超高压填料组失效的原因分析.docx
《超高压填料组失效的原因分析.docx》由会员分享,可在线阅读,更多相关《超高压填料组失效的原因分析.docx(15页珍藏版)》请在冰豆网上搜索。
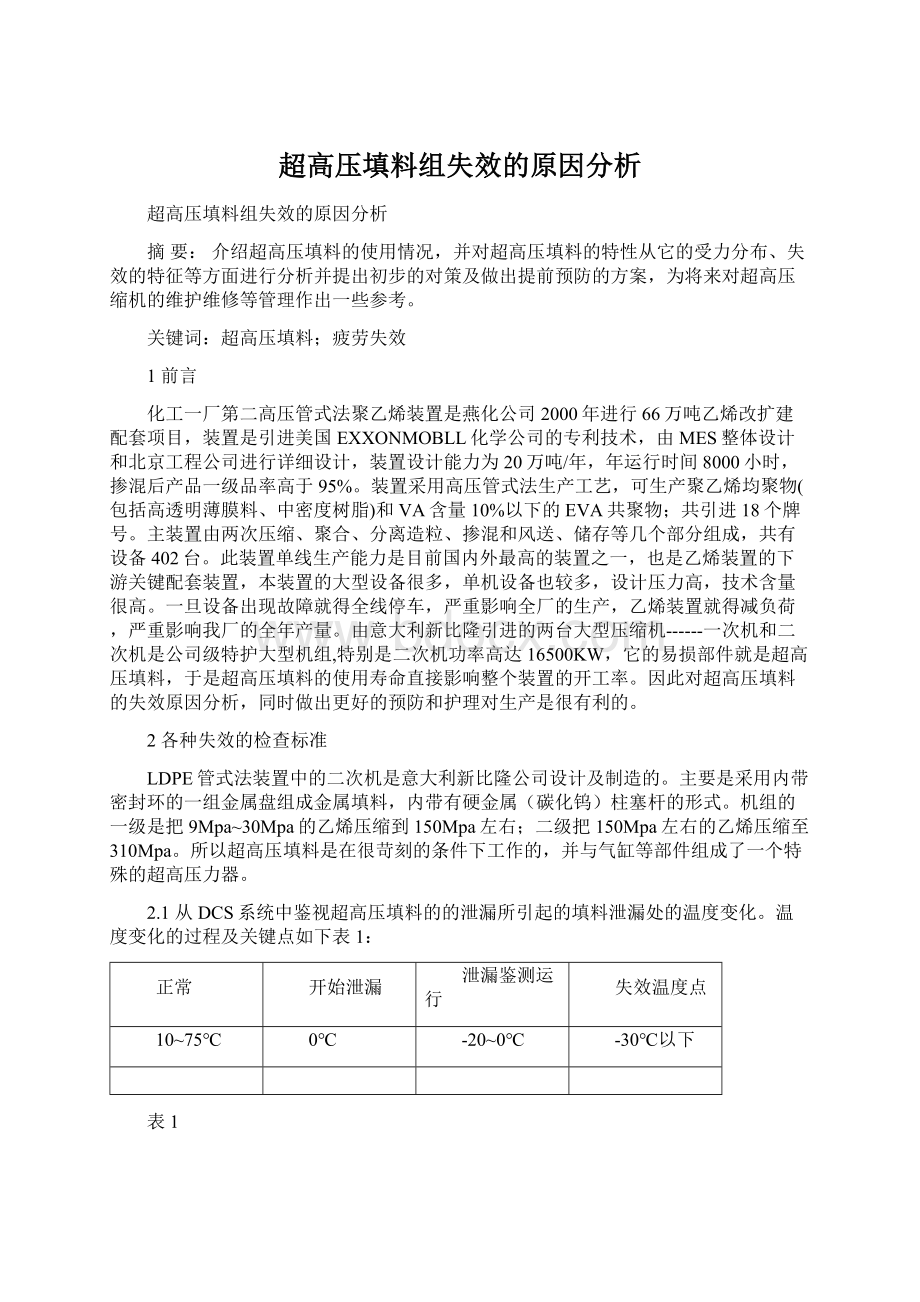
超高压填料组失效的原因分析
超高压填料组失效的原因分析
摘要:
介绍超高压填料的使用情况,并对超高压填料的特性从它的受力分布、失效的特征等方面进行分析并提出初步的对策及做出提前预防的方案,为将来对超高压缩机的维护维修等管理作出一些参考。
关键词:
超高压填料;疲劳失效
1前言
化工一厂第二高压管式法聚乙烯装置是燕化公司2000年进行66万吨乙烯改扩建配套项目,装置是引进美国EXXONMOBLL化学公司的专利技术,由MES整体设计和北京工程公司进行详细设计,装置设计能力为20万吨/年,年运行时间8000小时,掺混后产品一级品率高于95%。
装置采用高压管式法生产工艺,可生产聚乙烯均聚物(包括高透明薄膜料、中密度树脂)和VA含量10%以下的EVA共聚物;共引进18个牌号。
主装置由两次压缩、聚合、分离造粒、掺混和风送、储存等几个部分组成,共有设备402台。
此装置单线生产能力是目前国内外最高的装置之一,也是乙烯装置的下游关键配套装置,本装置的大型设备很多,单机设备也较多,设计压力高,技术含量很高。
一旦设备出现故障就得全线停车,严重影响全厂的生产,乙烯装置就得减负荷,严重影响我厂的全年产量。
由意大利新比隆引进的两台大型压缩机------一次机和二次机是公司级特护大型机组,特别是二次机功率高达16500KW,它的易损部件就是超高压填料,于是超高压填料的使用寿命直接影响整个装置的开工率。
因此对超高压填料的失效原因分析,同时做出更好的预防和护理对生产是很有利的。
2各种失效的检查标准
LDPE管式法装置中的二次机是意大利新比隆公司设计及制造的。
主要是采用内带密封环的一组金属盘组成金属填料,内带有硬金属(碳化钨)柱塞杆的形式。
机组的一级是把9Mpa~30Mpa的乙烯压缩到150Mpa左右;二级把150Mpa左右的乙烯压缩至310Mpa。
所以超高压填料是在很苛刻的条件下工作的,并与气缸等部件组成了一个特殊的超高压力器。
2.1从DCS系统中鉴视超高压填料的的泄漏所引起的填料泄漏处的温度变化。
温度变化的过程及关键点如下表1:
正常
开始泄漏
泄漏鉴测运行
失效温度点
10~75℃
0℃
-20~0℃
-30℃以下
表1
2.3现场泄漏管线鉴测。
这个鉴测是对DCS系统中的鉴视的进一步确认。
测量的泄漏管线的温度变化也是以表1中的数据为标准进一步确认超高压填料的泄漏失效。
2.4如图1中的孔1处用测爆仪进行测量。
如果泄漏值超出范围也确认超高压填料失效的标准。
本装置所用的测爆仪型号为:
XP-311A;厂家是:
COSMOTECTOR。
所定的标准如表2:
正常
泄漏鉴测运行
失效指标
绿色区(0~20%)
黄色区(20~90%)
红色区(90~100%)
注:
100%为乙烯浓度为2.7%(对大气中乙烯含量)
2.5从填料冷却油处观察判断泄漏的情况:
如表3
表3
正常
泄漏鉴测运行
失效现象
无气泡
有少量气泡,已串气
有大量气泡,油管结冰
3超高压填料组失效的分析及预防建议
3.1第一道填料盘的失效
3.1.1由于气体压力经过逐级密封后压力下降,从第一道密封环以后的密封环润滑不足,气缸由于与吸入,排出管线相联,在阀室孔的外侧承受着相对静止的吸入压力;在阀室孔的内侧承受相对静止的排出压力。
自紧密封环将它们与外界分隔开来,这样做有双重目的:
a允许外界压力对阀体有一个预压缩,以减少拉伸应力;
b在吸入、排出通道消除高的应力波动。
另外这些高应变区域开始就处于预压缩状态,这是自增强的功劳。
在压缩室和填料盘高应变区域进行热套预压缩。
所以第一道填料承受着多种高应变力,填料的受力如图a、图b、图c、图d。
每个气缸部件在不同的单元负荷情形下,在运转时同时出现的各种动作,以便弹性动作能够确定。
如预负荷图a气体压力(可视为不变压力图b和由于密封环引起的压降图c的组合)、预压缩图d和温度图e的作用下,填料盘中单元负荷情形。
负荷状态表明了不同部件间作用力的交换。
在填料盘接触表面上的应力和节点作用力也可以得到。
从受力图中还可以看出无论从温度,压降情况看第一道填料函所受的应力都远大于其它的填料函,于是它也是最先失效的原因之一。
3.1.2如图2中的填料组,1为第一道填料。
它距离高压侧最近,受压最高。
因此润滑油注入是最困难的。
即润滑情况很是不良。
在这种工作环境很恶劣的情况下填料组也很容易受损。
3.1.3超高压缩机的气体是脉动形式的,第一道填料和填料盘的冲击力是最大的。
这也是第一道填料组容易损坏的原因之一。
3.1.4对第一道填料盘的预防措施
第一道填料盘的径向密封面与气缸体接触处的脉动冲击太大,在高压下很容易产生振动磨损。
所以从设计开始就做了一道0.02mm的银层做保护。
每次损坏只是银层,经过研磨后再镀上0.02mm的银层做密封和保护又可以再做备件了。
3.2超高压填料盘密封面的分析
3.2.1超高压填料盘的组成如图2所示,共有8个盘组成一套填料组,密封填料分为三种形式。
如图2中的①②③所示:
3.2.2填料盘接触面的形式及主要的应力分布
3.2.2.1填料盘接触面形式,如图3所示:
中间的密封面为白色。
气
保缸部件间的密封表面在证气缸能很好地工作起着重要的作用,这些部件通常是表面光滑、状态,研磨到8微英寸,通过坚固螺栓连接,以使它们能很好地接触而达到密封。
于是适当选择紧固螺栓的轴向预负荷也是非常重要的,如果太大,会在受压缩和不受压缩填料盘的不连续处产生应力集中。
采用图4中a,b,c,d中不同同形状可减少应力集中,使接触应力峰值平滑。
如轴向负荷过大,填料盘失效可能性也较大,以致一些填料盘在使用一段时间后重装时无法复位;另一方面,当出现疲劳失效后,在接触表面会出现磨损。
在两连接填料盘接触表面变形有不同的形式。
事实上,上游的填料盘(图4中Ф1)的内径比其后跟的(图4中Ф2)内径大,由于密封环的减压作用,上游也承受着较大的作用,如预紧力不足以使填料盘成一整体,在压力差的作用下会造成接触表面的相对运动而磨损。
如图5显示出了较严重磨损和气体渗透,对填料密封造成威胁。
另一要考虑的主要问题是气缸工作温度,它影响部件寿命长度,也就影响轴向负荷。
如同前述,在聚乙烯装置里压缩机气缸是一个非常复杂的压力容器,不仅是因为它的几何形状,还因为沿着填料不同的压力分布,在这方面还须进行更广泛的研究以适应最严重情况的需求,这比其它压力容器需更先进的弹性分析设计方法,建立在有限元之上的计算设计方法得以发展,建立了整个气缸的弹性性能。
通过确定适当的预负荷、主要部件的应力状况以避免前述严重情况发生。
图4
3.2.2.2填料盘接触面的主要应力分布及分析
接触表面上周向应力(σ)和剪切应力(τ)构成了典型的形式。
通过曲线选择最佳轴向负荷,根据填料盘直径在同一图上能得到轴向应力σZ(接触应力)和τ/f比值,τ为剪切应力,使得填料盘相互错位,f为一系数,当[τ/f]>[σZ]时,填料盘被剪切移动,磨损。
这样的一个实例见图6,显示了两接触表面沿填料盘轴向应力分布曲线。
当压缩室排出压力为300Mpa时,有不同的压力,曲线A为100Mpa,曲线B为150Mpa。
从两曲线可看出,当压差增大时,在内径附近区域接触应力有较大的衰减,另外,相邻盘P1和P2在不同的压力下有不同的变形,随着压差的增加时引起接触表面剪切力的增大而产生损坏。
事实上,在A情形下τ/f>σZ时,A情形下半径上只有1.1mm的磨损,B情形下达到2.4mm。
另外在B情形下第一个半径1.4mm的密封区域轴向力比气体压力低,意谓着气体能渗透到里面而使密封面分开。
在压缩环当气体压力下降时,密封面不再分离,密封面通过一个滑移过程又结合在一起。
撞击和滑移都是导致表面损坏的原因。
为防止这些现象的发生,只有使轴向应力大于τ/f和整个密封面盘内压力,这个最小轴向预紧力就是最佳的预负荷。
当压紧预负荷不太大情形时。
事实上,当知到在吸入、排出下盘接触现的主要应力,就可估算接触情形。
图7显示了径向、轴向和环向应力,与图6填料盘相同,只是在不同的运行情况下。
虽然在设计时用这种方法估算预负荷很的用,但只是作为一个参考值而不是最终结果。
事实上还包括选择摩擦系数、压力分布等一些不能忽略的因素,前者较难确定,后者在不同时间不一样是一个不确定因素。
另外,计算程序无法由于气体渗透而引起的现场变形和接触区域的应力分布。
3.2.3起高压填料盘抗疲劳改进的建议
前已叙述,在填料承压和不承压间的不连续区域(图4a、b、c、d)有高的应力集中,在制造中需高度重视。
这个区域,在高的压差下的大的应力集中,如果这样,支承密封环的环状肩在其压力侧易有大的弯曲,引起拉伸应力(径向和环向),还可能起过因热套而产生的预压缩,设想如图4b那样的几何形状是非常危险的,可能在底部释放沟槽产生大的应力集中。
在想得到这个特殊地点的应力状况的详细情况时,通过研究气缸的关键点作用力的分布,对一套填料盘在负荷作用下的详细分析,通过叠加作用,可有针对性地对关键点进行检测。
吸入、排出下的三种主要应力(如表4中σc、σt、σn)可以确定。
主要应力通过VonMises准则可确每种情况下理想应力σid和吸入、排出时的应力差Δσid,如表4所示。
由于高的压差σt在排出
表4
操
作
条
件
压力
典型应力气缸曲面槽
完好表面
有开槽表面
P1
P2
σid
Δσid
σid
Δσid
1
吸入
排出
160
195
160
160
110
10
200
20
2
吸入
排出
160
260
160
160
215*
100
505
140
3
吸入
排出
190
290
140
150
225*
105
460
155
4
吸入
排出
140
290
140
140
313*
172
753
218
5
吸入
排出
150
330
140
230
225
120
460
150
6
吸入
排出
160
300
160
160
274*
170
700
195
7
吸入
排出
160
340
160
160
274*
172
900
260
时为拉伸应力,有*表示,可看出即使在安全极限内失效,应力仍是很大的。
考虑到它们承受的压力分布为理想状况,在偶然压力升高情况下会发生危险,如在释放槽处有突发刻痕。
为此需对释放槽周围区域分析,当压差越来越重要,还可能超过材料的强度极限。
由于在工作时无法改进,需对表面预压缩处理,例如冷辊压、喷丸硬化、渗氮等。
本装置中采用了在填料盘表面进行镀银0.02mm的银层,效果很好。
3.3超高压填料失效的分析及研究
3.3.1一、二级超高压填料的压力分布分析
为了更好地研究填料的受力情况,简化方法是在润滑油注入衬套处测量,有三处,另外也在压缩室处测量。
如图8在轴向和环向表面有应变仪。
通过放大器,测量信号可通过示波器或电流启示录仪得出,还可通过机身上的特殊传感器显示出死点位置。
这样气缸以及压缩室中压力可精确得出。
第一组测试在一台管式法透平驱动二次机第二级气缸上得出,填料包括两个三瓣减压环与直径间隙为0.08mm和五组径向、切向密封环,和减压环一样,其轴向间隙为0.15mm。
由此得出图9压力分布曲线。
通过此方法可以较清楚地知到每道环的工作状况以及不同的压力或静压对它的影响。
密封环处的压力不能通过测量得到,而是通过有关迷宫密封公式得到。
第二组测试在反应装置上一台53000Kg/H压缩机一、二级气缸上测得的。
一、二级填料都有一个三瓣减压环,有较小的环向间隙,有五组密封环,所有的密封元件有0.15mm的轴向间隙。
如图9中所示。
考虑第二组气缸填料工作情况;填料在800bar的吸入和2500bar的排出压力下工作。
可看出在第一个和第二个减压环后压力曲线为多变压缩和多变膨胀过程,这些环所受的压差不够充分,有800~900bar压力降,等于压缩和膨胀期间在吸入排出间波动压力的55%。
由于直径间隙的不同,两减压环在整个前冲程中不同,因此第二环有较大的压降。
开始两副密封环有较明显的阻塞和密封,这些元件在一个较长时期的排放中承受着1300bar压力波动,是气缸中总的压力波动的70%。
这可从图9中的二级填料压力分布图中可以看出。
开始三组密封元件受气缸内压力波动的影响,而最后两组承受基本不变的压力。
第一组承受的压力波动70%传递到下一组,30%传递到到第三组,最后两组承受的压力波动基本可以忽略。
可看出最后润滑油注入衬套处有不变的压力,通过预先的假设计算60%多的压力由最后的密封环承受。
吸入阀上游和排出阀下游的压力波动对气缸内压力产生较大影响。
第一级出口压力波动与压缩频率相吻合,而第一级吸入、第二级吸入排出为其两倍,在压缩和膨胀中起到较好的密封作用。
减压环承受着80%多的压力波动,一级为700bar,二级为1000bar,在第一级里效果更佳,从其压力曲线不太陡上可看出,这可能是气体容积变化较大,第一级为16%,第二级为5%。
这可用来解释一、二级多变指数有差异的部分原因。
可知气体物性越接近液体,减压环起作用困难越大,效果也越差。
再者我们对运行了1000~2000hr的填料进行检查时。
如图9中的吸入二级填料压力分布图中显示在第一级和第二级填料重装时的径向厚度,这样我们有了每个元件的磨损曲线,可看出在第一级和最后级的磨损加剧了。
在径向环和切向环,在第一级和第二级,曲线发展非常相似。
从磨损的数值可看出,切向环比径向环磨损严重,其起的密封作用也较大。
在第一级上好象没有磨损的机会,这是由于连接销断了,可能是回流造成的。
这样气体就作用在第二环上,加重了其磨损,切向环的磨损比允许的还多,这个说明了环和磨损不是一致的。
在第二级,回流使第一组密封环的弹簧折了,失去了作用,而第二组连接销断了,气体压力就第三组承受了。
在一、二级中机身侧的最大磨损是由承受的恒定压力造成的。
第一级填料的最后一道径向环的磨损是一个例外,这种情况在其它压缩机上也出现过,原因如下:
当径向环承受一恒定压时,对杆来说基本不起密封作用,只是对切向环起保护作用,阻止切向环受气体压力。
在承受的压力变化时,在吸气阶段,当气体又有返回到气缸中的趋势时,径向环被迫起到密封作用,这个密封作用不可能彻底,因为径向环留有气体通道。
但这个暂时、有限的作用造成了可观的磨损,在这种情况下径向环的磨损的压力侧最大,在较小的压力区域磨损较小。
通过尺寸检查和以上分析,可知磨损方式与填料压力分布有关。
恒定压造成的磨损如图10曲线a所示,最大的磨损在机身侧密封件上。
压力波动造成的磨损情况相反,如曲线b所示,最大的磨损在第一组密封环。
综合磨损如曲线c所示,最大的磨损在填料的尾部。
当压力波动与压力恒定谁取主要作用时,最大磨损就出现在相应侧。
实际的磨损曲线如d所示,由于回流现象迟早会造成一些密封环失效,它们的磨损也就比其它的小得多。
通过分析可知,密封环的受压情形与其磨损情况相吻合。
填料密封效果的好坏与减压环通道大小有关,这样由回流造成的危险可大大降低。
另外,如果柱塞对中良好,填料寿命也会延长。
3.3.2超高压填料的性能分析研究
超高压压缩机工作在1500bar~3500bar,气缸和密封件的工作状况非常恶劣。
在一、二级填料进行研究,经过一段时间的运行后(约1000~2000H),在密封面上的轻微的磨损。
从填料的结构上看出,填料包括一个或两个剖分减压环和五组径向、切向密封环(如图8中的R环和T环)所示,为特殊铜合金,有优良性能,保证足够的强度、低摩擦系数、高的热传导率,摩擦热通过填料盘能迅速消耗掉,它的布氏硬度在55~80之间。
填料的密封性能受到柱塞的光洁度、气缸的润滑油性能的因素和减压环的影响,对减压环须特殊考虑。
我们可以通过分析填料的运动来考虑它们的作用,让我们设想任何时候在气缸中压力可分为与吸入压力
相等的恒压和出入压差相等的压力波动值所组成。
这样我们就可得出静压部分,作用于机身侧最后的密封环上。
通过实验,在恒定压运转的气体在压缩机内,最后的密封环几乎承受着所有的负荷。
各种形式的压缩可通过多变压缩来表示,在一个陡的膨胀下降过程,由于气体留在余隙容积里,在提出和吸入保持着相同的压力。
当气体压力突然增大时,减压环对其减压,阻止了气体的逃跑,并将传播到密封环的气体减小到最小。
减压环最重要的作用是当柱塞开始往机身侧运动时,阻止气体从密封环中向气缸中反冲。
如果这个阻止作用失败,第一道密封环中气体压力马上下降,接下来的过程是在压缩室中进行沿陡曲线下降的膨胀过程,压力很快回到吸入压力,作用在第一道环上的作用突然反向,造成径向环特别是切向环的突然撞击,而起密封主要作用的是切向环。
这种突发现象与减压环的效果有关,对填料环有如下的破坏作用:
-使径向环、切向环连接销折断
-切向环唇口折断
-对弹簧有损害
经过一段时间后,第一道密封环失效,上述现象又在第二道密封环上上演,只不过是时间的快慢而已。
所以对填料的性能分析和研究是很的必要的。
3.3.3对超高压填料的必要磨合措施
磨合的目的是为了在运动部分得到较小的空隙,也即是在这种情况下使气体流过空隙的数量减少到最好状态。
此种密封方法的优点是:
摩擦很小并且严密性仅逐渐地改变。
实践中,在压缩机(4000bar的压缩机)必需对其填料进行一定的磨合。
平均速度在2~3米/秒的柱塞杆也都以磨合方法来达到密封。
从而由下面的公式可能计算出每秒钟气体流过环形密封环的量:
式中
----环形间隙cm
----环开间隙之平均直径实际上等于孔之直径cm
----密封前后之压力差数kg/cm2
----液体的粘滞系数kg.秒/cm2
-----密封长度cm
以上方程式对计算同心环形间隙时是很正确的。
当柱塞偏心时,每秒钟的流量能增大1.5倍。
一般在柱塞杆的磨合表面上开环形槽,实际上并不能提高密封的严密性,而其宽度则应自密封的总长---L内减去。
槽之优点为能积储与润滑油一起落入密封中的固体颗粒,这就可防止磨合表面发生划痕及很快地磨损。
如果间隙极小,则会产生分子粘着力,此力能减低流体之流动。
此外,在往复运动之机器中,由于润滑油被运动部分由间隙带出,故润滑油通过的流量比计算所得的流量要大些。
所以对超高压填料,特别是金属填料的新组装后做必要的磨合是很关键的,这样不但保证密封的可靠性,还直接影响超高压填料的使用寿命。
4结束语
超高压填料的使用寿命的长短直接影响超高压压缩机的运行周期,而填料就是它的一个最弱的环节,所以对超高压压缩机的超高压填料组的分析研究,作出对策及预防措施是很有必要的,对装置的运行,对生产的稳定都起到了不可估量的作用。
参考文献:
1Ъ.A.柯仑多尔夫著.化学工业设计院翻译科译.化工高压技术.化学工业出版社.1958
2意大利新比隆超高压压缩机基础资料