数控加工技术教案.docx
《数控加工技术教案.docx》由会员分享,可在线阅读,更多相关《数控加工技术教案.docx(66页珍藏版)》请在冰豆网上搜索。
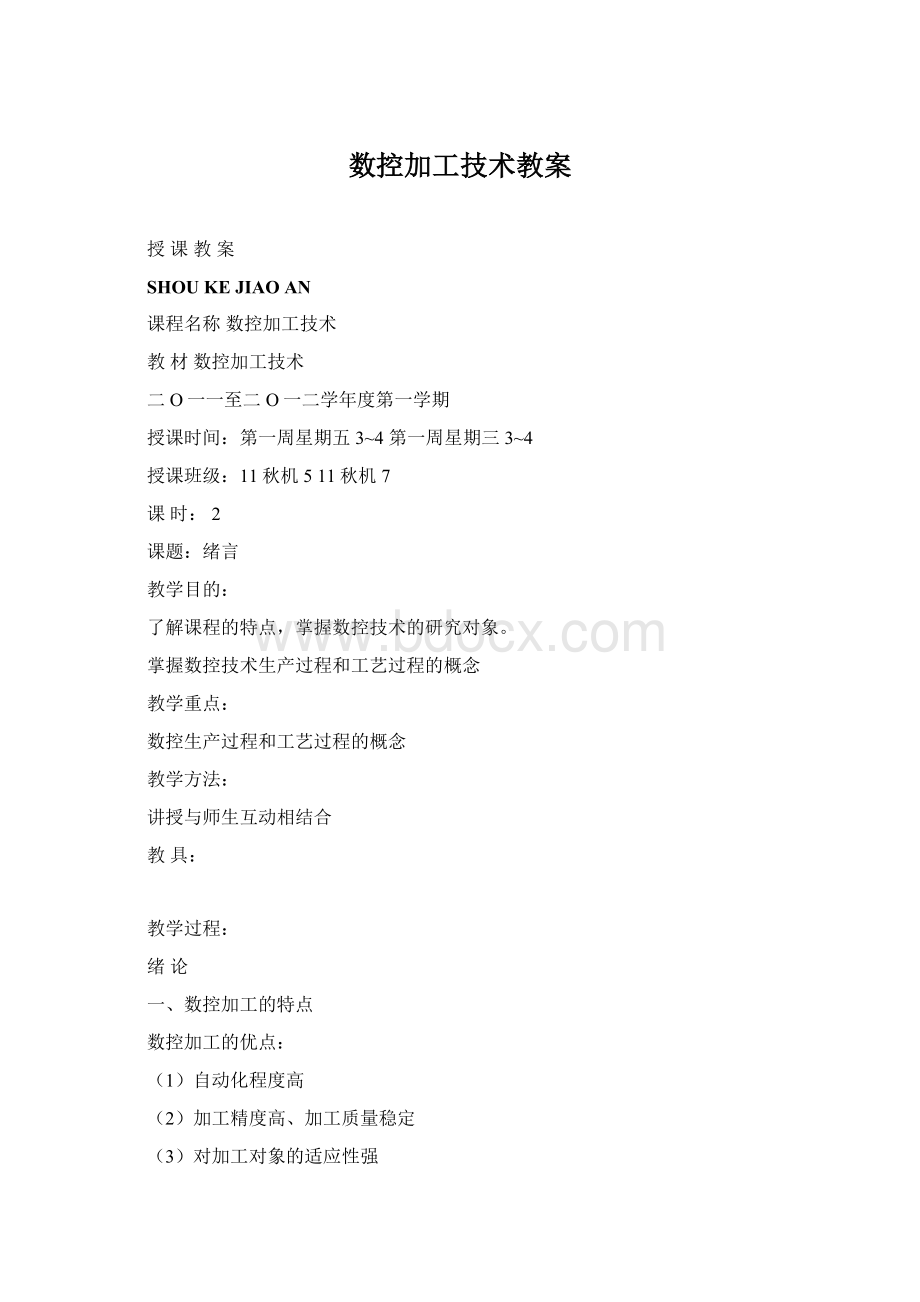
数控加工技术教案
授课教案
SHOUKEJIAOAN
课程名称数控加工技术
教材数控加工技术
二O一一至二O一二学年度第一学期
授课时间:
第一周星期五3~4第一周星期三3~4
授课班级:
11秋机511秋机7
课时:
2
课题:
绪言
教学目的:
了解课程的特点,掌握数控技术的研究对象。
掌握数控技术生产过程和工艺过程的概念
教学重点:
数控生产过程和工艺过程的概念
教学方法:
讲授与师生互动相结合
教具:
教学过程:
绪论
一、数控加工的特点
数控加工的优点:
(1)自动化程度高
(2)加工精度高、加工质量稳定
(3)对加工对象的适应性强
(4)生产效率高
(5)易于建立计算机通信网络
数控加工的缺点:
数控机床价格昂贵,加工成本高,技术复杂,对工艺和程序编制要求高,加工中难以调整,维修困难。
需要高素质的加工操作人员。
二、数控机床的适用范围
1、数控机床的适用范围
一般来说,数控机床特别适合于加工零件较复杂、精度要求高、产品更新频繁、生产周期要求短的场合。
零件复杂及生产批量的不同,三种机床的应用范围的变化,当零件不太复杂,生产批量又较小时,宜采用通用机床;当生产批量很大,宜采用专用机床;而随着零件复杂程度的提高,数控机床越显得适用。
目前,随着数控机床的普及,应用范围止由BCD向EFG线复杂性较低的范围扩大。
通用机床、专用机床和数控机床零件加工批量与生产成本的关系。
在多品种、中小批量生产情况下,采用数控机床总费用更为合理。
根据数控加工的优缺点及国内外大量应用实践,一般可按适用程度将零件分为三类:
(1)最适用类
1.形状复杂,加工精度要求高,用通用机床无法加工或虽然能加工但很难保证产品质量的零件。
2.用数学模型描述的复杂曲线或曲面轮廓零件。
3.有难测量、难控制进给、难控制尺寸的不开敞内腔的壳体或盒型零件。
4.必须在依次装夹中合并完成铣、镗、铰或螺纹等多工序的零件。
(2)较适用类
1.在通用机床加工时极易受人为因素(如:
情绪波动、体力强弱、技术水平高低等)干扰,零件价值又高,一旦质量失控会造成重大经济损失的零件。
2.在通用机床上加工时必须制造复杂的专用工装的零件。
3.需要多次更改设计后才能定型的零件。
4.在通用机床上加工需要作长时间调整的零件。
5.用通用机床加工时,生产率很低或体力劳动强度很大的零件。
(3)不适用类
1.生产批量大的零件。
2.装夹困难或完全靠找正定位来保证加工精度的零件。
3.加工余量不稳定,且数控机床上无在线检测系统可自动调整零件坐标位置的零件。
4.必须用特定的工艺装备协调加工的零件。
2、数控机床的结构特点
1.主运动常用交流或直流电动机拖动,采用变频调速,简化了主传动系统的机械结构,而且转速高、功率大,速度变换迅速、可靠;能无级变速。
合理选择切削用量。
2.主轴部件和支承件均采用了刚度和抗振性较好的新型结构。
如采用动静压轴承的主轴部件,采用钢板焊接结构的支承件等。
3.采用了摩擦因数很低的塑料滑动导轨、滚动导轨和静压导轨,以提高机床运动的灵敏性。
4.进给传动中,一方面采用无间隙的传动装置和元件,如滚珠丝杠副、静压蜗杆蜗条副、预加载荷的双齿轮齿条副等。
另一方面采用消除间隙措施,如偏心套式、锥度齿轮式及斜齿轮垫片错齿等消隙结构。
5.采用了多主轴、多刀架的结构,以提高单位时间内的切削功率。
6.具有自动换刀和自动交换工件的装置,以减少停机时间。
7.采用自动排屑、自动润滑装置等。
授课时间:
第二周星期三1~2第二周星期二3~4
授课班级:
11秋机511秋机7
课时:
2
课题:
切削运动与切削要素
教学目的:
熟悉切削运动的概念及分类,掌握切削用量三要素。
教学重点:
切削用量、切削层参数。
教学难点:
切削层参数
教学方法:
讲授与师生互动相结合
教具:
教学过程:
第一章数控加工的基础知识
第一节切削运动与切削要素
一、切削运动
1.切削运动的基本概念
指切削加工时,刀具与工件间的相对运动。
分为主运动与进给运动。
2.主运动和进给运动
(1)主运动:
a.由机床或者人力提供的主要运动,是完成切削加工所必需的最基本的运动。
B通常,它是速度最高、消耗功率最多的。
c一台机床只有一个主运动。
(2)进给运动:
是除主运动以外的,用于连续切下切屑的运动,一般它的速度较低、消耗的功率较小。
一台机床可以有多个进给运动。
二、切削用量和切削层参数
1.切削过程中工件上的表面
待加工表面:
即将切除的工件表面
已加工表面:
已被切去多余金属而形成的工件新表面
过渡表面:
正在切除的表面
2.切削用量
(1)切削速度Vc
a指切削刃选定点相对与工件主运动的瞬时速度.
b主运动为旋转运动时的切削速度:
Vc=3.14dn/1000(m/min)
(2)进给量f
指刀具或者工件在进给运动方向上相对与工件或者刀具移动的距离.
车削时:
f为每转移到量(mm/r)
钻削时:
f为每转移动量(mm/r)
铣削时:
f可为每齿进给量、每转进给量、进给速度
Vf=fn=fzZn
(3)背吃刀量ap
指工件上以加工表面与被加工表面间的垂直距离。
3.切削层要素
(1)切削层公称宽度Bd
(2)切削层公称厚度Hd
(3)切削层公称面积Ad
Ad=Bd×Hd=ap×
三、作业与思考
1.车床、铣床、磨床、钻床有哪些运动,其中,哪个是主运动?
进给运动是哪些?
2.切削运动三要素是什么?
各自的单位如何?
授课时间:
第二周星期五3~4第二周星期三3~4
授课班级:
11秋机511秋机7
课时:
2
课题:
刀具切削部分的几何角度
教学目的:
理解刀具的组成、辅助平面,掌握车刀的主要角度,理解车刀的工作角度。
教学重点:
车刀的几何角度和工作角度
教学难点:
车刀的工作角度
教学方法:
讲授与师生互动相结合
教具:
教学过程:
第二节刀具切削部分的几何角度
一、刀具切削部分的组成
如图所示为普通外圆车刀,由刀体和刀柄两部分。
刀体用于切削,刀柄用于装夹。
刀具切削部分一般由三个面、两个切削刃和一个刀尖组成。
1.三个表面
前面(前刀面)Aγ:
刀具上切屑流过的表面称为刀具的前面。
后面(主后刀面)Aα:
刀具上与过渡表面相对的表面称为刀具的后面。
副后面(副后刀面)A´α:
刀具上与已加工表面相对的表面称为刀具的副后面。
2.两个切削刃
主切削刃S:
前面和后面的交线为主切削刃。
副切削刃S´:
前面和副后面的交线为副切削刃。
3.刀尖:
主切削刃和副切削刃的交点。
刀尖实际上是一段短直线或圆弧。
不同类型的刀具,其刀面、切削刃的数量不完全相同。
二、刀具静止参考系
(1)基面pr过主切削刃选定点平行或垂直于刀具上的安装面(轴线)的平面,车刀的基面可理解为平行刀具底面的平面。
(2)切削平面ps过主切削刃选定点与主切削刃相切并垂直于基面的平面。
(3)正交平面po过主切削刃选定点同时垂直于基面与切削平面的平面。
上述三个平面在空间是相互垂直的。
三、车刀的几何角度
1.在正交平面po内测量的角度
(1)前角γo前面与基面在正交平面内测量的夹角。
(2)后角αo后面与切削平面在正交平面内的投影之间的夹角。
(3)楔角βo前刀面与后面在正交平面内的投影之间的夹角。
2.在基面内测量的角度
(1)主偏角kr主切削刃在基面上的投影与进给运动方向的夹角。
主偏角一般为正值。
(2)副偏角k′r副切削刃在基面上的投影与进给运动反方向的夹角。
副偏角一般为正值。
(3)刀尖角εr主、副切削刃在基面内的投影之间的夹角。
3.在切削平面内测量的角度
刃倾角λs:
在切削平面中测量的主切削刃与基面间的夹角。
四、车刀的几何角度
1.在正交平面Po内测定的角度
(1)前角γo前面与基面在正交平面内的投影之间的夹角。
(2)后脚αo主后面与切削平面在正交平面内的投影之间的夹角。
(3)契交βo前面与主后面在正交平面内的投影之间的夹角。
注:
γo+αo+βo=90°在基面Pr内测量的角度
(1)主偏角Kr主切削刃在基面内的投影与进给运动方向之间的夹角.
(2)副偏角Kr′副切削刃在基面内的投影与进给运动反方向之间的夹角.
(3)刀尖角εr主、副刃在基面内的投影之间的夹角。
注:
εr+Kr+Kr′=180°
(4)在切削平面内测量的角度
刃倾交λs主切削刃和基面在切削平面内的投影之间的夹角。
当刀尖为主切削刃的最低点时刃倾角为负;当刀尖为最高点时刃倾角为正;当主切削刃为水平时刃倾角为零。
五、车刀的工作角度
1.车刀的工作角度
车刀工作时,由于工作条件与理想条件不符,其实际角度不等于标注角度,这种变化了的角度称为实际工作角度。
2.车刀安装情况对工作角度的影响
(1)安装高度对工作角度的影响:
a.刀尖高与工件轴线:
工作前角γoe增大,工作后角αoe减小。
b.刀尖低与工件轴线:
工作前角γoe减小,工作后角αoe增大.
(2)刀柄偏斜对工作角度的影响:
a.刀柄右偏:
主偏角Kr增大,副偏角Kr′减小。
B.刀柄左偏:
主偏角Kr减小,副偏角Kr′增大。
授课时间:
第三周星期三1~2第三周星期二3~4
授课班级:
11秋机511秋机7
课时:
2
章节及课题:
刀具材料
教学目的:
熟悉车刀主要角度、了解刀具角度与切削加工的关系。
熟悉熟悉刀具材料的性能和种类
教学重点、难点:
刀具材料的性能和种类
教学方法:
讲授法、师生交流法
教学过程:
第三节刀具材料
1.刀具材料应具备的性能
(1)高的硬度
(2)足够的强度和韧性(3)高的耐磨性
(4)高的耐热性(5)良好的工艺性能
2.常用刀具材料的种类
(1)高速钢又称锋钢、白钢,硬度可达62~67HRC,在550~600℃时仍能保持常温下的硬度和耐磨性,有较高的抗弯强度和冲击韧度,并易磨出锋利的切削刃。
因此,特别适宜制造形状复杂的切削刀具,如钻头、丝锥、铣刀、拉刀、齿轮滚刀等刀具,其允许切削速度一般为vc<30m/min。
(2)硬质合金硬质合金具有高耐磨性和高耐热性,硬度可达74~82HRC,能耐850~1000℃的高温,允许使用的切削速度可达100~300m/min,因此得到广泛的应用。
但硬质合金抗弯强度低,冲击韧性差,一般制成各种形状的刀片焊接或夹固在刀体上,使用中很少制成整体刀具。
用于制作切削刀具的材料还有陶瓷、人造金刚石、立方氮化硼、稀土硬质合金。
授课时间:
第三周星期五3~4第三周星期三3~4
授课班级:
11秋机511秋机7
课时:
2
章节及课题:
金属切削过程中的物理现象及控制
教学目的:
1.了解积屑瘤对切削加工的影响及如何控制
2.了解切削力、切削热对切削过程的影响
3.了解刀具磨损的形式及刀具耐用度、刀具寿命
教学重点、难点:
切屑的形成过程、切削力、刀具磨损
教学方法:
讲授法、师生交流法
教学过程:
第四节金属切削过程中的物理现象及控制
(一)
一、切屑的形成及切屑类型
1.切屑的形成
切削时,在刀具切削刃的切割和前刀面的推挤作用下,使被切削的金属层产生变形、剪切滑移的过程称为切削过程,也是切屑形成的过程。
2.切屑的类型
(1)带状切屑
(2)挤裂切屑(3)单元切屑(4)崩碎切屑
二、积屑瘤
用中等切削速度切削钢料或其他塑性金属时,有时在车刀前刀面的近切削刃处,牢固地粘着一小块金属,这就是积屑瘤。
1.积屑瘤的形成
2.积屑瘤对加工的影响
(1)保护刀具
(2)增大实际前角
(3)影响工件表面质量和尺寸精度
3.切削速度对积屑瘤产生的影响
三、切削力
1.总切削力的分解
(1)主切削力FC是切削合力沿主运动方向的分力,垂直于基面,又称切向力。
(2)进给力Ff是切削合力沿进给运动方向上的分力,在基面内,与进给方向即工件轴线方向平行,故又称进给抗力或轴向力。
(3)背向力FP是切削合力沿工作平面垂直方向上的分力,在基面内,与进给方向垂直,即通过工件直径方向,故又称径向力或吃刀抗力。
2.影响切削力的因素
(1)工件材料是影响切削力的主要因素
(2)刀具角度
(3)切削用量
四、切削热
1.切削热的来源和传散
在切削过程中,由于金属的弹性、塑性变形以及摩擦产生的热,称为切削热。
切削热通过切屑、工件、刀具和周围介质传散。
一般情况下切屑带走的热量最多。
2.影响切削热的主要因素
凡是能增大切削力的因素,都使切削热增多;凡是能减小切削力的因素,都使切削热减少。
另外,材料的导热性好,有利于降低切削温度。
五、刀具磨损
1.刀具磨损的形式
(1)前面磨损
(2)后面磨损
(3)前、后面磨损
2.刀具耐用度与寿命
刀具两次刃磨之间实际进行切削的总时间,称为刀具耐用度,用符号T表示,单位是min。
刀具寿命是指一把新刀从投入切削起,到报废为止实际切削总时间,其中包括该刀具的多次重磨。
影响刀具耐用度的关键因素是切削用量中的切削速度。
[课堂小结]
1.刀具材料应具备的性能,常用的刀具材料种类
2.切屑的形成及切屑类型,积屑瘤形成及对加工的影响
3.影响切削力的因素
4.切削热的来源和传散及影响切削热的主要因素
5.刀具磨损的形式及刀具的使用寿命
授课时间:
第四周星期三1~2第七周星期二3~4
授课班级:
11秋机511秋机7
课时:
2
章节及课题:
金属切削过程中的物理现象及控制
教学目的:
熟悉提高切削效率的几种途径
教学重点、难点:
1.刀具角度的合理选择
2.切削用量的选择原则
教学方法:
讲授法、师生交流法
教学过程:
第五节金属切削过程中的物理现象及控制
(二)
一、提高工艺系统的刚度
工艺系统
工艺系统必须有足够的刚度。
[举例]车削轴类零件时用的中心架、跟刀架;机床上粗而短的主轴;粗而短的外圆车刀刀杆等。
二、合理选用刀具角度
1.前角γo的选择
选用前角的原则是在满足强度要求的前提下选用较大前角。
例如,切削正火状态的45钢,前角一般选γo=15º~2Oº;切削经淬火的45钢,硬度大大提高,要求足够的刃口强度,常选前角γo=-5º~-15º。
2.后角αo的选择
粗加工时,刀具所承受的切削力较大并伴有冲击,为保证刃口强度,后角应选小一些。
精加工时,切削力较小,切削过程平稳,为减少摩擦,后角应稍大一些。
例如,45钢工件粗车时,后角选αo=4º~6º;精车时后角选αo=6º~8º。
3.主偏角kr的选择
主偏角的大小影响刀尖的强度、散热条件、背向力的大小等。
当工艺系统刚度好时,应选用较小的主偏角。
当工艺系统刚度差时,应选用较大的主偏角。
4.副偏角k′r的选择
副偏角的主要作用是减小副切削刃与已加工表面的摩擦。
外圆车刀的副偏角常取k′r=6º~10º。
粗加工时,可取得大一些;精加工时可取得小一些。
5.刃倾角λs的选择
刃倾角影响刀尖强度,并控制切屑流动的方向。
负的刃倾角使切屑流向已加工表面,正的刃倾角使切屑流向待加工表面,刃倾角为零时切屑沿垂直切削刃的方向流出。
粗车一般钢料和灰铸铁时,常取λs=0º~-5º,以提高刀尖强度;精车时常取λs=0º~+5º,以防止切屑划伤已加工表面。
三、合理选用切削用量
基本原则:
1)根据工件加工余量和粗、精加工要求,选定背吃刀量。
2)根据加工工艺系统允许的切削力,其中包括机床进给系统、工件刚度及精加工时表面粗糙度要求,确定进给量。
3)根据刀具耐用度,确定切削速度。
4)所选定的切削用量应该是机床功率允许的。
四、使用切削液
切削液具有冷却、润滑、清洗和防锈的作用。
常用切削液有如下三种:
(1)水溶液主要成分是水,并加入防腐剂等添加剂,冷却性能好,润滑性能差。
(2)乳化液用乳化剂稀释而成,具有良好的流动性和冷却作用,也有一定的润滑作用,应用广泛。
低浓度乳化液用于粗车和磨削;高浓度乳化液用于精车、钻孔和铣削。
(3)切削油主要是矿物油,少量采用动、植物油或混合油,它的润滑性能好,但冷却性能差。
其主要作用是减少刀具磨损和降低工件表面粗糙度值。
主要用于齿轮加工、铣削加工和攻螺纹。
7.4.5改善工件材料的加工性
1.工件材料的切削加工性
工件材料的切削加工性,是指在一定的生产条件下材料被加工的难易程度。
切削加工性是一个综合评定指标,很难用一个简单的物理量来表示。
2.改善工件材料切削加工性的方法
金属材料的硬度为170~230HBW时,切削加工性较好。
因此常通过热处理工艺调整材料的硬度,以改善其切削加工性。
例如,对低碳钢进行正火处理,对高碳钢进行球化退火,对铸铁件中局部白口组织进行石墨化退火等。
[课堂小结]
1.提高切削效益的途径
2.刀具角度对切削效益的影响
3.切削用量对切削效益的影响
4.润滑液对切削效益的影响
授课时间:
第四周星期五3~4第七周星期三3~4
授课班级:
11秋机511秋机7
课时:
2
课题:
工件的定位
教学目的:
熟悉夹具的作用和组成,掌握六点定位原理及应用。
教学重点:
六点定位原理及应用。
教学难点:
六点定位原理及应用。
教学方法:
讲授与师生互动相结合
教具:
教学过程:
第六节工件的定位
(一)
一、机床夹具概述:
1、夹具在机械加工中的作用:
.
2、机床夹具的分类:
3、机床夹具的组成:
1)定位元件:
夹具上与工件直接接触,并用以确定工件正确位置的零件。
2)夹紧装置:
包含夹紧机构和动力源。
其功能是夹紧工件,使其保持正确位置,以防外力作用而产生位移或振动。
3)夹具体:
是夹具的基础件。
4)导向元件和对刀元件。
5)其它元件和装置。
二)工件的定位原理:
1、六点定位规则:
夹具利用合理分布的六个支承点来限制工件和六个自由度,使工件在夹具中的位置完全确定。
2、六点定位规则的应用:
1)应限制的自由度的确定:
能影响加工精度的自由度即为需要限制的自由度。
2)定位方式:
(1)完全定位:
工件的六个自由度均被限制。
(2)不完全定位:
只限制影响加工精度的自由度,而对不影响加工精度的自由度不加以限制。
是一种合理的定位方式。
(3)欠定位:
对影响加工精度的自由度没有完全限制。
决不允许出现。
(4)重复定位:
由多个定位支承点重复限制同一个自由度的现象。
其是否可行,需视具体情况而定。
授课时间:
第五周星期三1~2第八周星期二3~4
授课班级:
11秋机511秋机7
课时:
2
课题:
工件的定位
教学目的:
了解工件常用的定位方式、常用的定位元件及应用场合,能初步分析定位元件所限制的自由度。
教学重点:
用的定位元件及应用场合,常用定位元件所限制的自由度。
教学难点:
常用定位元件所限制的自由度。
教学方法:
讲授与师生互动相结合
教具:
教学过程:
第七节工件的定位
(二)
常见定位方式及定位元件
一)工件以平面定位
1、主要支承:
用来限制工件的自由度,起定位作用的支承。
常用的有固定支承、可调支承、自位支承。
1)固定支承:
支承钉和支承板两种。
图3-61.
2)可调支承:
用于工件定位过程中支承钉的高度需要调整的场合。
图3-62.
3)自位支承:
在工件定位过程中能自动调整位置的支承,只限制一个自由度,用于以工件粗基准定位或刚性不足的场合。
图3-63.
2、辅助支承:
只用来提高工件的装夹刚度和稳定性,不起定位作用。
图3-64.
二)工件以园孔定位
1、定位销:
1)园柱销:
图3-65.长销:
限制四个自由度;短销:
限制三个自由度。
2)圆锥销:
图3-66.单圆锥销:
限制两个自由度;双圆锥销:
限制五个自由度。
2、定位心轴:
1)圆柱心轴:
图3-67a、b):
有间隙配合和过盈配合两种,主要用于车、铣、刨、磨、齿轮加工等机床上加工套筒和盘类零件。
2)圆锥心轴:
图3-67c):
定位精度高,适于工件定位精度不低于IT7的精车和磨削加工,但不能加工端面。
三)工件以外园柱面定位
常用定位元件:
V型块、套筒、半圆孔
1、V型块:
图3-68.对中性好,安装方便。
2、定位套:
图3-69.常与端面联合定位,定位精度不高,只适用于精基准。
四)常用定位元件所限制的自由度
详见P74表3-12.
授课时间:
第五周星期五3~4第八周星期二3~4
授课班级:
11秋机511秋机7
课时:
2
课题:
工件的夹紧
教学目的:
了解夹紧装置的组成和要求,掌握夹紧力方向、位置的确定原则。
教学重点:
夹紧力方向、位置的确定原则。
教学难点:
夹紧力方向、位置的确定原则。
教学方法:
讲授与师生互动相结合
教具:
教学过程:
第八节工件的夹紧
一、工件的夹紧
(一)夹紧装置的组成和基本要求
夹紧装置:
工件在夹具中定位后,用来产生夹紧力使工件固定,并保持准确的定位位置的机构。
1、夹紧装置的组成:
力源装置、中间传动机构、夹紧元件。
2、对夹紧装置的基本要求:
1)夹紧过程可靠。
2)夹紧力大小适当。
3)结构性好4)使用性好。
(二)夹紧力的确定
包括夹紧力的大小、方向、作用点。
1、夹紧力作用点的确定:
1)夹紧力作用点必须作用在定位元件的支承表面上或作用在几个定位元件所形成的稳定受力区域内。
图3-71.
2)夹紧力作用点应作用在工件刚性较好的部位。
图3-72.
3)夹紧力的作用点应适当靠近加工表面。
图3-73.
2、夹紧力方向的确定:
1)夹紧力的作用方向不应破坏工件的定位,工件在夹紧力的作用下要确保其定位基面紧贴在定位元件的工作表面上,为此,要求主夹紧力的方向应指向主要定位基准面。
图3-74.
2)夹紧力方向应使工件的夹紧变形小。
图3-75.
3)夹紧力方向应使所需夹紧力尽量小。
图3-76.
3、夹紧力大小的确定:
(略)
二、几种常用夹紧机构
一)斜楔夹紧机构:
图3-77.
1、夹紧力的计算:
Fj=Fq/「tanφ1+tan(φ2+α)」
2、自所条件:
α≤(φ1+φ2)α=6°~8°
二)螺旋夹紧机构
1、单个夹紧机构:
图3-78.
2、螺旋压板机构:
图3-80.
三)偏心夹紧机构:
图3-81
四)联动夹紧机构
1、多点夹紧机构:
图3-82
2、多件夹紧机构:
图3-81.
五)定心夹紧机构:
图3-84.
授课时间:
第六周星期三1~2第八周星期三3~4
授课班级:
11秋机511秋机7
课时:
2
课题:
数控车削加工
教学目的:
了解数控车削加工方法。
掌握车削加工工件装夹。
数控车床切削用量的选择。
教学重点:
车削加工工件装夹。
教学难点:
车削加工工件装夹。
教学方法:
讲授与师生互动相结合
教具:
教学过程:
第二章数控切削加工方法
第一节数控车削加工
数控车削是数控加工中用得最多的加工方法之一。
由于数控车床具有加工精度高、具有直线和圆弧插补功能以及在加工过程中能自动变速等特点,因此其加工范围比普通车床宽得多。
凡是能在数控车床上装夹的回转体零件都能在数控车床上加工。
与普通车床相