我国玻璃纤维工业现状与差距.docx
《我国玻璃纤维工业现状与差距.docx》由会员分享,可在线阅读,更多相关《我国玻璃纤维工业现状与差距.docx(12页珍藏版)》请在冰豆网上搜索。
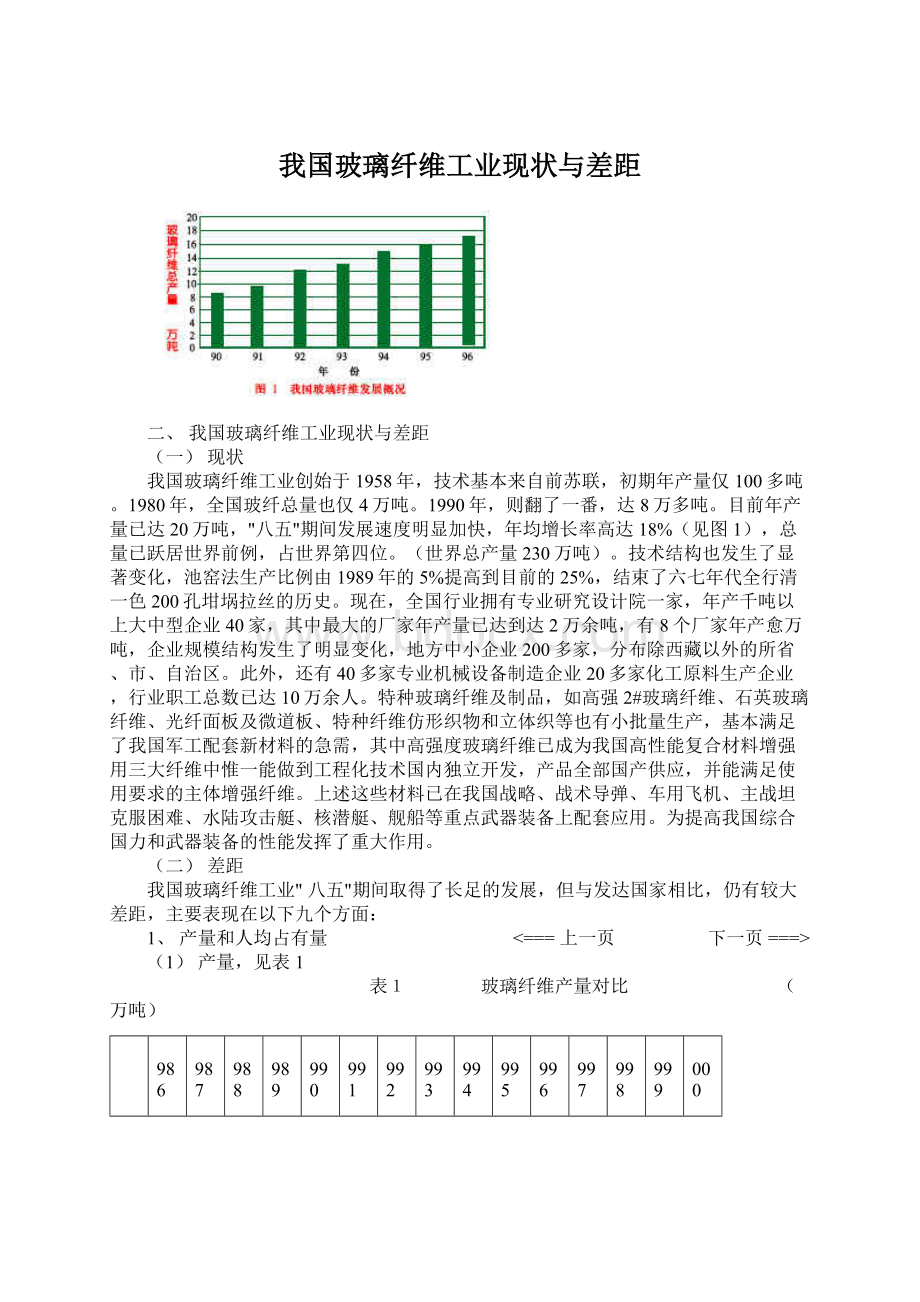
我国玻璃纤维工业现状与差距
二、我国玻璃纤维工业现状与差距
(一)现状
我国玻璃纤维工业创始于1958年,技术基本来自前苏联,初期年产量仅100多吨。
1980年,全国玻纤总量也仅4万吨。
1990年,则翻了一番,达8万多吨。
目前年产量已达20万吨,"八五"期间发展速度明显加快,年均增长率高达18%(见图1),总量已跃居世界前例,占世界第四位。
(世界总产量230万吨)。
技术结构也发生了显著变化,池窑法生产比例由1989年的5%提高到目前的25%,结束了六七年代全行清一色200孔坩埚拉丝的历史。
现在,全国行业拥有专业研究设计院一家,年产千吨以上大中型企业40家,其中最大的厂家年产量已达到达2万余吨,有8个厂家年产愈万吨,企业规模结构发生了明显变化,地方中小企业200多家,分布除西藏以外的所省、市、自治区。
此外,还有40多家专业机械设备制造企业20多家化工原料生产企业,行业职工总数已达10万余人。
特种玻璃纤维及制品,如高强2#玻璃纤维、石英玻璃纤维、光纤面板及微道板、特种纤维仿形织物和立体织等也有小批量生产,基本满足了我国军工配套新材料的急需,其中高强度玻璃纤维已成为我国高性能复合材料增强用三大纤维中惟一能做到工程化技术国内独立开发,产品全部国产供应,并能满足使用要求的主体增强纤维。
上述这些材料已在我国战略、战术导弹、车用飞机、主战坦克服困难、水陆攻击艇、核潜艇、舰船等重点武器装备上配套应用。
为提高我国综合国力和武器装备的性能发挥了重大作用。
(二)差距
我国玻璃纤维工业"八五"期间取得了长足的发展,但与发达国家相比,仍有较大差距,主要表现在以下九个方面:
1、产量和人均占有量 <===上一页 下一页===>
(1)产量,见表1
表1 玻璃纤维产量对比 (万吨)
1986
1987
1988
1989
1990
1991
1992
1993
1994
1995
1996
1997
1998
1999
2000
美国
62.88
77
71.3
70.37
70
85
90
96
西欧
33.37
36.8
42.2
47.1
43.8
43.2
44.9
43.7
51.1
56
60
中国
6.7
7.05
7.42
8.29
8.8
9.68
12.06
13
14.9
16
17.2
22
(2)人均占有量,见图2。
人均占有量北美地区第一为3.4kg/人(其中美国为3.7/人),为全球玻纤消费最高地区,日本第二为2.1kg/人,东欧为0.6kg/人,中国为0.13kg/人,拉美为0.1kg/人,中国与工业发达国家差距较大。
2、企业布局不合理,生产规模小、效益差
国外玻纤池窑规模大都是万吨以上,最大规模已达6万吨,且已发展为群体工程,产业规模和企业规模都很大,有的已超过数10万吨。
我国玻璃纤维企业数量多、规模小、分布广。
近几年,在玻纤技术引进和技术改造方面的投入约10亿元人民办币。
但由于宏观调控不力,资金使用分散,引进或改造的生产主线年产量大部分仅为千吨左右,出现了低水平,重复引进的现象。
行业大部分企业规模在1000-5000吨的水平上,难以产生规模效益。
表2玻璃纤维工业企业/生产规模对比
序号
项目
中国
美国
1
总产量(万t/a)
16
90
2
生产厂商(公司)规模(万t/a)
240
6
3
最大生产企业(公司)规模(万t/a)
2.8
40
4
最小生产企业(公司)规模(万t/a)
0.03
1
5
最大池窑生产能力(万t/座·a)
1
6
3、生产工艺技落后,能耗高,和平效率低
国际上玻纤生产大都采用800-4000孔漏板的池拉丝技术,最近已达6000孔。
其产量已占总产量的95%以上,无纺材料生产全部采用池窑法;坩埚法已被淘汰。
而国内75%以上仍采用坩支技术生产,能量高,生产效率低,单机的日产量为110-350kg。
国内现有的池窑生产线与国外相比,也有较大差距,详见表3。
表3国内坩埚法与国外池窑法生产技术及主要技术经济指标比较
坩埚法
国外池窑
国内池窑
生产规模(块漏板/座)
由坩埚多少决定
20-1200
7-32
漏板孔数(孔/台)
200-400
800-6000
800-2000
单机产量(kg/d·台)
110-350
700-2000
570-1000
拉丝机卷装量(kg/筒)
0.5-3.0
4.0-25.0
4.0-25.0
纺织纱卷装量(kg/锭)
0.5
4.0
4.0
粗纱卷装量(kg/ 筒)
16-25
16-180
16-25
能耗(t标煤/t纱)
2-4
<1.0
1.5
铂耗(g/t纱)
<2.0
<0.5
<0.5
实物劳动生产率(t/a· 人)
2-4
30-220
20
4、产品结构不合理,产品品种少、质量差
目前,世界玻璃纤维产品品种已有3000多种,规格50000多种,其中70%-80%用于树脂增强复合材料的增强基材,如各类玻纤纱、玻纤材等制品。
产品品种多、质量好,且实现了系列化、标准化。
国际上无纺材料已成为玻纤工业主要产品,发展十分迅速,前景非常广阔,大量用热塑料的增强材料,在建筑和交通运输及电子业有着广泛地应用,其市场容量约占玻纤总产量的80%。
我国玻璃纤维中碱占70%左右,而且仅有60多个品种,600多种规格,纤维支数不匀率偏差较大,产品质量不高。
树脂基复合材料用高品质增强基材,如玻纤连续毡、针刺毡、短切毡、湿法薄毡等毡材以及军用特种玻璃纤维由少,甚至是空白,无法满足复合材料机械化成型的需求,以至于复合材料的研究开发者要利用力学设计的办法来弥补基材品种缺少的不足,甚至不惜代价进口基材,严重影响到引进玻璃钢机组的正常生产。
据统计,全国已引进玻璃生产设备100多台(套),而平均开工率仅30%左右,全国已引进电子工业用覆铜板生产线10多条,每条和平线年产覆铜板500万m2,年需用7628就达到6000万m以上。
目前引进生产线能力仅为1000万m,而至今尚无以国产化技术生产的高品质的G级玻璃纤维织物等基材,满足不了市场需要,缺口很大,国家每年要花数千万美元外汇进口基材。
这种基础原料工落后于加工工业的状态已严重影响到玻璃钢制品及电子工业的应用领域开发,严重影响我国军用高性能结构功能材料的研制配套,也必然严重影响玻璃纤维工业自身的发展。
5、玻璃纤维织物及其后处理技术落后,制品性能低,无法满足高技术领域的需求
玻璃纤维织尤其是印制是路板等高新技术领域用玻纤织物要求十分严格,工业发达国家均采用浆纱工艺,低捻单纱织造,再经热清洗处理和表面化学处理等技术生产,为提高和确保玻纤织物性能、质量提供了极为重要的技术保证。
我国目前尚没有(缺少)上述成套先进技术装备。
由于我国玻璃纤维大都采用坩埚法生产,纤维品质低,纱线卷装量小,仅为1000m,接头多,而美、日等发达2000-3000m。
我国纱线捻度较高,达到40捻/m上,无法保证织物表面平整度和树脂浸透速度,而美、日则在28捻/m以下。
后处理技术由于国外的严密封锁,差距更大:
连续热处理或分批热处理织物的白度低,保留强度不稳定,偶联剂品种少,稳定性差,配制技术落后,还有跑偏、接头、恒张力控制等均达不到严格的规定要求,无法生产出高品质的玻纤织物。
此外。
我国高性能的玻璃纤维立体织物技术综合水平及能力不满足不了我国军用高性能结构-防热-透波多功能材料发展的要求。
6、特种玻璃纤维应用领域差距较大
我国特种玻璃主要为军工和高新技术产业配套。
由于特种玻璃纤维尚未形成产业化,从产量、质量、品种等三个方面与国外应用领域相比,差距较大,例举如下:
(1)高强度玻璃纤维方面
表4国内外高强度玻璃针维应用领域对比表 <===上一页 下一页===>
应用产品及需求量
国外(1991年)
国内(1995年)
年总需求
2480t(其中美国1560t)
40t
直升飞机
320t
试验
重型装备
270t
30t
其中:
导弹发动机
有
3-5t
我国玻纤产量至2000年达到21万吨。
2010年将达到34万吨以上,市场需求潜力巨大。
国际上几大著名玻纤公司为争取中国市场的最大份额,纷纷前来我国洽谈独资、合资办厂事宜,对中国玻纤这一民族工业构成了很大威。
胁法国博舍公司与中国华原纺织集团有限公司合资,在上海市青浦县中国纺织工业城,新建一座年产2500万m的确8布工厂,法方股份占85%。
由于我国玻纤工业起步较晚,投入总量不足,工艺装备水平低,产品能耗高、质量差,届时将面临激烈技术竞争的严峻考验。
为确保玻纤这一民族工业的健康发展,打破国际垄断,迅速改变我国玻纤落后面貌,我们必需认清形势,采取有效措施和对策,抓住机遇,夯实基础,迎接挑战。
21世纪我国国防现代化建设要实现建成现代化军兵种目标,对待特种玻璃纤维提出强劲的挑战。
必须密切配合国防重点战略武器和技术武器发展的需求;开发新一代结构纤维、功能纤维特种织物,提高现有的特种玻璃纤维生产能力,稳定质量、降低成本,迎接挑战。
四、战略目标和发展重点
(一)战略目标
根据我国国民经济、国防军工及高科技发展的需要,以支柱产业为重点,以满足国防军工配套新材料的迫切需求为向导,集中力量,攻克高效、节能、优质的池窑拉丝生产技术及多排多孔大漏板的设计、加工和安装技术、多品种、系列化、、高品质浸润剂和粘结剂技术,推动行业的技术进步和快捷发展。
在此基础上,开发一批高品质玻璃纤维制品的规模生产技术,不断调整企业结构和产品结构,使国内玻纤总体生产水平和产量达到90年代国际先进水平,实现以下目标。
表7玻纤总目标
此外,要加强特种玻璃纤维的应用基础研究,开发低成本、高性能、特种用途的玻璃纤维及制品的制备技术,研究多功能特种玻璃纤维立体织物的编织技术,以满足国防军工新一代武器装备为突破口。
逐步扩大应用领域,推动学科的发展。
(二)发展重点
1、基础研究
(1)无碱无硼低氟玻璃成份研究,探索降低资源、环境负荷新技术。
(2)玻纤超速冷却型机理研究,提高拉丝速度30%以上,以提高单机产量。
3)玻纤浸润剂、玻纤界面与复合材料性能三维空间相互关系的研究,在分微观结构的基础上,建立数学模型。
(4)特种纤维织物组织、结构与性能的关系的研究,为开发应用提供理论依据。
(5)微通道板皮、芯、吸收料三组分优化相图及皮芯微观结构研究,开发第三四代微通道板、弯曲通道微通板和异型光学纤维面板器件。
(6)宽频带反制导干扰无机新材料研究。
2、工程技术研究
(1)用万吨级玻璃纤维池窑拉丝技术,推动行业的技术进步,加速行业的跨越式发展,缩小与发展发达国家的差距。
建议国家采取有效措施,继续支持先进池窑的消化吸收与创新工作,攻克6-8万t/a规模的池窑技术、4000-6000孔高效率纤维成型技术、形成具有我国自主知识产权的池窑拉丝技术。
(2)实施可持续发展战略,开展玻纤环境、节能工程技术研究。
--玻纤池窑余热的二次利用技术。
采用余热锅炉、热水换热器、金属换热器等多种形式,开展余热利用技术研究,不断提高玻纤池窑热效率。
--废丝的综合利用技术。
重点研究废丝回窑技术以及以废丝为原料的新产品制备技术。
--玻纤池窑纯氧燃料技术。
。
研究纯氧助燃系统工艺与装备及相应的单元窑结构形式达到节能50%、提高熔化效率、改善玻璃质量、延长窑炉寿命、降低环境污染的目的。
(3)加强新产品的开发应用技术研究。
攻克一批高品质玻纤制品的规模生产技术,重点研究玻纤无纺材料的大幅宽、大规模生产技术,在交通运输,电子和建筑等应用领域要有重大突破。
(4)开展优质高产精细玻璃纤织物工艺与装备的攻关,重点攻克低捻卷装退介技术、高速一次整经技术、高效率浆纱技术、宽幅大卷装喷气织机织造技术及后处理等技术关键,实现玻纤织物用设备,如预脱浆机、热脱浆机及表面处理机及配套的浆料、偶联剂、表面处理添加剂的国产化。
提高织物性能,扩大应领域。
(5)加强特种玻璃纤维及制品的低成本、高性能制造技术研究,满足国防军工新一代武器装备对配套新材料需要,重点开发:
新一代高强度玻璃纤维、低介电、抗静电、屏蔽玻璃纤维、可编织二氧化硅玻璃纤维、氧化铝纤维、高强度空心玻璃纤维、耐辐照玻璃纤维,超低损耗光学玻璃纤维。
(6)加强特种三四代微光夜视仪关键器件及电磁波和红外雷达干扰材料及工艺技术研究,以提高我军全天候作战能力。
--超低损耗高光透过率光学纤维面板及生产技术研究。
--长寿、低噪声三代四代微通道板及单光子倍增器件和新工艺技术研究。
--大截面玻璃光纤象束生产技术水平研究。
--电磁波和红外雷干扰箔条及生产技术研究。
(7)加强防热-透波-承载等多功能特种玻璃纤维立体织物及编织技术研究,推动学科进一步发展。
--混杂纤维的编织技术研究。
采用不同性能的纤维,编织成整体织物,形成具有多种纤维的复合材料基材,以满足武器装备对材料的多功能要求。
混杂纤维编织技术要攻克纤维混杂形式对性能的影响,混杂过渡区域的结构特性及均匀性等编织技术关键。
--三维多向织物及编织技术研究。
三维编织技术是立体织物的重要成形技术,三维编织可以编织四向、五向、七向等多向织物,满足不同应用环境下的使用要求,开展该项技术研究一方面要满足新一代导弹弹头防热承载的工程急需,同时要开展编织工艺与结构对应关系的研究。
攻克三维十三向编织技术,使该学科达到世界领先水平。
--机织、针织及组合结构的立体织物的研究。
随着立体织物编织技术的发展,低成本、高速度、大尺寸的编织技术和织物受到了军用及其他工业领域的高度重视。
为此,开展机织、针织及组合结构的立体织物研究,将机织、针织有机组合,研究低成本,高速度成型的立体织物,为21世纪立体织物的扩大应用提供技术保证。
仿形计算技术整体厚织物的研究。
实际使用的纤维增强复合材料,不仅要有很高的结构强度,而且还要求具有异形曲面,如导弹、飞机整流罩等。
为此,开展本项研究要攻克异形曲面的仿形技术、异形结构整体厚织物编织等技术关键,使我国武器装备的头罩彩整体复合材料头罩,提高战术水平。
--等高度站位厚度仿形技术的研究。
高性能飞机透波雷达罩不仅要有高的结构强度,还要有良好的透渡性能,是飞机研制的关键技术之一,该技术主要解决变厚飞机雷达罩的技术关键,通过研究控制等高度站位技术关键及仿形技术,确保雷达罩电度要求的变壁厚的实现。
五、建议与对策
1、建立玻纤池窑工业性试基地和玻璃纤维评价心,跟踪世界先进技术,推动行业总体水平不断提高。
2、加强资金投入,重视特种玻璃纤维及织物的基础研究、应用技术技术研究和工程化技术开发。
3、发展玻璃纤维民族工业要与引进外资、引进技术有机结合起来,促使我国玻纤工业健康、快速发展。
4、强制贯彻玻璃纤维的产业和技术政策,努力加强标准化工作。
实现玻璃纤维工业的技术结构和产品结构的调整及市场的规范。
5、加强宏观调控,调整企业结构,要逐从逐步从粗犷形经营向集约化、规模化经营转变。
到2010年,企业要达到年产3-5万吨的经济规模。
玻璃纤维包括连续玻璃纤维和特种玻璃纤维及制品,它是一类性能优异的无机非金属材料,也是国民经济、国防建设和高新技术不可缺少的配套基础材料,由于它具有为燃、耐高温、电绝缘、拉伸强度高、化学稳定性好、吸音、绝热等一系列综合优良特性,而且可以通过组分结构或工艺设计使其具有各种用途所需要的特殊性能,还可以采用表面改性技术不增加适制品深加工工艺及扩大制品应用技术领域所需的特殊性能。
因此,玻璃纤维包括高强度玻璃纤维、高弹性模量玻璃纤维、耐辐射玻璃纤维、高强度空心玻璃纤维、镀金属玻璃纤维、非通迅光学纤维、光学纤维面板、微通道板、特种织物等。
玻璃纤维用途十分广泛,可用作增强材料,代替传统的金属材料、木材、混凝土材料等,还可用作电绝缘材料、工业及环境保护用高温耐腐蚀过滤材料、保温吸音材料、光学及其他功能材料等,其应用领域不仅广泛涉及到石油、化工、炼建筑、交通运输、医药卫生、农业等传统产业部门,还广泛涉及到航空、航天、舰船、电子、核能、兵器、通讯等国防及高新技术部门,推动了这些部门的技术进步及产品质量的提高。
尤其是特种玻璃纤维及织物在发展新型战略、战术武器,提高作战性能等国防建设方面起到了极其重要的作用。
历来受到各国政府的重视和支持,年均发展速度都在10%以上。
我国的战略、战术导弹的发动机壳体、弹头防热材料、透波材料、飞机雷达罩、核能开发以及水中兵器等都离不开高强度玻璃纤维和特种纤维仿形织物及立体织物;高光透过率的光纤面板、窗口材料及微通道板等光纤材料已经用在我国兵器重大配套工程;高强度心玻璃纤维和高硅氧玻纤已应用在战略术导弹中以改善耐烧蚀隔热性能;国防重点工程需用低介电玻纤提高雷达波的高透能力;涂金属玻璃纤维是实现反制导的干扰材料;非通讯光纤已成为传感、传能、传象、传光的军工产品和高科技产品中不可缺少的重要材料。
因此,它不仅是促进传统产业技术进步和发展高新技术所需的基础材料,而且其本身就是高新技术领域的一个组成部分,在国民经济和国防建设中起着举足轻重的作用。
历史的画卷翻开了21世纪的扉页。
世纪之交,全面分析国际经济形势,得出了一个结论:
经济全球化趋势已经和正在给各国经济发展带来深刻的影响,我们既面临着新的发展机遇,也面临着严峻的挑战。
我国玻纤工业走过了42年的成长路程。
改革开放,特别是"八五"以来,这个新兴的产业得到了长足发展,但与全外发达国家玻纤工业相比还存差距,主要表现在:
一是行业整体技术水平较低,池窑拉丝技术和国际水平相比仍有差距。
要国内玻璃纤维产品总量中,池窑产品产量不到30%(国外占95%),还有70%以上为代铂漏板坩埚法技术所生产;制品加工技术装备特别是纺织制品加工设备仍然是五六十年代的老设备,很难生产出优质产品。
二是企业规模小,过于分散。
我国拥有约240家玻纤企业,在1999年只生产了18万吨玻璃纤维,最大生产企年产2.8万吨,最小的企业年产300吨,最大池窑规模1万吨,而美国6个公司年产90万吨,最大企业年产40万吨,最小企业也有万吨,池窑最大规模为6万吨。
如此小而散的企业结构,是难以和国际跨国集团公司较量和竞争的。
三是产品结构不合理,名牌产品有待开发。
优质产品比较少,而中低档产品太多过且总量过剩,只能适应国内市场和国外市场某些用户的需要。
因此,我国玻璃纤维工业要抓住结构调整这条主线,通过资产重组、技术创新、新产品开发,优化企业结构、技术结构和产品结构,从而提高行业整体素质,增强竞争实力,以顺应经济全球化的历史潮流。
以资产为纽带,优化企业结构
无机非金属新材料中,长期发展规划要求,我国玻璃纤维产量2005年要达到30万吨,池窑拉丝产品要占总产量的60%;2010年产量达45-50万吨,池窑拉丝占80%。
"十五"期间要重点支持形成3-5个年产量3万吨以上规模,并具有国际竞争力的大型企业集团。
中化建集团巨石公司2001年产量将超过4万吨,规划2005年将超过10万吨;泰山复合材料厂已实现了债转股,第二期1.5万吨级池窑拉丝生产线将在2001年初投产,年产能力超过3.5万吨,到2005年也将形成具有年产3万吨以上的生产能力。
以上三大玻纤公司将发挥其在资本运营、技术创新、市场开拓等方面优势,在同内外市场需求景气的舰带动下,成为玻纤行业的航母舰和主力舰,成为参与国际竞争的产要力量。
对于那些产品没有市场,但负担过重、经营困难的企业,通过兼并、联合等形式进行资产重组和结构调整,盘活存量资产。
对那些产品没有市场,经营不善,负债累累,资不抵债的企业可以实行破产、转业、拍卖等。
大力发展多种所有制形式的玻璃纤维制品深加工企业。
今后中、小型玻纤企业除少部规模化或进入企业集团之外,大部分将改造成为专业的制品加工厂。
加大技术创新力度、促进技术进步和产业升级
要使玻纤工业持续、快速、健康发展,必须适应全球产业结构调整的大趋势,加快技术进步和产业升级,要以市场为导向,采用高新技术和装备改造玻纤工业,围绕开发新品,提高质量,增加效益和扩大出口,加大现有企业技术创新的力度,以适应高新技术产业和传统产业对玻璃纤维产品的需求。
<===上一页 下一页===>
、积极推广和完善池窑拉丝技术和制品加工技术,提高玻纤工业整体和平技术水平。
要支持和推进大中型池窑拉丝和平线建设,开展日熔化量为60-120吨大型池窑的研究设计,研究和推广4000-6000孔特大漏板和多分拉等纤维成形技术,采用纯氧燃烧技术和电助熔技术,进一步降低能耗,提高劳动生产率。
大力推广先进技术和稳定池窑操作,努力提高成品率和扩大品种。
鉴一协内外玻璃纤维市场变化多端,建设池窑操作拉丝生产线切不可一哄而起,更要防止低水平和重复建设,发展规模速度应根据市场变化而定。
坩埚法拉丝技术在今后仍有一定的发展空间,但要限制新建坩埚法生产线,并围绕提高质量,降低能耗,提高成品率和劳动生产率等加强对现有坩埚生产线进行技术改造和设备更新。
要加大淘汰落后的陶土坩埚拉丝工艺技术设备的力度。
2、推广适应多种不同基材、不同成形工艺、不同用途的拉丝浸润剂。
增强型浸润剂要形成配套的系列产品,配方中必须含有偶联剂,711、811无蜡非增强型浸润剂应予以淘汰。
纺织型浸润剂必须彻淘汰已经用了40多年的石蜡型浸润剂。
行业技术政策上要明文规定,所有无碱、中碱玻纤纺织制品都应逐步采用淀粉型系列浸润剂。
3、加快纺织加工技术改造,逐步淘汰落后装备。
玻纤工业从50年代开始采用的150B捻线机、槽筒落纱机、分条整经机、1511有梭织机等老设备,已经不可能生产出具有国际市场竞争力的产品,因此必须下决心淘汰。
我们要利用纺织行业设备更新的成果,使技术装备适应玻璃纤维生产要求。
有条件的企业也可以引进国外先进设备。
同时,要积极开发玻纤织物的各种表面处理和涂层技术,完善各向同性的无纺织物,从而扩大玻纤制品的应用范围。
调整产品结构、扩大国内外市场
目前,我国增强型玻璃纤维制品已占玻纤总产量的50%,无碱制品占55%以上,连同纺制品,估计有800余个品种规格,国外则有3000余个品种规格,4万余种用途。
可见我国玻纤制品有待开发的领域宽广。
开发玻纤制品,扩大应用领域必须充分发挥玻璃纤维强度高、耐腐蚀、不燃烧、耐高温、电绝缘性能好、伸长率低等物化特性的优势,尽量避免用在磨损的领域,在选择试制新产品和推广应用中,一定要扬长避短。
每个企业在选择自己的产品发展方向时,一是要注意市场信息,了解国内外市场需求变化;二是发挥玻纤物化特性的优势;三是尽量不和化学纤维、合成纤维撞车,如果不可避免,就必须在性能上、应用上或价格上胜其一筹;四是要从企业实际出发,发挥自己的优势。
调整产品结构是一个长期的需要不断进行的工作。
其含义一是老产品更新换代,并不断赋予其新的性能;二是创试新的品种,开发新的用途。
企业选定产品之后,就一定要坚持做好,具有自己的特色,拥有自主知识产权,创名牌、精品,而且要不断提高质量、更新换代