年产2万吨导电性聚氯乙烯车间设计化工.docx
《年产2万吨导电性聚氯乙烯车间设计化工.docx》由会员分享,可在线阅读,更多相关《年产2万吨导电性聚氯乙烯车间设计化工.docx(60页珍藏版)》请在冰豆网上搜索。
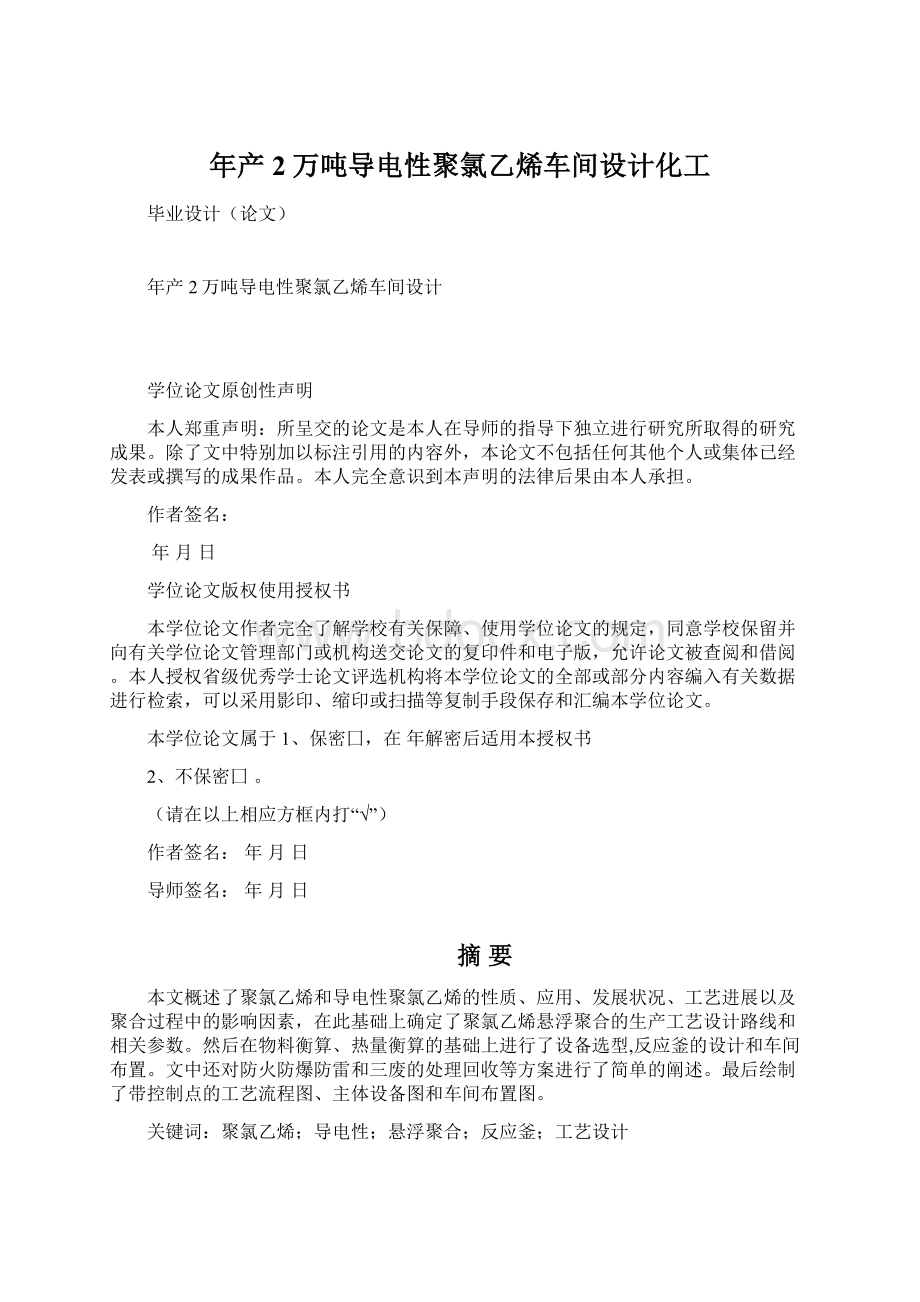
年产2万吨导电性聚氯乙烯车间设计化工
毕业设计(论文)
年产2万吨导电性聚氯乙烯车间设计
学位论文原创性声明
本人郑重声明:
所呈交的论文是本人在导师的指导下独立进行研究所取得的研究成果。
除了文中特别加以标注引用的内容外,本论文不包括任何其他个人或集体已经发表或撰写的成果作品。
本人完全意识到本声明的法律后果由本人承担。
作者签名:
年月日
学位论文版权使用授权书
本学位论文作者完全了解学校有关保障、使用学位论文的规定,同意学校保留并向有关学位论文管理部门或机构送交论文的复印件和电子版,允许论文被查阅和借阅。
本人授权省级优秀学士论文评选机构将本学位论文的全部或部分内容编入有关数据进行检索,可以采用影印、缩印或扫描等复制手段保存和汇编本学位论文。
本学位论文属于1、保密囗,在年解密后适用本授权书
2、不保密囗。
(请在以上相应方框内打“√”)
作者签名:
年月日
导师签名:
年月日
摘要
本文概述了聚氯乙烯和导电性聚氯乙烯的性质、应用、发展状况、工艺进展以及聚合过程中的影响因素,在此基础上确定了聚氯乙烯悬浮聚合的生产工艺设计路线和相关参数。
然后在物料衡算、热量衡算的基础上进行了设备选型,反应釜的设计和车间布置。
文中还对防火防爆防雷和三废的处理回收等方案进行了简单的阐述。
最后绘制了带控制点的工艺流程图、主体设备图和车间布置图。
关键词:
聚氯乙烯;导电性;悬浮聚合;反应釜;工艺设计
Abstract
Theproperties,application,developmentandthetechnologyprogressofPVCandconductivePVCweresummariedinthispaper.Aftertheinfluencefactorsofsynthesisprocessdiscussed,theproductionofaceticanhydrideprocessrouteandrelatedparametersaredetermined,andthematerialbalanceandheatbalanceofmainequipmentswerecalculated.Basedonthis,theequipmentsselection,agitatedreactorandworkshoplayoutwereaccomplished.Inaddition,theprotectionoffire,lightning,poisonand"threewastes"treatmentrecoveryplanweresimplydiscussed.Finallytheprocessflowchartwithcontrolpoint,thefigureofmainequipmentsandworkshoplayoutweredrawn.
Keywords:
PVC;conductive;suspensionpolymerization;agitatedreactor;processdesign
1绪论
1.1聚氯乙烯简介
聚氯乙烯(PolyVinylChloride)简称PVC,下同。
它是由氯乙烯在引发剂作用下聚合而成的热塑性树脂,是氯乙烯的均聚物。
PVC为无定形结构的白色粉末,支化度较小。
工业生产的PVC相对分子量一般在5万~12万范围内,具有较大的多分散性,相对分子量随聚合温度的降低而增加;无固定熔点,80~85℃开始软化,130℃变为粘弹态,160~180℃开始转变为粘流态;有较好的机械性能,抗张强度60MPa左右,冲击强度5~10kJ/m2;有优异的介电性能。
但对光和热的稳定性差,在100℃以上或经长时间阳光曝晒,就会分解而产生氯化氢,并进一步自动催化分解,引起变色,物理机械性能也迅速下降,在实际应用中必须加入稳定剂以提高对热和光的稳定性。
PVC很坚硬,溶解性也很差,只能溶于环己酮、二氯乙烷和四氢呋喃等少数溶剂中,对有机和无机酸、碱、盐均稳定,化学稳定性随使用温度的升高而降低。
PVC溶解在丙酮-二硫化碳或丙酮-苯混合溶剂中,用于干法纺丝或湿法纺丝而成纤维,称氯纶。
具有难燃、耐酸碱、抗微生物、耐磨并具有较好的保暖性和弹性。
1.2导电性聚氯乙烯简介[1]
PVC本身不导电,要使PVC具有导电性能,一般有两种方法。
一种是用化学方法(无规共聚和接枝共聚),产品通常被称为结构型导电材料;另一种方法是机械共混法(与导电组分物理共混),产品通常被称为复合型导电材料。
这类材料主要用于抗静电,电磁屏蔽和导电等领域。
如在抗静电方面应用最广的是集成电路及其部件的包装材料,处理或组装集成电路的工作台和地板,炸药厂,医院手术室,制药厂及其他无菌室的导电地板砖,防尘墙壁材料,防静电传送带,导电聚氯乙烯管子和管件等。
此外,还可广泛用于抗静电工作服,鞋,薄膜,开关等。
本设计采用机械共混法,填充导电材料为导电炭黑,故主要任务为PVC的生产和PVC与导电炭黑的共混设计。
1.3炭黑填充导电塑料的发展状况[2]
导电塑料领域的开发主要集中在炭黑填料的改性及新型导电炭黑的开发这两个方面,炭黑改性通常进行高温热处理,增加炭黑表面积,并改善表面化学特性;而新型导电炭黑的研究开发也引人注目,用高温裂解法从石油和焦油中制得的导电炭黑,其比表面积达900~1400m2/g,孔隙率80%~90%,灰分含量仅为0.1%~1.5%,将其填充到LLDPE中,可使复合材料表面电阻率降至6.2×103~1.1×104Ω,而力学性能基本不变。
此外,美国Cabot公司研制的SuperConductive炭黑和哥伦比亚化学公司的Conductex40~200等均为专用高效的超细导电炭黑。
这些新型炭黑虽然价格相对昂贵,但由于其导电率比普通炭黑高出2~3倍,只要填充很少的量就能满足材料的抗静电的要求,因此对基体聚合物的原有性能影响不大。
炭黑填充导电塑料的电阻值可以在10-4~109Ω·cm之间调节,分别用于研制抗静电材料,抗电磁屏蔽材料,半导体材料,以至高导电电材料,还可以根据热敏电阻特性开发自限温发热材料,广泛应用于化工、电子、电器、军工、采矿、农业及日常生活等领域。
1.4国内外聚氯乙烯悬浮聚合的工艺进展
经过长期的不懈努力,PVC生产技术已经取得了较大进展。
目前,世界各大PVC厂家都已形成了各自的工艺特点和风格,并已拥有许多专利和技术,也有各自追求的工业目标。
1.4.1国内聚氯乙烯悬浮聚合的工艺进展
国内PVC生产行业的发展近几年来一直呈现良好的势头。
各主要厂家都在积极采用先进的生产技术,不断改进工艺控制条件和工艺配方,努力提高产品质量,缩短聚合时间。
以北京二化、山东齐鲁石化公司和上海氯碱总厂等为代表的古德利奇大釜技术、工艺计算机自控技术和防粘釜技术等,均已达到和接近国际先进水平。
内蒙古亿利化学工业有限公司40万tPVC项目采用悬浮法生产聚氯乙烯,有聚合、干燥、成品三大装置。
主要包括VCM和脱盐水加料、化学品配制、聚合、汽提、回收、离心干燥、包装等工序,聚合加料采用双加料技术[3]。
内蒙古君正化工有限责任公司(二部)(以下简称君正化工二部)前身为内蒙古第二通用机械厂,于1992年建成6kt/aPVC、6kt/a烧碱生产装置,对PVC生产装置进行了不断技改和持续优化,解决了一系列制约生产装置连续运行的瓶颈问题,在2010年2~5月创造了氯乙烯生产装置安全生产79天无停车的记录[4]。
悬浮法PVC大型生产装置成套工艺技术是北京化二股份有限公司(以下简称北京化二)在消化吸收数套国外引进装置的基础上,汲取多年的生产经验并结合我国的实际情况而自主研制开发的工艺技术。
该成套工艺技术主要包括聚合生产配方、密闭入料、等温水入料、高效防粘釜、中途注水、新型汽提、新型旋风干燥、粉料输送和成品混料、高压回收氯乙烯单体、全自动包装码垛和DCS控制等项技术[5]。
1978年齐鲁石化率先引进信越127m3大釜,随后锦化、北二化引进古德里奇70.5m3大釜。
特别是锦化与锦化机联合开发的70.5m3大釜在国内得到广泛使用,小型釜所占比重逐步下降[6]。
目前我国的PVC生产技术与国外还有一定的差距,技术的“引进—吸收—消化—创新”是目前PVC生产的主要途径,通过对汽提技术及设备、干燥器、聚合配方、防粘釜技术等的改进,提高了我国PVC生产企业的效益,发展了我国的PVC工业[7-9]。
青岛海晶化工集团有限公司于2001年成功开发了1套工艺技术先进、操作简单方便、投资经济合理、居国内同行业领先水平的聚氯乙烯装置,使公司聚氯乙烯装置产能由4万t/a扩大至8万t/a[10]。
贵州大学开发的一种原位悬浮聚合PVC树脂的方法,提高了PVC的高抗冲性[11]。
1.4.2国外聚氯乙烯悬浮聚合的工艺进展[12-15]
古德利奇(B.F.Goodrich)公司主要采取通过提高单釜产量和延长清釜周期的方式来提高生产效率,其悬浮工艺特点是清釜和脱挥发分技术。
赫斯特(Hoechst)公司的悬浮聚合技术和密闭聚合釜技术、许尔斯(WerkeHuls)公司的悬浮聚合技术以及法国阿托(ATO)化学公司悬浮聚合汽提技术目前居于世界领先地位。
此外,欧洲的其他一些公司,如意大利的赛斯(Cris)公司则是在防粘釜技术方面领先。
从综合技术方面上看,日本公司具有较高的水平并各具特色。
西素(Chisso)公司、吉昂(Zeon)公司等拥有先进的悬浮技术和工艺。
佳友(Sumitomo)化学公司悬浮聚合树脂产品的质量品质最好。
日箭(SunArrow)拥有多牌号产品的生产技术。
此外,这些公司不仅在以上诸方面处于领先地位,而且在缩短聚合操作周期,提高生产效率方面也取得了较大进步。
从PVC的生产工艺层面上看,西欧一些国家采用本体法和乳液法的比重较大,而美国、日本和我国等国家和地区则以悬浮法为主,日本悬浮法所占比重最高。
对于悬浮聚合工艺主要发展方向是积极开发连续悬浮聚合工艺流程,并已取得许多重要成就。
从提高生产效率层面上看,所普遍采用的技术手段是:
开发和应用新型复合引发剂、发散剂;采用计算机数控技术工艺;采用多种强化传热措施(如增加回流冷凝器)等。
从防粘釜技术层面上看,意大利的赛斯(Cirs)公司居世界领先地位。
其NOXOLWSW和NOXOLETH的防粘釜剂系列十分著名。
该防粘釜剂无毒无害。
每喷涂一次,可以连续350~500釜次不用人工清釜。
美国B.F古德里奇(B.F.Goodrich)公司的防粘釜技术也已达到400釜次的水平。
防粘釜技术的迅速发展,使聚合操作辅助时间得到大大缩短。
目前,平均清釜周期多数己达100~500釜次。
韩国LG化学、日本的太阳乙烯衍生物公司、信越(Shin-Etsu)化学工业公司、金子公司和新第一塑料公司等公司开发的连续悬浮聚合工艺流程较为典型。
其流程概况是:
流程主体为两个或三个串联的塔式反应器。
第一个反应器采用注水工艺操作,同时加入NaNO2等抑垢剂,以减少粘壁物和污垢,该反应器结构新颖。
其外形特征是顶端部分较小。
操作时,该结构一方面可使反应器顶部只存有少量气相物,从而减小了气液相界面;另一方面,该气相部分还具有聚合压力安全缓冲装置的作用。
第一反应器的聚合反应温度为67.5℃。
单体转化率控制在15%~30%之间;第二反应器中的单体转化率为89%~91%。
第二反应器的热负荷较大,其聚合热采用冷却夹套换热方式。
反应器内顶部表面温度要求低于30℃。
主要目的是避免气液界面形成粘壁聚合物。
该工艺生产的树脂具有相同的粒度和粒度分布,生产强度达198~259t/(m3·a)。
赫斯特(Hoechst)公司开发的连续悬浮聚合工艺、意大利阿托公司以法国Pechinen-Saint-Gobain的两段法本体合工艺,具有较为鲜明的传统技术特色。
该流程主体也由三个串联的管式反应器组成,但工艺作用、工艺条件以及设备结构与日本流程有所不同。
第一反应器的工艺作用是进行预聚,以调控粒度和粒度分布。
工艺目标是获得窄的粒度分布。
关键工艺指标转化率的控制范围一般在5%~8%之间。
第二反应器的工艺作用仅仅是为了使聚合进一步进行,单体转化率控制在30%~35%;第一反应器的长径比为10:
1,采用电化抛光表面处理,材料为不锈钢。
搅拌采用7层搅拌器,等距安装在中心轴上。
搅拌速度为600r/min,以便于形成轴向活塞流。
第二反应器的长径比为5:
1,材质为碳钢搪瓷,0~20o斜卧放置。
内置搪瓷桨叶搅拌器,转速为70r/min。
流体为活塞流,以减少聚合物形成粘釜物和污垢。
第三反应器与第一聚合釜结构及放置方式均相同,但材质为不锈钢,夹套除热,搅拌速度为50r/min。
其主要功能是提供适宜的除热能力。
反应时加入酒石酸、NaNO2等抑垢剂。
工艺设备在连续操作500h以后,釜内粘壁物大约为15~30ppm(以聚合物计)。
该流程可用于聚合温度为50~66℃的PVC生产。
产品粒度分布窄,品均粒度为130~150μm。
1.5聚合工艺实践方法
目前,世界上PVC的主要生产方法有4种:
悬浮法、本体法、乳液法和微悬浮法。
其中以悬浮法生产的PVC占PVC总产量的近90%,在PVC生产中占重要地位,近年来,该技术已取得突破性进展。
1.5.1本体聚合生产工艺[16]
本体聚合生产工艺,其主要特点是反应过程中不需要加水和分散剂。
聚合分2步进行,第1步在预聚釜中加人定量的VCM单体、引发剂和添加剂,经加热后在强搅拌(相对第2步聚合过程)的作用下,釜内保持恒定的压力和温度进行预聚合。
当VCM的转化率达到8%~12%停止反应,将生成的“种子”送人聚合釜内进行第2步反应。
聚合釜在接收到预聚合的“种子”后,再加人一定量的VCM单体、添加剂和引发剂,在这些“种子”的基础上继续聚合,使“种子”逐渐长大到一定的程度,在低速搅拌的作用下,保持恒定压力进行聚合反应。
当反应转化率达到60%~85%(根据配方而定)时终止反应,并在聚合釜中脱气、回收未反应的单体,而后在釜内汽提,进一步脱除残留在PVC粉料中的VCM,最后经风送系统将釜内PVC粉料送往分级、均化和包装工序。
1.5.2乳液聚合生产工艺[16]
氯乙烯乳液聚合方法的最终产品为制造聚氯乙烯增塑糊所用的的聚氯乙烯糊树脂(E-PVC),工业生产分两个阶段:
第一阶段氯乙烯单体经乳液聚合反应生成聚氯乙烯胶乳,它是直径0.1~3µm聚氯乙烯初级粒子在水中的悬浮乳状液。
第二阶段将聚氯乙烯胶乳,经喷雾干燥得到产品聚氯乙烯糊树脂,它是初级粒子聚集而成得的直径为1~100µm,主要是20~40µm的聚氯乙烯次级粒子。
这种次级粒子与增塑剂混合后,经剪切作用崩解为直径更小的颗粒而形成不沉降的聚氯乙烯增塑糊,工业上称之为聚氯乙烯糊。
1.5.3悬浮聚合生产工艺
悬浮法PVC生产技术易于调节品种,生产过程易于控制,设备和运行费用低,易于大规模组织生产而得到广泛的应用,成为诸多生产工艺中最主要的生产方法。
工艺特点:
悬浮聚合法生产聚氯乙烯树脂的一般工艺过程是在清理后的聚合釜中加入水和悬浮剂、抗氧剂,然后加入氯乙烯单体,在去离子水中搅拌,将单体分散成小液滴,这些小液滴由保护胶加以稳定,并加入可溶于单体的引发剂或引发剂乳液,保持反应过程中的反应速度平稳,然后升温聚合,一般聚合温度在45~70℃之间。
使用低温聚合时(如42~45℃),可生产高分子质量的聚氯乙烯树脂;使用高温聚合时(一般在62~71℃)可生产出低分子质量(或超低分子质量)的聚氯乙烯树脂。
近年来,为了提高聚合速度和生产效率,国外还研究成功两步悬浮聚合工艺,一般是第一步聚合度控制在600左右,在第二步聚合前加入部分新单体继续聚合。
采用两步法聚合的优点是显著缩短了聚合周期,生产出的树脂具有良好的凝胶性能、模塑性能和机械强度。
现在悬浮法聚氯乙烯品种日益广泛,应用领域越来越广,除了通用型的树脂外,特殊用途的专用树脂的开发越来越引起PVC厂家的关注,球形树脂、高表观密度建材专用树脂、消光树脂、超高(或超低)分子质量树脂等已成为开发的热点[17]。
悬浮法PVC的发展趋:
在工业化生产PVC时,以悬浮法产量最大,悬浮法生产具有设备投资少和产品成本低等优点。
各种聚合方法的发展方向是逐步向悬浮法聚合生产路线倾斜,一些过去采用其它方法生产的树脂品种已开始采用悬浮聚合工艺生产。
自从乳液聚合法工业化以后,欧洲、日本在连续悬浮聚合工艺方面开展了大量的研究工作,目前尚未工业化生产,但连续法设备费用低,生产效率高,工艺难题少,已引起了各国科研院所和生产厂家的重视。
另外,为进一步提高悬浮法生产的通用树脂和专用树脂的质量,提高产品的专用化、市场化水平,国外厂家在聚合工艺的工艺条件及配料体系等方面做了大量的研究工作,进一步提高了聚合转化率,缩短了聚合周期,提高了生产效率,同时也开发出一系列性能好、易于加工的PVC专用树脂如:
超高(或超低)聚合度树脂、高表观密度树脂、无皮树脂、耐辐射树脂、医用树脂、耐热树脂等。
可见,各种专用料的开发是悬浮聚合树脂发展的标志,是提高产品使用性能、开发新的应用领域的重要手段[18]。
本设计采用悬浮法PVC生产技术。
1.6悬浮聚合生产工艺的两种操作方法的比较[14,15]
1.6.1连续式操作
连续聚合流程具有形成规模经济迅速等特点和优势,但存在工艺灵活性差、产品品种单一等不足。
其技术开发的核心,依然是如何开发新型引发剂、分散剂、防粘釜剂以及其它助剂,以提高聚合反应速率,缩短聚合生产周期;关键工艺技术所面临的也还是传热和搅拌这两个基本问题。
1.6.2间歇式操作
间歇法工艺流程具有生产品种灵活多样、工艺挖掘潜力大等诸多优点。
因而具有较强的生命力。
为进一步提高通用树脂、专用树脂和糊树脂的质量,提高产品的专用化、市场化水平,近年来,国内外许多PVC生产厂家在间歇法工艺的研究上,紧紧抓住生产过程中聚合温度和搅拌这两个基本问题,一方面从设备的结构、材质等方面入手,不断提高聚合釜容积。
目前,大釜技术和先进的除热手段在工业生产中已经得到广泛应用,容积为200m3的聚合釜已屡见不鲜。
同时,为了缩短聚合周期并使工艺运行达到最优化状态,计算机控制技术的应用也正趋广泛。
这些技术的应用,使聚合周期得到相对缩短,产品质量更加稳定,生产成本也不断降低。
单釜效率己达到或超过原来的3倍。
本设计采用的是间歇式操作方式。
1.7氯乙烯悬浮聚合生成聚氯乙烯过程中的影响因素
1.7.1纯水的影响[19]
入料的水质直接影响树脂产品的质量,如硬度(表征水中金属等阳离子含量)过高,会影响产品的电绝缘性能和热稳定性;氯根(表征水中阴离子含量)过高,特别是对于聚乙烯醇分散体系,易使颗粒变粗,影响产品的颗粒形态;纯水的PH值影响分散剂的稳定性,较低的值对明胶有明显的破坏作用,较高或较低的值都会引起聚乙烯醇的部分醇解,影响分散效果及颗粒形态,还会影响引发剂的解速率。
此外,水质还会影响粘釜及鱼眼。
1.7.2乙炔的影响[19]
乙炔是一种很强的链转移剂,它会和引发剂游离基、单体游离基或链游离基发生链转移反应。
乙炔含有叁键,氢原子又活泼,既可以和游离基加成,又可发生氢原子转移反应,这种转移反应速率比单体髙,但产生游离基的活性都比较低。
因此,不仅使PVC聚合度降低,还使聚合速率变慢。
所产生的炔型游离基进行链增长反应,使PVC大分子中含烯丙基氯(或乙炔基)链节,导致PVC产品的热稳定性。
1.7.3高沸物的影响[19]
单体中含有1,1—二氯乙烷、1,2—二氯乙烷、1,1,2—三氯乙烷、乙醛、偏二氯乙烯、甲烷等高沸物,均为活泼的链转移剂,会降低聚合速率和PVC的聚合度。
氯乙烯单体中的高沸物主要为二氯乙烷和乙醛,单体中含量低时,可以清除PVC大分子端基双键,对PVC热稳定性有好处,二氯乙烷和乙醛等高沸物在较高含量下才显著影响聚合度及反应速率。
1.7.4聚合体系中氧的影响[19]
氧对氯乙烯聚合起阻聚作用,氯乙烯单体易吸收氧,而生成平均聚合度低于10的氯乙烯过氧化物。
这种过氧化物能引发单体聚合,使大分子中存在该过氧化物链段,并且有较低的分解温度,在聚合条件下易分解为氯化氢、甲醛和一氧化碳而降低反应介质的PH值。
此种过氧化物存在聚氯乙烯中,将使其热稳定性显著变坏,产品易变色。
一般入料纯水通过真空脱氧后加入聚合釜。
1.7.5聚合体系中铁的影响[19]
无论水、单体、引发剂还是分散剂中的铁,都对聚合反应有不利的影响。
铁能与有机过氧化物引发剂反应,使聚合诱导期增长,反应速率减慢,产品的热稳定性变坏,还会降低产品的介电性能。
此外,铁还会影响产品的均匀度。
1.7.6分散剂的影响[23]
分散剂及适当的搅拌强度可以优化VCM液滴的分散,提高PVC颗粒粒径的规整度、颗粒的多孔性和干流动性,改善PVC的塑化性能,提高PVC的白度和加工性能。
分散剂用量的选择,要根据聚合釜的形状、大小、搅拌状态以及产品要求而定。
分散剂用量过多,不仅不经济,还会增大体系粘度,造成悬浮液泡沫多,气相粘釜严重,浆料汽提操作困难,VCM回收泡沫夹带增加,树脂颗粒变细,堵塞回收管路;分散剂用量少,则起不到应有的稳定作用,体系稳定性差,容易产生大颗粒物料,产品颗粒不规整,甚至造成聚合颗粒的粘结而酿成事故。
一般悬浮法聚氯乙烯生产都选用复合分散体系。
包永忠等[20]通过研究聚乙烯醇助分散剂对悬浮聚氯乙烯树脂颗粒特性的影响发现,在复合主分散剂PVA/HPMC(羟丙基甲基纤维素)基础上加入LM22(聚乙烯醇助分散剂)助分散剂,随着含量增加分散体系水溶液—三氯乙烯界面张力和保胶能力降低,PVC树脂的平均粒径和增塑剂吸收量增加,PVC树脂颗粒表面粗糙度增加并逐渐出现少皮膜的表层结构,颗粒内部孔隙率增加,初级粒子聚集程度降低,颗粒内部孔径分布变窄。
1.7.7引发剂的影响[19]
引发剂的用量根据聚合釜设备的传热能力和实际需要而确定,用量多,单位时间内所产生的游离基增多,反应速率快,聚合时间短,设备利用率髙;一旦反应热不能及时移出,将发生爆聚。
另外,引发剂过量易使产品颗粒变粗,孔隙率降低。
引发剂用量太少,反应速率慢,聚合时间长,设备利用率低。
目前大部分生产企业选用复合引发剂体系,尽量避免反应放热峰的出现或尽量减小峰高,使反应速率尽可能均匀,这样聚合反应热就能及时移出,达到安全平稳生产的目的。
1.7.8涂釜剂的影响[19]
涂壁效果不好易造成粘釜,粘釜会导致聚合釜传热系数和生产能力降低;粘釜料若混入产品中,会导致塑化加工中不塑化的“鱼眼”产生,影响产品外观及内在质量;粘釜物的清理将延长聚合釜的辅助时间及增加人工劳动强度,降低设备的利用率。
此外,粘釜还影响聚合釜自动控制的实施。
1.7.9调节剂的影响[19]
在聚合生产中,体系的PH值对树脂颗粒的粗细有很大的影响,值过高或过低都会使颗粒变粗。
在聚合系统中加人PH调节剂碳酸氢铵,维持釜内体系的PH值在中性范围,确保分散剂和聚合体系的稳定性,使PVC树脂具有较好的粒度。
1.7.10聚合温度的影响[19]
在不添加链转移剂的情况下,聚氯乙烯聚合度取决于聚合温度,聚合温度越高,所产生的树脂聚合度越低,自由基的能量就越高,分子链中越易生成支链、末端基双键等不稳定结构,如果聚合反应体系中还存在氧,PVC分子内越容易形成羧基烯丙基,产品的热老化性能就越差。
因此在生产中,对于某一给定聚合度的PVC树脂,可适当降低反应温度,以利于PVC热稳定性的提高。
一般说来,当聚合温度波动2℃时,平均聚合度相差366。
聚合反应温度控制在±0.2℃以内,这样使聚合度分布集中,易于加工,产品热稳定好。
因此,聚合工艺推荐使用热水入料工艺,热水入料不仅可降低水中含氧量,而且因为减少了聚合升温时间,降低了相对分子量分散性,也提高了产品的加工热稳定。
1.