瓦线淀粉黏合剂的制备及常见问题分析.docx
《瓦线淀粉黏合剂的制备及常见问题分析.docx》由会员分享,可在线阅读,更多相关《瓦线淀粉黏合剂的制备及常见问题分析.docx(11页珍藏版)》请在冰豆网上搜索。
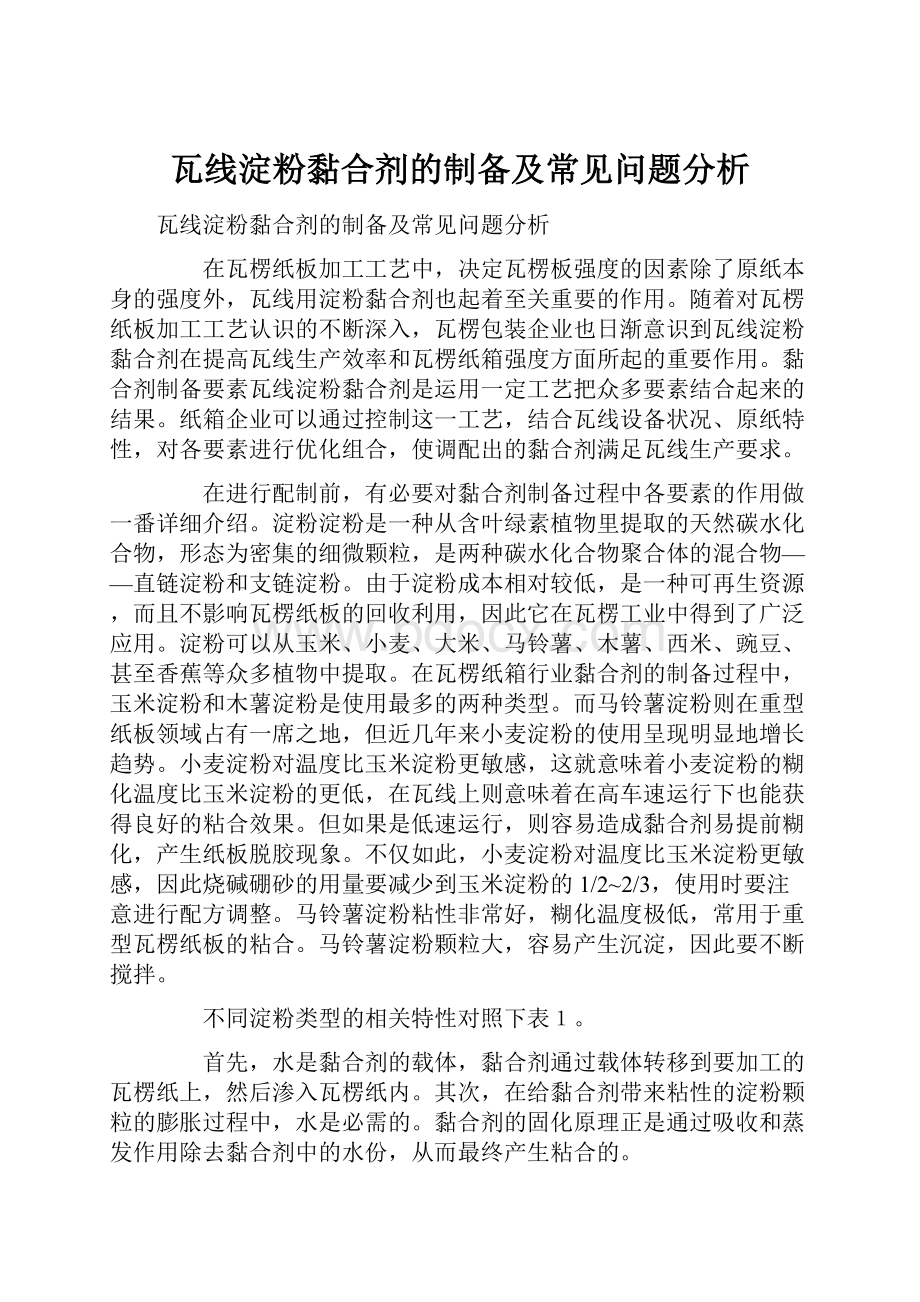
瓦线淀粉黏合剂的制备及常见问题分析
瓦线淀粉黏合剂的制备及常见问题分析
在瓦楞纸板加工工艺中,决定瓦楞板强度的因素除了原纸本身的强度外,瓦线用淀粉黏合剂也起着至关重要的作用。
随着对瓦楞纸板加工工艺认识的不断深入,瓦楞包装企业也日渐意识到瓦线淀粉黏合剂在提高瓦线生产效率和瓦楞纸箱强度方面所起的重要作用。
黏合剂制备要素瓦线淀粉黏合剂是运用一定工艺把众多要素结合起来的结果。
纸箱企业可以通过控制这一工艺,结合瓦线设备状况、原纸特性,对各要素进行优化组合,使调配出的黏合剂满足瓦线生产要求。
在进行配制前,有必要对黏合剂制备过程中各要素的作用做一番详细介绍。
淀粉淀粉是一种从含叶绿素植物里提取的天然碳水化合物,形态为密集的细微颗粒,是两种碳水化合物聚合体的混合物——直链淀粉和支链淀粉。
由于淀粉成本相对较低,是一种可再生资源,而且不影响瓦楞纸板的回收利用,因此它在瓦楞工业中得到了广泛应用。
淀粉可以从玉米、小麦、大米、马铃薯、木薯、西米、豌豆、甚至香蕉等众多植物中提取。
在瓦楞纸箱行业黏合剂的制备过程中,玉米淀粉和木薯淀粉是使用最多的两种类型。
而马铃薯淀粉则在重型纸板领域占有一席之地,但近几年来小麦淀粉的使用呈现明显地增长趋势。
小麦淀粉对温度比玉米淀粉更敏感,这就意味着小麦淀粉的糊化温度比玉米淀粉的更低,在瓦线上则意味着在高车速运行下也能获得良好的粘合效果。
但如果是低速运行,则容易造成黏合剂易提前糊化,产生纸板脱胶现象。
不仅如此,小麦淀粉对温度比玉米淀粉更敏感,因此烧碱硼砂的用量要减少到玉米淀粉的1/2~2/3,使用时要注意进行配方调整。
马铃薯淀粉粘性非常好,糊化温度极低,常用于重型瓦楞纸板的粘合。
马铃薯淀粉颗粒大,容易产生沉淀,因此要不断搅拌。
不同淀粉类型的相关特性对照下表1。
首先,水是黏合剂的载体,黏合剂通过载体转移到要加工的瓦楞纸上,然后渗入瓦楞纸内。
其次,在给黏合剂带来粘性的淀粉颗粒的膨胀过程中,水是必需的。
黏合剂的固化原理正是通过吸收和蒸发作用除去黏合剂中的水份,从而最终产生粘合的。
一般情况下,配制瓦线黏合剂的水要求使用洁净的自来水,有的工厂为了节省用水成本,也使用经过污水处理的循环水。
但使用循环水配制的黏合剂,稳定性会受到很大影响。
如果在两步法中使用,强烈建议仅限于在该工艺的第二步中使用,且一定要对循环水进行杀菌处理。
一步法制浆相对来讲对循环水的要求要低一些,但也一定要对循环水进行杀菌处理。
烧碱
烧碱的作用是使淀粉糊化而产生一定的粘性。
糊化是淀粉颗粒吸收热量并快速膨胀的过程,对确保粘合质量及粘合强度至关重要,淀粉的粘合性能即来自糊化过程。
糊化温度主要会受糊料中加入烧碱量的影响。
事实上不断加入烧碱甚至有可能把糊化温度降低到与周围环境相同的温度。
在两步法制糊工艺中,烧碱被用来糊化载糊淀粉增强其粘性。
在一桶式制糊工艺中,淀粉膨胀时添加烧碱也可以增强粘性。
在生产稳定性较强的黏合剂过程中,烧碱还有润湿剂的功能,有助于黏合剂渗透到原纸中。
一般烧碱的添加量约为淀粉量的2%~4%之间,具体视淀粉的类别而定。
此外,高温天气烧碱添加量要比低温天气少,以防止糊料在浆盘和输浆管内糊化并堵塞输送管道。
搅拌
在制备阶段,搅拌是通过剪切力的作用来降低黏合剂的粘度以使之达到一个稳定水平的方法,这种方法可以避免黏合剂在泵到机台及在各机台处进行小循环时粘度急剧下降。
硼砂
在淀粉糊化过程中,硼砂能促进淀粉分子交联结合,增强黏合剂的粘性,加快粘合速度。
此外,硼砂与熟淀粉发生作用,可改变黏合剂的粘度,影响其流动性与渗透性。
在一桶式制糊工艺的制备过程中硼砂可以使淀粉黏合剂达到所需粘性后停止膨胀。
它与烧碱一起使用也可提高初粘强度和粘度稳定性。
硼砂用量一般在1%左右。
添加剂
为了改善淀粉黏合剂的粘合性能或赋予黏合剂在某方面的特殊性能,通常在配制过程中会加入一些添加剂。
常用的的添加剂类型有防腐剂、防水添加剂(交联树脂)、增粘剂、稳定剂等。
熟淀粉糊和膨胀的淀粉分子容易发生细菌降解。
防腐剂有助于避免污染,防止糊料滋生细菌而引起粘性降低。
传统上常使用甲醛一类的防腐剂,但由于甲醛对人体危害较大,近些年来已逐渐被一些更环保更安全的产品取代。
多数纸箱厂配制的黏合剂通常在两三天内即用完,因此,一般不使用防腐剂。
有些瓦楞纸箱在包装后需在冷冻条件下存储,冷冻环境凝成的水汽渗入糊线,容易导致糊线乳化而出现纸板开胶,这就需要黏合剂有很强的防水性能。
增加糊线的防水性能,一般可通过添加交联树脂达成。
交联树脂的作用在于使糊胶固化后不容易再乳化。
增粘剂~般用来提高粘合性能。
粘度添加剂经常用在生产特殊产品(七层瓦楞纸板)或粘合难度大的纸张(如施胶度高的纸张)时。
一般情况下,这种添加剂可不加,除非是先前得知粘合不良的根源并确定不是机器或配方方面的问题。
稳定剂可以用来改善黏合剂粘度下降的问题,而粘度下降多是由搅拌过度、循环使用过程中变稀或腐坏变质造成的。
使用稳定剂后五到十分钟内便可恢复其粘度并在24小时内一直保持该粘度的稳定。
稳定剂通常在特殊而非常规的情况下使用,即在查清粘度下降的根源后使用。
淀粉黏合剂的制备工艺
淀粉黏合剂最初的配制方法是把水和淀粉直接混合,而在实际应用时这种黏合剂对本行业来说用处不大,因为这种黏合剂需要不停顿地搅拌,否则淀粉就会改变悬浮状态而很快沉淀下来。
另外,这种黏合剂的粘性差,施胶操作困难,而且糊化温度要求太高,使设备运转速度变慢,需要大量的热量才能完成粘合过程。
多年来,人们一直没有停止对黏合剂配制工艺的探索,最终有两种工艺逐渐被采用。
霍尔工艺
斯坦霍尔法(SteinHall),俗称"两步法",是美国SteinHall公司于1934年~1936年发明的,此方法制作的淀粉黏合剂是瓦楞纸板用黏合剂中跨时代的发明。
两步法就是在制作黏合剂过程中,用两个制作容器(或称两个浆糊罐),一只安装在上方的罐(制作淀粉熟浆的)称载体罐,另一只安装在下方的罐(制作淀粉生浆的)称为主体罐。
载体罐中载体部分的制作过程,是先将定量的水及淀粉混合搅拌,缓慢加入定量的烧碱溶液,搅拌足够时间,制成粘度高的糊状液,俗称熟浆。
主体罐中主体部分的制作包括两个部分。
首先,将定量的水、淀粉及硼砂混合搅拌足够时间:
然后,将载体罐中的熟浆缓慢注入主体罐中,继续搅拌至合适粘度为止。
斯坦霍尔黏合剂工艺中,主要部分即载体部分可以使未煮熟的淀粉悬浮在糊液中,增加其粘性,存留水分以利于主体淀粉的糊化,影响其与纸张的粘性或吸附性,有助于增加初粘强度。
载体部分在淀粉黏合剂中的比例通常在15%~20%之间。
主体淀粉的作用在于使楞尖上的黏合剂受热加压后糊化,使粘度迅速增加,最终形成粘合。
斯坦霍尔黏合剂工艺现有多种形式,包括"整体混合法"制成的黏合剂及各淀粉黏合剂生产商依业内不同用途生产的专用黏合剂。
一桶式工艺
一桶式黏合剂只有一种状态,即部分膨胀的淀粉颗粒,可使混合物有足够的粘度,防止沉淀。
一桶式黏合剂的制备过程如下:
■准备好一桶烧碱溶液,按3%~5%比例稀释:
■在混合桶内把淀粉和水按一定比例混合并搅拌均匀;
■倒入烧碱溶液于混合桶内使淀粉颗粒膨胀:
■当达到所需粘性时,加入硼砂来增强初粘强度及剪切的稳定性;
■加入防腐剂延长黏合剂的保质期;
■通过搅拌的剪切力作用把混合物粘度降低到所需水平。
一桶式工艺在欧美应用比较广泛,尤其备受许多大型纸箱厂家的青睐。
一桶式工艺的优点在于可制出高固含量低粘度的黏合剂,适合高速瓦线以及重型纸板的需求。
影响黏合剂质量的因素
淀粉黏合剂粘合过程中几大影响因素如下:
固含量
固含量是指黏合剂中干物质的含量占黏合剂总量的比例。
一般淀粉黏合剂固体含量高,水份相对减少,并且较少上胶量即可保证纸板的粘合,因此可以使纸板粘合速度加快,保证高速瓦线生产下产品质量的稳定。
此外,高固含量的黏合剂,使纸板在加工过程中水份变化较小,因而可以减轻纸板翘曲现象。
特别是高速宽幅瓦楞纸板机有的车速达200m/min以上,黏合剂固含量一定要高。
与传统的瓦楞纸板粘合时所用黏合剂相比,微瓦纸板粘合时所用黏合剂的固含量较高,有时高达33%~34%。
有试验表明,固含量高达40%的黏合剂用于粘合微瓦纸板,效果也是非常好的。
但并非所有的瓦楞纸板加工工艺都适用高固含量的黏合剂,有些纸板线速度在60m/min以下,且瓦楞纸渗透性很强,黏合剂中的水分很容易被纸张吸收,所余水分不足以使淀粉颗粒完全糊化,容易造成粘合不良。
还有些精度不够的瓦线设备,如果上胶量太薄,就会导致纸板局部上不到胶而产生粘合不良。
粘度
简单说来,一种物质的粘度可定义为其对流动的抗拒性。
这种特性可用粘度杯(斯坦霍尔杯与涂4#最为常用)来测定。
斯坦霍尔粘度杯为金属杯,杯上的提手可保证杯子在测试时处于垂直状态,底部钻有精度极高的流出孔。
测试时先把粘度杯沉入糊料中装满,然后把粘度杯提出置于糊料液面之上,当杯中糊料的位置达到第一条交叉线时开始用秒表计时,到第二条交叉线出现时停止计时。
两条交叉线之间的糊料容量为10cm3,10cm3的糊料从杯中流出的时间就是糊料的粘度。
通常斯坦霍尔杯测出的粘度值范围在30s~80s之间。
有些自动制糊系统还配有粘度测试装置。
黏合剂的粘度对上胶均匀度及黏合剂对原纸的渗透都有重大影响,粘度合适的黏合剂有利于保证上胶量的足量和均匀,也有利于黏合剂对原纸的渗透,从而直接影响到车速、纸板粘合、平整度及硬度。
一般坑机的粘度应在30S~40S(涂4#杯测量)之间,糊机的粘度应在45s~65s之间。
糊化温度
糊化温度被认为是淀粉颗粒开始膨胀时的温度,此时糊胶会出现明显变稠现象。
糊化温度值通常在540℃~640℃之间,它可以通过加热糊胶样品直至出现变稠而测出。
测试时温度不断上升,到糊料变稠时停顿,此时的温度便可被认为是糊化温度。
若糊化温度太高则糊化反应会延后发生,粘合难度就会加大,这样就必须减慢车速。
若糊化温度太低,糊胶会提前膨胀,也会影响纸板黏合。
且容易造成糊料在糊胶桶、糊胶盘或传送系统内糊化,从而对生产造成极大困扰。
黏合剂的技术指标
根据实践经验,在此给出瓦线黏合剂的技术指标,以供同行参考。
配制黏合剂时常见问题及解决方案
要查出黏合剂的任何问题,一个重要方法是测出其固含量、粘度及糊化温度,并比照其与正确参数的差异。
下表列出淀粉黏合剂形成过程中常见问题的可能原因和改善方法。
影响瓦楞纸板黏合强度的因素主要有哪些?
(1)黏合剂的质量 这是影响瓦楞纸板黏合强度的主要因素。
黏合剂是由淀粉或聚乙烯醇等黏性物质再配以其他化学物质制成的,它的配
方、制作工艺、加水比例等对纸页间的黏合起决定作用。
(2)生产环境因素 环境过于潮湿;纸页之间初黏速度太慢,进入下道工序时,易产生分离;环境于燥,黏合剂过快失掉水分,纸页还未充分吸收黏合剂,也影响黏合强度。
(3)设备和加工因素 如瓦楞辊缺口,表面不平易造成局部黏合不上,压辊压力不匀或不足,车速快慢等都能影响瓦楞纸板的黏合质量。
(4)纸张质量除了黏合剂作为黏合的中间媒体之外,纸的质量对黏合也产生一定影响。
纸的质量主要应注意纸的水分、施胶度、平滑度等。
(5)其他因素生产中糊液量使用多少,要根据黏合的速度来调整用糊量;不同的楞型,其黏合的面积不一样。
在一定长度内,楞数越多,黏合面积越大,黏合的强度也越大。
如何才能确保瓦楞纸板的粘合强度
瓦楞纸板粘合强度的高低主要取决于粘合剂的质量和瓦楞纸板生产线的施胶质量。
粘合剂的质量
粘合剂的质量主要取决于粘合剂制作工艺的优劣和使用原料的质量。
粘合剂使用的主要原料是淀粉,一般采用工业一级品以上的玉米淀粉。
若使用等级较低的淀粉,由于其加工精细度差,蛋白质、脂肪等杂质较多,将消耗更多的烧碱,使粘合剂不稳定,粘合的瓦楞纸板易吸潮,并且粘合剂易以较大的淀粉颗粒和杂质为核心产生凝胶,使流动性变差。
固含量、初黏力、黏度、糊化温度等是衡量粘合剂质量的重要指标:
1.固含量
粘合剂的固含量应根据设备精度、运行速度及原纸实际情况确定,一旦高速宽幅瓦楞纸板生产线的车速达到200米/分钟以上,就要求粘合剂的固含量一定要高,水与淀粉的比例通常在2.5:
1—3:
1之间。
粘合剂固含量高,水分就相对减少,较少的上胶量即可保证瓦楞纸板的粘合;并且在瓦楞纸板加工过程中水分变化较小,可以减轻瓦楞纸板翘曲。
如果企业设备精度低、车速慢、原纸易透,粘合剂的固含量就要低一点,否则会造成瓦楞纸板脱胶、糊线晶化及爆线等质量问题。
2.初黏力
初黏力是保证瓦楞纸板粘合以及提高车速的关键。
在瓦楞纸板生产中,加大原纸预热面积,或者在制作粘合剂时添加交联剂和分别在主体与载体罐中增加硼砂、提高粘合剂固含量,都可以使粘合剂涂布后在较短的时间内开始产生粘合力,并且其黏力可以破坏纸面纤维。
3.黏度
粘合剂黏度越低,流动性越好。
粘合剂流动性决定了粘合剂的渗透性、上胶的均匀度和胶量大小,直接影响到车速、纸板粘合、纸板平整度及强度。
另外,不是粘合剂中淀粉所占比例越高,流动性越差;高固含量的粘合剂通过调整配制工艺,也可以保持很低的黏度。
一般情况下,粘合剂在循环使用中,其黏度每通过循环泵一次,就会有所降低。
此时,应兑入新制作的粘合剂混合使用。
4.糊化温度
糊化温度是指把淀粉粘合剂变成糊浆时所需的初始温度,粘合剂的糊化温度是保持高速生产的关键因素之解决粘合剂的糊化温度问题,除了通过调整烧碱用量及加热的方法外,适当加入一些添加剂也可起到同样的效果。
糊化温度不能太低,否则会造成粘合剂在循环过程中糊化而影响粘合剂的流动性。
应根据季节变化来调整粘合剂的糊化温度,冬季可将糊化温度调低至55—60℃,夏季则可将糊化温度调高至61℃—66。
瓦楞纸板生产线的施胶质量
在欧美国家,对瓦楞纸箱质量的检查,最重要的一条是对瓦楞纸板粘胶线宽度的检查。
标准的施胶是位置准确,粘合剂在整个楞峰上被均匀、流畅地涂抹,糊胶线轮廓清晰,并且没有粘合剂从瓦楞上横向抛射,没有拖拽的糊胶痕迹。
施胶不良主要与瓦楞纸板生产线设备状态、粘合剂质量、原纸质量有关,常见的施胶不良导致的质量问题主要表现在以下几个方面:
1.点滴上胶现象
上胶辊上有污垢,如纸屑、淀粉结块及其他异物等,或者辊面网穴处有异物堵塞,导致上胶辊不能顺利上胶,只能传递少量粘合剂,并且容易被擦落,上胶时就会出现在楞峰上胶量不足,出现断断续续的点滴上胶现象。
这样的瓦楞纸板表面就会出现面纸与芯纸分层的痕迹,纸箱的抗压强度、边压强度和粘合强度都会降低。
当上胶辊和下瓦楞辊之间的间隙太宽时,上胶辊不能接触到下瓦楞辊的地方,瓦楞楞峰上就没有足够的粘合剂。
2.粘合剂横向抛射现象
粘合剂黏度太高;太低或里面硼砂含量太高时,在生产线高速运行时都容易出现粘合剂横向抛射现象,这样会引起纸板翘曲或纸板发软,纸箱的粘合、边压和抗压强度者都会降低。
3.导爪痕迹或真空痕迹
在施胶部分出现导爪痕迹或真空痕迹,这样的瓦楞纸板做成的纸箱,在使用时通常会断裂,瓦楞纸板的边压强度和纸箱的抗压强度会大大降低。
有导爪的单面机生产出来的瓦楞纸板经常会在施胶部分出现导爪痕迹(一条清晰没有粘合剂的空白),通常主要是由于导爪挡板弯曲、磨损、位置偏或调整压力大;粘合剂就在挡板上积累、凝结成块,这些硬化的淀粉就会擦落上胶辊上的粘合剂,形成导爪空白痕迹。
另外,瓦楞原纸含水率高、上胶辊上因磨损造成凹槽或上胶辊上出现较宽的粘合剂被异物擦掉,都会导致此质量问题。
无导爪的单面机常会在施胶部分出现真空痕迹,这主要是由于瓦楞辊真空太多造成的,真空会将瓦楞原纸过度粘贴于瓦楞辊上,造成芯纸凹陷,上胶辊无法将粘合剂涂到凹陷的芯纸楞峰上。
4.严重模糊的断断续续施胶现象
这种现象发生在上胶辊之前,主要是由于导爪挡板与瓦楞辊之间的距离太大、导爪挡板损坏或磨损、瓦楞原纸含水率高、压力辊上压力不均匀、瓦楞辊上有污垢、芯纸原纸上制动器松弛、瓦楞辊上压力不均匀或压力过低、瓦楞辊上无真空或暂时无真空等。
5.不规则的施胶形状
不规则的施胶形状主要是由于导爪和芯纸经过各种辊之间时,位置不准确引起的瓦楞高低不平导致的,芯纸的质量、瓦楞辊上有污垢、表面磨损粗糙、导爪磨损、损坏、弯曲,导爪上有异物,无导爪真空压力不足或真空孔堵塞,压力辊上压力不当、芯纸上制动张力太大或不均匀等。
6.粘合剂上胶不足或无粘合
粘合剂黏度太低、上胶辊网穴堵塞、刮胶辊和上胶辊间隙太小,都会导致上胶不足。
上胶辊和瓦楞辊间隙过大,蒸汽凝结物滴落在上胶辊上,胶量中的粘合剂液面太低,下瓦楞辊和压力辊之间接触不良,瓦楞辊中高及位置不准都会导致无粘合现象的发生。
7.粘合剂上胶过量
粘合剂上胶过量通常是因为上胶辊与刮胶辊间隙过大,或粘合剂黏度过高。
不仅造成粘合剂锒费,而且会导致搓板状纸板问题或纸板翘曲问题的出现,严重时会出现明显的褶皱。
8.瓦楞辊对施胶的影响
瓦楞辊上有凹陷、表面有污垢、瓦楞棍受损或磨损,瓦楞辊夹压力不均匀,瓦楞辊瓦楞不平行都会影响瓦楞成型,直接导致施胶不良。
9.纵切边缘处施胶不良
瓦楞纸板的纵切边缘面纸与瓦楞芯纸未粘合,出现面纸松散现象,主要原因是由于纵切刀具不锋利、纵切机超速运行、纵切刀重叠太多、纵切边缘有导爪或真空痕迹、面纸边缘含水率不均匀、原纸纸幅不同引起的瓦楞辊磨损不均匀、压力辊或下瓦楞辊上有粘合剂结块等。
解决“粘合不良”提高瓦楞纸板质量
在瓦楞纸箱的生产实践中,各种纸张间的粘合是非常重要的一个环节,并且在相当程度上决定了产品的质量水平。
各层纸页之间粘合是否紧密牢固,直接影响瓦楞纸板的质量。
粘合良好的瓦楞纸板表面平整,不起泡、无褶皱、不翘曲,加工成瓦楞纸箱后纸页之间不会产生分离,外观硬挺,有较好的抗压和缓冲性能,能有效地保护内装商品免受外界不利因素影响而受损。
但是,在瓦楞纸板生产线上出现瓦楞纸板粘合不良(起泡、脱胶、假粒)的现象时有发生。
据了解,瓦楞纸板生产线产生的废次品中,因粘合问题造成的占了近七成。
所以,要真正达到降本增效的目的,必须将因粘和问题产生的废品率控制在合适范围内。
接下来,我们将找出纸板“粘合不良”产生的原因,为您在实际生产中遇到问题时,提供一系列解决方案。
瓦楞纸板是否粘合良好是对瓦楞纸板进行物理性能检验的一个重要指标。
影响瓦楞纸板粘合强度的原因比较复杂,概括地讲,原纸、黏合剂、瓦楞纸板机械、生产计划安排和员工操作水平等等,均对其施加了影响,并且以上因素之间还相互影响。
原纸
在此主要表现在几个方面:
1.原纸的含水率:
箱板纸或瓦楞原纸过于干燥(低于6%)或水分过大(高于12%),都会造成瓦楞纸板粘合不佳。
太干燥时,黏合剂的膨润和粘合所必需的水分被原纸吸收,结果造成胶未糊化现象。
水分过大时,多余的水分对热量的吸收,导致热量不足,从而粘合不佳。
解决方案是严格控制原纸的水分,太干燥时须喷湿处理,水分过大时,须适当增加原纸的水分,预热面积,如果仍旧不佳,则必须换纸。
2.原纸的吸水性或透水性的好坏:
原纸的材质、紧度和施胶度,决定了其吸水性或透水性。
吸水性或透水性太差的原纸,会抑制黏合剂的渗透粘合;吸水性或透水性太强的原纸,一会造成胶未糊化现象,二会产生透胶现象。
前一种的解决方案是黏合剂中使用了添加剂,利用添加剂改善原纸表面的疏水性质,使黏合剂得以渗透。
此外,适当增加黏合剂涂布量也是必要的。
我们知道,瓦楞纸板的粘合首先是楞纸楞峰涂胶,然后与面里纸或夹芯的结合,黏合剂在任一层面间的转移受到阻碍,都将影响粘合效果。
例如,德州沪平永发造纸A公司的A级草浆瓦楞纸,经过重施胶处理,吸水性差,不使用耐水型黏合剂无法得到良好的粘合。
后一种的解决方案是适当增加黏合剂粘度。
3.原纸的裂断长:
它是原纸张强度与定量的比率,表示一定宽度的纸条被自身重量拉断时所需的长度。
如果原纸裂断长较低,那么在瓦线速度达到一定程度时,势必造成经常断纸和停机,此时停留在烘道中的瓦楞纸板吸收过多的热量,再好的黏合剂也无法得到良好的粘合。
这种情况,解决办法是降低机速,或提高原纸质量,把裂断长纳入原纸检验项目。
4.原纸一边松懈:
如果是瓦楞纸一边松,会造成高低不平瓦楞,影响与纸板的贴合;如果是纸板一边松,则会在纸板表面形成折皱。
严重时均形成粘合不佳。
解决办法惟有更换原纸。
黏合剂的质量
此处主要反映在两方面:
一是淀粉质量的好坏。
淀粉的等级较低,意味着加工精细度差,蛋白质、脂肪和灰份等杂质较多,使用这样的淀粉,一是将消耗更多的氢氧化钠,使黏合剂不稳定,粘合的瓦楞纸板易吸潮,在潮湿环境下短时间放置,会使瓦楞纸板脱胶;二是黏合剂易以较大的淀粉颗粒和杂质为核心产生凝胶,使黏合剂流动性变差,涂布不均,使瓦楞纸板局部无胶、少胶,产生粘合不佳。
解决办法是使用高质量的淀粉,若是玉米淀粉,宜采用工业一级品以上。
二是黏合剂制作工艺优劣。
黏合剂制作工艺优劣显得更加重要。
瓦楞纸板的黏合剂,有适当的固体含量、粘度以及必要的糊化温度。
一般的黏合剂在循环使用中,其粘度每通过循环泵一次,就有降低的趋势。
此时,应加入新制备的黏合剂混合使用。