但是浇口凝料去除困难,需要切削加工或冲切法去除.
b、浇口位置的选择
模具设计时,浇口的位置及尺寸要求比较严格,初步试模后还需进一步修改浇口尺寸,无论采用何种浇口,其开设位置对塑件成型性能及质量影响很大,因此合理选择浇口的开设位置是提高质量的重要环节,同时浇口位置的不同还影响模具结构。
总之要使塑件具有良好的性能与外表,一定要认真考虑浇口位置的选择,;.
.
通常要考虑以下几项原则:
1.尽量缩短流动距离。
2.浇口应开设在塑件壁厚最大处。
3.必须尽量减少熔接痕。
4.应有利于型腔中气体排出。
5.考虑分子定向影响。
6.避免产生喷射和蠕动。
7.浇口处避免弯曲和受冲击载荷。
8.注意对外观质量的影响。
根据本塑件的特征,综合考虑以上几项原则,进浇点的分流道开型芯台阶上。
4、型芯、型腔结构的确定
整体式型腔是直接在一整块材料上加工而成的凹模即为整体式凹模(如上图a),其特点是牢固,不易变形,有较高的强度和刚度,成型的塑件表面不会有模具接缝痕迹.当塑件结构简单时,制作整体式凹模比较容易,所以选择整体式型腔。
型腔尺寸和设计如下:
;.
.
型芯设计如下:
;.
.
四、成型零件尺寸计算
%~Q=1PP的收缩率为查有关手册得该塑件的成型零件尺寸均按平均值法计算.模具的制造公差根据塑件尺寸公差要求,S=(1+3)/2=2%;故平均收缩率为3%,cp。
△/4Z=取塑件公差的1/4,即δ
类塑件尺寸计算公式型腔
别
;.
.
600.44?
mm60.9
0型32腔0.44?
mm32.480计180.44?
mm18.27算18
0.44?
mm18.270
160.44?
mm16.24056
0mm56.84
0.44?
型320芯mm32.480.44?
计160mm16.24算
0.44?
中mm0.2890?
90心距
五、冷却系统的设计、冷却的直径和位置1冷却冷却直径尽量大,在满足冷却所需要的传热面积和模具结构允许的前提下,,冷却水道应易于加工和清理,10mm水道孔边与型腔表面之间的距离一般大于。
8mm,这里取16mm因此直径一般不小于2、冷却介质℃℃和50℃PP属于流动性较好的材料,其成型温度及模具温度分别为200~22070℃,用常温水对模具进行冷却。
~90℃。
所以模具温度初步选定为
六、模架的尺寸
如果侧壁或底板的强度不足塑料模具型腔在成型过程中承受着塑料熔体的高压,,使脱模困难造成溢料如果强度不足,,则可能产生过大的变形,,则可能产生开裂大尺,一般情况下,型腔侧壁和底板厚度的计算方法有强度计算和刚度计算两种小尺寸型腔强度不足是主要问,寸型腔刚度不足是主要问题应按刚度条件计算,;.
.
题,应按强度条件计算.
根据制件的尺寸分析,本制件的成型型腔属于较大尺寸,所以应按刚度来计算,而型腔采用的是整体式,根据型腔的材料和经验,壁厚应50~80mm由此按经验参考
图如下
七.排气系统的设计
该塑件由于采用侧浇口进料熔体经塑件上方的台阶向下充满型腔,所以型腔顶部不会造成憋气现象,气体会沿着分型面和型芯与推件之间的轴向间隙向外排出,所以不需另进行设计。
八.导向与定位结构的设计
注射模的导向机构用于动、定模之间的开合模导向和脱模机构的运动导向。
按作用分为模外定位和模内定位。
模外定位是通过定位圈与注射机相配合,使模具的浇口套能与注射机喷嘴精确定位;而模内定位机构则通过导柱导套进行合模定位。
锥面定位则用于动、定模之间的精密定位。
本模具所成型的塑件比较简单,模具定位精度要求不是很高,因此可采用模架本身所带的定位机构。
九、推件方式选择
因为塑件是罩子、壳体形,适合用推件板推出机构,推件板借助于动、定模的导柱导向;故导向方便可靠,推件板不必另设复位机构,在合模过程中,推件板依靠合模力的作用而复位。
这种机构的特点是,在制品的整个周边进行推出,因而脱模力大而均匀,运动平稳,无明显推出痕迹。
推杆的设计,一般的直径为15~25mm,长度大于60mm,与推杆孔的配合可采用H7/f7或H8/f8,一般的推杆形状为,如下图:
;.
.
但是为了增加细长推杆的刚性,可将其设成台阶形,如下图:
十、模具的总装图
;.
.
设计小结
通过本次的塑料注射模具的设计,加深了我对所学的专业课程《塑料模具设计》等的了解和掌握,系统地整理了我们在大学所学的专业知识并进一步运用到这次的设计实践中,提高了我的专业知识水平以及动手能力。
在这次的注射模具的设计中,基本知道了注射模设计的步骤通过对本次的注射模设计,掌握了注射模的整个设计流程,了解了如何根据产品的要求,塑件的形状,材料的性能来设计模具从而最终生产处满足要求的产品的模具。
在整个设计过程中,我们运用到了很多专业的知识,所以我们必须查找各种公式,数据,虽然这个过程是繁琐的、枯燥的、乏味的甚至到了让我想放弃的地步,但是为了设计出合格的模具,我还是坚持了下来。
在设计过程中我犯过很多错误甚至懒惰到不想设计,最后我设计出了基本合乎要求的模具。
参考文献
[1]翁其金,徐志扬.塑料模塑成型技术机械工业出版社,2010
[2]伍先明,王群等.塑料模具设计指导.北京:
国防工业出版社,2009.
[3]齐卫东简明塑料模具设计手册北京理工大学出版社
[4]李海梅,申长雨等.注塑成型及模具设计实用技术.北京:
化学工业出版社,2002.
[5]王昆,何小柏等.机械设计课程设计.北京:
高等教育出版社,1996.
;.