旋压技术在现代工业中的应用研究.docx
《旋压技术在现代工业中的应用研究.docx》由会员分享,可在线阅读,更多相关《旋压技术在现代工业中的应用研究.docx(23页珍藏版)》请在冰豆网上搜索。
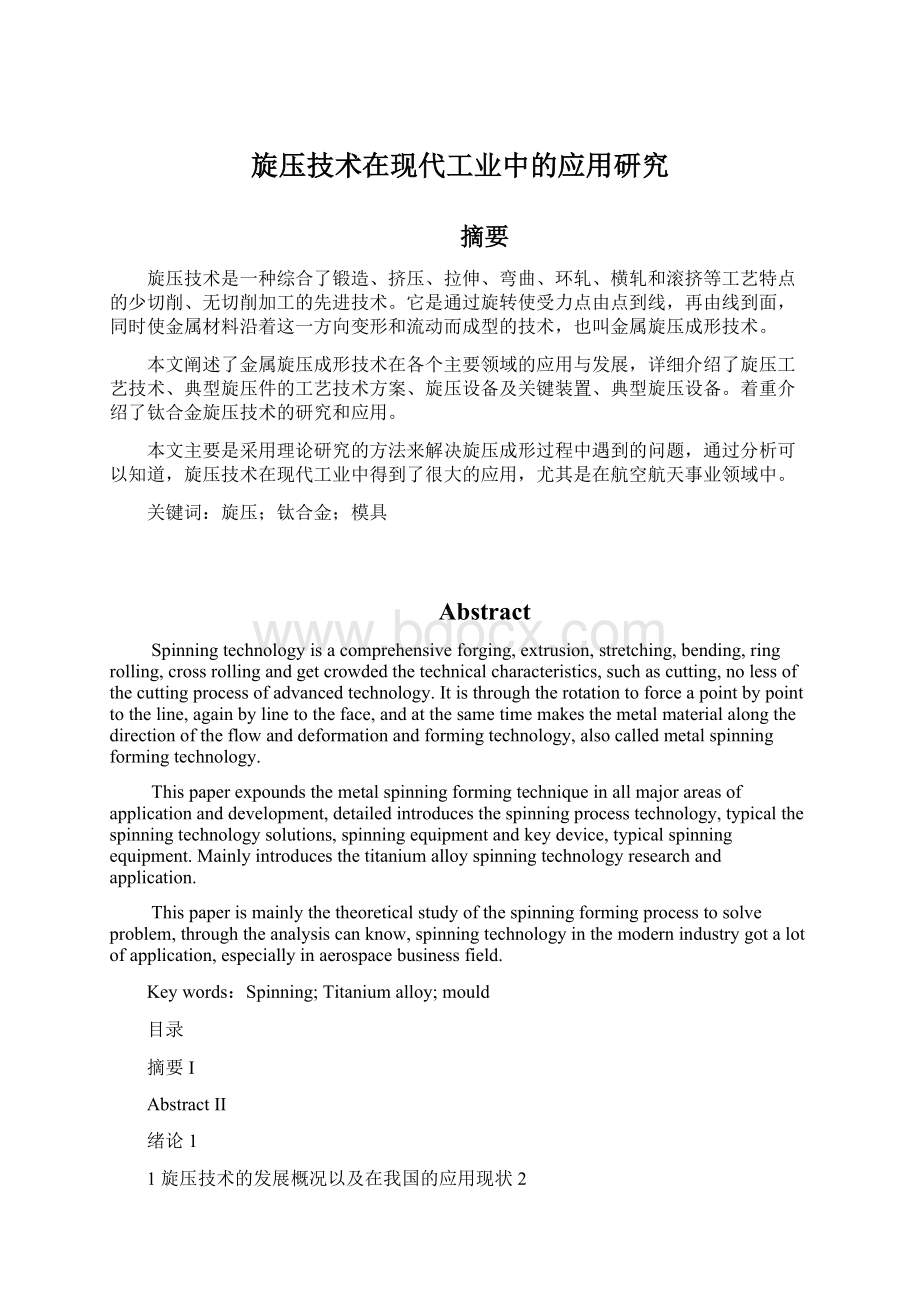
旋压技术在现代工业中的应用研究
摘要
旋压技术是一种综合了锻造、挤压、拉伸、弯曲、环轧、横轧和滚挤等工艺特点的少切削、无切削加工的先进技术。
它是通过旋转使受力点由点到线,再由线到面,同时使金属材料沿着这一方向变形和流动而成型的技术,也叫金属旋压成形技术。
本文阐述了金属旋压成形技术在各个主要领域的应用与发展,详细介绍了旋压工艺技术、典型旋压件的工艺技术方案、旋压设备及关键装置、典型旋压设备。
着重介绍了钛合金旋压技术的研究和应用。
本文主要是采用理论研究的方法来解决旋压成形过程中遇到的问题,通过分析可以知道,旋压技术在现代工业中得到了很大的应用,尤其是在航空航天事业领域中。
关键词:
旋压;钛合金;模具
Abstract
Spinningtechnologyisacomprehensiveforging,extrusion,stretching,bending,ringrolling,crossrollingandgetcrowdedthetechnicalcharacteristics,suchascutting,nolessofthecuttingprocessofadvancedtechnology.Itisthroughtherotationtoforceapointbypointtotheline,againbylinetotheface,andatthesametimemakesthemetalmaterialalongthedirectionoftheflowanddeformationandformingtechnology,alsocalledmetalspinningformingtechnology.
Thispaperexpoundsthemetalspinningformingtechniqueinallmajorareasofapplicationanddevelopment,detailedintroducesthespinningprocesstechnology,typicalthespinningtechnologysolutions,spinningequipmentandkeydevice,typicalspinningequipment.Mainlyintroducesthetitaniumalloyspinningtechnologyresearchandapplication.
Thispaperismainlythetheoreticalstudyofthespinningformingprocesstosolveproblem,throughtheanalysiscanknow,spinningtechnologyinthemodernindustrygotalotofapplication,especiallyinaerospacebusinessfield.
Keywords:
Spinning;Titaniumalloy;mould
目录
摘要I
AbstractII
绪论1
1旋压技术的发展概况以及在我国的应用现状2
1.1旋压技术简介2
1.1.1旋压技术2
1.1.2旋压技术特点4
1.2旋压技术发展概况4
1.3旋压设备5
1.3.1旋压设备的类型5
1.3.2旋压设备组成6
1.4旋压技术的应用7
2旋压技术原理8
2.1普通旋压技术的基本原理8
2.2强力旋压技术的基本原理10
2.3典型旋压产品的技术工艺12
2.3.1圆筒形件强力旋压12
2.3.2锥筒形件剪切旋压13
2.3.3封头普旋成形13
2.3.4车轮辋旋压14
3钛旋压技术研究16
3.1钛合金及其成形特点16
3.1.1钛合金简介16
3.1.2钛合金分类16
3.1.3钛合金成形特点16
3.2钛合金旋压技术的发展17
3.3钛合金旋压的关键技术20
3.4钛旋压技术存在的问题及解决措施21
4旋压模具的简单设计23
4.1旋压模具的组成23
4.1.1旋轮结构设计23
4.1.2芯模结构设计23
4.2热处理24
4.2.1热处理概述24
4.2.2一些常见的热处理概念25
结论26
致谢27
参考文献28
绪论
旋压作为一种典型的连续局部塑性成形技术,以其静压成形(无冲击、振动和环境危害)、产品精度高、工艺柔性好、易于实现机械化与自动化、节约材料等诸多优点而成为精密塑性成形技术的重要发展方向,是实现薄壁回转体零件的少切削或无切削加工的先进制造技术,广泛应用于机械、电子、化工、汽车以及航空航天等国防工业领域。
旋压技术的发展也促进了国内旋压设备及其相关技术的发展,特别是近年来航空航天等国防领域的旺盛需求,加之国内制造业整体水平的提高,使我国的选用设备研制达到了一个新的高度,进入了稳步发展阶段。
但仍不能适应国民经济的发展需要,因此需进一步研究和推广。
本研究课题的主要内容是通过对旋压技术的深入了解,进一步分析旋压技术在我国现代工业领域中的应用现状。
从以下四个方面进行研究:
1旋压技术发展概况以及在我国的应用现状;2旋压技术原理介绍;3钛旋压技术研究;4旋压模具的简单设计。
采取理论研究的方法对旋压技术在现代工业中的应用进行深入的研究,通过看专业书籍和上网查询相关的最新知识,信息来对钛旋压技术进行全面的研究,通过对旋压技术的学习和研究来设计简单的实用的旋压模具。
1旋压技术的发展概况以及在我国的应用现状
旋压技术是一项具有悠久历史的传统技术,据文献记载最早起源于我国唐代,由制陶工艺发展出了金属的旋压工艺。
到20世纪中叶以后,随着工业的发展和宇航事业的开拓,普旋工艺大规模应用于金属板料成形领域,从而促进了该工艺的研究与发展。
在二十世纪中叶以后,普通旋压有了以下三个方面的重大进展:
一是:
普通旋压设备逐渐机械化与自动化,即采用液压助力器等驱动旋轮往复移动,以实现进给和回程,因而减轻了劳动强度。
二是:
在20世纪60—70年代出现了能单向多道次进给的、电器液压程序控制的半自动旋压机。
三是:
由于电子技术的发展,于20世纪60年代后期,国外在半自动旋压机的基础上,发展了数控和录返式旋压机。
这些设备的快速发展将旋压工艺带进了中、大批量化的生产中。
强力旋压是上世纪五十年代在普通旋压的基础上发展起来的,最早是在瑞典、德国被用于民间工业(例如,加工锅皿等容器)。
由于旋压工艺的先进性、经济性和实用性,且该工艺具有变形力小,节约原材料等特点,在近四十年中,旋压技术得到了长足的发展,不仅在航空航天领域,而且在化工、机械、轻工等民用工业中都得到了广泛应用。
目前,旋压技术已日趋成熟,已经成为金属压力加工中的一个新领域。
近20年来,旋压成形技术突飞猛进,高精度数控和录返旋压机不断出现并迅速推广应用,目前正向着系列化和标准化方向发展。
在许多国家,如美国、俄罗斯、德国、日本和加拿大等国己生产出先进的标准化程度很高的旋压设备,这些旋压设备己基本定型,旋压工艺稳定,产品多种多样,应用范围日益广泛。
我国旋压技术的发展状况与国外先进水平相比有较大差距。
但近年来取得了较大发展,许多产品精度和性能都接近或达到了国外较先进水平,国内许多研究所(如北航现代技术研究所、黑龙江省旋压技术研究所、长春55所等)已经研制出了性能较好的旋压机。
1.1旋压技术简介
1.1.1旋压技术
旋压技术是一种综合了锻造、挤压、拉伸、弯曲、环轧、横轧和滚挤等工艺特点的少、无切削加工的先进技术,将金属筒坯、平板毛坯或预制坯用尾顶顶紧在旋压机芯模上,由主轴带动芯棒和坯料旋转,同时旋压轮从毛坯侧面将材料挤压使材料产生逐渐连续的塑性变形,从而获得各种母线形状的空心旋转体零件。
旋压技术的加工原理如图1-1。
图1-1旋压示意图
1芯模2毛坯3尾顶4旋轮
根据旋压加工过程中毛坯厚度的变化情况,一般将旋压工艺分为普通旋压和强力旋压两种。
普通旋压简称普旋。
普旋过程中毛坯的厚度基本保持不变,成型主要依靠坯料沿圆周的收缩及沿半径方向上的伸长变形来实现,其重要特征是在成型过程中可以明显看到坯料外径的变化。
普通旋压的基本方式有:
拉深旋压(拉旋)、缩径旋压(缩旋)和扩径旋压(扩旋)等三种。
强力旋压是在普通旋压基础上发展起来的一种近无余量加工方法,其实质为利用旋压辊子加高压于坯料,旋转坯料借助外力沿成形模具进行局部逐渐辗压产生塑性变形而变薄,从而得到高精度薄壁回转体零件。
根据旋压轮是否在同一截面上还可将强力旋压分为错距旋压和同步旋压。
普通旋压主要是改变毛坯的形状,而壁厚改变很小或不改变,其毛坯形状及尺寸的设计计算是关键技术。
其工艺要素为旋压轮运动轨迹、旋轮直径、旋压间隙、进给率、主轴转速、旋压线速度、旋轮圆角半径、旋轮前侧面与模具母线夹角等。
强力旋压主要是改变工件的壁厚和直径尺寸,工件长度会相应作改变,其工艺要素为旋轮直径、旋轮圆角半径、旋轮前角、旋轮后角、旋压攻角、主轴转速、进给率、旋压间隙、旋压道次、减薄率、工件半锥角、旋压线速度等。
金属材料的热处理也是旋压工艺中主要的因素,在旋压过程中由于受到强大的压、拉应力,致使材料硬化严重,必须采取热处理手段加以软化,为了改变最终工件的机械性能也需要进行必要的热处理。
此外,材料要具有较高的延伸率、断面收缩率,抗拉及屈服强度也要适当。
1.1.2旋压技术特点
(1)旋压属于局部连续性的加工,瞬间的变形区小,总的变形力小。
(2)一些形状复杂的零部件或高难度难变形的材料,传统工艺很难甚至无法加工,用旋压的办法就可以加工出来,如皮带轮,灯具配件等。
(3)旋压加工的公差很小可以达IT8左右,表面粗糙度小于3.2,强度和硬度均有显著提高。
(4)旋压加工材料利用率高,模具费用要低于冲压模具的二分之一以上。
旋压成型的经济性与生产批量、工件结构、设备和劳动费用等有关系。
多数加工用旋压加工与冲压加工,剪板加工,超声波清洗,电镀加工等工艺配套应用,以获得最好的经济效益。
(5)可旋压加工的形状只能是旋转体,主要有桶状、圆椎型、曲母线状和组合型。
(6)可加工的材料有:
铁板、铝板、不锈钢、铜板等。
1.2旋压技术发展概况
我国金属旋压成型技术的发展历史近四十年,在国防工业的应用研究尤为广泛,研究应用水平很高,特别是在旋压成型工艺及装备方面,已经处于国内领先地位。
旋压机的设计和制造能力也很强。
带轮旋压成形式工艺与设备是一项先进的技术,带轮旋压工艺上取得了折叠式带轮、劈开式带轮、滚压式多V型带轮和组合式带轮一系列科研成果,在理论与实践两个方面解决了旋压成形中的各种技术难题,并成功地用于生产。
随着我国旋压技术的发展,旋压技术产业化的进程不断加深,为我国国民经济的发展做出了显著贡献。
从80年代中期至今,国内车用皮带轮的旋压成形已经形成大规模生产,工艺已经相当成熟,基本上已经取代了传统的铸造——车削工艺。
从折叠式、劈开式到多锲式乃至其中两种的组合式,年产量达数百万套,在多种品牌车上都能看到国产的旋压皮带轮。
大型封头的冷旋压技术也得到了广泛的推广,形成了规模生产的态势。
生产效率高,生产成本低。
旋压技术产业化的不断拓展,促进了旋压技术的发展,给专用旋压设备的研制提供了契机。
旋压产品的大规模生产对旋压机床的精度、功能性、可靠性及自动化程度提出了更高的要求;与此同时,专用旋压设备的研制又推动了旋压产业化的进程,促进了我国旋压技术整体水平的提高。
但是,我国的旋压技术与国外先进水平相比,无论是在产品种类、尺寸精度、设备能力和自动化程度等方面,还是在工艺理论研究方面还都有一定的差距。
诸多科技工作者正在致力于该项研究工作,近20年来取得了较大发展,许多产品精度和性能都接近或达到了国外先进水平。
国内少数高等院校,如哈尔滨工业大学、北航、西工大等,以及一些有实力的研究所已在研制CNC旋压机、并进行理论探讨和开发新工艺。
尤其在近几年中,我国一些工厂从国外引进了先进的数控旋压机,使我国的旋压技术日趋成熟。
国内许多研究所(如北航现代技术研究所、黑龙江旋压技术研究所、长春55所等)已经研制出了较稳定可靠的多种类型的旋压机,在国内市场已有一定份额,但部分机种仍依赖于进口。
1.3旋压设备
1.3.1旋压设备的类型
旋压机按其运动方式、主轴方位、旋轮个数等可分为多种类型,按其功用大致可分为强力旋压机、普旋机和专用旋压机。
强力旋压机主要以流动旋压和剪切旋压成形为主,设备要求有较高的动静态刚度,所受旋压力及主轴扭矩较大。
普旋机主要成形有色金属复杂曲母线形面工件,设备旋轮头所受旋压力较小。
专用旋压机主要承担一种或较少种类似结构的工件加工任务,象气瓶收口机、轮毂旋压机、带轮旋压机等。
1.3.2旋压设备组成
旋压设备的组成主要包括:
控制系统、驱动系统、导向系统、旋轮座和旋轮头、旋压工装。
控制系统,近年来,国内研制的数控旋压机床大都实现了NC或CNC控制。
一般来说,用于金属切削机床的数控系统都可以作为旋压机床的数控系统。
这些系统主要有德国SIEMENS、法国NUM、日本FANUC以及国内的中国珠峰公司、北京航天机床数控系统公司等的数控系统。
驱动系统旋压机床的驱动系统包括主轴驱动和进给驱动两个部分。
主轴驱动可采用交流变频电机和直流变频电机驱动;进给驱动主要采用伺服电机+滚珠丝杠和伺服液压缸驱动两种方式。
导向系统,导向系统主要有滑动导轨、静压导轨和滚动导轨三种形式。
图1-2轮毂旋压机
图1-3气瓶热收口旋压机图1-4封头旋压机
1.4旋压技术的应用
近20年来,旋压成形技术突飞猛进,高精度数控和录返旋压机不断出现并迅速推广应用,目前正向着系列化和标准化方向发展。
在许多国家,如美国、俄罗斯、德国、日本和加拿大等国己生产出先进的标准化程度很高的旋压设备,这些旋压设备己基本定型,旋压工艺稳定,产品多种多样,应用范围日益广泛。
我国旋压技术的发展状况与国外先进水平相比有较大差距。
但近年来取得了较大发展,许多产品精度和性能都接近或达到了国外较先进水平。
国内许多研究所(如北航现代技术研究所、黑龙江省旋压技术研究所、长春55所等)已经研制出了性能较好的旋压机。
旋压产品形状各式各样(如图1-5示),通过旋压可完成成形、缩径、收口、封底、翻边、卷边、压筋等各种工作,其产品广泛应用于各行各业(图1-6)。
图1-5旋压成型的工件形状
图1-6各种旋压制件
2旋压技术原理
旋压技术的基本原理类似于我国古代陶瓷炼制过程。
旋压成形的零件一般为回转体筒形,旋压零件的毛坯通常是厚壁筒形件或圆形板料。
在旋压机床上,与主轴同轴联接的是一芯模(轴),旋压毛坯套在芯模(轴)上;旋轮通过与套在芯模(轴)上的毛坯接触产生的摩擦力反向被动旋转;与此同时,旋轮架在轴向大推力油缸的作用下,作轴向运动。
旋轮架在轴向、旋轮在径向力的共同作用下,对坯料表面实施逐点连续塑性变形。
在车床尾顶支架的位置上,设计成与主轴同一轴线的尾顶液压缸,液压缸对套在芯模(轴)上的坯料端面施加轴向推力。
2.1普通旋压技术的基本原理
普通旋压技术就是在旋压过程中,板厚基本保持不变,旋压成形主要依靠坯料圆周方向与半径方向上的变形来实现。
普通旋压种类繁多,应用范围极其广阔,采用形式多样的旋轮运动轨迹,可加工形状复杂零件。
普通旋压技术的基本原理如图2-1。
图2-1普通旋压原理图
但是,由于普通旋压技术的局部加载和连续回转成形的特点,增加了问题的复杂性,我们现在对其工艺成形的理论研究相对薄弱。
由于旋轮轨迹、旋轮圆角半径和进给比等各项工艺参数的选择严重影响工件的成形质量,因此一直是普旋中的主要研究内容。
旋轮运动轨迹的合理确定是影响加工成败的关键因素。
对于多道次普通旋压,每道次可根据不同的工况,使用不同的运动轨迹获得较佳的旋压效果,各道次运动轨迹的包络线构成了零件的母线。
旋压的运动轨迹通常有直线型、曲线型、直线-曲线型、往复圆弧型四种。
2.1.1旋压力
旋压力,就是指在旋压成形过程中承受的应力,我们计算旋压力的原理是采用叶山假设,计算值受μa影响较大。
在工程上采用如下计算公式:
(式2-1)
其中,P为普旋的单位塑流压力,
为所旋压材料的抗拉强度。
普通旋压技术的成形极限是:
旋压成形时,金属板料上缩颈或破裂区表面应变量成为表面成形极限。
对于圆筒件拉旋,一般用第一道拉深的成形极限表示方法,以极限拉深比K或极限拉深系数m来表示:
K=D
/d(式2-2)
m=1/K=d/D
(式2-3)
式中,D0——毛坯直径,d——成形芯模直径。
最近几年以来,有限元数值模拟方法在普通旋压技术领驭中的应用变的非常广泛。
我们假设旋压局部变形为小变形物理非线性问题,将旋轮对坯料的作用简化为集中应力,忽略相对厚度t/D
的限制,采用目前比较成熟的壳体分析单元之--曲面壳元,分析计算了封头旋压中间道次变形过程,初步探讨了封头件旋压成形原理。
利用动态显式有限元程序LS-DYNA3D,采用薄壳单元,对变形区及附近的区域局部细分网络,大大提高了计算效率;同时假设毛坯静止,旋轮质心沿螺旋线进给,对薄壁筒收口旋压变形进行数值模拟,分析了毛坯的纬向应变、经向应变及壁厚的分布和变化过程,从而建立起了对收口旋压变形过程的整体认识。
应用商用ANSYS软件,考虑材料加工硬化和摩擦边界条件,对缩口旋压变形过程进行三维数值模拟,得到了与试验比较接近的结果。
目前,对普通旋压变形过程的有限元数值模拟大都还只是初步试探性的研究。
随着普通旋压加工优越性的日益突出,以及各种价格昂贵的新型难变形结构材应用的日益广泛,通过高精度的数值计算,模拟多道次普旋的精确成形规律,已经成为该领域中迫切需要解决的重要基础性的研究课题。
2.2强力旋压技术的基本原理
强力旋压相对于普通旋压发展比较迅速,尤其是进入21世纪以来更得到了飞速的发展。
芯模、毛坯和尾顶块一起随机床主轴旋转,强力旋压时,每点的变形对其他未变形的部分影响很小,变形后基本保持原样。
强力旋压技术的基本原理如图2-2
图2-2强力旋压原理图
1芯模2毛坯3尾顶块4零件5旋输
按变形方式,强力旋压可分为正旋和反旋两种方式。
正旋时,材料流动方向与旋转前进方向相同,反旋则方向相反。
筒形件强力旋压成形在生产薄壁超长高精度筒形件时具有突出的优点,故得到广泛的应用。
建立了筒形件强力旋压的平面应变力学模型,通过刚塑性有限元方法,分别模拟了正旋和反旋变形过程,发现旋压变形是不均匀的,在靠近旋轮处变形较大,靠近芯模处变形较小。
而且,发现旋压同样长度的工件,正旋所需的时间是反旋的两倍,这与实际生产结果基本吻合。
也正是由于反旋相对正旋具有较高的生产率,以及模具简单,工件长度不受芯模长度和旋轮纵向行程的限制等优点,反旋的应用范围较广,对其研究也比较深入。
强力旋压采用三维刚塑性有限元的方法分析,分析考虑了旋轮的几何轨迹,旋轮与毛坯的接触界面的形状,以及毛坯随芯棒的旋转运动,对筒形件反旋加工进行了分析。
分析结果表明,旋轮作用区周向两侧存在两个产生切向收缩变形的区域,当两侧区域的收缩变形大于旋轮作用区的切向伸长量时,就产生了缩径。
在此基础上,运用三维弹塑性有限元,以三旋轮筒形件强力旋压为对象,取毛坯的1/3建立力学模型,考虑旋轮与毛坯及毛坯与芯模的接触问题,通过给定旋轮初始位移进行加载,对反旋成形过程进行数值模拟,得到了变形区应力与应变场的基本分布规律。
从上述的实验结果中发现,筒形件强力旋压时,与旋轮接触区的坯料金属径向被压缩而沿轴向和切向流动,引起整个坯料的轴向微量不均匀伸长。
正是由于强力旋压过程中不均匀的塑性变形,在旋压件内会产生残余应力,残余应力的大小及其分布规律对旋压件的使用性能产生严重影响。
应用商用的ABAUQS软件,运用三维动态显式有限元法,计算分析了三旋轮强旋残余应力的问题。
运用弹塑性有限元法也模拟了旋压件内的残余应力的分布。
这些研究结果表明:
减薄率、进给比、旋轮工作角、毛坯壁厚、材料性能等因素都影响残余应力的分布,其中随减薄率的增大,残余应力绝对值亦增加;在整个壁厚方向上,轴向残余应力的绝对值比切向残余应力的绝对值大,也就是说,筒形件旋压时,切向变形量较小。
由于强力旋压主要通过壁厚减薄实现,所需要的旋压力相对普旋比较大,而旋压力的大小是确定旋压工艺参数、设计旋压工具和选用旋压设备的重要依据,因此在强旋研究中,求解旋压力仍然是一个需要深入研究的课题。
除了理论分析与试验相结合的方法外,人们还尝试用三维刚塑性有限元法对强旋力进行分析。
根据强旋时的实际接触情况,采用数值计算方法分别计算了筒形件正旋和反旋时的旋压力,系统分析了旋轮工作角、旋轮圆角半径、减薄率、进给比、旋轮直径及毛坯原始壁厚等各工艺参数对旋压力的影响,其中旋轮圆角半径的影响比较小。
2.3典型旋压产品的技术工艺
2.3.1圆筒形件强力旋压
圆筒形件强力旋压,其材料变形过程始终遵循体积不变原则,工件形状的改变为旋压前后圆筒壁厚的减薄、直径的变小、长度的增加,同时产品内径也会因工艺参数的不同而有不同程度的改变,最终产品要素为圆筒外(内)径、壁厚、长度、直线度、圆度等,产品长度可用式2-4计算。
(式2-4)
其中:
L
--工件长度
L
--毛坯长度
S
--毛坯厚度
S
--工件厚度
d
--内径
在圆筒形件强力旋压中有一种特殊的旋压方式就是分层错距旋压,是指多个旋轮在周向相互错开而在径向又依次使毛坯厚度减薄的旋压过程。
这种旋压方式可以在一道次旋压过程中完成多道次旋压,提高了生产效率,同时由于对材料变形区增加了约束致使工件直径精度得到了提高。
工艺方案及参数的制定主要考虑毛坯材料的延伸率、断面收缩率、抗拉强度、屈服强度等因素。
旋压单道次材料减薄率不能大于极限减薄率
可通过在多道次旋压中间增加热处理软化工序成形最终产品,主要的工艺参数为道次减薄率、旋压间隙、旋轮进给比、旋轮成形角、旋轮圆角半径以及错距量等,旋轮成形角、旋压间隙要合理匹配,负责旋轮前沿材料极易产生局部隆起、堆积以至失稳开裂。
2.3.2锥筒形件剪切旋压
锥筒形工件形状的改变主要是壁厚的减薄、锥度减小和高度的增加,最终产品要素为锥筒段高度、半锥角、壁厚、已知位置的直径、锥筒段母线直线度、圆度等。
工艺方案及参数的制定也因考虑所旋材料的延伸率、断面收缩率等因素。
根据变形程度的大小,可适当增加剪切旋压道次,在道次中间增加热处理工序以软化材料,增加可旋性。
在铝合金材料的剪切旋压中由于变形程度较大,可通过热旋压的方式成形工件,具体是将毛坯均匀预热到再结晶温度以上,同时将旋压模具加热到200~300℃,在旋压过程中可用乙炔焰直接加热毛坯,以保证温度不会过快降低,使材料处于软化状态,有利于旋压成形。
其主要工艺参数除无错距量外,其余同圆筒强力旋压,为了增大材料变形区面积,防止材料所受拉应力过大,旋轮前沿处材料局部隆起过高,旋轮大多使用大圆角的普旋旋轮。
毛坯的设计主要依据剪切旋压正弦理论,工件壁厚与锥度成特定关系。
因形状变化较大,旋压时应防止局