1#板坯工艺技术操作规程.docx
《1#板坯工艺技术操作规程.docx》由会员分享,可在线阅读,更多相关《1#板坯工艺技术操作规程.docx(15页珍藏版)》请在冰豆网上搜索。
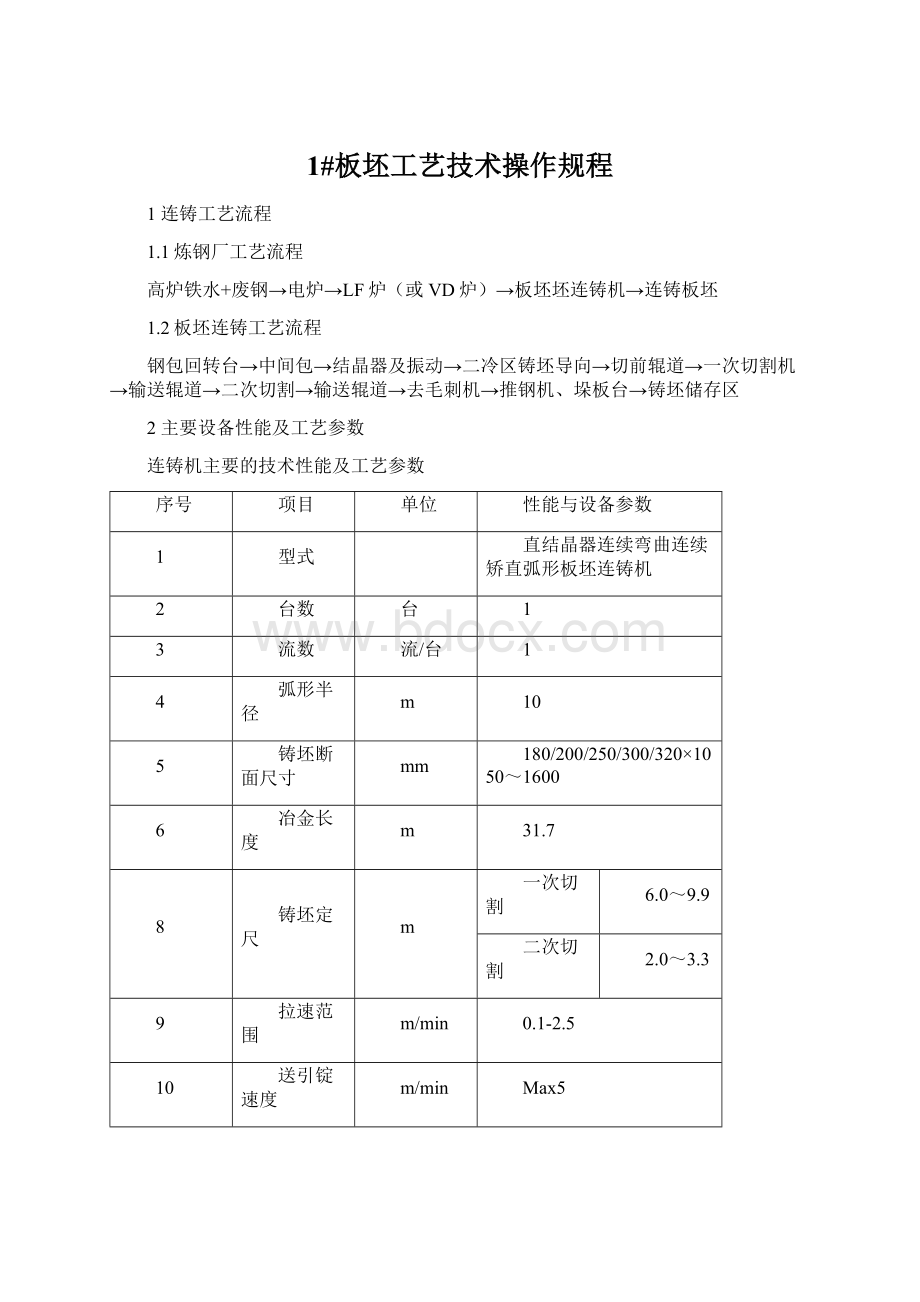
1#板坯工艺技术操作规程
1连铸工艺流程
1.1炼钢厂工艺流程
高炉铁水+废钢→电炉→LF炉(或VD炉)→板坯坯连铸机→连铸板坯
1.2板坯连铸工艺流程
钢包回转台→中间包→结晶器及振动→二冷区铸坯导向→切前辊道→一次切割机→输送辊道→二次切割→输送辊道→去毛刺机→推钢机、垛板台→铸坯储存区
2主要设备性能及工艺参数
连铸机主要的技术性能及工艺参数
序号
项目
单位
性能与设备参数
1
型式
直结晶器连续弯曲连续矫直弧形板坯连铸机
2
台数
台
1
3
流数
流/台
1
4
弧形半径
m
10
5
铸坯断面尺寸
mm
180/200/250/300/320×1050~1600
6
冶金长度
m
31.7
8
铸坯定尺
m
一次切割
6.0~9.9
二次切割
2.0~3.3
9
拉速范围
m/min
0.1-2.5
10
送引锭速度
m/min
Max5
11
送引锭杆插入方式
下装式
12
结晶器
直结晶器铜板铜板长度900mm
13
振动装置
液压振动
14
中间罐容量
t
浇注液位(1035mm)~37.2
溢流液位(1105mm)~40.3
15
铸坯导向及拉矫装置
扇形段分散驱动,连续弯曲,连续矫直包括1个弯曲段6个弧形段2个矫直段5个水平段
16
二冷系统冷却方式
水+汽水雾化
17
引锭存放方式
辊道侧面存放
18
设计产量
万吨/年
115
19
一次冷却水
m3/h
638
20
二次冷却水
m3/h
650
21
设备水
m3/h
650
22
结晶器事故水
m3/h
213(供水时间20min)
23
二次冷却事故水
m3/h
220(供水时间25min)
24
设备冷却事故水
m3/h
220(供水时间25min)
3连铸钢水要求
3.1对钢水化学成分要求
到站钢水化学成分符合钢种要求。
品种钢连铸钢水必须经过炉外精炼,保证充分脱氧。
连铸钢水要求成份均匀,温度均匀,连浇炉次炉与炉之间成份波动范围小。
3.2钢水温度控制
3.2.1液相线温度计算:
液相线温度TL=1536.6-(90*C%+8*Si%+5*Mn%+30*P%+25*S%
+3*AL%+1.55*Cr%+4*Ni%+2.0*Mo%+18*Ti%+80*N%+5.0*Cu%)
3.2.2中间罐中钢水过热度:
中间罐钢水过热度,不同钢水分组如下:
钢种分组中间罐钢水过热度
A、低碳钢25±5℃
B、包晶钢25±5℃
C、中碳钢、中碳合金钢25±5℃
D、高碳钢20±5℃
E、超高碳钢15±5℃
如中间包温度超过最大温度——每超过5℃——拉速降低10%;
如果中间包温度超过最大温度15℃——停止浇注!
!
3.2.3钢水罐中钢水温度:
T罐=T液+T中过+(30~35)
T罐:
钢水罐中钢水温度
T液:
钢水液相线温度
T中过:
中间罐中钢水过热度
到达连铸平台的钢水温度应符合连铸浇铸的规定。
连铸中间罐钢水温度应符合各组钢种规定要求。
连铸第一炉相应提高5~10℃,新包、挖补包不能作为第一炉。
对于新砌钢水罐的情况,到达连铸的钢水温度可提高5~10℃。
钢水最终化学成分要符合钢种操作要点的要求。
钢水准备要严格按照《电弧炉工艺技术操作规程》和《精炼工艺技术操作规程》执行。
4浇注前的准备与参数调整
4.1中间包准备与烘烤
中间包的砌筑和工作层的涂抹要严格按照耐火材料工艺技术规程执行。
中间包水口安装前要严格检查,不得有裂纹和缺陷。
安装好的水口必须垂直于水平面,塞棒在安装前要严格检查,不得有裂纹和缺损,塞棒固定前,手动调整塞棒导向机构,使塞棒有上、下运动量。
塞棒安装完毕,要检查塞棒和水口的对中情况并校对,直到塞棒头部正确复位。
中间包内衬预热时间大于2.5小时,预热结束时中间包内衬表面温度≥1100℃。
4.2浇注前介质、机械、电气自动化和计量系统的检查
介质系统包括结晶器水、二冷水、设备水、压缩空气、氧气、氩气、天然气、煤气等,必须正常;机械、液压系统、自动化系统工作正常;称重、测温、测长系统工作正常。
4.3保护渣、保温剂的准备
入厂检验合格的保护渣、保温剂等消耗材料应在浇注平台上干燥存放。
保护渣的水份不得超过0.5%,不同厂家的保护渣分别存放,不得混用。
4.4振幅、振频相关参数及与拉坯速度的关系:
振动型式:
液压振动
设计参数
振幅(mm)
行程0~7m
频率范围
0~350次/min
振动频率的设定
振动频率在L1-HMI设定。
振幅和振动频率与拉速的关系式如下:
振幅:
A=(A1+A2)V/2
频率:
f=F1+F2V
V---拉速
F1,F2为频率常量参数
As---非正弦系数0~0.4
其中上式中的各参数推荐见下表,具体可现场调整:
钢种
A1
A2
F1
F2
包晶钢
3
3
150
-10
低、中碳钢
3
3
155
-10
高碳钢
3
4
130
10
注:
设定的最小的频率为40次/min。
4.5结晶器冷却水的调整
该系统为半闭路循环系统,使用加腐蚀抑制剂的软化水,分配到结晶器的宽面和窄面。
冷却水的供水压力0.90MPa、回水压力0.3MPa;供水温度最大40℃。
进出口温度差应在4~8℃之间,温度差在要求的水量时大于12℃停止浇铸。
当遇到故障时使事故水塔的事故供水系统供水,将铸机中的铸坯拉出。
结晶器冷却水水量调节在冷却水阀门站人工通过手动调节阀控制,水量与拉速无关。
结晶器每个回路的冷却水流量如下:
宽面外弧侧
4500L/min
宽面内弧侧
4500L/min
窄面左侧
820L/min
窄面右侧
820L/min
水质要求:
水质要求
单位
结晶器冷却水
PH值
8~9
总硬度CaCO3
ppm
﹤20
m-硬度CaCO3
-
CO2-腐蚀性
无
氯化物
ppm
﹤50
硫化物
ppm
﹤50
Fe+Mn
ppm
﹤0.5
SiO2
ppm
﹤1.0
沉淀和悬浮物
ppm
﹤20
颗粒度
μm
≤300
油(石油醚可萃取的)
ppm
无
总的溶解固体物
ppm
﹤300
传导率
μs/cm
﹤600
4.6结晶器的检查
在每次浇注之前必须对结晶器铜板表面进行检查。
结晶器铜板上口往下250mm水平区间内不得有任何损伤;低于这个水平,允许有深度不得大于2mm较小损坏,但这些损坏要低于平均磨损值。
用直尺和塞尺检查铜板的平滑度。
铜板上下口处的允许磨损值宽边为1mm,窄边为3mm,允许误差值<0.5mm.用塞尺和压缩空气清理杂物,确认结晶器四角缝隙符合要求。
检查结晶器的密封性,确认所有法兰连接紧密,不允许水渗进结晶器内部。
清除结晶器足辊沉积的渣壳和其他杂物,确认足辊无破损,并运转自如,结晶器足辊突出铜板下部约0.5mm。
可用直尺直接测量。
确认喷水集管位置正确,检查喷嘴位置和喷水形式正确,无堵塞。
4.7二冷水的调整与检查
每次开浇前必须确认:
二冷区冷却水管道畅通,喷嘴无堵塞,无歪斜、喷水均匀。
二冷水的配水制度要根据钢种、拉速和铸坯断面设定。
由过程控制计算机自动调整,人工设定。
二冷水及设备开路水供水压力1MPa(主管道、标高+1.0m),供水温度最大35℃,升温约25℃。
二冷水及开路设备水的水质、水压要求如下:
水质要求
单位
二冷及设备开路水
PH值
8.5~8.9
总硬度CaCO3
ppm
<350
m-硬度CaCO3
<100
CO2-腐蚀性
无
氯化物
ppm
<100
硫化物
ppm
<250
Fe+Mn
ppm
<0.5
SiO2
ppm
-
沉淀和悬浮物
ppm
<20
颗粒度
μm
≤300
油(石油醚可萃取的)
ppm
<5
总的溶解固体物
ppm
<600
传导率
μs/cm
<1200
4.7.1二冷水及开路设备水冷却方式
二冷水及开路设备包括铸坯冶金喷淋冷却系统及扇形段9~13段导辊的外部冷却。
铸坯的冶金冷却(二次冷却)采用纯水和汽水雾化喷淋冷却。
每个冷却区的空气压力由压力调节阀控制,空气压力0.3MPa。
9I和9X回路用于保护辊子,防止过热。
发生断路故障时,采用事故水塔供水。
4.7.2冷却区的布置
4.7.2.1二次冷却区(冶金冷却)
冷却区段
位置及设备组成
冷却系统
1N
结晶器窄边(足辊)
喷水冷却
1I+O
结晶器足辊,内弧+外弧
喷水冷却
2I+O
弯曲段上部,内弧+外弧
汽雾冷却
3I+O
弯曲段中部,内弧+外弧
汽雾冷却
4I+O
弯曲段下部,内弧+外弧
汽雾冷却
5I+O
扇形段1段内弧+外弧
汽雾冷却
6I
扇形段2+3段内弧
汽雾冷却
6O
扇形段2+3段外弧
汽雾冷却
7I
扇形段4+5段内弧
汽雾冷却
7O
扇形段4+5段外弧
汽雾冷却
8I
扇形段6+7+8段内弧
汽雾冷却
8O
扇形段6+7+8段外弧
汽雾冷却
9I
扇形段9~13段内弧
汽雾冷却
4.7.2.2开路设备冷却
冷却区段
设备组成
冷却系统
9I
扇形段9~13段内弧
汽水雾化冷却
9X
扇形段9~13段外弧左、右侧
交叉喷水冷却
其它
出坯区(辊道、切割机等)
辊子、设备冷却
4.7.2.3冷却水水嘴型号及个数
区域
冷却区
排数
每排喷嘴个数
水嘴总数
喷嘴型号
备注
1区
内弧
2
8
16
3/8PZ10095B
180、200mm
外弧
2
8
16
3/8PZ10095B
180、200mm
内弧
2
8
16
3/8PZ8795B
250mm
外弧
2
8
16
3/8PZ8795B
250mm
左侧
5
1
5
3/8PZ87110B
右侧
5
1
5
3/8PZ87110B
2区
内弧
3
4
12
PZWH6.6-100W6
外弧
3
4
12
PZWH6.6-100W6
3区
内弧
6
4
24
PZWH5.6-95W6
外弧
6
4
24
PZWH5.6-95W6
4区
内弧
8
4
32
PZWH4.6-95W6
外弧
8
4
32
PZWH4.6-95W6
5区
内弧
7
2
14
PZWH6.7-110W61
外弧
7
2
14
PZWH6.7-110W61
6区
内弧
14
2
28
PZWH4.4-110W61
外弧
14
2
28
PZWH5.4-110W61
7区
内弧
14
2
28
PZWH3.4-110W61
外弧
14
2
28
PZWH4.4-110W61
8区
内弧
21
2
42
PZWH3.4-110W61
外弧
21
2
42
PZWH3.4-110W61
9区
内弧
35
2
70
PZWH3.5-110W61
左右
35
2
70
1/2PZ6800B
4.7.3二次冷却水配水标准
钢种分组二次冷却方式
一级二级
A、低碳钢软冷包晶
B、包晶钢、包晶合金钢软冷包晶
C、中碳钢、中碳合金钢中冷中碳、中碳合金
D、高碳钢强冷高碳
E、超高碳钢强冷超高碳
4.8设备闭路冷却水
该系统主要用于扇形段导向辊子轴芯和轴承冷却。
每个回路的冷却水在冷却水阀门站通过手动调节阀和流量开关的指示进行调节。
浇注过程中如果发生断电故障,采用事故水箱供水。
设备闭路水供水压力0.9MPa,回水压力0.3MPa供水温度max40℃,升温不大于15℃。
设备闭路水的水质要求如下:
水质要求
单位
二冷及设备开路水
PH值
8~9
总硬度CaCO3
ppm
﹤20
m-硬度CaCO3
-
CO2-腐蚀性
无
氯化物
ppm
﹤50
硫化物
ppm
﹤50
Fe+Mn
ppm
﹤0.5
SiO2
ppm
﹤1.0
沉淀和悬浮物
ppm
﹤20
颗粒度
μm
≤300
油(石油醚可萃取的)
ppm
无
总的溶解固体物
ppm
﹤300
传导率
μs/cm
﹤600
4.9驱动辊压力的设定
驱动辊有两套压力系统
4.9.1引锭杆压力用于引锭杆操作和扇形段的夹紧。
工作压力为max20MPa。
引锭杆压力在液压站通过操作阀站上相应的手动控制阀设置。
4.9.2热坯压力:
热坯压力用于热态板坯操作,工作压力约1.5-5.0MPa。
热态板坯压力可在OS2(普通操作)按电钮设置,也可在液压站控制箱(事故操作)按电钮设置。
4.10切割长度
4.10.1切割长度的确定
热坯切割长度按下列公式计算:
L(热坯)=L(冷坯)×X+S
式中:
L(热坯)[mm]—热板坯切割长度,此值在火切机测长装置上调整。
L(冷坯)[mm]—冷态板坯长度(约+20°时),即要求的板坯定尺长度。
S[mm]—切缝宽度,取决于割枪质量,通常为8~10。
X—收缩系数,取决于板坯切割温度和钢种的化学成分。
通常,板坯切割温度一般应为800~900℃。
在计算板坯切割长度时,收缩系数可采用下列数值。
X=1.013,(此数据可根据实际情况进行调整)
4.10.2切头切尾的长度
切头原因切头长度(m)
开始浇注(头)0.6
结束浇注(尾)0.65
浇注中断切尾切头
同钢种接痕0.60.6
异钢种接痕0.70.6
注:
非同类钢种(按C含量分类)严禁倒包。
4.11切割前的操作
切割检查切割气体压力的情况,检查切割枪割嘴,调整切割枪火焰,火焰要呈圆锥形,否则更换割嘴。
5引锭杆操作及封引锭
5.1上引锭前,要求再次确认所有信号、通讯及自动化显示系统、机械设备以及风、水、电、气、液压的供给情况,所有条件都要符合上引锭要求。
5.2浇注前的检查:
首先确认使用的引锭杆头与浇注断面的宽度和厚度一致。
然后检查引锭杆的对中情况及运行是否平稳等。
对于上次浇注的引锭杆,在与铸坯脱开送到存放位置后,应及时将引锭头燕尾槽中的残留物诸如石棉绳、碎金属切削等杂物清除,以备下次浇注使用。
在引锭杆活动链节之间的金属残留物也必须清除,以免送引锭杆时造成链节损坏及辊道的磨损。
5.3结晶器的封底和引锭杆头的填塞:
为进行结晶器的封底和引锭杆头的密封填塞,应将引锭杆头从连铸机下部送入结晶器内浇注起始位置,从结晶器铜板上缘往下测量,距引锭头顶约500mm左右。
封引锭头前,引锭头和结晶器内必须干燥。
封引锭头的操作要严格按照具体操作步骤进行。
6开浇操作
6.1开浇前提
6.1.1已完成对结晶器冷却水、设备冷却水、二冷水、结晶器振动装置、切割等设备的检查,并确认能正常使用。
6.1.2结晶器冷却水已打开。
6.1.3结晶器液位控制系统已准备好。
6.1.4再次检查各关键部位的风、水、电、气、液压供给显示数据。
6.1.5引锭头已封装完毕,浇注所需材料和工具都已摆放到指定位置。
6.1.6钢水罐内钢水测温合格后,上回转台,回转台低位接受钢水罐,钢水罐加盖,安装滑动水口液压缸,然后升到高位旋转至浇注位。
6.1.7中间罐预热停止,检查中间罐,保证水口碗处没有残留物,预热结束后塞棒要处于关闭状态,中间罐车升起行走,到浇注位后,用堵头封死塞棒中心的氩气通道。
确认水口的对中,偏差:
宽面≤±5mm、窄面≤±3mm。
使浸入式水口插入深度>300mm。
6.2钢水罐开浇
6.2.1在调整中间罐的同时,钢水罐转至中间罐上方,钢水罐水口与中间罐冲击区对正后,安装钢水罐保护套管,保护套管要对正压紧滑动水口。
6.2.2若钢水罐未能自动开浇,移走保护套管,烧氧引流开浇。
钢水罐开浇后到钢液埋入保护套管下端时,加入中间罐覆盖剂。
6.3中间罐开浇
中间罐预热停止到中间罐开始浇注的时间要尽可能短,不能超过7分钟。
中间罐上下水口间密封的氩气流量调节以结晶器钢水液面不翻为准。
中间罐浇注形式为塞棒控制浇注,中间罐开浇方法为手动开浇、自动开浇两种。
6.4手动开浇
6.4.1当中间罐钢水达到设定重量(大约10~12吨)时,手动开塞棒,开始将钢水注入结晶器。
钢水注入过程是由浇钢工控制的,开始浇注不宜太快,否则容易造成起步漏钢,一般每注入结晶器100mm深度的时间大约4秒,至少不能低于25秒。
6.4.2结晶器液位在距上口150mm时,浇钢工通过按下OS1上的“start”按钮开始起步。
6.4.3依次加入开浇渣及结晶器保护渣,随后开启氩气。
6.4.4手动开浇后,通过按下塞棒控制手操器(LC141\LC151)上的“Auto”按钮,将结晶器液位控制转为自动。
6.5自动开浇
6.5.1中间罐钢水到设定重量(大约10~12吨)
6.5.2按下塞棒控制手操器(LC141\LC151)上的“Auto”按钮,打开塞棒,钢水自动注入结晶器。
通过结晶器液位信号控制拉矫的驱动开始。
7正常浇注操作
7.1保护套管与钢水罐滑动水口连接处要用氩气Ar密封。
7.2正常浇注时中间罐钢水液面控制在38吨。
7.3视中间罐液面情况及时补加覆盖剂,中间罐内不得有裸露钢液。
7.4中间包测温时,开浇后5分钟、10分钟各测一次,以后每隔10分钟测一次。
如中间包温度超过最大温度—每超过5℃——拉速降低10%;如果中间包温度超过最大温度15℃——停止浇注!
!
7.5向结晶器内加入的保护渣应使整个钢液面均匀的覆盖,保持“黑面”操作。
保护渣层厚度应控制在25~40mm内,其中液渣层的合理厚度在8~14mm。
若液渣厚度大于18mm,则必须进行“捞渣”操作。
在浇注过程中应及时清除钢液面四周形成的较大渣条。
清除时,必须用挑渣棍向上挑,杜绝挑渣棍向下按,以免破坏液渣层。
7.6保持结晶器中钢液面稳定。
结晶器钢液面应控制在结晶器铜板上口下方100mm处。
7.7根据钢种、铸坯断面、钢水过热度控制拉坯速度,尽量保持恒速拉坯。
参考拉速见下表:
钢种
组别
钢种
拉速m/min
180
200
250
A
低碳钢
1.8
1.6
1.3
B
包晶钢金钢
1.6
1.4
1.2
C
中碳钢
1.6
1.4
1.2
D
管线钢(微合金)
1.6
1.4
1.2
E
高碳钢、超高碳钢
1.5
1.3
1.1
7.8铸坯矫直温度为900~1050℃。
7.9切割室根据生产计划定尺切割铸坯。
7.10铸坯打号、试样切割以及出坯和精整等工作要严格执行岗位操作规程。
8浇注结束操作
8.1根据钢水罐称重系统显示和观察下渣情况确定钢水罐浇注结束。
连浇最后一炉浇注结束后则进入连铸浇注结束操作。
8.2当钢水罐浇注结束后,要结合中间罐称重进行探杆操作,开始逐渐降低拉坯速度。
当中间罐钢水达到大约15t时,浇注速度降低到0.8m/min,停止向结晶器加保护渣;当中间罐钢水达到大约8t时,浇注速度降低到0.5m/min;当浇注速度降低到0.4m/min时,将结晶器内的保护渣捞净。
并逐步移开保护渣盘和不必要的工具。
中间罐液面达150-200mm时关闭中间罐水口,移出中间罐车至放渣位置,结晶器内铸坯采用喷水封顶。
8.3当结晶器液面下降至结晶器上口以下500mm时,操作人员在OS1按下“浇注结束”按钮,以通知跟踪系统打开“清理机器模式”,铸机自动进入“尾坯”工作方式。
8.4尾坯切割一定要保证铸坯后部无缩孔。
8.5每一炉切割结束时,核对铸坯片数,保证不混炉。
9倒包浇注操作
9.1提前检查好待用烘烤完毕的中间包,首先逐步降低拉速,当中包钢水剩余8~10吨时,拉速降至0.3m/min。
9.2关闭塞棒,用盲板堵住上水口,升起中间包,将浇注位的中间包车开走,并用挑渣棍挑走结晶器四壁内渣带,在有条件的情况下尽可能的捞净结晶器内残留保护渣。
9.3当尾坯拉至引锭头位置距结晶器上口400~450mm时,按扭转到降速位,同时按动“快加速”,将拉速降至0位。
9.4备用中包车开至浇铸位,进行对中、降包,完成后大包开浇,当中包钢水达到10吨左右,中包开浇,起步时间60~90秒。
9.5钢水没过水口侧孔后,加入保护渣,并用挑渣棍搅拌防止起壳。
9.6液位到达距结晶器上口150mm(视情况为准)此时扳到“加速位”同时按下“快加速”将拉速调至0.4m/min(注:
结晶器内有渣条,或渣块及时捞出并补充新保护渣,倒包时间超过6min,不允许倒包,视为失败)逐步将拉速长至正常拉速,同时开启冷却压缩空气及密封氩气。