特种陶瓷材料实验指导书.docx
《特种陶瓷材料实验指导书.docx》由会员分享,可在线阅读,更多相关《特种陶瓷材料实验指导书.docx(10页珍藏版)》请在冰豆网上搜索。
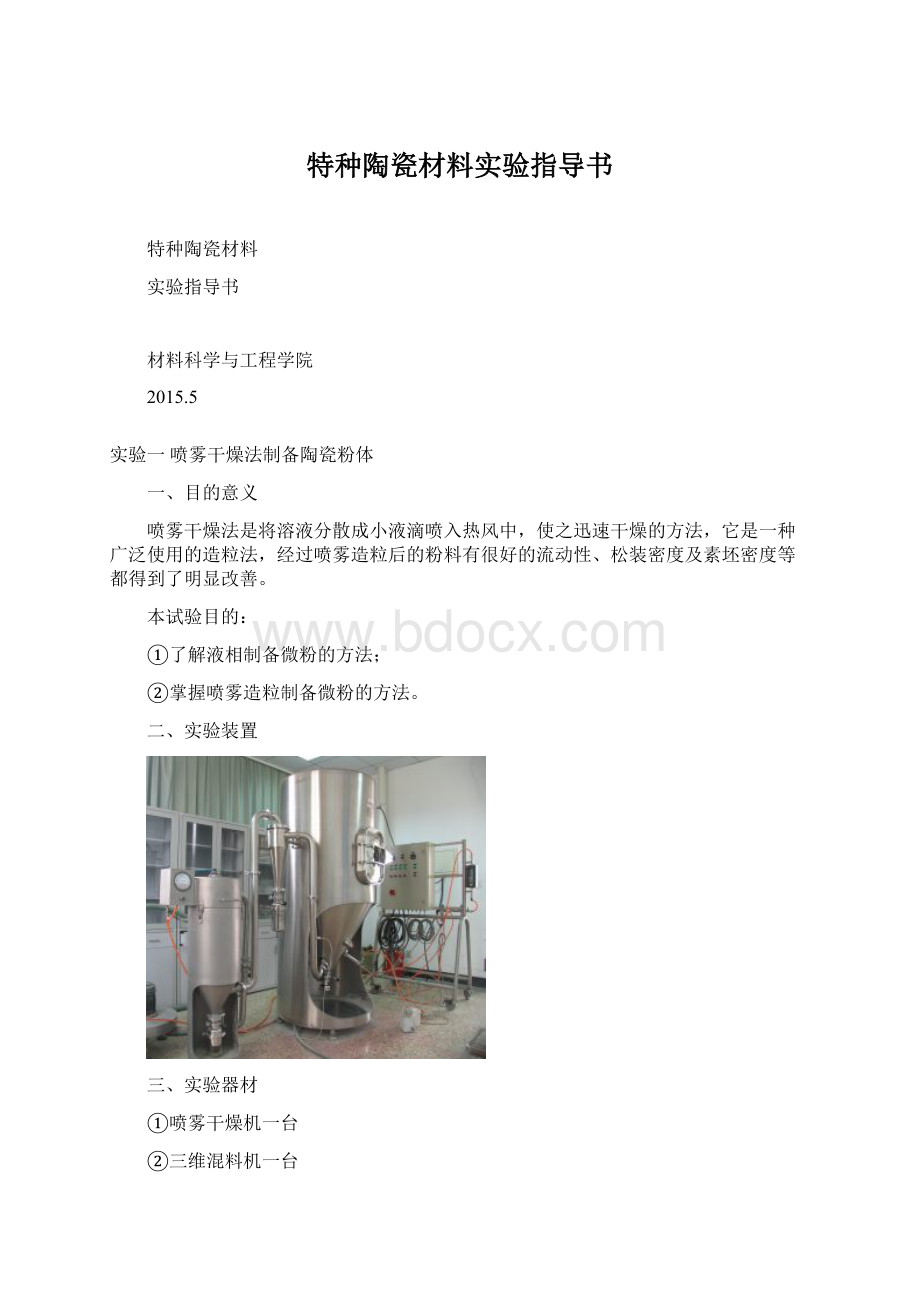
特种陶瓷材料实验指导书
特种陶瓷材料
实验指导书
材料科学与工程学院
2015.5
实验一喷雾干燥法制备陶瓷粉体
一、目的意义
喷雾干燥法是将溶液分散成小液滴喷入热风中,使之迅速干燥的方法,它是一种广泛使用的造粒法,经过喷雾造粒后的粉料有很好的流动性、松装密度及素坯密度等都得到了明显改善。
本试验目的:
①了解液相制备微粉的方法;
②掌握喷雾造粒制备微粉的方法。
二、实验装置
三、实验器材
①喷雾干燥机一台
②三维混料机一台
③电子天平一台
④粘度计4台
⑤塑料搅拌罐四个
⑥油酸、添加剂、乙醇、蒸馏水等
⑦玻璃器皿
四、实验步骤
①设计SiC陶瓷粉料不同的配方;
②用三维混料机制备流变性能良好的料浆;
③将制备好的料浆用氨水调节PH值,使料浆呈现中性;
④用蠕动泵将料浆打入喷雾造粒机中,在设定的进出口温度下造粒;
⑤测量喷雾造粒后粉体的流动性、松装密度;
⑥再将粉料进行颗粒级配后再次测定级配后的流动性和松装密度。
五、思考题
①喷雾造粒时,进出口温度对造粒有何影响?
②为什么要浆料的PH值调节为中性?
③如何制备出流动性好、松装密度高的粉体?
④为了保证流动性和松装密度都比较理想应该对喷雾造粒的粉料怎样处理?
实验二特种陶瓷材料的成型
一、目的意义
新型陶瓷材料的成型方法很多,有压制成型(干压成型和等静压成型)、注射成型、技压成型等,最常用的是压制成型方法。
由于新型陶瓷材料的成型是陶瓷制备的关键技术环节,选择合适的成型方法有利于陶瓷制品的烧结和改善烧结体的性能。
本试验目的:
①了解新型陶瓷材料的先进的成型方法;
②掌握新型陶瓷材料常用成型方法的成型原理与步骤。
二、成型方法
1、干压成型
将经过造粒、流动性好,颗粒级配合适的粉料装入模具内,通过成型压机的柱塞施以外加压力,把配料压制成具有一定几何尺寸坯件的方法,是应用最广泛的一种成型方法。
加压方式有单向加压和双向加压两种。
干压成型应注意的问题如下。
(1)控制干压成型的坯料含水量在4%~8%左右。
(2)加压方式不同其成型结果也不同。
单向加压时,直接受压一端的压力大,密度大;远离加压一端的压力小,坯体密度小。
双向加压时,坯体两端直接受呀,因此两端密度大,中间中间密度小。
如果坯料加润滑剂、经过造粒,再进行双向加压,则坯体密度非常均匀。
(3)成型压力。
成型压力的大小直接影响瓷体的密度和收缩率。
成型压力小,瓷体收缩大。
(4)加压速度和时间。
2、冷等静压成型
等静压成型又称静水压成型,它是利用液体介质不可压缩性和均匀传递压力的一种成型方法,等静压成型方法有冷等静压成型和热等静压成型两种。
冷等静压成型又分湿式等静压成型和干式等静压成型两种。
等静压成型的特点是:
①适于压制形状复杂,大件且细长的新型陶瓷制品。
②湿式等静压容器内可同时放入几个模具,还可压制不同形状的坯体。
③可以任意调节成型压力。
④压制的产品质量高,烧成收缩小,坯体致密不易变形。
三、测定装置
四、实验器材
①干压成型的压力机
②冷等静压成型机
③电子天平一台
④金属模具三套
⑤橡胶模具一套
⑥油酸溶液
五、实验步骤
①将经过喷雾造粒后的SiC陶瓷粉料装在金属模具中;
②设定干压成型的压力(10T或16T),保压时间为1min,进行预成型;
③测量不同压力下干压成型后素坯体的尺寸和密度;
④将预成型的陶瓷坯体用橡胶套包封好置于冷等静压成型机中的高压容器内;
⑤设定冷等静压成型所需的不同压力(200MPa、250MPa),最终成型;
⑥测量经过不同压力下冷等静压成型后素坯体的尺寸和密度。
六、注意事项
①试样成型前模具必须保证清洁、干净,以免造成素坯体受污染;
②干压成型时,保压时间无法自动控制,需要手动记录;
③冷等静压成型后卸压时一定要缓慢进行。
七、思考题
①碳化硅陶瓷成型的压力设计多大最合适?
②如何保证素坯体不分层、不开裂?
③卸压时为什么要缓慢卸压,否则会发生什么现象?
附件:
实验记录表
实验号
成型压力
保压时间
素坯体尺寸
素坯体密度
干压
冷等静压
干压
冷等静压
干压
冷等静压
干压
冷等静压
1
2
3
实验三特种陶瓷材料烧结方法研究
一、实验目的和意义
1、了解陶瓷材料的烧结和性能检测的工艺流程,掌握吸水率,表面气孔率,实际密度,线收缩率的测定方法。
2、利用实验找出材料的最优烧结工艺,包括烧结温度和烧结时间。
二、实验背景知识
1、烧结实验
在粉体变成的型坯中,颗粒之间结合主要靠机械咬合或塑化剂的粘合,型坯的强度不高。
将型坯在一定的温度下进行加热,使颗粒间的机械咬合转变成直接依靠离子键,共价键结合,极大的提高材料的强度,这个过程就是烧结。
陶瓷材料的烧结分为三个阶段,升温阶段,保温阶段和降温阶段。
在升温阶段,坯体中往往出现挥发分排出、有机粘合剂等分解氧化、液相产生、晶粒重排与长大等微观现象。
在操作上,考虑到烧结时挥发分的排除和烧结炉的寿命,需要在不同阶段有不同的升温速率。
保温阶段指型坯在升到的最高温度(通常也叫烧结温度)下保持的过程。
粉体烧结涉及组成原子、离子或分子的扩散传质过程,是一个热激活过程,温度越高,烧结越快。
在工程上为了保证效率和质量,保温阶段的最高温度很有讲究。
烧结温度与物料的结晶化学特性有关,晶格能大,高温下质点移动困难,不利于烧结。
烧结温度与材料的熔点有关系,对陶瓷而言是其熔点的0.7—0.9倍,对金属而言是其熔点的0.4-0.7倍。
冷却阶段是陶瓷材料从最高温度到室温的过程,冷却过程中伴随有液相凝固、析晶、相变等物理化学变化。
冷却方式、冷却速度快慢对陶瓷材料最终相的组成、结构和性能等都有很大的影响,所以所有的烧结实验需要精心设计冷却工艺。
由于烧结的温度如果过高,则可能出现材料颗粒尺寸大,相变完全等严重影响材料性能的问题,晶粒尺寸越大,材料的韧性和强度就越差,而这正是陶瓷材料的最大问题,所以要提高陶瓷的韧性,就必须降低晶粒的尺寸,降低烧结温度和时间。
但是在烧结时,如果烧结温度太低,没有充分烧结,材料颗粒间的结合不紧密,颗粒间仍然是靠机械力结合,没有发生颗粒的重排,原子的传递等过程,那么材料就是不可用的。
2、性能检测
材料是否烧结良好,需要一定的检测手段。
烧结的致密程度一般表现在密度是否高、材料内部的气孔的多少、表面的气孔多少和大小以及吸水能力的强弱。
在本实验中,主要考察材料表面气孔率、相对密度、吸水率以及线收缩率。
(1)目测
很多的实验,在烧结的过程中,可能由于很多的原因而出现表面裂纹,有些会出现表面的凹陷,所以,烧结后检测的第一步就是目测试样。
如果出现以上的问题,则试样肯定是不合格的,其他的实验可以不用做了。
目测的项目有是否出现表面裂纹、是否有变形现象,是否表面出现凹陷或者突出。
(2)密度测试
试样经110C°干燥之后之重量与试样总体积之比,用g/cm3表示。
材料烧结好坏的一个重要方面就是密度是否接近理论密度。
在烧结过程中,随着晶界的不断移动,伴随着液相和固相传质的进行,颗粒间的空隙会逐渐在表面消失,其中会有些气孔保留,大多数的气孔会逐渐缩小甚至消失。
达到良好烧结的标准就是气孔率小,密度接近理论密度。
例如原料采用99%的氧化铝,则理论密度为3.9g/cm3(全部按照α-Al2O3来计算)。
(3)线收缩率
在烧结后,最直观,最明显的变化就是尺寸的巨大收缩,如果在变形量很小的情况下,线收缩率越大,说明样品烧结得越致密。
一般的收缩率有体积收缩率和线收缩率两种,由于工具简便,准确度较高,所以线收缩率是比较常见的测试方法。
取几个比较具有代表性的尺寸(对圆片状的样品来说,取直径d和高度h),计算每一个尺寸的缩小尺寸和原尺寸的百分比,然后平均。
(4)表面气孔率
和密度相关的量,如果气孔率越大,则密度就越小。
而表面气孔率可以在很程度上反映材料的致密程度。
如表面有很多的开口气孔,则材料的烧结就是不致密的。
其定义是一定表面的气孔的体积和材料的总体积的比,用百分数来表示。
(5)吸水率
吸水率——试样孔隙可吸收水的重量,与试样经110C°干燥之后之重量之比,用百分率表示。
和表面气孔率相似,如果表面气孔越多,吸取水的能力就越强。
和表面气孔率一起更加准确的表示材料的致密程度。
三、实验内容
1、烧结实验
实验仪器
烧结炉(1300℃硅钼棒炉,1600℃硅碳棒炉)、精确度为0.01g天平、承烧板若干、游标卡尺。
(1)原料的选用
原料有很多种,各有不同的烧结温度,有的材料中有掺杂,则烧结温度又会发生变化。
制定一个合适的烧结温度,首先要根据实际的材料,查阅有关文献,了解大致的温度范围,然后制定合适的方案。
例如采用纯度为99%的氧化铝材料,则烧结温度大约在1600℃。
则可以设计烧结温度为1500℃、1600℃、1700℃这三个温度。
如果在原料中有MgO,CaO这些帮助烧结的掺杂物,则烧结温度可以适当降低。
如纯度为75%的氧化铝,则烧结温度可能只有1200℃。
这种材料具有烧结温度低,材料较致密,一定温度下产生很多液相很容易促进烧结的优点。
一般来说,材料选用可以有一定比较的选择。
比如选择氧化铝作为主要的原料,则可以在其中掺杂CaO、MgO、SiO2等,制成几种不同的原料的坯体,考察原料的成分变化对于材料烧结性能的影响。
(2)成型
烧结实验用的试样可以由各种成型方法制得。
在本实验室的其他实验中,可以选择的方法有流延成型,丝网印刷,模压成型,热压注成型四种。
除开模压成型,其他成型方法均需要脱脂步骤。
将每一种不同原料配方的坯体根据方案制备一定数量(比如有三个烧结温度,则可以做12个左右的试样,每一个温度有4个完全相同原料的试样)。
(3)烧结前准备
在放入烧结炉前,对样品的重量,尺寸进行测量,比如对于圆片状坯体,尺寸上需要测定的有:
试样高度h,试样的直径R;如果是方形试样,则需要测定的尺寸有长l、宽w、高h。
记录这些数据以备在烧结后测定材料的烧结收缩。
将制好的坯体放在承烧板上,各个样品不相互接触,承烧板要求表面洁净,放样品的面光滑平整,在预定烧结温度下,本身不和样品发生任何物理和化学反应。
将试样有顺序的放入炉中,记录好各自的位置。
(4)烧结
关好炉门,对烧结炉进行程序设计。
升温过程中,常温-700℃采用手动控制,升温速率大约是0.5-1℃/min。
700-1600℃升温速率一般为2℃/min。
降温时采用自然降温。
200℃是可以打开炉门空冷。
烧结的保温时间一般为120min。
等待样品冷却后,就进入下一步的工作,性能检测。
2、性能检测
性能检测的项目包括目测、样品的密度、相对致密度、表面气孔率、烧结尺寸变化。
(1)目测
将烧结好的试样从炉中取出,观察试样表面是否有裂纹,裂纹的大小、深浅和个数;观察材料是否发生了变形、弯曲。
在下表中作记录:
试样名称
测试人
测定日期
试样处理
编号
裂纹数量
裂纹长度
是否有变形
(2)实际密度,吸水率,气孔率的测定
实际密度采用排水法测定。
计算气孔率和密度关键是要知道试样的体积和气孔的体积,可以根据阿基米德原理,用液体静力称重法来测定。
将试样开口孔隙中的空气排出,充以液体,然后称量饱吸液体的试样在空气中的重量及悬吊在液体中的重量,由于液体浮力的作用,此两次称量的差值等于被试样所排开的同体积液体,此值除以液体的密度即得试样的真实体积。
试样饱吸液体之前与饱吸液体之后,在空气中的重量之差值,除以液体的密度即为试样开口孔隙所占体积。
欲使试样孔隙中的空气,在较短时间内被液体代替,必须采用强力排气,常用方法有煮沸法和抽真空法,在本实验中采用抽真空法。
设已知:
干燥试样重go(g)、饱吸液体试样在空气中的重量g1(g)、饱吸液体试样在液体中的重量g2(g)、液体的密度r(g/cm3)、陶瓷的理论密度,可按下式分别计算陶瓷试样的吸水率、开口气孔率、实际密度和总气孔率:
吸水率=100(g1—go)/go(%)
开口气孔率=100(g1—go)/(g1—g2)(%)
实际密度=rgo/(g1—g2)(g/cm3)
总气孔率=100(理论密度—实际密度)/理论密度(%)
仪器及材料
电子天平、真空泵、真空干燥器、压力表、液体槽、支架、吊篮、烘箱、小烧杯、镊子、试样、橡皮管。
实验步骤
1)将试样编号以后,放入105—110C°干燥烘箱烘至恒重,在干燥器中冷却至室温,然后在电子天平上称其重量go。
2)将试样放入真空装置(见图1)的中真空干燥器中,作真空处理:
先将试样在真空度不小于95%的条件下保持10分钟;注入液体,直至试样完全被淹没;再抽真空,直至试样中没有气泡出来为止(约需30分钟);先放入空气,再关闭真空泵;打开真空干燥器的盖,取出试样。
3)在天平上架好支架、吊篮及液体槽,注意吊篮不要与液体槽相接触(见图2),液体要完全淹没试样。
试样进入吊篮前,天平要进行调零;试样进入吊篮后,天平给出的重量就是饱吸液体的试样在液体中的重量g2。
4)从液体中取出试样,用湿毛巾均匀地抹去试样表面的液体,在天平上迅速称取饱吸液体试样在空气中的重量g1。
图2液体静力天平
实验记录
陶瓷吸水率、气孔率及体积密度的测定
试样名称
测定人
测定日期
试样处理
编号
干燥试样重go(g)
饱吸液体试样在空气中的重量g1(g)
饱吸液体试样在液体中的重量g2(g)
吸水率(%)
开口气孔率(%)
实际密度(g/cm3)
总气孔率(%)
3.2.3尺寸变化
采用游标卡尺测定材料烧前和烧后的尺寸(包括高h和半径R)。
烧收率(%)=(L0-L)/L0
试样名称
测定人
测定日期
烧结温度
编号
烧前h
烧后h
h变化率
烧前R
烧后R
R变化率
总烧收率
如有必要,可以使用SEM测定材料的微观结构。
思考题
1原料中不同的成分对材料烧结性能有什么影响?
2不同的烧结温度对材料的性能有什么影响?
3从结果上看,吸水率、表面气孔率、体积密度、线收缩率之间是否有一定的相关性?
如何解释?
4查阅资料,说明是否烧结致密的试样一定机械强度、断裂韧性等力学性能就一定很好?