浅谈机械加工中的新工艺方法资料.docx
《浅谈机械加工中的新工艺方法资料.docx》由会员分享,可在线阅读,更多相关《浅谈机械加工中的新工艺方法资料.docx(15页珍藏版)》请在冰豆网上搜索。
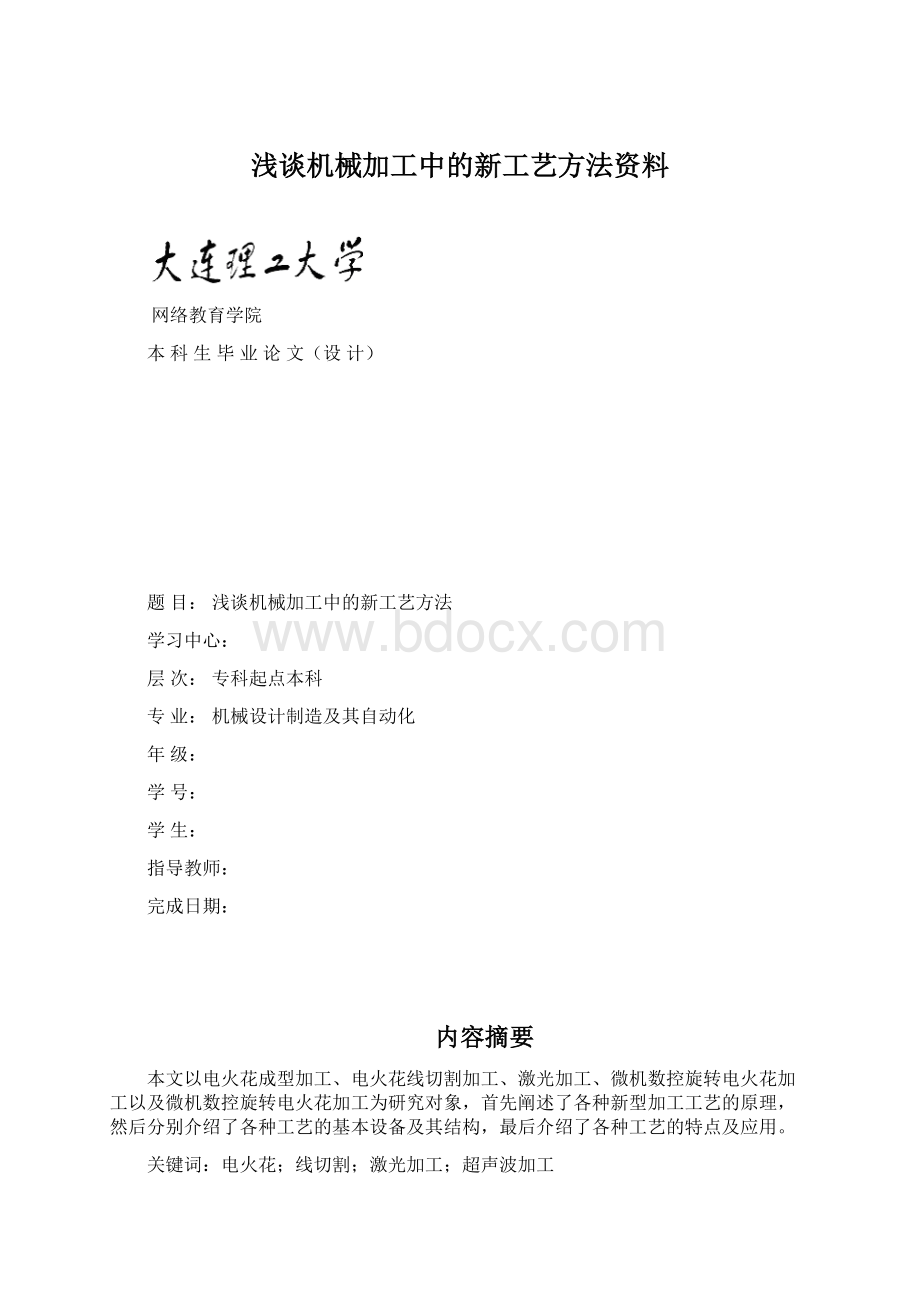
浅谈机械加工中的新工艺方法资料
网络教育学院
本科生毕业论文(设计)
题目:
浅谈机械加工中的新工艺方法
学习中心:
层次:
专科起点本科
专业:
机械设计制造及其自动化
年级:
学号:
学生:
指导教师:
完成日期:
内容摘要
本文以电火花成型加工、电火花线切割加工、激光加工、微机数控旋转电火花加工以及微机数控旋转电火花加工为研究对象,首先阐述了各种新型加工工艺的原理,然后分别介绍了各种工艺的基本设备及其结构,最后介绍了各种工艺的特点及应用。
关键词:
电火花;线切割;激光加工;超声波加工
1.电火花成型加工
1.1电火花成型加工原理
电火花成型加工是利用脉冲放电对导电材料的蚀除作用去除材料,满足一定形状和尺寸要求的一种加工方法,也称作放电加工。
工艺系统如图1-1所示。
图1-1电火花成型加工系统
脉冲电源发出一连串单脉冲电压,施加在浸入工作液(绝缘介质,一般用煤油)中的工具电极和工件电极之间。
当两极之间的间隙很小(一般为0.01~0.3mm)时,由于电极的微观表面凸凹不平,极间某凸点处电场强度最大,其间工作液最先电离为电子和正离子而被击穿,形成放电通道。
在电场力的作用下,通道内的电子高速奔向阳极,正离子奔向阴极,产生火花放电。
由于受到放电时磁场力和周围工作液的压缩,致使放电通道的横截面积很小,通道内电流密度很大,达到104~107A/cm2。
电子和正离子在电场力作用下高速运动,互相碰撞,并分别轰击阳极和阴极,产生大量热量。
整个放电通道形成一个瞬时热源,通道中心温度高达10000℃左右,使电极表面局部金属迅速熔化甚至汽化。
由于一个脉冲放电时间极短,熔化和汽化的速度极高,具有爆炸性质。
爆炸力把熔化和汽化了的金属微粒迅速抛离电极表面。
每个脉冲放电后,在工件表面上形成一个微小的凹坑,如图1-2(a)所示。
放电过程多次反复进行,随着工具电极不断进给,材料逐渐被蚀除,工具电极的轮廓形状即可复印在工件上,从而达到成型加工的目的,整个表面是由无数凹坑组成的,如图1-2(b)所示。
(a)(b)
图1-2工具电极与工件电极间隙的放大图
1.2电火花成型加工机床的组成与结构
电火花成型加工机床逻辑上有四部分组成,即机床本体、脉冲电源、伺服进给控制系统和工作液循环过滤系统,如图1-3所示。
图1-3电火花成型机床
(1)机床本体
机床本体由床身、立柱、主轴头和工作台等组成。
1)床身和立柱
床身和立柱是一个基础结构,由它确保电极与工作台、工件之间的相互位置。
其精度的高低对加工质量有直接的影响,
2)工作台
工作台主要用来支承和装夹工件,它分上、下两层(上溜板和下溜板)。
在实际加工中,通过转动上、下溜板的丝杠调整电极与工件的相对位置。
工作台上装有工作液箱,使电极和被加工件浸在工作液里,起到冷却、排屑作用。
3)主轴头
主轴头是电火花加工机床的一个关键部件,它的结构由伺服进给机构,导向和防扭机构、辅助机构三部分组成。
它控制工件和电极之间的放电间隙。
(2)脉冲电源
电火花加工的脉冲电源的作用是把工频交流电转换成一定频率的单向脉冲电流,以供给火花放电间隙所需要的能量来蚀除金属。
脉冲电源对电火花加工的生产率、表面质量、加工速度、加工过程的稳定性和工具电极损耗等技术经济指标有很大的影响,
(3)伺服进给控制系统
电火花加工是“不接触加工”。
正常电火花加工时,工具和工件间有一放电间隙S,如图1-4所示。
S过大时,脉冲电压不能击穿间隙中的绝缘工作液,不会产生火花放电。
当间隙过小时,工具工件会接触而短路(S=0)。
伺服进给控制系统的任务就是通过改变、调节进给速度,使进给速度接近并等于蚀除速度,以维持一定的“平均”放电间隙S,保证电火花加工正常而稳定地进行,获得较好的加工效果。
图1-4放电间隙
(4)工作液循环过滤系统
由工作液、工作液箱、工作液泵、滤芯和导管组成。
工作液起绝缘、排屑、冷却和改善加工质量的作用。
每次脉冲放电后,工件电极与工具电极之间必须迅速恢复绝缘状态,否则脉冲放电就会转变为持续的电弧放电,影响加工质量。
在加工过程中,工作液可把加工过程中产生的金属颗粒迅速从电极之间冲走,使加工顺利进行。
工作液还可冷却受热的电极和工件,防止工件变形。
1.3电火花成型加工的工艺特点与应用
1.3.1电火花成型加工的工艺特点:
1、电火花加工时,由于不是靠刀具的机械方法去除金属,加工时无任何机械力的作用,因此可以用来加工小孔、窄槽及各种复杂形状的型孔和型腔。
2、由于电脉冲参数可以任意调节,故在同一台机床上可对零件进行粗、中、精加工及连续加工,节省了设备,提高了效率。
3、电火花加工是直接用电能加工,故便于实现生产中的自动控制及加工自动化。
4、电火花加工时是利用局部高温蚀除金属,任何硬、脆的金属材料都无法抵抗这种高温,只要能导电,就能进行加工,因此,它能加工淬硬模具,并不会产生过多变形。
5、经过电火花加工后的零件精度高,表面粗糙度可达Ra1.25μm,因此,利用电火花加工后的零件,稍加修正后即可装配使用。
6、型腔的加工余量一般较大,尤其是在不预加工的情况下,蚀除的金属量更多,因此,对电源的要求是:
降低损耗和提高生产率。
7、型腔属于盲孔加工,其电蚀产物的排出较为困难,尤其是深型腔加工时更甚,因此,在工艺上必须采用冲油或抽油式来实现排屑。
8、由于型腔的形状多较复杂,电极损耗引起其尺寸的变化会直接影响型腔的精度,因此要求电极的损耗越小越好。
13.2电火花成型加工的应用
电火花成形加工主要用于电火花穿孔(用电火花成形加工方法加工通孔)和电火花型腔加工。
电火花穿孔加工主要用于加工冲模和异形孔,电火花型腔加工主要用于加工各类型腔模和各类复杂的型腔零件。
型腔加工属于盲孔加工,金属蚀除量大,工作液循环困难,电蚀产物排除条件差,电极损耗不能用增加电极长度和进给来补偿;加工面积大,加工过程中要求电规准的调节范围也较大;型腔复杂,电极损耗不均匀,影响加工精度。
2电火花线切割加工
2.1电火花线切割原理
电火花线切割加工与电火花成形加工的基本原理一样,都是基于电极间脉冲放电时的电火花腐蚀原理,实现零部件的加工。
所不同的是,电火花线切割加工不需要制造复杂的成形电极,而是利用移动的细金属丝(钼丝或铜丝)作为工具电极,工件按照预定的轨迹运动,“切割”出所需的各种尺寸和形状。
图1-5电火花线切割加工原理
电火花线切割加工的原理如图1-5所示。
工具电极丝接直流脉冲电源的负极,工件接直流脉冲电源的正极。
当来一个电脉冲时,在电极丝和工件之间可能产生一次火花放电,在放电通道的中心温度可高达5000℃以上,高温使工件局部金属熔化,甚至有少量气化,高温也使电极丝和工件之间的工作液部分产生气化,这些气化后的工作液和金属蒸气瞬间迅速热膨胀,并具有爆炸的特性。
靠这种热膨胀和局部微爆炸,抛出熔化和气化了的金属材料而实现对工件材料进行电蚀切割加工。
图1-6为工具电极丝切割工件的过程。
图1-6切割过程中
2.2电火花线切割机床的组成
机床组成分为四部分:
机床本体,直流脉冲电源,控制系统,工作液循环系统。
(1)机床本体包括床身、工作台、运丝机构和丝架。
工作台可在X、Y两个方向上运动,并可在控制系统的控制下实现二维插补。
运丝机构的储丝筒做往复的转动带动电极丝往复运动,以使整个电极丝都能够放电加工。
(2)直流脉冲电源。
电火花线切割的脉冲电源的作用是把工频交流电转换成一定频率的单向脉冲电流,以供给火花放电间隙所需要的能量来蚀除金属。
(3)控制系统主要是指切割轨迹控制系统和进给控制系统,此外还有走丝机构控制,机床操作控制以及其它辅助控制等。
切割轨迹控制系统实质上是数控系统,控制电极丝的运动轨迹。
进给控制系统是根据放电间隙的大小自动控制进给速度。
(4)工作液循环系统由工作液泵、工作液箱、过滤器和管路组成。
其主要作用是绝缘、冷却、排屑。
2.3电火花线切割的特点
因为数控电火花线切割是数字系统控制下直接利用电能加工工件的一种方法,因些与其他加工方式相比有自己独立的特点:
(1)直接利用线状的电极丝作电极,不需要制作专用电极,可节约电极的设计、制造费用。
(2)可以加工用传统切削加工方法难以加工或无法加工的形状复杂的工件。
对不同的工件只需编制不同的控制程序,对不同形状的工件都很容易实现自动加工,很适合小批量形状复杂零件、单件和试制品的加工,且加工周期短。
(3)利用电蚀加工原理,电极丝与工件不直接接触,两者之间的作用很小,故而电极丝、夹具不需要太高的强度。
(4)传统的车、铣、钻加工中,刀具硬度必须比工件大,而数控电火花线切割机床的电极丝材料不必比工件材料硬,可节省辅助时间和刀具费用。
(5)直接利用电、热能进行加工,可以方便地对影响加工精度的加工参数(脉冲宽度、间隔、伺服速度等)进行调整,有利于加工精度的提高,便于实现加工过程的自动化控制。
(6)工作液一般采用水基乳化液或纯水,成本低,不会发生火灾。
(7)利用四轴或五轴联动,可加工锥度、上下面异形体或回转体等零件。
(8)由于电极丝比较细,可以方便地加工微细异形孔、窄缝和复杂截面的型柱、型孔。
由于切缝很窄,实际金属去除量很少,材料的利用率很高。
对加工、节约贵重金属有重要意义。
(9)采用移动的长电极丝进行加工,使单位长度电极丝的损耗较少,从而对加工精度的影响比较小,特别在慢走丝线切割加工中,电极丝一次性使用,电极丝损耗对加工精度的影响更小。
正是由于电火花线切割加工有许多突出的特点,因而在国内外发展都很快,在塑料模具加工中已获得了广泛的应用。
2.4电火花线切割的应用
1)试制新产品
在新产品开发过程中需要单件的样品,使用线切割直接切割出零件,无需模具,这样可以大大缩短新产品的开发周期并降低试制成本。
如在冲压生产时,未开出落料模时,先用线切割加工的样板进行成形等后续加工,得到验证后再制造落料模。
2)加工特殊材料
切割某些高硬度,高熔点的金属时,使用机加工的方法几乎是不可能的,而采用线切割加工既经济又能保证精度。
3)加工模具零件
电火花线切割加工主要应用于冲模、挤压模、塑料模、电火花型腔模的电极加工等,由于电火花线切割加工速度和精度的迅速提高,目前已达到可与坐标磨床相竞争的程度。
例如,中小型冲模,材料为模具钢,过去用分开模和曲线磨削的方法加工,现在改用电火花线切割整体加工的方法,制造周期可缩短3/4~5/4,成本降低2/3~3/4,配合精度高,不需要熟练的操作工作。
因此,一些工业发达国家的精密冲的磨削等工序,已被电火花和电火花线切割加工所代替。
3激光加工
3.1激光加工原理
图1-7激光加工原理
如图1-7所示,激光具有高亮度、高方向性、高单色性和高相干性。
当激光照射在工件的加工部位时,工件材料迅速被熔化甚至气化,随着激光能量的不断被吸收,材料凹坑内的金属蒸气迅速膨胀,压力突然增大,熔融物爆炸式地高速喷射出来,在工件内部形成方向性很强的冲击波。
因此,激光加工是工件在光热效应下产生高温熔融和受冲击被抛出的综合作用过程。
3.2激光加工基本设备的组成
激光加工的基本设备由激光器、导光聚焦系统和加工机(激光加工系统)三部分组成。
(1)激光器
激光器的作用是把电能转变成光能,产生所需要的激光束。
按工作物质的种类可分为固体激光器、气体激光器、液体激光器和半导体激光器四大类。
由于He-Ne(氦—氖)气体激光器所产生的激光不仅容易控制,而且方向性、单色性及相干性都比较好,因而在机械制造的精密测量中被广泛采用。
而在激光加工中则要求输出功率与能量大,目前多采用二氧化碳气体激光器及红宝石、钕玻璃、YAG(掺钕钇铝石榴石)等固体激光器。
(2)导光聚焦系统
根据被加工工件的性能要求,光束经放大、整形、聚焦后作用于加工部位,这种从激光器输出窗口到被加工工件之间的装置称为导光聚焦系统。
(3)激光加工系统
激光加工系统主要包括床身、能够在三维坐标范围内移动的工作台及机电控制系统等。
随着电子技术的发展,许多激光加工系统已采用计算机来控制工作台的移动,实现激光加工的连续工作。
3.3激光加工的特点
激光具有高亮度、方向性强、单色性好、相干性好、空间控制和时间控制性好等优越性能,容易获得超短脉冲和小尺寸光斑,能够产生极高的能量密度和功率密度,几乎能加工所有的材料。
特别适用于加工自动化,而且对被加工材料的形状、尺寸和加工环境要求很低。
(1)无接触加工。
激光加工是通过激光光束进行加工,与被加工工件不直接接触,降低了机械加工惯性和机械变形,方便了加工。
同时,还可加工常规机械加工不能或很难实现的加工工艺,如内雕、集成电路打微孔、硅片的刻划等。
(2)加工质量好,加工精度高。
由于激光能量密度高可瞬时完成加工,与传统机械加工相比,工件热变形小、无机械变形,使得加工质量显著提高;激光可通过光学聚焦镜聚焦,激光加工光斑非常小,加工精度很高,如PC机硬盘高速转子采用激光平衡技术,其转子平衡精度可达微米或亚微米级。
(3)加工效率高。
激光切割可比常规机械切割提高加工效率几十倍甚至上百倍;激光打孔特别是微孔可比常规机械打孔提高效率几十倍至上千倍;激光焊接比常规焊接提高效率几十倍;激光调阻可提高效率上千倍,且精度亦显著提高。
(4)材料利用率高,经济效益高。
激光加工与其他加工技术相比可节省材料10~30%,可直接节省材料成本费,且激光加工设备操作维护成本低,对加工费用降低提供了先决条件。
3.4激光加工的应用
1)激光快速成型技术。
激光快速成型技术一改传统加工“去除”成型加工工艺,改为“堆积”成型加工工艺,在加工领域具有划时代的意义。
2)激光焊接技术。
激光焊接是利用高能量激光束照射焊接工件,工件受热融化,然后冷却得到焊接的目的。
激光焊接的显著特征是大熔、焊道、小热影响区,以及高功率密度,大气压力下进行不要求保护气体,不产生X射线,在磁场内不会出现束偏移,更加之该法焊速快、与工件无机械接触、可焊接磁性材料便于实现遥控等优点,尤其可焊高熔点的材料和异种金属,并且不需要添加材料,因此很快在电子行业中实现了产业化。
激光焊接有两种基本方式:
传导焊与深熔(小孔)焊。
3)激光打孔技术。
激光打孔技术具有精度高、通用性强、效率高、成本低和综合技术经济效益显著等优点。
激光打孔技术朝着多样化、高速度、高精度、直径更微小的方向发展。
4)激光切割技术。
激光切割以其切割范围广、切割速度高、切缝窄、切割面粗糙度低、热影响区域小、加工柔性好、可实现众多复杂零件的切割等优点而应用越来越广。
激光切割技术可广泛应用于金属和非金属材料的加工中,可大大减少加工时间,降低加工成本,提高工件质量。
脉冲激光适用于金属材料,连续激光适用于非金属材料,后者是激光切割技术的重要应用领域。
5)激光打标技术。
激光打标是利用高能量密度的激光对工件进行局部照射,使表层材料汽化或发生颜色变化的化学反应,从而留下永久性标记的一种打标方法。
激光打标可以打出各种文字、符号和图案等,字符大小可以从毫米量到微米量级,这对产品的防伪有特殊的意义。
6)激光刻蚀技术。
激光刻蚀技术主要应用在高集成度电路的制作。
(准分子激光)
7)激光微调技术。
激光微调主要用于调整厚膜电路或薄膜电路中的电阻、电容以及其他多种功能参数。
激光调阻时,受到照射的部位受热汽化挥发,阻值区域截面面积减小,随之阻值增大。
激光微调的实质是打孔,每次打孔都很浅,约至几十纳米至几十微米之间,然后通过连续不断的打孔,搭接成一条线。
激光微调电阻除用强光照射将部分电阻膜气化外,还可通过无损伤照射改变膜的结构达到调整阻值的目的。
激光调阻技术主要应用于精密电阻阻值调解,精度可达0.1‰~0.02‰。
8)激光存储技术。
激光存储技术是信息以反射/非反射带(正常表面和凹坑)的序列编码,已达到信息存储的目的。
因数据存储密度与激光波长的平方成反比,所以,发展波长更短的激光是提高激光存储技术的关键。
9)激光划线技术。
由于激光对划片材料几乎不产生机械冲力和压力,加上激光光斑小、划缝窄,所以特别适宜于对细小部件作各种精密加工。
但由于用于激光加工的整套设备技术含量高,售价亦很高。
10)激光清洗技术。
激光清洗技术的使用有效地解决了集成电路的清洗。
11)激光热处理。
激光热处理是指利用激光高能量密度的能量照射金属材料表面时,材料表层温度迅速升高,当激光停止作用后,材料基体温度迅速下降,从而使材料表层经历一个热处理过程。
激光热处理技术由于成本高、控制复杂,还处于实验室技术层面,还没有大范围、大面积的工业化应用。
12)表面处理技术。
激光表面处理主要包括以下几方面的工艺:
激光表面相变硬化(LTH)、激光表面熔化(LSM)、激光表面合金化(LSA)、激光表面涂覆(LSC)以及激光表面冲击硬化(LSH)。
4微机数控旋转电火花加工
4.1旋转电火花加工机理
图1-10所示为旋转电火花加工机床,旋转电火花加工是一种电火花加工和传统的机械加工相结合的复合加工方法。
其实现方法为:
采用旋转的高纯石墨轮(或紫铜)电极作为工具电极,被加工的工件如聚晶金刚石等作为工件电极,工具电极与工件电极间保持适当的放电间隙,如果工件电极与工具电极之间的间隙过大,则无法形成火花放电,加工过程将中断,如果间隙过小,则出现短路,加工也无法正常进行。
因此,在加工过程中保持适当的放电间隙尤为重要。
4.2旋转电火花加工机床
图1-10旋转电火花加工机床
4.3旋转电火花加工的特点
旋转电火花加工放电形成过程与一般电火花放电形成过程基本是一致的,但旋转电火花加工具有两个特点:
一是电极是旋转的,二是采用了冲液冷却。
因此,它具有一些特殊的机理:
工具电极与工件电极间存在一个相对运动,放电通道是移动的,其间隙电压随放电通道的移动而频繁的变化;采用冲液方法进行冷却,可以使放电中产生的电蚀产物、气泡等许多杂质能很快的从间隙中排除,并把放电产生的热量迅速带走,保证了放电间隙中工作液介质的纯净及较低的温度。
4.4旋转电火花加工的应用
能加工平面、外圆、螺旋槽以及各种异型孔、槽等超硬导电材料的复杂型面,实现了传统机械加工和普通电火花加工所不能完成的加工要求。
旋转电火花加工平面的过程如图1-11所示。
直流电机驱动机床主轴工件安装-聚晶金刚石调整车刀和刀具
输入程序和放电参数开始加工
图1-11旋转电火花加工平面
5超声波加工
5.1超声波加工的基本原理
超声波加工是利用工具端面作超声频振荡,再将这种超声频振荡,通过磨料悬浮液传递到一定形状的工具头上,加工脆硬材料的一种成形方法。
加工原理如图1-12所示。
图1-12超声波加工原理示意图
1-工具2-冷却器3-加工槽4-夹具5-工件6-磨料悬浮液7-振动头
5.2超声波加工设备的组成
(1)超声波发生器
超声波发生器也称超声或超声频发生器,其作用是将50Hz的交流电转变为有一定功率输出的16 000Hz以上的超声高频电振荡,以提供工具端面往复振动和去除被加工材料的能量。
其基本要求是输出功率和频率在一定范围内连续可调,最好能具有对共振频率自动跟踪和自动微调的功能,此外要求结构简单、工作可靠、价格便宜、体积小等。
(2)超声振动系统
超声振动系统的作用是把高频电能转变为机械能,使工具端面作高频率小振幅的振动,并将振幅扩大到一定范围(0.01~0.15mm)以进行加工。
它是超声波加工机床中很重要的部件。
由换能器、变幅杆(振幅扩大棒)及工具组成。
(3)磨料工作液及循环系统
对于简单的超声波加工装置,其磨料是靠人工输送和更换的,即在加工前将悬浮磨料的工作液浇注堆积在加工区,加工过程中定时抬起工具并补充磨料。
也可利用小型离心泵使磨料悬浮液搅拌后注入加工间隙中去。
对于较深的加工表面,应将工具定时抬起以利于磨料的更换和补充。
大型超声波加工机床采用流量泵自动向加工区供给磨料悬浮液,且品质好,循环也好。
(4)机床本体
超声波加工机床一般比较简单,机床本体就是把超声波发生器、超声波振动系统、磨料工作液及其循环系统、工具及工件按照所需要位置和运动组成一体。
还包括支撑声学部件的机架及工作台、使工具以一定压力作用在工件上的进给机构及床体等部分。
5.3超声波加工的特点
1)工具可用较软的材料、做成较复杂的形状,且不需要工具和工件作比较复杂的相对运动,便可加工各种复杂的型腔和型面。
一般,超声加工机床的结构比较简单,操作、维修也比较方便。
2)超声加工的面积不够大,而且工具头磨损较大,故生产率较低。
3)适合加工各种硬脆材料,尤其是玻璃、陶瓷、宝石、石英、锗、硅、石墨等不导电的非金属材料。
也可加工淬火钢、硬质合金、不锈钢、钛合金等硬质或耐热导电的金属材料,但加工效率较低。
4)由于去除工件材料主要依靠磨粒瞬时局部的冲击作用,故工件表面的宏观切削力很小,切削应力、切削热更小,不会产生变形及烧伤,表面粗糙度也较低,可达Ra0.63-0.08um,尺寸精度可达正负0.03mm,也适于加工薄壁、窄缝、低刚度零件。
总之,超声波打孔机是磨料悬浮液中的磨粒,在超声振动下的冲击、抛磨和空化现象综合切蚀作用的结果。
其中,以磨粒不断冲击为主。
由此可见,脆硬的材料,受冲击作用愈容易被破坏,故尤其适于超声加工。
5.4超声波加工的应用
1)成形加工
超声波加工各种硬脆材料的圆孔、型孔、型腔、沟槽、异形贯通孔、弯曲孔、微细一孔、套料等。
虽然其生产率不如电火花、电解加工,但加工精度及工件表面质量则化于电火花、电解加工。
例如,生产上用硬质冶金代替合金工具钢制造技深模、拉丝模等模具,其耐用度可提高80-100倍。
采用电火花加工,工件表面常出现微裂纹,影响了模具表面质量和使用寿命。
而采用超声加工则无此缺陷,且尺寸精度可控制在0.01-0.02mm之内、内孔锥度可修整至8'。
对硅等半导体硬脆材料进行套料等加工,更显示了超声波加工的特色。
例如,在直径90mm、厚0.25mm的硅片上,可套料加工出176个直径仅为1mm的元件,时间只需1.5min,合格率高达90%-95%,加工精度为正负0.02mm。
此外,近年来,超声加工已经排除其通向微细加工领域的障碍。
图5-14是日本东京大学工业科学学院采用超声加工方法,加工出的微小透平胜和玻璃上直径仅9um的微孔。
2)切割加工
超声精密切割半导体、铁氧体、石英、宝石、陶瓷、金刚石等硬脆材料,比用金刚石刀具切割具有切片薄、切口窄、精度高、生产率高、经济性好的优点。
例如,超声切割高7mm、宽15-20mm的锗晶片,可在3.5min内切割出厚0.08mm的薄片;超声切割单晶硅片一次可切割10-20片。
再如,在陶瓷厚膜集成电路用的元件中,加工8mm、厚0.6mm的陶瓷片,1min内可加工4片;在4X1mm2的陶瓷元件上,加工O.03mm厚的陶瓷片振子,0.5-1min以内,可加工18片,尺寸精度可达正负0.02mm。
3)焊接加工
超声焊接是利用超声频振动作用,去除工件表面的氧化膜,使新的本体表面显露出来,并在两个被焊工件表面分子的高速振动撞击下,摩擦发热。
亲和粘接在一起。
其不仅可以焊接尼龙、塑料及表面易生成氧化股的铝制品等,还可以在陶瓷等非金属表面挂锡、挂银、涂覆薄层。
由于超声焊接不需要外加热和焊剂,焊接热影响区很小,施加压力微小,故可焊接直径或厚度很小的(O.015-0.03)不同金属材料,也可焊接塑料薄纤维及不规则形状的硬热塑料。
目前,大规模集成电路引线连接等,已广泛采用超声焊接。
4)超声清洗加工
主要用于几何形状复杂、清洗质量要求高的中、小精