金刚石涂层刀具综述.docx
《金刚石涂层刀具综述.docx》由会员分享,可在线阅读,更多相关《金刚石涂层刀具综述.docx(8页珍藏版)》请在冰豆网上搜索。
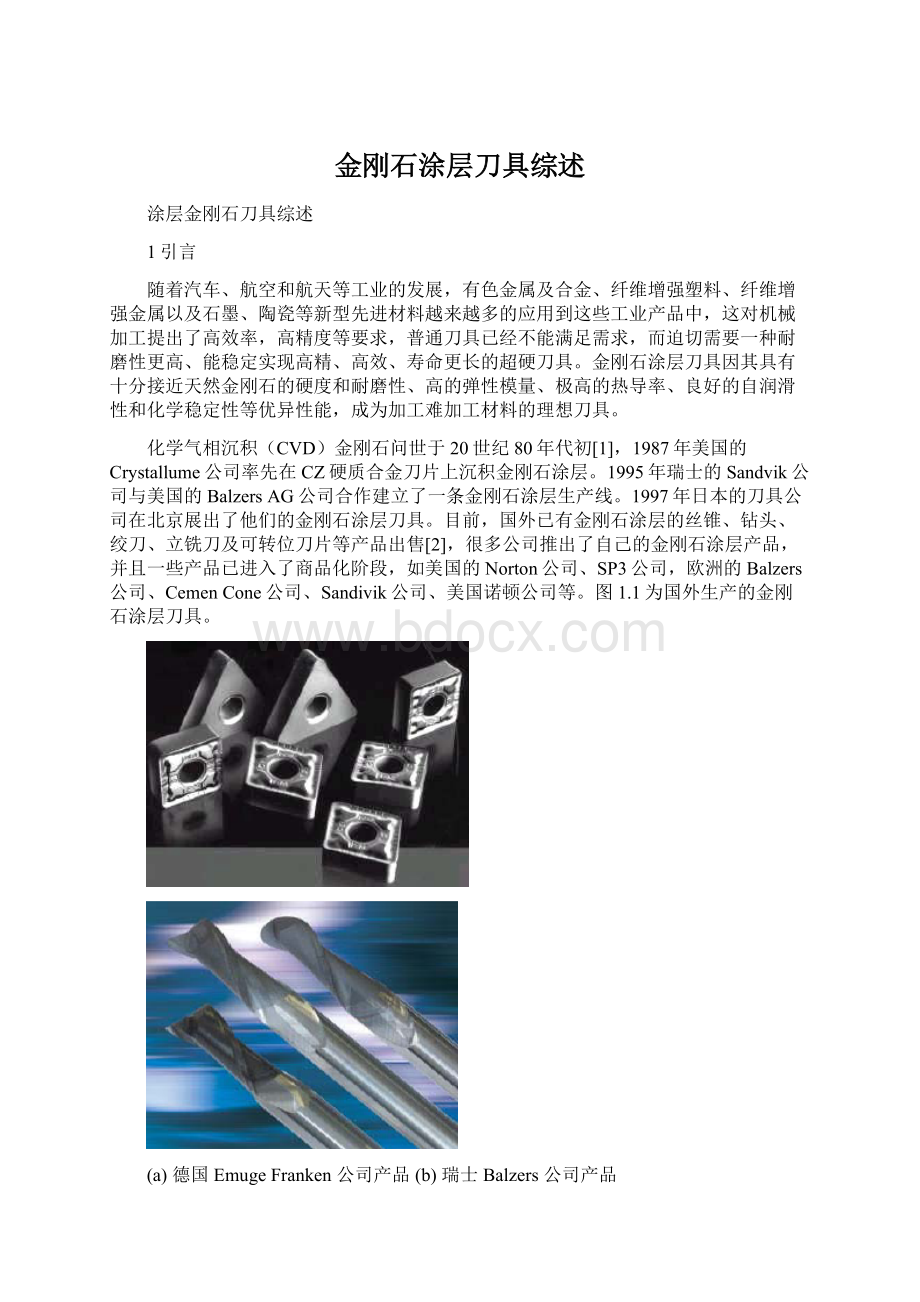
金刚石涂层刀具综述
涂层金刚石刀具综述
1引言
随着汽车、航空和航天等工业的发展,有色金属及合金、纤维增强塑料、纤维增强金属以及石墨、陶瓷等新型先进材料越来越多的应用到这些工业产品中,这对机械加工提出了高效率,高精度等要求,普通刀具已经不能满足需求,而迫切需要一种耐磨性更高、能稳定实现高精、高效、寿命更长的超硬刀具。
金刚石涂层刀具因其具有十分接近天然金刚石的硬度和耐磨性、高的弹性模量、极高的热导率、良好的自润滑性和化学稳定性等优异性能,成为加工难加工材料的理想刀具。
化学气相沉积(CVD)金刚石问世于20世纪80年代初[1],1987年美国的Crystallume公司率先在CZ硬质合金刀片上沉积金刚石涂层。
1995年瑞士的Sandvik公司与美国的BalzersAG公司合作建立了一条金刚石涂层生产线。
1997年日本的刀具公司在北京展出了他们的金刚石涂层刀具。
目前,国外已有金刚石涂层的丝锥、钻头、绞刀、立铣刀及可转位刀片等产品出售[2],很多公司推出了自己的金刚石涂层产品,并且一些产品已进入了商品化阶段,如美国的Norton公司、SP3公司,欧洲的Balzers公司、CemenCone公司、Sandivik公司、美国诺顿公司等。
图1.1为国外生产的金刚石涂层刀具。
(a)德国EmugeFranken公司产品(b)瑞士Balzers公司产品
图1.1国外公司生产的CVD金刚石涂层刀具
CVD金刚石涂层刀具是利用化学气相沉积的方法在韧性好,强度高的硬质合金基体上沉积一定厚度的金刚石薄膜制造而成的。
目前金刚石涂层刀具常用的基体材料为与金刚石的热膨胀系数较为接近的Si3N4系陶瓷和WC系硬质合金。
其中Si3N4系陶瓷具有较高的硬度、耐磨性和热稳定性,与金刚石的热膨胀系数最为接近,因此一直被认为是CVD金刚石涂层较为理想的基体材料。
但是,由于Si3N4陶瓷本身脆性大,抗冲击性能差,一般认为,Si3N4基金刚石涂层刀具仅宜用于精加工,而不宜进行冲击切削加工。
而WC系硬质合金具有较高的硬度和红硬度,韧性较好,其与CVD金刚石涂层的结合,有效解决了传统刀具材料硬度与韧性之间的矛盾,大大提高了硬质合金刀具的切削性能和使用寿命,是当前应用最为广泛的刀具材料[2]。
下面主要对硬质合金金刚石涂层刀具技术做一详细综述。
2金刚石涂层刀具技术研究现状
金刚石涂层是在真空室中采用氢气和具有金刚石结构甲基(—CH3)的分子(如甲烷、丙酮等)的碳源气体形成的。
通常,这些气体是以50:
1的比例加到真空室中,以氢气为主。
研究发现[3-7],选择具有金刚石结构的分子(如甲烷、丙酮等)为碳源气体,更有利于生成甲基。
大量的甲基与衬底表面作用以及它们之间的相互作用,形成碳碳连接的共价键,进而在衬底表面上形成金刚石晶核。
在高能粒子的持续作用下,用活性的甲基逐步取代晶核中的氢,不断循环下去就能形成金刚石薄膜,其反应机理如下图:
图2.1金刚石薄膜反应机理
2.1金刚石薄膜技术
CVD金刚石涂层刀具是利用CVD技术在刀具基体表面沉积一层厚度一般为10~30μm的金刚石薄膜。
为了达到高精度机械加工的要求,一般要求薄膜的结构要均匀、缺陷尽可能的少。
目前应用较为广泛的化学气相沉积合成金刚石薄膜的方法主要有热丝CVD、微波等离子CVD、直流电弧等离子喷射CVD等。
图2.2是热丝CVD法的系统装置图。
图2.3为几种常用的CVD金刚石膜制备方法的特点比较[8-10]。
图2.2热丝CVD系统装置图
图2.3几种常用CVD金刚石膜制备方法的特点比较。
常规CVD金刚石薄膜晶粒度较大,表面较粗糙,导致耐用度和寿命下降,也很大程度的影响了切削性能、加工精度和工件表面质量,并且其后续抛光处理很困难。
因此,改善常规金刚石薄膜的表面粗糙度和后续抛光技术尤显重要。
从CVD金刚石沉积过程来看,控制沉积工艺参数,如碳源浓度、衬底温度、反应气体、有无偏压等参数都能在一定程度上改善薄膜的表面粗糙度[11]。
目前许多研究单位已经利用通过改变金刚石薄膜沉积工艺条件来得到较细颗粒甚至纳米级的金刚石。
表面抛光技术是平整优化CVD金刚石薄膜表面,降低薄膜表面粗糙度、减小摩擦和刀具磨损的传统方法。
但其适用范围有限,对高硬度、高耐磨性的金刚石薄膜进行抛光工艺难度较大,工艺设备比较复杂,且有可能对金刚石薄膜质量和使用寿命产生不良影响。
因此,如何有效减小薄膜表面粗糙度,是降低CVD金刚石薄膜刀具制造成本、实现产业化需要解决的关键问题。
随着CVD沉积金刚石薄膜技术的发展与成熟,微米与纳米金刚石涂层技术应运而生。
纳米金刚石薄膜晶粒非常细小,表面光滑,而且纳米金刚石薄膜的硬度比传统金刚石薄膜低10-20%,非常有利于薄膜进行后续抛光。
但是纳米金刚石生长条件非常苛刻,不利于降低成本,为此有研究提出了纳米金刚石-微米金刚石-纳米金刚石的梯度复合涂层,以更好地提高薄膜与硬质合金基体的粘附性和降低薄膜表面粗糙度。
2.2金刚石薄膜与基体间的附着力问题
金刚石涂层刀具寿命的决定因素是涂层与基体之间的附着力。
研究认为[12],附着力差的原因可归结为三方面:
(1)金刚石涂层的形核密度低,使得涂层与基体之间的界面上存在大量孔隙;
(2)硬质合金基体中的Co具有催石墨化的作用;(3)金刚石与WC-Co硬质合金热膨胀系数不匹配导致涂层内存在较大的残余应力。
2.2.1金刚石膜厚度对附着力的影响
选择合适的厚度是金刚石涂层刀具合理性价比的关键。
CVD金刚石薄膜太薄,磨损快,刀具使用寿命不高;薄膜太厚,与硬质合金基体的粘附性变差且制造成本增加。
黄树涛等人[13]对薄膜厚度对刀具性能的影响进行了研究,结果表明:
金刚石薄膜涂层刀具的附着强度随涂层厚度的增加而下降。
2.2.2CVD金刚石涂层硬质合金刀具的基体预处理技术
对硬质合金基体表面进行预处理主要是抑制钴对金刚石薄膜形核及生长的不利影响,减少石墨或非晶碳的生成;增加基体与反应气源间的接触面积;提高硬质合金的表面活性,减少薄膜与基体间的晶格失配度和热膨胀系数的差异,促进金刚石的成核与生长,提高金刚石薄膜与硬质合金刀片的结合强度,改善金刚石薄膜的质量。
典型的硬质合金表面预处理方法主要有:
除去或钝化刀具表面层的粘结相Co、施加过渡层、机械处理等。
在实际应用中,为了更好地提高金刚石薄膜与硬质合金基体的结合强度,往往同时综合采用多种表面预处理方法。
1)除去或钝化刀具表面层的粘结相Co
硬质合金中的钴,一方面使硬质合金获得了良好的韧性和抗弯强度,另一方面催化非金刚石碳的形成,影响金刚石晶体的长大,促进金刚石的二次形核,并与金刚石之间形成碳化物的CoC固溶体,从而严重降低了沉积的金刚石薄膜的质量和粘结性能。
要增强硬质合金与金刚石薄膜之间的结合力,必须改善其表面物理性能和化学性能。
国内外大量的实验研究表明,采用腐蚀性的酸溶液浸蚀(酸洗)[14]、等离子体刻蚀、氧化处理、化学热处理以及采用其它材料代替钻作为粘结剂等方法,均能在不同程度上消除钻粘结相的不利影响,从而提高CVD金刚石涂层与硬质合金刀具之间的附着力。
酸液浸蚀钴的方法即酸洗法是将硬质合金放入腐蚀性的酸液中进行腐蚀,使表面层的钴与酸液发生化学反应,形成稳定的化合物,从而达到去除表面层钴的目的。
其一般分为一步法脱Co和二步法脱Co[15-16],一步法脱钴是用一种酸或混合酸对基体进行一次浸蚀脱钴处理。
两步浸蚀脱钴法是先用Murakami试剂浸蚀碳化钨相,消除碳化钨对酸浸蚀的阻碍影响;后用酸处理钴相,在有效地去除硬质合金基体表面的钴的同时,显著粗化硬质合金基体表面,提高薄膜的附着力。
之后,马玉平等提出了非常适合预处理复杂形状硬质合金基体的醇碱两步法。
该方法可以省去传统的手工研磨等过程,大大提高衬底的预处理效率。
同时避免了传统两步法中的强酸腐蚀去钴带来的危险,以及由于腐蚀时间短带来的操作上的不便。
等离子体刻蚀法兼顾除钴和脱碳两方面[17],是利用O、H、Ar原子(离子)或CO等与硬质合金基体中的碳化钨、金属钴发生反应而到达脱钴的目的,并且对WC相有改性作用,有效提高了膜基之间的附着力。
但是等离子刻蚀处理法操作复杂,成本较高。
化学热处理主要是对硬质合金基体进行渗硼、硼氮共渗和碳氮共渗等处理方法,使其在硬质合金表面形成Co2B、Co2N等化合物。
这些化合物层在金刚石沉积中能有效地阻挡粘结相钴的扩散,抑制金刚石膜中非晶碳或石墨碳的形成,克服了钴对金刚石薄膜沉积的不利影响。
氧化处理是将刀片置于CO2气氛的微波等离子体气氛中,使刀片表面的WC及Co元素发生氧化反应,由于WC及Co的氧化速度有差异,WC颗粒间的粘结相Co被快速氧化,然后将刀具放入碱溶液中去除刀具表面的W及Co的氧化物。
氧化处理后,基体表面的Co含量下降,WC颗粒裸露明显,从而增大了表面粗糙度,有利于金刚石的成核和初期成长。
氧化处理适用于复杂形状刀具的衬底预处理,并较容易实现批量处理。
改变基体材料成分,可以彻底消除金属Co的影响。
Weihnache等[18]报道,采用Ni3Al或NiAl代替Co作为粘结剂,可大大提高金刚石涂层的形核密度和附着力。
他们发现用这种镍铝合金作为粘结剂的硬质合金基体,不仅可以抑制石墨相的形成,而且还具有很好的高温特性。
2)施加各种过渡层
在金刚石薄膜和硬质合金基体之间预沉积单层或复合过渡层,也是重要的基体预处理方法。
其作用主要是:
阻碍基体中促进石墨生长的钴的扩散或与钴反应生成稳定的化合物;减少金刚石和基体材料的晶格参数、热膨胀系数不匹配而造成的内应力;与金刚石薄膜、WC硬质合金两种异质材料均能形成较强的结合键,提高附着力;提高金刚石的形核密度。
在设计时,过渡层的厚度太薄将难以消除Co的不利影响,厚度太厚又会降低刀具的性能,所以设计适当的过渡层很重要。
目前普遍采用的过渡层材料有:
Si、SiC、B、Ti、Cr、Cu、TiN、TiC、TiCN、Si3N4、SiC、SiCxNy、Nx、无序碳、DLC膜、WC/W、Cr/CrN/Cr、TiN/TiCN/TiN、TiCN/Ti、Cu/T、TiC/TiN等。
过渡层的制备方法主要有离子植入、离子镀、电子蒸发、激光辐射气相沉积、射频脉冲激光沉积和CVD等[19-21]。
一般过渡层制备完成之后,在制备CVD金刚石膜之前,还需要对过渡层进行一些必要的后处理,以提高过渡层的表面活性,增强CVD金刚石的成核与附着。
图2.4即为用H等离子对电沉积过渡层进行后续处理之后的沉积金刚石涂层刀具的模型[22],电沉积的金属原子由于等离子的作用与硬质合金基体组成元素之间相互溶解扩散,使电沉积层与基体的结合由机械结合变成化学结合,增强了附着力。
图2.4硬质合金上CVD金刚石涂层沉积模型。
3)机械处理
常用的机械处理方法有:
机械研磨、超声波清洗、高能粒子轰击、水射流、激光辐照等[22]。
研磨法就是利用金刚石微粉或金刚石研磨膏对基体进行研磨处理,使基体表面或表层出现大量的机械划痕,增大表面缺陷密度,从而增加金刚石形核密度及金刚石膜/基间附着力。
并且,残留在基体表面的金刚石微粉可作为金刚石形核的籽晶,对金刚石形核密度和膜/基间的附着力也会起到有利影响。
超声波清洗法是利用微晶或纳米大小的金刚石微粉悬浮液(如乙醇、丙酮等)对基体表面进行处理,不仅能较彻底的清洗基体表面,同时也可将分散的金刚石微粉植于基体上提高金刚石薄膜的形核率,是一种简单、有效、经济的基体预处理方法。
对基体表面预处理方法有很多,在实际应用中,往往同时综合利用上述各种方法,以到达更好地改善CVD金刚石涂层在刀具基体上的附着性能的目的。
3金刚石涂层刀具的应用及发展前景
金刚石涂层刀具由于其良好的机械加工性能,在切削加工领域具有广阔的应用前景,是加工石墨、金属基复合材料(MMC)、高硅铝合金及许多其它高磨蚀材料的理想刀具。
目前其主要应用领域是汽车和航空航天工业。
由于金刚石涂层刀具是在刀具基体上直接沉积金刚石薄膜而成,因而它具有制造复杂形状刀具的潜力。
CVD金刚石刀具一直被人们关注,经过多年的发展,金刚石涂层与硬质合金基体间的附着力问题已经得到了很大程度的改善,金刚石涂层硬质合金刀具产业化也已经初步形成。
然而,现阶段金刚石涂层刀具的发展也仍然面临很多问题,主要包括:
涂层与基体间附着力的进一步优化;金刚石膜生长速度慢;金刚石膜制备工艺复杂,成本高;金刚石涂层刀具的高效刃磨抛光技术的发展;金刚石膜低温生长技术的完善以及复杂形状金刚石涂层刀具的研究开发与应用等。
尽管金刚石刀具的广泛应用还需要很多努力,但是我相信随着金刚石沉积技术的进一步完善和制备成本的不断降低,金刚石涂层刀具必将逐渐替代PVD刀具,占据刀具市场的主导地位。
参考文献:
[1]MATSUMOTOS.SATOY.KAMOM.Vapourdepositionofdiamondparticlesfrommethane[J].JApplPhys,1982.24(4):
183.
[2]杨仕娥,马丙现,李会军等.金刚石涂层刀具的研究进展[J].真空与低温,2001,7
(2):
68-71.
[3]H.Liander,E.Lundblad,Ark.Kemi,1960,16:
139-148.
[4]FordIJ.J.Phys,1996,29:
2229-2234.
[5]B.V.Deryagin,D.V.Fedoseev,Sci.Am.1975,233[5]:
102-109.
[6]DeryaginBVetal.Dokl.Akad.NaukSSSR,1976,231:
333-335.
[7]B.V.Deryagin,D.V.Fedoseev,GrowthofDiamondandGraphiteFromtheGasPhase(Nauka,Moscow,1977).
[8]杨国伟.低压气相生长金刚石薄膜成核机理研究.微细加工技术,1994,2:
51-57.
[9]王丽军.金刚石薄膜CVD制备方法及其评述.真空与低温,2000.2(6):
80-85.
[10]卢文壮.基于过渡层在硬质合金上沉积CVD金刚石薄膜的研究.[硕士论文],南京,南京航空航天大学,2002.
[11]马玉平.金刚石涂层工具制备及其应用研究[D].上海交通大学:
2007.
[12]SODERBERGS,GERENDASA,SJOSTRANDM.Factorinfluencingtheadhesionofdiamondcoatingsoncuttingtools[J].Vacuum,1990,41(4-6):
1317.
[13]黄树涛,张志军,姚英学,袁哲俊.涂层厚度对金刚石薄膜附着强度的影响[J].制造技术与机床,1999,(04).
[14]F.Deuerler,H.、乞ndenBerg,R.几berskyetal.,Diam.Relat.MateLS,1478(1996).
[15]刘沙,易丹青,余志明,等.金刚石涂层用硬质合金基体表面预处理研究新进展.稀有金属材料与工程,2001,30(5):
392-395.
[16]R.Haubner,W.D.Schubert,B.Lux.Interactionsofhardmetalsubstratesduringdiamonddeposition.InternationalJournalofRefractoryMetalsandHardMaterials,1998,16:
177-185.
[17]杨仕娥.硬质合金刀具基体上金刚石涂层的制备及其附着性能的研究[D].郑州大学,2002.
[18]VOLKERWEIHNACHE,FANWD,JAGANNADHAMK,etal.Anewdesignoftungstencarbidetoolswithdiamondcoatings[J].JMaterRes,1996.11(9):
2220.
[19]苏革,闻立时,成会明.金刚石薄膜与基材之间过渡层技术的研究.材料科学与工艺,1998,4(6):
22-24.
[20]黎向锋,左敦稳,王珉.通过过渡层改善金刚石膜和基体间的结合性能.材料开发与应用,2000,1(15):
35-39.
[21]卢文壮.CVD金刚石涂层刀具的制备及其切削性能研究[D].南京航空航天大学,2008.
[22]卢文壮,左敦稳,王珉等.CVD金刚石刀具的制备工艺研究[J].机械工程师,2003,(8):
7-10.