机电一体化课程设计挖掘机液压系统设计.docx
《机电一体化课程设计挖掘机液压系统设计.docx》由会员分享,可在线阅读,更多相关《机电一体化课程设计挖掘机液压系统设计.docx(10页珍藏版)》请在冰豆网上搜索。
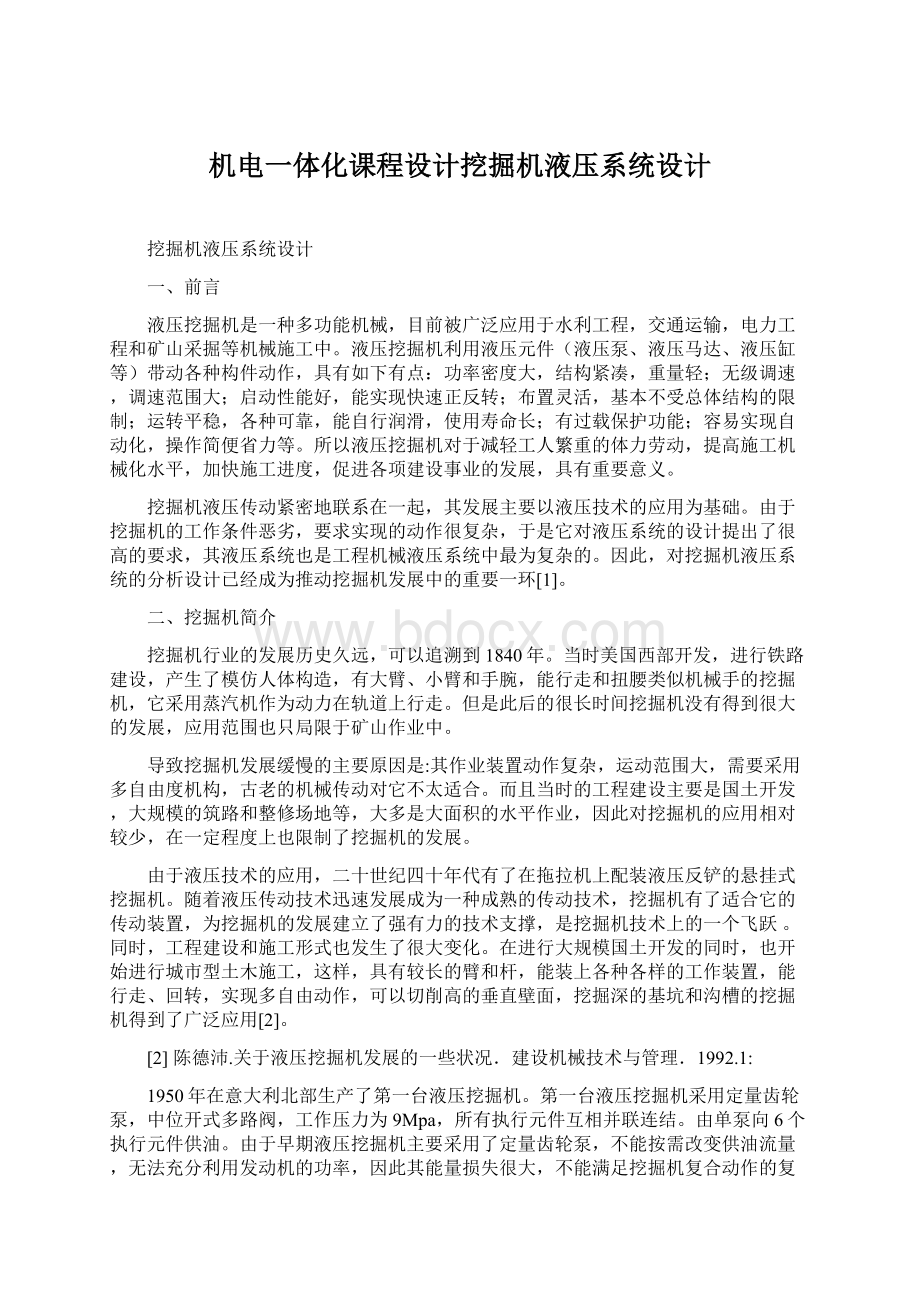
机电一体化课程设计挖掘机液压系统设计
挖掘机液压系统设计
一、前言
液压挖掘机是一种多功能机械,目前被广泛应用于水利工程,交通运输,电力工程和矿山采掘等机械施工中。
液压挖掘机利用液压元件(液压泵、液压马达、液压缸等)带动各种构件动作,具有如下有点:
功率密度大,结构紧凑,重量轻;无级调速,调速范围大;启动性能好,能实现快速正反转;布置灵活,基本不受总体结构的限制;运转平稳,各种可靠,能自行润滑,使用寿命长;有过载保护功能;容易实现自动化,操作简便省力等。
所以液压挖掘机对于减轻工人繁重的体力劳动,提高施工机械化水平,加快施工进度,促进各项建设事业的发展,具有重要意义。
挖掘机液压传动紧密地联系在一起,其发展主要以液压技术的应用为基础。
由于挖掘机的工作条件恶劣,要求实现的动作很复杂,于是它对液压系统的设计提出了很高的要求,其液压系统也是工程机械液压系统中最为复杂的。
因此,对挖掘机液压系统的分析设计已经成为推动挖掘机发展中的重要一环[1]。
二、挖掘机简介
挖掘机行业的发展历史久远,可以追溯到1840年。
当时美国西部开发,进行铁路建设,产生了模仿人体构造,有大臂、小臂和手腕,能行走和扭腰类似机械手的挖掘机,它采用蒸汽机作为动力在轨道上行走。
但是此后的很长时间挖掘机没有得到很大的发展,应用范围也只局限于矿山作业中。
导致挖掘机发展缓慢的主要原因是:
其作业装置动作复杂,运动范围大,需要采用多自由度机构,古老的机械传动对它不太适合。
而且当时的工程建设主要是国土开发,大规模的筑路和整修场地等,大多是大面积的水平作业,因此对挖掘机的应用相对较少,在一定程度上也限制了挖掘机的发展。
由于液压技术的应用,二十世纪四十年代有了在拖拉机上配装液压反铲的悬挂式挖掘机。
随着液压传动技术迅速发展成为一种成熟的传动技术,挖掘机有了适合它的传动装置,为挖掘机的发展建立了强有力的技术支撑,是挖掘机技术上的一个飞跃。
同时,工程建设和施工形式也发生了很大变化。
在进行大规模国土开发的同时,也开始进行城市型土木施工,这样,具有较长的臂和杆,能装上各种各样的工作装置,能行走、回转,实现多自由动作,可以切削高的垂直壁面,挖掘深的基坑和沟槽的挖掘机得到了广泛应用[2]。
[2]陈德沛.关于液压挖掘机发展的一些状况.建设机械技术与管理.1992.1:
1950年在意大利北部生产了第一台液压挖掘机。
第一台液压挖掘机采用定量齿轮泵,中位开式多路阀,工作压力为9Mpa,所有执行元件互相并联连结。
由单泵向6个执行元件供油。
由于早期液压挖掘机主要采用了定量齿轮泵,不能按需改变供油流量,无法充分利用发动机的功率,因此其能量损失很大,不能满足挖掘机复合动作的复杂要求,且可操纵性差。
另外,早期试制的液压挖掘机是采用飞机和机床的液压技术,缺少适用于挖掘机各种工况的液压元件,配套件也不齐全,制造质量不够稳定。
从二十世纪六十年代到八十年代中期,液压挖掘机进入了推广和蓬勃发展的阶段,各国挖掘机制造厂和品种增加很快,产量猛增。
1968-1970年间,液压挖掘机产量己经达到挖掘机总产量的83%,其时对挖掘机液压系统的研究也已经十分成熟,液压挖掘机已经具有了同步控制系统和负载敏感系统L。
自第一台手动挖掘机诞生以来的160多年当中,挖掘机一直在不断地飞跃发展,其技术已经发展到相对成熟稳定的阶段。
目前国际上迅速发展全液压挖掘机,对其控制方式不断改进和革新,使挖掘机由简单的杠杆操纵发展到液压操纵、气压操纵、液压伺服操纵和电气控制、无线电遥控、电子计算机综合程序控制。
在危险地区或水下作业采用无线电操纵,利用电子计算机控制接收器和激光导向相结合,实现了挖掘机作业操纵的完全自动化。
所有这一切,挖掘机的全液压化为其奠定了坚实的基础,创造了良好的前提[3]。
据有关专家估算,全世界各种施工作业场约有65%至70%的土石方工程都是由挖掘机完成的。
挖掘机是一种万能型工程机械,目前已经无可争议地成为工程机械的第一主力机种,在世界工程机械市场上己占据首位,并且仍在发展扩大。
挖掘机的发展主要以液压技术的应用为基础,其液压系统已成为工程机械液压系统的主流形式。
随着科学技术的发展和建筑施工现代化生产的需要,液压挖掘机需要大幅度的技术进步,技术创新是液压挖掘机行业所面临的新挑战。
在技术方面,挖掘机产品的核心技术就是液压系统设计,所以对其液压系统的分析研究具有十分重要的现实意义。
三、国内外研究现状及发展动态
(1)国外研究状况及发展动态
从20世纪60年代液压传动技术开始应用在挖掘机上至今,挖掘机液压系统己经发展到了相当成熟的阶段。
目前国际上先进的挖掘机产品的额定压力大都在30MPa以上,并且随着材料科学技术的进步,有朝着更高的压力甚至采用超高压液压技术方向发展的趋势;流量通常在每分钟数百升;功率在数百千瓦以上。
如德国Orensttein&
Koppe制造的目前世界上首台最大的RH40。
型全液压挖掘机,铲斗容量达42m3,液压油源为18台变量轴向柱塞泵,总流量高达10200L/min,原动机为2台QSK60柴油发动机,总功率高达2014kW,由于液压挖掘机经常在较恶劣环境下持续工作,其各个功能部件都会受到恶劣环境的影响.系统的可靠性日益受到重视。
美、英、日等国家推广采用有限寿命设计理论,以替代传统的无限寿命设计理论和方法,并将疲劳损伤累积理论断裂力学、有限元法、优化设计、电子计算机控制的电液伺服疲劳试验技术、疲劳强度分析方法等先进技术应用于液压挖掘机强度研究方面,不断提高设备的可靠性。
美国提出了考核动强度的动态设计分析方法。
日本制定了液压挖掘机构件的强度评定程序,研制了可靠性信息处理系统使液压挖掘机的运转率达到85%-95%,使用寿命超过1万小时。
近几年来,随着液压挖掘机产量的提高和使用范围的扩大,世界上著名的挖掘机生产商纷纷采用各种高新技术,来提高自己挖掘机在国际上的竞争力,主要表现在五个方面:
(1)液压系统逐渐从开式系统的转变;
(2)系统的节能技术成为研究的重点;(3)系统的高压化和高可靠性发展趋势日益凸显;(4)系统的操纵特性上升到很重要的地位;(5)液压系统与电子控制的结合成为潮流[5]。
[5]章崇焕.国外大型矿用挖掘机的最新发展.矿山机械.1993
(1)开式向闭式液压系统的转变
采用三位六通阀,其特点是有两条供油路,其中一条是直通供油路,另一条是并联供油路。
由于这种油路调速方式是进油节流调速和旁路节流调速同时起作用,其调速特性受负载压力和油泵流量的影响,因此这种系统的操纵性能、调速性能和微调性能差。
另外,当液压作用元件一起复合动作时,相互干扰大,使得复合动作操纵非常困难。
由于挖掘机作业工程中要求对液压元件能很好地控制其运动速度和进行微调,而且在其工作的许多工况下要求多个执行元件完成复合动作,而长期以来使用的开式液压系统无法满足挖掘机的调速和复合动作的要求。
近年来在国外的挖掘机液压系统中出现了闭式负载敏感系统(CLSS)。
它可以采用一个油泵同时向所有液压作用元件供油,每一个液压作用元件的运动速度只与操纵阀的阀杆行程有关,与负载压力无关,泵的流量按需提供,而且多个液压作用元件同时动作时相互之间干扰小,因此操纵性好是闭式液压系统的主要特点。
这种系统非常符合挖掘机操作的要求,它操纵简单,对司机的操纵技巧要求低,在国际上己经获得较广泛的使用,是挖掘机液压系统的发展趋势。
目前日本小松公司已经把大量挖掘机液压系统从开式系统改为闭式系统了。
(2)节能技术的应用
目前液压挖掘机上典型的节能技术基本上有两种。
即负载敏感技术和负流量控制技术,目前液压挖掘机都选用其中一种控制技术来实现节能要求。
负载敏感技术是一种利用泵的出口压力与负载压力差值的变化而使系统流量随之相应变化的技术。
德国曼内斯曼(Mannesmann)公司研制的一种负载传感系统,将其安装在液压系统中,可以控制一个或几个液压作用元件,而与对其施加的载荷无关。
该系统不仅易于操纵,而且微动控制特性很好。
其最大的特点就是可以根据负载大小和调速要求对油泵进行控制,从而实现在按需供流的同时,使调速节流损失△P控制在很小的固定值,从而达到节能的目的lzs.e57负流量控制技术是通过位于主控制阀后面的节流阀建立的压力对主泵的排量进行调节的技术。
日前以韩国现代(HYUNDAI)、日本小松(KOMATSU)和日本日立(HITACHI)为代表的许多国外著名品牌的挖掘机生产商都在自己的挖掘机液压系统中使用了负流量控制技术。
这种控制技术具有稳定性好、响应快、可靠性和维修性好等特点,但在起始点为重负荷下作业时,因流量与负载有关,所以可控制性较差[6]。
[6
(3)提高负载能力和可靠性
为了提高挖掘机的负载能力,直接的方法是提高其液压系统工作压力、流量和功率。
目前,国际上先进的挖掘机产品的额定压力大都在30MPa以上,并且随着材料科学技术的进步,有朝着更高的压力甚至采用超高压液压技术方向发展的趋势;流量通常在每分钟数百升;功率在数百千瓦以上。
如德国Orensttein&Koppe制造的型全液压挖掘机,铲斗容量达42立方米液压油源为18台变量轴向柱塞泵,总流量高达100200
L/min,原动机为2台QSK60柴油发动机,总功率高达2014kW,由于液压挖掘机经常在较恶劣环境下持续工作,其各个功能部件都会受到恶劣环境的影响。
系统的可靠性日益受到重视。
美、英、日等国家推广采用有限寿命设计理论,以替代传统的无限寿命设计理论和方法,并将疲劳损伤累积理论、断裂力学、有限元法、优化设计、电子计算机控制的电液伺服疲劳试验技术、疲劳强度分析方法等先进技术应用于液压挖掘机强度研究方面,不断提高设备的可靠性。
美国提出了考核动强度的动态设计分析方法。
日本制定了液压挖掘机构件的强度评定程序,研制了可靠性信息处理系统,使液压挖掘机的运转率达到85%-95%,使用寿命超过1万小时。
(4)重视操纵特性
挖掘机液压系统的操纵特性越来越受到重视。
日前国际上迅速发展全液压挖掘机,不断改进和革新控制方式,使挖掘机由简单的杠杆操纵发展到液压操纵、气压操纵、液压伺服操作和电气控制,无线电遥控、电子计算机综合程序控制。
各种高新技术的应用,使得挖掘机液压系统操纵特性大大提高。
(5)电子一液压集成控制成为当前主要研究目标
电子控制技术与液压控制技术相结合的电子一液压集成控制技术近年来获得了巨大发展,特别是传感器、计算机和检测仪表的应用,使液压技术和电子控制有机结合,开发和研制出了许多新型电液自动控制系统,提高了挖掘机的自动化程度,推动着挖掘机的迅猛发展。
目前国外先进品牌的挖掘机在电液联合控制方面的研究己趋成熟。
美国林肯一贝尔特公司新C系列LS-5800型液压挖掘机安装了全自动控制液压系统,可自动调节流量,避免了驱动功率的浪费。
日本住友公司生产的FJ系列五中新型号挖掘机配有与液压回路连接的计算机辅助的功率控制系统,利用精控模式选择系统,减少燃油、发动机功率和液压功率的消耗,并延长了零部件的使用寿命。
(2)国内研究情况及发展动态
从国内情况来看,我国挖掘机行业整体发展水平较国外缓慢,在挖掘机液压系统方面的理论还比较薄弱。
国内大部分挖掘机企业在挖掘机液压系统传统技术方面的研究具有一定基础,但由于采用传统液压系统的挖掘机产品在性能、质量、作业效率、可靠性等方面均较差,因此采用传统液压系统的挖掘机在国内市场上基本失去了竞争力,取而代之的是采用各种高新技术的国外挖掘机产品。
先进的挖掘机液压系统都被国际上一流的生产企业垄断,国内企业在该领域的研究几乎是空白,这样国内的挖掘机生产厂家就无法独立制造出性能优异的挖掘机,绝大部分的市场份额都被国外各种品牌的挖掘机所占据。
以20t级的中型液压挖掘机为例,国产20t级挖掘机大多数是欧洲80年代初的技术,同90年代初以来在国内形成批量的日本小松、日立、神钢以及韩国大宇、现代等机型相比,其主要差距柴油机功率偏低,液压系统流量偏小,液压系统特性差,导致平台回转速度低,行走速度低,各种性能参数均偏小,整机性能和作业效率较国外偏低[7]。
[7]陈正利.我国液压挖掘机发展的几个重要阶段及其前景展望.建筑机械.1999.
四、液压挖掘机的基本类型和主要特点
单斗液压挖掘机可按用途及其主要装置的特征进行分类。
按液压挖掘机主要用途及工作装置的不同分为通用型和专用型两种。
中小型挖掘机大多数为通用型,以挖掘土攘容重18000N,1m3为标准反铲斗的主要装置外,还配有道于挖掘各种轻重土质和挖掘幅度的反铲、正铲、抓斗、起重等多种装置而大型液压挖掘机则以矿用正铲为主要装置外,一般亦配有挖掘轻重土、各种挖掘幅度的正、反铲等装置。
主要用于矿山采掘和装载、称采矿或矿用型。
按工作装置的结构不同分为铰接式和伸缩臂式挖掘机,常用者均为铰接式,伸缩臂式挖掘机因可用于平整清理场地等作业,所以有挖掘平地机之称.按行走装置的不同,液压挖掘机分为履带式、轮胎式、汽车式、悬挂式及拖式等种。
履带式因有良好通过性能应用最广,对松软地面或沼泽地带还可采用加宽、加长以及浮式履带来降低接地比应。
轮式挖掘机具有行走速度快,机动性好、可在城市道路边行,故近年来在中小型挖掘机中发展较快。
汽车式、悬挂式是以汽车及拖拉机为基础机械装设挖掘或装载工作装置的小型挖掘机.适用于城建小量土方工程及农村建筑.拖式则没有行走驱动机构,转移时由牵引车牵引,主要优点为结构简单、成本低。
按回转部分转角的不同,液压挖掘机有全回回转式的,小型液压挖掘机如悬挂式等工作装置仅能作1800左右的回转,为半回转式。
液压挖掘机按主要机构是否全部采用液压传动又分为全液压式与半液压式两种。
两者区别在于半液压传动挖掘机的行走机构采用机械传动,少数挖掘机仅工作装置采用液压传动,如大裂矿用挖掘机等。
目前国产轮胎式液压挖掘机多采用半压式。
五、液压挖掘机结构与工作原理
液压挖掘机由于在动力装置和工作装置之间采用容积式液压传动,靠液体的压力能进行工作,相对机械传动具有许多优点:
能无极调速且调速范围大,最大速度和最小速度之比可达1000:
1能得到较低的稳定转速;快速作用时,液压元件产生的运动惯性较小,并可作高速反转;传动平稳,结构简单,可吸收冲击和振动;操纵省力灵活,易实现自动化控制;易实现标准化、通用化、系列化。
因此液压挖掘机逐步取代机械式挖掘机是必然的趋势。
单斗液压挖掘机是装有一只铲斗并采用液压传动进行挖掘作业的机械。
它是目前挖掘机械中重要的机种。
单斗液压挖掘机的作业过程是以铲斗(一般装有斗齿)的切削刃切削土壤并将土装入斗内,斗满后提升。
回转至卸上位置进行卸土,卸空后铲斗再转回并下降到地面进行下一次挖掘。
当挖掘机挖完一段土后,机械移动一段距离,以便继续作业。
因此单斗液压挖掘机是一种周期作业的自行式上方机械[7]。
[7
(1)液压挖掘机整机性能
液压挖掘机可分为:
动力系统、机械系统、液压系统、控制系统,如图2.1所示。
液压挖掘机作为一个有机整体,其性能的优劣不仅与工作装置机械零部件性能有关,还与液压系统、控制系统性能有关[8]。
[8
图2.1液压挖掘机整体系统图
1、动力系统
挖掘机工作的主要特点是环境温度变化大,灰尘污物较多,负荷变化大,经常倾斜工作,维护条件差。
因此液压挖掘机原动力一般由柴油机提供,柴油机具有工作可靠、功率特性曲线硬、燃油经济等特点,符号挖掘机工作条件恶劣,负荷多变的要求。
挖掘机的额定负荷与汽车。
拖拉机不同,汽车和拖拉机指在最高转速下、连同机油泵、发电机等必要附件,巧分钟内的最大功率;挖掘机是指在额定转速下一小时以上的额定功率。
挖掘机采用车用柴油机时,最大功率指数降低。
2、机械系统
液压挖掘机的机械系统部分是完成挖掘机各项基本动作的直接执行者,主要包括:
行走装置是整个机器的支撑部分,承受机器的全部重量和工作装置的反力,同时能使挖掘机作短途行驶.按照结构的不同,分履带式和轮胎式。
回转机构使挖掘机上车围绕中央回转轴作360度的回转的机构,包括驱动装置和回转支撑。
工作装置是挖掘机完成实际作业的主要组成部分,常用的有反铲、正铲、装载、起重等装置,而同一种装置可以有多种结构形式,前面所述的反铲装置应用最为广泛。
3、液压系统
液压挖掘机的回转、行走和工作装置的动作都由液压传动系统实现,原动机驱动双联液压泵,把压力油分别送到两组多路换向阀。
通过司机的操纵,将压力油单独或同时送往液压执行元件(液压马达和液压油缸)驱动执行机构工作。
液压挖掘机的主要运动有整机行走、转台回转、动臂升降、斗杆收放、铲斗转动等。
这些运动都靠液压传动。
根据以上工作要求,把各液压元件用油管有机地连接起来地组合体既是液压挖掘机地液压系统。
该系统地功能是把发动机地机械能以油液为介质,利用油泵转变为液压能,传送给油缸、油马达等转变为机械能,再传动各执行机构,实现各种运动和工作过程。
液压系统设计得合理与否,对挖掘机的性能起着决定性的作用。
同样的元件,若系统设计不同,则挖掘机性能差异很大。
液压系统习惯上按主油泵的数量、功率调节方式和回路的数量来分类。
4、控制系统
液压挖掘机控制系统是对发动机、液压泵、多路换向阀和执行元件(液压缸、液压马达)等进行控制的系统。
电子技术和计算机技术的飞速进步,使挖掘机有了越来越先进的控制系统,使液压挖掘机向高性能、自动化和智能化发展。
目前挖掘机研究重点正逐步向智能化机电液控制系统方向转移[9]。
[9
(2)液压挖掘机结构
1.液压挖掘机组成
为了实现液压挖掘机的各项功能,单斗液压挖掘机需要两个基本组成部分,即机体(或称主机)和工作装置。
机体是完成挖掘机基本动作并作为驱动和操纵挖掘机进行工作的荃础,可以是履带牵引车辆或轮式牵引车辆。
可细分为行走装置、回转装置、液压系统、气压系统、电气系统和动力装置。
其中动力装置、操纵机构、回转机构和辅助设备均可在回转平台上,总称上车部分,它与行走机构(又称下车部分)用回转支撑相连,平台可以围绕中央回转轴作3600的全回转。
工作装置根据工作性质的不同,可配备反铲、正铲、装载、起重等装置,分别完成挖掘、装载、抓取、起重、钻孔、打桩、破碎、修坡、清沟等工作。
挖掘机的基本性能决定于各部分的构造、性能及其综合的效果[11]。
2.单斗反铲液压挖掘机
反铲装置主要用于挖掘停机面以下的土壤。
斗容量小于1.6M3的中小型液压挖掘机通常选用反铲装置,它分为整体臂式和组合臂式。
其中长期作业条件相似的挖掘机反铲装置大多采用整体鹅颈式动臂结构。
采用这种动臂有利于加大挖掘深度,且结构简单、价格低廉。
刚度相同时,其重量比组合动臂轻,是目前应用最广泛的液压挖掘机工作装置结构形式。
铰接式反铲是单斗液压挖掘机最常用的结构型式,动臂、斗杆和铲斗等主要部件彼此铰接,在液压缸的作用下各部件绕铰接点摆动,完成挖掘、提升和卸土等动作。
如图2.1所示,整体鹅颈式动臂反铲挖掘机工作装置主要由动臂、动臂油缸、斗杆、斗一杆油缸、铲斗、铲斗油缸、摇臂、连杆、销轴等组成。
装置各运动部件之间全部采用销轴铰接,以动臂油缸来支撑和改变动臂的倾角,通过动臂油缸的伸缩可使动臂绕下。
铰点转动实现动臂的升降。
斗杆铰接于动臂的上端,由斗杆油缸控制斗杆与动臂相对角度。
当斗杆油缸伸缩时,斗杆可绕动臂上铰点转动。
铲斗与斗杆前端铰接,并通过铲斗油缸伸缩使铲斗转动。
为增大铲斗的转角,通常采用摇臂连杆机构来和铲斗联。
3.液压挖掘机工作循环过程
1、斗杆油缸2、动臂3、油管4、动臂油缸5、铲斗
6、斗齿7、侧齿8、连杆9、摇杆10、铲斗油缸11、斗杆
图2.2反铲挖掘机工作装置
首先液压挖掘机驱动行走马达和配套土方运输车辆一起进入作业面,运输车辆倒车、调停,停靠在挖掘机的侧方或后方。
挖掘机司机扳动操纵手柄,使回转马达控制阀接通,于是回转马达转动并带动上部平台回转,使工作装置转向挖掘地点,在执行上述过程的同时操纵动臂油缸换向阀,使动臂油缸上腔进油,将动臂下降,直至铲斗接触地面,然后司机操纵斗杆油缸和铲斗油缸的换向阀,使两者的大腔进油,配合动作以加快作业进度,进行复合动作的挖掘和装载:
铲斗装满后将斗杆油缸和铲斗油缸的操纵手柄扳回中位,使铲斗和斗杆油缸闭锁,再操纵动臂油缸换向阀,使动臂油缸的下腔进油,将动臂提升,举起装满土的铲斗离开工作面,随即扳动平台回转换向阀手柄,使上部平台回转,带动铲斗转至运输车辆上方,再操纵斗杆油缸使铲斗高度稍降一些,并在适当的高度操纵铲斗油缸使铲斗卸土。
土方卸完后,使平台反转并降低动臂,直到铲斗回到作业点上方,以便进行下一工作循环[12]。
(3)液压挖掘机传动原理
液压挖掘机采用三组液压缸使工作装置具有三个自由度,铲斗可实现有限的平面转动,加上液压马达驱动回转运动,使铲斗运动扩大到有限的空间,再通过行走马达驱动行走(移位),使挖掘空间可沿水平方向得到间歇地扩大,从而满足挖掘作业的要求。
液压挖掘机传动示意图,如图2.3所示,柴油机驱动液压泵,操纵分配阀,将高压油送给各液压执行元件(液压缸或液压马达)驱动相应的机构进行工作。
液压挖掘机的工作装置采用连杆机构原理,各部分的运动通过液压缸的伸缩来实现。
反铲工作装置由铲斗1、斗杆2、动臂3、连杆4及相应的三组液压缸5.6.7组成。
动臂下铰点铰接在转台上,通过动臂缸的伸缩,使动臂连同整个工作装置绕动臂下铰点转动。
依靠斗杆缸使斗杆绕动臂的上铰点转动;而铲斗铰接于斗杆前端,通过铲斗缸和连杆则使铲斗绕斗杆前铰点转动。
挖掘作业时,接通回转马达,转动转台,使工作装置转到挖掘位置,同时操纵动臂缸小腔进油使液压缸回缩;动臂下降至铲斗触地后再操纵斗杆缸或铲斗缸,液压缸大腔进油而伸长,使铲斗进行挖掘和装载工作。
铲斗装满后,铲斗缸和斗杆缸停动并操纵动臂缸大腔进油,使动臂抬起,随即接通回转马达,使工作装置转到卸载位置,再操纵铲斗缸或斗杆缸回缩,使铲斗翻转进行卸土。
卸完后,工作装置再转至挖掘位置进行第二次挖掘循环。
在实际挖掘作业中,由于土质情况、挖掘面条件以及挖掘机液压系统的不同,反铲装置三种液压缸在挖掘循环中的动作配合可以是多样的、随机的[13]。
[13]
1、铲斗2、斗杆3、动臂4、连杆5、6、7、液压油缸
I、挖掘装置II、回转装置III、行走装置
图2.3液压挖掘机传动示意图
总之,液压挖掘机是由多学科、多系统组成的有机整体,只有在系统层面上的各系统、各学科协同优化才能获取挖掘机整机的最佳性能。
六、液压系统方案及参数确定
表4.1WY200C液压履带式挖掘机主要技术参数
项目名称
单位
数值
标准斗容量
m3
1
发动机型号
6135K-16
发动机标定输出功率
kW/r/min
106/2100
最大挖掘半径
m
最大挖掘高度
m3/h
最大挖掘深度
m
最大卸载高度
m
回转速度
r/min
行走速度
km/h
爬坡能力
%
70
作业循环时间
S
18-22
主机长/宽度
MPa
履带平均接地比压
MPa
发动机额定转数
r/min
2100
整机质量
t
理论生产率
m3/h
200
最大挖掘力
kN
142
系统工作压力
MPa
36
履带板宽度
m
主机运输尺寸
(长X宽X高)
mm
9850x3000x3100