高精度及极薄钢带的生产.docx
《高精度及极薄钢带的生产.docx》由会员分享,可在线阅读,更多相关《高精度及极薄钢带的生产.docx(33页珍藏版)》请在冰豆网上搜索。
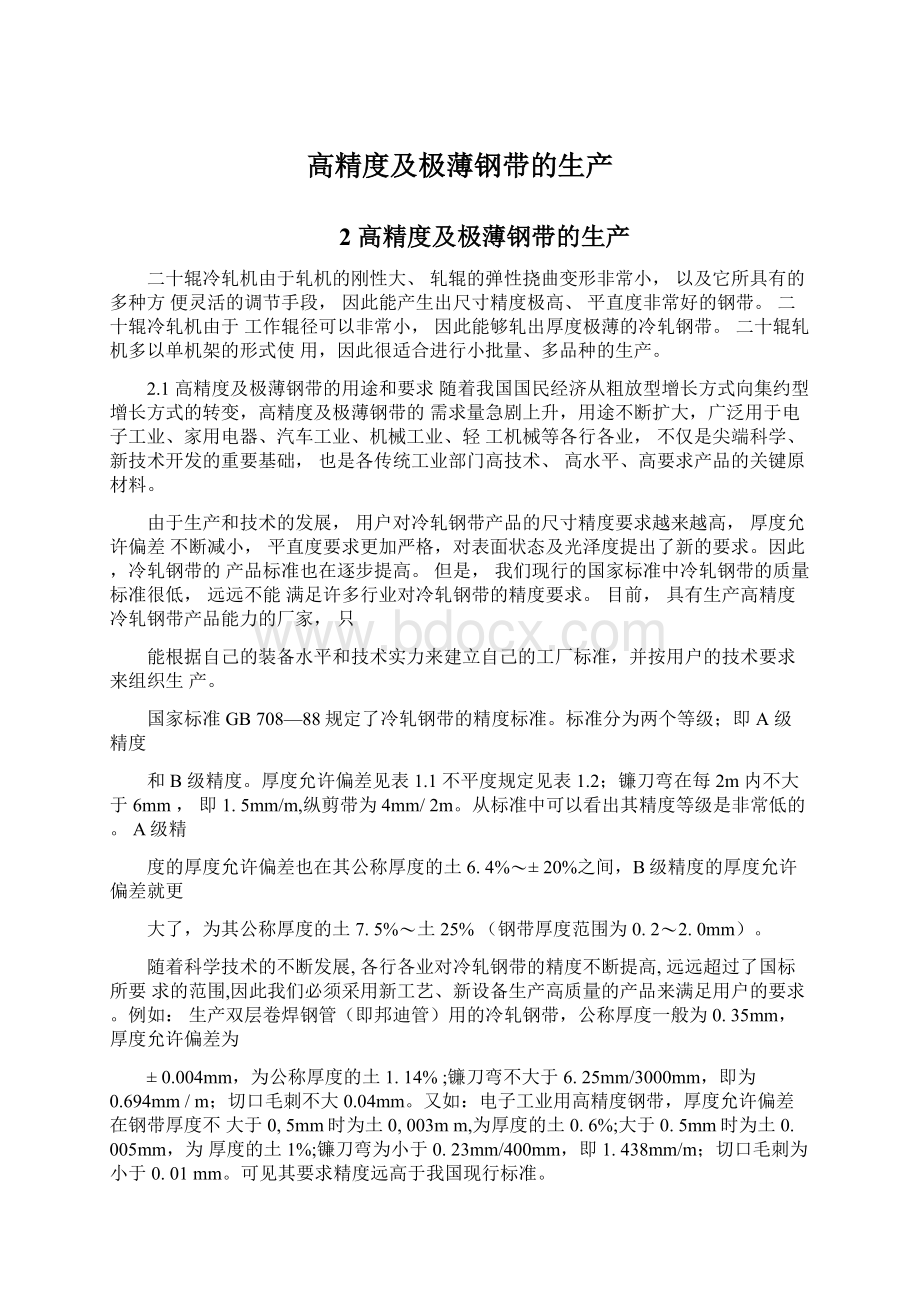
高精度及极薄钢带的生产
2高精度及极薄钢带的生产
二十辊冷轧机由于轧机的刚性大、轧辊的弹性挠曲变形非常小,以及它所具有的多种方便灵活的调节手段,因此能产生出尺寸精度极高、平直度非常好的钢带。
二十辊冷轧机由于工作辊径可以非常小,因此能够轧出厚度极薄的冷轧钢带。
二十辊轧机多以单机架的形式使用,因此很适合进行小批量、多品种的生产。
2.1高精度及极薄钢带的用途和要求随着我国国民经济从粗放型增长方式向集约型增长方式的转变,高精度及极薄钢带的需求量急剧上升,用途不断扩大,广泛用于电子工业、家用电器、汽车工业、机械工业、轻工机械等各行各业,不仅是尖端科学、新技术开发的重要基础,也是各传统工业部门高技术、高水平、高要求产品的关键原材料。
由于生产和技术的发展,用户对冷轧钢带产品的尺寸精度要求越来越高,厚度允许偏差不断减小,平直度要求更加严格,对表面状态及光泽度提出了新的要求。
因此,冷轧钢带的产品标准也在逐步提高。
但是,我们现行的国家标准中冷轧钢带的质量标准很低,远远不能满足许多行业对冷轧钢带的精度要求。
目前,具有生产高精度冷轧钢带产品能力的厂家,只
能根据自己的装备水平和技术实力来建立自己的工厂标准,并按用户的技术要求来组织生产。
国家标准GB708—88规定了冷轧钢带的精度标准。
标准分为两个等级;即A级精度
和B级精度。
厚度允许偏差见表1.1不平度规定见表1.2;镰刀弯在每2m内不大于6mm,即1.5mm/m,纵剪带为4mm/2m。
从标准中可以看出其精度等级是非常低的。
A级精
度的厚度允许偏差也在其公称厚度的土6.4%〜±20%之间,B级精度的厚度允许偏差就更
大了,为其公称厚度的土7.5%〜土25%(钢带厚度范围为0.2〜2.0mm)。
随着科学技术的不断发展,各行各业对冷轧钢带的精度不断提高,远远超过了国标所要求的范围,因此我们必须采用新工艺、新设备生产高质量的产品来满足用户的要求。
例如:
生产双层卷焊钢管(即邦迪管)用的冷轧钢带,公称厚度一般为0.35mm,厚度允许偏差为
±0.004mm,为公称厚度的土1.14%;镰刀弯不大于6.25mm/3000mm,即为0.694mm/m;切口毛刺不大0.04mm。
又如:
电子工业用高精度钢带,厚度允许偏差在钢带厚度不大于0,5mm时为土0,003mm,为厚度的土0.6%;大于0.5mm时为土0.005mm,为厚度的土1%;镰刀弯为小于0.23mm/400mm,即1.438mm/m;切口毛刺为小于0.01mm。
可见其要求精度远高于我国现行标准。
生产高质量的产品必须要有高精度的生产设备。
二十辊冷轧机就是生产高精度冷轧钢带的最理想的设备。
图1.1给出了国标中冷轧钢带厚度允许偏差及二十辊冷轧机所能达到的钢带厚度精度。
从图1.1不难看出,二十辊轧机具有极高的精度:
当产品厚度大于0.1mm
时,产品的厚度偏差在其厚度的土1%以内;厚度大于0.5m时,产品的厚度偏差在土0.5%以内;在产品厚度小于0.1mm的条件下,产品的厚度偏差可以达到±0.001mm
2.2生产工艺
高精度冷轧钢带、极薄钢带、热镀锌钢带以及彩色涂层钢带的生产工艺流程如图1.2所示。
产品供应状态有钢板、钢带或者纵剪钢带等形式。
图1.3是高精度冷轧钢带及极薄钢带车间平面布置一例,图1.4是该车间的工艺流程图。
该车间使用一台二十辊森吉米尔冷轧机,生产厚度为0.05—1.0mm、宽度为250〜
450mm的高精度冷轧钢带及极薄钢带,最高轧制速度为400m/min
图1.5是一个典型小型冷轧钢带车间的平面布置图,图1.6是该车间的工艺流程图。
该小型冷轧车间的年生产能力在20万t至35万t的范围;小型涂层线的年生产能力为
5万t至10万t车间采用一台二十辊森吉米尔冷轧机(如ZR22—52”型),用宽度为650—
1250mm、厚度为2〜6mm的热轧钢带卷,生产厚度为0.3—1.6mm的冷带,最大卷重20t最大轧制速度为600m/min;配套设备有一条推拉式酸洗线、一条小型连续热镀锌线、一条小型带卷彩色涂层线及一条横切线。
该车间的中间产品为热轧酸洗钢带及高硬度的冷轧钢
带。
2.3原料准备
2.3.1冷轧钢带的原料
冷轧钢带生产是钢带轧制的精加工过程。
冷轧钢带的原料就是热轧钢带。
要获得高质的
冷轧钢带,必须要有良好的热轧钢带原料来保证。
钢的化学成分、纯净度及热轧工艺的控制,对最终冷轧钢带产品的组织、性能有极大的
响;热轧钢带的外形尺寸、板形及表面状态,将直接影响冷轧钢带的尺寸精度、板形和表面
2.3.1.1钢质对冷轧钢带性能的影响
炼钢时控制好钢的化学成分是保正生产出优质冷轧钢带的基础,钢的化学成分与钢的成
形性能有密切的关系。
钢的碳含量对钢带成形性能的影响是通过影响钢的屈服极限cs和塑性应变比R来实现
的。
碳是提高钢的强度最显著的元素之一,碳含量增加,R值减小、成形性能变坏。
碳对钢
带成形性能的影响可以从图1.7中看出。
塑性应变比只是拉伸试验中宽度应变与厚度应变的比值,可以用下式表示:
式中B、H――分别为试样的宽度、厚度;
脚注0、1――分别代表试样变形前及变形后的数字。
通常钢板具有各向异性,故R值应取与轧制方向成90°、45°、00角的试样试验结果的
平均值,即:
当R<1时,说明材料厚度方向容易变形减薄、致裂,冲压性能不好。
当R>1时,说明
在冲压成形过程中,长度和宽度方向的变形容易,能抵抗厚度方向的变薄,而厚度减薄是冲压过程中发生断裂的原因,所以尺值大,成形性能好。
匚S也上升。
锰使钢加工硬
(质量分数)一般不低于
锰是提高屈服极限6的一个因素,随着钢中锰含量的增加,比。
但是,锰含量太低也将失去防止钢的热脆的能力。
因此,锰含量
0.02%。
硫、磷一般在钢中以有害元素身份出现。
硫是钢发生热脆的根源;硫化物夹杂促使钢中形成带状组织,恶化深冲性能;硫有提高屈服极限cs的趋势,不利于冲压成形,参见图1.8。
为防止硫对冲压用钢的不良影响,冲压
用钢的硫含量(质量分数)一般都限定在不大于0.025%,最好小于0.02%。
磷能溶解于铁素体内,使铁索体在室温下硬度和强度增高、塑性下降,即产生冷脆现象;
同时磷能引起剧烈的加工硬化;它又是偏析比较严重的一种元素,并且很难经扩散退火完全
消除,所以容易出现带状组织,给冲压带来不利影响。
钢中磷含量(质量分数)越低越好,应
不大于0.02%。
硅是深冲用钢不希望含有的一种元素,因为它可提高钢的硬度和强度,一般硅含量(质
量分数)被限制在不大于0.01%的范围内。
铝加入钢中的目的是做脱氧剂,钢中适量的铝能消除钢的时效硬化性,提高冲压性能,其关系见图1.9。
钢中的氧和氮都是产生时效硬化的元素,加入铝使氧和氮固定在AL2O2和
A1N中,能排除时效硬化的可能性;同时,铝还可控制晶粒度和晶粒形状,形成{111}织构,
AIN后,多余的金属铝在钢中则起到了合金化的作用,使钢的屈服极限
趋势。
因此,钢中金属铝的理想含量(质量分数)应是0.04%〜0.05%,但是实际生产中很
难将铝含量控制在如此窄的范围内,一般标准将其控制在0.025%〜0.07%的范围内。
为提高钢带的冲压性能,应尽量降低钢中碳、锰含量,在较窄的范围内控制铝的含量,严格控制有害元素硫、磷含量。
表6-6列出了几家深冲用钢08AI的化学成分标准及实际的
出厂成分。
冲压钢板按发展历史和冲压性能水平,可分为三代产品。
冲压用钢的主要要求之一是具有占优势的有利织构,即有利织构系数111/[100]高。
低碳优质沸腾钢代表了第一代产品,
它与各向同性的无取向正火钢相比是一个进步,它有较弱的{1111}织构,塑性应变比R值为
1.0〜1.2,冲压成形性较差,沸腾钢中的固溶氮含量较高,具有明显的应变时效性。
铝镇静钢是第二代产品,通过对A1N的固溶和析出的控制,铝镇静钢具有强的{111}织构,从
而获得了良好的深冲性能,R值为1.4〜1.8,铝镇静钢在罩式炉退火过程中绝大部分碳
析出成Fe3C,经平整后其性能稳定;因此,自铝镇静钢问世之后,绝大多数钢铁生产厂家的冲压用薄钢板都是以铝镇静钢为基础生产的。
冲压用钢的第三代产品是20世纪80年代中
迅速发展起来的IF钢,IF钢具有超低碳、微合金化和钢质纯净的特点,IF钢具有极为强烈
的{111}织构,R值可达1.8—2.8,可用于大尺寸整体成形极其复杂的冲压件,IF钢无时
效性。
IF钢又称无间隙原子钢。
碳含量低是IF钢最显著的特征,一般W(C)<0.005%。
IF
钢中添加的微合金元素主要是强碳、氮化物形成元素钛或铌,一般按下式加入:
从式中可以看出,钢水中的碳、氮含量必须设法减少,才能节约钛和铌降低成本。
在
IF钢中杂质元素一般控制在很低的水平,钢质非常纯净,杂质含量为:
为使IP钢成分合格,应采甩特殊冶炼和浇注工艺。
需选用杂质含量低、成分均匀的生铁,铁水进行预处理,达到W(S)<0.01%的水平。
冶炼后进行真空脱气处理,使铁水脱碳。
连铸时,应采用氩气进行保护浇注,中间罐吹氩,应用无碳保护渣等措施。
三代冲压用钢性能比较见表1.7。
表1.7中的n为加工硬化指数。
加工硬化指数可表示如下:
式中一一分别为拉伸15%和5%时的力;
――分别为拉伸15%和5%时的长度;
――分别为拉伸15%和5%时的长度与厚度之差。
n值大,拉伸能力强,冲压性能好;而n值小时,冲压性能差。
加工硬化指数,2、塑性应变比R都是评价材料冲压或成形性能的重要参数,但是二者
又有所侧重。
一般冲压变形是冲压和拉延复合变形的过程,可能以其中一种变形为主。
当以冲压变形为主时,要求钢的塑性应变比R值要高;当以拉延变形为主时,则要求钢具
有较高的加工硬化能力,即n值要大。
在冲压变形和拉延变形都存在的复合变形情况下,同
时要求具有较大的R值和n值。
即使在一种变形为主,另一种变形为辅的情况下,只值和n
值都大,也有利于冲压成形,故一般常用这两个指数一块来评价。
2.3.1.2热轧工艺对冷轧钢带性能和组织的影响
热轧钢带的组织和性能直接影响到冷轧钢带的组织和性能。
影响热轧钢带组织和性能的
因素有:
钢坯的加热温度和加热时间、轧制温度、终轧变形程度及卷取温度等。
对于低碳钢,热轧、冷轧的组织特征都是铁素体晶粒组织和一定数量的渗碳体,所以决
定其组织特征的铁素体晶粒大小,形状及均匀程度,渗碳体的尺寸大小及分布的弥散程度决
定了钢的性能的好坏。
冷轧退火后钢板的铁素体晶粒的大小,除与冷轧热处理条件有关外。
也与热轧钢带的显微组织有关。
热轧钢带的显微组织特征会保持在冷轧钢带上,冷轧时消除
不了热轧变形时得到的粗大晶粒、过细晶粒及晶粒不均,这些都将遗传到冷轧钢带上。
这些
现象已为生产实践所证明。
热轧时钢坯的加热温度和加热时间的控制实质上是对奥氏体晶粒度的控制。
加热温度一般为1150~1250C,加热时必须防止产生过烧、过热及严重脱碳现象,保温时间不宜超过均热要求的时间。
热轧过程中,调整控制终轧温度及终轧变形程度,对控制奥氏体的再结晶而言无疑是非
常重要的。
关于热轧终轧变形程度不应该是临界变形量(小于10%),因为这时得到的是大晶
粒和不均匀晶粒,有时表面为大晶粒,而中间晶粒细小。
但是不能孤立地考虑终轧变形程度,必须充分估计到整个轧制过程变形积累性的影响。
终轧温度及卷取温度对热轧钢带的组织和性能的影响更重要。
低的终轧温度和卷取温度,使钢带形成变形晶粒。
在这种情况下,冷轧退火后的冷轧钢带将得到过于细小的晶粒,相伴产生拉长了的铁素体晶粒组织,冷变形很困难。
从高的终轧温度和卷取温度缓慢冷却下来时,将得到粗大晶粒并析出大的渗碳体。
在冷轧时粗大晶粒和大的渗碳体被轧碎,这就创造了冷轧后产生条状渗碳体的条件,这正是在
冲压时产生断裂的原因。
渗碳体尺寸决定于热轧卷取的温度,而渗碳体在钢组织中的分布是由热轧终轧温度决定的。
为了得到均匀的铁素体晶粒和细小分散、均匀分布的渗碳体,最佳的热轧条件是:
终
轧温度应略高于Ar3,轧后快速冷却保证成卷温度低于Ari。
图1.10是低碳钢的终轧温度与卷取温度的配合及其组织示意图。
图1.10之〉区,为低碳钢在Ar3温度线以上完成轧制,卷取温度在680C以下,可得
到最好的效果,可以保证获得均匀等轴细晶组织,以及弥散程度较高的碳化物;b区,终轧
温度在Ar3以下,并在680C以下低温卷取,获得不均匀晶粒结构,在钢带表面出现粗晶;区,终轧温度在Ari以下,出现被延伸的铁素体晶粒,在低温卷取时,拉长的晶粒仍然保留下来;d区,是在Ar3以上完成轧制过程,在705C以上进行高温卷取,从而生成均匀的粗晶组织,同时碳化物已有相当程度的积聚;e区,在Ar3以下轧完并进行高温卷取,产生很
不均匀的粗晶组织,表面的晶粒极为粗大;/区,终轧温度在Ari以下进行低温轧制,而进
行高温卷取,由于自身回火进行再结晶而造成粗晶组织。
加热温度高、开轧温度高、终轧温度高及卷取温度低的“三高一低”轧制工艺,是深冲用钢以冷轧后在罩式退火炉中进行再结晶为基础的传统工艺。
高温加热有利于使晶粒均匀;
低温卷取可防止AIN沉淀析出,这样钢带冷轧后在罩式炉退火的加热过程中,在再结晶开始以前的缓慢加热的某个适当的温度范围内,AIN呈极微细的析出,促使有利于深冲性
能的{111}再结晶织构形成和抑制不利结构{100},{110}的发生。
20世纪70年代以后,冶炼技术和热轧生产的进步使得连续退火机组生产冲压板获得了成功,并且超过了罩式炉。
如果冷轧后采用连续退火机组生产冷轧钢带,则要在热轧时采用高温卷取而不是低温卷取。
卷取温度为700〜750C,比传统工艺高100—150C。
高温卷取使得铁素体晶粒和碳化物粗大,再结晶退火时的MnS以适当尺寸析出,由此消除了阻碍晶粒长大的主要因素
MnS和碳化物,并且再结晶时碳化物在a-Fe中再溶解缓慢,由于MnS在晶界析出,
特定的结晶方位发达,可得到高的R值。
现代超低碳钢冶炼工艺,改变了生产深冲冷轧钢带的传统工艺。
IF钢具有优异的深
冲性和无时效性。
IF钢由于添加了微合金元素钛和铌,板坯加热温度高对材料力学性能有不利影响,采用低的板坯加热温度比较合适,一般为1050C左右。
终轧温度对钛处理IF钢
的尺值影响很小,对铌一钛复合处理IF钢影响则要大一些,铌处理IF钢终轧温度变化对性
能有重要影响。
快速大压下轧制,提高终轧温度(高于Ar3),已为目前IF钢生产广泛采用,
特别是铌处理和复合处理IF钢,有利于碳氮化合物的粗化。
IF钢对卷取温度要求较宽松,
有人研究认为,Ti—IF钢高温卷取(》750C)比低温卷取(<650C)的R值高。
考虑到高温卷取导致氧化铁皮厚、酸洗效率降低、成材率下降,1F钢本质上又具有超深冲性,可以补偿
低温卷取带来的性能不足,IF钢宜采用低温卷取,卷取温度为650〜700C。
热轧时应设法
获得均匀、细小的铁素体组织,以利于深冲性能的提高。
采用不同的冷轧退火工艺的铝镇静钢及IF钢的热轧工艺变化如图1.11所示。
2.3.1.3热轧钢带几何尺寸对冷轧钢带精度的影响
钢带由于其断面的宽高比很大,并且一般是在带有前后张力的条件下进行轧制,特别是
二十辊轧机等多辊轧机是采用大张力轧制,因此在钢带冷轧过程中几乎就没有宽展发生,钢
带厚度的减薄完全转变成钢带长度的增加。
为了保证冷轧钢带产品的平直度,冷轧过程中冷
轧钢带产品的横断面尺寸应按热轧钢带的横断面尺寸成比例地减少,否则将影响冷轧钢带产
品的平直度,产生浪形或镰刀弯。
但是,热轧钢带在长度方向的厚度不均,经过冷轧加工后
可以减轻,特别是现代化的冷轧机,在采用了AGC自动厚度控制技术后,冷轧钢带的纵向
厚度偏差可以控制在产品厚度的土1%的范围内,产品厚度大、冷轧加工量大,则厚度精度
更高。
另外,热轧钢带板形不好、钢带头尾偏差大、浪形大、厚度不均也会严重影响冷轧正常
进行。
当进行全连轧时,头尾厚度偏差过大,会使对焊时焊接不牢而容易造成断带。
2.3.2原料酸洗
2.3.2.1热轧钢带表面的氧化铁皮
热轧钢带表面的氧化铁皮是钢带在热连轧机上轧制时,在高温下生成的二次氧化铁皮。
由于钢的化学成分、轧制温度、终轧温度、轧后冷却速度及卷取温度的不同,表面氧化铁皮的组织和结构也有所不同。
冷轧前必须将钢带表面的氧化铁皮去除干净。
低碳钢热轧钢带表面的氧化铁皮,主要是铁的氧化物,直接附在基铁表面的一层是FeO
和Fe3O4的固溶体,其组织是疏松、多孔的细结晶组织;再上面一层是磁性氧化铁FEO4,
其组织是致密、无孔和无裂纹,呈玻璃状的断口组织;最上面一层是氧化铁Fe2O3,呈柱状
结晶构造。
由于碳钢中含有少量的碳、锰、硅、硫、磷等兀素,因此,在氧化铁皮中除了铁的氧化物之外,还含有部分其他元素的氧化物。
低碳钢热轧钢带氧化铁皮的厚度,一般在6〜15」m范围内,个别达到20」m。
如果热连轧后采用层流冷却方式,氧化铁皮厚度小于10」m。
当在570C低温卷取时,氧化铁皮
厚度大约为6」m;如果在750C高温卷取,则铁皮厚度达到12」m。
钢带表面氧化铁皮的
最内层FeO和Fe304的固溶物是氧化铁皮中最厚的一层,大约占整个氧化铁皮厚度的80%;
中间的磁性氧化铁Fe304,占整个氧化铁皮厚度的约18%;最外层的氧化铁Fe2O3,仅占整个氧化铁皮厚度的约2%。
氧化铁皮的单重波动在35—55g/m2范围内。
2.3.2.2酸洗方式
碳素钢热轧钢带的酸洗采用硫酸作酸洗介质和采用盐酸作酸洗介质都是可行的。
新建钢
带酸洗机组具体采用何种酸洗方式,还得根据机组的生产能力、酸液供给、成本等因素综合考虑。
20世纪60年代以前,除了镀层钢带采用盐酸酸洗外,其他钢带酸洗基本上都是采用硫酸酸洗方式。
从60年代起,由于对酸洗工艺及设备的研究,成功地设计和建立了盐酸酸洗废液的再生装置,解决了废盐酸的再生回收问题;钢带盐酸塔式酸洗机组的发明,为钢带采
用盐酸酸洗开辟了一条新路;随着现代工业的发展,新的耐酸材料的出现;以及盐酸与硫酸
价格比发生了变化,这就使得盐酸酸洗方式逐渐得到推广,盐酸酸洗的经济效益和酸洗工艺
上的优点就被充分显示出来。
以后,除新建了许多大型的连续盐酸酸洗机组外,还将许多原
有的硫酸酸洗机组逐步改造成了盐酸酸洗机组。
盐酸酸洗机组之所以得到如此大的发展,是因为盐酸酸洗比硫酸酸洗具有更多的优点:
首先,盐酸可以完全溶解钢带表面氧化铁皮中的3种氧化铁(FeO、Fe3O4、Fe2O3)。
这
样,酸洗后钢带表面没有残留的氧化铁存在,因此酸洗钢带表面质量好;同时在钢带表面上的酸洗反应物一般为亚铁盐,它极易溶于水,因之酸洗后容易用水将其从钢带表面上冲洗干净,所以一般盐酸酸洗钢带具有清洁、光亮、没有斑痕,呈银白色的平滑表面,对于下一步冷轧工序极为有利;酸洗速度快,它几乎是硫酸酸洗速度的两倍;不需要破鳞,这不仅省掉了破鳞机,而且避免了机械损伤钢带表面,因而也改善了钢带表面质量;在酸洗槽内和中间储酸罐内,没有氧化铁皮(铁鳞片)积存。
其次,盐酸酸洗几乎不浸蚀钢带机体。
这样,钢带不容易发生过酸洗和氢脆现象,酸洗缺陷少;酸洗铁损少,盐酸酸洗比硫酸酸洗金属损失少20〜25%。
第三,用于酸洗的盐酸可以完全再生成为新酸(再生酸),酸气和废酸都可以完全回收,
整个系统是一个封闭的循环系统,系统中没有被遗弃的酸液和酸气,排出的是Fe2O3粉。
高质量的Fe2O3粉可作软磁合金的高档原料使用;大颗粒的Fe2O3粉也可作为矿石使用。
盐酸用于酸洗,除了它的许多优点外,也有它的一些问题。
60年代以前,正是由于这
些问题没有得到解决,限制了盐酸酸洗的发展:
第一,盐酸极易挥发,生产设备不易密封,造成车间内酸气弥漫,不仅严重腐蚀厂房、设备,而且酸气刺鼻呛人,腐蚀皮肤,使得劳动条件恶劣;
第二,盐酸的腐蚀性强,它的储存和运输不如硫酸方便;
第三,废盐酸液的处理问题没有解决,在当时的情况下,废盐酸中的FeCl2很难用普通的方法分离出来,而采用中和处理的费用又很高;
第四,质量分数为98%的硫酸比质量分数为32%的工业盐酸价钱便宜。
A硫酸酸洗
纯净的硫酸是无色、黏稠、透明的油状液体,不易挥发。
常用浓硫酸的质量分数为98%,密度约为1..84kg/L。
硫酸具有极为活泼的化学性质,它可以与金属及金属的氧化物发生化学反应,生成盐、氢气或水。
酸洗正是利用硫酸的这种化学性质来清除碳钢表面的氧化铁皮。
在硫酸溶液中酸洗时的化学反应式是:
Fe2O3、Fe3O4很不易溶解于硫酸,反应式1-6、式1-7进行得很缓慢。
反应式1-8进行得特别快,因为FeO在硫酸中溶解最快。
在这种情况下,反应式1-9的纯铁与硫酸反应而析出氢气,氢气的析出对酸洗有很大的帮助,它机械地使未溶解的氧化铁皮自基铁表面剥落下来。
在连续酸洗中,硫酸的质量分数一般为15%一25%,酸洗速度与酸液的质量分数和温
度有很大的关系。
对硫酸而言,温度升高的影响大于质量分数增加的影响。
质量分数为25%--30%的H2SO4在95C时酸洗时间最短,而且铁损也最少。
图1•14示出了酸洗时间与酸
洗温度的关系,图中也清楚地示出,当温度从90—95C继续提高到100C时,酸洗时间不会再缩短很多。
图1-15示出了酸洗时间与硫酸的质量分数的关系。
B盐酸酸洗
纯净的盐酸是五色、透明的液体,有刺激性气味,浓盐酸中约含37%(质量分数)的氯化氢,密度约为1.19kg/L。
一般工业用盐酸的质量分数为30%~35%,由于含有杂质而带黄
色。
常见的含31%(质量分数)HCI的工业盐酸密度为1.154kg/L,每升含HCI357.9g,1t质量分数为31%的工业盐酸含HCl310kg。
盐酸具有酸的一切化学性质,它可与金属及金属的氧化物发生化学反应,生成盐、氢气或水。
碳钢在盐酸溶液中酸洗时的化学反应式是:
在盐酸溶液中反应式1-12的反应速度最快,反应式1—10、式1—11次之,反应式1—13最慢。
盐酸酸洗主要是通过化学作用溶解钢带表面的氧化铁皮,其酸洗侵蚀能力随着温度和盐酸质量分数的提高而剧烈增大。
盐酸具有很大的溶解能力,酸洗速度相当高。
图1—
16为盐酸质量分数、温度与酸洗时间的关系。
在现代新的密闭式盐酸酸洗机组中酸洗温度为70~90C,盐酸酸洗液的HCI含量(质
量分数)为5%〜20%。
盐酸酸洗时,金属铁与盐酸作用首先产生氢原子(反应式1—13)。
一部分氢原子相互结
合为氢分子,促使氧化铁皮的剥离。
另一部分氢原子靠其化学活泼性及很强的还原能力,将高价铁的氧化物和高价铁盐还原成易溶于盐酸溶液的低价铁及低价铁盐。
其反应式为:
分析使用过的盐酸酸洗溶液会发现,酸液中只含有极少量的三价铁离子,这