B0503造型工岗位操作规程铸铁件部分.docx
《B0503造型工岗位操作规程铸铁件部分.docx》由会员分享,可在线阅读,更多相关《B0503造型工岗位操作规程铸铁件部分.docx(12页珍藏版)》请在冰豆网上搜索。
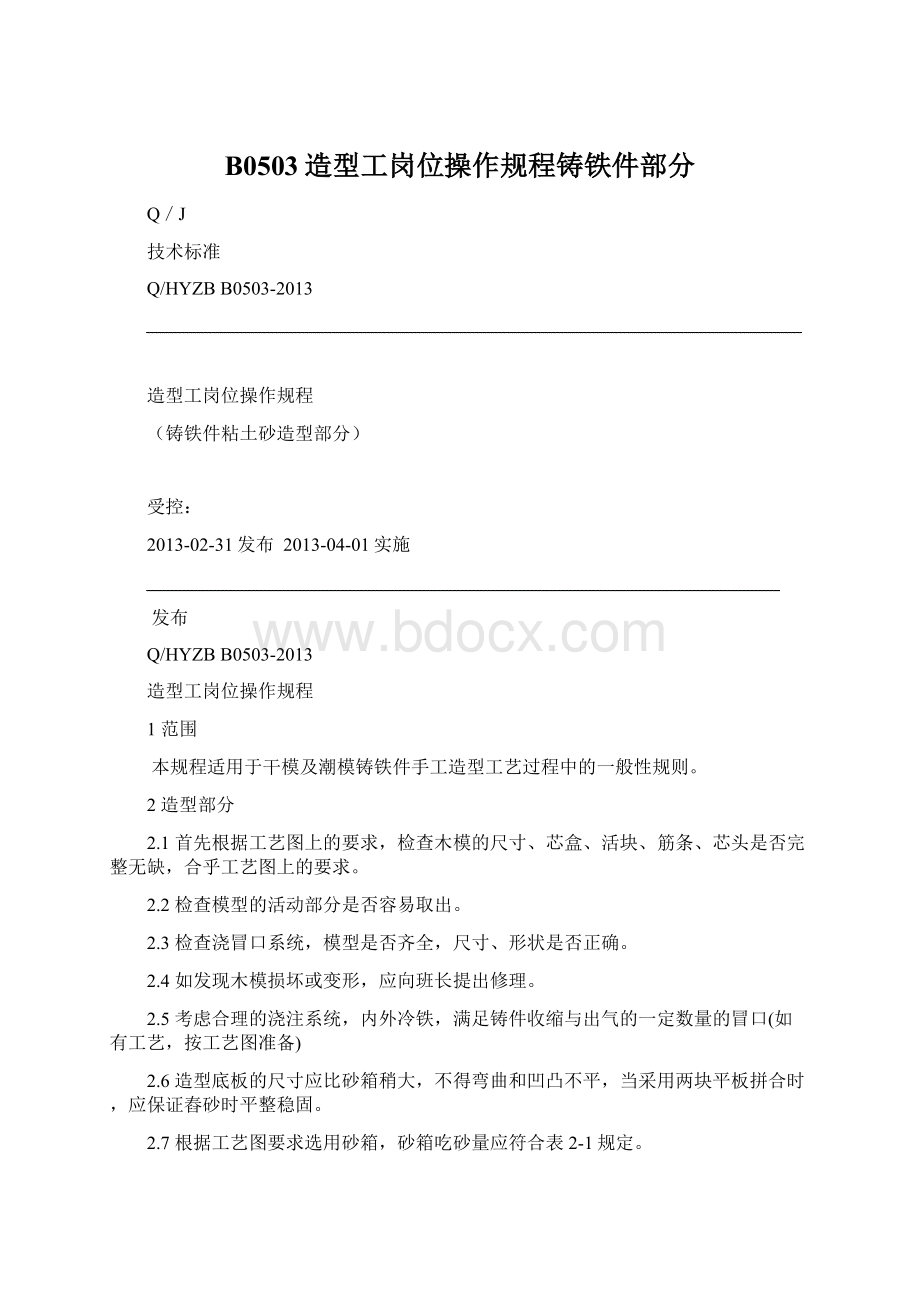
B0503造型工岗位操作规程铸铁件部分
Q/J
技术标准
Q/HYZBB0503-2013
造型工岗位操作规程
(铸铁件粘土砂造型部分)
受控:
2013-02-31发布2013-04-01实施
发布
Q/HYZBB0503-2013
造型工岗位操作规程
1范围
本规程适用于干模及潮模铸铁件手工造型工艺过程中的一般性规则。
2造型部分
2.1首先根据工艺图上的要求,检查木模的尺寸、芯盒、活块、筋条、芯头是否完整无缺,合乎工艺图上的要求。
2.2检查模型的活动部分是否容易取出。
2.3检查浇冒口系统,模型是否齐全,尺寸、形状是否正确。
2.4如发现木模损坏或变形,应向班长提出修理。
2.5考虑合理的浇注系统,内外冷铁,满足铸件收缩与出气的一定数量的冒口(如有工艺,按工艺图准备)
2.6造型底板的尺寸应比砂箱稍大,不得弯曲和凹凸不平,当采用两块平板拼合时,应保证舂砂时平整稳固。
2.7根据工艺图要求选用砂箱,砂箱吃砂量应符合表2-1规定。
2.8箱带下端与木模有一定吃砂量,一般铸件为25~40mm,大件为40~80mm。
2.9砂箱各部分的氧化铁皮、残余干砂和铁水渣在使用前必须清理干净。
2.10砂箱如发现箱壁或箱带断裂(箱带指大箱带),缺少吊轴或吊轴有裂纹,箱带妨碍浇冒口的正确位置等不能使用,箱带与直浇冒口、冒口间的距离,不得小于30mm。
表2-1手工造型的吃砂量mm
铸型
类型
砂箱内平均尺寸
(长×宽)/2
模样至砂箱
内壁尺寸
浇道冒口至
砂箱内壁尺寸
模样顶部至
箱带底部尺寸
干模
<500
>40~50
>30
15~20
500~1000
60~100
>60
20~25
l0OO~2000
100~150
>100
25~30
2000~3000
150~200
>120
30~40
>3000
>250
>150
>40
潮模
<300
>30
>40
>30
300~800
>60
>60
>50
>800
>100
>100
>70
2.11打箱后的热砂箱不能使用。
2.12为了使铸型牢固地附在砂箱内,可在砂型内壁和箱带上涂上泥浆水。
2.13准备造型,选择面砂、背砂和加强砂型强度的铁丝铁棒等。
2.14摆木模时,泥芯头安放出气孔,在适当的地方放好出气位置。
2.15按工艺规定的位置、数量、尺寸,放浇冒口和冷铁、泥芯撑(冷铁、泥芯撑必须除锈)。
2.16为了方便起模,应事先考虑好吊盘的位置和方向。
2.17填砂前应将模型和底板打扫干净,如有型砂粘附模型时,应用麻头或棉纱浸煤油擦净。
2.18一般铸件面砂的厚度为20~35mm,特殊要求的另外规定。
车板造型必须先车转背砂,再车转面砂,面砂的厚度为30~40mm。
2.19型砂内插入浸附泥浆的金属钩子时,钩子距木模表面8~lOmm,并且应牢固地挂在箱带上且不过高的突出型砂面外,钩子的数量、安置位置,应保证应有的强度。
2.20铺面砂后,在模型及浇冒口有凹入或不易舂实的部分,舂砂前应先用手将此部分型砂压实,然后再加背砂逐层舂实,舂砂时,每次填砂不可太厚,按铸件大小及形状不同,采用如下标准:
a.用手工舂砂时,型砂填入厚度为75~100mm:
b.用风动工具舂砂时,型砂填入厚度为l00~150mm。
2.21舂砂时砂舂得不得太靠近木模,应保持20~30mm的距离。
2.22舂砂时不得使模型活动部分,浇冒口系统及冷铁变动位置。
2.23舂砂时应使砂型松紧均匀。
2.24舂砂时严格执行安全规程,集中精神,避免舂头砸伤脚
2.25舂砂后的砂型应有足够的硬度,硬度决定于铸件的大小及由型砂底部至浇口杯高度,一般为50~90单位。
2.26潮模造型时,舂砂特别注意浇注系统及转角等地方的硬度较其它地方高些。
2.27填满型砂后,用φ5~φ8mm的铁钎插通气孔,每箱不得少于3~5个,通气孔距模型表面为10~15mm左右。
2.28放有直浇口的箱角要用面砂春紧(大件放浇口砖),特大铸件防止射箱。
2.29为了从较大的泥芯中导出出气孔,可在填砂之前,在泥芯部分,放置适当的通气管或木棒,通到砂型表面。
2.30取出浇冒口,保证内部光滑,修平四周,干模造型要刷好涂料。
2.31砂箱要精确的定位,打号泥至少三面三点定位做基准,且细、直。
2.32在附近适当的地方打一平地,平地表面松软,以备翻箱、起模和修理。
3起模部分
3.1将砂箱放于平板或已备好的松软平地上。
3.2开箱后,翻转上箱,然后松去带样的铁丝和铁棒,将砂箱放在已备好的松软平地上。
3.3重量为50公斤以下的砂箱可以人工起模,超过50公斤的可用天车起模。
3.4修整分型面,干模造型,使披缝不得超过3mm,潮模造型不得超过1mm。
3.5起模前,在摇动木模时,为了不损坏模型,敲模时应使用木垫板。
3.6起模时,起模针应固定在模型的重心处,避免起模时将砂型碰坏。
3.7木模松动后,再平衡地仔细取出模型。
3.8轻轻地敲动活动块部分和浇注系统部分,再仔细地取出。
4修型部分
4.l起模后要检查不同的地方的砂型硬度情况,当发现局部松软或损坏的部分,应仔细地用面砂填补,修补后,必须插钉子和气孔,以保证必要的强度和通气。
4.2木摸起出后,发现有背砂的地方,要挖掉后补上面砂。
4.3修型时,不应损坏砂型的几何形状,浇注系统应光平和尺寸正确。
4.4潮模修型时,不能使用墁刀在一处往复墁平,以免起皮、掉砂。
4.5所有砂型的凸面处、吊砂、沟槽、浇注系统各部分凹凸面及棱角处都应用水笔稍微润湿,并插钉子加固,大平面的部分应插钉子加固,以免起皮、起夹子等。
4.6芯头部分不允许大修理,小修理时,不应损坏其几何形状及尺寸精度。
4.7下芯时,应用卡板或量具检查有关尺寸,应保证泥芯安装牢固,泥芯头排气通畅。
4.8用工具作出填砂时未做出的芯头出气通道。
4.9与木模、工艺图校对是否有搭子和筋条等遗漏。
4.10干模造型,修完型后,底箱、盖箱、分型面、平面都要刷涂料。
4.11潮模造型,修完型后,用微弱的压缩空气或皮老虎轻轻地吹去表面浮砂,然后用粉袋的方法,均匀地撒上一层石墨粉,必要时可用造型工具抹平,然后用气轻轻地吹去多余的粉末。
4.12潮模制造较厚的铸件时,如工艺卡片中规定用的液体涂料,则按工艺卡片规定喷、刷。
4.13泥芯厚大的部分与泥芯头处,在进窖前要掏到焦炭或煤渣止。
5手工制造大、中、小、泥芯部分
5.1制造泥芯前的准备工作
5.1.1检查芯盒是否符合所制定的铸造工艺要求。
5.1.1.1有无变形、裂纹以及定位不精确和不牢固的情况。
5.1.1.2活动部分是否齐全和易于取也。
5.1.1.3检查固定部分的紧固程度和精密度是否符合工艺要求。
5.1.1.4有无做出通气道和吊盘位置的标志。
5.1.2造型材料及辅助工具的检查
5.1.2.1泥芯砂性能是否符合造型材料工艺守则的规定。
5.1.2.2芯骨的尺寸、形状、强度的检查。
5.1.2.3填充物(煤渣、焦炭渣)是否适用。
5.1.2.4泥浆水、涂料及造泥芯用的手工工具是否齐全。
5.1.2.5准备芯板,如泥芯不是平的,须具备填砂用的木框或特制泥芯托架等。
5.2泥芯的填砂
5.2.1芯骨要保证以下要求:
a.保证有支持泥芯各部分的必要强度。
b.不妨碍铸件的正常收缩。
C.不影响泥芯的正常收缩。
5.2.2芯骨的材料可根据要求,采用铸铁、铸钢、焊接件,小泥芯可采用软铁丝,退火后的铁丝或铁棒等。
5.2.3芯骨的大小由泥芯决定
5.2.3.1芯骨与芯盒边的距离:
大芯:
50~80mm;中芯:
30~80mm;小芯:
10~30mm
5.2.3.2铸铁芯骨横梁的一般尺寸
500×1000mm泥芯35×30mm;2000×2500mm泥芯50×40mm
5.2.3.3芯骨插齿粗细(直径)
芯骨高1000X1500mm25~35mm
芯骨高500X700mm15~25mm
5.2.3.4圆形泥芯,芯骨直径尺寸。
泥芯直径30~lOOmm4~18mm
5.2.4金属芯骨应按工艺图的形状、尺寸进行制备。
5.2.5除了高度较小或较薄泥芯外(低于200mm),一般此类泥芯都作成空心的,泥芯内部加煤渣、焦炭渣等。
泥芯砂层厚度:
500×l000mm,60~100mm;
2000×2500mm,100~150mm
5.2.6在泥芯填砂前,要将芯盒内腔擦干净,芯盒形状比较复杂的,要定期用滑石粉涂擦。
5.2.7芯骨应事先放在泥浆中浸湿,然后放在芯盒中已轻轻地舂实的芯砂层上,再逐步填砂,逐层舂紧为止。
5.2.8对凸台及易于垮砂部位应事先放上吊砂钩、铁棒,必要时应与芯骨扎紧。
5.2.9在制作大型泥芯时,按放泥芯撑的位置,可预先放上耐火砖或铁板等。
5.2.10如需要安放内外冷铁,则应按工艺规程规定执行。
5.2.1l泥芯的通气
5.2.11.1如填砂面是芯头时,应挖出通气道。
并沿通气道用3~5mm铁针向泥芯四周放射方向,均匀插通气孔,各孔相距15mm,不应插穿泥芯的表面。
5.2.11.2如果填充面是芯头,同时砂中放入了填充物,可在填充物上放木棒或铁棒,高出芯盒平面,制完芯子,取出木棒或铁棒作为出气孔。
5.2.11.3用合适的制模工具,在泥芯分型面处挖通气道,用直径3~5mm铁针,在通气道四周插孔,每孔相距15~25mm,不应插穿泥芯的表面。
5.2.11.4高的泥芯要在芯头中间挖凹,并用直径3~5mm的铁针插通气孔。
5.2.11.5圆形泥芯通气孔尺寸:
泥芯外径(mm)
20以下
20~40
40~70
70~100
100以上
通气孔直径(mm)
3
5
7
10
不规定
5.2.11.6对要求比较复杂的泥芯,铁针难以达到的地方,要用其它的代用品作通气道,其尾端必须与泥芯通道或芯头部分相连。
5.2.12如在泥芯表面装入活动块时,必须在装这些活块的位置挖出一些芯砂,弄松后,将活动块仔细地放入,垫上木板再敲入。
5.2.13泥芯填砂面上,如有深大的凹处,须先铺报纸,再用填充砂或者其它的砂子,填满凹的地方为止,泥芯板不平或者填砂面为曲面而没有合适的泥芯托板时,则在泥芯托板上须按形状填一层砂。
5.3泥芯的修正
5.3.1制好的泥芯,应检查各部分填砂是否均匀,对已发现的缺陷,应仔细修好。
5.3.2修正泥芯的外表,不应损坏其几何形状和精确度,在修理泥芯芯头时,严禁大修芯头。
5.3.3对泥芯中凸出的、最易损坏的部分,如薄的砂层、转角、凸台等,必须插入浸过泥浆的型钉或其它的加固物。
5.3.4在修泥芯时,对提泥芯的吊盘,应挖在工艺图上指定的位置,并保证使用方便。
5.3.5泥芯的排气孔道,应挖在工艺图上指定的位置,挖到有填充物或与其他通气道相通处。
5.3.6在主泥芯体上,需放置辅助泥芯时,两者要合紧,并将缝隙修得与表面一样平。
5.3.7修好的泥芯表面,需要刷涂料,涂刷涂料应尽量均匀平滑。
5.4泥芯的烘干
5.4.1烘干的泥芯水份应在O.2%以下。
5.4.2没有烘干的泥芯,不得使用,应进行第二次烘干。
5.4.3当发现泥芯烘干过度,而使泥芯松散或破裂者,不得使用。
5.4.4烘干后的泥芯,如有大裂纹,应润湿后,用同一种砂子修补,如裂纹较小,可用稠涂料等物抹平,然后进行局部烘干。
5.4.5小泥芯刷涂料时,防止通气道堵塞。
5.5泥芯的配合
5.5.1两半泥芯配合时,必须符合下列规定:
a.两半泥芯外形完全符合。
b.通气道干净并相符合。
c.配合好的主要足寸,必须符合规定的精确度。
d.用粘土浆或铁丝,将泥芯的两半结合牢固。
e.两半泥芯的接缝处应填平修光。
5.5.2干燥后的泥芯须安装在主体泥芯上时,应注意下列情况:
a.安装后的尺寸要进行检查。
b.泥芯的通气道要畅通。
c.与主体泥芯配合要牢圈。
d.在安装辅助泥芯时所产生的缝隙,要填平刷涂料进行局部烘干。
6砂型及泥芯的烘干部分
6.1干燥规范
6.1.l泥芯的干燥规范,根据工艺卡片规定进行。
6.1.2砂型的干燥规范,根据工艺卡片规定进行。
6.1.3不同粘结剂的泥芯干燥温度见表6-1。
表6-1不同粘结剂的泥芯干燥温度
泥芯的类别
干燥温度(℃)
最高温度
最适应的温度
烘干规范
糖浆泥芯
150~180
150~175
加热和缓慢冷却
松香和面粉泥芯
175以下
快速烘干
植物油泥芯
200~240
200~220
加热和缓慢冷却
粘土泥芯
300~350
250~300
缓慢烘干
6.1.4不同类型的砂型烘干时间见表6-2。
表6-2不同类型的砂型烘干时间
砂箱尺寸(mm)
铸铁和有色金属砂型
烘干时间h
铸钢砂型烘干时间h
500×400×200以下
1000×800×400以下
3000×2000×500以下
5000×3000×700以下
4~6
6~12
8~12
12~24
6~8
12~16
12~16
16~24
6.1.5特殊的砂型,泥芯的升温,保温及降温的规范曲线,按工艺卡规定执行。
6.2干燥的准备和检查工作。
6.2.1装车前应进行下列检查,发现有毛病及时解决:
a.炉体是否有毛病,如裂纹、倒塌等。
b.通风设备,通风管及闸门是否正常。
c.炉条有无损坏。
d.烘车各部份是否牢固,钢丝绳是否断裂,有无危险,车轮运转是否正常。
e.启动部分是否灵活安全。
6.2.2设备的仪表、工具及燃料。
6.3操作及控制
6.3.1装炉
6.3.1.1每炉装入的砂型及泥芯必须是干燥规范相似的。
6.3.1.2大砂型放在温度较高的位置,小砂型放在温度较低处。
6.3.1.3装车时不可冲撞砂型,防止砂型碰坏。
6.3.1.4装大砂箱时,砂型应与烘车台相距30mm以上。
6.3.1.5装车时,应注意将砂箱垫平稳。
6.3.1.6装车完毕后,清除轨道上的障碍,烘车拉入窖,将窖门关上,并用泥浆土封闭空隙,以免干燥时发生漏气现象。
6.3.2点火
6.3.2.1点火前先将烟道门打开,将鼓风机开动2~3分钟,清除炉内灰渣,同时可以检查鼓风机的运转晴况和烟道有无堵塞等。
6.3.2.2点火初期不开鼓风机,待木柴燃旺时,加上少量的燃料后,方可开动鼓风机。
6.3.3升温和保温
6.3.3.1燃料层的厚度,应根据炉子和燃烧程度决定,燃料层的厚度保持均匀。
6.3.3.2燃料及通风是否合适,应根据实际经验,看火焰的燃烧情况,予以调整。
6.3.3.3当燃烧层烧到一定的程度,应进行透炉及增添燃料。
6.3.3.4透炉时应立即停止鼓风,透炉及增添燃料要迅速,以缩短开火门的时间。
6.3.3.5在工作过程中,应随时根据炉内温度,调整鼓风的闸门,以保证温度在规定范围之内。
6.3.4降温、停火和出炉
6.3.4.1保温一定的时间,应停止增添燃料,使温度按规范降至出窑温度。
6.3.4.2每次燃烧工作结束时,消除炉内未燃烧完的燃料及灰渣,以便应用。
6.3.4.3根据干燥规范或曲线达到干燥时间后,方可出窑。
7合箱部分
7.1砂型干燥后的水分不得超过0.2%,如超过时应重新进行烘干。
7.2砂型干燥后,其干燥深度不得少于40~60mm。
7.3把下砂箱放在有十字通道的软地平上,以便浇注时排出气体。
7.4除净型内的灰及浮砂,检查砂型是否有损坏,如有损坏,用面砂填补,上涂料后进行烘干。
7.5下芯的次序,应按工艺卡片或工艺图规定进行。
7.6下芯须使芯头的通气道与砂型的通气道相接通。
7.7下芯时要注意检查,防止因芯铁、砂芯强度不够,或吊运时滑落砸伤操作者。
7.8泥芯气孔往盖箱上走的,砂型气孔要对准芯头气孔,必要时,四周用油泥等围好,要压牢防止走铁水。
7.9扣箱要按照工艺扣,以防泥芯落反和落错,不得损坏泥芯和砂型。
7.10当大中泥芯固定在上箱时,泥芯应有两点以上用铁丝或螺栓,将泥芯固定。
7.11泥芯吊盘地方,要用面砂修补,要插加固钉,刷涂料后,要进行表面烘干。
7.12小泥芯可用砂钩或插钉固定。
7.13铸件的壁厚应符合零件图公差规定,不符合规定时,必须进行精修。
7.14泥芯撑的数量、位置和尺寸,应按工艺图选择安放,应防止泥芯下落、移动、浮起,受力较大的泥芯撑,应放在工艺图上规定的预先放在砂型中的垫铁上。
7.15绝对禁止使用没有镀锡、生绣和表面被沾污的泥芯撑。
7.16在检查铸件上箱的厚度时,应使用验箱泥,同时根据验箱泥的尺寸,选择泥芯撑的高度。
7.17合箱前,潮模造型为了防止跑火,应用造型工具,在砂型的四周掘起一圈砂堤
7.18合箱前,浇冒口要进行检查,以免有砂子和其它的东西。
7.19最后将砂型中的浮砂吹净,然后对准定位销或号泥进行合箱(干模造型四周要围好石棉绳)。
7.20合箱后,立即用纸或盖子盖好浇冒口、出气孔,以防止掉入脏物。
8浇注部分
8.1浇注前的准备工作
8.1.l30公斤以上的铸件用的浇冒口圈都是干的。
8.1.2为了防止砂型被压坏,可在砂箱分型面的四角处,垫上铁片或金属垫,其厚度不可大于箱缝的厚度,然后在箱缝间抹泥。
8.1.3压铁应按工艺图规定的大小均匀地放在砂箱壁上或专门的垫上,用螺丝拧紧时,应尽量使其均匀对称,以免紧固时,砂箱歪斜或压坏砂型与泥芯。
8.1.4合箱后的砂箱上,按工艺图规定,用粉笔写上零件号、铁水牌号和铁水重量。
8.1.5负责浇注的班长应与化铁炉班长联系熔化和浇注工作的配合。
8.1.6大小砂型周围要事先准备好刨花等,以便引火,准备好草灰,以便保温聚渣。
8.1.7检查铁水包是否修好,是否已烘干及预热,数量是否足够,转动是否灵活。
8.1.8检查浇注地区的通道是否有无堵塞。
8.2浇注守则
8.2.1盛铁水后的包子,应撒集渣剂仔细地扒去表面的渣子,均匀地撒上一层草灰或珍珠岩集渣剂。
8.2.2铸铁件的浇注温度参见表8-1。
表8-1铸铁件浇注温度参考表
铸件种类
铸件壁厚(mm)
浇注温度℃
灰口铸铁与高强度铸铁
4以下
1450~1360
4~10
1430~1340
10~20
1400~1320
20~50
1380~1300
50~100
1340~1230
100~150
1300~1200
150以上
1280~l180
8.2.3铁水包嘴应尽量接近浇口杯,其距离吊包150~300mm,手抬包50~200mm。
8.2.4浇注时应有专人挡渣,挡渣扒使用前应预热。
8.2.5浇注时铁水浇入浇口杯的方向应是没有直浇口的一面,铁水不得直接冲在直浇口上,并不得引起铁水飞溅或发生旋涡,浇注过程中,浇口杯应充满铁水,浇注不得中断。
8.2.6剩余的铁水应倒入倒剩余铁水的铁水模。
8.2.7铁水包要保持清洁、完整、如有损坏和结渣多时,应停止使用。
8.2.8浇注时应准备好抹箱泥,以便发生跑火迅速堵塞。
8.2.9浇注时无关人员要远离浇注现场,防止砂型呛火或跑火钢(铁)水飞溅伤人
8.2.10浇注后的一定时间,去掉浇冒口圈,如工艺图有特殊规定(如松箱等)应按规定进行。
8.2.11浇注后,应将包内剩余铁水倒出,并将工具集中保管。
9安全
9.1工作中应正确穿戴好劳保用品。
9.2舂砂时严格执行安全规程,集中精神,避免舂头砸伤脚
9.3砂型烘干装车时,应注意将砂箱垫平稳,防止跨塌伤人。
9.4浇注时无关人员要远离浇注现场,防止砂型呛火或跑火钢(铁)水飞溅伤人。