X说明书.docx
《X说明书.docx》由会员分享,可在线阅读,更多相关《X说明书.docx(41页珍藏版)》请在冰豆网上搜索。
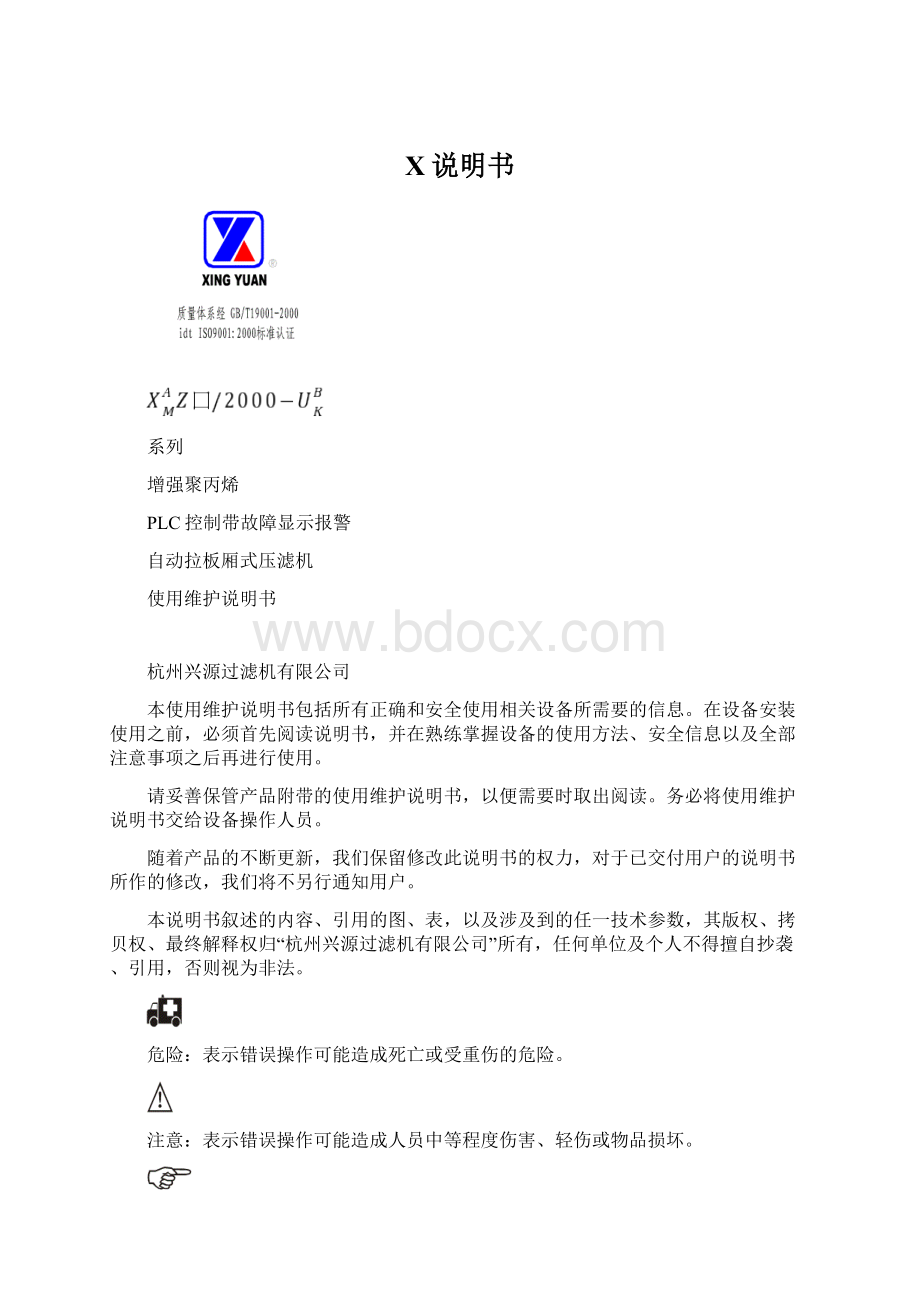
X说明书
系列
增强聚丙烯
PLC控制带故障显示报警
自动拉板厢式压滤机
使用维护说明书
杭州兴源过滤机有限公司
本使用维护说明书包括所有正确和安全使用相关设备所需要的信息。
在设备安装使用之前,必须首先阅读说明书,并在熟练掌握设备的使用方法、安全信息以及全部注意事项之后再进行使用。
请妥善保管产品附带的使用维护说明书,以便需要时取出阅读。
务必将使用维护说明书交给设备操作人员。
随着产品的不断更新,我们保留修改此说明书的权力,对于已交付用户的说明书所作的修改,我们将不另行通知用户。
本说明书叙述的内容、引用的图、表,以及涉及到的任一技术参数,其版权、拷贝权、最终解释权归“杭州兴源过滤机有限公司”所有,任何单位及个人不得擅自抄袭、引用,否则视为非法。
危险:
表示错误操作可能造成死亡或受重伤的危险。
注意:
表示错误操作可能造成人员中等程度伤害、轻伤或物品损坏。
提示:
表示我们的提示、建议或说明。
设计注意事项
●在进行压滤机的地基设计时请按设备供应商提供的图纸为准,并在两支脚的放置位置上加承重梁。
说明书中的地基图仅作参考。
因产品的改进而影响设备的外形、地基尺寸等,恕不通知用户。
●在产品设计上,若过滤温度超过90℃,请在订货时特殊说明,若把普通滤板当作高温滤板使用,将影响滤板的使用寿命,甚至引起滤板破损。
●常规产品不能用于防爆场合。
用户如有防爆要求,请在订货时特殊说明防爆等级及使用环境。
●产品在选型过程中,应严格按照厂方所提供产品的过滤压力进行设计和订货,以免影响机器的过滤效果和滤板的使用寿命。
●设备吊装时,应勾住设备的吊装孔进行起吊。
●设备安装时,应将设备安装基础的水平度控制在0.5/1000以内。
●设备的地脚螺栓采用二次水泥灌浆,外露螺纹50~60mm。
●设备安装就位后,应测量压滤机主梁的水平度,并控制在±2mm以内,两主梁的对角偏差不超过4mm 。
否则设备在使用过程中会因受力不均而引起主梁变形。
●所选用滤布的规格不同,其厚度也不相同,有时会造成拉板卸饼的开挡距离变小,属正常现象,选型时应注意。
使用时的注意事项
●在开启机器前,必须确认设备的启动不会有人员伤害。
●设备通电时请不要打开电控箱触摸端子,也不要打开电机的接线盒,否则可能引起触电、误操作。
●设备进料没有结束时请不要按回程松开滤板,否则会引起物料泄漏,重则会造成人员伤亡。
●压滤机的电接点压力表和溢流阀如损坏应及时更换,否则会使液压站、油缸长期处于超高压状态而缩短液压站和油管的使用寿命,引起油管破裂,甚至造成油缸爆裂。
●压滤机压紧或拉板时,请不要将手伸入滤板之间整理滤布,否则会造成人员损伤。
如果要整理滤布,请停止压紧或拉板状态。
●液压站在运转时,请不要拆开液压元件,否则高压液压油会溅出伤人,必须在液压站卸压(压强≤0.05Mpa)后拆卸液压元件。
●设备试运转时,应按照使用维护说明书中的要求将液压站的液压油加满,否则会使压滤机的油缸没有充满,影响液压站的正常工作,导致液压泵损坏。
●应按照使用维护说明书中的要求定期更换液压油,并及时清洗液压阀和泵,否则会影响液压站的正常工作。
●进料压力不允许超过设备的正常过滤压力,否则会引起滤板破损。
●未接受过设备和系统维护培训的人员不得擅自打开电控箱接线,否则可能接线错误引起误动作。
●设备维修时,应关闭压滤机的总电源开关。
●开始新的过滤循环时,必须清除滤板密封面上残留的滤饼,否则由此引起的主梁变形,滤板破裂,跑料等事故,不属“三包”之列。
一、执行标准
二、型号意义
三、主要技术参数
四、结构组成与工作原理
五、设备安装与调试
六、操作规程及使用方法
七、滤布加工与安装方法
八、注意事项
九、保养及故障排除
十、试车前的准备工作
十一、随机文件
十二、液压油
十三、压滤机总装基础图及管口尺寸
附表一、水嘴规格及材质
附表二、压滤机装箱发货清单
附表三、易损件清单
图一、过滤和洗涤流程图
图二、油缸结构示意图
图三、液压站结构及油口联接示意图
图四、系统图液压
图五、电气原理及接线图
图六、管线布置图
质量保修单
产品质量意见征求书
用户在阅读此说明书时,请查阅所购设备的型号。
对于不同型号的设备,将具备不同的功能,请仔细核对。
如果您所购的设备增加了翻板、接液、滤布曲张等其它功能,我们将附加功能说明书为您详细介绍。
本说明书所提及的各种图、表、国家标准等技术参数,主要起说明、示意作用,订货时,将以我们提供的技术图纸为准。
另外,因产品改进,以及国家标准、企业标准的更新而导致设备技术参数的变更,恕不另行通知。
(具体型号请参考下面的型号意义)
一、执行标准
本系列压滤机执行标准:
JB/T5152《厢式压滤机和板框压滤机型式与基本参数》,JB/T4333《厢式压滤机和板框压滤机技术条件》。
二、型号意义
│││││││└──B为不可洗式,K为可洗式
││││││└────滤板材质为增强聚丙烯
│││││└─────────滤板外形尺寸(mm)
││││└────────────过滤面积(m2)
│││└─────────────自动拉板
││└───────────────出液方式:
A为暗流,M为明流
│└────────────────机型改进号
└──────────────────厢式压滤机
三、主要技术参数
名称
参数
过滤工作压力(MPa)
≤1.0
过滤工作温度(℃)
-10-90
最大液压保护压力(Mpa)
29
最高液压压紧工作压力(MPa)
25
止推板侧主进料孔公称通径(mm)
DN200
压紧板侧辅助进料孔公称通径(mm)
DN100
洗涤/出液口公称通径(mm)
DN100
油缸最大有效行程(mm)
1250
油缸公称直径(mm)
450
系列压滤机技术参数表
过滤面积(m2)
560
630
710*
750*
800*
900**
1000**
1080**
滤板块数(块)
81
93
105
111
117
135
147
177
滤室容积(m3)
8.40
9.45
10.65
11.28
12.0
13.5
15.0
17.7
滤板厚度(mm)
70
滤饼厚度(mm)
30
主机长度(mm)
10320
11160
12000
12420
12840
14100
14940
17040
设备外形
尺寸(mm)
长
11230
12070
12910
13330
13750
15010
15850
17950
宽
2640
3210
高
2600(主机高)+400(拉线开关高)=3000
进料孔孔径(mm)
DN200
出液孔(洗涤孔)
孔径(mm)
DN100
压紧板侧辅助进料口孔径(mm)
DN100
整机重量(Kg)
40395
42795
45490
46725
48585
53015
55720
62445
1、带*号的表示有一对中间支撑,带**号的表示有二对中间支撑;滤板块数不包括墙板。
2、以上数据是以标准板厚70mm,标准饼厚30mm为例,当滤板(滤饼)厚度发生变化时,
以上数据也会相应增减。
四、设备结构与工作原理
型压滤机是集机、电、液于一体的技术水平先进的固液分离机械产品。
它由五大部分组成:
即机架部分、过滤部分(滤板、滤布)、自动拉板部分、液压部分和电气控制部分。
具体结构见附图一。
⒈机架部分
机架部分是设备的主体,用以支撑过滤机构,连接其它部件。
它主要由止推板总成、压紧板总成、油缸压紧装置和主梁等部件组成。
设备工作时,油缸体内的活塞推动压紧板,将位于压紧板与止推板之间的滤板、滤布压紧达到密封效果,以保证带有工作压力的料浆在滤室内进行加压过滤。
⒉过滤部分
过滤部分是由按一定次序排列在主梁上的滤板和夹在滤板之间的滤布组成,滤板和滤布的相间排列,形成了若干个独立的过滤单元──滤室(见图一:
过滤和洗涤流程图)。
过滤开始时,料浆在进料泵的推动下,经止推板侧的进料口及压紧板侧的进料口进入各滤室内,并借进料泵产生的压力进行过滤。
由于滤布的作用,使固体留在滤室内形成滤饼,滤液由水嘴(明流)或出液阀(暗流)排出(水嘴规格见附表一)。
若需洗涤滤饼,可由止推板上的洗涤口通入洗涤水,对滤饼进行洗涤;若需要较低含水率的滤饼,同样可从洗涤口通入压缩空气,穿过滤饼层,以带走滤饼中的部分水分(适用于Uk机型)。
在压滤机使用过程中,滤布起着关键的作用,其性能的好坏,选型的正确与否直接影响着过滤效果。
目前所使用的滤布中,最常见的是由合成纤维纺织而成,根据其材质的不同可分为涤纶、维纶、丙纶、锦纶等几种。
除此之外,常用的过滤介质还包括棉纺布、无纺布、筛网、滤纸及微孔膜等,根据实际过滤要求而定。
如贵单位需要这方面的技术服务,请与本公司联系。
⒊自动拉板部分(具体详见电气使用维护说明书)
拉板机构由叶片泵组、液压马达、拉板传动机构及旋转编码器检测元件等组成。
液压马达通过二级减速传动带动拉板部分的输送链,从而带动联接在其上的拉板器运动,将滤板逐一按序拉开。
推拉板器的自动换向靠由拉板旋转编码器发出的检测信号通过PLC控制来设定完成。
液压马达的转速可通过拉板液压回路中的节流调速阀加以调节。
⒋液压部分(以下针对手动程式,手动及自动程式及各控制元器件动作过程详见电气使用维护说明书)
液压部分是驱动压紧板压紧滤板和松开滤板的动力装置,配置了柱塞组合泵及各液压控制阀(详见图四:
液压系统图)。
压紧滤板时,将电源接通,工作程式选择“手动”档,按下“压紧滤板”按钮,柱塞泵电机组启动,电液换向阀线圈得电动作,柱塞泵向油缸无杆腔供油,活塞杆前移,压紧滤板;当油缸油压上升到电接点压力表设定上限值时,电接点压力表上限位接通而停泵,此时压滤机即进入自动保压状态,保压指示灯亮;当油压降至电接点压力表调定的下限值时,柱塞泵重新启动,继续向油缸内补充压力油,保证过滤所需油缸工作压力在25MPa以内;当压滤机被锁定在保压工作状态下时,此时按“松开滤板”、“拉板卸饼”等按钮均无效,以确保进料过滤过程的正常进行;
压紧板回程时,必须按下“暂停”按钮来清除保压状态,按下“松开滤板”按钮,柱塞泵电机启动,电液换向阀执行换向动作,柱塞泵向油缸前腔供油,活塞杆带动压紧板回程,滤板松开;当压紧板触发油缸座侧接近开关时,回程自动停止。
拉板时,按下“拉板卸饼”按钮,叶片泵组向液压马达供油,通过旋转编码器检测器件及PLC控制电磁换向阀切换,使拉板器自动往复拉板,当拉完最后一块板时,拉板器自动返回,当拉板器回至起始位置时,触发接近开关而自动停止。
在前后位置时,通过机架上的撞块使拉板器上的拨杆带动拉板爪换向切换,使拉板器能往复循环运行实现拉板。
在拉板过程中如出现异常情况,随时可通过机架上方的拉线开关中止拉板动作。
电控箱操作面板示图
⒌电控部分
电控部分是整个系统的控制中心,具体请参看“电气使用维护说明书”,电气原理及接线图可参见附图五。
五、设备安装与调试
㈠机器的安装
⒈由于吊运能力所限及考虑到设备采用活动联接结构,本机应分几大部件拆散装运
机组吊运时,由于机组较大,需在本公司技术人员的指导下,可视吊机吨位拆散成几大部件吊装。
吊运时须找准重心,钢丝绳选择合理,钢丝绳与部件接触部位需用布或其它软质材料衬垫。
⒉压滤机基础的安装
一般情况下,压滤机应水平地安装于混凝土基础结构架上,油缸支座、止推板座分别用8个M27×500的地脚螺栓、中间支撑用M24×300地脚螺栓(中间支撑有无见系列表)二次灌浆固定;主梁与止推板座用M30的螺钉联接紧固,止推板体可绕两支承轴块在一定角度内旋转;而油缸座支脚与主梁之间不联接紧固可滑动,以保证主梁在受力状况下有一定的自由度以防变形。
基础应采用二次灌浆而成,基础平面需光滑,标高以卸渣操作方便为准,同时应考虑厂房流水地沟及料池的开设。
安装时,机架应进行水平及对角线校正。
安装地点离处理料浆场地越近越好,考虑到压滤机在卸料时便于操作,机架周围留一米左右的空间。
电气控制柜可放置在油缸座侧的地基平台上,安装时应避免电气元件受损,影响正常工作。
滤板的排列顺序应以出厂时的排列顺序为准,不得随意颠倒。
尤其注意压紧板端的墙板不得移至其它位置使用。
滤布可用电烙铁等专用工具烫料,以免滤布起毛边。
进料泵压力和流量的选择应与我公司产品相匹配,并在进料管路上安装回流管和压力表,以保证压力调节的需要。
如机型为可洗的,洗涤泵的选择要求与进料泵相同,但洗涤水压力应略高于进料压力。
最好在进料泵前安装粗过滤装置,以防止垃圾杂物进入泵和机器内损坏机件。
进料时,慢慢旋转进料阀门,使压力逐渐升高。
进料总阀门的安装应靠近止推板。
液压站安装的位置可根据用户实际场地而定,管道应尽可能地短,同时应避免其它料浆混入油箱中,影响液压元件动作的灵敏性,甚至损坏液压元件。
3.管路系统的安装
管道的安装可根据管线布置参考图(见附图六)及结合用户单位现场实际进行安装,但应注意管路的安装、使用及维修必须方便,管道不得接错,管线应尽量短。
其中止推板侧各进料及出液接管与管道系统联接时须采用JGD型可曲挠单球体橡胶接头作过渡联接;压紧板侧进料管与管路采用软管联接,保证压紧板在活动时可伸缩(适用于压紧板侧双向进料机型)。
此外,本机还可根据需要配备空气压缩机一台,储气罐一只,以供吹气用。
以上设备及各种阀门均由用户自备。
进料泵的选择,可根据流量、颗粒度、粘度等要求而定,但压力不能超过设备最大过滤压力。
㈡设备的调试
⒈检查整机
⑴将液压站、电控箱擦干净,油箱内部清洗干净,检查电源以及压紧、回程、拉板油管是否安装正确,电接点压力表(DY)上下限压力调定是否合适,电源布线是否安全合理。
⑵将机架、滤板、活塞杆擦干净,检查滤板排列是否整齐、正确;检查滤布安装有无折叠现象,如有,需展平。
⑶检查进料、水洗、吹气(如带反吹系统)、出液等管路、阀门的配置是否正确、合理。
⑷用户负责将所需合格电源接线至我方提供的压滤机电控箱内,从电控箱至压滤机接线由我方负责。
各进料泵及自动控制阀等需我方二次控制设备的接线,均需用户负责接线至我方提供的电控箱内。
⒉电控液压调试(见图三:
液压站结构及油口联接示意图和图四:
液压系统图)
(1)当以上所需检查的各项检查确认无误后,向油箱内注入过滤清洁的液压油至规定油位(大约500公斤),接通电源,将电气箱面板上的工作程式开关转到“手动”位置,点动“松开滤板”按钮,观察高压柱塞泵电机(14)是否沿机盖所示箭头方向正转;然后,顺时针方向旋紧安全溢流阀(10),逆时针方向旋松高压溢流阀(13),按“压紧滤板”按钮,调整高压溢流阀(13)至2MPa左右,然后使活塞反复走动数次,以通过排气阀排尽油缸内空气。
(2)首先根据进料压力及流量选择合适的高压溢流阀(13)锁定压力及电接点压力表(8)上下限值。
调节时,将高压溢流阀(13)压力调到最高,逆时针打开安全溢流阀(10),启动高压柱塞泵(14),缓慢顺时针转动调节安全溢流阀(10),当压力表(8)的指示数为29MPa时,停泵,锁定安全溢流阀(10)。
启动高压柱塞泵(14),缓慢逆时针转动调节高压溢流阀(13),当电接点压力表(8)上限的读数为27Mpa时,停泵,锁定高压溢流阀(13);将电接点压力表(8)的上限设为25Mpa,下限设为21Mpa。
(安全溢流阀、高压溢流阀、电接点压力表出厂前均已调好,一般不需用户调节。
如需改变调定的压力,可按上述方法调节。
)
(3)重新让活塞杆带动压紧板来回走动三次,查看油压上升至电接点压力表(8)上限值时是否会自动停机;观察油压下降情况,在第一次上压时,压力下降速度≤3MPa/10min为正常,当压力降至电接点压力表(8)下限后,高压柱塞泵(14)电机自动启动上压,第二次压降速度≤2MPa/20min属正常。
⒊过滤部分调试
(1)、压紧滤板并保压。
(2)、打开所有出液阀门,关闭水洗、吹气(可洗机型)阀门,进料阀门打开四分之一左右,启动进料泵,观察滤液及进料压力变化,如压力超高,需打开回流管路上的阀门进行调节。
由于滤布的毛细作用,刚开始过滤时,滤液稍许浑浊属正常现象。
一般,明流机型待过滤5-10分钟后可将进料阀门开大,暗流为10-20分钟。
六、压滤操作程序及使用方法
压滤机的操作规程按下列过程进行:
操作保压保压
停不可洗
停机拉板回程
以下针对手动工作程式(手动及自动程式及各控制元件动作过程详见电气使用维护说明书,在此不再详述)
1.压紧滤板
当拉板机械手在起始位置时,并在拉板停止接近开关触发条件下,按下“压紧滤板”按钮,高压柱塞泵电机组启动,压紧电液换向阀动作,高压柱塞泵向油缸后腔(无杆腔)供油,活塞杆前移,压紧滤板;当油缸油压上升到电接点压力表的上限值时,电接点压力表接通上限电路而停泵;此时压滤机自动进入保压状态,保压指示灯点亮;当油压降至电接点压力表调定的下限值时,高压柱塞泵重新启动,压紧电磁阀动作,继续向油缸内补充压力油,保证过滤所需工作压力在压力表上限和下限之间;油缸压紧滤板时的压紧压力超过一定值达到报警电接点压力表上限时,此时压力表发信给PLC,停止油泵电机及压紧电磁阀并发出报警信号启动声光报警器。
2.进料过滤
进入保压状态后,检查各管路阀门开闭状况,确认无误后按“进料启动”按钮启动进料泵,慢慢开启进料阀,料浆即通过止推板上的进料孔进入各滤室,在规定压力下实现加压过滤,形成滤饼。
3.吹气或洗涤滤饼
过滤完毕,由洗涤孔通入洗涤水至各滤室内,渗过滤饼层,通过洗涤以便回收滤饼中的有效成份,或除去其中有害成份。
若需对滤饼进行吹气,则可从洗涤孔通入压缩空气,带走滤饼中的一部分水分。
(适合于Uk型压滤机)
4.松开滤板
先按“暂停”按钮来清除保压状态,按下“松开滤板”按钮,先接通卸压电磁换向球阀,再启动高压油泵电机,并使回程压电液换向阀动作,高压柱塞泵向油缸前腔供油,活塞杆带动压紧板回程,滤板松开;当压紧板触发回程停止接近开关时,压紧板回程自动停止。
5.拉板卸饼
当回程到底以后并使压紧板回程停止接近开关导通,按下“拉板卸饼”按钮,拉板系统开始动作,拉板机械手往返动作,将滤板逐块拉开,同时滤饼靠自重卸掉。
拉板时出现异常情况时,可以通过拉线开关或“暂停”按钮中断拉板动作,当排除故障后再次拉动拉线开关使由PLC控制动作复位。
当拉板全部完成后,拉板器会自动回退到油缸一端并停机。
6.清洗整理滤布
拉板卸料以后,残留在滤布上的滤渣必须清理干净,滤布应重新整理平整,开始下一循环。
当滤布的截留能力衰退,则需对滤布进行清洗或更换。
七、滤布加工与安装方法
本节是以滤板厚70mm,滤饼厚30mm为例进行说明。
由于机型不同,以及各种工况条件下的过滤工艺不同,滤布的制作方式也各不相同,用户可向我公司技术部咨询。
(1)滤布套加工方法
⒈首先参照模板示意图(a)所示,用三夹板或其它材料制作模板一块,圆孔的周围用铁片包好,以防电铬铁工作时烫坏模板。
⒉将滤布裁成2080×2100mm作为滤布片,裁成820×70mm作为滤布套中间连接圈。
⒊将滤布片三边翻起宽度10mm左右,并用工业缝纫机缝好(滤布边上双层加固,注意滤布为长方形,缝好后滤布片可参看图(b),括号内尺寸为参考尺寸)。
⒋在滤布片上三周烫孔Φ5左右(可根据电铬铁头部直径的大小),烫在单层滤布上,位置可参考示意图(b)。
⒌将模板放在滤布片上,用电铬铁烫出中间孔及水洗孔。
水洗孔的开孔位置及开孔个数按实际滤板规格确定。
⒍拿二块滤布片和一块中间联接布,先将中间联接布在滤布片中间孔周围缝一圈,直径大约为Φ260左右,然后逐渐向孔内缝3-4圈,直至内圈直径为Φ230;接着再缝好中间联接圈两头联接处;最后以同样方法将中间联接圈与另一块滤布片缝合在一起。
(参见图(c))
⒎A孔表示上进料口,B孔表示中进料口。
通常情况下,二者只有其一,这两种进料方式的滤布,其加工及安装方法相同。
(2)滤布片加工方法
1.将滤布裁成2080×4200mm作为滤布片,其加工方法参见图(d)及
(1)中所述。
2.A、B表示中进料孔,C、D表示上进料孔。
只能同时开A、B或C、D孔。
3.用电铬铁烫出进料孔及水洗孔,水洗孔的开孔位置及开孔个数按实际滤板规格确定。
(3)安装方法
1.安装滤布套时,将其中的一面滤布卷成圆筒状,然后穿过滤板中间孔,再展开铺平,同一块滤板上的滤布用带子扎紧在一起(参见图e:
滤布套安装示意图)。
2.安装滤布片时,通常要用滤布夹(图g所示滤布夹材质为聚丙烯,滤布夹材质为不锈钢时,其外形与图g略有不同,本说明书不另行示意)固定,安装方法参见图f和图g。
(4)滤布制作及安装注意事项
1.电铬铁可采用500W。
2.烫滤布时要小心,滤布的过滤部分不要烫着,否则滤布上有小孔,料浆很容易穿过滤布,造成出液浑浊及两边压力差不一样,严重时会损坏滤板。
3.滤布要缝合好,否则使用一段时间后,缝合处容易裂开,造成出液浑浊。
4.缝纫机的针脚应选择合理,否则容易从针脚处漏料。
5.滤布片上穿绳子的小孔应避开手柄及水嘴位置,且保证滤布平整地包在滤板外面。
6.用户在滤布开孔前,应充分了解该滤布物性。
对于易缩水滤布,必须进行缩水处理,出液口(洗液口)开孔大小为滤板孔的70%左右。
安装滤布时,需注意滤布孔与滤板孔要对准,不得有折叠现象,以免造成泄漏。
滤布上端及左右两端大于滤板30mm为好。
滤布使用一段时间后要变硬,其过滤性能下降,为此滤布要定期检查,若有变硬现象,则用相应的低浓度弱酸或弱碱去中和(浸泡24小时),恢复其性能。
八、注意事项
⒈压滤机在压紧后,通入料浆开始工作,进料压力必须控制在出厂标牌上标定的最大过滤压力(表压)以下,否则将会影响机器的正常使用。
⒉两个电接点压力表指针的上、下限出厂前已调好,用户一般不用动,若用户要调节压力,则下限以不漏液为准,上限不能超过27MPa。
⒊过滤开始时,进料阀应缓慢开启,起初滤液往往较为浑浊,然后转清,属正常。
⒋在冲洗滤布和滤板时,注意不要让水溅到电控各接线箱(盒)处,以防意外事故发生。
⒌由于滤布纤维的毛细作用,过滤时,滤板密封面之间有清液渗漏属正常现象。
⒍高压溢流阀(13)在出厂前已调到27MPa,若用户要自行调节油缸公称压力,则应把高压溢流阀(13)全部调松,然后启动柱塞泵(13),慢慢地调整高压溢流阀(13)到需要的压力,但切勿超过28MPa。
⒎安全溢流阀(10)在出厂前已调到29MPa,用户切不可随意调动。
⒏搬运、更换滤板时,用力要适当,防止碰撞损坏,严禁摔打、撞击,以免破裂。
滤板的位置切不可放错;过滤时切不可擅自拿下滤板,以免油缸行程不够而发生意外;滤板破裂后,应及时更换,不可继续使用,否则会引起其它滤板破裂。
⒐在压紧滤板前,勿必将滤板整齐排列,且靠近止推板端,平行于止推板放置,避免因滤板放置不正而引起主梁弯曲变形。
10.料浆泵及进料阀,洗涤水泵及进水阀,压缩空气及进气阀在同时只允许开启其中之一。