机械设计与制造毕业论文定稿版.docx
《机械设计与制造毕业论文定稿版.docx》由会员分享,可在线阅读,更多相关《机械设计与制造毕业论文定稿版.docx(15页珍藏版)》请在冰豆网上搜索。
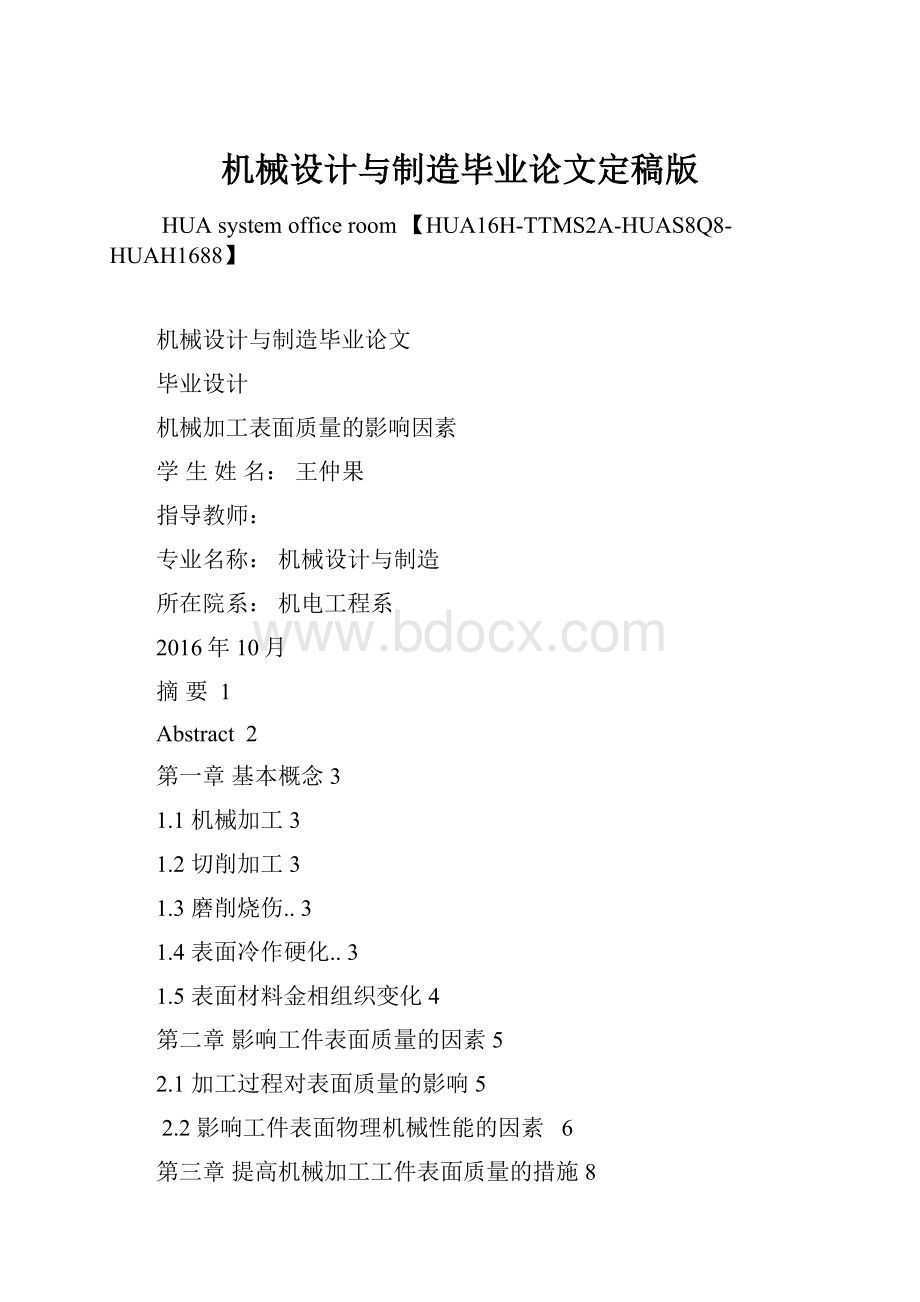
机械设计与制造毕业论文定稿版
HUAsystemofficeroom【HUA16H-TTMS2A-HUAS8Q8-HUAH1688】
机械设计与制造毕业论文
毕业设计
机械加工表面质量的影响因素
学生姓名:
王仲果
指导教师:
专业名称:
机械设计与制造
所在院系:
机电工程系
2016年10月
摘要1
Abstract2
第一章基本概念3
1.1机械加工3
1.2切削加工3
1.3磨削烧伤..3
1.4表面冷作硬化..3
1.5表面材料金相组织变化4
第二章影响工件表面质量的因素5
2.1加工过程对表面质量的影响5
2.2影响工件表面物理机械性能的因素6
第三章提高机械加工工件表面质量的措施8
3.1刀具方面8
3.2工件材料方面8
3.3切削条件方面8
3.4加工方法方面8
第四章机械加工表面质量对零件使用性能的影响10
4.1表面质量对零件耐磨性的影响10
4.2表面质量对零件疲劳强度的影响10
4.3表面质量对零件耐腐蚀性能的影响10
4.4表面质量对零件间配合性质的影响11
4.5表面质量对零件其他性能的影响11
第五章结论12
致谢13
参考文献14
摘要
部分的机械设备零件的破坏,总是从零件表面开始的。
产品的性能,特别是它的可靠性和耐久度,在很大程度上取决于零件表面层的质量。
研究机械加工表面质量,其目的就是为了掌握机械加工中各个工艺对加工表面质量影响的规律,以便利用这些规律来控制加工过程,最终达到改善产品质量、增强产品使用性能的目的。
随着工业技术的飞速发展,机器的使用要求越来越高,一些重要零件在高压力、高速、高温等高要求条件下工作,表面层的任何缺陷,不仅直接影响零件的工作性能,而且还可能引起应力集中、应力腐蚀等现象,将进一步加速零件的失效,这一切都与加工表面质量有很大关系。
因而表面质量问题越来越受到各方面的重视。
一台机器在正常的使用过程中,由于其零件的工作性能逐渐变坏,以致不能继续使用,有时甚至会突然损坏。
其原因除少数是因为设计不周而强度不够,或偶然事故引起了超负荷以外,大多数是由于磨损、受到外界介质的腐蚀或疲劳破坏。
磨损、腐蚀和疲劳损坏都是发生在零件的表面,或是从零件表面开始的。
因此,加工表面质量将直接影响到零件的工作性能,尤其是它的可靠性和寿命。
本文对机械加工表面质量进行了分析,指出了影响机械加工表面质量的因素,并提出了提高机械加工表面质量的措施,对工程实践有一定的指导作用。
而且,正确地理解零件表面质量内涵,分析机械加工过程中影响加工表面质量的各种工艺因素,通过改变这些因素从而改善工件表面质量,提高产品的使用性能及对未来机械行业的发展具有重要的意义。
关键词表面质量,粗糙度,机械性能,切削参数
Abstract
Partofthemachineryandequipmentpartsdamage,alwaysstartfromthepartsofthesurface.Productperformance,especiallythereliabilityanddurabilityofitsquality,toalargeextentdependsonthepartsurfacelayer.Studyonthesurfacequalityofmachining,thepurposeistograspthevariousmachiningprocessonthemachiningsurfacequalityofthelaw,inordertousetheserulestocontroltheprocess,ultimatelyimprovetheproductquality,increaseproductperformance.Withtherapiddevelopmentofindustrialtechnology,requiresthatthemachineisusedmoreandmorehigh,someimportantpartsinhighpressure,highspeed,hightemperature,highrequirements,anydefectsonthesurfacelayer,notonlydirectlyaffecttheperformanceofparts,butalsomaycausestressconcentration,stresscorrosion,willfurtheracceleratethepartsfailure,allthishasmuchtodowiththequalityofthemachinedsurface.Thusthesurfacequalityproblemsbecomemoreandmoreimportant.Amachineinnormalusageprocess,theworkingperformanceofthepartgraduallydeteriorated,sothatcannotcontinuetouse,andsometimeseventhesuddendamage.Thereasonisbecausethedesignisnotinafewweeksandthestrengthisnotenough,oraccidentcausedbyoverload,mostlyduetowear,corrosionordamagetheexternalmediumfatigue.Wear,corrosionandfatiguedamageoccursinpartsofthesurface,orfrompartsofthesurface.Therefore,themachinedsurfacequalitywilldirectlyaffecttheperformanceofparts,especiallyitsreliabilityandlifetime.Basedontheanalysisofthemachiningsurfacequality,pointedoutthefactorsinfluencingthesurfacequalityofmachining,andproposestoimprovethemachinedsurfacequalitymeasures,therearesomeguidanceforengineeringpractice.Moreover,thecorrectunderstandingofthecontentofthesurfacequalityofparts,varioustechnologicalfactorsaffectingsurfacequalityanalysisofmachiningprocess,bychangingthesefactorssoastoimprovethequalityoftheworkpiecesurface,improvetheperformanceofproductsandplaysanimportantroleinthefuturedevelopmentofmachineryindustry.
Keywordsurfacequality,surfaceroughness,mechanicalproperties,cuttingparameters
第一章基本概念
1.1机械加工
机械加工:
广意的机械加工就是凡能用机械手段制造产品的过程;狭意的是用车床、铣床、钻床、磨床、冲压机、压铸机等专用机械设备制作零件的过程。
1.2切削加工
刀具几何形状的复映刀具相对于工件作进给运动时,在加工表面留下了切削层残留面积,其形状是刀具几何形状的复映。
减小进给量、主偏角、副偏角以及增大刀尖圆弧半径,均可减小残留面积的高度。
此外,适当增大刀具的前角以减小切削时的塑性变形程度,合理选择润滑液和提高刀具刃磨质量以减小切削时的塑性变形和抑制刀瘤、鳞刺的生成,也是减小表面粗糙度值的有效措施。
工件材料的性质。
加工塑性材料时,由刀具对金属的挤压产生了塑性变形,加之刀具迫使切屑与工件分离的撕裂作用,使表面粗糙度值加大。
工件材料韧性愈好,金属的塑性变形愈大,加工表面就愈粗糙。
加工脆性材料时,其切屑呈碎粒状,由于切屑的崩碎而在加工表面留下许多麻点,使表面粗糙。
磨削加工影响表面粗糙度的因素。
正像切削加工时表面粗糙度的形成过程一样,磨削加工表面粗糙度的形成也是由几何因素和表面金属的塑性变形来决定的。
影响磨削表面粗糙的主要因素有:
砂轮的粒度、砂轮的硬度、砂轮的修整磨削速度、磨削径向进给量与光磨次数工件圆周进给速度与轴向进给量冷却润滑液。
影响加工表面层物理机械性能的因素。
在切削加工中,工件由于受到切削力和切削热的作用,使表面层金属的物理机械性能产生变化,最主要的变化是表面层金属显微硬度的变化、金相组织的变化和残余应力的产生。
由于磨削加工时所产生的塑性变形和切削热比刀刃切削时更严重,因而磨削加工后加工表面层上述三项物理机械性能的变化会很大。
1.3磨削烧伤
磨削烧伤:
在磨削加工中,由于多数磨粒为负前角切削,磨削温度很高,产生的热量远远高于切削时的热量,而且磨削热有60~80%传给工件,所以极容易出现金相组织的转变,使得表面层金属的硬度和强度下降,产生残余应力甚至引起显微裂纹,这种现象称为磨削烧伤。
1.4表面冷作硬化
冷作硬化:
通过冷加工而是零件表面产生的表面应力,使零件的表面比加工前的表面硬度耐磨性等有所提高。
冷作硬化及其评定参数。
机械加工过程中因切削力作用产生的塑性变形,使品
格扭曲、畸变,晶粒间产生剪切滑移,品粒被拉长和纤维化,甚至破碎,这些都会使表面层金属的硬度和强度提高,这种现象称为冷作硬化(或称为强化)。
表面层金属强化的结果,会增大金属变形的阻力,减小金属的塑性,金属的物理性质也会发生变化。
被冷作硬化的金属处于高能位的不稳定状态,只要一有可能,金属的不稳定状态就要向比较稳定的状态转化,这种现象称为弱化。
弱化作用的大小取决于温度的高低、温度持续时间的长短和强化程度的大小。
由于金属在机械加工过程中同时受到力和热的作用,因此,加工后表层金属的最后性质取决于强化和弱化综合作用的结果。
影响冷作硬化的主要因素。
切削刃钝圆半径增大,对表层金属的挤压作用增强,塑性变形加剧,导致冷硬增强。
刀具后刀面磨损增大,后刀面与被加工表面的摩擦加剧,塑性变形增大,导致冷硬增强。
切削速度增大,刀具与工件的作用时间缩短,使塑性变形扩展深度减小,冷硬层深度减小。
切削速度增大后,切削热在工件表面层上的作用时间也缩短,将使冷硬程度增加。
进给量增大,切削力也增大,表层金属的塑性变形加剧,冷硬作用加强。
工件材料的塑性愈大,冷硬现象就愈严重。
1.5表面材料金相组织变化
当被磨工件表面层温度达到相变温度以上时,表层金属发生金相组织的变化,使表层金属强度和硬度降低,并伴有残余应力产生,甚至出现微观裂纹,这种现象称为磨削烧伤。
在磨削淬火钢时,可能产生以下三种烧伤:
回火烧伤:
如果磨削区的温度未超过淬火钢的相变温度,但已超过马氏体的转变温度,工件表层金属的回火马氏体组织将转变成硬度较低的回火组织(索氏体或托氏体),这种烧伤称为回火烧伤。
淬火烧伤:
如果磨削区温度超过了相变温度,再加上冷却液的急冷作用,表层金属发生二次淬火,使表层金属出现二次淬火马氏体组织,其硬度比原来的回火马氏体的高,在它的下层,因冷却较慢,出现了硬度比原先的回火马氏体低的回火组织(索氏体或托氏体),这种烧伤称为淬火烧伤。
退火烧伤:
如果磨削区温度超过了相变温度,而磨削区域又无冷却液进入,表层金属将产生退火组织,表面硬度将急剧下降,这种烧伤称为退火烧伤。
改善磨削烧伤的途径:
磨削热是造成磨削烧伤的根源,故改善磨削烧伤由两个途径:
一是尽可能地减少磨削热地产生;二是改善冷却条件,尽量使产生地热量少传入工件。
正确选择砂轮;合理选择切削用量;改善冷却条件。
第二章影响工件表面质量的因素
2.1加工过程对表面质量的影响
1.工艺系统的振动对工件表面质量的影响
在机械加工过程中工艺系统有时会发生振动,即在刀具的切削刃与工件上正在切削的表面之间除了名义上的切削运动之外,还会出现一种周期性的相对运动。
振动使工艺系统的各种成形运动受到干扰和破坏,使加工表面出现振纹,增大表面粗糙度值,恶化加工表面质量。
2.刀具几何参数、材料和刃磨质量对表面质量的影响
刀具的几何参数中对表面粗糙度影响最大主要是副偏角、主偏角、刀尖圆弧半径。
在一定的条件下,减小副偏角、主偏角、刀尖圆弧半径都可以降低表面粗糙度。
在同样条件下,硬质合金刀具加工的表面粗糙度值低于高速钢刀具,而金刚石、立方氮化硼刀具又优于硬质合金,但由于金刚石与铁族材料亲和力大,故不宜用来加工铁族材料。
另外,刀具的前、后刀面、切削刃本身的粗糙度直接影响加工表面的粗糙度,因此,提高刀具的刃磨质量,使刀具前后刀面、切削刃的粗糙度值应低于工件的粗糙度值的1~2级。
3.切削液对表面质量的影响
切削液的冷却和润滑作用能减小切削过程中的界面摩擦,降低切削区温度,使切削层金属表面的塑性变形程度下降,抑制积屑瘤和鳞刺的产生,在生产中对于不同材料合理选用切削液可大大减小工件表面粗糙度。
4.工件材料对表面质量的影响
工件材料的性质;加工塑性材料时,由刀具对金属的挤压产生了塑性变形,加之刀具迫使切屑与工件分离的撕裂作用,使表面粗糙度值加大。
工件材料韧性越好,金属的塑性变形越大,加工表面就愈越粗糙。
加工脆性材料时其切屑呈碎粒状,由于切屑的崩碎而在加工表面留下许多麻点使表面粗糙。
一般韧性较大的塑性材料,加工后表面粗糙度较大,而韧性较小的塑性材料,加工后易得到较小的表面粗糙度。
对于同种材料,其晶粒组织越大,加工表面粗糙度越大。
因此,为了减小加工表面粗糙度,常在切削加工前对材料进行调质或正火处理,以获得均匀细密的晶粒组织和较高的硬度。
5.切削条件对工件表面质量的影响
与切削条件有关的工艺因素,包括切削用量、冷却润滑情况。
中、低速加工塑性材料时,容易产生积屑瘤和鳞刺,所以,提高切削速度,可以减少积屑瘤和鳞刺,减小零件已加工表面粗糙度值;对于脆性材料,一般不会形成积屑瘤和鳞刺,所以,切削速度对表面粗糙度基本上无影响。
进给速度增大,塑性变形也增大,表面粗糙度值增大,所以,减小进给速度可以减小表面粗糙度值,但是,进给量减小到一定值时,粗糙度值不会明显下降。
正常切削条件下,切削深度对表面粗糙度影响不大,因此,机械加工时不能选用过小的切削深度。
6.切削速度对表面粗糙度的影响
一般在粗加工选用低速车削,精加工选用高速车削可以减小表面粗糙度。
在中速切削塑性材料时,由于容易产生积屑瘤,且塑性变形较大,因此加工后零件表面粗糙度较大。
通常采用低速或高速切削塑性材料,可有效地避免积屑瘤的产生,这对减小表而粗糙度有积极作用。
7.磨削加工对表面质量的影响
(1).砂轮的影响砂轮的粒度越细,单位面积上的磨粒数越多,在磨削表面的刻痕越细,表面粗糙度越小;但若粒度太细,加工时砂轮易被堵塞反而会使表面粗糙度增大,还容易产生波纹和引起烧伤。
砂轮的硬度应大小合适,其半钝化期愈长愈好;砂轮的硬度太高,磨削时磨粒不易脱落,使加工表面受到的摩擦、挤压作用加剧,从而增加了塑性变形,使得表面粗糙度增大,还易引起烧伤;但砂轮太软,磨粒太易脱落,会使磨削作用减弱,导致表面粗糙度增加,所以要选择合适的砂轮硬度。
砂轮的修整质量越高,砂轮表面的切削微刃数越多、各切削微刃的等高性越好,磨削表面的粗糙度越小。
(2).磨削用量的影响增大砂轮速度,单位时间内通过加工表面的磨粒数增多,每颗磨粒磨去的金属厚度减少,工件表面的残留面积减少;同时提高砂轮速度还能减少工件材料的塑性变形,这些都可使加工表面的表面粗糙度值降低。
降低工件速度,单位时间内通过加工表面的磨粒数增多,表面粗糙度值减小;但工件速度太低,工件与砂轮的接触时间长,传到工件上的热量增多,反面会增大粗糙度,还可能增加表面烧伤。
增大磨削深度和纵向进给量,工件的塑性变形增大,会导致表面粗糙度值增大。
径向进给量增加,磨削过程中磨削力和磨削温度都会增加,磨削表面塑性变形程度增大,从而会增大表面粗糙度值。
为在保证加工质量的前提下提高磨削效率,可将要求较高的表面的粗磨和精磨分开进行,粗磨时采用较大的径向进给量,精磨时采用较小的径向进给量,最后进行无进给磨削,以获得表面粗糙度值很小的表面。
另外,由于磨削温度高,合理使用切削液既可以降低磨削区的温度,减少烧伤,还可以冲去脱落的磨粒和切屑,避免划伤工件,从而降低表面粗糙度值。
2.2影响工件表面物理机械性能的因素
1.表面层冷作硬化。
切削刃钝圆半径增大,对表层金属的挤压作用增强,塑性变形加剧,导致冷硬增强。
刀具后刀面磨损增大,后刀面与被加工表面的摩擦加剧,塑性变形增大,导致冷硬增强。
切削速度增大,刀具与工件的作用时间缩短,使塑性变形扩展深度减小,冷硬层深度减小。
切削速度增大后,切削热在工件表面层上的作用时间也缩短了,将使冷硬程度增加。
进给量增大,切削力也增大,表层金属的塑性变形加剧,冷硬作用加强。
工件材料的塑性愈大,冷硬现象就愈严重。
2.表面层材料金相组织变化。
当切削热使被加工表面的温度超过相变温度后,表层金属的金相组织将会发生变化。
(1)磨削烧伤当被磨工件表面层温度达到相变温度以上时,表层金属发生金相组织的变化,使表层金属强度和硬度降低,并伴有残余应力产生甚至出现微观裂纹,这种现象称为磨削烧伤。
(2)改善磨削烧伤的途径磨削热是造成磨削烧伤的根源,故改善磨削烧伤由两个途径:
一是尽可能地减少磨削热的产生;二是改善冷却条件,尽量使产生的热量少传入工件。
正确选择砂轮合
理选择切削用量改善冷却条件。
3.磨削表面层金相组织变化——磨削烧伤
(1).磨削表面层金相组织变化与磨削烧伤
机械加工过程中产生的切削热会使得工件的加工表面产生剧烈的温升,当温度超过工件材料金相组织变化的临界温度时,将发生金相组织转变。
在磨削加工中,由于多数磨粒为负前角切削,磨削温度很高,产生的热量远远高于切削时的热量,而且磨削热有60~80%传给工件,所以极容易出现金相组织的转变,使得表面层金属的硬度和强度下降,产生残余应力甚至引起显微裂纹,这种现象称为磨削烧伤。
产生磨削烧伤时,加工表面常会出现黄、褐、紫、青等烧伤色,这是磨削表面在瞬时高温下的氧化下膜颜色。
不同的烧伤色,表明工件表面受到的烧伤程度不同。
磨削淬火钢时,工件表面层由于受到瞬时高温的作用,将可能产生以下三种金相组织变化:
(2).如果磨削表面层温度未超过相变温度,但超过了马氏体的转变温度,这时马氏体将转变成为硬度较低的回火索氏体或索氏体,这叫回火烧伤。
如果磨削表面层温度超过相变温度,则马氏体转变为奥氏体,这时若无切削液,则磨削表面硬度急剧下降,表层被退火,这种现象称为退火烧伤。
干磨时很容易产生这种现象。
(3).如果磨削表面层温度超过相变温度,但有充分的切削液对其进行冷却,则磨削表面层将急冷形成二次淬火马氏体,硬度比回火马氏体高,不过该表面层很薄,只有几微米厚,其下为硬度较低的回火索氏体和索氏体,使表面层总的硬度仍然降低,称为淬火烧伤。
4.磨削烧伤的改善措施
(1).影响磨削烧伤的因素主要是磨削用量、砂轮、工件材料和冷却条件。
由于磨削热是造成磨削烧伤的根本原因,因此要避免磨削烧伤,就应尽可能减少磨削时产生的热量及尽量减少传入工件的热量。
具体可采用下列措施:
合理选择磨削用量;不能采用太大的磨削深度,因为当磨削深度增加时,工件的塑性变形会随之增加,工件表面及里层的温度都将升高,烧伤亦会增加;工件速度增加,磨削区表面温度会增高,但由于热作用时间减少,因而可减轻烧伤。
(2).工件材料工件材料对磨削区温度的影响主要取决于它的硬度、强度、韧性和热导率。
工件材料硬度、强度越高,韧性越大,磨削时耗功越多,产生的热量越多,越易产生烧伤;导热性较差的材料,在磨削时也容易出现烧伤。
(3).砂轮的选择硬度太高的砂轮,钝化后的磨粒不易脱落,容易产生烧伤,因此用软砂轮较好;选用粗粒度砂轮磨削,砂轮不易被磨削堵塞,可减少烧伤;结合剂对磨削烧伤也有很大影响,树脂结合剂比陶瓷结合剂容易产生烧伤,橡胶结合剂比树脂结合剂更易产生烧伤。
(4).冷却条件为降低磨削区的温度,在磨削时广泛采用切削液冷却。
为了使切削液能喷注到工件表面上,通常增加切削液的流量和压力并采用特殊喷嘴,并在砂轮上安装带有空气挡板的切削液喷嘴,这样既可加强冷却作用,又能减轻高速旋转砂轮表面的高压附着作用,使切削液顺利地喷注到磨削区。
此外,还可采用多孔砂轮、内冷却砂轮和浸油砂轮,切削液被引入砂轮的中心腔内,由于离心力的作用,切削液再经过砂轮内部的孔隙从砂轮四周的边缘甩出,这样切削液即可直接进入磨削区,发挥有效的冷却作用。
第三章提高机械加工工件表面质量的措施
通过前面的分析,我们知道影响表面粗糙度的因素有切削条件(切削速度、进给量、切削液)、刀具(几何参数、切削刃形状、刀具材料、磨损情况)、工件材料及热处理、工艺系统刚度和机床精度等几个方面。
在了解了影响表面粗糙度的因素之后,我们必须根据需要降低加工表面的粗糙度,改善机械加工的表面质量。
3.1刀具方面
在切削加工中,工件由于受到切削力和切削热的作用,使表面层金属的物理机械性能产生变化,最主要的变化是表面层金属显微硬度的变化、金相组织的变化和残余应力的产生。
由于磨削加工时所产生的塑性变形和切削热比刀刃切削时更严重,因而磨削加工后加工表面层上述三项物理机械性能的变化会很大。
为了减少残留面积,刀具应采用较大的刀尖圆弧半径、较小的副偏角或合适(=0)的修光刃或宽刃精刨刀、精车刀等。
选用与工件材料适应性好的刀具材料,避免使用磨损严重的刀具,这些均有利于减小表面粗糙度。
3.2工件材料方面
工件材料性质中,对加工表面粗糙度影响较大的是材料的塑性和金相组织。
对于塑性大的低碳钢、低合金钢材料,预先进行正火处理以降低塑性,切削加工后能得到较小的粗糙度。
工件材料应有适宜的金相组织(包括状态、晶粒度大小及分布)。
加工塑性材料时,由刀具对金属的挤压产生了塑性变形,加之刀具迫使切屑与工件分离的撕裂作用,使表面粗糙度值加大。
工件材料韧性愈好,金属的塑性变形愈大,加工表面就愈粗糙。
加工脆性材料时,其切屑呈碎粒状,由于切屑的崩碎而在加工表面留下许多麻点,使表面粗糙。
3.3切削条件方面
切削用量:
切削塑性材料时,采用高速切削,可减小切削变形,且可以抑制积屑瘤的产生,有利于减小表面粗糙度;切削脆性材料时,切削速度对表面粗糙度影响不大。
减小进给量f可降低残留面积高度,减小表面粗糙度。
但是,进给量f不能过小,否则刀刃由于切削厚度过小而无法切入工作,与工件发生强烈的挤压和摩擦,反而使粗糙度值增大。
以较高的切削速度切削塑性材料可抑制积屑瘤出现,减小