钢水浇注基本操作规程.docx
《钢水浇注基本操作规程.docx》由会员分享,可在线阅读,更多相关《钢水浇注基本操作规程.docx(26页珍藏版)》请在冰豆网上搜索。
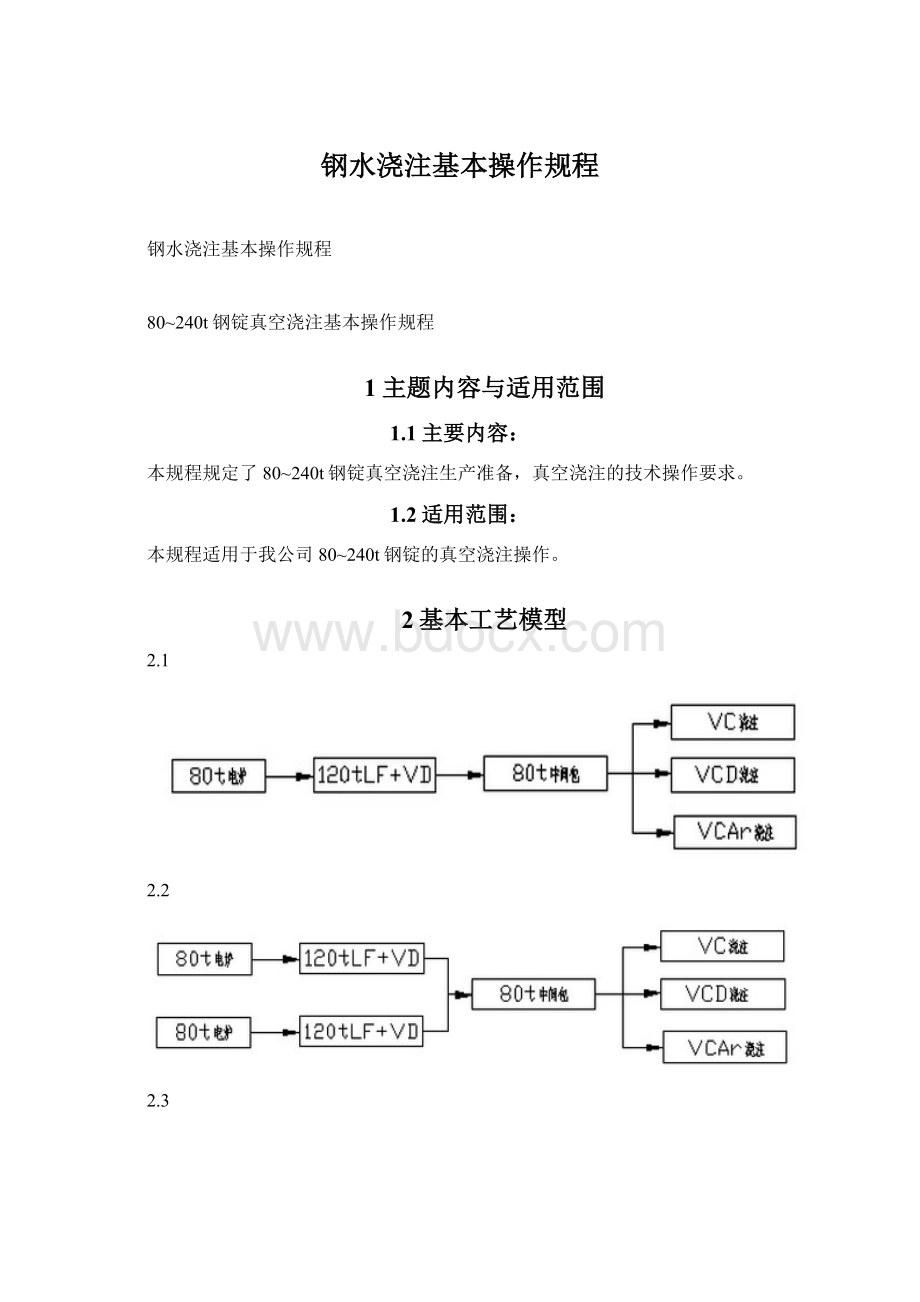
钢水浇注基本操作规程
钢水浇注基本操作规程
80~240t钢锭真空浇注基本操作规程
1主题内容与适用范围
1.1主要内容:
本规程规定了80~240t钢锭真空浇注生产准备,真空浇注的技术操作要求。
1.2适用范围:
本规程适用于我公司80~240t钢锭的真空浇注操作。
2基本工艺模型
2.1
2.2
2.3
2.4
2.5
3真空铸锭工艺流程
4生产准备
4.1精炼包的准备
4.1.1钢包的砌筑,详见附件3《精炼钢包砌筑施工要求》。
4.1.2钢包烘烤要求,详见附件4《钢包烘烤制度》。
4.1.3钢包水口及滑板安装,详见附件5《精炼钢包水口及滑板安装操作规程》。
4.1.4钢包透气砖安装,详见附件6《钢包透气砖安装工艺技术操作规程》。
4.1.5粗炼钢水对出钢包的要求:
普通铸件及碳钢可以烧新包,其余钢种不准烧新包。
4.2中间包准备
4.2.1中间包的砌筑,详见附件7《中间包砌筑施工要求》。
4.2.2中间包烘烤要求,详见附件4《钢包烘烤制度》。
4.2.3中间包水口、塞杆组装及安装,详见附件8《中间包塞杆组装及安装操作规程》。
4.2.4中间包水口的选择
中间包水口大小选择:
70~100t(包括100t)锭型水口直径选用Ф50mm;100t以上锭型水口直径选用Ф55mm,满足工艺要求水口直径可适当调整。
如果中间包采用塞头吹氩方式,水口直径加大5mm。
4.2.5中间包使用要求
新包和新包底只能用于浇注普通钢种,包底砸刚玉料面积不超过300×300mm2,不得用于重要钢种。
4.3钢锭模准备
4.3.1新钢锭模验收应严格按附件9《冒口、钢锭模、加高圈及底盘验收标准》进行验收,不合格的钢锭模不能使用。
4.3.2新钢锭模在使用前先进行烘烤,烘烤时要尽量用小火烘烤,升温速度不可过快,烘烤时可采用钢锭模下口朝上的方式进行,钢锭模摆放时一定将火焰位置置于模子中心,连续烘烤大于4h,烘烤温度大于120℃,最高不能超过350℃,坐模时温度不能超过120℃。
4.3.3冬季超过一周没用的凉模(模温≤30℃),使用前要进行烘烤,烘烤温度80~120℃,使用时模温>30℃的钢锭模,不需烘烤可直接使用。
4.3.4烘烤后的钢锭模应进行打磨。
4.3.5钢锭模接触钢水部位应磨光、吹净。
4.3.6钢锭模存在裂纹未达到报废标准的,要进行打锯板修补。
4.3.7钢锭模报废应符合附件10《冒口、钢锭模、加高圈及底盘报废标准》。
4.4底盘准备
4.4.1新底盘验收应严格按附件9《冒口、钢锭模、加高圈及底盘验收标准》进行验收,不合格的底盘不能使用。
4.4.2底盘直接用厚钢板垫至净空高度要求尺寸,尽量不用砖砌,如用砖砌的底盘,所用砖必须经过烘烤干燥。
4.4.3新底盘及长时间未用的凉底盘按钢锭模烘烤制度要求进行烘烤。
4.4.4底盘上表面平整,使用前将底盘能接触到钢水的部位打磨清除铁锈及残钢、残渣。
4.4.5底盘报废应符合附件10《冒口、钢锭模、加高圈及底盘报废标准》。
4.5加高圈准备
4.5.1新加高圈验收应严格按附件9《冒口、钢锭模、加高圈及底盘验收标准》进行验收,不合格的底盘不能使用。
4.5.2新加高圈及长时间未用的凉加高圈按钢锭模烘烤制度要求进行烘烤。
4.5.3加高圈上、下表面平整,使用前打磨清除铁锈及残钢、残渣。
4.5.4加高圈报废应符合附件10《冒口、钢锭模、加高圈及底盘报废标准》。
4.6保温冒的准备及烘烤
4.6.1新保温冒验收应严格按附件9《冒口、钢锭模、加高圈及底盘验收标准》进行验收,不合格的冒口不能使用。
4.6.2保温冒口共砌筑三层,第一层5mm厚的隔热板,第二层40mm厚的轻质保温砖,第三层160mm的粘土砖。
保温帽砌砖要保持与铁壳一致的锥度和要求的尺寸,砖缝小于2mm,砌好后用直尺检查斜面的不平度,误差不大于10mm,然后烘烤5h以上,使内衬完全干燥。
4.6.3使用后的保温帽要进行修补,修补后应保持原来的尺寸和锥度,以保证保温帽的容积。
真空浇注保温帽原则上不刷泥料,但距下沿200mm处允许修补。
4.6.4保温帽内衬损坏到不能保持原来的形状或脱帽有困难时,需要拆除重砌。
4.7导流管准备及烘烤
4.7.1导流管提前12h进行组装。
4.7.2导流管子母口破损、砖体有裂纹及内表面破损的不能使用。
4.7.3填缝用河砂必须干燥,受雨淋或潮湿的不能使用。
4.7.4导流管组装后,上口用泥料抹平,粘在导流管砖及壳体上的泥料清理干净。
4.7.5导流套烘烤:
导流管采用由下向上的烘烤方式,烘烤时,导流管要先在小火(火焰烤至下数第二环砖位置,约500mm)预热1.5h,然后将火焰调至下数第五环位置,并打开压缩空气使火焰充满,烘烤总时间大于6h,导流管烘烤温度在800℃以上。
4.8真空室的清理
4.8.1浇前将真空室内清理干净,真空盖内衬的残钢、残渣清净,特别是护板上表面的残渣必须清净,并用压缩空气吹扫干净。
4.8.2清理真空盖上表面,并用压缩空气吹扫干净。
4.8.3检查各密封法兰与密封胶圈是否正常,如存在问题及时处理。
4.9中间包盖的清理
4.9.1中间包盖要求上面清理,下面打磨,尤其注口内的残渣、残钢必须清净。
4.9.2中间包盖扣盖前要用压缩空气吹扫干净。
4.10发热剂和保温剂准备
发热剂和保温剂在运输及储存过程中应注意防护,严禁被雨水淋湿,在使用的前三天运到干燥室内干燥,干燥室内的温度不小于50℃。
5真空浇注操作
5.1钢锭模装配
5.1.1底盘套所有面都要打磨干净,铁锈清除干净,所有焊缝处的焊豆清除干净。
5.1.2底盘、钢锭模、加高圈、帽口按顺序吹风干净,进行装配。
5.1.3装配好的钢锭模用洁净钢板将帽口盖上,防止落入油污及杂物。
5.2座钢锭模
5.2.1钢锭模下真空坑后,在准备坐中间包前保证钢锭模口盖好,防止杂物和油污落入。
5.2.2根据所浇锭型的装配高度,用一定高度的底盘垫钢锭模,确保坐好后的钢锭模帽口距离导流管下沿保持200~500mm。
5.2.3保证坐好的钢锭模处于真空室中心,偏差不大于100mm。
5.3安装导流套
5.3.1用铁钎将导流管内表面未清理掉的残渣和砂粒清净,将上口多余的泥料清净,用压缩空气将导流管内、外彻底吹风。
5.3.2导流管安到真空盖上方导流管孔内。
5.3.3将钢锭模盖吊走,扣好真空盖。
5.4座中间包
5.4.1将中间包从烘烤位吊出,用压缩空气将中间包底部彻底吹扫干净。
5.4.2从下部检查塞棒的塞头是否正常,有问题及时处理。
5.4.3执行塞杆吹氩工艺的中间包,芯杆试吹氩,如透气不正常及时处理,处理无效时要更换塞棒。
5.4.4将中间包坐到真空盖上,打开真空阀开始抽真空。
5.4.5抽真空同时观察真空度上升情况,如真空度上升缓慢要进行系统检漏并及时处理。
5.5中间包测温及吸风
5.5.1中间包测温,测温位置为塞棒正对着的包壁1/2高度处,要求此时温度≥300℃且<500℃。
5.5.2中间包扣盖后进行包内吸风,将包内的残渣、灰尘等杂物彻底吸净。
5.6精炼包吊出
5.6.1VC真空度达到100Pa时,吊包温度符合工艺要求,即可吊出。
5.6.2精炼包吊出后外引流。
5.6.3外引流同时中间包内进行氩气置换。
5.6.4安装好氩气保护罩。
5.7真空浇注
5.7.1精炼包水口对正中间包浇口,停止中间包氩气置换变为向氩气保护罩内通入氩气。
5.7.2精炼包开浇,浇注过程中,精炼包水口距氩气保护罩距离≤80mm,浇注时注流取成品样,中间包内取气体样。
5.7.3执行塞杆吹氩工艺时,在中间包开浇前20秒,通过芯杆以0.15~0.3MPa的压力通入氩气,并保持整个浇注过程。
5.7.4中间包内钢水>2000mm,真空度达到67Pa以下,中间包内钢水达到3/4以上时测量中间包钢水温度后,方可压开塞棒。
各钢种浇注温度,详见附件1。
5.7.5中间包在浇注过程中随时调整精炼包注流,不得使包内钢水面下降到1500mm以下。
5.7.6多包合浇的钢锭,更换精炼包操作要快速完成,从前一包关闭水口到下一包开浇保证中间包内钢水高度≤1500mm。
5.7.7精炼包浇注结束时,要严格进行卡渣操作,防止精炼渣进入中间包。
5.7.8中间包浇完见渣关闭塞棒,进行卡渣操作。
5.8浇后
5.8.1中间包关闭后,打开放散阀破坏真空。
5.8.2加入第一批发热剂:
用量为锭型≤100t加一袋(25kg),100t<锭型≤300t加2袋(50kg)。
5.8.3吊走中间包盖与中间包。
5.8.4打开真空盖。
5.8.5加入第二批发热剂:
在打开真空盖后,立即通过筛网加入剩余全部发热剂,两次用量合计为1.5kg/t钢。
5.8.6待发热剂充分燃烧,火燃平熄后(发热剂加完3~8分钟),通过筛网加入碳化稻壳,用量为1.0kg/t钢。
5.8.7用氧气清理导流管内壁残钢残渣,清理后能继续使用的吊出等待下炉使用,不能继续使用的,吊出扒除导流管砖重砌。
5.9钢锭脱模
5.9.1到达工艺要求脱模时间时,立即脱模,脱模后在1h内完成热送,不能耽搁。
5.9.2脱模时注意不能碰撞模子。
5.10冒口欠浇高度判定
发现帽口内钢水高度有可能欠浇时,要在钢锭脱模热送前测量帽口的实际高度,按实际测得的帽口高度进行欠浇量判定。
5.11钢锭热送
5.11.1钢锭热送前进行表面测温,测温位置距水帽口各200mm处测量两点。
5.11.2热送温度≥550℃。
5.11.3质量判定,根据附件2《钢锭验收标准》执行。
5.11.4热送到大锻件分公司后,钢锭必须切肩、切割水帽口。
附件1各种钢种的钢锭浇注温度表:
钢种
浇注温度℃
钢种
浇注温度℃
35
1550-1570
SA-508Gr3.CL.1
1570-1590
45
1540-1560
30CrMoNiV511
1560-1580
16Mn
1570-1590
30Cr1Mo1V
1560-1580
20SiMn
1560-1580
5CrNiMo
1530-1550
35CrMo
1560-1580
30Cr2Ni4MoV
1550-1570
34CrNi3Mo
1545-1565
70Cr3Mo
1520-1540
20MnMo
1570-1590
34CrMo1A
1560-1580
25CrNiMoV
1560-1580
30CrMo
1560-1580
42CrMo
1555-1575
5CrMnMo
1530-1550
备注:
精炼包吊包温度下限按表中温度下限+40℃,吊包温度范围为10℃。
附件2钢锭验收标准
1钢锭验收标准:
1.1钢锭热送表面温度550~750℃,测温位置:
钢锭按《钢锭热送管理制度》执行。
1.2锭身出现裂纹时,裂纹位置在以下范围内,按合格钢锭处理:
所有钢锭,裂纹至锭尾距离小于50mm。
1.3锭身有裂纹或断流截痕时,不得热送,按废品处理。
如经质量管理部门鉴定可锻原件的,仍应送大锻件分公司,如认为需要试锻时,冶铸分公司向大锻件分公司办理委托手续,注明缺陷情况。
2接收钢锭标准:
2.1热送钢锭温度低于400℃不接收,由大锻件分公司运锭设备原因造成的除外。
2.2轧辊、水电用上注24棱钢锭帽口欠浇不得大于15%,其它规格钢锭帽口欠浇不得大于20%。
2.3钢锭帽口如有领带形或锥形深度达到帽口高度50%的缩孔时,不接收。
2.4对于表面有裂纹的钢锭,有顺纹不接收,横纹最大单个长度超过300mm以上不接收。
2.5在冶炼浇注过程中出现真空失效或达不到真空度要求等严重异常情况的钢锭不接收。
附件3钢包砌筑施工操作要领
1钢包材料要求
1.1钢包永久层:
铝镁浇注料打结厚度包壁100mm、包底120mm
1.2钢包工作层,渣线:
镁碳砖(MT-14A),包沿异型砖封口;熔池:
镁碳砖(MT-12);包底非冲击区:
铝镁碳砖(LMT);包底冲击区:
刚玉砖;工作层砌筑过程中所需膨胀砂、刚玉料、包沿料、镁质火泥。
1.3刚玉座砖(水口座砖、透气座砖)。
1.4耐材配置,80~110t及110~150t精炼钢包包壁工作层:
熔池铝镁碳砖(厚200mm,高100mm);渣线镁碳砖(厚230mm,高100mm);包底冲击区刚玉砖(高350mm);包底非冲击区铝镁碳砖(高300mm)。
2钢包砌筑要求
2.1钢包永久层浇注要求
2.1.1浇注前应检查各主要尺寸,水口孔、透气砖孔是否符合图纸及工艺要求。
2.1.2准备好搅拌机、振动棒,平板振动器、检查钢质胎具、水口胎具、透气口胎具的尺寸是否满足要求;各胎具外刷一层废机油并可再贴废旧报纸等纸张,保护内衬,以利脱模。
2.1.3安正水口砖胎具、透气砖胎具,钢包底、包壁采用10mm厚度石棉板作绝热层,接缝应小于5mm。
2.1.4采用铝镁浇注料,按配方要求分批配料,充分搅拌均匀后出料。
2.1.5包底浇注:
将混好的料转入钢包底,用平板振动器充分振动,达到排气密实即可,80~110t和110~150t精炼钢包包底浇注层厚度为120±5mm。
包底自然干燥至一定的耐压强度后(一般24h即可)吊入包壁胎具,定位固定,准备浇注包壁永久层。
2.1.6包壁浇注:
检查包壁胎具的定位及固定情况,核对满足图纸要求后,分批加入经充分搅拌混合均匀的浇注料,并立即用振动棒振捣,充分排气,均匀密实,80~100t和110~150t精炼钢包浇注层厚度100±5mm,注意防止料偏析过大或密度不均匀,待浇至包口30~50mm处收平。
2.1.7浇注永久层作业为连续作业,不能因其它原因中断作业。
2.1.8钢包浇注完毕后自然干燥24h方可脱胎具。
仔细检查浇注层,有不符合技术要求处,应立即进行修补打结;脱胎具后自然干燥48h以上方可砌筑工作层。
2.1.9钢包永久层浇注冬季(气温小于0℃)不准施工。
2.2座砖安装要求
2.2.1座砖与基准板之间不抹火泥,但必须保证座砖下表面与基准板表面平行、吻合。
2.2.2座砖中心线与基准孔中心线的相对偏差应≤2mm。
2.2.3安装座砖前,应对座砖外观质量进行确认。
2.3钢包工作层砌筑要求
2.3.1钢包工作层砌筑原则上必须干砌作业,砌筑砖缝:
不得大于1mm。
2.3.280~110t及110~150t精炼钢包包底工作层冲击区域应加厚50mm以适应80t电炉出钢时钢流的冲击。
2.3.3砌筑之前必须确认钢包永久层表面质量及水口座砖、透气座砖基准板是否平整。
2.3.4水口座砖和透气座砖安装完毕后,开始砌筑包底砖,包底砖与座砖紧贴(缝隙≤1mm)或包底砖与座砖之间留60~70mm的缝隙,缝隙之中用刚玉料打结。
水口座砖上表面应低于包底砖的上表面;透气座砖上表面应不低于包底砖的上表面。
2.3.5包底工作层四周与包壁的缝隙用浇注料打结;并确认平整后才能砌筑包壁砖。
2.3.6包壁砖应与永久层靠紧,挑选合适的砖型摆圈,最后封口砖要封紧。
2.3.7上下砌砖径向偏差≤10mm,同层周向错台≤10mm。
2.3.8砌筑上层砖时必须清理干净下层砖上表面的异物、包壁残留物、待砌耐火砖上的灰尘及异物,上下层砖之间不能出现贯通砖缝。
2.3.9永久层与包壁砖之间的弓形缝用膨胀砂填充。
2.4其它要求
2.4.1钢包工作层砖的外形尺寸应相对工整,必须能够满足干砌要求,保证砖缝≤1mm。
2.4.2钢包内衬各部位,即渣线、包壁、包底、包沿在使用过程中严禁发生漏钢。
2.4.3钢包在使用过程中,包沿浇注料不得自动脱落而露出包沿压块。
2.4.4各种散状材料的施工性能必须符合现场工艺需要。
2.4.5钢包内衬修砌完毕,必须把包内的异物清理干净。
3钢包停用修砌要求
3.1钢包永久层停用修砌要求
3.1.1钢包永久层使用寿命达到200次必须全部拆除。
3.1.2钢包永久层脱落或熔损面积大于300mm×300mm,深度大于50mm,部位超过两处,必须全部拆除。
3.1.3钢包永久层脱落或熔损面积大于150mm×150mm,深度大于30mm,部位超过五处,必须全部拆除。
3.1.4钢包永久层脱落或熔损露出钢包包壁(钢板),面积超过150mm×150mm,部位超过一处,必须全部拆除。
3.1.5冬季挖补必须采取防冻措施。
3.2钢包工作层停用修砌要求
3.2.1渣线工作层有一处残砖厚度小于120mm时,应停用修砌。
3.2.2熔池工作层有一处残砖厚度小于140mm时,应停用修砌。
3.2.3渣线或包壁工作层出现平缝或立缝且不能准确判断缝深度的,应停用维修。
3.2.4包底工作层出现50mm以上的坑或出现砖缝且不能准确判断缝深度的,应停用维修。
3.2.5包沿最上一层砖因掉砖或侵蚀快造成高度低于钢包压块30mm以上的停用维修或更换。
3.2.6包壳任何一个部位见红或漏钢,要立即停用待修砌。
附件4钢包烘烤制度
1新砌与挖补过的钢水包或中间包:
使用前必须充分烘烤干燥,烘烤时间见下表:
换砖范围
钢包名称
烘烤时间(h)
烘烤温度
新永久层
新工作层
80~110T精炼包
30
>800℃
110~150T精炼包
80T中间包
新工作层
80~110T精炼包
24
>800℃
110~150T精炼包
80T中间包
换渣线、换包底
80~110T精炼包
20
>800℃
110~150T精炼包
80T中间包
正常运转的旧包
精炼包
4
>800℃
中间包上塞杆后
3
300~500℃
2钢包烘烤曲线
烘烤曲线图如下:
曲线1:
永久层及工作层全部更换时烘烤曲线
曲线2:
只更换工作层时烘烤曲线
曲线3:
更换渣线或包底时烘烤曲线
曲线4:
正常运转的精炼包烘烤曲线
附件5精炼钢包水口及滑板安装操作规程
1滑动水口技术参数
1.1机构
序号
名称
主要参数
1
型号
YNMHK–5D
2
浇注孔径
φ80~110mm
3
弹簧规格(螺旋簧)
81×Φ63×Φ13
4
滑动行程
190mm
5
面压
10t
6
驱动方式
水平驱动(D)型
1.2油缸
序号
名称
主要参数
1
型号
SYG-6-D110/d50-210
2
油缸内径mm
φ110
3
活塞杆外径mm
φ50
4
行程mm
200
5
工作压力MPa
16
2必要的工具
2.1上水口安装工具
2.2上、下滑板拆卸工具
2.2.1铁榔头
2.2.2铁棒(φ25mm×1000mm)
2.2.3电筒
2.2.4风动扳手
3操作规程
3.1上水口的安装:
清除座砖孔内残钢、残渣、火泥等异物,试装上水口砖,检查上水口砖能否就位,在其外表面均匀涂上一层特种火泥,上口外沿稍微多点(见图1)。
用上水口安装工具将上水口砖推入座砖孔内(如图2所示),使上水口平面与安装板腔室平面装平。
上水口的倾斜度在1mm以内,清除多余火泥,擦清安装板表面,冷钢包必须烘烤上水口砖,待上水口砖火泥硬结后,才能安装上滑板。
3.2下滑板的安装:
3.2.1用压缩空气吹清滑动框内异物。
3.2.2将下滑板放入滑动框内。
3.3上滑板的安装:
3.3.1清除上水口凹口处及边沿的火泥硬块及冷钢、钢渣,清除安装板表面的火泥硬块。
3.3.2在上滑板凸口处涂抹火泥(如图3所示)。
3.3.3将上滑板砖推入固定框架内,用榔头木柄均匀敲紧、敲平,将上滑板固定。
3.3.4擦清上、下滑板表面。
3.3.5将门框关闭,转动肘节连杆到弹簧压板位置,用风动扳手对角交叉压紧弹簧压板。
3.4下水口砖的安装。
3.4.1在下水口凹口处均匀涂上滑板专用火泥,将下水口放入顶紧器内,旋紧顶紧器,用2.5磅榔头顺时针方向均匀敲打顶紧器四个桩头,使下水口凹口平面紧贴下滑板凸口平面,然后用榔头木柄插入下水口内试晃动,确认下水口是否被顶紧。
3.4.2用铁棒将水口孔内挤出泥浆捅干净。
3.4.3试拉2~3次,检查滑板是否安装合格,合格后打开滑动水口,拆下油缸,吊到烘烤工位烘烤,等待出钢。
3.5出钢操作:
3.5.1接到出钢指令后,关闭滑动水口,填充引流砂,接钢水精炼。
3.5.2精炼完,钢包吊至模铸作业区,挂上油缸。
启动油缸,使上下滑板孔对准(拉是开、推是关),如果钢水下不来,立即可以使用烧氧管把浇口填料捅开,如钢水已结壳,则需要点火吹氧开浇。
注意:
在吹氧时,须使吹氧管顶住结壳处,要垂直引流,以免烧坏耐火材料。
引流砂流净后,并有钢水出来,将下滑板关到底,氩气打开由下滑板吹氩,保证上水口内钢水不凝固,开浇后关闭下滑板氩气。
在获得良好的钢流后,根据需要调节滑板开度。
3.5.3钢水浇完钢流出渣子时,快速关上滑动水口。
3.5.4离开模铸作业区,拆下油缸,起吊钢包,倒渣。
挂上油缸,将钢包卧倒,启动油缸,使上下滑板孔对准。
烧氧清洗水口。
洗净后,将滑板处于全关状态。
3.5.5下水口砖拆卸,用榔头松开下水口顶紧器,拆下下水口砖。
用风动扳手对角松开弹簧压板顶紧螺丝。
翻开两边的肘节连杆。
打开门框。
拆卸上、下滑板,并重新安装一套滑动水口砖。
4维护
4.1简介:
在日常生产中,滑动机构需要良好的维护、管理及充分的备件组织。
4.2维护,YNMHK-5D型滑动机构的维护管理分为三个档次:
日常维修;一般维修;彻底维修。
4.3日常维修,每次在更换滑动机构耐材时都要进行以下机构维护工作:
4.3.1要用压缩空气、铲子和刷子将灰尘清除干净。
4.3.2在上下滑条工作面、滑动框与门框之间添加机油或二硫化钼。
4.3.3在门框铰链部位、连杆与轴销座等所有传动、转动部位加油润滑。
4.3.4铲除隔热板上飞溅的渣子,冷钢。
4.3.5检查空冷管接头是否完好,装卸是否方便,如发现问题必须立即修复。
4.3.6焊缝检查:
滑动水口机构安装在钢包上经使用后,由于热应力作用,焊缝可能会产生裂纹或脱焊,所以对所有焊缝务必严格检查,发现裂纹必须补焊加固后方可使用。
4.3.6.1安装板部件(YNMHK-5D-2-0)四只轴销座与安装板焊缝是否有脱焊或裂纹如有必须补焊加固。
4.3.6.2门框部件(YNMHK-5D-3-0)的铰链、弹簧箱托架与门框的焊缝是否有脱焊或裂纹。
4.3.6.3肘节连杆部件(YNMHK-5D-8-0)的销轴与连杆是否脱焊,肘节杆上4只面压螺钉旋转是否灵活,要经常加润滑油。
4.3.6.4以上焊缝若产生裂纹后需补焊时必须用角向砂轮将原有焊缝磨去后再重新补焊。
4.3.7紧固件:
准备好M10、12、16、20四种内六角螺钉板手,使用前对所有螺钉必须再紧固一次,以后每逢钢包大修后使用前再紧固一次,发现损坏及时更换,更换时承受拉力的螺钉拧入深度要求≥1.5D。
重点紧固部位有:
4.3.7.1门框底板与门框螺钉千万不能松动,尤其是门框中部螺钉,否则会影响压缩量不足,造成滑板间跑钢事故。
必要时可以用点焊焊死。
4.3.7.2顶紧套与滑动框连接的四只M16(20)螺钉不能松动,若松动会造成顶紧器顶不紧下水口或将下水口顶斜,造成下滑板与下水口接缝之间漏钢事故发生。
4.3.8活动部位:
4.3.8.1检查四根轴弹性圆柱销有否脱落,若有脱落及时补上。
4.3.8.2肘节连杆:
转动是否灵活,如不灵活则加润滑油调试,如仍不灵活则应及时修理或更换。
4.3.8.3滑动框在门框内有否卡死现象,如发现滑动框在门框内卡死则检查门框及