渗透检测通用工艺规程编制.docx
《渗透检测通用工艺规程编制.docx》由会员分享,可在线阅读,更多相关《渗透检测通用工艺规程编制.docx(11页珍藏版)》请在冰豆网上搜索。
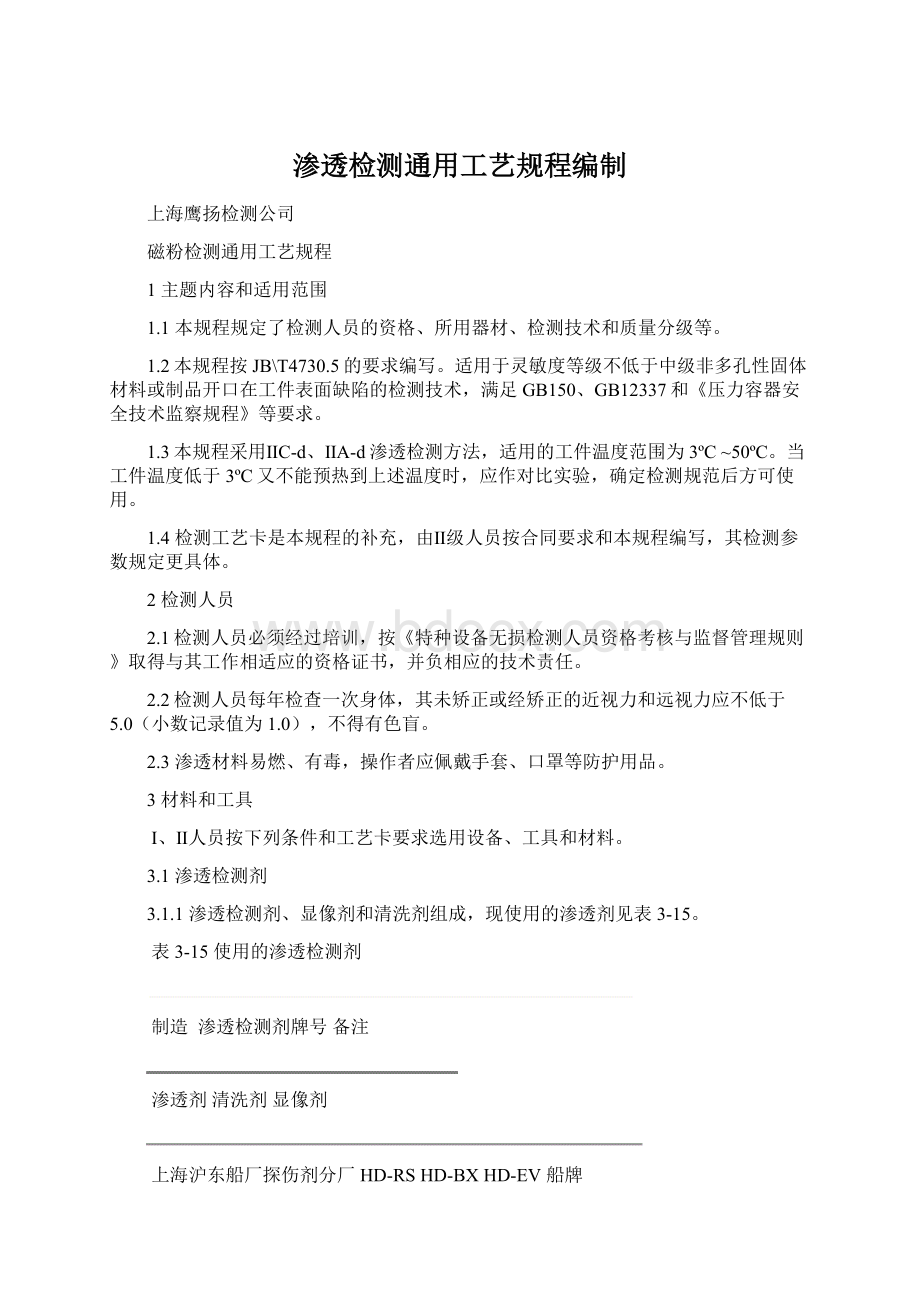
渗透检测通用工艺规程编制
上海鹰扬检测公司
磁粉检测通用工艺规程
1主题内容和适用范围
1.1本规程规定了检测人员的资格、所用器材、检测技术和质量分级等。
1.2本规程按JB\T4730.5的要求编写。
适用于灵敏度等级不低于中级非多孔性固体材料或制品开口在工件表面缺陷的检测技术,满足GB150、GB12337和《压力容器安全技术监察规程》等要求。
1.3本规程采用ⅡC-d、ⅡA-d渗透检测方法,适用的工件温度范围为3ºC~50ºC。
当工件温度低于3ºC又不能预热到上述温度时,应作对比实验,确定检测规范后方可使用。
1.4检测工艺卡是本规程的补充,由Ⅱ级人员按合同要求和本规程编写,其检测参数规定更具体。
2检测人员
2.1检测人员必须经过培训,按《特种设备无损检测人员资格考核与监督管理规则》取得与其工作相适应的资格证书,并负相应的技术责任。
2.2检测人员每年检查一次身体,其未矫正或经矫正的近视力和远视力应不低于5.0(小数记录值为1.0),不得有色盲。
2.3渗透材料易燃、有毒,操作者应佩戴手套、口罩等防护用品。
3材料和工具
Ⅰ、Ⅱ人员按下列条件和工艺卡要求选用设备、工具和材料。
3.1渗透检测剂
3.1.1渗透检测剂、显像剂和清洗剂组成,现使用的渗透剂见表3-15。
表3-15使用的渗透检测剂
制造渗透检测剂牌号备注
渗透剂清洗剂显像剂
上海沪东船厂探伤剂分厂HD-RSHD-BXHD-EV船牌
上海日用化学制罐厂GE-PLGE-WLGE-DL金睛牌
苏州美柯达器材厂DPTDPTDPT美柯达
注:
对同一检测件,不同类型的渗透检测剂禁止混用
3.1.2渗透检测剂的鉴定
(1)生产厂应对每批渗透检测剂的灵敏度和主要性能进行试验,出具合格证,标明生产日期和有效期。
进厂的渗透检测剂应在低温避光处存放。
(2)对镍基合金材料检测时,应有生产厂提供的一定量渗透检测剂蒸发后残渣中硫元素含量的重量比不超过1%的合格证明;对奥式体钢、钛及钛合金材料检测时,应有生产提供的一定量渗透检测剂蒸发后残渣中氯、氟元素含量的重量比不超过1%的证明。
3.2试块
3.2.1铝合金试块(A型对比试块)
铝合金试块尺寸如图3-13所示,试块由同一试块剖开后具有相同大小的两部分组成,并打上相同序号,分别表以A、B记号,A、B试块上均应具有细密相对称的裂纹图形。
主要用于:
(1)在标准温度使用的情况下,检测渗透检测剂能否满足要求,以及比较两种渗透检测剂性能的优劣;
(2)对非标准温度下使用,确定检测工艺参数。
3.2.2镀铬试块(B型试块)
将一块尺寸为130mm*40mm*4mm、材料为0Cr18Ni9Ti或其它不锈钢材料的试块上单面镀铬,用布氏硬度法在其背面施加不同负荷形成3个辐射状裂纹区,按大小顺序排列区位号分别为1、2、3,其位置、间隔及其他要求应符合JB\T6064B型试块相关规定。
裂纹尺寸分别对应JB\T6064B型试块上的裂纹区位号2、3、4.
主要用于检测操作系统检测灵敏度(中级灵敏度应显示裂纹区位号为2~3)及操作工艺的正确性。
3.2.3试块的清晰和保存
试块使用后要进行彻底清洗。
清洗通常用丙酮仔细擦拭后,再放入装有丙酮和无水酒精的混合液(混合比例1:
1)密闭容器中保存,或用其他有效方法保存。
3.3其他材料和工具
3.3.1对镍基合金、奥氏体不锈钢、钛及钛合金检测时,清理金属表面时需用不锈钢刷子。
3.3.2抹布:
去除多余渗透剂的抹布采用干净的棉布、无毛棉纱或吸水纸等。
3.3.3预清洗或后清洗采用的清洗剂除按表3-15选用外,还可用丙酮。
3.3.4照度计:
照度计用于测量白光照度。
3.3.5照明:
通常工件被检处白光照度应大于或等于1000lx;当现场采用便携式设备检测,由于条件所限无法满足时,可见光照度可以适当降低,但不得低于500lx。
4检测时机
4.1除非另有规定,焊接接头的渗透检测应在焊接工序完成后进行。
对有延迟裂纹倾向的材料,至少应在焊接完成24小时后进行渗透检测。
4.2紧固件和锻件的渗透检测一般应最终热处理后的检测结果为准。
5被检表面的制备
5.1任何表面的焊渣、飞溅和毛刺等必须处理到不掩盖的干扰缺陷显示为度。
5.2必须清理的表面的油污、锈蚀、氧化皮以及漆涂层等。
5.3表面可以打磨,但禁止使用喷砂或喷丸,以防堵塞缺陷开口。
5.4机加工价表面粗糙度Ra≤12.5μm。
5.5局部检测时,制造的范围应从检测部位四周向外扩展失少25mm。
5.6被检表面经检查人员和检测人员认可。
6检测技术
ⅠⅡ级人员检测前应查看喷灌外观质量及有效期。
使用新的渗透剂、改变或更换渗透剂类型或检测规程时,应采用镀铬试块检验系统灵敏度和操作工艺(条件不改变的情况下,每周进行一次),合格后方可按图3-14的程序进行检测。
如果检测面积太大,不能在规定的时间内完成,可将表面分成几个适当的区域进行测。
6.1预清洗
用本规程第3.3.3条规定的清洗剂去除被检区油污、锈蚀等干扰渗透检测的杂物。
清洗后,检测面上遗留的溶剂和水分等必须干燥,且应保证在施加渗透剂前不被污染。
6.2施加渗透剂
6.2.1清洗干燥后,可通过涂刷或喷雾施加渗透剂覆盖整个被检表面,并在整个渗透时间内保持润湿状态。
对于大批量的小工件,也可采用浸渍施加。
(a)溶剂去除型图3-14(b)水洗型
表3-6渗透滞留时间
最短渗透时间(min)最短的显像时间(min)
*3℃<10℃≥10℃-15℃3℃-<10℃≥10℃-50℃
25
注:
*3℃<10℃的渗透检测规范,是ASME取证时,工件温度为3℃,在授权检验师的监督下进行对比试验的数据。
6.3去除多余的渗透剂
6.3.1溶剂去除型
6.3.1.1规定的渗透时间过后,用抹布将多余的渗透剂擦掉。
6.3.1.2将少许清洗剂喷在抹布上,吧被检表面擦拭干净,禁止用清洗剂直接清洗和往复擦拭。
6.3.2水洗型
6.3.2.1用冲洗装置冲洗时,水射束与被检面的夹角以30º为宜,水温为10-40℃。
如无特殊规定,冲洗装置喷嘴处的水压不超过0.34MPa。
在无冲洗装置时,可采用抹布蘸水擦洗,严禁过清洗。
6.3.2.2清洗后的工件表面,用抹布擦干。
6.4干燥
用水洗型去除多余渗透剂后,工件表面应进行干燥处理。
可采用自然干燥或热风(小于或等于50℃)干燥,干燥时间一般为5-10min为宜;溶剂去除多余渗透剂后,应在室温下自然干燥。
6.5显像
6.5.1施加显像剂采用喷灌喷,要覆盖整个被检表面,形成均匀的薄膜,但禁止涂刷。
6.5.2施加显像剂之前,喷灌应摇动,以保持显像剂的悬浮状态。
6.5.3使用喷灌时,喷嘴距被检表面300-400mm,喷洒方向与被检表面夹角30º-40º为宜。
6.5.4显像时间从被检表面显像剂薄膜干燥后计算,不少于表3-16的规定时间。
6.6缺陷显示的观察和评定按本规程第7章处理。
6.7后清洗
检测完毕后应进行后清洗,可采用清洗剂或抹布去除。
7观察及评定
由Ⅱ级以上人员进行观察和评定。
7.1检测部位的照明应符合本规程第3.3.5条的要求。
7.2按表3-16给出的显像时间,在显像过程中,检测人员应注意观察渗透剂吸出扩散的趋势,以确定缺陷显示的种类。
做出最终评定应在60min内完成,如果吸出过程不影响检测结果,最终评定可超过60min。
7.3显示难以辨认真伪时,可用5-10倍放大镜观察。
当出现下列情况之一时,需进行复验:
(3)检测结束用试块验证检测灵敏度不符合要求时;
(4)发现检测过程中操作方法有误或技术条件改变时;
(5)合同各方有争议或认为有必要时。
7.4对返修和需复验的部位应彻底清洗,按本规程第6.1条-第6.7条的规定重新检测。
7.5渗透显示的分类
7.5.1长宽比大于3的缺陷显示,按线性缺陷处理;长宽比小于3的缺陷显示,按圆形缺陷处理。
7.5.2缺陷显示长轴方向与工件(轴类或管类)轴线或焊接接头中心母线的夹角大于或等于30º时,按横向缺陷处理,其他按纵向缺陷处理。
7.5.3两条或两条以上缺陷显示在同一直线上,当间距小于或等于2mm时,按同一条缺陷处理,其长度为缺陷显示长度之和加间距。
7.5.4小于0.5mm的显示不计。
8质量分级
8.1不允许任何裂纹和白点,紧固件和轴类零件不允许任何横向缺陷显示。
8.2焊接接头和坡口的质量分级按表3-17进行。
8.3其他部件质量分级评定见表3-18。
表3-17焊接接头和坡口的质量分级
等级线性缺陷显示圆形缺陷显示(评定框尺寸35mm×100mm)
Ⅰ不允许d≤1.5,且在评定框内少于或等于1个
Ⅱ不允许d≤4.5,且在评定框内少于或等于4个
ⅢL≤4d≤8,且在评定框内少于或等于6个
Ⅳ大于Ⅲ级
注:
L为线性缺陷指示长度,mm;d为圆形缺陷显示在任何方向上的最大尺寸,mm。
表3-18其他部件的质量分级
等级线性缺陷显示圆形缺陷显示(评定框尺寸为2500mm²,其中一条举行边长最大为150mm)
Ⅰ不允许d≤1.5,且在评定框内少于或等于1个
ⅡL≤4d≤4.5,且在评定框内少于或等于4个
ⅢL≤8d≤8,且在评定框内少于或等于6个
Ⅳ大于Ⅲ级
注:
L为线性缺陷显示长度,mm;d为圆形缺陷显示在任何方向上的最大尺寸,mm。
超声检测通用工艺规程
1一般要求
1.1主题内容与适用范围
1.1.1本规程规定了检测人员资格、仪器、探头、试块、检测范围、检测方法和质量分级等。
1.1.2本规程按JB/T4730.3编制,采用A型脉冲反射式超声探伤仪器,适用于压力容器的钢板、锻件和焊接接头的检测。
符合《压力容器安全技术监察规程》、GB150和GB12337等要求。
1.1.3检测工艺卡是本规程的补充,由Ⅱ级人员按合同要求及本规程编制,其检测额参数规定得更具体。
1.2规范性引用文件
JB/T4730.3─2005《承压设备无损检测》第3部分:
超声检测
GB150─1998《钢制压力容器》
JB/T7913─1995《超声检测用钢质对比试块的制造和校验方法》
JB/T9214─1999《A型脉冲反射式超声波探伤系统工作性能测试方法》
JB/T10061─1999《A型脉冲反射式超声波探伤仪通用技术条件》
JB/T10062─1999《超声波探伤探头性能测试方法》
JB/T10063─1999《超声探伤用1号标准试块技术条件》
GB12337─1998《钢制球形储罐》
SY/T4019─2005《石油天然气管道无损检测》
1.3检测人员
1.3.1检测人员必须经过培训,按《特种设备无损检测人员考核与监督管理规程》的要求,经理论实践考试合格,取得相应的等级资格证书。
检测由Ⅱ级以上人员进行,Ⅰ级人员仅作检测的辅助工作。
1.3.2检测人员每年应检查一次身体,其未经矫正或经矫正近(距)视力和远(距)视力应不低于5.0(小数记录值为1.0)
1.4仪器、探头和试块
1.4.1仪器和探头
使用汕头超声仪器厂生产的CTS─22、CTS─26和CTS─2000型仪器和探头。
(1)探伤仪
采用A型脉冲反射式超声波探伤仪,其工作频率范围为0.5MHz─10MHz,仪器至少在荧光屏满刻度的80%范围内呈线性显示。
探伤仪应具有80dB以上的连续可调衰减器,步进级每挡不大于2dB,其精度为任意相邻12dB的误差在±1dB以内,最大累计误差不超过1dB。
水平线性误差不大于1%,垂直线性误差不大于5%。
其余指标应符合JB/T10061的规定。
(2)探头
1晶片面积一般不应大于500mm²,且任意边长原则上不大于25mm。
2单斜探头声束轴线水平偏离角不应大于2°,主声速垂直方向不应有明显的双峰。
(3)超声探伤仪和探头的系统性能
1在达到所探工件的最大检测声程时,其有效灵敏度余量应不小于10dB。
2仪器和探头的组合频率与公称频率误差不得大于±10%。
3仪器和直探头组合的是脉冲宽度(在基准灵敏度下):
对于频率为5MHz的探头,宽度不大于10mm;对于频率为2.5MHz的探头,宽度不大于15mm。
4直探头的远场分辨力应不小于30dB,斜探头的远场分辨力应不小于6dB。
5仪器和探头的系统性能应按JB/T9214和JB/T10062的规定进行测试。
1.4.2试块
(1)试块分为标准试块和对比试块两种。
试块应采用与被检工件相同或声学性能相近的材料制成,该材料用直探头检测时,不得有大于ø2mm平底孔当量直径的缺陷。
(2)标准试块的制造要求应符合JB/T10063和JB/T7913的规定。
(3)现场检测时,也可采用其他的对比试块。
1.5检测的一般方法
1.5.1扫查覆盖率
检测时,探头每次扫查的覆盖率应大于探头直径的15%。
1.5.2探头的移动速度
探头移动的扫查速度不应超过150mm/s。
当采用自动报警装置扫查时,不受此限制。
1.5.3扫查灵敏度
扫查灵敏度不低于基准灵敏度。
1.5.4耦合剂
采用机油、糨糊、甘油、专用耦合剂和水等透声性好,且不损伤检测表面的耦合剂。
1.5.5检测面的制备
(1)所确定的检测面应保证工件被检部分均能得到充分检查。
(2)检测面应经外观检查合格,所有影响超声检测的锈蚀、飞溅和污物都应予以清洗,表面的不规则状态不得影响检测结果的准确评定,否则应做适当的修磨。
对于锻件其表面粗糙度Ra小于或等于6.3μm。
1.5.6灵敏度补偿
灵敏度补偿包括耦合补偿、衰减补偿和曲率补偿,应按不同检测方法确定其补偿值,计入检测灵敏度中。
1.6系统校准和复核
1.6.1仪器校准
每隔三个月至少对仪器的水平线性和垂直线性进行一次测定,测定方法按JB/T10061的规定进行。
1.6.2新购探头测定
新购探头须有探头性能参数说明书,新探头使用前应进行前沿距离、K值、主声束偏离、灵敏度余量和分辨力等主要参数的测定。
测定方法应按JB/T10062的有关规定进行,并满足其要求。
1.6.3检测前仪器和探头系统测定
(1)使用仪器─斜探头系统,检测前应测定前沿距离、K值和主声束偏离,调节或复核扫描量程和扫查灵敏度。
(2)使用仪器─直探头系统,检测前应测定始脉冲宽度、灵敏度余量和分辨力,调节或复核扫描量程和扫查灵敏度。
1.6.4检测过程中仪器和探头系统的复核
遇有以下情况应对系统进行复核:
(1)校准后的探头、耦合剂和仪器调节旋钮发生改变时;
(2)检测人员怀疑扫描量程或扫查灵敏度有变化时;
(3)连续工作4h以上时;
(4)工作结束时。
1.6.5检测结束前仪器和探头系统的复核
(1)每次检测结束前,应对扫描量程进行复核。
如果任意一点在扫描线上的偏移超过扫描线读书的10%,则扫描量程应重新调整,并对上一次复核以来所有的检测部位进行复检。
(2)每次检测结束前,应对扫查灵敏度进行复核。
一般对距离-波幅曲线的校核不应少于3点。
如曲线上任何一点幅度下降2dB,则应对上一次复核以来所有的检测部位进行复检;如幅度上升2dB,则应对所有的记录心好进行重新评定。
1.7报告和存档
按报告格式由Ⅱ级以上人员填写报告,经责任工程师认可后,转捡查科(资料室)存档,保存时间不少于7年。
2承压设备钢板的超声检测
2.1适用范围
本条适用于板厚为6~250mm的钢制压力容器用板材的超声检测和质量分级。
奥氏体钢板的超声检测也可参照本条执行。
2.2探头的选用
2.2.1探头应按表3-19选用。
表3-19承压设备用板材超声检测探头援用
板厚,mm采用探头公称频率,MHz探头晶片尺寸
6-20双晶直探头5晶片面积不小于150mm²
20-40单晶直探头5Φ14mm-Φ20mm
40-250单晶直探头25Φ20mm-Φ25mm
THANKS
致力为企业和个人提供合同协议,策划案计划书,学习课件等等
打造全网一站式需求
欢迎您的下载,资料仅供参考