事故现象判断与处理.docx
《事故现象判断与处理.docx》由会员分享,可在线阅读,更多相关《事故现象判断与处理.docx(12页珍藏版)》请在冰豆网上搜索。
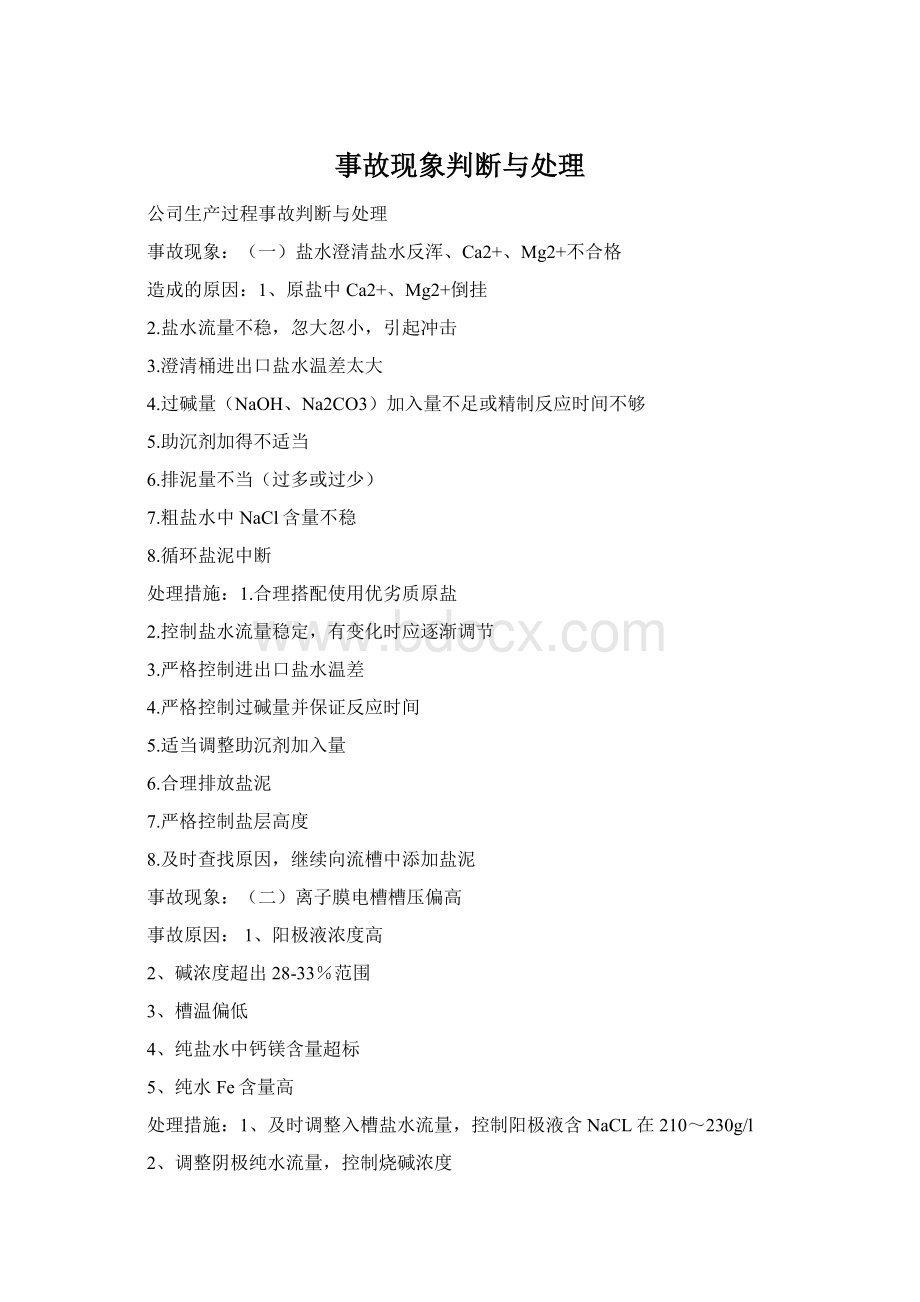
事故现象判断与处理
公司生产过程事故判断与处理
事故现象:
(一)盐水澄清盐水反浑、Ca2+、Mg2+不合格
造成的原因:
1、原盐中Ca2+、Mg2+倒挂
2.盐水流量不稳,忽大忽小,引起冲击
3.澄清桶进出口盐水温差太大
4.过碱量(NaOH、Na2CO3)加入量不足或精制反应时间不够
5.助沉剂加得不适当
6.排泥量不当(过多或过少)
7.粗盐水中NaCl含量不稳
8.循环盐泥中断
处理措施:
1.合理搭配使用优劣质原盐
2.控制盐水流量稳定,有变化时应逐渐调节
3.严格控制进出口盐水温差
4.严格控制过碱量并保证反应时间
5.适当调整助沉剂加入量
6.合理排放盐泥
7.严格控制盐层高度
8.及时查找原因,继续向流槽中添加盐泥
事故现象:
(二)离子膜电槽槽压偏高
事故原因:
1、阳极液浓度高
2、碱浓度超出28-33%范围
3、槽温偏低
4、纯盐水中钙镁含量超标
5、纯水Fe含量高
处理措施:
1、及时调整入槽盐水流量,控制阳极液含NaCL在210~230g/l
2、调整阴极纯水流量,控制烧碱浓度
3、检查精制盐水流量,温度及纯水流量
4、提高二次精制效果,严格控制精制盐水含Ca2++Mg2+≤20ppb
5、协调了解纯水工序,确保纯水含铁≤0.5ppm
事故现象:
(三)树脂塔出口盐水含Ca2+、Mg2+、Sr2+等超标
事故原因:
1、饱和盐水的质量如温度、PH、Ca2+、Mg2+、Sr2+、SS、ClO-等指标不合格
2、螯合树脂问题
3、再生处理的过程存在问题
处理措施:
1、调整盐水温度、PH及饱和盐水的Ca2+、Mg2+、Sr2+、SS等指标
2、检查确认螯合树脂的型号、性能及树脂高度等是否满足要求
3、检查确认再生过程每一步操作,流量、浓度等指标满足再生要求
事故现象:
(四)单台电解槽(6.0万吨/年)停车
事故原因:
1、单元泄漏严重,滴漏液体成线,尤其是阳极液泄漏
2、离子膜破漏严重时(⑴通过电解槽普查分析,单槽氯气纯度降低,O2/CL2上升;⑵通过停车机会,对离子膜进行MELIS实验,短时间内膜电压下降到1.7V以下时,确定更换离子膜)
3、其他电解槽配件(循环管、垫片等)发现泄漏,造成电解槽接地
处理措施:
1、对单台电解槽进行除槽,除槽详细步骤如下:
⑴了解调度、电气及氯氢处理,得到允许后开始降电流。
⑵将该列单元电压联锁旁通。
⑶按照每3分钟1KA的速度下调该排运行负荷,根据下调负荷调整调节软水和盐水的流量
⑷当降至3KA时,了解调度(氯化氢解除单排联锁)后,继续降至1.5KA,通知调度切槽。
(注意:
降电流期间注意氯气及氢气的吸力。
)
⑸现场将跳槽开关SW101闭合,确认闭合后,将SW102断开,确认断开后切下电槽。
⑹给电解槽送入150A极化电流后,确认打印跳闸0时刻,极化电流5分钟、10分钟、15分钟时的单元槽电压。
2、除槽后,电槽冲洗处理操作
阴极侧:
1)关闭进电槽的软水供料阀。
2)关闭阴极液循环阀17#。
3)关闭氢气隔离阀。
4)打开单槽氢气放空。
5)适当打开单槽充氮阀。
6)打开开车烧碱阀对电槽进行冲洗,观察电槽阴极液溢流正常。
阳极侧:
1)打开电槽开车E517供盐水阀,关闭E519供盐水阀,保持入槽盐水流量不变,对电槽进行阳极冲洗,确保电槽阳极液溢流正常。
2)适当打开单槽空气进气阀。
3)关闭单槽氯气隔离阀。
4)15分钟后,将极化电流降至40A。
5)后关闭阳极液循环阀18#。
3、冲洗结束操作
⑴化验室分析电槽冲洗盐水的浓度达260~280g/l。
⑵1.5小时后,化验室分析冲洗盐水的游离氯含量,当游离氯为0时,停止极化电流,然后停止冲洗电槽。
⑶将电解槽阴阳极循环阀门17#、18#打开外,关闭电解槽其他所有阀门关闭。
(并检查相邻电槽阀门开关情况,防止误操作。
)
4、排液操作
⑴.拆除排液阀后的盲板改为连通方式。
⑵.打开液面管阀,确认用于指示阴阳极液位的透明胶管畅通
阳极侧:
①确认氯气隔离阀关闭。
②打开氯气分离器排空阀。
③适当打开2#阳极液排放阀;
阴极侧:
①确认氢气隔离阀关闭。
②打开氢气放空阀。
③打开充氮阀。
④适当打开1#阴极液排放阀。
⑶排放过程中,始终确保电解槽阴极液位高于阳极液位100-200mm。
⑷根据检修要求排放至规定液位。
①关闭阴阳极排液阀。
②关闭充氮阀。
③关闭氢气放空阀。
④关闭排空阀
⑸排液结束后,除17#、18#阴阳极液循环阀、液位指示阀打开外,其余所有阀门关闭。
事故现象:
(五)单排电解槽(6.0万吨/年)停车
事故原因:
1、计划停车
2、单排跳闸⑴出槽淡盐水(现场手动阀)关闭
⑵一台槽中有3个以上单元槽压≥4.0V
处理措施:
1、协调了解并汇报相关部门和领导。
2、迅速检查单排氢气联锁是否启动,如没有启动,立即手动操作。
3、检查确认极化电流启动,并了解提到150A,检查所有离子膜情况。
4、立即对该排电解槽进行冲洗处理。
事故现象:
(六)全部电解槽(6.0万吨/年)停车
事故原因:
1、计划停车
2、意外跳闸⑴淡盐水罐高位触点动作
⑵精制盐水罐D516低位≤15%
⑶氯压机A、B停车
⑷氢压机任一台停车
处理措施:
1、协调了解并汇报相关部门和领导。
2、迅速检查两排氢气联锁是否启动,如没有启动,立即手动操作。
3、迅速检查氯气联锁是否启动,如没有启动,立即手动操作。
并及时了解氯氢处理工序,将离子膜氯气水封加水。
4、检查确认极化电流启动,并了解提到150A,检查所有离子膜情况。
5、检查联锁启动后,将所有联锁置于旁通位置。
6、立即对所有电解槽进行冲洗处理。
事故现象:
(七)运行中的氯压机跳闸
事故原因:
1、设备机械故障
2、氯压机主机联锁启动
处理措施:
1、立即检查两套离子膜电解是否联锁停车,若没有,则了解离子膜电解进行紧急停车。
2、立即检查隔膜电解是否联锁停车,若没有,则按下隔膜电解紧急停车按钮。
3、将氯压机开关切至“停”的位置。
4、检查隔膜氯气阀门PICA701是否联锁关闭,若没有,则到手动关闭PICA701阀及手动阀。
5、检查隔膜氢气阀门PICA-703是否联锁关闭,若没有,则到手动关闭PICA701阀及手动阀。
6、确认事故氯正常开启情况下(事故氯循环碱浓度≥8%),确认隔膜事故氯阀HV1702联锁打开。
7、关闭氯压机出入口阀及大回流阀,开本机回流阀和事故氯阀HC706A/B。
8、关闭钛冷却器的冷冻水阀TIC701,防止氯水结晶,关闭进泡罩塔的进酸阀门。
9、现场三套电解氯气水封加水,使氯气去事故氯系统。
事故现象:
(八)氢压机停车(运行中的氢压机任意一台停车操作)
事故原因:
1、设备机械故障
2、三套电解全部停车
处理措施:
与事故(七)同样操作
事故现象:
(九)氯气纯度差太大
事故原因:
1、负压系统有泄漏
2、负压太大
3、氯压机充气太大
处理措施:
1、检查负压系统漏点
2、调节氯压机回流,减小负压
3、减小氯压机充气量。
★事故现象:
(十)汽化器列管泄漏
事故原因:
1、设备整理问题
2、腐蚀或超压运行
处理措施:
1、通过检测热水出口PH值呈酸性,确定泄漏。
2、通知CPE停车,停热水泵,停蒸汽。
3、停屏蔽泵,关闭汽化器本体加液氯阀门,全开调节阀。
4、开启加液氯的旁通阀门,关闭汽化器氯气出口阀门,开启排污阀门,关闭排污器入口阀门,。
5、打开汽化器和液氯真空储槽进排污器的连通阀门,利用真空储槽闪抽汽化器内的液氯,到液位为0,关闭连通阀门。
6、开真空泵,对汽化器进行抽空操作,直到真空为止。
7、通过填加纯碱,对热水罐罐水质进行中和处理,直到检测水质PH值为中性。
事故现象:
(十一)液化器发生泄漏
事故原因:
1、设备整理问题
2、腐蚀或超压运行
处理措施:
1、确认具体的泄漏液化器,并了解汇报
2、连接抽气软管,对准泄漏部位进行抽风处理
3、紧急处理(操作时注意风向,尽可能站在上风向)
4、对泄漏的液化器进行抽真空。
5、开启备用液化器,停泄漏液化器。
事故现象:
(十二)联锁所有送气炉熄火
事故原因:
1、执行界外联锁熄火(三套电解中的全部或者两套、单套停车,隔膜电解氯气高压PICA701≥800Pa,低压PICA701≤-1500Pa;6.0万吨/年离子膜氯气PICA051022≥80mmH2O,低压PICA051022≤-150mmH2O,氢气高压PICA20106≥200mmH2O;2.0万吨/年氯气PICA2001A≥80mmH2O,低压PICA2001A≤-150mmH2O,氢气高压PICA2001B≥500mmH2O;氯氢处理氢气分配台压力≤60KPa)
处理措施:
1、确认报警类别查看最新报警窗口,确认执行哪项报警,通知调度,关闭报警。
2、DCS紧急处理⑴观察氢气放空量,若一路放空量不能满足要求,改为两路放空。
⑵关闭熄火炉的氢气、氯气调节阀(MV=0%)。
了解调度,解除联锁。
3、关阀门⑴.现场关闭炉前的氯气阀门⑵现场关闭送气总阀,打开各炉入降膜阀门,关送气阀门。
4、对置换系统备炉过程⑴停炉自动吹氮气置换系统。
⑵吹氮气15分钟后,DCS工关闭氮气切断阀。
⑶卸氢气插头、卸炉门。
⑷打开接风机阀门关闭尾气放空阀。
开风机。
⑸擦拭视镜。
检查垫子,损坏时更换。
⑹风机抽系统15分钟后,停风机
5、取样分析。
合成工与分析工一起取含氢直至系统含氢≤0.5%。
6、点火前检查现场检查、调试各炉调节阀、切断阀。
确认:
①各炉切断阀动作灵敏、回讯正确;②各炉调节阀动作灵敏、阀门输出现场与中控室一致;③DCS显示数据无异常;火焰监视器上各炉显示清晰、正确。
化验室分析氢气纯度合格,合成炉具备开车条件。
事故现象:
(十三)联锁4台送气炉熄火
事故原因:
1、执行界外联锁熄火(6.0万吨/年离子膜单排停车)
处理措施:
1、确认报警类别查看最新报警窗口,确认执行哪项报警,通知调度,关闭报警。
2、DCS紧急处理⑴迅速将氯气总压降至70Kpa。
⑵迅速调整保留炉配比,确保不过氯。
3、关阀门⑴.现场关闭熄火炉炉前现场氯气阀门。
⑵关闭熄火炉的氢气、氯气调节阀(MV=0)。
4、保留炉改出酸⑴DCS将各保留炉加吸收水,阀门开度MV≥30%,通知班长。
⑵现场确认下酸后,停供合成气改出酸。
。
⑶了解调度,解除各炉联锁。
⑷观察合成炉出口压力为0,吸收水流量有显示时,通知班长。
。
⑸合成工打开出酸阀门。
确认储罐液位、平衡阀、氮气阀门打开。
。
⑹DCS工调节保留炉配比,配比系数≥1.2,合理调节吸收水流量。
5、置换系统备炉过程⑴停炉自动吹氮气置换系统。
⑵吹氮气15分钟后,DCS工关闭氮气切断阀。
⑶卸氢气插头、卸炉门。
⑷打开接风机阀门关闭尾气放空阀。
开风机。
⑸擦拭视镜。
检查垫子,损坏时更换。
⑹风机抽系统15分钟后,停风机。
6、取样分析。
合成工与分析工一起取含氢直至系统含氢≤0.5%。
7、点火前检查现场检查、调试各炉调节阀、切断阀。
确认:
①各炉切断阀动作灵敏、回讯正确;②各炉调节阀动作灵敏、阀门输出现场与中控室一致;③DCS显示数据无异常;火焰监视器上各炉显示清晰、正确。
化验室分析氢气纯度合格,合成炉具备开车条件。
事故现象:
(十四)单台合成炉故障、熄火
事故原因:
1、灯头破漏(灯头检修);2、下酸管(视镜)破漏;3、周期性检查
处理措施:
1、确认待检修炉炉号
2、待检修合成炉停供气改出酸⑴通知该合成炉降流量。
⑵通知合成工序和生产调度。
⑶该合成炉流量降至氯气流量≈150m3/h时,通知班长停合成气。
⑷班长做好准备后,通知DCS工加吸收水(MV≥30%)。
⑸合成工上5楼改吸收水,DCS工观察吸收水流量有显示后通知班长。
⑹班长确认下酸后打开入降膜阀、关闭送气阀,并打开出酸阀门。
3、负荷调节⑴按操作法要求调节送气炉负荷,满足合成需要。
⑵了解化验室复查HCL纯度。
4、降待检修炉负荷⑴DCS工降该合成炉负荷,氯气流量≤100m3/h时,通知班长熄火。
⑵DCS工点击停车按钮,熄火;停吸收水;关闭氯气、氢气调节阀⑶班长关闭炉前氯气阀门以及氯气、氢气总阀,不下酸时,关闭出酸阀门
5、系统置换及处理按照第(十二)、(十三)中系统置换处理步骤操作
6、取样分析7、合成炉检修
事故现象:
(十五)乙炔发生器进人检修,检查搅拌耙子等
处理措施:
原则是切断排渣排气
1、确认电石用完⑴现场用木锤敲击中间贮斗和加料贮斗底部,通过空洞的声音判断无电石,然后打开中间贮斗氮气调节阀前后手阀;⑵DCS工启动加料贮斗振锤,通过声音判断加料贮斗无电石;加大振动筛电流到8A并维持10分钟,观察发生器压力不上涨。
⑶等待30分钟,让发生器内电石全部反应完。
2、撤压后氮排乙炔。
⑴DCS工关闭振动筛,确认加料活门关闭,使中间活门处于开启状态,发生器温度自控阀关闭,打开加料贮斗、中间贮斗放空开关阀撤压,打开加料贮斗、中间贮斗氮气调节阀充氮排气,保证压力在6Kpa以上。
3、现场关闭该发生器二次水阀。
4、断开系统排乙炔。
发生操作工关闭溢流阀,给正逆水封加水,直到正水封取样口有水淌出为止(需要操作工多次开关检查)。
依次打开正逆水封放空阀、发生器本体氮气阀。
5、现场微开排渣活门。
6、排渣冲洗降温,DCS工打开仪表排渣活门排渣,并通过中间贮斗氮气调节阀开度控制发生器压力≥1Kpa,同时打开发生器温度自控阀加自来水冲洗降温。
7、关排渣活门当发生器内无浆料流出后,发生操作工关闭现场排渣活门。
8、恢复氮气开度DCS工调节中间贮斗氮气调节阀开度,保证压力在6Kpa以上。
9、加水排气当发生器液面达80%时,DCS工关闭发生器温度自控阀。
10、DCS工了解化验室取样,同时由工段长了解安全员和环保安全处有关人员到达现场。
11、发生操作工配合取样人员从正水封、中间贮斗取样阀处取样。
12、三方(工段、车间、环保安全处)确认合格(打开系统前30分钟内有效)
13、发生操作工把安全水封放水至液封管0.5米处,利用发生器内部压力排安全水封死角,打开发生器本体放空阀,关闭发生器本体氮气阀。
14、排水发生操作工全开现场排渣活门,排渣到无水流出后,关闭冲渣水,停搅拌耙。
15、关闭氮气DCS工关闭中间贮斗、加料贮斗氮气调节阀,打开加料活门对空;现场关闭加料贮斗、中间贮斗氮气调节阀前后手阀。
16、打开人孔安全员与环保安全处有关人员办理相关手续,班长见到进罐证后方可打开发生器人孔,进人检修。
17、检修结束,恢复人孔,DCS工关闭仪表排渣活门、加料活门、中间活门、加料贮斗放空阀、中间贮斗放空阀。
18、加水排气发生操作工打开二次水阀,DCS工打开发生器温度自控阀加水到50%液面时关闭,发生操作工关闭二次水阀。
19、准备氮气试压现场打开加料贮斗、中间贮斗氮气调节阀前后手阀,关闭发生器本体放空阀,关闭正逆水封放空阀,关闭现场排渣活门。
20、DCS工打开中间贮斗氮气调节阀(30%开度),当压力达到8±0.5Kpa时关闭,维持2分钟。
21、发生器、中间贮斗试漏DCS工观察加料贮斗和发生器压力,如果2分钟内恒定,证明中间活门和发生器试漏合格,否则继续处理中间活门或发生器,直到试漏合格。
22、氮排空气发生操作工依次打开正逆水封放空阀和发生器本体氮气阀,DCS工依次打开中间贮斗放空开关阀和氮气调节阀。
23、取样分析了解化验室取样,配合取样人员从正水封、中间贮斗取样阀处取样。
同时由工段长了解安全员和环保安全处有关人员到达现场,确认合格。
24、发生操作工微开发生器本体放空阀1分钟后关闭,排除发生器死角。
25、关氮气⑴DCS工依次关闭中间贮斗放空开关阀、中间贮斗氮气调节阀;⑵现场关闭中间贮斗氮气调节阀前后手阀。
26、发生器保压现场关闭正逆水封放空阀、发生器本体氮气阀保压6±0.5Kpa。
27、准备开车现场打开现场排渣活门和冲渣水阀,启动搅拌耙,打开二次水阀。
28、乙炔排氮
(1)开启振动筛发生乙炔
(2)打开正逆水封放空阀放空(3)十分钟后,取样分析含乙炔大于98.5%为合格(4)关闭放空阀。
29、发生器并入系统给正逆水封放水到1/2-3/5液面,给安全水封加水到溢流口有溢流,打开溢流阀。
事故现象:
(十六)发生器压力过高
事故原因:
1、气柜卡住或气柜水槽结冰
2.气柜进气管存水过多
3.正水封液面高
4.振动筛电流太大,电石加入量过多
5.压力计管内存水或结冰
6.冷却塔堵塞
7.预冷器下水管堵塞
处理措施:
1.检修气柜滑轮或向水槽内通蒸汽,将冰溶化
2.放掉气柜进气管存水
3.放至水规定液面
4.停止振动筛运转
5.疏通压力计
6.停车检修
7.停车疏通
事故现象:
(十七)合成工序转化器单组转化器转化后含乙炔≥3%;转化器进气阀门全开;四个测温点温度下降到115℃以下;转化器压差偏高
事故原因:
1、触媒活性降低或分布不均
处理措施:
抽翻触媒,具体操作如下(以一串一连接的转化器为例):
1、断开系统依次关闭该组转化器的主物料进出口阀和待打开转化器的热水进出口阀。
2、撤压打开两台转化器放酸口,撤至平压。
3、排放打开待处理转化器热水放净口和放气孔。
4、氮排氯乙烯从两台转化器顶部各接一氮气软管连续通入氮气。
5、抽电阻体由仪表人员将转化器上的电阻体摘除。
6、化验室取样分析VC含量≤0.2%后,通知环保安全处有关人员到达现场。
7、加盲板确认给抽翻触媒的转化器主物料进出口阀加盲板。
8、关闭氮气阀和底部放酸阀,通知触媒班长。
9、拆除上封头由检修人员缓慢地将上封头吊离转化器。
10、启动真空泵触媒班人员确认抽管安装到真空管路上,开启真空泵,进行抽翻触媒。
11、触媒收集抽到触媒储槽内的触媒经分离筛分离除去粉末后,装入袋中备用。
12、回装触媒确认触媒符合回装条件后,检修人员先将四个测温点套管用袋状物堵住,将触媒均匀的倒入列管中。
装满列管后,将一定量的旧触媒倒入转化器列管顶部,到列管上方一定厚度。
(说明:
如抽翻触媒回装时不够,可添加一些原来抽翻的旧触媒。
严禁填加新触媒。
)
13、回装上封头触媒回装完毕后,将堵套管的袋状物拿出。
垫好胶垫,回装上封头。
14、回装电阻体由仪表人员对电阻体进行回装。
15、氮排空气打开氮气阀,进行氮排空气操作。
16、通知化验人员从放酸口取样,直到分析含氧≤3%为合格。
17、撤去所加盲板,确认关闭放酸口和氮气阀保压。
依次打开各热水阀和主物料进出口阀。
事故现象:
(十八)出现第(十七)现象,经抽翻触媒后,约一周左右有重复出现以上现象,且转化后含乙炔≥30%
事故原因:
触媒失去活性
处理措施:
更新触媒,具体操作参照第第(十七)现象处理。
事故现象:
(十九)合成停车
事故原因:
1、计划停车
2、联锁停车
处理措施:
1、按照计划下调运行负荷①降流量到2000m3/h左右;②摘除低流量联锁开关。
2、DCS人员①把乙炔回流阀置于手动,配比投到“无效”;②关混合器乙炔电磁阀,迅速打开水洗放空开关阀。
3、合成岗位操作工①打开水洗放空现场阀;②关进碱洗塔阀门;③关乙炔预冷器入口蝶阀。
4、DCS人员①通知氯化氢DCS停送氯化氢;②关闭水洗去泡沫塔调节阀;③无氯化氢流量显示后,手动关闭混冷器和深冷器温度调节阀。
5、合成岗位操作工关闭混冷器和深冷器的温度调节阀前手阀;关闭乙炔预冷器盐水阀。
6、如果合成短时停车,在停乙炔后,DCS人员①关闭水洗往泡沫塔的流量调节阀;②打开水洗液封阀门,控制好水洗液面。
7、如果合成停车时间较长,DCS按“6”操作后,合成岗位操作工①关闭密闭泵出口阀;②停密闭泵电机;③停碱泵。
事故现象:
(二十)聚合釜反应过程釜压超标
事故原因:
1、配方(引发剂量多、填充比过大、分散剂量不足或含固量不足等)。
以下因素基本都是由于温度上升而导致压力上涨(温度越高,饱和蒸汽压越高)。
2、循环水总管温度高:
传热差。
3、单向阀脱落:
循环水走近路。
4、循环水压力低:
循环水供给量不足。
5、循环水泵故障停转:
循环水量不足。
6、换热系统结垢较多:
影响传热。
7、换热系统有杂物:
底夹套淤泥或内冷管内存在阻挡物(也与内部结构有关)。
8、热水阀门不严:
如果泵压高会造成二次升温。
9、搅拌停转。
10、单体质量有问题:
偏酸或含乙炔等。
11、中间注水量过多,导致气相空间小。
12、抽真空不合格,气相空间存在大量惰性气体。
13、程序问题:
如阀门开启滞后。
处理措施:
1、主控室停止升温,打开循环水调节阀。
2.现场打开循环水支路阀降温(停电则开自来水)。
3.检查处理①立即到现场检查搅拌是否停转,如果停转立即再次启动,如果无法启动或启动后釜压继续上涨,则立即加紧急终止剂;
②除搅拌原因外,其它情况全部按加紧急终止剂处理;
③检查喷淋水阀及终止剂罐高压水阀都关闭。
4、加紧急终止剂操作:
①打开紧急终止剂罐平衡阀;②打开紧急终止剂罐根部阀;③打开单体分配台平衡阀;④打开单体分配台的根部阀。
5、空釜平衡如果压力继续上升,①观察有空釜则进行空釜平衡;②通知聚合操作工放空撤压。
6、放空撤压:
聚合操作工缓慢反复打开放空阀撤压到0.9Mpa以下。