各种无损检测相关知识1.docx
《各种无损检测相关知识1.docx》由会员分享,可在线阅读,更多相关《各种无损检测相关知识1.docx(27页珍藏版)》请在冰豆网上搜索。
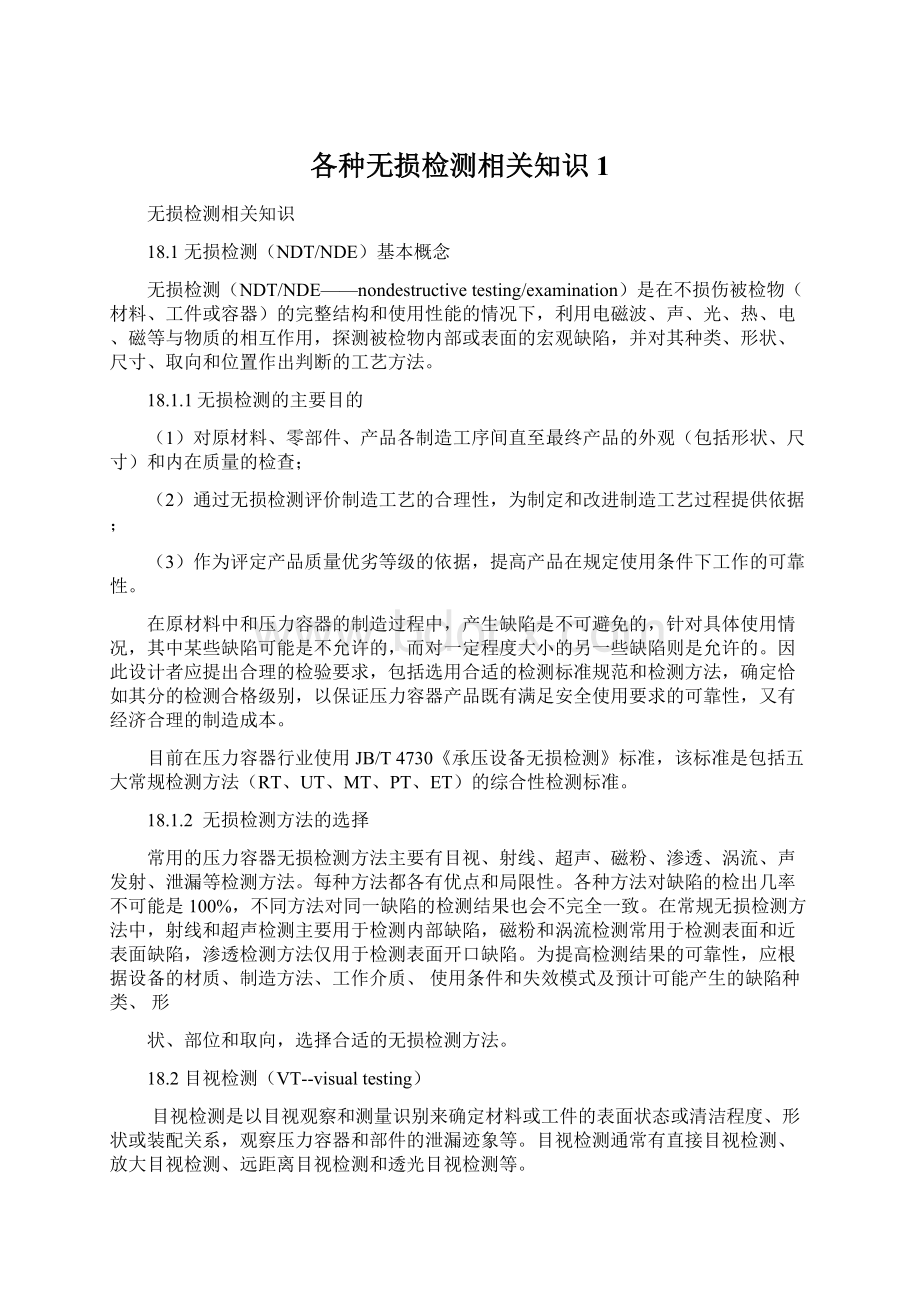
各种无损检测相关知识1
无损检测相关知识
18.1无损检测(NDT/NDE)基本概念
无损检测(NDT/NDE——nondestructivetesting/examination)是在不损伤被检物(材料、工件或容器)的完整结构和使用性能的情况下,利用电磁波、声、光、热、电、磁等与物质的相互作用,探测被检物内部或表面的宏观缺陷,并对其种类、形状、尺寸、取向和位置作出判断的工艺方法。
18.1.1无损检测的主要目的
(1)对原材料、零部件、产品各制造工序间直至最终产品的外观(包括形状、尺寸)和内在质量的检查;
(2)通过无损检测评价制造工艺的合理性,为制定和改进制造工艺过程提供依据;
(3)作为评定产品质量优劣等级的依据,提高产品在规定使用条件下工作的可靠性。
在原材料中和压力容器的制造过程中,产生缺陷是不可避免的,针对具体使用情况,其中某些缺陷可能是不允许的,而对一定程度大小的另一些缺陷则是允许的。
因此设计者应提出合理的检验要求,包括选用合适的检测标准规范和检测方法,确定恰如其分的检测合格级别,以保证压力容器产品既有满足安全使用要求的可靠性,又有经济合理的制造成本。
目前在压力容器行业使用JB/T4730《承压设备无损检测》标准,该标准是包括五大常规检测方法(RT、UT、MT、PT、ET)的综合性检测标准。
18.1.2无损检测方法的选择
常用的压力容器无损检测方法主要有目视、射线、超声、磁粉、渗透、涡流、声发射、泄漏等检测方法。
每种方法都各有优点和局限性。
各种方法对缺陷的检出几率不可能是100%,不同方法对同一缺陷的检测结果也会不完全一致。
在常规无损检测方法中,射线和超声检测主要用于检测内部缺陷,磁粉和涡流检测常用于检测表面和近表面缺陷,渗透检测方法仅用于检测表面开口缺陷。
为提高检测结果的可靠性,应根据设备的材质、制造方法、工作介质、使用条件和失效模式及预计可能产生的缺陷种类、形
状、部位和取向,选择合适的无损检测方法。
18.2目视检测(VT--visualtesting)
目视检测是以目视观察和测量识别来确定材料或工件的表面状态或清洁程度、形状或装配关系,观察压力容器和部件的泄漏迹象等。
目视检测通常有直接目视检测、放大目视检测、远距离目视检测和透光目视检测等。
目视检测的具体方法和要求,在国内还没有统一的标准。
通常根据图样和技术文件的要求,由制造、安装单位自行编制操作规程对压力容器产品的原材料、装配、中间产品和最终产品进行目视检测。
18.2.1按检测范围划分
a.结构检查
(1)简体与封头的连接,封头型式;
(2)人孔、接管和上下引出管;
(3)底座与压力容器本体的连接;
(4)安全附件等等。
b.母材及焊接接头的内、外表面检查
(1)表面腐蚀,机械损伤;
(2)焊接坡口;
(3)本体A、B类焊缝,接管对接环焊缝,角焊缝等处咬边、裂纹、过热、变形、泄漏等;
(4)焊缝对口错边量、棱角度、焊缝预告,角焊缝焊脚高度;
(5)检查有无开裂、脱落、局部鼓包、凹坑、孔洞等缺陷。
18.2.2按制造工艺过程划分
(1)钢板、锻件、管材等外观质量和厚度的检测;
(2)冷、热加工成型表面外观质量和厚度的检测;
(3)破口表面质量和压力容器部件几何尺寸的检测;
(4)压力容器装配间隙和结构尺寸的检测;
(5)焊接接头表面质量和几何尺寸检测;
(6)接管、支座的标高、方位的检测;
(7)压力容器耐压试验和安全附件检测。
对于目视检测的具体参数要求可按GB150、《压力容器安全技术监察规程》、GB50094《球形储罐施工及验收规范》、GB12337《钢制球形储罐》等法规和标准的具体规定。
18.3射线检测(RT--radiographictesting)
18.3.1射线检测原理和特点
射线检测是利用强度均匀的X和γ射线(都是波长很短的电磁波)照射工件,使照相胶片感光,由于工件内缺陷与无缺陷部位的密度和厚度差异,射线在这些部位的衰减程度不同,就可得到和工作内部有无缺陷相对应的不同黑度的图像(射线底片)。
从而检查出缺陷的种类、大小和分布状况等,并确定工件的质量等级。
射线检测的主要特点:
(1)根据射线底片的缺陷图像,可以精确地判别缺陷在垂直于射线透照方向的二维平面的位置、尺寸和缺陷的种类,但缺陷在壁厚方向(射线透照方向)的自身高度和深度则很难确定。
(2)对于体积状缺陷(体积状未焊透、气孔、夹渣、疏松、锁孔)检测灵敏度比较高。
对于面状缺陷(如微细的裂纹、未熔合和面状未焊透等)检测灵敏度相对较低,只有当射线透照方向和缺陷平面相平行,才有较高的检出灵敏度。
据有关资料介绍,对于面状缺陷,当入射射线与缺陷平面的夹角θ=9度时,检出率为70%;当夹角θ=14度时,检出率为50%。
从而认为,射线检测时体积状缺陷的检测灵敏度要高于面状缺陷的检测灵敏度。
(3)通过底片评价工作的质量就直观、定性定量准确、重复性好、易于保存归档。
(4)射线对人体有伤害作用,防护设备投资高。
射线检测时,胶片和有关药品消耗量大,成本高。
(5)射线检测可用于碳素钢、低合金钢、奥氏体不锈钢、镍及镍基合金、铜及铜合金、铝及铝合金、钛及钛合金和复合材料等的焊接接头和铸件,但一般不适用于锻件、管材、板材等。
(6)对于被检工件的厚度下限没有限制。
射线检测是采用穿透法,因此必须将射线源和射线胶片放置在被检工件的两侧。
18.3.2射线透照检测技术
不同用途,不同使用要求的压力容器对于焊接接头有不同的质量检测要求。
射线检测技术分为三级:
A级——低灵敏度技术;AB级——中灵敏度技术;B级——高灵敏度技术。
一般情况下,锅炉、压力容器及压力管道对接接头采用AB级进行检测,其支撑件和结构件的检测可采用A级。
对关键设备,如:
材料对裂纹(包括冷、热、再热、疲劳、应力腐蚀裂纹等)敏感,此时应采用B级检测技术。
1.各种射线源的最大穿透厚度
一般来说不同能量的X和γ射线可以穿透不同厚度的材料,其吸收率和厚度值呈指数函数关系。
表18.3列出不同能量的X和γ射线对钢和铝的实际穿透界限。
这些数值与许多因素有关,并且是一些近似值。
表18.3.2各种射线源的检测厚度范围
射线源
AB级,透照厚度,mm
X射线,200KV
≤20
X射线,400KV
≤50
X射线,1MeV~4MeV
30~200
X射线,9MeV
50~400
X射线,25MeV
80~500
Se-75
10~40
Ir-192
20~100
Co-60
40~200
2.射线源的选择
射线能量越大,不清晰度越大;X射线要比γ射线的不清晰度数值小。
不清晰度的数值大小通常表征着射线透照检测细长缺陷的能力。
其数值大,检出该类缺陷的能力低。
因此射线源的选择应考虑以下因素:
(1)在曝光时间允许的条件下,尽量采用较低能量的射线源;
(2)对铝、钛、铜等有色金属材料推荐采用X射线源;
(3)为了保证较高的清晰度,应尽量采用较小尺寸的射线源和较大的焦距。
3.射线检测灵敏度和像质计
像质计是控制射线透照质量必不可少的工具,国内主要采用单丝式线型像质计,像质指数Z(等于底片上能识别出的最细钢丝的线编号)和底片可识别最细钢丝的线径d(mm)的关系表达为:
Z=6-10x1gd(18.3.2)
式中:
lgd------以10为底d的对数值。
压力容器射线检测时应根据规范要求选择合适的像质指数。
4.射线透照胶片
胶片对射线透照质量有明显的影响,胶片的分类至关重要。
国内参照ISO11699-1(1998)对胶片的分类进行了规定。
目前压力容器行业使用的射线胶片系统分为四类,即T1、T2、T3、T4类。
T1为最高类别,T4为最低类别。
A级和AB级技术应采用T3类或更高类别的胶片,B级技术应采用T2类或更高类别的胶片。
胶片的本底灰雾度应不大于0.3,采用γ射线对裂纹敏感性大的材料,应采用T2类或更高类别的胶片。
通常如需提高射线透照的底片质量,则应采用低噪声、高梯度和高梯度噪声比的胶片。
5.裂纹射线检测灵敏度
射线检测的裂纹检出率所涉及的裂纹的主要参数是:
(1)X射线透照方向和裂纹面的夹角θ;
(2)裂纹的长度t;
(3)裂纹的开口宽度w.
为了保证裂纹的检出效果,通常在射线照相检测标准中都作出了一些直接或间接的技术规定:
(1)直接对裂纹检验角θ进行规定,如美国的一些军标就要求θ≤10度;
(2)规定透照厚度比K值进行间接控制。
(3)直接规定有效透照区长度进行间接控制。
评价射线照相质量的主要指标是射线照相灵敏度,所研究的基本问题是建立缺陷影像的可识别性和影像质量因素的关系,以及影像质量因素和射线照相技术因素之间的关系。
射线照相灵敏度一般由三个因素控制:
即对比度、不清晰度和颗粒度。
对比度描述的是细节影像与背景影像的黑度差,对缺陷而言则是缺陷影像与背景影响的黑度差,它决定缺陷影像的可识别度。
不清晰度描述影像边界的扩展程度或者说是模糊程度,它也影响缺陷影像的可识别度。
尤其是对于小缺陷影响程度更大。
颗粒度是影像黑度分布不均匀的视觉影像,由形成影像的银团随即分布产生,它直接对应于信噪比。
为满足灵敏度要求,应根据JB/T4730的规定,选用适当的射线种类和能量、胶片型号、像质指数、增感屏类型、几何布置、曙光条件及暗室处理。
18.3.3射线透照方式
射线透照方式按射线源、工件和胶片相互关系,为纵缝透照法、环缝外透法、环缝内透法、双壁双影法和双壁单影法等五种,见图18.3.3.射线中心束应垂直指向透照区中心。
1.纵缝透照法
即可以是外透,也可以是内透,直径较小时,也可以将射线源和胶片分置于压力管道和压力容器筒体的两侧形成所谓的双壁单影法透照。
2.环缝外透法
是压力容器环焊缝检测普遍采用的检测方法,简单易行,但一般每次只拍一片,效率较低,底片端部影像质量较差。
3.环缝内透法
如果可能应尽量选用射线源在部件中心的布置,可对整条焊缝进行一次性周向曝光,其底片灵敏度均一,射线照相质量好。
4.双壁单影法
适用直径较小的压力容器筒体(ф≤600mm)或外径大于89mm的管子环焊缝,原则上采用垂直透照(近似垂直),当使用垫板时应进行斜透照,以避免前壁垫板的影响。
对焊缝进行分段透照,主要检测靠近胶片侧部位的焊缝。
5.双壁双影法
这种检测方法主要用于检测小口径(ф≤89mm)的环向对接焊缝,射线以一定角度透过管子的上下焊缝,在胶片上形成椭圆形影像,上焊缝距胶片远,影像质量差。
当透照位置有困难时,也可以采用双壁双影垂直透照法。
18.3.4压力容器焊接接头的射线检测质量等级
1.焊接缺陷
焊缝内部缺陷主要有:
气孔(porosity)、夹渣(slaginclusion)、未焊透(incompletejointpenetration)、未熔合(incompletefusion)、裂纹(crack)。
裂纹又分为热裂纹、冷裂纹、延迟裂纹、再热裂纹等。
2.焊缝的表面质量(包括焊缝余高)的要求
⑴焊缝的表面缺陷(如焊瘤、咬边、烧穿、凹坑、未焊满、沟槽等)将直接反映在底片上,往往掩盖了焊缝内的埋藏缺陷或与之相混淆,给缺陷的评定、分级和返修带来很大的困难。
为此在射线检测前应进行外观检查,必要时进行修磨和补焊处理。
⑵焊缝余高对焊缝缺陷的检出有一定的影响,余高越高,对底片的宽容度要求愈高,缺陷检出相对比较困难,因此,应将焊缝余高去除或控制在一定的尺寸范围内。
3.射线底片上缺陷长度和宽度的确定
射线底片上的影像尺寸是缺陷的投影尺寸,通常射线源到胶片的距离要比缺陷到胶片的距离大许多倍,因此除非透照检测很厚的工件之外,缺陷在胶片上投影产生的线性放大很少超过5%。
所以,评定缺陷长度时,可直接以底片上的投影长度作为测定依据,当缺陷长度方向与胶片方向有明显夹角时,评片可按经验对缺陷投影长度乘上一个修正系数来确定缺陷长度。
缺陷在底片上的影像宽度是由缺陷的投影宽度加上总的影响不清晰度构成。
除了考虑到宽度很窄的缺陷、或固有不清晰度较大的高能射线、或γ射线检测进行修正外,在一般情况下,底片上测出的影像投影宽度通常就作为缺陷的宽度。
3.质量等级评定
压力容器焊接接头质量等级评定应根据JB/T4730中的规定来进行。
该标准分别给出2mm~250mm厚的碳素钢、低合金钢、不锈钢、镍及镍基合金、壁厚大于或等于2mm的钢及钢合金、铝及铝合金、钛及钛合金材料制锅炉、压力容器及压力管道制造和安装时对接焊缝的射线透照检测和质量等级评定,全面仅介绍钢制压力容器焊接接头。
根据缺陷的性质和数量,将焊缝分为四个等级:
Ⅰ级焊缝内部允许存在裂纹,未熔合、未焊透和条状缺陷;
Ⅱ级焊缝内不允许有裂纹、未熔合和未焊透存在
Ⅲ级焊缝内部允许有裂纹、未熔合及双面焊或相当于双面焊的全焊透对接焊缝和垫板单面焊中的为焊透存在;
焊缝缺陷超过Ⅲ级者为Ⅳ级。
18.4超声检测(UT—ULTRASONICTESTING)
18.4.1超声检测原理和特点
1.超声检测原理
超声检测按作用原理可以有三类“脉冲反射法,穿透法和共振法。
前一种用的脉冲波,后两种用
的是连续波。
目前广泛只用的是脉冲反射法,其工作原理为:
超声波探头在高频电脉冲激发下,发射
出持续时间极端的脉冲反射波,通过探头与工件间的耦合剂在工件终传播,当遇到工件内的缺陷或是
1件的界面即反射,返回的超声波被探头接受,并转换成电信号在仪器荧光品上显示,根据传播时间
和回波的波幅高低,发现缺陷并对缺陷的位置、长度和波幅进行测定。
2.超声检测的特点
(1)由于目前超声检测只能提供波幅和传播时间两个基本参数,对缺陷的判断是根据:
缺陷反射回波的形状、静态波形、动态波形、回波包络线;
工件的材料特性、结构、制造工艺及热处理条件等。
焊缝的焊接方法、焊接工艺、工件形状、坡口形式、热处理状态来判断缺陷类型和性质。
缺陷的波幅高度、位置、取向。
判断的正确性主要取决于检测人员的技术水平和实践经验。
(2)缺陷检测灵敏度受缺陷反射面的影响很大。
对于体积状缺陷,如果缺陷不是相当大或是
比较密集的话,就不能提供好的反射面和获得足够的反射回波,对于面状缺陷,不管其厚度如何
薄。
只要超声波垂直射向它,就能够获得足够的反射回波,从理论上说,随着探头K值(探头K值
是指斜探头入射声束折射角的正切值,斜探头角度规格是按K值为简单数字而系列化的,图K=1,
1.5,2,2.5.。
。
。
。
。
)的变化,总可以使入射声束垂直面状缺陷的反射面。
因此超声检测对面状
缺陷(如板材的分层和裂纹)的检出率比较高,而对体积状缺陷(如气孔和夹渣等)的检出率比较低。
(3)除了某些先进的带记录或成像的超声检测技术外,一般多数情况是没有明确的记录、缺乏
直观性。
(4)超声检测通常适用于金属板材、管材、棒材、钢锻件、焊缝等的检测;不适用或很难适用粗晶
材料(如奥氏体钢铸件和焊缝)、形状复杂或表面粗糙的工件。
(5)采用纵波直射法探测工件(如锻件等)内部缺陷,其最大有效探测深度可达1m左右,对于有
些钢种可以高达3m;采用横波斜射法探查工件(如焊缝等)其最大有效探测深度可达0.5m以上。
(6)超声检测采用反射法,一般主要将案头放置在被检工件的单面即可。
(7)超声检测可以较好地确定缺陷在被检工件在厚底方向的位置和缺陷的自身高度。
18.4.2超声检测灵敏度
1.术语
(1)超声波(ultrosonicwave):
人耳能听到的物体振动频率是20Hz~2000Hz,超过这个范围的声
波为超声波。
超声检测使用的频率范围是0.5Hz~10MHz,使用的波型有纵波、横波、表面波和板波。
(2)纵波(longitudinalwave):
声波在介质中传播时,介质质点的振动方向与波的传播方向一致的波。
只可在各种介质中传播,当在固体介质中传播时,速度为横波的2倍。
(3)横波(transversewave):
声波在介质中传播时,介质质点的振动方向与波的传播方向垂直的波。
只能在固体和切变模数高的粘滞液体中转播。
又称为剪切波。
(4)表面波(surfacewave):
沿介质两个相邻表面传播的波。
介质表面质点在其平衡位置附近作椭圆轨迹的振动。
继而作用于相邻的质点而在介质表面传播。
其幅值随传播深度增加而迅速减小,其传播速度约为横波的0.9倍。
又称瑞利波(Rayleighwave).
(5)板波(platewave):
在无限大板状介质的整个厚度范围内传播的超声波。
其传播速度与材质、板厚和频率有关,又称兰姆波(lambwave)
2.超声波探伤仪
压力容器超声波检测多采用A型脉冲反射式超声波探伤仪。
所谓A型是指A型显示,即以荧光屏的水平基线表示声波传播时间或距离,以垂直基线表示反射回波幅度的信息显示方法,此外还有B型显示,能显示缺陷垂直于探测面的界面图像。
C型面试,能显示缺陷平行于探测面的平面图像。
A型脉冲反射式超声波探伤仪可以使模拟式的,通常只能显示波形;也有数字式的,随着信息数字化处理技术和计算机系统的广泛应用,开发的新型数字式超声波探伤仪可以显示图文、波形信息,可以就分别接受、处理、储存进行多个内置通道的设置,可以与外界设备如计算机、打印机、数码录音、录像机连接。
从而实现检测时机、状态的可记录性,进一步法杖还可以实行超声波检测自动化。
3.超声波探头
超声波探头是一种电声换能器,主要由压电晶片组成,其主要作用是在高频电脉冲激发下发射超声波信号,再将接收到的超声波信号转换成电信号,从而以波幅和数字形式显示出来。
(1)超声波探头按形式,晶片尺寸、功能、使用条件等可以分为直探头,斜探头、水浸探头、可变角探头,聚焦探头等。
压力容器行业的超声检测中最常用的有单晶、双晶直探头(纵波)和单晶斜探头(横波)。
纵波单晶片直探头:
主要用于锻件、钢板的超声检测。
纵波双晶片直探头:
实际上由两个单晶直探头组合在一起,其中一个镜片发射,另一个接收,这种探头减小盲区,提高了分辨率。
主要用于薄工件的检测。
横波单晶斜探头:
利用探头中有机玻璃制斜锲使超声波产生折射,倾斜入射工件进行检测。
主要勇于焊缝检测以及锻件、钢板的横波检测。
锻件、钢板的横波检测主要用于合同有要求或是重要且可能出现问题的厚壁材料。
(2)晶片有效面积一般不应大于500平方米,单斜探头声束轴线水平偏离角不应大于2度,主声束垂直方向不应有明显的双峰
超声探伤仪和探头的系统性能:
在达到所探工件的最大检测声程时,其有效灵敏度余量应大于或等于10dB,直探头远场分辨力应大于或等于30dB,斜探头的远场分辨力应大于或等于6dB仪器和探头的系统性能应按JB/T9214《A型脉冲反射式超声波探伤系统工作性能测试方法》和JB/T10062《超声探伤用探头性能测试方法》的规定进行测试。
4,超声检测试块
(1)超声检测主要采用标准试块和对比试块来调整检测范围、检测灵敏度并进行超声仪器和探头的系统性能试验。
常见的有钢板检测用的阶梯试块、Φ5MM平底孔试块、尖角槽试块,锻件检测用的圆柱形平底试块、平底孔试块、尖角槽试块、钢管检测用的尖角槽试块,焊缝检测用的长横孔试块、短横孔试块、平底孔试块、堆焊层检测用的长横孔试块、平底孔试块等等。
(2)超声校准用人工反射体:
通过超声校准用人工反射体有长横孔、短横孔、横通孔、平底孔、V型槽和其他线切割槽等、横通孔和长横孔具有轴对称特点,反射波幅比较稳定,有线性缺陷特征,适用于各种K值探头一般代表工件内部有一定长度的裂纹、未焊透、未熔合和条状夹渣。
通常使用在寒风、堆焊层的超声检测中,也有用在螺栓件和铸件检测的。
短横孔在近场区表现为线状反射体特征,在远场区表现为点状反射体特征。
主要用于焊缝检测,适用于各种K值探头.平底空一般具有点状面积型反射体的特点,主要用于锻件、钢板、焊缝、复合板、堆焊层的超声检测。
通常适用于直探头和双晶探头的校准和检测。
V型槽和其他切割槽具有表面开口的线性缺陷的特点,适用于钢板,钢管,锻件等工件的横波检测,也可,模拟其他工件或焊缝表面或近表面缺陷以调整检测灵敏度,检测或校准时,通常采用K1斜探头,根据需要,也可采用其他K值探头。
5.超声检测灵敏度的确定
超声检测灵敏度反映超声波探伤仪和探头两者组合后所具有的检测最小缺陷的能力。
检出的缺陷越小,或可检出同样大小缺陷的可探测距离越大,则表示检测灵敏度愈高。
实际工件检测灵敏度高,则应根据具体情况来调整,通常有两种方法,一种是将标准试块上人工缺陷的回波高度调整到适当的高度,以此作为基准灵敏度。
扫查灵敏度一般不得低于基准灵敏度。
18.4.3各类型工件的超声检测
检测面和检测范围的确定原则上应保证检查到被检工件的整个体积范围。
对于板材、锻件、管材,螺栓件等,应检查到整个工件区域。
而对熔接焊缝来说,则应检测到整条焊缝,熔合线和热影响区。
检测面应经外观检查合格,所有影响超声检测的锈蚀、飞溅和污物等都应予以清除,其表面粗糙度应符合检测要求(一般为6.3UM).表面的不规则状态不得影响检测结果的正确性和完整性,否则应作适当的修理。
1.压力容器用碳素钢、低合金钢、不锈钢、镍及镍基合金板材的超声检测
1,板材的表面缺陷主要有裂纹、重皮和折叠;内部缺陷主要有分层和白点(白点仅可能发生在厚板中)。
板材由于经受巨大的压延变形,所产生的缺陷大都是平行于板材表面的片状缺陷,因此板材检测采用单晶或双晶直探头直接接触法或液浸法在板材表面进行超声检测,对于轧制比不足或较厚的板材经供需双方同意也可加用超声斜探头以检测非分层状缺陷,对于可能存在的表面裂纹,也可加用磁粉或渗透检测。
板材质量等级评定主要考虑三个因素:
单个缺陷指示长度(mm)、单个缺陷指示面积(平方厘米),在任一1Mx1M检测面积内存在的缺陷面积百分比(%)、,验收按JB/T4730的规定,共分为五个等级。
对奥氏体、双相不锈钢板材、铝及铝合金板材和钛及钛合金板材、压力容器用复合板材的超声检测方法和质量等级评定详见JB/T4730的规定。
2.压力容器用碳钢和低合金钢锻件超声检测
(1)碳钢和低合金钢锻件的主要缺陷和超声检测范围:
锻件缺陷主要有锁孔参与、疏松、夹杂、白点和裂纹等。
锻造缺陷一般呈面状,且垂直于主锻造方向,因此,锻件超声检测时,一般选用直探头采用纵波进行检测。
由于有些锻件形状比较复杂,而且锻件方向多变,可能产生取向各异的和各种缺陷,除直探头纵波检测外,还必须增加横波检测,如超高压整体锻造气瓶、筒形和环形锻件等。
(2)锻件质量等级评定主要考虑单个缺陷的波幅和位置、缺陷引起的底波降低量、密集区缺陷等三个参数。
具体划分按JB/T4730要求。
(3)验收级别按JB4726{压力容器用碳素钢和低合金钢锻件}、JB4727{低温压力和容器用用低合金钢锻件}.GB150和图样的规定选取。
3.压力容器用奥氏体、双相不锈钢锻件的超声检测。
奥氏体钢锻件超声检测应按JB/T4730的规定进行。
双相钢的组织是铁素体加奥氏体,目前在化工行业得到广泛应用。
对于这类锻件:
(1)当奥氏体含量小于或等于50%时,可采用碳钢和低合金钢锻件超声检测的相关规定进行超声检测;
(2)当奥氏体含量大于60%至80%时,应进行对比试验(主要是衰减、杂波等),以确定是采用碳钢和低合金钢锻件超声检测,还是采用奥氏体钢锻件超声检测的规定进行检测;
(3)当奥氏体含量大于80%时,可直接采用奥氏体钢锻件超声检测的有关规定进行超声检测。
4.压力容器用高压无缝钢管的超