试样加工作业指导书.docx
《试样加工作业指导书.docx》由会员分享,可在线阅读,更多相关《试样加工作业指导书.docx(12页珍藏版)》请在冰豆网上搜索。
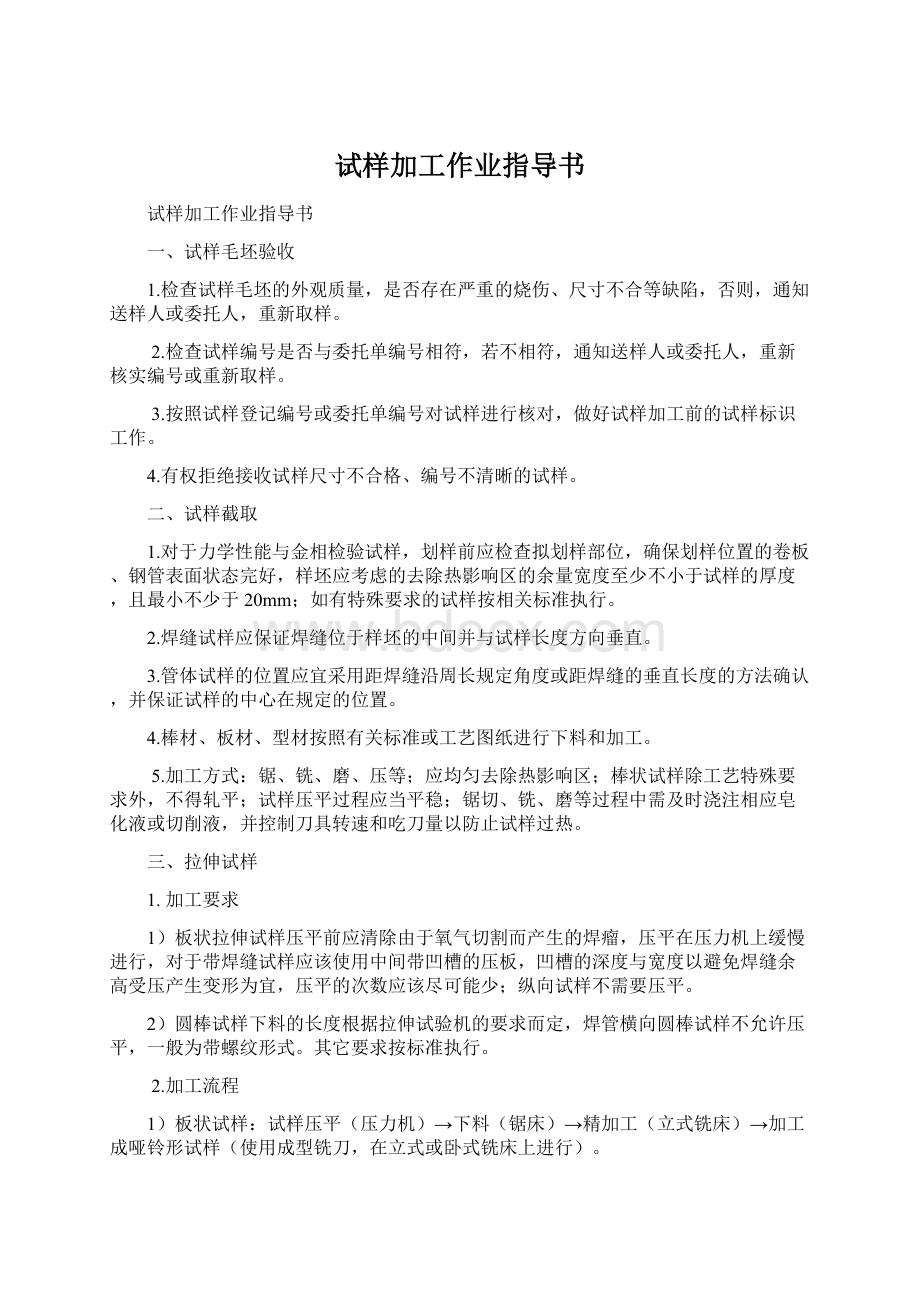
试样加工作业指导书
试样加工作业指导书
一、试样毛坯验收
1.检查试样毛坯的外观质量,是否存在严重的烧伤、尺寸不合等缺陷,否则,通知送样人或委托人,重新取样。
2.检查试样编号是否与委托单编号相符,若不相符,通知送样人或委托人,重新核实编号或重新取样。
3.按照试样登记编号或委托单编号对试样进行核对,做好试样加工前的试样标识工作。
4.有权拒绝接收试样尺寸不合格、编号不清晰的试样。
二、试样截取
1.对于力学性能与金相检验试样,划样前应检查拟划样部位,确保划样位置的卷板、钢管表面状态完好,样坯应考虑的去除热影响区的余量宽度至少不小于试样的厚度,且最小不少于20mm;如有特殊要求的试样按相关标准执行。
2.焊缝试样应保证焊缝位于样坯的中间并与试样长度方向垂直。
3.管体试样的位置应宜采用距焊缝沿周长规定角度或距焊缝的垂直长度的方法确认,并保证试样的中心在规定的位置。
4.棒材、板材、型材按照有关标准或工艺图纸进行下料和加工。
5.加工方式:
锯、铣、磨、压等;应均匀去除热影响区;棒状试样除工艺特殊要求外,不得轧平;试样压平过程应当平稳;锯切、铣、磨等过程中需及时浇注相应皂化液或切削液,并控制刀具转速和吃刀量以防止试样过热。
三、拉伸试样
1.加工要求
1)板状拉伸试样压平前应清除由于氧气切割而产生的焊瘤,压平在压力机上缓慢进行,对于带焊缝试样应该使用中间带凹槽的压板,凹槽的深度与宽度以避免焊缝余高受压产生变形为宜,压平的次数应该尽可能少;纵向试样不需要压平。
2)圆棒试样下料的长度根据拉伸试验机的要求而定,焊管横向圆棒试样不允许压平,一般为带螺纹形式。
其它要求按标准执行。
2.加工流程
1)板状试样:
试样压平(压力机)→下料(锯床)→精加工(立式铣床)→加工成哑铃形试样(使用成型铣刀,在立式或卧式铣床上进行)。
①去除毛坯样上的气割焊瘤,把试样放到压力机上进行压平,压力机压平试样时应缓慢进行,对于带焊缝试样应该使用中间带凹槽的压板,凹槽的深度与宽度以避免焊缝余高受压产生变形,压平的次数应该尽可能少。
②试样压平后,按要求画出试样锯削加工的中心线(宽度方向轮廓线)、轮廓线尺寸(从单侧起),留出精加工的加工量。
上锯床进行下料作业,去除试样上的热影响区(两侧各去除不小于试样厚度的一倍,且最小不小于20mm),这道工序最好为冷加工,在没有锯床的情况下也可以用立式铣床等其他加工设备,但必须保证试样在加工过程中不得过热影响试样性能。
③夹持试样,均匀分配加工余量,锯切试样到要求的尺寸,并根据试样编号清晰对棒状及板状试样编号;根据图纸要求上立式铣床进行精加工,直到试样尺寸符合标准要求。
④试样精加工后,使用成型铣刀在立式或卧式铣床上加工试样工作部分,加工后检查试样是否符合标准要求,如不符合标准要求则需返工或报废,报废后须按标准重新取样。
2)圆棒试样:
下料(锯床)→确定试样端面的顶尖中心并钻孔(卧式车床或摇臂钻床)→车削圆棒试样(卧式车床)。
①去除毛坯样上的气割焊瘤,然后上锯床进行下料作业,去除试样上的热影响区(两侧各去除不小于试样厚度的一倍),加工成方形毛坯样。
②确定试样端面的顶尖中心后在车床上(或摇臂钻床)钻出中心孔。
③试样上车床进行车削加工试样工作部分并加工出丝扣,直至符合图纸要求。
3.板状试样加工
1)压平试样:
用压样机压平试样。
2)铣削:
按要求试样铣削加工的的轮廓线320×50×t(mm)。
3)铣削试样:
按照技术规范铣削试样缩减段长度到规定尺寸。
4)修磨试样:
用锉刀或纸砂轮去除试样的毛边。
4.棒状试样加工(以Φ12.7mm缩减段为例)
1)管体或钢板或卷板展平试样
①锯切:
管体纵向及钢板或卷板展平试样锯成要求尺寸(一般130×20×厚度t(mm))。
②中心孔定位:
利用车床三爪装夹,打中心孔。
③车削:
采用一夹一顶的加工方法,把四方原料试样加工成Φ16mm圆棒。
④挑扣:
采用中间装夹两头挑扣的工艺方法完成M16的加工。
⑤车削缩减段:
使用铜皮垫扣等方式的装夹完成Φ12.7mm缩减段部分的加工。
⑥修磨试样:
用砂纸打磨试样缩减段以保证试样粗糙度。
⑦标记:
用记号笔或粘性标签标记试棒。
2)管体横向检验试样
①将试样标注编号写入指定标签纸上,并于车削后将标签纸贴与对应试样上。
②锯切:
管体横向及卷板展平试样锯成130×20×t(mm)尺寸试样。
③中心孔定位:
在原料试样加3.5mm厚的工装平垫,使原料试样圆弧中心线上移,达到可以加工两头M16、中间Φ12.7mm、总长130mm的加工标准,打中心孔。
④车削:
采用一夹一顶的加工方法,把四方原料试样加工成Φ16mm圆棒。
⑤挑扣:
采用中间装夹两头挑扣的工艺方法完成M16的加工。
⑥车削缩减段:
使用铜皮垫扣等方式的装夹完成Φ12.7mm缩减段部分的加工。
⑦修磨试样:
用砂纸打磨试样缩减段以保证试样粗糙度。
⑧标记:
用记号笔或粘性标签标记试棒。
4.焊缝试样
1)去除切割造成的铁瘤。
2)压平试样:
用压样机压平试样。
3)划线:
按要求画出试样锯削加工的中心线,长、宽的轮廓线(试样长轴垂直于焊缝),轮廓线尺寸320×50×t(mm)。
4)锯切试样:
夹持试样(试样长轴垂直于焊缝),均匀分配加工余量,锯切试样到要求的尺寸。
5)铣削:
按要求试样铣削加工的的轮廓线。
7)铣削试样:
按照技术规范铣削试样缩减段长度到规定尺寸。
8)修磨试样:
用锉刀或纸砂轮去除试样的毛边。
四、夏比冲击试样
41.加工要求
1)在锯床下料后在铣床上铣到要求上磨床的厚度,再上锯床或卧铣和磨床进行加工,以保证试样长度,垂直度及后续加工。
2)试样的缺口加工使用与试样缺口形状尺寸一致的成型拉刀拉削出缺口,拉出缺口后用冲击缺口投影仪检查缺口形状及尺寸,以保证试样缺口符合标准要求。
3)对于焊缝及热影响区试样,按照有关标准铣削外焊缝后,腐蚀(3%~10%的硝酸酒精溶液)后划出焊缝和热区的缺口位置线,然后进行加工。
4)试样尺寸及精度要求执行有关标准。
2.加工流程
1)管体及钢板:
划线下料(锯床)→精加工和两面铣平(立式铣床)→锯成条状(卧式铣床或锯床)→磨削试样(平面磨床)→缺口加工(工具磨床或专用拉床)。
①去除毛坯样上的气割焊瘤,在坯样上做好标记,然后划出试样中心线及外轮廓线,锯床切割加工去除热影响区部分并留有加工余量。
②将试样置于立式铣床进行精加工,去除试样两面多余部分,留出磨削余量。
③将试样置于卧式铣床或锯床切成条状并在试样两端做好标记(注意留出磨削余量)。
④将切成条状的试样置于磨床进行磨削加工,直至符合标准要求。
。
2)焊缝试样:
划线下料(锯床)→精加工和两面铣平(立式铣床)→锯成条状(锯床或卧铣)→缺口腐蚀、划线,试样加工到规定长度→磨削试样(平面磨床)→缺口加工(工具磨床或专用拉床)。
①去除毛坯样上的气割焊瘤,在坯样上做好标记,按要求画出试样锯削加工的中心线,长、宽的轮廓线(焊缝及热影响区冲击试样应使试样长轴平行于焊缝),轮廓线尺寸t×55×l(mm);锯床切割加工去除试样两面及端部热影响区部分。
②将试样置于立式铣床进行精加工,去除试样外焊缝至标准要求后,用3%~10%的硝酸酒精溶液浸蚀至显出外焊缝轮廓,划出试样轮廓并去除两面多余部分,留出磨削余量。
③将试样置于卧式铣床或锯床切成条状并在试样两端做好标记,切削试样为条状,一般为3条。
试样尺寸为t×55×10.5(mm);t一般为5.5mm、8mm、10.5mm。
④将切成条状的试样置于磨床进行磨削加工,直至符合标准要求。
五、落锤撕裂试样
1.加工要求
1)试样展平应使用压力机缓慢压平,如果出现试样中部下凹的情况,则应先从试样两端开始压,对于出现落锤试验不合格的情况,应按APIRP5L3:
1996的规定只将试样两端部分压平而保持试样中部为原始弧面。
2)在锯床下料后宜设精加工工序,以保证试样长度,垂直度及后续加工。
3)对于标准规定需要采用人字型缺口的情况,压制缺口工序则由加工人字型缺口代替。
4)试样尺寸及精度要求执行有关标准。
2.加工流程试样展平(压力机)→下料(锯床)→精加工(立式铣床)→压制缺口(采用万能试验机或专用缺口压制装置)。
1)去除毛坯样上的气割焊瘤,在坯样上做好标记,放置压力机上进行缓慢压平,如果出现试样中部下凹的情况,则应先从试样两端开始压,对于出现落锤试验不合格的情况,应按APIRP5L3:
1996的规定只将试样两端部分压平而保持试样中部为原始弧面。
然后在工作台上划出试样中心线及外轮廓线。
2)按要求画出试样锯削加工的中心线,长、宽的轮廓线(焊缝及热影响区冲击试样应使试样长轴平行于焊缝),轮廓线尺寸t×90×305(mm)。
3)锯切、铣削试样:
夹持试样(焊缝拉伸试样应使试样长轴垂直于焊缝),均匀分配加工余量,锯切试样到要求的尺寸,然后在铣床上将试样铣削到规定尺寸:
t×76×305(mm)。
六、导向弯曲试样
1.加工要求
1)试样的压平应在压力机上缓慢进行,对于焊接接头试样应该使用中间带凹槽的压板,凹槽的深度与宽度以避免焊缝余高受压产生变形为宜,压平的次数应该尽可能少。
2)在锯床下料后宜设精加工工序,以保证试样长度,垂直度及后续加工。
3)对于焊接接头试样,试样的焊缝余高在铣削后可能存在与母材没有良好过渡,则采用角磨机(纸质砂纸)修磨,并且磨痕应与试样长度方向平行。
4)试样尺寸及精度要求执行有关标准。
2.加工流程试样展平(压力机)→下料(锯床)→精加工(立式铣床)→去掉焊缝余高(立式铣床或卧式铣床)。
1)去除毛坯样上的气割焊瘤,在坯样上做好标记,放置压力机上进行缓慢压平,对于焊缝试样应使用中间带凹槽的压板,凹槽的深度与宽度以避免焊缝余高受压产生变形为宜,压平的次数应该尽可能少。
2)使用锯床去除试样热影响区,去除部分不得小于一个试样璧厚,且留有5~10mm加工余量。
3)使用立式铣床进行精加工至试样标准尺寸。
4)使用卧铣和角磨机(纸质砂纸)去除、修磨焊缝余高。
七、硬度试样、金相、化学分析试样
1.加工要求
1)在锯床下料后宜设精加工工序,以保证试样长度,垂直度及后续加工。
2)试样尺寸及精度、以及截取位置要求执行有关标准。
3)晶粒度和显微组织试样观察面一般和轧制方向垂直、带状组织和夹杂物试样观察面一般和轧制方向平行。
2.加工流程下料(锯床)→精加工(立式铣床)→磨削试样(平面磨床)。
化学分析试样一般不经磨床工序。
1)去除毛坯样上的气割焊瘤,在坯样上做好标记,使用锯床去除试样热影响区,去除部分不得小于一个试样璧厚,且留有5~10mm加工余量。
2)加工前要检查试样的位向、数量,试样推荐加工尺寸:
圆形,φ10~12mm;方形,边长10×10mm;卷板,板厚×20mm。
3)使用立式铣床进行精加工并留有适当磨削余量。
4)试样置于磨床进行磨削加工,直至符合标准要求。
5)定碳定硫用粉末试样,需用铣床进行铣削,注意试样的碎屑要均匀、洁净,防过烧、防油污、防杂物混入等,并用试样袋做好试样标拉伸试验作业指导书
一、试样验收
1.检查试样的外观质量,是否存在严重的烧伤、尺寸不合等缺陷,否则,通知有关人员重新取样或加工。
2.检查试样编号是否与委托单编号相符,若不相符,通知送样人或委托人,重新核实编号或重新取样。
3.按照试样登记编号或委托单编号对试样进行核对,并做好记录。
二、试验
1.试验前要检查试验机工作是否正常。
2.复核试样尺寸和加工质量:
试样的尺寸进行复核测量,是否符合标准要求;试样是否有加工缺陷或气孔、夹渣等材料缺欠(无论是在试验前还是在试验后发现,均可将该试样作废,并从同一根钢管上另取试样代替)并记录,如果不合格,应重新加工。
3.试样划线
1)在试样上划出中心线。
2)以试样中心线为中心,划出原始原始标距线,原始标距的长度符合相应技术规范规定。
4.试样尺寸的测量
1)根据横截面尺寸选择合适的量具,0.1~10mm,选用千分尺,大于10mm,选用游标卡尺,在标距两端及中间处分别测量,取三处测得横截面积的平均值。
矩形试样横截面积按公式计算。
2)记录试样的编号、标距L0、原始尺寸等数据。
5.试验
1)打开试验机及微机系统,启动试验程序;
2)选择合适的量程及引伸计型号,输入检验项目、试样编号、试验的原始尺寸、试样原始标距等。
3)夹持试样:
把试样放入钳口,使试样的中心与拉伸试验机的拉伸轴线重合,按动上钳口夹紧按钮,使上钳口夹紧试样,试样的夹持部分要在钳口的3/4以上,把微机的拉力值清零,按动下钳口夹紧按钮,使下钳口夹紧试样。
4)安装引伸计。
5)试样加载:
选择适宜的速率控制方式和加载速率对试样加载,按微机程序的试验按钮,注意观察试验曲线;当有卸掉引伸计提示时卸掉引伸计,继续加载,一直到试样被拉断。
6)卸下试样,把试样对好,测量试样的断后标距Lu,输入微机,记录屈服力、最大力、断后延伸率等数据。
7)按照技术规范要求评定试验结果。
8)试验完毕,关闭微机系统和拉伸试验机电源;如发生打滑现象,该试验无效,重新取样,清理钳口并喷涂二硫化钼,然后在确认不打滑后重新试验。
只要发现试样有加工缺陷或与相应性能试验无关的材料缺欠(如气孔、夹渣等),无论是在试验前还是在试验后发现,均可将该试样作废,并从同一根钢管上另取试样代替。
9)填写试验原始记录。
三、填写试验报告
1.试验报告单要由Ⅰ级或Ⅰ级以上资格的人按照试验原始记录认真填写;
2.试验报告经Ⅱ级或Ⅱ级以上资格的人审核才能发出。
弯曲试验作业指导书
一、试样验收
1.检查试样的外观质量,是否存在严重的烧伤、尺寸不合等缺陷,否则,通知有关人员重新取样或加工;
2.检查试样编号是否与委托单编号相符,若不相符,通知送样人或委托人,重新核实编号或重新取样;
3.按照试样登记编号或委托单编号对试样进行核对,并做好记录。
二、试验
1.试验前要检查试验机工作是否正常。
2.复核试样尺寸和加工质量:
试样的尺寸进行复核测量,是否符合标准要求;试样是否有加工缺陷或气孔、夹渣等材料缺欠(无论是在试验前还是在试验后发现,均可将该试样作废,并从同一根钢管上另取试样代替)并记录,如果不合格,应重新加工
3.弯曲:
选择合适的阴模与压头,安装阴模与压头;或选择合适的压头、调节弯曲用间距。
打开试验机,放好试样,把试样弯曲到规定的角度
4.在弯曲过程中,注意试样的变化,若出现裂纹、裂缝或断裂,停止试验,记录出现裂纹的角度。
5.按照技术规范规定评定试验结果;只要发现试样有加工缺陷或与相应性能试验无关的材料缺欠(如气孔、夹渣等),无论是在试验前还是在试验后发现,均可将该试样作废,并从同一根钢管上另取试样代替。
6.试验完毕,关闭试验机电源;
7.填写试验原始记录。
三、填写试验报告
1.试验报告单要由Ⅰ级或Ⅰ级以上资格的人按照试验原始记录认真填写;
2.试验报告经Ⅱ级或Ⅱ级以上资格的人审核才能发出。
冲击试验作业指导书
一、试样验收
1.检查试样的外观质量,是否存在严重的烧伤、尺寸不合、粗糙度不合等缺陷,否则,通知有关人员重新取样或加工。
2.检查试样编号是否与委托单编号相符,若不相符,通知送样人或委托人,重新核实编号或重新取样。
3.按照试样登记编号或委托单编号对试样进行核对,并做好记录。
二、试样制备
开缺口:
焊缝及热影响区试样经腐蚀后(母材试样不用腐蚀),焊缝轮廓要清晰可见,在缺口拉床上拉缺口,第一个缺口要在投影仪上检查,如果不合格,应找出原因,经解决,检查合格后,才能继续加工。
三、试验
1.试验前要检查试验机工作是否正常。
2.复核试样尺寸:
用游标卡尺或千分尺测量试样的尺寸,复核是否符合标准要求,并记录,如果不合格,应重新取样加工。
3.校核试验机:
打开冲击试验机,先进行空打试验,检查摆锤空打时被动指针的回零差,不应超过最小分度值的四分之一。
4.冷却和保温试样:
把试样和试样钳放入装有酒精的低温槽中,盖上盖对试样进行冷却,根据标准设置冷却温度和保温时间。
室温推荐温度为20±5℃,液体介质温度与要求的试验温度的偏差不得大于±1℃,在规定的试验温度下保温时间最少5min;如采用气体介质冷却,则在规定的试验温度下保温时间最少30min。
控制好不同冷却温度范围的过冷度。
5.冲击:
试验条件合格后,用试样钳把试样放入冲击试验机,按冲击按钮,记录冲击吸收功、试验温度。
在合适位置按扬摆按钮,升起摆锤,使指针到最大值,取出冲断试样,进行下一次试验。
当试验不在室温进行时,试样从高温或低温装置中移出至打断的时间不大于5s,否则,重新把试样冷却足够时间后重新冲击。
6.断口评定:
依据有关标准或技术规范进行评定。
只要发现试样有加工缺陷或与相应性能试验无关的材料缺欠(如气孔、夹渣等),无论是在试验前还是在试验后发现,均可将该试样作废,并从同一试件上另取试样代替。
7.试验结果评定:
按照技术条件。
8.试验完毕,使摆锤处于最低位置,关闭冲击试验机电源。
9.填写试验原始记录。
四、填写试验报告1.试验报告单要由Ⅰ级或Ⅰ级以上资格的人按照试验原始记录认真填写。
2.试验报告经Ⅱ级或Ⅱ级以上资格的人审核才能发出。
落锤试验作业指导书
一、试样验收
1.检查试样的外观质量,是否存在严重的烧伤、尺寸不合等缺陷,否则,通知有关人员重新取样或加工。
2.检查试样编号是否与委托单编号相符,若不相符,通知送样人或委托人,重新核实编号或重新取样。
3.按照试样登记编号或委托单编号对试样进行核对,并做好记录。
二、试验
1.试验前要检查试验机工作是否正常。
2.复核试样尺寸:
复核是否符合标准要求,并记录;如果不合格,应重新取样加工。
3.压制缺口:
使用卷尺或板尺确定试样长度方向中心线,用记号笔或不影响试验结果的标识方式在试样宽度方向缺口压制侧距离端面5mm画一条端面的平行线作为试样V型缺口压制的终止线,使用专用缺口压制/铣削装置或万能试验机压制/铣削缺口。
4.冷却和保温试样:
把试样和试样钳放入装有酒精的低温槽中,盖上盖对试样进行冷却,根据标准设置冷却温度和保温时间。
液体介质温度与要求的试验温度的偏差不得大于±1℃。
锤击:
用试样钳把试样放入落锤试验机,使试样对中,按动“落锤”按钮使锤头自由下落,将试样冲断。
按下降按钮,进行下一次试验,试样从浴槽中取出至用锤击断的时间应在10s内完成;否则,重新把试样冷却保温至少10min后重新冲击。
试验机冲击试样时对应锤体的高度在1.28m~4.14m之间。
6.断口评定:
按照有关标准或技术规范评定。
只要发现试样有加工缺陷或与相应性能试验无关的材料缺欠(如气孔、夹渣等),无论是在试验前还是在试验后发现,均可将该试样作废,并从同一根钢管上另取试样代替。
7.试验结果判定:
按照产品技术条件。
8.试验完毕,关闭落锤试验机电源。
9.填写试验原始记录。
三、填写试验报告单
1.试验报告单要由Ⅰ级或Ⅰ级以上资格的人按照试验原始记录认真填写。
2.试验报告经Ⅱ级或Ⅱ级以上资格的人审核才能发出。
金相检验作业指导书
一、试样验收
1.检查试样的外观质量,是否存在严重的烧伤、灰尘、油污、生锈、霉变等缺陷,检查试样是否达到粗糙度要求,检查试样尺寸是否达到要求;否则,通知有关人员重新取样或加工。
2.检查试样编号是否与委托单编号相符,若不相符,通知送样人或委托人,重新核实编号或重新取样。
3.按照试样登记编号或委托单编号对试样进行核对,并做好记录。
二、试样制备
1.用砂轮或砂纸去除磨削造成的毛刺。
2.粗细磨:
在金相磨样机上依次用180#、400#、1000#、1200#(也可添加中间号数砂纸)砂纸磨制试样。
每道砂纸磨后,试样的磨痕应均匀一致;注意不可用力太重,每次时间不得太长。
3.抛光:
在金相抛光机上抛光试样,抛光过程中加入适量抛光粉剂或抛光剂(规格:
3或5μm),抛去试样上的磨痕;抛光后用水洗净并吹干。
4.浸蚀(不含带状和夹杂物试样)试样:
用棉花沾蘸无水乙醇溶液,擦拭试样,吹干;然后将试样放入3~5%的硝酸酒精(或其它相适宜的腐蚀液)溶液中,并且不停的在棉花上移动试样,一般浸蚀15~20s,直到待观察体的轮廓清晰可见;移出试样,用棉花沾蘸无水乙醇溶液擦拭试样,吹干。
若试样浸蚀过浅,可重新浸蚀;若过深则要重新抛光再浸蚀试样。
三、试验
1.观察环境条件是否符合要求,合格后开启总电源。
依次接通显示器、打印机、主机、显微镜主机电源。
2.复核试样编号:
观察试样编号,看试样编号是否清晰,否则,按照来样登记本重新编号。
3.把制备好的试样小心放在载物台上,小心调节焦距,先粗调、后细调,进行对焦,严防试样碰及物镜镜头,焦距到位后,调节亮度调节旋扭,选择最佳的观察亮度,用前后左右调节旋钮进行调节,以便观察试样不同部位的组织及变化。
4.根据标准,观察组织、夹杂物、晶粒度、带状组织以及断口形貌、缺陷等项目,并给以判级。
需拍照片的,应选择合适的放大倍数、适当的亮度、试样的适当的部位,然后选择控制器中照片的标尺、曝光时间等,调整显微镜焦距,使显示的组织清晰,按照相按钮,并及时在计算机中给以提取、存储和打印。
物镜转换时应仔细、缓慢,勿使物镜碰及试样;
5.分析结束后,切断电源,清理卫生,待显微镜机身冷却之后罩上防尘罩。
6.试验结果评定,并填写试验原始记录。
四、填写试验报告单
1.试验报告单要由Ⅰ级或Ⅰ级以上资格的人按照试验原始记录认真填写。
2.试验报告经Ⅱ级或Ⅱ级以上资格的人审核才能发出。
硬度试验作业指导书
一、试样验收
1.检查试样的外观质量,是否存在严重的烧伤、灰尘、油污、生锈、霉变等缺陷,检查试样是否达到粗糙度要求,检查试样尺寸是否达到要求;否则,通知有关人员重新取样或加工。
2.检查试样编号是否与委托单编号相符,若不相符,通知送样人或委托人,重新核实编号或重新取样。
3.按照试样登记编号或委托单编号对试样进行核对,并做好记录。
二、试样制备
1.用砂轮或砂纸去除磨削造成的毛刺。
2.粗细磨:
在金相磨样机上依次用180#、400#、1000#、1200#(也可添加中间号数砂纸)砂纸磨制试样。
每道砂纸磨后,试样的磨痕应均匀一致;注意不可用力太重,每次时间不得太长。
3.抛光:
在金相抛光机上抛光试样,抛光过程中加入适量抛光粉剂或抛光剂(规格:
3或5μm),抛去试样上的磨痕;抛光后用水洗净并吹干。
4.浸蚀试样:
用棉花沾蘸无水乙醇溶液,擦拭试样,吹干;然后将试样放入3~5%的硝酸酒精(或其它相适宜的腐蚀液)溶液中,并且不停的在棉花上移动试样,一般浸蚀15~20s,直到待观察体的轮廓清晰可见;移出试样,用棉花沾蘸无水乙醇溶液擦拭试样,吹干。
若试样浸蚀过浅,可重新浸蚀;若过深则要重新抛光再浸蚀试样。
三、试验1.观察环境条件是否符合要求,合格后开启总电源。
依次接通显示器、打印机、主机、显微镜主机电源。
2.复核试样编号:
观察试样编号,看试样编号是否清晰,否则,按照来样登记本重新编号。
3.检查试样支撑面、压头表面及试台是否清洁。
试样是否能稳固地放置于试台上,否则进行调整。
4.按照工艺或标准要求压痕位置进行硬度试验。
5.按照仪器使用规程对试样加载、保压、卸载、观