毕业设计数控技术专业毕业设计.docx
《毕业设计数控技术专业毕业设计.docx》由会员分享,可在线阅读,更多相关《毕业设计数控技术专业毕业设计.docx(41页珍藏版)》请在冰豆网上搜索。
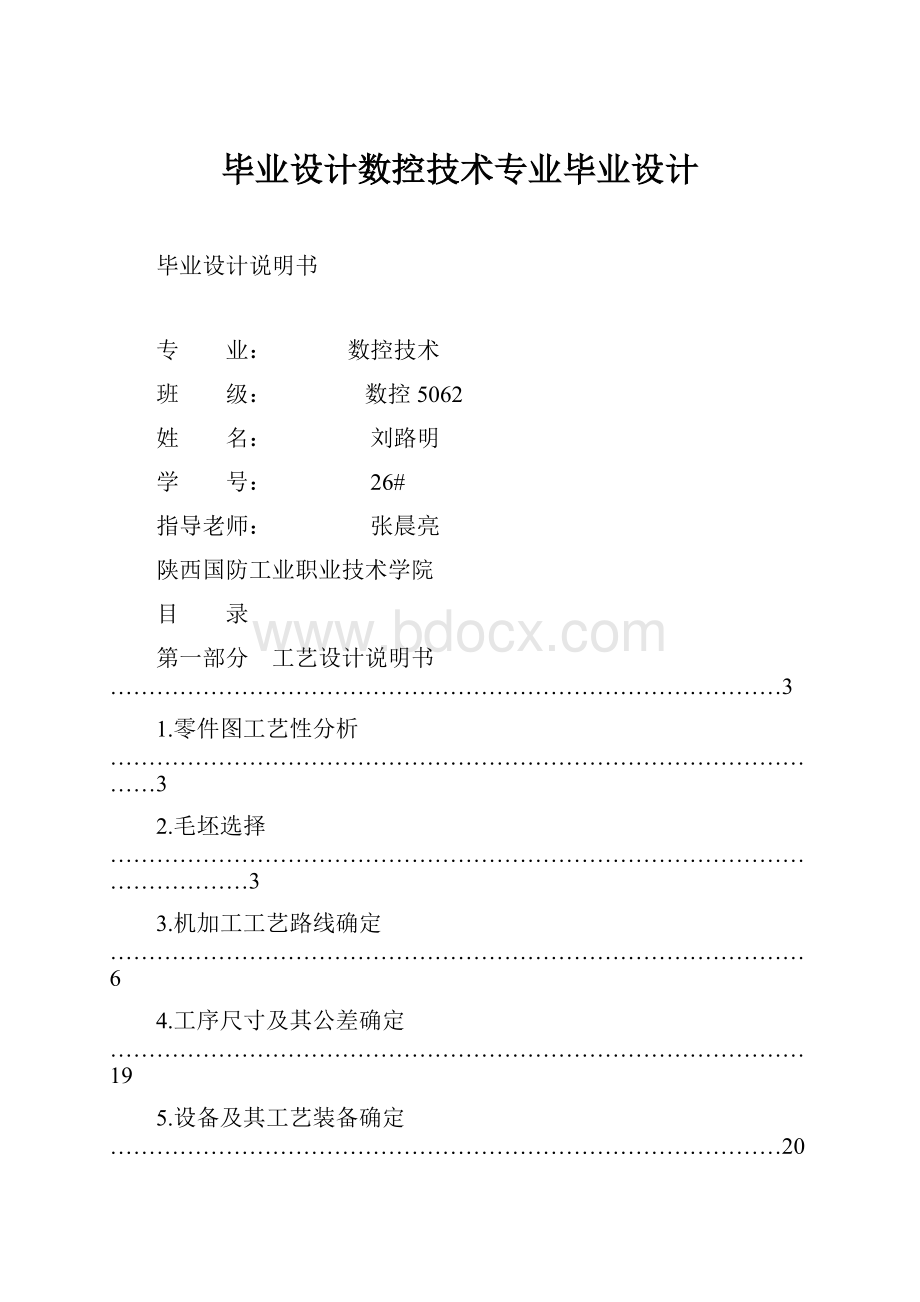
毕业设计数控技术专业毕业设计
毕业设计说明书
专 业:
数控技术
班 级:
数控5062
姓 名:
刘路明
学 号:
26#
指导老师:
张晨亮
陕西国防工业职业技术学院
目 录
第一部分 工艺设计说明书……………………………………………………………………………3
1.零件图工艺性分析……………………………………………………………………………………3
2.毛坯选择………………………………………………………………………………………………3
3.机加工工艺路线确定………………………………………………………………………………6
4.工序尺寸及其公差确定………………………………………………………………………………19
5.设备及其工艺装备确定……………………………………………………………………………20
6.切削用量及工时定额确定…………………………………………………………………………21
7.工艺设计总结……………………………………………………………………………………………28
第二部分 第四号工序夹具设计说明书……………………………………………………………29
1.工序尺寸精度分析……………………………………………………………………………………29
2.定位方案确定……………………………………………………………………………………29
3.定位元件确定……………………………………………………………………………………29
4.夹紧方案及元件确定………………………………………………………………………………30
5.夹具总装草图……………………………………………………………………………31
第三部分 第八号工序量具设计说明书……………………………………………………………32
1.工序尺寸精度分析……………………………………………………………………………………32
2.量具类型确定………………………………………………………………………………32
3.极限量具尺寸公差确定…………………………………………………………………………………32
4.极限量具尺寸公差带图…………………………………………………………………………………33
5.极限量具结构设计……………………………………………………………………………………34
第四部分 第四号工序数控编程设计说明书………………………………………………………37
1.工序数控加工工艺性分析………………………………………………………………………………37
2.走刀路线的确定…………………………………………………………………………………………37
3.刀具及切削用量的选择…………………………………………………………………………………37
4.编程原点的确定及数值计算……………………………………………………………………………37
5.程序编写及程序说明…………………………………………………………………………………37
第五部分 毕业设计体会………………………………………………………………………………39
第六部分参考资料……………………………………………………………………………………40
第一部分 工艺设计说明书
1.零件图工艺性分析
1.1零件结构功用分析
该弯臂零件是圆柱和底座之间由一个梯形柱连接,并且圆柱侧面钻孔,底座面上有固定机构。
此零件结构简单、紧凑,它应用于两零件之间的连接。
1.2零件技术条件分析
通过对零件形状、尺寸和精度的分析,该零件形状简单,对于简单的零件采用整体分析法,该零件的主要加工表面为Φ8(上偏差+0.039下偏差0)和Φ20(上偏差+0.021偏差0)的两孔、Φ38圆柱表面和底座各表面,以及底座上的两个固定槽,经分析其设计基准为A表面。
1.3零件结构工艺性分析
通过对零件形状、尺寸和精度的分析,该零件形状简单,在实际应用中用于轴的固定于支撑,因而在工作中要承受很大部分的力,故要求工件表面要无裂纹、气孔、残缺等。
2.毛坯选择
2.1毛坯类型
零件材料为HT200、形状简单、中批量生产、经查表与分析:
毛胚应选用铸件,并且毛胚的铸造方法应为铸造中的砂型机器造型及壳型的生产类型。
2.2毛坯余量确定
1)铸件尺寸公差等级的选用
因为此零件为中批量生产、材料为HT200,毛胚制造方法为砂型机器造型及壳型的生产类型,所以公差等级应IT10。
(2)铸件机械加工余量等级的确定
因为此零件为中批量生产、材料为HT200,毛胚制造方法为砂型机器造型及壳型的生产类型,所以加工余量的公差等级为G。
(3)铸件机械加工余量的确定
因为零件的基本尺寸为80×80,查铸件机械加工余量表得尺寸公差等级为IT10级,加工余量等级为G,所以铸件的机械加工余量为3.5—2.5。
2.3毛坯-零件合图草图
3.机加工工艺路线确定
3.1加工方法分析确定
毛胚:
铸造。
Φ20上偏差为+0.021下偏差为0的孔:
因为精度要求为IT7级,表面粗糙度为1.6;所以加工方案为:
钻——绞——精绞。
。
Φ8上偏差为+0.039下偏差为0的孔:
因为精度要求为IT8级,表面粗糙度为1.6;所以加工方案为:
钻——绞——精绞。
。
Φ38的圆柱的两端面:
因为精度要求无,表面粗糙度为3.2;加工方案为:
粗铣——半精铣
Φ16的圆柱:
因为精度要求为IT8级,表面粗糙度为3.2;所以加工方案为:
粗铣——半精铣。
5×30的槽:
因为精度要求无要求,表面粗糙度为3.2;所以加工方案为:
粗铣——半精铣。
底座表面上的两个R5的固定槽:
因为精度要求无要求,表面粗糙度为3.2;所以加工方案为:
粗铣——半精铣。
底座80×80下表面:
因为精度要求无要求,表面粗糙度为3.2;所以加工方案为:
粗铣——半精铣。
底座80×80四周表面:
因为精度要求无要求,表面粗糙度为3.2;所以加工方案为:
粗铣——半精铣。
3.2加工顺序的安排和定位基准选择
(第一套方案)
1.毛胚铸造。
2.热处理。
3.以80×80的底座为定位基准,粗铣底表面。
4.以80×80的底座为定位基准,半精铣底表面。
5.以80×80的底座为定位基准,粗铣底表面5×30的槽。
6.以80×80的底座为定位基准,半精铣底表面5×30的槽。
7.以80×80的底座为定位基准,粗铣底座表面上的两个R5的固定槽。
8.以80×80的底座为定位基准,半精铣底座表面上的两个R5的固定槽。
9.以Φ38圆柱的右端面为定位基准,粗铣Φ38左端面。
10.以Φ38圆柱的右端面为定位基准,半精铣Φ38左端面。
11.以Φ38圆柱的左端面为定位基准,粗铣Φ38右端面。
12.以Φ38圆柱的左端面为定位基准,半精铣Φ38右端面。
13.以80×80的底面为定位基准,粗铣Φ16与Φ8的圆柱表面。
14.以80×80的底面为定位基准,半精铣Φ16与Φ8的圆柱表面。
15.以80×80的底面为定位基准,钻Φ8(上偏差为+0.039下偏差为0)的孔。
16.以80×80的底面为定位基准,铰Φ8(上偏差为+0.039下偏差为0)的孔。
17.以80×80的底面为定位基准,精铰Φ8(上偏差为+0.039下偏差为0)的孔。
18.以Φ38圆柱的右端面为定位基准,钻Φ20(上偏差为+0.021下偏差为0)的孔。
19.以Φ38圆柱的右端面为定位基准,铰Φ20(上偏差为+0.021下偏差为0)的孔。
20.以Φ38圆柱的右端面为定位基准,精铰Φ20(上偏差为+0.021下偏差为0)的孔。
21.加工Φ38圆柱表面的倒角。
22.以5×30的槽为定位基准,粗铣80×80的底座四周各表面。
23.以5×30的槽为定位基准,半精铣80×80的底座四周各表面。
(第二套方案)
1.毛胚铸造。
2.热处理。
3.以80×80的底座为定位基准,粗铣底表面。
4.以80×80的底座为定位基准,半精铣底表面。
5.以80×80的底座为定位基准,粗铣底表面5×30的槽。
6.以80×80的底座为定位基准,半精铣底表面5×30的槽。
7.以80×80的底座为定位基准,粗铣底座表面上的两个R5的固定槽。
8.以80×80的底座为定位基准,半精铣底座表面上的两个R5的固定槽。
9.以5×30的槽为定位基准,粗铣80×80的底座四周各表面。
10.以5×30的槽为定位基准,半精铣80×80的底座四周各表面。
11.以Φ38圆柱的右端面为定位基准,粗铣Φ38左端面。
12.以Φ38圆柱的右端面为定位基准,半精铣Φ38左端面。
13.以Φ38圆柱的左端面为定位基准,粗铣Φ38右端面。
14.以Φ38圆柱的左端面为定位基准,半精铣Φ38右端面,以及倒角。
15.以Φ38圆柱的右端面为定位基准,钻Φ20(上偏差为+0.021下偏差为0)的孔
。
16.以Φ38圆柱的右端面为定位基准,铰Φ20(上偏差为+0.021下偏差为0)的孔。
17.以Φ38圆柱的右端面为定位基准,精铰Φ20(上偏差为+0.021下偏差为0)的孔。
18.以80×80的底面为定位基准,粗铣Φ16与Φ8的圆柱表面。
19.以80×80的底面为定位基准,半精铣Φ16与Φ8的圆柱表面。
20.以80×80的底面为定位基准,钻Φ8上偏差为+0.039下偏差为0的孔。
21.以80×80的底面为定位基准,镗Φ8上偏差为+0.039下偏差为0的孔。
(第三套方案)
1.毛胚铸造。
2.热处理。
3.以Φ38圆柱的右端面为定位基准,粗铣Φ38左端面。
4.以Φ38圆柱的右端面为定位基准,半精铣Φ38左端面。
5.以Φ38圆柱的左端面为定位基准,粗铣Φ38右端面。
6.以Φ38圆柱的左端面为定位基准,半精铣Φ38右端面。
7.加工Φ38圆柱表面的倒角。
8.以80×80的底座为定位基准,粗铣底表面。
9.以80×80的底座为定位基准,半精铣底表面。
10.以80×80的底座为定位基准,粗铣底表面5×30的槽。
11.以80×80的底座为定位基准,半精铣底表面5×30的槽。
12.以Φ38圆柱的右端面为定位基准,钻Φ20(上偏差为+0.021下偏差为0)的孔。
13.以Φ38圆柱的右端面为定位基准,铰Φ20(上偏差为+0.021下偏差为0)的孔。
14.以Φ38圆柱的右端面为定位基准,精铰Φ20(上偏差为+0.021下偏差为0)的孔。
15.以80×80的底面为定位基准,粗铣Φ16与Φ8的圆柱表面。
16.以80×80的底面为定位基准,半精铣Φ16与Φ8的圆柱表面。
17.以80×80的底面为定位基准,钻Φ8上偏差为+0.039下偏差为0的孔。
18.以80×80的底面为定位基准,铰Φ8上偏差为+0.039下偏差为0的孔。
19.以80×80的底面为定位基准,精铰Φ8上偏差为+0.039下偏差为0的孔。
20.以80×80的底座为定位基准,粗铣底座表面上的两个R5的固定槽。
21.以80×80的底座为定位基准,半精铣底座表面上的两个R5的固定槽。
22.以80×80的底座为定位基准,粗铣80×80的底座四周各表面。
23.以80×80的底座为定位基准,半精铣80×80的底座四周各表面。
3.3加工阶段的划分说明
粗加工阶段——主要切除各表面的大部分余量,提高生产率。
半精加工阶段——完成次要表面加工为精加工做准备
精加工阶段——保证主要表面达到图样要求
(第一套方案)
工序1:
加工工件的80×80底座下表面。
因为80×80底座面粗糙度为3.2,需经过粗铣——半精铣。
工序2:
加工工件的80×80底座下表面上5×30的槽。
因为精度要求无要求,表面粗糙度为3.2;需经过粗铣——半精铣。
工序3:
加工底座上表面上的两个固定槽,并保证两固定槽相邻两边之间的距离为50,、两固定槽宽均为5。
因两固定槽表面粗糙度为3.2;需经粗铣——半精铣。
工序4:
加工圆柱的左端面,因为Φ38的圆柱两端面表面粗糙度为3.2,所以Φ38的圆柱两端面需经过粗铣——半精铣。
工序5:
加工圆柱的右端面并保证厚度为60,因为Φ38圆柱两端面表面粗糙度为3.2,所以Φ38的圆柱两端面需经过粗铣——半精铣。
工序6:
加工Φ16圆柱端面,因为Φ16圆柱端面表面粗糙度为3.2,所以Φ38的圆柱两端面需经过粗铣——半精铣
工序7:
加工Φ8(上偏差为+0.039下偏差为0的孔)的孔,因Φ8(上偏差为+0.039下偏差为0的孔)的孔的尺寸精度为IT8级表面粗糙度为1.6,所以Φ20(上偏差为+0.021下偏差为0)的孔需经过钻——绞——精绞。
工序8:
加工Φ20(上偏差为+0.021下偏差为0)的孔,并保证控中心与底座下表面之间的垂直度。
因Φ20(上偏差为+0.021下偏差为0)的孔的尺寸精度为IT7级表面粗糙度为1.6,所以Φ20(上偏差为+0.021下偏差为0)的孔需经过钻——绞——精绞。
工序9:
加工工件底座四周各个面,保证尺寸为80×80,表面粗糙度为3.2;需经过粗铣——半精铣。
(第二套方案)
工序1:
加工工件的80×80底座下表面。
因为80×80底座面粗糙度为3.2,需经过粗铣——半精铣。
工序2:
加工工件的80×80底座下表面上5×30的槽。
因为精度要求无要求,表面粗糙度为3.2;需经过粗铣——半精铣。
工序3:
加工底座上表面上的两个固定槽,并保证两固定槽相邻两边之间的距离为50,、两固定槽宽均为5。
因两固定槽表面粗糙度为3.2;需经粗铣——半精铣。
工序4:
加工工件底座四周各个面,保证尺寸为80×80,表面粗糙度为3.2;需经过粗铣——半精铣。
工序5:
加工圆柱的左端面,因为Φ38的圆柱两端面表面粗糙度为3.2,所以Φ38的圆柱两端面需经过粗铣——半精铣。
工序6:
加工圆柱的右端面并保证厚度为60,因为Φ38圆柱两端面表面粗糙度为3.2,所以Φ38的圆柱两端面需经过粗铣——半精铣、及加工倒角。
工序7:
加工Φ20(上偏差为+0.021下偏差为0)的孔,并保证控中心与底座下表面之间的垂直度。
因Φ20(上偏差为+0.021下偏差为0)的孔的尺寸精度为IT7级表面粗糙度为1.6,所以Φ20(上偏差为+0.021下偏差为0)的孔需经过钻——绞——精绞。
工序8:
加工Φ16圆柱端面,因为Φ16圆柱端面表面粗糙度为3.2,所以Φ38的圆柱两端面需经过粗铣——半精铣
工序9:
加工Φ8(上偏差为+0.039下偏差为0的孔)的孔,因Φ8(上偏差为+0.039下偏差为0的孔)的孔的尺寸精度为IT8级表面粗糙度为1.6,所以Φ20(上偏差为+0.021下偏差为0)的孔需经过钻——绞——精绞。
(第三套方案)
工序1:
加工圆柱的左端面,因为Φ38的圆柱两端面表面粗糙度为3.2,所以Φ38的圆柱两端面需经过粗铣——半精铣。
工序2:
加工圆柱的右端面并保证厚度为60,因为Φ38圆柱两端面表面粗糙度为3.2,所以Φ38的圆柱两端面需经过粗铣——半精铣。
工序3:
加工Φ38圆柱表面的倒角。
工序4:
加工工件的80×80底座下表面。
因为80×80底座面粗糙度为3.2,需经过粗铣——半精铣。
工序5:
加工工件的80×80底座下表面上5×30的槽。
因为精度要求无要求,表面粗糙度为3.2;需经过粗铣——半精铣。
工序6:
加工Φ20(上偏差为+0.021下偏差为0)的孔,并保证控中心与底座下表面之间的垂直度。
因
Φ20(上偏差为+0.021下偏差为0)的孔的尺寸精度为IT7级表面粗糙度为1.6,所以Φ20(上偏差为+0.021下偏差为0)的孔需经过钻——绞——精绞。
工序7:
加工Φ16圆柱端面,因为Φ16圆柱端面表面粗糙度为3.2,所以Φ38的圆柱两端面需经过粗铣——半精铣
工序8:
加工Φ8(上偏差为+0.039下偏差为0的孔)的孔,因Φ8(上偏差为+0.039下偏差为0的孔)的孔的尺寸精度为IT8级表面粗糙度为1.6,所以Φ20(上偏差为+0.021下偏差为0)的孔需经过钻——绞——精绞。
工序9:
加工工件的80×80底座上的两个固定槽,表面粗糙度为3.2;需经过粗铣——半精铣。
工序10:
加工工件底座四周各个面,保证尺寸为80×80,表面粗糙度为3.2;需经过粗铣——半精铣。
根据加工的合理性,与一般人的加工零件的习惯等,所以第一套方案比第二套方案合理,所以选第一套方案。
3.4主要机加工工序简图
工序1:
工序2:
工序3:
工序4:
工序5:
工序6:
工序7:
工序8:
工序9:
4.工序尺寸及其公差确定
1、孔径为Φ20,孔深为Z=60mm通孔,7级精度机床为数控铣床材料为HT200,因为工件工作面因而查表得公差为(上偏差为+0.021下偏差为0)。
2、孔径为Φ8,孔钻通至Φ20孔,8级精度机床为数控铣床材料为HT200,因为工件工作面因而查表得公差为(上偏差+0.039下偏差0)。
3、底座下表面为80×80,精度要求无要求,表面粗糙度为3.2,机床为数控铣床材料为HT200,因不是主要工作面所以加工时无需公差。
4、底座上两固定槽,直径为10mm、长为20mm、深为Z=15mm,精度要求无要求,表面粗糙度为3.2,机床为数控铣床材料为HT200,因起固定作用非工作表面所以加工时无需公差。
5、底座下表面上的槽,宽为30mm、长为80mm、深为Z=5mm,精度要求无要求,表面粗糙度为3.2,机床为数控铣床材料为HT200,因起固定作用非工作表面所以加工时无需公差。
6、底座四周表面为15×80,精度要求无要求,表面粗糙度为3.2,机床为数控铣床材料为HT200,因不是主要工作面所以加工时无需公差。
7、圆柱面两边端面,圆柱为Φ38、厚度为60mm,精度要求无要求,表面粗糙度为3.2,机床为数控铣床材料为HT200,因起固定作用非工作表面所以加工时无需公差。
8、圆柱端面,圆柱为Φ16、距Φ38圆柱体侧面距离为3mm,精度要求无要求,表面粗糙度为3.2,机床为数控铣床材料为HT200,因起固定作用非工作表面所以加工时无需公差。
5.设备及其工艺装备确定
1、底座下表面为80×80的加工;机床为数控铣床、所用刀具有Φ50面铣刀、夹具为专用夹具、量具为游标卡尺。
2底座下表面上的槽的加工;机床为数控铣床、所用刀具有Φ10立铣刀、球头刀,夹具为专用夹具、量具为游标卡尺。
3底座上两固定槽的加工;机床为数控铣床、所用刀具有Φ10立铣刀、夹具为专用夹具、量具为游标卡尺。
4、圆柱面两边端面的加工;机床为数控铣床、所用刀具有Φ50面铣刀、夹具为专用夹具、量具为游标卡尺。
5、圆柱端面的加工;机床为数控铣床、所用刀具有Φ20面铣刀、夹具为专用夹具、量具为游标卡尺。
6、孔径为Φ20的加工;机床为数控铣床、所用刀具有Φ18钻头、Φ20铰刀,夹具为专用夹具、量具为塞规。
7、孔径为Φ8的加工;机床为数控铣床、所用刀具有Φ7.8钻头、Φ8铰刀,夹具为专用夹具、量具为塞规。
8、底座四周表面的加工;机床为数控铣床、所用刀具有Φ20面铣刀、夹具为专用夹具、量具为游标卡尺。
6.切削用量及工时定额确定
㈠.孔径为Φ20,孔深为Z=60mm通孔,7级精度.机床为数控铣床材料为HT200
1>进给量f
按加工要求决定进给量:
材料为HT200,钻头直径为Φ18时,f=0.70~0.86mm/r
故,f=0.70mm/r
2>入切量及超出量
y+Δ=8mm
3>决定钻头磨钝标准及耐用度
当d0=18时,
钻头后刀面最大磨损量为0.4~0.8mm,取为0.6mm
刀具寿命T=60min=3600s,取耐用度T=3600s
由表9
4>决定切削速度
由表1.15得,Vc=11m/min
因Vc=1000/πdn
d——切削刃选定点处所对应的工件或刀具的回转直径
d=18mm=0.018m
n——工件或刀具转速
故,Vc=1000/π×18n
故,n=1000/11×0.018π≈1608r/min
5>计算基本工时:
Tm=L/nf式中L=Z+Y+Δ
因Z=60mm,y+Δ=10mm,故L=60+10=70mm
故Tm=70/0.70×1608≈0.62189min=37.3134s≈38s
㈡.孔为Φ8,孔深为Z=22mm8级精度机床为数控铣床材料为HT200
1>进给量f
按加工要求决定进给量:
材料为HT200,钻头直径为Φ7.5mm时,f=0.36~0.44mm/r
故,选f=0.40mm/r
2>入切量及超出量
y+Δ=2mm
3>决定钻头磨钝标准及耐用度
当d0=7.5时,
钻头后刀面最大磨损量为0.4~0.8mm,取为0.6mm
刀具寿命T=35min=2100s,取耐用度T=2100s
4>决定切削速度
由表1.15得,Vc=13m/min
因Vc=1000/πdn
d——切削刃选定点处所对应的工件或刀具的回转直径
d=7.5mm=0.0075m
n——工件或刀具转速
故,Vc=1000/π×18n
故,n=1000/13×0.0075π≈3266r/min
5>计算基本工时:
Tm=L/nf式中L=Z+Y+Δ
因Z=22mm,y+Δ=2mm,故L=22+2=24mm
故Tm=24/0.40×3266≈0.018371min=1.10226s≈2s
7.工艺设计总结
回顾工艺设计的过程,我在指导老师和同学的支持与帮助下,严格要求自己,按照任务书的要求,较好地完成了工艺部分的设计。
将工艺设计过程的情况总结如下:
第一,工艺设计对我而言是一个熟悉的环节,所以设计的效率有待进一步提高;
第二,在设计的过程中有些工作还不够过细;
第三,通过设计感觉自己的理论水平还不太适应实际设计的要求。
第二部分 第四号工序夹具设计说明书
1.工序尺寸精度分析
此工序需加工底座四周表面中与φ38圆柱左端面平行的一边和φ38圆柱左端面,并且表面质量为3.2。
2.定位方案确定
对零件图的尺寸精度和设计基准的分析,完成此工序,应选底座四周表面中与φ38圆柱左端面平行的一边相对一面与φ38圆柱右端面来定位。
3.定位元件确定
定位元件应选两个圆柱销,一个定位在底座上边平面附近、一个定位在φ38圆柱附近,并且在在底平面设计凸台,防止工件加工时产生的倾斜,限制1个自由度两个圆柱销限制2个自由度。
4.夹紧方案及元件确定
圆柱销(两个)
5.夹具总装草图
第三部分 第八号工序量具设计说明书
1.工序尺寸精度分析
φ20孔精度为H7,上偏差ES=0.021mm,下偏差EI=0mm。
确定量规制造公差位置要素值按<<表6-1查得>>精度为IT7,基本尺寸为φ20孔量规公查T=0.0024.位置Z=0.0034
2.量具类型确定
因φ20H7孔是工件的工作部分,有精度要求,为了保证工件要求尺寸加工完成后无误,所以采用专用塞规来进行测量。
3.极限量具尺寸公差确定
φ20H7孔用塞规
通规
上偏差ES=EI+Z+T/2=0+0.0034+0.0024/2
=0.0046mm
下偏差EI=EI+Z+T