毕业设固定管板式换热器设计说明书计.docx
《毕业设固定管板式换热器设计说明书计.docx》由会员分享,可在线阅读,更多相关《毕业设固定管板式换热器设计说明书计.docx(48页珍藏版)》请在冰豆网上搜索。
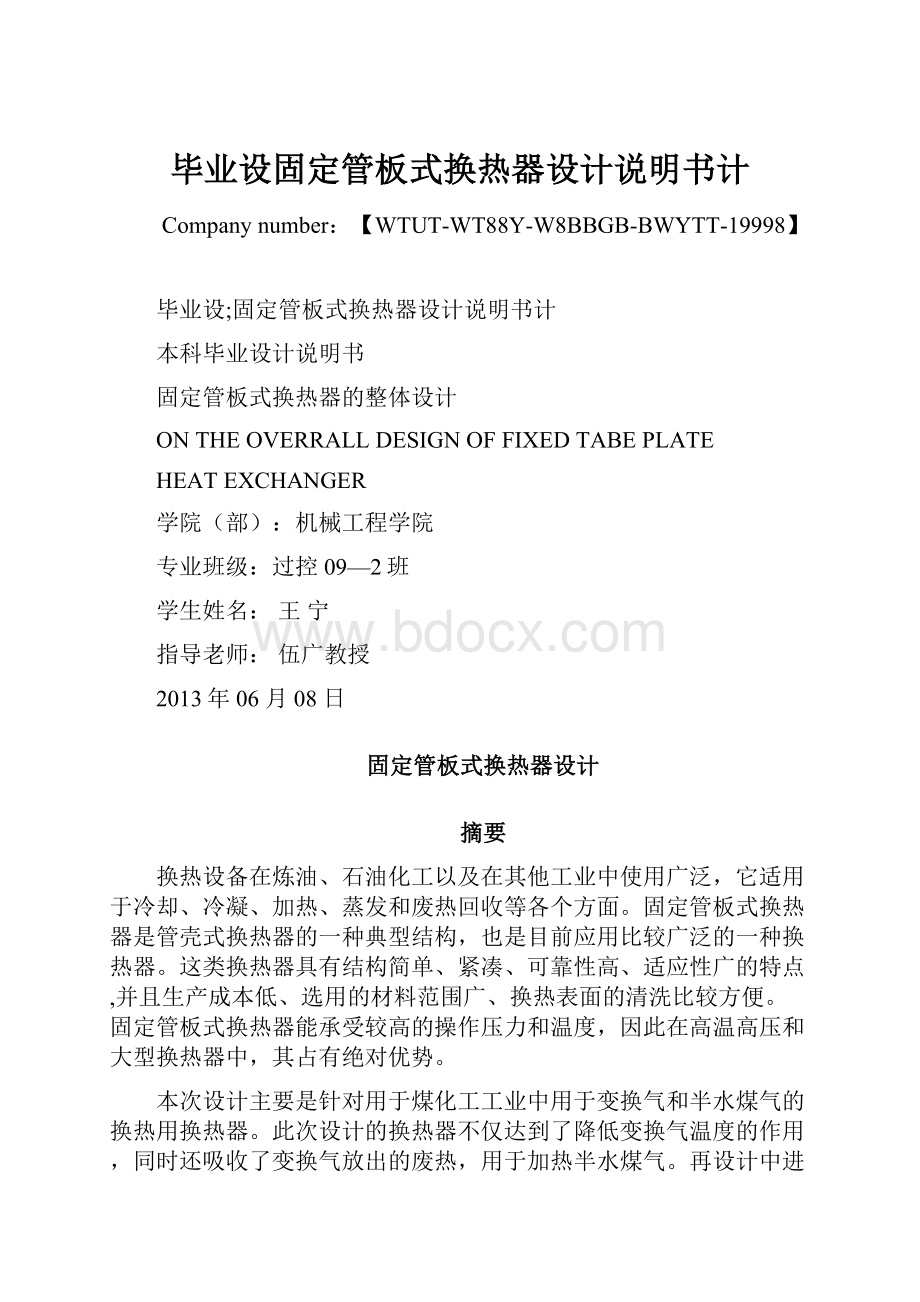
毕业设固定管板式换热器设计说明书计
Companynumber:
【WTUT-WT88Y-W8BBGB-BWYTT-19998】
毕业设;固定管板式换热器设计说明书计
本科毕业设计说明书
固定管板式换热器的整体设计
ONTHEOVERRALLDESIGNOFFIXEDTABEPLATE
HEATEXCHANGER
学院(部):
机械工程学院
专业班级:
过控09—2班
学生姓名:
王宁
指导老师:
伍广教授
2013年06月08日
固定管板式换热器设计
摘要
换热设备在炼油、石油化工以及在其他工业中使用广泛,它适用于冷却、冷凝、加热、蒸发和废热回收等各个方面。
固定管板式换热器是管壳式换热器的一种典型结构,也是目前应用比较广泛的一种换热器。
这类换热器具有结构简单、紧凑、可靠性高、适应性广的特点,并且生产成本低、选用的材料范围广、换热表面的清洗比较方便。
固定管板式换热器能承受较高的操作压力和温度,因此在高温高压和大型换热器中,其占有绝对优势。
本次设计主要是针对用于煤化工工业中用于变换气和半水煤气的换热用换热器。
此次设计的换热器不仅达到了降低变换气温度的作用,同时还吸收了变换气放出的废热,用于加热半水煤气。
再设计中进行对物料及热量衡算,并对换热器整体机构进行计算和对换热器的基本附件进行选择和设计。
最后绘出非标零件图和装配图。
关键词:
流量,换热面积,结构设计,换热管,管板,封头,壳体
ONTHEOVERRALLDESIGNOFFIXEDTABEPLATE
HEATEXCHANGER
ABSTRACT
Heatexchangerinoilrefining,petrochemical,andwidelyusedinotherindustries,itissuitableforcooling,heating,evaporationandcondensation,heatrecovery,andvariousotheraspects.Fixedtubeplateheatexchangerisatypicalstructureoftheshellandtubeheatexchangerandawiderangeofheatexchanger.Thistypeofheatexchangerhasthecharacteristicsofasimplestructure,compact,highreliabilityandwideadaptability,andlowcostoftheproduction,widechoiceofusedmaterials,moreconvenientofcleaningheatexchangerthesurface.Fixedtubeplateheatexchangercanwithstandsthehigheroperatingpressureandtemperature,soithastheabsoluteadvantageinthepossessionofhightemperatureandhighpressureheatexchangersandlarge.
Thisdesignismainlyusedforheatexchangeofheatexchangerusedingasandwatergasforcoalchemicalindustry.Heatexchangerofthedesignnotonlycanreducetheairtemperaturechangeeffect,italsoabsorbsthewasteheatreleasedforheatingventilation,semiwatergas.Inthedesignofthematerialandheatbalance,thebasicaccessoriesheatexchangerandwholebodywerecalculatedandtheheatexchangerselectionanddesign.FinallyIdrawthenon-standardpartsdrawingandassemblydrawing.
KEYWARDS:
discharge,theheatexchangearea,structuraldesign,heatexchangetube,tubesheet,heads,housings
.
1绪论
化工设备简介
化工生产离不开化工设备,化工设备是化工生产必不可少的物质技术基础,是生产力的主要因素,是化工产品质量保证体系的重要组成部分。
然而在化工设备中化工容器占据着举足轻重的地位,由于化工生产中,介质通常具有较高的压力,化工容器一般有筒体、封头、支座、法兰及各种容器开孔接管所组成,通常为压力容器,因为压力容器是化工设备的主体,对其化工生产过程极其重要,国家对其每一步都有具的标准对其进行规范,如:
中国《压力容器安全技术监察规程》、GB150—2011《钢制压力容器》、GB151—2012《管壳式换热器》等。
在其中能根据不通的操作环境选出不同的材料,查出计其允许的工作压力,工作温度等。
换热器概述
换热器简单说是具有不同温度的两种或两种以上流体之间传递热量的设备。
在工业生产过程中,进行着各种不同的热交换过程,其主要作用是使热量由温度较高的流体向温度较低的流体传递,使流体温度达到工艺的指标,以满足生产过程的需要。
此外,换热设备也是回收余热,废热,特别是低品位热能的有效装置。
换热设备在炼油、石油化工以及在其他工业中使用广泛,它适用于冷却、冷凝、加热、蒸发和废热回收等各个方面。
对同一种形式的换热器,由于各种条件不同,往往采用的结构亦不相同。
在工程设计中,除尽量选用定型系列产品外,也常按其特定的条件进行设计,以满足工艺上的需要(得到适合工况下最合理最有效也最经济的便于生产制造的换热器等等)〔1〕。
板式换热器
板式换热器是一种高效紧凑型热交换设备。
它具有传热效率高,阻力损失小,结构紧凑,拆装方便,操作灵活等优点。
目前广泛应用于冶金、机械、电力、石油、化工、制药、纺织、造纸、食品、城镇小区集中供热等各个行业和领域〔1〕。
管壳式换热器的分类
根据管壳式换热器的结构特点,常将其分为固定管板式、浮头式、U型管式、填料函式、滑动管板式、双管式等〔2〕。
1、固定管板式换热器
固定管板式换热器的典型结构如下图所示。
管束连接在管板上,管板与壳体焊接。
其优点是结构简单、紧凑、能承受较高的压力,造价低,管程清洗方便,管子损坏时易于堵塞或更换;缺点是当管束与壳体的壁温或材料的线胀系数相差较大时,壳体与管束将会产生较大的热应力。
这种换热器适用于壳测介质清洁且不易结垢、并能进行清洗、管程与壳程两侧温差不大或温差较大但壳测压力不高的场合〔2〕。
一般固定管板式换热器的结构如图1—1。
图1—1固定管板式换热器结构图
(图片来源于GB151-2012)
2、浮头式换热器
浮头式换热器的典型结构如下图所示。
两端管板中只有一端与壳体固定,另一端可相对壳体自由移动,称浮头。
浮头由浮头管板、钩圈和浮头端盖组成,是可拆连接,管束可从壳体内抽出。
管束与壳体的热变形互不约束,因而不会产生热应力。
浮头换热器的特点是管间与管内清洗方便,不会产生热应力;但其结构复杂,造价比固定管板式换热器高,设备笨重,材料消耗大,且浮头端小盖在操作中无法检验,制造时对密封要求较高。
适用于壳体与管束之间壁温差较大或壳程介质易结垢的场合〔2〕。
一般浮头式换热器的结构如图1—2。
图1—2浮头式换热器结构图
(图片来源于GB151-2012)
3、U形管换热器〔2〕
U形管式换热器的典型结构如下图所示。
这种换热器的结构特点是,只有一块管板,管束由多根U形管组成,管的两端固定在同一根管板上管子可自由伸伸缩。
当壳体与U形换热管有温差时,不会产生热应力〔2〕。
一般U形管换热器的结构如图1—3。
图1—3U形管换热器结构图
(图片来源于某换热器工厂宣传图)
由于弯管曲率半径的限制,其换热管排布较少管束最内层管间距较大,管板的利用率较低,壳程流体易形成短路,对传热不利,当管子泄漏损坏时,只有管束外围处的U形管才便于更换,内层换热管坏了不能更换,只能堵死,而且坏一根U形管相当于坏两根管,报废率较高。
U形管结构比较简单、价格便宜、承压能力强、壳壁温差较大或壳程介质易结垢需清洗、又不适宜采用浮头式和固定管板式的场合。
特别适用于管内走清洁而不易结垢的高温、高压、腐蚀性大的物料。
4、填料函式换热器
填料函式换热器的典型结构如下图所示。
这种换热器的结构特点与浮头式换热器相类似,浮头部分露在壳体以外,在浮头与壳体的滑动接触面处采用填料函式密封结构。
由于采用填料函式密封结构,使得管束在壳体轴向可自由伸缩,壳壁与管壁不会产生热变形差,从而避免可热应力。
其结构较浮头式换热器简单,加工制造方便,节省材料,造价比较低廉,且管束从壳体内可以抽出你,管内,管间都能清洗,维修方便〔2〕。
一般填料函式换热器的结构如图1—4。
图1—4填料函式换热器结构图
(图片来源于GB151-2012)
管壳式换热器结构
管壳式换热器的主要零部件有壳体、接管、封头、管板、换热管、折流元件等,对于温差较大的固定管板式换热器,还应包括膨胀节。
管壳式换热器的结构应该保证冷、热两种流体分走管程和壳程,同时还要承受一定温度和压力的能力。
1、管板:
管板是换热器的重要元件,主要是用来连接换热器,同时将管程和壳程分隔,避免冷热流体相混合。
当介质无腐蚀或有轻微腐蚀时,一般采用碳素钢、低合金钢板或其锻件制造〔3〕。
2、管子与管板的连接:
管子与管板的连接必须牢固,不泄漏。
既要满足其密封性能,又要有足够的抗拉强度。
其连接形式主要有强度胀接、强度焊接、胀焊结合]〔13〕。
3、管箱:
其作用是把管道中来的流体均匀分布到各换热管中,将换热管内流体汇集在一起送出换热器〔3〕。
4、折流板和支承板:
壳程内侧装设折流板或支承板,折流板的作用是组
壳间流道,使流体以适当的流速冲刷管束,提高传热系数,改善传热效果,以达到一定的传热强度。
常用的折流板有弓形和圆环形两种,弓形折流板又分为单弓形、双弓形和三弓形〔3〕。
5、拉杆和定距管:
折流板的安装一般是用拉杆和定距管组合并与管板固
在一起。
拉杆与管板连接的一端可用焊接或螺纹连接,另一端也用焊接或螺纹固定。
一般拉杆的直径不得小于10mm、数量不得小于4根[4]。
管板与壳体的连接:
其连接型式可分为不可拆式和可拆式。
换热器研究内容及发展动向
板式换热器出现是在二十世纪20年代,主要应用于食品工业。
以板代管制成的换热器,主要特点是结构紧凑,传热效果好,因此陆续发展为多种形式。
在30年代初,瑞典首次制成螺旋板换热器。
接着英国用钎焊法制造出一种由铜及其合金材料制成的板翅式换热器,用于飞机发动机的散热。
接着30年代末,瑞典又制造出第一台板壳式换热器,用于纸浆工厂。
在这十多年的时间里,为了解决强腐蚀性介质的换热问题,人们对新型材料制成的换热器开始关注。
到了60年代左右,因为空间技术和尖端科学的迅速发展,迫切需求各种高效能紧凑型的换热器,又加上冲压、钎焊和密封等技术的发展,换热器制造工艺得到进一步完善,从而推动了紧凑型板面式换热器的蓬勃发展和广泛应用。
此外,自60年代开始,为了适应高温和高压条件下的换热和节能的需要,典型的管壳式换热器也得到了进一步的发展。
到了70年代中期,为了强化传热,在研究和发展热管的基础上又创制出热管式换热器[10]。
当前换热器的基本发展趋势是:
继续提高设备的传热效率,促进设备结构的紧凑性,加强生产制造成本的标准系列化,并在广泛的范围内继续向大型化发展,并CDF(ComptationalFluidDynamics)模型化技术、强化传热技术及新型换热器开发等形成一个高技术体系。
管壳式换热器具有结构坚固、弹性大和使用范围广等独特优点,一直被广泛应用。
尤其在高温高压和大型化的场合下,以及制造工艺上的进一步自动化和机械化,管壳式换热器今后将在广泛的领域内得到继续发展。
而板翅式换热器(冷箱)主要用于乙烯裂解,空气分离和天然气液化等。
板翅式换热器现在生产制造技术已经达到了世界先进水平,流道多达15股,单体外形尺寸达6m××,最高设计压力达。
随着换热器广泛应用于各行业,诞生了各种新型的换热器,这使得传热理论不断完善,换热器相关技术也得到不断提高,换热器研究、设计、制造等技术不断改进和发展,传热技术发展的同时又让各种新型高效换热器不断地产生。
目前各国为了提高换热器性能而进行的研究方向主要是强化传热,强化传热的途径主要有扩大传热面积、提高传热系数和增大传热温差等方式,其中提高传热系数是强化传热的重点,其方法主要是通过强化管程传热和壳程传热两个方面得以实现。
目前,管壳式换热器强化传热方法主要有[1]:
1、采用改变传热元件本身的表面形状及其表面处理方法,以获得粗糙的表面和扩展表面。
2、用添加内插物的方法以增加流体本身的绕流、
3、将传热管的内外表面轧制成各种不同的表面形状,使管内外流体同时产生湍流并达到同时扩大管内外有效传热面积的目的,提高传热管的传热性能。
4、将传热管表面制成多孔状,使气泡核心的数量大幅度增加,从而提高总传热系数并可增加其抗污垢能力。
5、改变管束支撑形式以获得良好的流动分布,充分利用传热面积等。
换热器相关技术的发展主要表现在以下几发面:
防腐技术,防结垢技术,强化技术,抗振技术,制造技术,研究手段以及大型化与小型化并重,。
随着工业中经济效益与社会环境保护的要求,制造水平的不断提高,新能源的逐渐开发,研究手段的日益发展,各种新思路的与新结构的涌现,换热器将朝着更高效、经济、环保的方向发展。
2工艺计算
设计参数:
1、物料
表2—1物料参数
名称
操作压力(表压MPa)
进口温度(°C)
出口温度(°C)
半水煤气
160
375
变换气
420
210
2、操作方式
逆流操作
3、换热器结构工艺尺寸
(1)壳体内径700mm
(2)换热管25×3×6000,295根,等边三角形排列,中心距34mm
(3)拉杆16×6
(4)圆缺形折流板高度510mm,板间距400mm,
(5)热流体进出管直径×长度Dg200×150
(6)冷流体进出管直径×长度Dg1500×150
换热器选择
选择换热器的类型
换热器的使用场合、使用目的、换热介质物性等因素的不同,决定了管壳式换热器的结构型式。
固定管板式换热器结构简单、紧凑、造价低,每根换热管可以单独清洗和更换,在外形尺寸相同的条件下,与浮头式和U形管式换热器相比,换热面积大〔2〕。
所设计换热器用于半水煤气和变换气的传热,粘度较小,不易结垢,不易腐蚀管道,所以选用固定管板式换热器,便于拆卸、清洗。
综上所述,换热器选择固定管板式换热器。
冷、热流体流动通道的选择原则〔2〕:
1、不洁净和易结垢的液体宜走管程(管内清洗方便);
2、腐蚀性流体宜走管程(以免管束和壳体同时受到腐蚀);
3、压强高的流体宜走管程(以免壳体承受压力);
4、饱和蒸汽宜走壳程(洁净,α与流速无关,冷凝液易排出);
5、被冷却的流体宜走壳程(便于散热);
6、若两流体温差较大,宜将α大的流体走壳程(以减小热应力);
7、流量小、粘度大的流体宜走壳程(Re>100即可达湍流,也可走管程,采用多管程);
综上所述,选择半水煤气走管程,变换气走壳程。
传热形式选择
管壁两侧流体温度差变化如下图2-1所示:
并流逆流
图2-1流体温度差变化图
如上图所示,若传热形式选择并流传热,则不符合热传递定律,所以流体传热形式选择逆流传热。
换热面积的计算
查JB/T4715得换热面积的计算公式为:
式中:
A—计算换热面积,
;
d—换热管外径,m;
L—换热管长度,m;
δ—管板厚度,m;
n—换热管根数。
查GB151-2012得:
1、用于易燃易爆及有毒介质等严格场合时,管板的最小厚度(不包括腐蚀裕量)应不小与换热管的外径。
2、管板与换热管采用焊接时管板的最小厚度应满足结构设计和制造要求,且不小于12mm。
因此暂取管板最小厚度δ=12mm
则换热面积计算如下:
物料与热量衡算
变换气主要成分是CO2、CO、N2、H2,还有少量的CO、CH4等。
半水煤气主要由N2、H2、CO、CO2、O2、组成,并含有少量H2S和惰性气体。
由《小合成氨厂工艺与设计手册》〔3〕查的半水煤气和变换气各组分比列如下(自贡市鸿鹤化工厂的实际数据):
表2-2变换气组分
组分
N2
CO
H2
CO2
H2O
CH4
含量(%)
表2-3半水煤气组分
组分
N2
CO
H2
CO2
O2
CH4
含量(%)
21
30
38
7
定性温度
对于一般气体和水等低粘度流体,其定性温度可取流体进出口温度的平均值。
故壳程流体(变换气)的定性温度为〔4〕:
管程流体(半水煤气)的定性温度为:
介质物性计算
根据定性温度,在定性温度下分别查《化学化工物性数据手册》〔6〕(无机、有机卷)得壳程和管程流体的物性数据如表2-5和2-6。
表2-4315℃
时变换气物性数据
组分
N2
CO
H2
CO2
H2O
CH4
含量xi(%)
密度kg/m3
(表格来源于《化学化工物性数据手册》(无机卷))
表2-5255℃
时半水煤气物性数据
组分
N2
CO
H2
CO2
O2
CH4
H2O
含量(%)
21
30
38
7
密度kg/m3
(表格来源于《化学化工物性数据手册》(无机卷))
根据定性温度,在定性温度下分别查《工程热力学》〔5〕得壳程和管程流体的比压热熔各项系数如表2-6和2-7。
表2-6变换气各组分的比压热熔各项系数
组分
N2
CO
H2
CO2
H2O
CH4
含量xi(%)
a0
a1(10-3)
a2(10-6)
a3(10-9)
(表格来源于《工程热力学》〔10〕附表2)
表2-7半水煤气各组分的比压热熔各项系数
组分
N2
CO
H2
CO2
O2
CH4
H2O
含量(%)
21
30
38
7
a0
a1(10-3)
a2(10-6)
a3(10-9)
(表格来源于《工程热力学》〔10〕附表2)
则计算得变换气和半水煤气各组分的比压热容及质量分数如表2-8和2-9。
表2-8变换气各组分的比压热熔及质量分数
组分
N2
CO
H2
CO2
H2O
CH4
含量xi(%)
比压热熔Cp
Cp=a0+a1(T)K+a2(T)2K+a3(T)3K
(KJ/)
质量分数(%)
)
表2-9半水煤气各组分的比压热熔及质量分数
组分
N2
CO
H2
CO2
O2
CH4
H2O
含量(%)
21
30
38
7
比压热熔Cp
Cp=a0+a1(T)K+a2(T)2K+a3(T)3K
(KJ/)
质量分数(%)
)
则半水煤气和变换气在各自定性温度和压力下的平均密度和比热容为:
变换气的平均密度
变换气的平均比热容为
半水煤气的平均密度
半水煤气的平均比热容
选择总传热系数
在列管式换热器中,两流体为气体—气体,总传热系数大致范围为10~40W/(数据来源于《化工原理》〔4〕152页表4-7)。
因为总传热系数增大,可减小换热器的传热面积。
所以选择总传热系数K=40W/。
平均温差
逆流
因
;所以
热负荷计算
由公式
得热负荷量。
管程流体(半水煤气)质量流量估算
由选取的管程流体在管内流速为20m/s。
换热管体积为
=×6000×295π×10-9
=
管路截面积为
=×295π×10-6
=
由公式Q=qm2Cp2(t2-t1)可得:
管程流体(变换气)质量流量为
管程流体(变换气)体积流量为
管程流体(变换气)流速为
流速及总传热系数的确定
常见的换热器中流体流速如表2-10。
根据表2-10,气体的在管程中的流速范围在5~30m/s,W/时,管程流体流速υ=s,符合要求,故选择总传热系数K=40W/合适。
表2-10换热器常用流速的范围
介质
循环水
新鲜水
一般液体
易结垢液体
低粘度油
高粘度油
气体
流速
管程流速,m/s
~
~
~3
>
~
~
5~30
壳程流速,m/s
~
~
~
>
~
~
2~15
(图表来源于GB150-2011)
壳程流体(变换气)流量确定
由公式
得
3结构计算
换热管的计算
管径和管子材质选择
由设计参数换热管管径选用25×3,由于半水煤气和变换气都不具有强腐蚀性,所以根据以及GB151-2012选用低合金钢无缝钢管,材质选择Q345R。
传热管数和管程数
根据给定设计参数,换热管管数为295根,长度为6000mm。
因采用逆流方式传热,根据JB/T4715表4得,选择单壳程单管程传热。
传热管的排列
管子的排列方式有等边三角形,正方形,转角正方形三种。
与正方形相比,等边三角形排列比较仅凑,管外流体湍动程度高,表面传热系数大。
正方形排列虽然比较松散,传热效果也较差,但管外清洗比较方便,对易结垢流体更为适用。
若将正方形排列的管束斜转45°安装,可在一定程度上提高对流传热系数〔7〕。
根据设计参数,等边三角形排列,中心距34mm。
如图3-1。
图3-1管子三角形排列图
(图片来源于GB151-2012)
管心距为34mm(焊接时)。
则隔板中心到力气最近一排管中心距离:
(公式来源于GB151-2012)
根据《化工设备设计基础》〔7〕表5—3得,公称直径DN=700,管径
=25排管数目为见表2-3。
表3