14华能沁北电厂国产超临界600MW机组启动实绩77.docx
《14华能沁北电厂国产超临界600MW机组启动实绩77.docx》由会员分享,可在线阅读,更多相关《14华能沁北电厂国产超临界600MW机组启动实绩77.docx(14页珍藏版)》请在冰豆网上搜索。
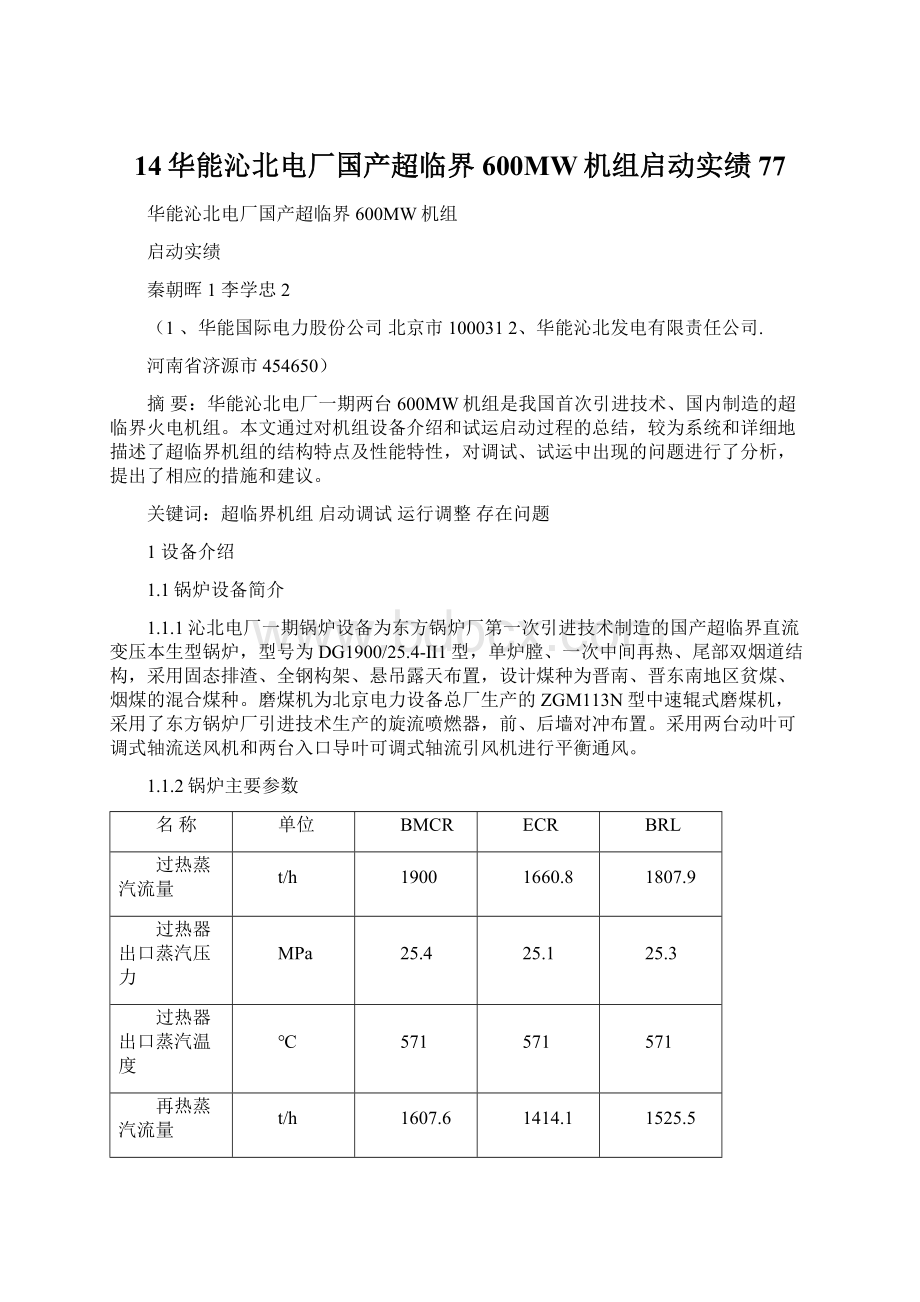
14华能沁北电厂国产超临界600MW机组启动实绩77
华能沁北电厂国产超临界600MW机组
启动实绩
秦朝晖1李学忠2
(1、华能国际电力股份公司北京市1000312、华能沁北发电有限责任公司.
河南省济源市454650)
摘要:
华能沁北电厂一期两台600MW机组是我国首次引进技术、国内制造的超临界火电机组。
本文通过对机组设备介绍和试运启动过程的总结,较为系统和详细地描述了超临界机组的结构特点及性能特性,对调试、试运中出现的问题进行了分析,提出了相应的措施和建议。
关键词:
超临界机组启动调试运行调整存在问题
1设备介绍
1.1锅炉设备简介
1.1.1沁北电厂一期锅炉设备为东方锅炉厂第一次引进技术制造的国产超临界直流变压本生型锅炉,型号为DG1900/25.4-Ⅱ1型,单炉膛、一次中间再热、尾部双烟道结构,采用固态排渣、全钢构架、悬吊露天布置,设计煤种为晋南、晋东南地区贫煤、烟煤的混合煤种。
磨煤机为北京电力设备总厂生产的ZGM113N型中速辊式磨煤机,采用了东方锅炉厂引进技术生产的旋流喷燃器,前、后墙对冲布置。
采用两台动叶可调式轴流送风机和两台入口导叶可调式轴流引风机进行平衡通风。
1.1.2锅炉主要参数
名称
单位
BMCR
ECR
BRL
过热蒸汽流量
t/h
1900
1660.8
1807.9
过热器出口蒸汽压力
MPa
25.4
25.1
25.3
过热器出口蒸汽温度
℃
571
571
571
再热蒸汽流量
t/h
1607.6
1414.1
1525.5
再热器进口蒸汽压力
MPa
4.71
4.15
4.47
再热器出口蒸汽压力
MPa
4.52
3.98
4.29
再热器进口蒸汽温度
℃
322
307
316
再热器出口蒸汽温度
℃
569
569
569
省煤器进口给水温度
℃
284
275
280
1.2汽机设备简介
1.2.1汽轮机由哈尔滨汽轮机厂与日本三菱公司联合设计生产,是国产首台超临界汽轮机,高、中压缸采用三菱公司的成熟设计,低压缸以哈汽成熟的600MW机组积木块为母型,与三菱公司一起进行改进设计,使之适应三菱公司的1029mm末级叶片。
1.2.2汽机旁路系统由高压旁路和低压旁路组成两级旁路系统,以满足机组冷态、温态、热态、极热态快速启动的要求。
给水系统配置两台汽动给水泵和一台电动给水泵,电动给水泵的前置泵由主泵同轴驱动,两台汽泵的前置泵采用分置式。
1.2.3汽轮机技术规范
名称
参数
汽轮机型式
超临界、一次中间再热、
三缸四排汽、单轴、凝汽式
连续出力KW
600,000
主蒸汽压力MPa
24.1
主蒸汽温度℃
566
再热蒸汽温度℃
566
回热级数
8级
调节控制系统型式
DEH
通流级数
44
末级动叶片长度mm
1029
盘车转速r/min
3.35
1.3电气设备简介
1.3.1发电机为哈尔滨电机厂有限责任公司制造的QFSN-600-2YHG型三相交流隐极式同步汽轮发电机,冷却方式采用水-氢-氢。
1.3.2发电机主要技术参数
名称
单位
数据
额定容量
MVA
667
额定功率
MW
600
最大连续功率
MW
654
额定功率因数
COSΦ
0.9(滞后)
额定定子电压
V
20000
额定定子电流
A
19245
额定励磁电压
V
421.8
额定励磁电流
A
4128
额定氢压
Mpa
0.4
励磁方式
静止励磁
绝缘等级
F
1.3.3采用ABB公司UNITROL5000型励磁系统,型号为Q5S-0/U251-S6000,正常运行期间,由机端电压经励磁变供电,启动期间,由220V直流系统的起励装置供电,建立10%额定定子电压后,可控硅桥投入工作。
励磁调节器为双自动通道加独立的备用控制器(EGC)控制。
1.4控制系统简介
1.4.1机组DCS采用ABB-贝利控制有限责任公司提供的Symphony系统,包括数据采集、模拟量控制、顺序控制、锅炉炉膛安全监控、电气控制、汽机DEH、汽动给水泵组MEH等子系统。
1.4.2辅助控制系统的主要功能是将水源地、综合水泵房、化学处理站、除灰系统、电除尘系统、灰渣系统、输煤系统等外围控制PLC通过冗余的100M工业以太网进行组网通信控制,实现集控室对辅助系统的监视和控制功能。
1.4.3网络监控系统NCS主要完成变电站500KV和220KV系统的设备数据采集和处理、监视和报警功能。
NCS根据运行人员输入的命令实现断路器、隔离开关的正常操作,实现断路器同步鉴定、操作出口的跳合闸闭锁、并发性操作闭锁等功能,同时实现电量统计、控制系统时钟同步、调度远动信息传送、系统在线自诊断等管理功能。
2机组启动准备工作
2.1分步试运工作回顾
2004年5月2日220KV高备变反送电成功,在#1机组6KV厂用电受电后,现场具备了分步试运条件。
在指挥部的统一领导下,严格根据节点要求,制定了详细的设备试运计划,明确了完成时间和责任人,生产人员全过程地参与设备试运工作,严格把好试运质量关。
针对超临界锅炉对汽水品质的高标准,试运指挥部就机组碱洗和酸洗的范围与措施进行了反复认真的讨论,确定了锅炉和机组凝结水系统、加热器进行碱洗,以及锅炉本体水冷壁和凝结水主管道进行酸洗的方案,收到了良好的化学清洗效果;确定了稳压和变压相结合的吹管方式:
变压吹管时,当主汽压力达到6.5Mpa时,开启临冲门,锅炉给水流量维持在475t/h,当压力降到2.0MPa时,关闭临冲门。
稳压吹管时,主汽压力维持在5Mpa,锅炉给水流量控制在600t/h。
实践证明,采用稳压与变压相结合的吹管方式,可达到满意的效果。
锅炉吹管的完成,标志着锅炉本体和辅机、汽机凝结水和给水等系统通过了实际运行的初步考验,机组整套启动前的工作重点顺利转移至汽机DEH系统、发电机辅助系统、汽机安全监控系统的调试工作。
2.2热控调试工作回顾
电厂组织检修和运行人员参与DCS系统组态设计、保护审核等工作的全过程,多次召开有关专题会议,优化热机工艺保护、联锁控制逻辑,如针对超临界机组的特性,增设了锅炉汽水分离器入口温度高保护;发电机跳闸联跳锅炉保护增加了锅炉热负荷判断逻辑;对单一条件的保护,采取了防止误动的措施;取消了一些辅机的过保护项目等等。
电厂成立了机组工艺保护定值小组和机组工艺保护审核小组,对所有的工艺保护进行带设备实际传动试验,要求模拟量保护必须在就地加信号,开关量保护必须在试验位置拉合开关或就地短接信号,MFT保护出口要求软逻辑和硬逻辑分别进行试验。
经过调试单位、安装单位、生产单位的共同努力,沁北电厂机组试运期间未发生保护拒动和误动事故,成功避免了多次辅机误跳闸。
3运行调整要点及总结
3.1直流锅炉的水冲洗
直流锅炉由于受结构的制约,无法设置专门的排污系统。
如果进入系统的盐类和机械杂质超标,将会造成锅炉受热面内部腐蚀和管壁超温、导致汽轮机的状态参数恶化并降低运行效率,因此,直流锅炉必须对系统进行严格的冲洗,以置换系统中存留的品质超标的水和清除残留的机械杂质,并在热态冲洗的过程中进一步溶解并清除锅炉水冷壁内部沉积的盐类。
冲洗分为凝结水系统冲洗、冷态冲洗和热态冲洗三个阶段。
冲洗系统流程图
3.1.1凝结水系统冲洗方法和指标
在凝结水水质合格后(控制值:
YD=0μmol/L;Fe≤10μg/L;DD≤0.3μs/cm),启动凝结水泵向除氧器上水,开启除氧器至锅炉疏水扩容器排水门,除氧器水位控制投入自动,开始对凝结水系统和除氧器进行冲洗。
在除氧器排水水质合格后,关闭除氧器至锅炉疏水扩容器排水门,开启除氧器放水至凝汽器排放门,投入凝结水精处理,直至给水泵入口给水水质合格(Fe<100μg/L)。
3.1.2锅炉冷态冲洗方法和指标
开启启动分离器储水箱至锅炉疏水箱排放门,关闭至凝汽器回收门,锅炉上水至启动分离器储水箱水位达12米后,保持给水流量475t/h(锅炉BMCR给水流量的25%),进行冷态冲洗。
分离器排水水质达到Fe<500μg/L后,开启分离器排水至凝汽器回收门,对锅炉冲洗排水进行回收,利用凝结水精处理装置清理系统中的盐类,直至分离器排水水质合格(DD<1μs/cm,Fe<100μg/L)。
3.1.3热态冲洗的方法及控制指标
由于在水温190℃时,水对盐类的溶解度最大,因此,在启动分离器入口温度达到190℃时,停止升温,安排进行热态冲洗,可收到理想的效果。
该温度主要由燃油流量进行控制,同时,辅以高旁调节,保持高旁前压力在1.25Mpa(190℃所对应的饱和压力),维持该压力即能保证理想的热态冲洗温度。
在分离器储水罐排水合格后(Fe≤50μg/L),热态冲洗结束。
3.2燃油阶段的燃烧调整
3.2.1解决点火油枪堵塞问题
在燃油运行初期,由于频繁发生油枪堵塞,造成雾化不良,甚至灭火,干扰了调试进程。
经过分析查找,确认了造成油枪堵塞的主要原因:
燃油管道安装结束后,蒸汽吹扫动量系数不够,管道内有残存杂物,加之点火油枪设计出力较小,雾化槽偏浅,遂导致油枪堵塞。
为解决该问题,在点火油枪前增设了滤网,由于滤网难以捕捉到细小的颗粒,收效不甚明显。
为此,电厂加强了就地巡查,一旦发现油枪有堵塞迹象,立即组织人员进行清洗,经过一段时间的反复清理,逐渐清除了残存杂质,消除了油枪堵塞现象。
3.2.2改善启动油枪的燃烧工况
原设计仅考虑启动油枪在启动期间短期使用,为简化系统,启动油枪安装在煤粉燃烧器中心,没有单独设置油枪配风(见燃烧器结构简图),同时,原设计采用12支启动油枪运行满足机组的启动要求,但考虑启动油枪的不对称运行对螺旋水冷壁热偏差的影响,将设计变更为最多8支启动油枪运行满足机组启动的要求,同时将单支油枪额定出力由原来的3.2t/h增大为4.7t/h,以满足热负荷的需要。
启动油枪的额定出力增大后,配风系统难以作相应的变更,造成油枪运行中根部补风不足,部分油雾裂化成难以燃烧的碳黑,形成黑烟。
针对上述情况,电厂采取了以下措施:
1、在点火燃油期间,将炉膛负压增大为-500Pa,增大冷却风量来强化油枪根部补风。
2、在点火的初始阶段,降低单支油枪的出力,缓解油枪对根部风量的需求。
3、维持雾化蒸汽与燃油的适当压差并尽量提高蒸汽温度。
通过上述调整,明显改善了启动油枪的燃烧情况。
燃烧器结构简图
3.2.3燃油阶段的热偏差问题
在吹管期间,当所有的启动油枪均投入(前墙中层和下层、后墙中层)时,螺旋水冷壁出口的最高金属温度偏差超过60℃,当只运行中间层油枪时,该温度偏差不超过5℃,此现象说明启动油枪的运行方式对螺旋水冷壁的受热状况有很大的影响。
油枪燃烧时,火焰行程短,热负荷集中,燃烧区域对受热面的传热强烈。
由下图可以看出,由于部分螺旋水冷壁管同时穿过前墙中层和下层启动油枪区域,该部分螺旋水冷壁管的受热强度远大于其他螺旋水冷壁管,所以在油枪投入不对称时,会造成螺旋水冷壁出口温度偏差明显增大的现象。
为此,电厂采取了相应的措施:
在锅炉点火时,全部投用中间层油枪,下层油枪作为故障备用,当需要增加热负荷时,则通过提升供油压力实现。
经过油枪运行方式的调整,螺旋水冷壁出口温度偏差可控制在5℃以内。
启动油枪对螺旋水冷壁受热状况的影响示意
3.3汽机冲车参数的确定
哈尔滨汽轮机厂提供的冷态冲车参数为:
主汽8.92MPa/360℃、再热汽1.0MPa/320℃。
依此规定,主汽过热度仅有58℃,加之高压主汽门冲车时存在一定的节流温降,选择该参数冲车,暖机效果难以得到保证,同时,在相同燃料量的情况下,降低主汽压力有利于对主汽温度的控制。
经研究,修改了#1机第一次启动的冲车参数:
主汽压力4.98/5.01MPa、主汽温度400℃;再热汽压力0.90MPa、再热汽温度389.9℃。
但实际暖机过程中,调节级温度仅升至85.3℃,未能达到预期的暖机效果。
经与汽轮机厂家共同探讨,认为单降主汽压力而未降再热汽压力,造成了高、中压缸进汽量不匹配,高压缸进汽量偏少是产生此次调节级升温缓慢的主要原因,为此,进一步对冲车参数控制曲线进行了修改,取得了满意的效果。
最终确定的冷态冲车控制曲线
3.4汽机冲转、暖机的要点
沁北电厂汽轮机采用高中压缸联合启动的方式,中调门自动按高调门的设定曲线开启,因此,冲车参数的选择即决定了高、中压缸进汽量的分配,若主、再热蒸汽参数匹配失当,将会导致进汽量的不平衡。
在比较高主门冲车和高调门冲车两种方式下节流温降的变化情况后,电厂采用了节流温降较小的高压主汽门冲车方式,在转速达2900rpm后,再切换至高调门的冲转。
汽轮机冲车过程中,高压缸排汽逆止门因旁路投入而保持关闭状态,为避免因高压缸鼓风摩擦而导致的高排温度过高,在高压缸排汽逆止门前设有启动排放阀(通风阀),其排汽进入凝汽器。
该阀在汽机复置后开启,发电机并网后关闭。
利用启动排放阀开度变化可调节高压缸内蒸汽的流通状况,同时,调节低旁压力以配合调整汽机高压缸的进汽量,可以有效地控制汽机调节级的温升率,通过以上手段,中速暖机可以达到理想的效果。
3.5煤粉燃烧器及燃烧调整
3.5.1煤粉燃烧器的特点
沁北电厂设计煤种和校核煤种具有中等结渣倾向,着火稳定性、燃烬特性较差,灰渣具有中等粘污性质。
炉膛设计和燃烧调整中既要充分考虑煤粉的着火、燃烧的稳定、高效,同时也要具备对煤种变化的适应能力并满足防止炉内结渣和水冷壁高温腐蚀、低NOX排放、低负荷稳燃等方面要求。
本锅炉采用的炉膛容积热负荷为91kW/m3,截面热负荷为5.1MW/m2,采用了日立HT-NR3燃烧器对冲布置方式,将24只高效低NOX旋流燃烧器分3层布置在前后墙上,在燃烧器上方设置了8支主燃烬风喷口和4支侧燃烬风喷口。
燃烧器的布置
本燃烧器综合了煤粉浓缩技术、钝角燃烧理论及焰内分解技术,基本满足了煤粉着火稳定性和低NOX的要求。
煤粉气流经过燃烧器内部的煤粉浓缩器分离后,在燃烧器喷口出口处形成外圈浓内圈稀的煤粉气流,在燃烧器出口稳燃环和稳燃齿形成的局部负压下卷吸高温烟气,迅速着火燃烧。
通过控制二次风量来维持煤粉燃烧器区域的过量空气系数在0.75-0.9,可使燃烧器区域存在较强的还原气氛,加快烟气中NOX的分解,最大限度地降低初级燃烧中NOX的生成。
未燃烬的可燃物进入燃烬风喷口区域,在旋流和直流相结合的双流式燃烬喷口送风的强烈扰动下,未燃烬的可燃物高效燃烧,可有效降低飞灰可燃物含量。
3.5.2燃烧调整情况
电厂设计燃用煤种为晋南、晋东南地区的烟煤和贫煤的混合煤种,校核1和校核2燃料的挥发份在10.84-20.15%之间,低位发热量在26290-23100之间。
但实际运行中,大量燃用的是低位发热量21000KJ/Kg左右、挥发份16%左右的郑煤和部分低位发热量25000KJ/Kg左右、挥发份6.5%左右的晋城煤。
由于燃料偏离设计值,给锅炉燃烧带来了一系列的问题。
晋城煤可磨系数较低,中速辊式磨煤机对该煤种的适应性较差,磨煤机设计煤种的额定出力为56.8T/H,在磨制晋城煤时,通常仅能达到35t/h左右的出力,最差时只有25t/h。
喷燃器设计稳燃出力下限为30t/h,燃用晋城煤时,喷燃器基本工作在稳燃出力的下限附近,加之晋城煤的挥发份远低于设计值,造成了着火点偏远和不稳定的状况。
为解决晋城煤稳燃特性差的问题,电厂在磨煤机的运行方式上进行了调整,采用固定的一层中间燃烧器和一层上层燃烧器燃用晋城煤与其他燃烧器进行掺烧,同时,调整了燃烧器三次风挡板、燃烬风挡板开度,加强了旋流强度,提高了对高温烟气的卷吸,减弱喷燃器附近区域的冷却作用,通过以上措施,晋城煤的稳燃问题基本得到了解决。
3.5.3受热面结焦情况
由于实际燃用的煤种偏离设计,锅炉运行中存在一般性的结焦现象。
在炉膛侧墙35.6米处,发现有明显的结焦现象,焦渣为软化状态并易脱落。
该区域位于上层燃烧器和燃烬风喷口标高之间,烟气温度高于灰的软化温度,且未设置吹灰器,使在该区域结焦并形成大焦块成为可能。
停炉后,发现部分喷燃器区域也存在结焦迹象。
虽然结焦未对系统的运行参数造成直接影响,但掉焦形成的冲击对冷灰斗水封和捞渣机造成了一定程度的破坏。
在现有条件下,电厂通过加强炉膛吹灰和燃烧调整来减缓结焦速度,一方面,加强炉膛的蒸汽吹灰,及时清除初期结焦,同时,将停运喷燃器的二次风挡板开启至30%进行冷却,防止停运喷燃器喷口结焦,通过燃烧调整,尽可能降低结焦区域的炉膛温度并提高燃烧器区域的氧化氛围来达到减缓结焦的目的。
3.6水冷壁对变工况的适应性
3.6.1水冷壁特点介绍
沁北电厂锅炉采用全焊接膜式水冷壁,炉膛下部及冷灰斗均采用螺旋水冷壁,上部采用垂直水冷壁,中间由过渡水冷壁转换连接。
炉膛水冷壁总体布置见下图。
锅炉本体布置结构图
由于采用轻型炉膛,汽水分离器以下的水冷壁系统中没有过多的联箱等厚壁部件,因此系统的热惯性很小,同时,水冷壁管采用小管径和内螺纹管,并且下部水冷壁采用螺旋水冷壁,管道内部的绝对流速高,受热面的换热系数大,因此,沁北电厂的超临界锅炉水冷壁对变工况具有较强的适应性。
3.6.2螺旋水冷壁出口金属温度偏差
由于锅炉采用对冲燃烧系统,使得炉膛内温度场相对比较均匀,同时,下部水冷壁采用螺旋管绕炉膛1.72圈的方式,使得螺旋水冷壁的出口温度相对比较均匀,即使在磨煤机采用非对称运行的情况下,也能保证较小的偏差。
在600MW、500MW、400MW时,实测螺旋水冷壁出口金属温度偏差分别为14.9℃、18.5℃、34.7℃。
可以看出,随着负荷和压力的降低,螺旋水冷壁的出口温度偏差呈增大的趋势,这主要是受锅炉运行压力降低的影响。
当压力降低,特别是降至临界压力以下时,介质比容受温度变化的影响加大,因炉膛内热负荷不均匀而导致并列运行水冷壁管的热偏差敏感性增强,造成金属温度偏差增大。
3.6.3垂直水冷壁出口金属温度偏差
垂直水冷壁区域水冷壁的温升较螺旋水冷壁的温升相对较小,负荷600MW时,垂直水冷壁的温升为26℃,螺旋水冷壁的温升为82℃。
在600MW、500MW、400MW负荷时,垂直水冷壁出口的金属温度最大偏差分别为79.8℃、50.6℃、60.6℃。
垂直水冷壁在温升远小于螺旋水冷壁的情况下,形成较大的金属温差的原因在于介质的相变点在垂直水冷壁区域,由于垂直水冷壁区域液态和汽态两相流体的同时存在,使得该区域的热负荷偏差可形成较大的水冷壁管内介质平均比容偏差。
电厂曾对一根故障管进行堵管处理(将故障管在两头联箱处断开并将断口封堵),在随后的运行中,发现故障管两侧的垂直水冷壁管由于中间故障管失去冷却作用,出口金属温度较相邻垂直水冷壁管高出15-20℃,可见垂直水冷壁区域的受热面出口金属温度对热偏差、流量偏差都是极为敏感的。
3.7直流炉的中间点温度控制
直流锅炉的中间点温度是反映煤/水比平衡、实现锅炉主汽温度超前控制的重要参数。
直流锅炉本身对热负荷扰动的适应能力相对较差,不具有汽包锅炉的温度自稳定能力,选取一个合适的中间点温度以实现主汽温度的超前控制是直流锅炉控制的关键因素。
沁北电厂直流锅炉中间点选取在汽水分离器入口前的垂直水冷壁出口混合联箱上,该点是水冷壁和过热器的分界点,在转直流运行前,中间点温度是汽水分界点,转直流后中间点温度具有微过热度。
中间点温度若选择过于滞后,则会因系统的热惯性,超前反映煤/水比平衡破坏的作用减弱,进行煤/水比调节时,容易引起过调或调节振荡;中间点若选择过于靠前,则会因参数变化幅度小,造成较大的调节误差,同样容易引起过调和调节震荡,同时,为防止过热器进水,将中间点选在水冷壁和过热器的分界点,也有利于保证进入过热系统的蒸汽过热度。
控制中间温度具有超前调控的作用,但由于锅炉系统具有一定的热惯性,单纯靠超前的中间点温度来控制一次系统的温度,难以满足系统抗干扰的要求,沁北电厂采用了一、二级减温水配合中间点温度控制的方式,达到了精确、快速、稳定的效果。
3.8锅炉自动调节系统特点
3.8.1锅炉控制系统的测量信号
控制系统中重要测量信号设置三个测点,采用三取中值逻辑供调节系统使用。
当任意一个测点与中值比较异常超差、测点量程超限时将发出报警信号;当两个测点同时发生故障,延时5秒发出“测点坏质量”信号,相关自动控制强制手动。
测点信号正常后,必须人为复置故障信号,才能重新投入自动。
次要控制用测量信号设置两个,选择二取均值逻辑供调节系统使用,当任意一个测点故障将发出“测点坏质量”信号,相关自动控制强制手动。
当模拟量输出模件电流信号回路故障时(电流大于20mA或小于4mA),相应调节器控制强制手动,当调节器输出信号与反馈信号不一致时,将发出报警信号。
3.8.2给水流量控制的特点
超临界锅炉给水流量变化直接影响机组负荷的变化,影响到机组协调控制品质。
沁北电厂采用了水跟煤的控制方案,即燃料控制负荷、给水配合燃料、控制锅炉中间点温度。
给水控制方案的核心是中间点温度的控制,实际是对汽水分离器过热度的控制,水在亚临界压力下有饱和温度,在超临界压力下有相变点温度(27.5MPa压力下相变点温度409℃),在相变点区域,水的比容、焓值、比热有较大的幅度变化,压力越高变化幅度越小,在超临界压力下,按照对应的相变点温度计算过热度。
锅炉给水控制原理见下图:
锅炉主控输出对应的给水流量需求,并由汽水分离器入口温度微分修正作为前馈,加上汽水分离器入口温度设定值与实际值偏差的PID调节输出作为锅炉给水流量的设定值。
给水流量的设定值和省煤器入口流量偏差的PID调节输出作为给水泵公共指令。
由于锅炉燃烧原因,当汽水分离器入口温度在设计值内,但锅炉过热汽和再热蒸汽温度达不到设定值时,可以在DCS系统工程师站人为设置偏置。
4试运过程中存在的问题
4.1汽机轴瓦磨损
#1汽机在第一次整套启动后,发现#5、#6瓦在原顶轴油压下无法顶起,提高顶轴油压后,发现#5、#6瓦顶轴高度与上次测量值相比,发生了比较大的变化,翻瓦检查发现#3、#4、#5、#6瓦发生了不同程度的磨损。
在#2锅炉吹管后,发现#2汽机顶轴油压不正常变化,翻瓦检查发现#3、#4、#5、#6瓦也发生不同程度的磨损。
#1、#2机组带负荷试运后,停机翻瓦检查发现#6瓦下瓦面磨损。
分析轴瓦磨损的原因主要有以下两点
1、油管路冲洗不彻底,汽机润滑油颗粒度欠佳。
汽机油循环冲洗采用外接大流量冲洗设备进行滤油,由于油系统普遍采用套装油管道,回油管道的冲洗不够彻底,冷油器冲洗流速较低,冲洗效果较差。
此后,电厂增加了润滑油滤油设备,严格控制润滑油的颗粒度,采用油循环和机械清扫相结合的方法,确保每一根管路均得到充分冲洗、清理,不留死角。
通过大量细致的工作,至今未发生异常情况。
2、顶轴油泵启停时机不合理。
按照哈尔滨汽机厂要求:
汽机冲转转速达到600rpm时,停止顶轴油泵,惰走转速达到600rpm时,启动顶轴油泵。
经观察发现,在汽机停机惰走期间,轴瓦温度有明显变化的现象,综合分析认为:
汽机低转速运行期间,顶轴油泵不宜过早停运,同时,#6瓦设计承载较大,油膜形成不良,易造成轴瓦磨损。
经与汽机厂协商后,进行了更改:
冲转转速达1000rpm时,停运顶轴油泵;惰走转速达1200rpm时,启动顶轴油泵。
4.2汽机中压主汽门门轴断裂
2004年10月26日,进行#1汽机#1中压汽门活动实验时,发生机组MFT事件;在该机组168试运时,发现锅炉再热器压力偏高、汽机中压汽门前后压差偏大、中压缸效率偏低的现象;在168完成后,进行该汽机#1中压汽门活动实验时,在#1中压汽门关闭后,中压缸后抽汽压力骤降至零,机组负荷急剧下降,再热器压力上升,立即紧急打闸停机。
综合分析以上现象,确认该汽机#2中压主汽门未能正常打开。
解体后,发现该阀门门轴断裂,阀门保持在关闭状态。
此后,