五轴数控机床的RTCP精度调整方法.docx
《五轴数控机床的RTCP精度调整方法.docx》由会员分享,可在线阅读,更多相关《五轴数控机床的RTCP精度调整方法.docx(9页珍藏版)》请在冰豆网上搜索。
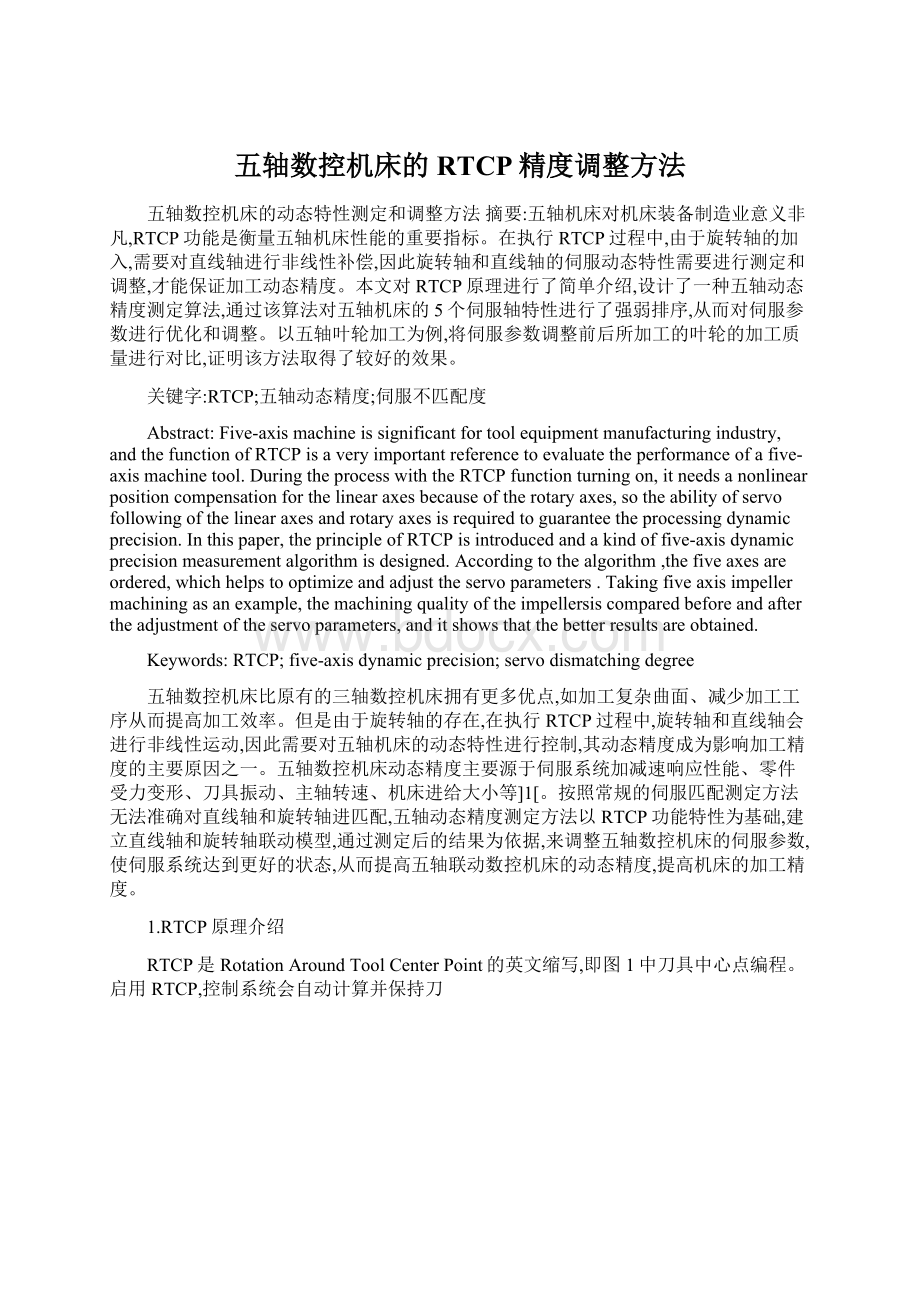
五轴数控机床的RTCP精度调整方法
五轴数控机床的动态特性测定和调整方法摘要:
五轴机床对机床装备制造业意义非凡,RTCP功能是衡量五轴机床性能的重要指标。
在执行RTCP过程中,由于旋转轴的加入,需要对直线轴进行非线性补偿,因此旋转轴和直线轴的伺服动态特性需要进行测定和调整,才能保证加工动态精度。
本文对RTCP原理进行了简单介绍,设计了一种五轴动态精度测定算法,通过该算法对五轴机床的5个伺服轴特性进行了强弱排序,从而对伺服参数进行优化和调整。
以五轴叶轮加工为例,将伺服参数调整前后所加工的叶轮的加工质量进行对比,证明该方法取得了较好的效果。
关键字:
RTCP;五轴动态精度;伺服不匹配度
Abstract:
Five-axismachineissignificantfortoolequipmentmanufacturingindustry,andthefunctionofRTCPisaveryimportantreferencetoevaluatetheperformanceofafive-axismachinetool.DuringtheprocesswiththeRTCPfunctionturningon,itneedsanonlinearpositioncompensationforthelinearaxesbecauseoftherotaryaxes,sotheabilityofservofollowingofthelinearaxesandrotaryaxesisrequiredtoguaranteetheprocessingdynamicprecision.Inthispaper,theprincipleofRTCPisintroducedandakindoffive-axisdynamicprecisionmeasurementalgorithmisdesigned.Accordingtothealgorithm,thefiveaxesareordered,whichhelpstooptimizeandadjusttheservoparameters.Takingfiveaxisimpellermachiningasanexample,themachiningqualityoftheimpellersiscomparedbeforeandaftertheadjustmentoftheservoparameters,anditshowsthatthebetterresultsareobtained.
Keywords:
RTCP;five-axisdynamicprecision;servodismatchingdegree
五轴数控机床比原有的三轴数控机床拥有更多优点,如加工复杂曲面、减少加工工序从而提高加工效率。
但是由于旋转轴的存在,在执行RTCP过程中,旋转轴和直线轴会进行非线性运动,因此需要对五轴机床的动态特性进行控制,其动态精度成为影响加工精度的主要原因之一。
五轴数控机床动态精度主要源于伺服系统加减速响应性能、零件受力变形、刀具振动、主轴转速、机床进给大小等]1[。
按照常规的伺服匹配测定方法无法准确对直线轴和旋转轴进匹配,五轴动态精度测定方法以RTCP功能特性为基础,建立直线轴和旋转轴联动模型,通过测定后的结果为依据,来调整五轴数控机床的伺服参数,使伺服系统达到更好的状态,从而提高五轴联动数控机床的动态精度,提高机床的加工精度。
1.RTCP原理介绍
RTCP是RotationAroundToolCenterPoint的英文缩写,即图1中刀具中心点编程。
启用RTCP,控制系统会自动计算并保持刀
具中心始终在编程的XYZ位置上,刀具中心
始终在编程坐标系中,转动坐标每个运动都
会被编程坐标系XYZ的直线位移所补偿]2[。
使用RTCP,可以直接编程刀具中心的轨迹,
而不用考虑五轴机床结构参数,大大简化了
五轴工艺编程和提高了加精度。
2.RTCP动态精度测定原理
在三坐标机床中,经常采用圆度测试
来检测任意直线轴间的动态特性是否匹配,但在五坐标机床运动过程中,由于旋转轴的加入,必须在每个插补点对旋转轴运动而带来的直线轴偏差进行非线性补偿,因此也必须对旋转轴和直线轴间的动态特性进行伺服匹配。
由于旋转轴和直线轴的控制单位不一样,不能像直线轴那样直接采用圆度测试,采用本方法,可以对五个轴的动态特性进行测试和排序,从而为伺服参数调整提供依据。
*基金项目:
“高档数控机床与基础制造装备”科技重大专项课题(2012ZX04001-012
以X、Y、Z直线轴加A、C转台轴的五轴机床为例,分析五轴之间的动态精度的调整方案。
本测定方案之前,需保证X、Y、Z直线轴按照普通三轴机床调试策略进行了直线轴之间的匹配。
在RTCP运动过程中,A轴运动会引起Y、Z轴运动,C轴运动会引起X、Y轴运动。
虽然加工过程中,五个轴会进行RTCP联动,其动态精度测定过程也需要五个轴进行插补运动。
但是由于建立五坐标RTCP动态测定模型比较困难,即使能够建立模型,反映动态匹配的指标也不能够直观地引导进行伺服参数的调整,因此需要对两个旋转轴以及关联的直线轴分别进行测定,简化RTCP动态测定模型。
本例中,A轴和Y、Z轴为一组测定,C轴和X、Y轴为另一组测定。
由于Y轴与A轴和C轴都有关联,在调试过程中Y轴伺服参数在一组测定完成后,另一组测定过程中不再进行调整。
以旋转轴A为例,在RTCP生效时,A轴旋转时,其关联的Y、Z轴实际运动轨迹是以转动半径为圆心的圆弧。
这里需要测定的内容包括:
Y、Z直线轴之间的匹配和A、Y、Z旋转轴和直线轴之间的匹配。
具体测定过程如下:
(1Y、Z直线轴之间的匹配
在旋转路径所在的象限中选取若干机床实际坐标采样点,计算每个采样点实际位置和指令位置之间的误差值(图2,根据每一象限误差总和ε
和采样点的个数N,由下面计算公式得出不匹配值:
4
4
2
2
3
3
1
1
N-
N-
N+
N=
εεεεμ(公式1
当计算结果:
大于零,Y轴比Z轴强;小于零,Y轴比Z轴弱。
对于C轴、X、Y轴的处理办法和A轴、Y、Z轴是一样的,以上测量过程就是常用的圆度测试方法。
(2A、Y、Z旋转轴和直线轴之间的匹配
在旋转路径所在的象限中选取若干机床实际坐标采样点,通过Y、Z轴的实际位置可以计算出A轴最优位置图3的值,A的实际位置由采样得到,计算A轴的最优位置和实际位置之间的误差值,根据误差总和ε和采样点的个数N,由计算公式:
ε
/
N得到误差平均值,就可以判断直线轴和旋转轴的强弱。
C轴与X、Y轴的判断方法和A轴的方法是一样的。
根据上面测定方法,确定五个轴的强弱程度的排序,以此来进行伺服参数的调整。
调整过程中,旋转轴的伺服参数不进行调整,只调整直线轴的伺服参数。
五轴动态精度测定流程见图4所示。
图4:
五轴动态精度测定流程图
3.功能测定及结果分析
为了测试算法的可行性,对叶轮加工做了对比实验,实验过程及结果如下:
3.1实验装置
1、DMG的AC双转台五轴机床(图5;
2、FANUC;
3、SSTT采样软件。
简单介绍一下SSTT采样软件,SSTT是伺服调整工具(ServoSelfTestTools的简称,主要用于配置FANUC数控系统的机床在线调试、诊断过程,也可以作为一种离线数据分析工具。
本实验主要通过SSTT工具采集各轴运动机床实际坐标数据,应用本文提出五轴动态精度测定方法来进行伺服参数调整,从而提高五轴RTCP动态特性。
3.2实验方案
第一步,按照机床原定的伺服参数,加工叶轮的流道、大叶片及小叶片。
第二步,采用RTCP动态精度测试方法,计算直线轴与直线轴、旋转轴与直线轴之间的不匹配度情况:
(1以A轴测试为例,在SSTT采样软件上设置好测试程序的相关参数,生成采样程序并发送到下位机,测试程序如下:
%12345;A轴行程-90度到0度,开启RTCP功能,实现A、Y、Z轴联动;
G54X-10Y-20Z-30F2000
G01A0
G128
M00
G01A-90
M00
G01A0
M30
机床运行该程序,由SSTT采集各轴的机床实际位置。
当程序运行到G43.4H1时,RTCP功能开启,运行到第一个M00时,SSTT采样开始,运行到第二个M00时,SSTT采样结束。
采样过程中,以时域图和圆轨迹图显示采样情况,如图6和图7。
图6:
采样时域图图7采样圆轨迹图
(2由采集的各轴的机床实际位置,用本文上述的RTCP动态精度测试方法,计算直线轴与直线轴、旋转轴与直线轴之间的不匹配度。
第三步,通过计算结果来指导机床伺服参数(主要是轴的位置比例增益调整,使其达到更佳的匹配状态。
如图1所示,五轴RTCP功能最基本的原理是保证旋转轴运动时刀具中心点保持不变,机床运动过程中使控制点绕着刀具中心点旋转,其刀具中心点到控制点的距离称为转动半径。
由于双转台类型结构的五轴机床,在实际加工中,刀位点是连续变化的,因此转动半径也是变化的,在动态精度测定前需要确定一个参考的转动半径作为测
试样本用例。
在本次实验中根据叶轮的加工区域选择最大的转动半径作为测试用例,测定速度2000mm/min为实际叶轮加工的切削速度。
测试中具体各轴调整情况如下:
(1A轴
Y、Z、A轴伺服匹配见表1。
表1:
Y、Z、A轴的伺服匹配情况
在进行A轴测定之前,由于旋转轴和直线轴之间控制单位不一样,需要先设定一个基准。
在本实验中,以旋转轴为基准,尽量将A轴的位置比例增益调整到最优位置,该机床A轴位置比例增益调整到1300为上限,接下来做匹配时只需调整直线轴Y轴和Z轴的位置比例增益。
以第三组实验为例,计算过程如下:
各象限的误差总和及采样点数分别为1ε=
-605.890×10-3mm,2ε=0,3ε=0,4ε=-544.922×10-3
mm,1N=1913,2N=0,3N=0,4N=1160,考虑转台的旋转方向矢量和G代码的指令方向,由计算公式1,计算出直线轴的伺服不匹配度为-1.525mμ;同理计算旋转轴和直线轴之间的不匹配度为-0.947mμ。
按照以上步骤计算A轴和C轴的各组实验数据,比较实验数据得实验结果。
A轴测定条件下,匹配情况最好时,A轴、Y轴和Z轴的位置比例增益分别为:
A1300,Z1283,Y1280。
(2C轴
表2:
X、Y、C轴的伺服匹配情况
C轴测定条件下,匹配情况最好时,C轴、X轴和Y轴的位置比例增益分别为:
C1280,X1280,Y1280。
第四步,调整参数后再次加工叶轮。
第五步,对比分析两次加工的叶轮的质量状况,从而分析算法的可靠性和可行性。
3.3实验结果与分析
(1调整前流道靠近小叶片顶端区域有明显的过切痕迹,调整后过切痕迹消失,表面光滑,见图8。
(a调整前(b调整后
图8:
调整前后流道区域加工比较
(2调整前大叶片背面底部有明显的过切痕迹,调整后过切痕迹消失,表面光滑,见图9。
(a调整前(b调整后
图9:
调整前后大叶片底部区域加工比较
从实验结果来看,经过五轴动态精度测定调整伺服参数后,叶轮中流道部分和叶片部分过切痕迹消失,加工表面质量有明显改善,取得非常好的效果,说明该五轴动态精度测定方法有效,具有现场应用调试能力。
4.结语
本文提出的五轴动态精度测定方法,通过现场应用调试,叶轮加工实验对比,以及分析实验结果可知,该方法确实能反映机床的动态精度,能够指导提升机床的加工精度和表面光洁度。
参考文献
[1]杜丽,张信,“S”形试件的五轴数控机床综合动态精度检测特性研究[J].电子科技大学学报,2014,43(4:
628-636.
[2]梁全,王永章,五轴数控系统RTCP和RPCP技术应用[J].组合机床与自动化加工技术,2008(2:
66-69.