全夹套管管线施工工法.docx
《全夹套管管线施工工法.docx》由会员分享,可在线阅读,更多相关《全夹套管管线施工工法.docx(13页珍藏版)》请在冰豆网上搜索。
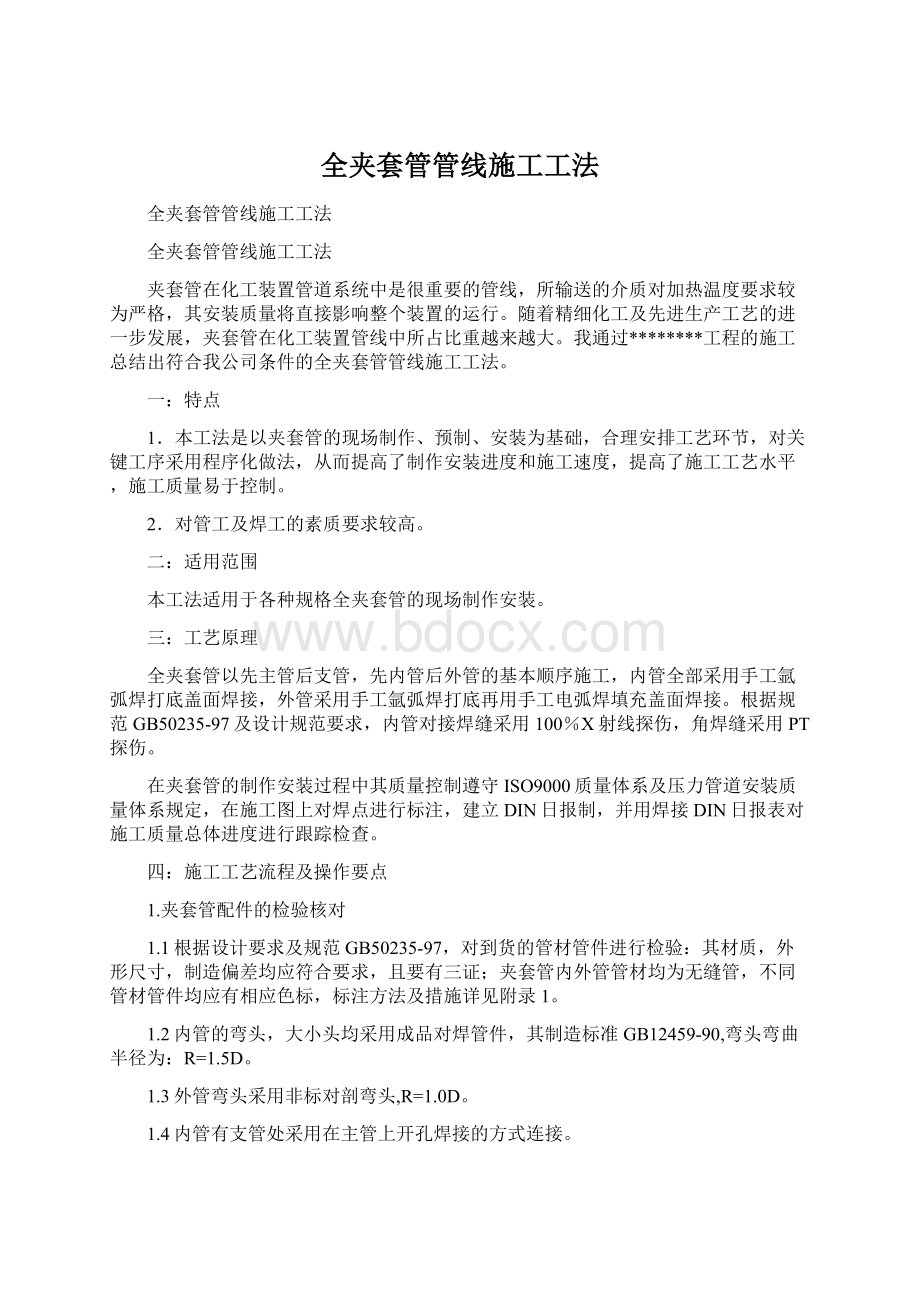
全夹套管管线施工工法
全夹套管管线施工工法
全夹套管管线施工工法
夹套管在化工装置管道系统中是很重要的管线,所输送的介质对加热温度要求较为严格,其安装质量将直接影响整个装置的运行。
随着精细化工及先进生产工艺的进一步发展,夹套管在化工装置管线中所占比重越来越大。
我通过********工程的施工总结出符合我公司条件的全夹套管管线施工工法。
一:
特点
1.本工法是以夹套管的现场制作、预制、安装为基础,合理安排工艺环节,对关键工序采用程序化做法,从而提高了制作安装进度和施工速度,提高了施工工艺水平,施工质量易于控制。
2.对管工及焊工的素质要求较高。
二:
适用范围
本工法适用于各种规格全夹套管的现场制作安装。
三:
工艺原理
全夹套管以先主管后支管,先内管后外管的基本顺序施工,内管全部采用手工氩弧焊打底盖面焊接,外管采用手工氩弧焊打底再用手工电弧焊填充盖面焊接。
根据规范GB50235-97及设计规范要求,内管对接焊缝采用100%X射线探伤,角焊缝采用PT探伤。
在夹套管的制作安装过程中其质量控制遵守ISO9000质量体系及压力管道安装质量体系规定,在施工图上对焊点进行标注,建立DIN日报制,并用焊接DIN日报表对施工质量总体进度进行跟踪检查。
四:
施工工艺流程及操作要点
1.夹套管配件的检验核对
1.1根据设计要求及规范GB50235-97,对到货的管材管件进行检验:
其材质,外形尺寸,制造偏差均应符合要求,且要有三证;夹套管内外管管材均为无缝管,不同管材管件均应有相应色标,标注方法及措施详见附录1。
1.2内管的弯头,大小头均采用成品对焊管件,其制造标准GB12459-90,弯头弯曲半径为:
R=1.5D。
1.3外管弯头采用非标对剖弯头,R=1.0D。
1.4内管有支管处采用在主管上开孔焊接的方式连接。
1.5在制作安装前,根据施工图对夹套管的管材管件阀门及导向块隔板等进行检查核对,应与施工图一致。
2.管道校直及内外表面处理
2.1到场的管道若有弯曲现象,应在专用校直工作平台上进行校直处理,不能用榔头等铁器工具敲击,不锈钢管严禁用火烤。
2.2管道若有明显油迹,应用碱,四氯化碳进行脱脂处理。
3.空视图焊口标注与核对
3.1在空视图上按介质流向,以先主管后支管的顺序对焊点进行标注,现场修改的焊点也应标注在相应修改图上,标注好的施工空视图为一式三份,管道焊接工程师及班组各一份。
3.2核对设备管口方位,坐标,标高,接口法兰标准形式,材质是否与施工图一致。
3.3核对空视图尺寸,并现场实测进行下料,确定特殊件,仪表件及支管具体位置。
4.特殊件,仪表件开孔
特殊件,仪表件及支管的开孔具体位置确定后,采用钻孔方式开孔,所开孔直径要比支管外径大4mm,便于支管焊接或仪表件自由插入,开孔完毕后用棒式砂轮机对所开孔进行清理。
5.内管预组对,预安装
5.1将已制作好的内管管段按空视图要求预组对,点焊,并进行预安装。
5.2经预组对,预安装再次调整各管段的尺寸,使其符合设计要求和现场实际。
5.3确定内管活口及调整段的具体位置,其操作原则为:
在X,Y,Z三个方向各留一个活口,用活口调整尺寸,如有法兰口,应尽量留在法兰口处,对半直管一般留在支管三通处,若无支管三通,可留在弯头或法兰处来调整外管尺寸。
5.4经预组对,预安装确定出合理的组装顺序。
5.5按预安装顺序将内管各管段编号,并在空视图上记录标注。
6.确定外管尺寸
根据内管预安装情况,以及调整半管的尺寸确定出套管的长度。
7.内管的局部组对,焊接,清洁
7.1按第5.4条所确定出的组装顺序,将内管局部组对焊接,焊接采用手工氩弧焊,在焊接过程中采用相应施工措施,如水冷却法,捆绑法等方法控制焊接变形。
7.2管段预制完毕后要再次进行校直处理,并进行100%无损检测。
7.3由于夹套管内部清洁度要求高,应对预制管段采用棒击和气吹除法进行管内清洁,操作方法见附录2。
8.导向块制作安装
8.1导向块按图1制作:
8.2导向块的制作尺寸见下表:
8.3导向块距弯头中心之间距离≤600mm,导向块布置按下表:
工艺管DN
15
20
25
40
50
80
100
150
200
导向块距离(m)
2.0
2.0
3.0
4.5
5.0
6.0
7.0
8.5
8.5
8.4导向块按设计要求的布置方式满焊在内管上如图2所示:
9.外管制作
9.1按上述第6条所确定的尺寸下料
9.2热源进出口点的确定
9.2.1对于蒸汽介质应高进低出,对于热水介质应低进高出;热源介质流向尽可能和内管介质流向相反,而且要做到夹套管能自行放空自行导淋,如图3所示:
9.2.2最小距离(Min)的要求:
夹套管要尽可能避免潜在的冻结点和死端,故热源引入引出口的距离应尽可能小,如图3中“Min”一般控制在25~35mm之间。
9.3跨越管(连通管)口及放空,导淋口位置确定,如图4所示:
9.3.1对于蒸汽夹套系统在两加热段之间需要跨越管连接时,应有两个跨越管,一个在上面作气相跨越,一个在下面作液相跨越。
9.3.2对于热水夹套系统两加热段之间需要跨越管连接时,跨越管应在上面,以防止气积存于套管内。
9.3.3在夹套管线的最高点及最低点,必须设置放空和导淋点。
9.3.4跨越管口及放空,导淋管口位置最小距离(min)要求,为了尽可能避免潜在的冻结点和死端,各跨越管口,导淋口,放空口位置一般控制在25~35mm之间。
9.3.5水平夹套管的跨越管应与夹套管切线方向连接。
9.3.6为方便组对,检查,拆卸,跨越管应采用标准法兰连接。
10.外管对热源引入引出,跨越管口的开孔
10.1热源管,跨越管管径的确定
10.1.1蒸汽夹套系统的热源管,跨越管管径均为DN20。
10.1.2热水系统,热源管,跨越管管径按下表中尺寸确定:
管道尺寸
工艺管线
公称直径
15
20
25
32
40
50
80
100
150
200
夹套管
公称直径
40
40
50
80
80
80
125
150
200
250
夹套管的热水进出管及跨越管
公称直径
15
15
15
15
15
15
20
25
40
40
10.2外管的开孔
10.2.1外管的开孔采用钻孔方式开孔,所开孔径要比热源管外径大4mm,开孔后应用棒式砂轮机,圆锉,半圆锉修孔,直至满足设计要求。
10.2.2对于跨越管口开孔,应在外管切线方向开孔,开孔后应用棒式砂轮机,半圆锉或圆锉修孔,将所开孔修整成跨越管和外管切线方向连接的相贯线形式。
对于不同管径外管和不同管径跨越管其相贯线均不相同。
11.夹套法兰的安装
11.1夹套法兰采用非标法兰,和内管以承插焊形式连接,和外管以对接角焊缝形式连接,见图5
11.2与夹套法兰连接的外管制作:
11.2.1在已下料的外管管段上切割抽条,并热闭管端而成,如图6所示。
11.2.2外管经热闭管端后的Φ值应符合下表:
名称
内管
外管
法兰
跨越管
Φ值
规格
DN15
DN40
见图5
DN15
38
规格
DN20
DN40
见图5
DN15
45
规格
DN25
DN50
见图5
DN15
51
规格
DN40
DN80
见图5
DN15
76
规格
DN50
DN80
见图5
DN15
89
规格
DN80
DN125
见图5
DN20
108
规格
DN100
DN150
见图5
DN25
133
规格
DN150
DN200
见图5
DN40
219
规格
DN200
DN250
见图5
DN50
273
规格
DN250
DN300
见图5
DN50
325
11.2.3在热闭管端时应严格控制Φ值及热闭后的椭圆度,特别是DN40这一规格的法兰,若Φ值及椭圆度控制不好,会出现热闭的外管与法兰焊接后没有螺帽的旋转空间或螺帽的端面不能与法兰面接触,以及热闭的管端与内管的角焊缝接触,使法兰的受热面减少,甚至没有加热面。
11.2.4热闭管端的施工速度慢,成本高,且质量很难保证,特别是DN40的内管其外管为DN80外径为Φ89,热闭后的Φ值为76mm,故应采用DN80*65PN25的同心大小头代替热闭管端,这样可避免热闭管端所产生的问题,且施工速度快成本底,能较好保证质量,见下表比较:
名称
采用热闭管端
采用成品大小头
材质
20#钢
20#钢
壁厚
3mm
3mm
大头外径
89mm
89mm
小头外径
76mm
76mm
可达到的长度
45mm
75mm
11.2.5经热闭厚的外管与夹套法兰连接后,以及热源管口位置确定后,应满足螺栓自由安装拆卸。
12.套入外管
12.1按第5.4条确定的组对顺序,在内管局部套入已制作好并清洁过的外管。
12.2外管套入时应防止内管和外管的大小头之间的夹套管腔变小或堵塞,如图7:
应保证E1=E2。
13.隔板的安装
隔板的材质一般用0Cr18Ni9Ti,其制作见图8:
隔板尺寸见下表,其安装见图9
尺寸
工艺管
夹套管
隔板
DN
外径Φ
DN
外径Φ
A
B
C
15
18
40
45
18.2
65
3
20
25
40
45
25.6
65
25
32
50
57
32.6
75
40
45
80
89
45.7
105
4
50
57
80
89
57.7
105
80
89
125
133
89.7
155
5
100
108
150
159
108.7
185
150
159
200
219
159.7
240
6
200
219
250
273
219.7
300
14.调整半管的制作
14.1根据施工图及外管的套入情况,确定调整半管的形式,并实测其长度。
14.2调整半管一般有两种形式,一种材质为0Cr18Ni9Ti,用于有支管焊接处,另一种材质为20#,用于无支管焊接处。
14.3将调整半管按实测尺寸下料并加工坡口,确定有支管焊接的开孔位置及开孔大小。
14.4有支管焊接的调整半管开孔,用手动砂轮机或磁力钻开孔,开孔后用棒式砂轮机修口,修口后的内径应比支管外径大4mm,开孔方位见图10。
14.5对已制作的调整半管编号,登记。
15.内管的整体连接
按第5.4条所确定出的组对顺序及第5.5条中对各管段的编号,对内管进行组对,焊接,整体连接,无损探伤。
并对内管上的焊缝进行酸洗钝化。
16.内管安装检查
16.1内管是否按施工图施工完毕,并符合设计要求。
16.2内管的焊口是否全部完成,并按设计规范要求已作无损检验。
16.3所有资料,记录是否齐全。
16.4以上工作完成后,内管按设计和《工业管道施工与验收规范GB50235-97》要求进行试压。
17.外管组对焊接及对半弯头的焊接。
17.1按第5.4条确定的组对顺序对外管进行组对焊接。
17.2对半弯头按施工图进行安装焊接,安装时按图11所示应保证E1=E2。
17.3外管组对时,要使热源引入,引出口及跨越管口导淋放空口处于正确位置。
18.外管的整体封闭,焊接
18.1核对各配件及其编号,对内管外管进行清理检查,并在内管试压合格后方能整体封闭。
18.2外管组对焊接完毕后,安装对半直管,对半直管按编号安装在正确位置。
18.3调整半管的安装见图10。
18.4外管整体封闭焊接后,对热源引入,引出口及跨越口,导淋,自动放空口,均要用封口胶将管口封住,防止脏物掉入管内。
19.隔膜式压力表接头的安装
19.1隔膜式压力表接头是采用壁厚为3mm,2”的不锈钢管加工而成,材质与夹套内管,调整半管相同,表接头与压力表由NPT螺纹连接。
19.2由于表接头要与内管,调整半管焊接,焊接量大,且焊缝距离较近,热量集中,焊接变形大,表接头在螺纹处椭圆度增大,使表接头与压力表不能密封。
19.3为减少焊接变形,在施工时可在三个方面进行控制,第一:
制作与隔膜式压力表相配套的2”NPT外螺纹接头,第二:
在焊接时采用氩弧焊,且焊接时要对称施焊,第三:
用湿纱布将表接头螺纹端包住,用水冷法减少焊接变形。
19.4由于表接头刚性小,连接处的密闭性仍不好,可采用聚四氟乙烯生料带涂高分子密封胶加以密封。
19.5为减少以上问题出现,表接头应采用锻件加工而成,且要增加表接头厚度,特别是螺纹连接处,以增加其刚性,减少焊接变形。
20.阀门与垫片的安装
20.1安装前应仔细检查阀门的编码与空视图是否一致,确定阀门的正确安装位置
20.2对于夹套管,垫片最好采用带外定位环的金属缠绕垫,可使垫片在法兰上准确定位。
21.非标件与特殊件安装
21.1安装前仔细核对非标件特殊件型号,位号是否和施工图一致。
21.2确定正确安装位置,避免错装。
22.坡度要求
夹套管一般都要求有坡度,安装时注意按施工图规定的坡度方向施工。
23.跨越管安装
跨越管应按第9条所确定的位置及方向安装,需拆卸的夹套管处的跨越管可采用线密封的活接头或法兰连接,一般优先选用法兰连接便于组对检查拆卸且密封性好。
24.热源管安装
24.1热源管安装的基本要求为自放空自导淋,蒸汽夹套的蒸汽应高进底出,避免积液,热水夹套的热水应底进高出,避免积液和积气。
24.2夹套外管的连通管应在施工前确定方向,满足自放空自导淋要求,确认无误后方可施工,热源管应保证畅通无阻。
五:
夹套管安装顺序小结
根据以上所述施工工艺流程及操作要点,对夹套管安装顺序总结如下,如图12
将法兰件号1焊接在工艺管件号2上,焊接A点;
按导向板的安装要求将导向板焊接在工艺管上;
将夹套管件号4套在工艺管上,焊接C点;
焊接工艺管弯头件号7,焊接B点;
用X射线检测焊缝A和B,并将夹套管件号5和件号6套在工艺管上;
焊接D点和E点;
用X射线检测焊缝D,并用磁粉探伤或着色渗透探伤检测焊缝E;
对工艺管进行压力测试;
焊接C点;
焊接夹套管弯头件号8,并将夹套管弯头件号8与夹套管件号6相焊接,焊接F点,将剖切夹套管件号9焊接在件号4和件号8上;
将支管件号11与其它工艺管焊接,焊接G点,用X射线检测焊缝G,并焊剖切三通件号10;
按照国标规范GB50235-97的要求对夹套管进行X射线检测;
对夹套管进行压力测试。
六:
附录
附录1:
关于管材,管件标注方法及措施
同种材质的管材和管件用同种颜色作色标,色标应从管材或管件一端通刷至另一端,色标宽度以20mm为宜,色标应均匀醒目,易于辨识;
对于无缝钢管和管件应刷单色标,即从头到尾通刷一根宽度为20mm的直线;
对于有缝钢管和管件应刷双色标,即从头到尾通刷两根宽度为20mm的同种颜色的直线。
各材质标注方法见下表
中国标准
美国标准
类别
色标方式
色标颜色
10#
A333-GRB
无缝
单线
黑色
有缝
双线
20#
A53-GRB
无缝
单线
白色
有缝
双线
Q235A
A106-GRB
无缝
单线
灰色
有缝
双线
12CrMo
无缝
单线
棕色
有缝
双线
00Cr18Ni10
A312-TP304L
无缝
单线
绿色
有缝
双线
0Cr18Ni9Ti
A312-TP321
无缝
单线
黄色
有缝
双线
00Cr17Ni14Mo2
A312-TP316
无缝
单线
红色
有缝
双线
附录2:
清洁管道采取措施
由于精细化工工程的管道在线仪表较多,设计要求管道内的清洁度特别高,故对到场的管道以及已预制的管道进行清洁,具体采用棒击法和吹除法:
棒击法是对进场的管材,已预制的管道用木棒敲击,将较大的渣子,脏物除掉;
吹除法是用瓶装氮气或空压机对管道吹除,将一些不易除掉的脏物焊渣等除去;
对已清洁的管道,用封口胶将管口密封,防止脏物进入管道。
附录3:
剖切管件安装图例,见图13