syt4109石油天然气钢质管道无损检测教学内容.docx
《syt4109石油天然气钢质管道无损检测教学内容.docx》由会员分享,可在线阅读,更多相关《syt4109石油天然气钢质管道无损检测教学内容.docx(64页珍藏版)》请在冰豆网上搜索。
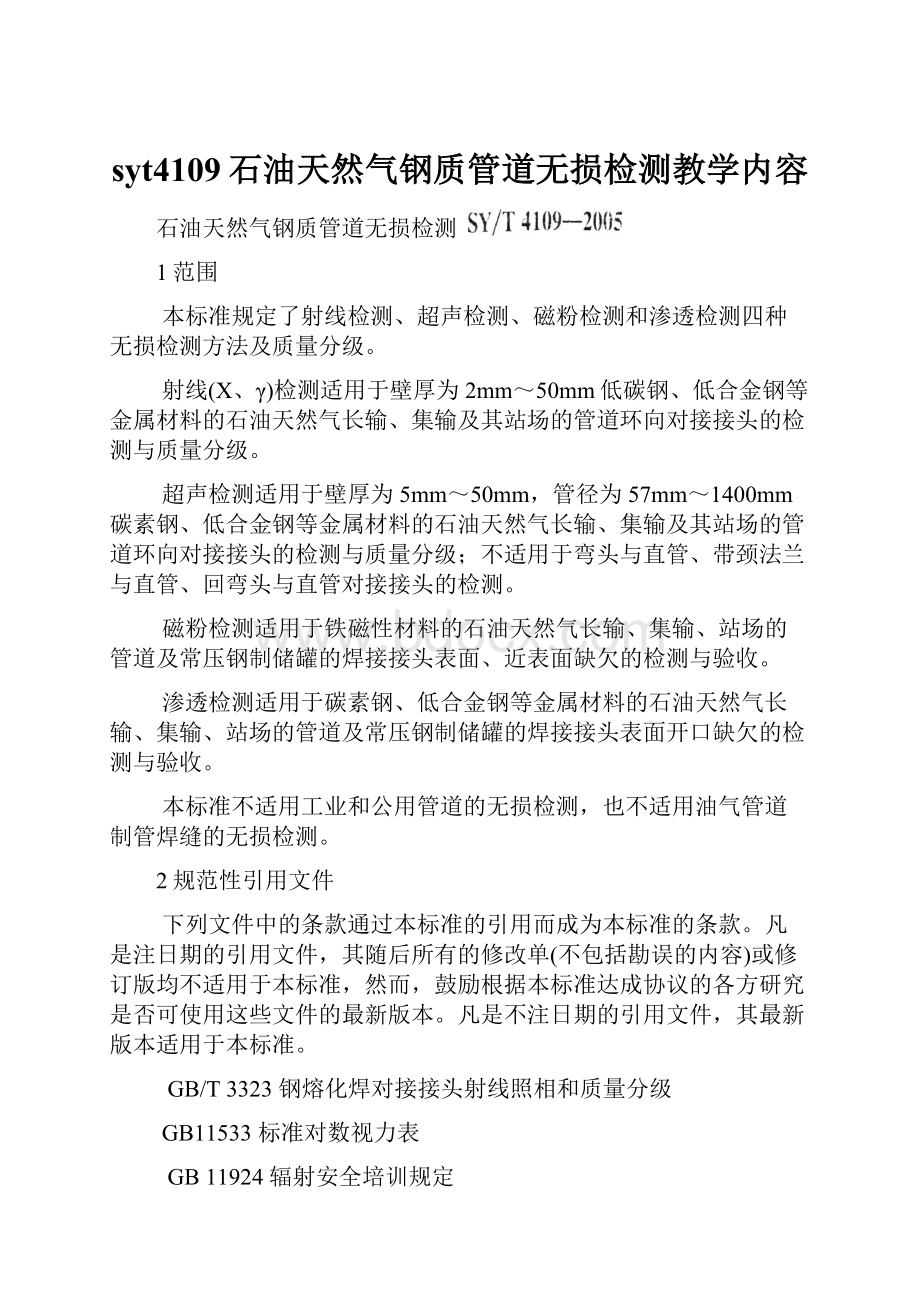
syt4109石油天然气钢质管道无损检测教学内容
石油天然气钢质管道无损检测
1范围
本标准规定了射线检测、超声检测、磁粉检测和渗透检测四种无损检测方法及质量分级。
射线(X、γ)检测适用于壁厚为2mm~50mm低碳钢、低合金钢等金属材料的石油天然气长输、集输及其站场的管道环向对接接头的检测与质量分级。
超声检测适用于壁厚为5mm~50mm,管径为57mm~1400mm碳素钢、低合金钢等金属材料的石油天然气长输、集输及其站场的管道环向对接接头的检测与质量分级;不适用于弯头与直管、带颈法兰与直管、回弯头与直管对接接头的检测。
磁粉检测适用于铁磁性材料的石油天然气长输、集输、站场的管道及常压钢制储罐的焊接接头表面、近表面缺欠的检测与验收。
渗透检测适用于碳素钢、低合金钢等金属材料的石油天然气长输、集输、站场的管道及常压钢制储罐的焊接接头表面开口缺欠的检测与验收。
本标准不适用工业和公用管道的无损检测,也不适用油气管道制管焊缝的无损检测。
2规范性引用文件
下列文件中的条款通过本标准的引用而成为本标准的条款。
凡是注日期的引用文件,其随后所有的修改单(不包括勘误的内容)或修订版均不适用于本标准,然而,鼓励根据本标准达成协议的各方研究是否可使用这些文件的最新版本。
凡是不注日期的引用文件,其最新版本适用于本标准。
GB/T3323钢熔化焊对接接头射线照相和质量分级
GB11533标准对数视力表
GB11924辐射安全培训规定
GB16357工业X射线探伤放射卫生防护标准
GB/T16673无损检测用黑光源(UV—A)辐射的测量
GB18465工业γ射线探伤放射卫生防护要求
GB18871电离辐射防护与辐射源安全基本标准
JB/T6063磁粉探用磁粉技术条件
JB/T6065磁粉探伤用标准试片
JB/T7902线型像质计
JB/T7913超声波检测钢制对比试块的制作与校验方法
JB/T8290磁粉探伤机
JB/T9214A型脉冲反射式超声波探伤系统工作性能测试方法
JB/T10061A型脉冲反射式超声波探伤仪通用技术条件
JB/T10062超声探伤用探头性能测试方法
JB/T10063超声探伤用1号标准试块技术条件
ZBY344超声探伤用探头型号命名方法
3术语和定义
下列术语和定义适用于本标准。
3.1
缺欠imperfeetion
按无损检测方法检出的不连续性。
3.2
缺陷defect
采用本标准验收超出合格级别的缺欠。
3.3
表面未熔合incompletefusion(IF)
表面未熔合是指熔焊金属与母材之间未能完全熔化结合且延续到表面,如图1所示。
图1表面未熔合
3.4
夹层未熔合incompletefusionduetocoldlap(IFD)
夹层未熔合是指熔焊金属之间(层间未熔合)或熔焊金属与母材之间(坡口未熔合)未能完全熔化结合,但不延续到表面,如图2所示。
图2夹层未熔合
4一般要求
4.1使用原则
4.1.1由于射线、超声、磁粉和渗透等检测方法都具有各自的特点和局限性,为提高检测结果的准确性,应根据被检产品的材质、制造方法、工作介质、使用条件和失效模式,预计可能产生的缺欠种类、形状、部位和取向,选择最合适的无损检测方法。
4.1.2射线和超声检测主要用于检测石油天然气钢质管道对接接头内部的缺欠;磁粉检测主要用于钢质管道焊接接头表面及近表面的缺欠;渗透检测主要用于检测钢质管道焊接接头表面开口的缺欠。
4.1.3石油天然气钢质管道对接接头内部的面状缺欠,宜采用超声检测;管道对接接头内部的体积状缺欠及薄壁管对接接头,通常采用射线检测。
4.1.4铁磁性材料表面检测时,宜优先采用磁粉检测。
4.1.5当采用两种或两种以上的检测方法对石油天然气钢质管道的同一部位进行检测时,应符合各自的合格级别。
如采用同种检测方法、不同检测工艺进行检测,当检测结果不一致时,应以质量级别最差的级别为准。
4.2检测单位(部门)责任
4.2.1按本标准进行检测,必须按4.3的要求编制出无损检测工艺规程。
4.2.2检测程序及检测结果应正确、完整并有相应责任人员签名认可。
检测记录、报告及底片等按规定要求存档,保存期不得少于7年。
7年后,若用户需要可转交用户保管。
4.2.3检测档案中,对于检测人员承担检测项目的相应资格等级和有效期应有记录。
4.2.4检测用的仪器、设备应定期检验合格并有记录。
4.3无损检测工艺规程
无损检测工艺规程由通用工艺规程和工艺卡两部分组成。
4.3.1无损检测通用工艺规程:
无损检测通用工艺规程按本标准编制,满足石油天然气相关法规、标准的要求。
一般由无损检测中级(Ⅱ级)及以上人员编制,无损检测责任工程师审核,本单位总工程师批准。
无损检测通用工艺规程修订更改时也应履行上述程序。
4.3.2无损检测工艺卡:
无损检测工艺卡根据设计图样和本标准编制,满足石油天然气相关法规、标准的要求。
无损检测工艺卡由无损检测中级(Ⅱ级)及以上人员编制,无损检测责任工程师审核。
无损检测工艺卡修订更改时也应履行上述程序。
4.4检测人员
从事无损检测的人员必须持有国家有关部门颁发的并与其工作相适应的资格证书。
4.5无损检测责任人员的职责
4.5.1无损检测责任工程师有责任保证本标准在使用中的正确实施。
4.5.2无损检测责任工程师,应由具有无损检测高级或中级资格的人员担任。
5射线检测
本部分规定了射线检测技术与质量分级的要求。
6辐射防护
6.1放射卫生防护应符合GB18871,GB16357和GB18465的有关规定。
6.2现场进行x射线照相检测时,应采用剂量测试设备测定环境的辐射剂量,按GB16357的规定划定控制区和管理区,设置警告标志。
6.3现场进行7射线照相检测时,应采用剂量测试设备测定环境的辐射剂量,按GB18465的规定划定控制区和管理区,设置警告标志。
6.4现场检测时,射线检测人员应佩戴个人剂量计。
7射线检测人员
射线检测人员除应符合4.4的有关规定外,还应符合以下要求。
7.1射线检测人员的健康状况应符合GB18871的有关规定,上岗前应按GB11924的规定进行辐射安全知识的培训。
7.2射线检测工作人员的视力必须满足下列要求:
a)校正视力不得低于5.0(小数记录值为1.0),测试方法应符合GB11533的规定。
b)从事射线评片人员应能辨别距离400mm远的一组高为0.5mm、间距为0.5mm的印刷字母,并一年检查一次。
8射线检测设备、器材和材料
8.1射线源和能量的选择
8.1-1X射线照相应尽量选用较低的管电压。
透照不同厚度焊缝时,允许使用的最高管电压应控制在图3的范围内。
在透照截面厚度变化大的工件时,允许采用超过图3规定的X射线管电压,但最高不得超过50kV。
8.1.2γ射线源的最小透照厚度见表1。
8.2胶片和增感屏
8.2.1胶片:
a)射线胶片分为T1,T2,T3,T4四类。
T1为最高类别,T4为最低类别。
b)在满足灵敏度要求的情况下,一般x射线选用T3类型胶片。
γ射线选用T2或T3型胶片。
8.2.2增感屏
a)采用铅增感屏或不用增感屏。
增感屏的表面应保持洁净和平整。
增感屏的选用见表2。
b)在透照过程中胶片和增感屏应始终紧密接触。
8.3像质计
8.3.1采用线型金属丝像质计,其型号和规格应符合JB/T7902的规定。
图3透照厚度和允许使用的最高管电压
表1γ射线源的最小透照厚度
γ射线源
最小透照厚度TA
mm
名称
平均能量
MeV
Se75
0.206
≥5
Irl92
0.350
≥10
表2增感屏的选用
射线种类
增感屏材料
前屏厚度
mm
后屏厚度
mm
≤400kV,X射线,Se75
铅
0.03~0.10
0.03~0.10
Irl92
铅
0.10~0.20
0.10~0.20
8.3.2像质计的选用
a)按透照厚度TA选择表3规定的像质指数。
按表4确定像质计型号,但钢管环缝的外径小于或等于89mm时,应采用GB/T3323-1987中图E的等丝专用像质计。
b)透照厚度TA按表5计算。
8.3.3像质计的放置:
a)像质计应放在射线源一侧的工件表面上,中心钢丝处于一次透照长度的1/4位置,钢丝横跨且垂直于焊缝,细丝置于外侧。
b)当对环缝作中心周向曝光时,像质计应放在内壁,每隔90°放一个。
c)双壁单影透照时,像质计应放于受检部位的内壁,具体部位与a)同。
d)对于管道环缝像质计无法在射线源侧放置,允许放在胶片侧,但像质计指数应提高一级,使实测像质指数达到表3的要求。
e)对外径小于或等于89mm的钢管环缝进行双壁双影透照时.像质计应放置于射线源测被检焊缝有效透照区中心部位。
8.3.4像质计的识别:
在焊缝影像上,如能清楚地看到长度不小于10mm(焊缝宽度小于10mm的除外)的像质计钢丝影像,就认为是可识别的。
专用像质计应能识别不少于二两根金属丝。
8.4无用射线和散射线的屏蔽
8.4.1为减少散射线的影响,应采用适当的屏蔽方法限制受检部位的照射面积.以减少前方散射线。
当工件与地面较近时,可采用加厚增感屏的后屏厚度或在暗袋后加薄铅板等,以减少后方散射线。
8.4.2为检查背散射,可在暗盒背面贴附一个“B”的铅字标记,一般B铅字的高度为13mm,厚度为1.6mm。
若在较黑背景上出现“B”的较淡影像,说明背散射线防护不够,应采取有效措施重照。
如在较淡背景上出现“B”的较黑影像,则不作为该底片判废的依据。
表3像质计灵敏度值
透照厚度TA
mm
要求达到的像质指数Z
线直径
mm
透照厚度n
mm
要求达副的
像质指数Z
线直径
mm
≤6
15
0.125
>20~25
10
0.400
>6~8
14
0.160
>25~32
9
0.500
>8~12
13
0.200
>32~50
8
0.630
>12~16
12
0.250
>50~80
7
0.800
>16~20
11
0.320
>80~120
6
1.000
表4像质计型号的选用
像质计型号
10/16
6/12
透照厚度
mm
≤16
>16~80
注:
对于双壁单影透照确定像质计的型号时,一般按透照部位的厚度计。
表5焊缝的母材厚度和透照厚度
母材厚度
焊缝余高
透照厚度TA
mm
单层透照
双层透照(含双壁单影)
T
无
T
T×2
T
单面
T+2
T×2+2
T
双面
T+4
T×2+4
注:
焊缝两侧母材厚度不同时。
以薄板计。
8.5识别系统
8.5.1识别系统由定位标记和识别标记构成。
8.5.2定位标记:
焊缝透照定位标记包括搭接标记(十)和中心标记(车呻。
当铅质搭接标记用英文字母或数字表示时,可不用中心标记。
8.5.3识别标记:
识别标记包括工程编号、桩号、焊缝编号(焊口号)、部位编号(片号)、施工单位代号、板厚、透照日期等。
返修部位还应有返修标记R1,R2……(其脚码表示返修次数)。
8.5.4标记位置:
上述定位标记和识别标记均需在底片适当位置显示,并离焊缝边缘至少5mm。
搭接标记均放于胶片侧;当管径小于或等于89mm时,底片上至少应有工程编号、焊缝编号、部位编号和返修部位。
工件表面的定位标记,通常沿介质流动方向从平焊位置顺时针用记号笔划定。
8.6观片灯和评片室
8.6.1观片灯:
观片灯的亮度至少应观察到黑度为4.0的底片,且观察的漫射光亮度可调。
对不需要观察或透光量过强的部分应采用遮光板以屏蔽强光。
8.6.2评片室:
评片一般应在专用评片室进行。
室内的光线应暗且柔和。
8.7黑度计和比较黑度片
采用数字显示型式的黑度计,黑度计误差应不超过±0.05。
所使用的标准黑度片至少应2年送国家指定的计量单位检定一次。
9表面状态
焊缝及热影响区的表面质量(包括余高高度)应经外观检查合格。
表面的不规则状态在底片上的影像应不掩盖焊缝中的缺欠或与之相混淆,否则应做适当的修整。
10射线检测技术
10.1透照方式
按射线源、工件和胶片之间的相互位置,管道环缝主要采用中心透照、双壁单影透照和双壁双影透照三种方式,见图4。
只要实际可行,优先采用单壁透照方式;当单壁透照方式不可行时,方可采用双壁透照方式。
10.2几何条件
10.2.1射线源至被检部位工件表面的距离应满足式
(1):
L1≥l0dL22/3。
……………………………………
(1)
式中:
L1——射线源至被检部位工件表面的距离(或称透照距离),mm;
d——焦点尺寸(方焦点取边长,长焦点取长短边之和的1/2),mm;
L2——被检部位工件表面至胶片的距离,mm。
10.2.2采用源在内中心周向曝光时,只要得到的底片质量满足黑度和灵敏度要求,L,值可以减小,但减小最多不超过规定值的50%。
10.2.3分段透照的次数:
每次透照所检测的焊缝长度称为一次透照长度L3,通常一次透照长度L3除满足几何不清晰度的要求外,还应满足透照厚度比K小于或等于1.1的要求。
但下述情况除外:
a)外径D小于或等于89mm钢管对接焊缝采用双壁双影透照,焦距不得少于600mm,射线束的方向应满足上下焊缝的影像在底片上呈椭圆形显示,焊缝投影内侧间距以3mm~10mm为宜,最大间距不超过15mm。
透照次数一般应不少于两次,即椭圆显示应在互相垂直的方向各照一次;当上下焊缝椭圆显示有困难时,可做垂直透照,透照不少于三次,互成120°。
b)对于公称直径小于250mm的管道环缝双壁单影透照时,K值和一次透照长度可适当放宽,但整圈焊缝的透照次数应符合下列要求:
1)当射线源在钢管外表面的距离小于或等于15mm时,可分为不少于三段透照,互成120°。
2)当射线源在钢管外表面的距离大于15mm时,可分为不少于四段透照,互成90°。
ll曝光量和曝光曲线
11.1曝光量
11.1.1X射线照相,当焦距为700mm时,曝光量的推荐值不小于15mA·min(小于或等于89mm
管对接焊缝除外)。
当焦距改变时,可按平方反比定律对曝光量进行换算。
11.1.2采用7射线源透照时,曝光时间不小于输送源往返所需时间的10倍。
11.2曝光曲线
11.2.1应根据设备、胶片和增感屏等具体条件制做或选用合适的曝光曲线,并以此选择曝光规范。
11.2.2对使用中的曝光曲线,每年至少应校验一次。
射线设备更换重要部件或大修理后应及时对曝光曲线进行校验或重新制作。
12胶片处理
12.1胶片的处理应按胶片说明书进行。
处理方式分为自动冲洗和手工冲洗,推荐采用自动冲洗方式处理。
12.2自动冲洗按照自动洗片机操作说明书进行。
自动冲洗时,应准确调节显影温度和冲洗周期。
a)中心透照法
b)双壁单影透照法
L1-射线源至透照部位工件表面的距离;L2一透照部位工件表面至胶片的距离。
c)双壁双影透照法
图4透照方式示意图
表6底片的黑度范围
射线种类
底片黑度D
X射线
1.5~4.()
γ射线
1.8~4.()
注:
底片有效评定区域内的黑度。
用搭接标记处焊缝的黑度和中心处热影响区的黑度表示。
13底片评定
13.1评片要求
13.1.1底片的评定应由Ⅱ级或Ⅱ级以上人员进行。
13.1.2底片的评定应在评片室进行。
评片室和观片灯应符合8.6的规定。
13.1.3黑度计和比较黑度片应符合8.7的规定。
13.2底片的质量
13.2.1底片黑度(包括胶片本身的灰雾度D0≤O.3)。
底片有效评定区域内的黑度应符合表6的规定。
13.2.2底片上的像质计和识别系统齐全,位置准确,且不得掩盖受检焊缝的影像。
13.2.3底片上至少应识别出表3规定的像质指数,且像质指数的识别应符合8.3.4的规定。
13.2.4底片有效评定区域内不得有胶片处理不当或其他妨碍底片准确评定的伪像(如水迹、划伤、指纹、脏物、皱折等)。
13.3评定
底片质量应符合13.2的要求,按第14章评定。
14射线检测质量分级
14.1质量分级的依据
根据存在缺欠的性质和数量,将对接接头分为四个等级:
a)I级内不允许存在裂纹、未熔合、未焊透、条状夹渣、烧穿和内咬边。
b)Ⅱ级内不允许存在裂纹、外表面未熔合和黑度大于或等于较薄侧母材黑度的烧穿。
c)Ⅲ级内不允许存在裂纹、外表面未熔合。
d)Ⅳ级为超过Ⅲ级者。
14.2缺欠的分级
14.2.1圆形缺欠的分级:
a)长宽比小于或等于3的缺欠定义为圆形缺欠。
他们可以是圆形、椭圆形、锥形或带有尾巴(在测定尺寸时应包括尾部)等不规则形状,包括气孔、夹渣和夹钨。
b)圆形缺欠用评定区进行评定,评定区域的大小见表7。
评定区框线的长边要与焊缝平行。
框线内必须包含最严重区域的主要缺欠。
与框线外切的不计点数,相割的计人点数。
c)评定圆形缺欠时,应将缺欠尺寸按表8换算成缺欠点数。
d)不记点数的缺欠尺寸见表9。
e)圆形缺欠的分级见表10。
f)圆形缺欠长径大于T/2时,评为Ⅳ级。
表7缺欠评定区
母材厚度,mm
≤25
>25~50
评定区尺寸,mm×mm
10×10
10×20
表8缺久点数换算表
缺久长径,mm
≤1
>1~2
>2~3
>3~4
>4~6
>6~8
>8
点数
1
2
3
6
10
15
25
g)工级对接接头和母材厚度小于或等于5mm的Ⅱ级对接接头内不计点数的圆形缺欠,在评定区内多于10点降一级。
h)底片上黑度较大的缺欠,如确认为柱孔或针孔缺欠,应评为Ⅳ级。
表9不计点数的缺久尺寸
母材厚度T
mm
缺欠长度
mm
≤25
≤0.5
>25~50
≤0.7
14.2.2条状夹渣的分级:
a)长宽比大于3的夹渣定义为条状夹渣(包括条孔)。
b)条状夹渣的质量分级见表11和表12。
表10圆形缺久分级
评定区,mm×mm
10×10
10×20
母材厚度,mm
2~5
>5一15
>15~25
>25~50
等级
I
1
2
3
4
Ⅱ
3
6
9
12
Ⅲ
6
12
18
24
Ⅳ
缺欠点数大于Ⅲ级者
表11外径大于89mm管道对接接头条状夹渣的质量分级
质量级别
缺欠宽度
mm
单个缺欠长度
mm
缺欠总长度
Ⅱ
≤2
≤T/3
最小可为10
任何连续300mm的焊缝长度内,其累计长度不得超过25mm
Ⅲ
≤2T/3
最小可为15
任何连续300mm的焊缝长度内,其累计长度不得超过50mm
Ⅳ
大于Ⅲ级者
表12外径小于等于89mm管道对接接头条状夹渣的质量分级
质量级别
缺欠宽度
mm
单个缺欠长度
mm
缺欠总长度
Ⅱ
≤2
≤T
最小可为8
圆周的5%,但最小可为12mm
Ⅲ
≤2T
最小可为13
圆周的8%,但最小可为20mm,最大不超过25mm
Ⅳ
大于Ⅲ级者
表13外径大于89mm管道对接接头根部未熔合的质量分级
质量级别
单个缺欠长度
mm
缺欠总长度
Ⅱ
≤10
任何连续300mm的焊缝长度内,其累计长度不得超过20mm
Ⅲ
≤12.5
任何连续300mm的焊缝长度内,其累计长度不得超过25mm
Ⅳ
大于Ⅲ级者
表14外径小于等于89mm管道对接接头根部未熔合的质量分级
质量级别
单个缺欠长度
mm
缺欠总长度
Ⅱ
≤5
圆周的5%,但最大不超过10mm
Ⅲ
≤7.5
圆周的8%,但最大不超过15mm
Ⅳ
大于Ⅲ级者或缺欠的射线影像黑度超过相邻较薄侧母材黑度者
14.2.3根部未熔合、夹层未熔合的质量分级:
a)根部未熔合的质量分级见表13和表14。
b)夹层未熔合的质量分级:
1)外径大于89mm管道对接接头夹层未熔合的质量分级与中间未焊透质量分级相同。
2)外径小于或等于89mm管道对接接头夹层未熔合的质量分级与表14相同。
14.2.4未焊透的质量分级见表15、表16和表17。
表15中间未焊透质量分级
质量级别
单个缺欠长度
mm
缺欠总长度
Ⅱ
≤12.5
任何连续300mm的焊缝长度内,其累计长度不得超过25mm
Ⅲ
≤25
任何连续300mm的焊缝长度内,其累计长度不得超过50mm
Ⅳ
大于Ⅲ级者或缺欠的射线影像黑度超过相邻较薄侧母材黑度者
表16根部未焊透和错边未焊透的质量分级
质量级别
根部未焊透
错边未焊透
单个缺欠长度
mm
缺欠总长度
单个缺欠长度
mm
缺欠总长度
Ⅱ
≤10
任何连续300mm的焊缝长度
内,其累计长度不得超过20mm
≤25
任何连续300mm的焊缝长度内,其累计长度不得超过50mm
Ⅲ
≤12.5
任何连续300mm的焊缝长度
内,其累计长度不得超过25mm
≤50
任何连续300mm的焊缝长度
内,其累计长度不得超过75mm
Ⅳ
大于Ⅲ级者或根部未焊透的射线影像黑度超过相邻较薄侧母材黑度者
表17外径小于等于89mm管道对接接头根部未焊透的质量分级
质量级别
单个缺欠长度
mm
连续或断续未焊透总长度占圆周总长度的百分比
Ⅱ
12
≤10%,且不大于18mm
Ⅲ
25
≤15%,且不大于25mm
Ⅳ
大于Ⅲ级者或缺欠的射线影像黑度超过相邻较薄侧母材黑度者
14.2.5内凹的质量分级:
内凹的影像黑度小于或等于较薄侧母材黑度时,长度不计,可评为工级;
内凹的影像黑度大于较薄侧母材黑度时,按表18和表19评定。
14.2.6烧穿的质量分级见表20。
14.2.7内咬边的质量分级见表21和表22。
14.2.8综合评级:
任何连续300mm的焊缝长度中,Ⅱ级对接接头内条状夹渣、未熔合(根部未熔合和夹层未熔合)及未焊透(根部未焊透或中间未焊透)的累计长度不超过35mm;Ⅲ级对接接头内条状夹渣、未熔合(根部未熔合和夹层未熔合)及未焊透(根部未焊透或中间未焊透)的累计长度不超过50mm。
15射线检测报告
射线检测报告至少应包括:
被检管线情况(工程编号、规格、材质、桩号、焊口编号等)、检测条件及工艺(仪器、胶片、增感方式、透照方式、检测标准等)、报告人(级别)、审核人(级别)、检测结论、报告日期及检测单位盖章等。
报告格式参见附录G。
表18外径大于89mm管道对接接头内凹的质量分级
质量级别
单个缺欠长度
mm
缺欠总长度
Ⅱ
≤25
任何连续300mm的焊缝长度内,其累计长度不得超过50mm
Ⅲ
≤50
任何连续300mm的焊缝长度内,其累计长度不得超过75mm
Ⅳ
大于Ⅲ级者
表19外径小于等于89mm管道对接接头内凹的质量分级
质量级别
连续或断续内凹总长度占圆周总长度的百分比
Ⅱ
≤15%,且不大于25mm
Ⅲ
≤20%,