库车球罐整体热处理方案.docx
《库车球罐整体热处理方案.docx》由会员分享,可在线阅读,更多相关《库车球罐整体热处理方案.docx(19页珍藏版)》请在冰豆网上搜索。
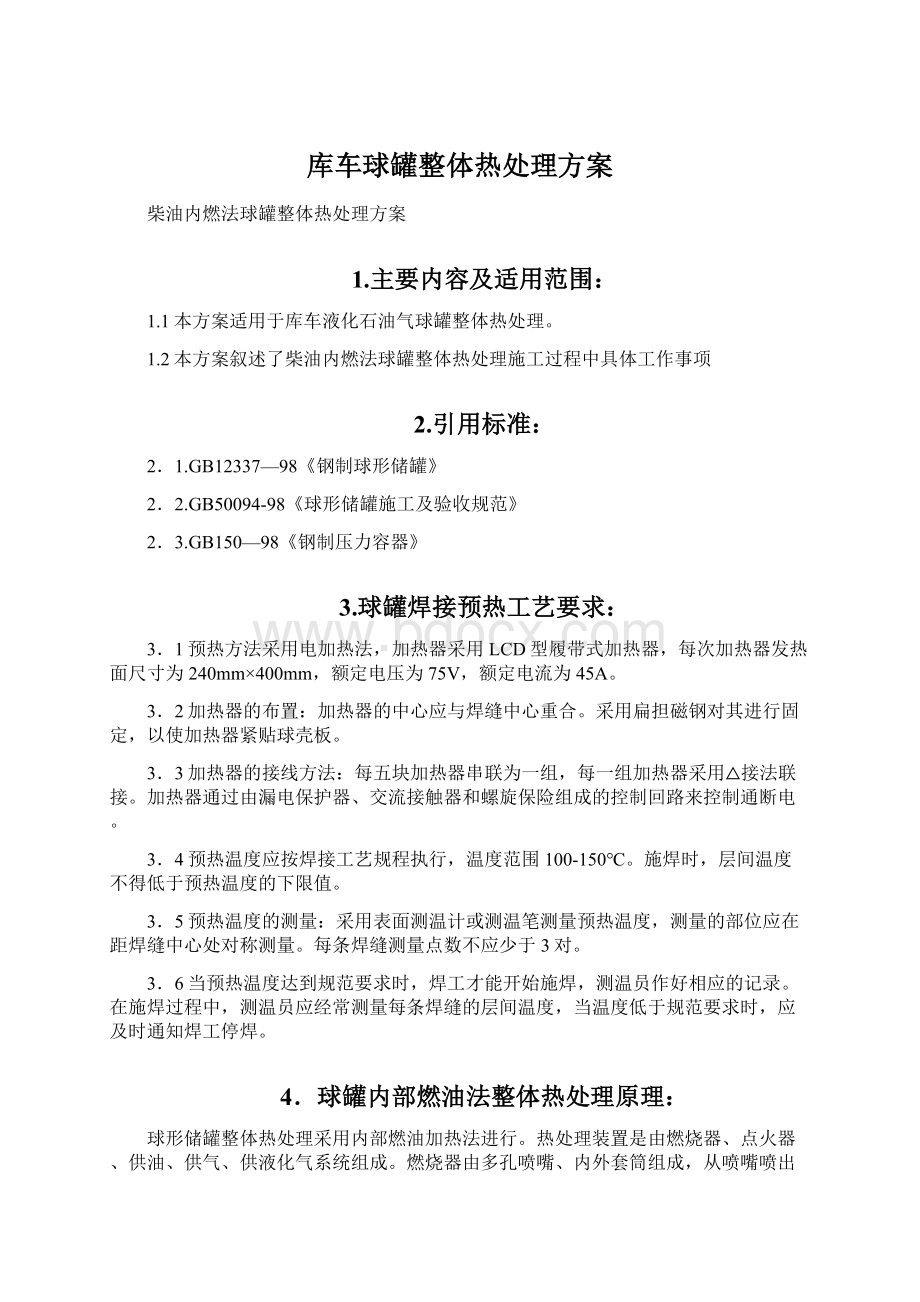
库车球罐整体热处理方案
柴油内燃法球罐整体热处理方案
1.主要内容及适用范围:
1.1本方案适用于库车液化石油气球罐整体热处理。
1.2本方案叙述了柴油内燃法球罐整体热处理施工过程中具体工作事项
2.引用标准:
2.1.GB12337—98《钢制球形储罐》
2.2.GB50094-98《球形储罐施工及验收规范》
2.3.GB150—98《钢制压力容器》
3.球罐焊接预热工艺要求:
3.1预热方法采用电加热法,加热器采用LCD型履带式加热器,每次加热器发热面尺寸为240mm×400mm,额定电压为75V,额定电流为45A。
3.2加热器的布置:
加热器的中心应与焊缝中心重合。
采用扁担磁钢对其进行固定,以使加热器紧贴球壳板。
3.3加热器的接线方法:
每五块加热器串联为一组,每一组加热器采用△接法联接。
加热器通过由漏电保护器、交流接触器和螺旋保险组成的控制回路来控制通断电。
3.4预热温度应按焊接工艺规程执行,温度范围100-150℃。
施焊时,层间温度不得低于预热温度的下限值。
3.5预热温度的测量:
采用表面测温计或测温笔测量预热温度,测量的部位应在距焊缝中心处对称测量。
每条焊缝测量点数不应少于3对。
3.6当预热温度达到规范要求时,焊工才能开始施焊,测温员作好相应的记录。
在施焊过程中,测温员应经常测量每条焊缝的层间温度,当温度低于规范要求时,应及时通知焊工停焊。
4.球罐内部燃油法整体热处理原理:
球形储罐整体热处理采用内部燃油加热法进行。
热处理装置是由燃烧器、点火器、供油、供气、供液化气系统组成。
燃烧器由多孔喷嘴、内外套筒组成,从喷嘴喷出的油已被压缩空气雾化,被点火器点燃,然后与内外套筒形成二、三次风相遇,使雾化的油充分燃烧,热气在罐内与罐壁的热交换靠辐射和对流两种方式进行。
燃烧火焰的长度、燃烧产物的流速可由风油比的调节来控制,适当地掌握火焰长度和燃烧产物的流速,可达到控制升温速度和调整上下温差的目的。
5.热处理工艺要求:
5.1热处理温度应符合设计图样要求。
当设计图样无要求时,常用钢材热处理温度可按下表的规定选用。
根据GB50094—98的规范的要求,常用钢材热处理温度如下:
钢号
热处理温度(℃)
20R
620±250C
16Mn
625±25
15MnVR
550—595
15MnVNR
565±15
07MnCrMoVR
565±20
5.2.热处理时,最少恒温时间应按最厚壳板对接焊逢的每25mm保温1h计算,且不少于1h。
5.3.加热时,在300℃及以下可不控制升温速度;在300℃以上,升温速度宜控制在50-80℃/h的范围内。
5.4.降温时,从热处理温度到300℃的降温速度宜控制在30-50℃/h范围内,300℃以下可在空气中冷却。
5.5.在300℃以上阶段,球壳表面上任意两测温点的温差不得大于130℃。
6.热工计算
6.1基本参数:
1000m3球罐为例,材质为20R
6.1.11000m3球罐有关设计数据如下表6-1:
名称
数量
名称
数值
球罐内径
12300mm
球壳
197.33吨
壳板最大厚度
48mm
球壳总重量
199吨
6.1.220R钢板在不同温度区间比热见下表6-2:
温度
100
200
300
400
500
600
导热系数KCal/Kg.0C
0.115
0.125
0.133
0.145
0.162
0.180
6.1.320R钢板导热系数见下表6-3:
温度
100
200
300
400
500
600
导热系数Kcal/kg.℃
43.92
41.04
37.8
34.02
30.96
28
6.1.4保温棉厚度按100mm计算。
6.1.5硅酸铝纤维毯导热系数见下表6-4:
温度
100
200
300
400
500
600
导热系数Kcal/kg.℃
0.025
0.04
0.055
0.07
0.085
0.1
6.1.6球体传热面积:
F球=4πR2=4×3.14×〔6.15〕2=475.0m2
6.1.7保温层的传热面积:
F=πD2=3.14×(12300+200)2=490.6m2
6.1.8柴油最低发热量:
Q底=9850Kcal/kg.℃
6.2计算过程:
…
6.2.1罐体加热至退火温度所需要的热量Q球
Q球=G×C×△T
式中:
G:
球体重量
C:
20R钢板的比热系数
△T:
温度差
球板升温所需热量计算结果见下表6-5:
温度区间
比热
计算公式
结果KCal
0-100
0.115
199000×0.115×100
2288500
100-200
0.125
199000×0.125×100
2487500
200-300
0.133
199000×0.133×100
2646700
300-400
0.145
199000×0.145×100
2885500
400-500
0.162
199000×0.162×100
3223800
500-600
0.180
199000×0.180×100
3582000
600-625
0.185
199000×0.185×25
920375
球体加热至退火温度所需的总热量:
Q球=2288500+2487500+2646700+2885500+3223800+3582000+920375=18034375(Kcal)
6.2.2加热时保温层所需的热量:
Kcal
保温层内壁取625℃,外壁取60℃。
计算温度取平均值=(625+60)/2=342.5℃
总的蓄热量:
Q=V×γ×c×t
式中V=保温层的体积
V=л/6(12.5003-12.3003)=48.28m3
γ=保温材料的比重取96KG/m3
C=保温材料的比热取0.25Kcal/kg.℃
Q被总=48.28×96×0.25×342.5=397026(Kcal)
6.2.3保温层向大气散热量
加热过程中部分的热量通过保温层散失到大气中去计算公式:
Q=(T1-T0)×F/(S1/λ1+S2/λ2+0.06)
T1:
各区间的温度 T0:
环境温度取20℃
F:
保温层面积 S1:
球壳壁厚取0.048m
λ1:
各温度区间钢材的导热系数
λ2:
各温度区间保温材料的导热系数
保温层向大气散热量计算结果见表6-6:
温度区间
计算公式
结果Kcal/h
0-100℃
Q1=80÷(0.048÷43.92+0.1÷0.025+0.06)×490
9652
100-200℃
Q2=180÷(0.048÷41.04+0.1÷0.04+0.06)×490
34439
200-300℃
Q3=280÷(0.048÷37.8+0.1÷0.055+0.06)×490
73017
300-400℃
Q4=380÷(0.048÷34.2+0.1÷0.07+0.06)×490
125050
400-500℃
Q5=480÷(0.048÷30.96+0.1÷0.085+0.06)×490
189983
500-600℃
Q6=580÷(0.048÷28+0.1÷0.1+0.06)×490
268113
600-625℃
Q7=605÷(0.048÷28+0.1÷0.1+0.06)×490
279406
升温阶段总时间向大气总的散热量
升温速率按每小时50℃h度计算
Q升散总=(Q1+Q2+Q3+Q4+Q5+Q6+)×2+Q7×0.5
=(9652+34439+73017+125050+189983+268113)×2+279406×0.5
=1540211
保温时间向大气的散热量
Q保散=Q7×2=279406×2=558812KCal
6.2.4废气带走的热量:
Q升废总=B×V废×t废×c废×T废
式中:
V废:
废气量标m3/Kg
V0+(n-1)×L0
V0:
理论燃烧产物量
VO=1.11×Q底/1000=1.11×9850/1000=10.93Nm3/kg
n:
过剩空气系数取1.15
LO:
理论空气需要量
L0=0.85×Q底/1000+2=0.85×9850/1000+2=10.373Nm3/kg
B:
燃料消耗量kg/h
t:
出炉废气温度取464℃
C:
废气平均比热取0.35Kcal/m3.℃
T:
升温时间取12.5小时
V废=10.93+(1.15-1)×10.373=12.486Nm3/kg
Q升废总=B×12.486×0.351×12.5×464=25416B
保温2小时废气带走的热量:
Q保废总=B′×V废×t废×c废×T废
V废取12.486Nm3/kg;B′保温阶段燃料消耗量
t废废气温度取700℃;c废700℃的废气比热0.36Kcal/m3.℃
T废:
保温时间取2小时
Q保废总=B′×12.486×700×0.36×2=6292.4B′
6.2.5热损失的计算
对于加热期间的热损失,取以上四项的20%
Q升热损总=(Q球总+Q被总+Q升散总+Q升废总)×20%
=(18034375+397026+1540211+25416B)×20%
=3994322.4+5083.8B
Q保热损=(Q保散总+Q报废总)×20%
=(558812+6292.48B′)×20%
=111762.4+1258.48B′
6.2.6所需燃料的计算
升温阶段的热量支出:
Q支=Q球总+Q被总+Q升散总+Q升废总+Q升损总
=18034375+397026+1540211+25416B+3994322.4+5083.2B
=23965934+30502.8B
升温时燃油放出的热量:
Q总放=B×Q底×T=B×9850×12.5=123125B
由Q总放=Q总支得:
23965934+30502.8B=123128B
B=258kg/h
在升温12.5小时内耗油量为:
258×12.5=3225kg
在保温阶段2小时的热量支出:
Q保总支=Q保散总+Q保废总+Q保损总
Q保总放=B,×Q底×T
B′×9850×2=558812+6292.4B′+111762.4+1258.48B′
B′=55.2kg/h
两小时需要的燃油量55.2×2=110.4kg
故升温、保温两个阶段需燃油量:
W=3225+110.4=3335.4kg
根据经验燃油率为73%,则实际用油量为:
3335.4÷73%=4568.5kg
7.球罐整体热处理准备工作:
热处理前需做许多准备工作,准备工作是否细致直接影响到整体热处理过程是否顺利,热处理质量能否保证。
球罐整体热处理前应做好以下工作:
设置热电偶;柱腿移动装置的安装;烟囱的制作与安装;雾化器的制作;保温棉的敷设;各种供风、供油分配装置及管路制作等。
7.1人员组织及要求:
7.1.1为了保证施工进度和工程质量的要求,应安排如下劳动力配合:
表7-1劳动力安排表
工种名称
需要人数
工程名称
需要人数
保温工
15名
风油比调节人员
2名
柱腿调整人员
8名
电工
1名
管工
1名
液化气调节人员
1名
起重工
1名
仪表记录监测人
2名
空压机操作工
2名
电焊
1名
气焊
1名
负责人
1名
7.1.2参加球罐整体热处理的热处理人员及其他相关工作人员应对自己的工作范围和职责清楚了解,并持从事岗位的上岗证。
7.2球罐整体热处理机具、材料
7.2.1施工用计量仪器(转子流量计、压力表、热电偶、记录仪表)应在使用前经过鉴定合格。
施工用机具材料应能满足整体热处理的施工需要。
7.2.2施工用主要机具、设备
表7-2球罐整体热处理主要机具、材料
序号
名称
规格
单位
数量
备注
1
喷嘴
1#
件
1
2
转子流量计
TZB-251000t/min
600L/h
只
2
3
12点长图记录仪
XWC-300型
台
2
4
油泵
台
2
5
空压机
台
2
6
千斤顶
8T
个
8
7
储油罐
5m3
台
1
现场制作
8
空气缓冲罐
2m3
台
1
现场制作
9
压缩空气分配器
Ф219×800
台
1
现场制作
10
柴油分配器
Ф156×800
台
1
现场制作
11
烟囱
Ф500×2000
个
1
现场制作
12
油过滤装置
个
1
现场制作
13
油雾化燃烧装置
套
1
现场制作
14
石油液化气混合气
个
1
15
压力表
20kg/cm3
个
4
7.2.3施工用措施材料及消耗材料
表7-3施工措施用料及消耗材料
序号
名称
规格
单位
数量
备注
1
柴油
0#
Kg
15000
三台球罐
2
硅酸铝纤维针刺毯
7000×600×40
M3
50
一台球罐
3
石油液化气
Kg
600
4
热电偶
K型铠装
支
50
5
补偿导线
铜-康铜
2*1.5MM2
M
4000
6
截止阀
Pg10Dg50
个
4
Pg10Dg25
个
8
7
无缝钢管
1″、2″
M
70
8
扁钢
30×2A3
M
1500保温用
9
铁钉
L=6″
个
3000
保温用
10
夹布胶管
1″
M
200
3/4″
M
300
11/2″
M
100
11
角钢
⊿50×50
M
柱腿移动用
12
槽钢
12#
M
200
柱腿移动用
13
园钢
Ф15
M
150
保温用
14
铁丝
10#
Kg
300
15
螺丝螺帽
M16×30
套
120
16
铁粉
Kg
20
17
滤油网
M2
1
7.3装设支柱移动装置
7.3.1随着整体热处理的实施,由于热胀冷缩,球罐各个支柱也将平行按径向向外向里移动,若柱腿不随热处理过程移动将导致柱子与球壳相贯线处产生永久变形和破坏,为此热处理前必须脱开球罐上所有影响自由膨胀和收缩的附属部件及连接部位,设置柱腿移动装置及移动位置测量装置,如图—柱腿移动测量示意图。
7.3.2柱腿在不同温度区间理论位移量计算:
计算公式:
△S=D×△T×α/2
式中:
D球罐外径1240mm,α膨胀系数mm/mm.℃,△T温度变化值℃
表7-4不同温度变化的膨胀系数
温度
100
200
300
400
500
600
700
α×10
8.31
10.99
12.31
13.22
13.71
13.94
14.00
表7-5位移值计算结果
温度区间
0-100
100-200
200-300
300-400
400-500
500-600
600-625
合计
位移值mm
5.152
6.813
7.632
8.196
8.500
8.642
2.170
47.10
7.3.3为了使支柱底板在基础上能够顺利移动,支柱移动采用滑板结构,滑板表面应光滑平整,支柱底板上的螺栓孔和螺栓之间应有足够空间保证位移量,所有相对滑动表面均应加注油滑脂。
7.3.4推动支柱移动千斤顶的受力结构应稳定,在升降温过程中,温度每变化100℃时,按计算结果调整相应的位移值,升温时柱腿向外移动,降温时柱腿向内移动,移动过程要平稳准确,并作好移动记录。
7.4温度测量和管理
7.4.1热处理过程的温度测量采用远距离连续自动检测系统,测温选用K型热电偶,铜-康铜补偿导线(2×1.52)和XWC-300型自动平衡记录仪实现温度测量。
热电偶和记录仪表热处理前须鉴定合格,准确度应达到±1%的要求,为了防止电压波动,可选用一台0.5KVA单相220V/0—250V,自动调压器为仪表供电,并按电压表核对电压值。
7.4.2要求测温点应均匀地布置在球壳表面,相邻测温点间距不得大于4500mm,距人孔与环球壳板环缝边缘200mm范围内以及产品试板上,必须设测温点。
根据GB50094—98要求,测温点数不应少于
球罐容积m3
50
120
200
400
650
1000
2000
≥2400
测温点数
8
8
12
12
12
16
24
36
7.4.3热电偶的安装
测温热电偶采用螺栓开孔固定方法,用M16×30的螺栓将热电偶固定在球壳表面和试板上,热电偶和补偿导线的连接应牢靠,保证热处理过程不松动。
7.4.4产品试板的安装
为了保证试板的温度,在试板上与球壳板的间隙处应填铁粉,在热处理过程中,试板温度滞后于球壳板的温度。
7.5壳体的保温措施
7.5.1敷设保温棉前如要求作硬度测定,测定部位应在每条纵缝和上下极环缝各选一处,中间环缝选三处,每处测焊缝、热影响区、母材三个区,热处理后仍在上述测量点相邻部位进行硬度测定,填写硬度测定报告,以此作为评定热处理效果的依据。
7.5.2球罐整体热处理保温材料选用硅酸铝纤维针刺毯,敷设100MM厚,保温材料应保持干燥,不得受潮,保温层应错开敷设,热处理过程应保证各保温层不得松动脱落,保温层应紧贴球壳板表面,局部间隙不得大于20mm,接管、连接板、排烟筒和球罐支柱上半部至少1m长度的范围内均须进行保温。
7.5.3固定保温材料的保温钉不得直接与球壳板焊接,应采用钢带组成的钢格套笼供焊接保温钉用。
钢带采用30×3的扁钢钢带间距1-1.2m为宜,钢带分为长短钢带、长钢带为圆周的一半,短钢带为圆周的1/4,保温钉在钢带上布置间距为700-1000mm,钢带定位用Ф15的元钢制成上下极环箍,赤道环箍,为防止下半球保温棉脱落,用带十字冲口卡片在铁钉上将保温棉压紧,并用10#铁丝拉紧缝合。
保温棉固定如图。
7.6烟囱的安装
热处理时,应在球罐上人孔安装一个Ф500×2000的烟囱,烟囱内设有翻板阀,为了防止受热膨胀,转动不灵,翻板的直径比烟囱内径小10mm,烟囱的固定与人孔法兰连接应牢固。
如图:
7.7燃烧系统的装置安装
燃烧系统的工艺设备主要有烧嘴、内外套筒、点火器、点燃气混合器、齿轮油泵、空气分配器、柴油分配器等。
烧嘴、内外套、点火器固定时,其中心要与人孔中心一致;中心偏差不得超过±1mm,点火器的燃烧圈与烧嘴的距离要以能点燃火焰而不影响喷射为准则。
烧嘴、进风套筒与点火器三者距离对整个球罐温度的均匀性有很大的影响,必须精心调试。
齿轮油泵、柴油分配器、压缩空气分配器、液化气混合器的放置要安全又便于操作。
贮油缸、液化气钢瓶要距火源15m以外,并有专人监测,从油槽到油泵须有过滤器,转子流量计的安装垂直度应符合要求,各系统情况见整体热处理系统图。
气路、油路的连接在保证安全使用的情况下尽量使线路走向最短,以减少液体阻力。
8.整体热处理过程
8.1操作准备
8.1.1各系统设施要仔细检查,发现问题及时解决或上报负责人协调解决,不得敷衍了事,消除一切隐患。
8.1.2各系统进行试运,并合格,燃烧器在现场应先进行试火,找出最佳火焰长度和最佳风油比,火焰长度应在1000-1500MM左右,风压一般控制在4kg/cm2。
8.1.3统一指挥,明确分工,责任到人,对各岗位人员进行操作和安全技术教育。
8.2操作程序
8.2.1烟囱翻板全开并且定位。
8.2.2启动齿轮油泵,检查油分配器油压是否稳定,使油压稳定在3kg/cm2。
8.2.3接通温度记录仪表电流,检查各测温点是否有短路或断路现象。
8.2.4启动空压机,使缓冲罐气压稳定在7Kg/cm2,待风压稳定后,用压缩空气向球罐内吹除5分钟。
8.2.5点火:
首先打开液化气混合阀,然后打开送向混合器的压缩空气开关,使压缩空气压力稳定在0.5Kg/cm2,再打开液化气钢瓶开关送液化气,用烤把进行点火,点火圈燃烧后,逐渐调节压缩空气压力,使点火圈火焰稳定并能承受从喷嘴喷出的5kg/cm2压缩空气而不熄灭。
使通向雾化器的风压稳定在2kg/cm2,缓缓打开供应阀门,经过雾化器的油经过燃烧着的点火圈,即可燃烧。
火焰刚开始燃烧时,让油压控制在70升/小时,调整风压使其安全燃烧。
如在半分钟内点不着火,应先停止供油检查原因。
点火后如发现喘息现象,说明风压过大,应通过降低风压或增加油量来调整,使火焰稳定。
8.2.6升温过程:
通过温度记录仪,对各测温点升温速率进行监控,按照热处理工艺要求300℃以下不控制升温速度,为缩短周期,节约燃料,应采用较大风油比,刚开始时,风油比太大时,火焰过长,温差容易较大,因此一般在200以下时,不要轻易调节风油比。
随着温度升高,罐内温差将有所减少,但是加热过程中易产生上极温度偏高,下极温度偏低的现象,要缩小温差时,可在喷嘴特性曲线上允许范围内尽量增加风压,缩短火焰长度,增加底部辐射,使高温下移,达到缩小温差的目的。
另外,温度超高,消耗油量越大,应先增加风压,再增加油量。
温度监测记录人员,应每30分钟记录一次温度,温度记录人员和风油比调节人员要紧密联系,发现异常尽快处理,由于球罐温升滞后于燃气的温度,风油比的调节要做到平稳、准确、不可操之过急。
柱腿调整应每升高或降低100℃,按计算位移量调整一次,调整时间要同时调节或对称调节,防止发生偏斜,柱腿调整时不可用力过猛,应在调整柱腿时缓慢加力,平稳移动。
8.2.7当球罐温度最高点达到600度时,应降低升温速率,缩小各点温差,当所有测温点进入600℃时,即为恒温开始,恒温期间,任意两测温点不得大于50℃,恒温阶段要保持恒温温度,应不断调整风油比,此时应注意废气温度的变化。
在恒温期间,废气温度的变化对壁温变化影响比较明显,随着温度升高和加热速度降低,废气与壁温温差逐渐降低,在恒温期间,废气温度的变化对壁温温差逐渐降低,在恒温时,温差最小,这时利用最小温差时的风油比控制恒温温度,使恒温效果较好。
8.2.8恒温结束后,按工艺要求冷却速度应为30—50℃/h,不得大于50℃/h,这时,应逐渐减少油量,当油量降低30L/h以下,就可以关闭烟囱翻板,随着温度降低,冷却速度越来越慢,当不需要油加热时,其冷却速度能满足50℃/h热处理工艺要求时,应先关闭油泵油阀,再关掉液化气阀,最后停止供风,关闭空压机熄灭全部火源,自然冷却,直到温度降至300℃以下,每半小时记录一次温度,在降温过程中,每100℃调整柱腿一次。
9.质量检验
9.1热处理后,应测量并调整支柱垂直度,使其允许偏差满足规范要求。
9.2热处理后,应在热处理前相邻部位测定硬度值,并填写硬度试验报告。
9.3热处理后,产品焊接试板的力学性能试验结果应符合GB150附录的规定。
9.4热处理过程的记录曲线和数据图表应清晰、整洁,不得随意涂改,最