焊接车间工艺平面布置设置.docx
《焊接车间工艺平面布置设置.docx》由会员分享,可在线阅读,更多相关《焊接车间工艺平面布置设置.docx(25页珍藏版)》请在冰豆网上搜索。
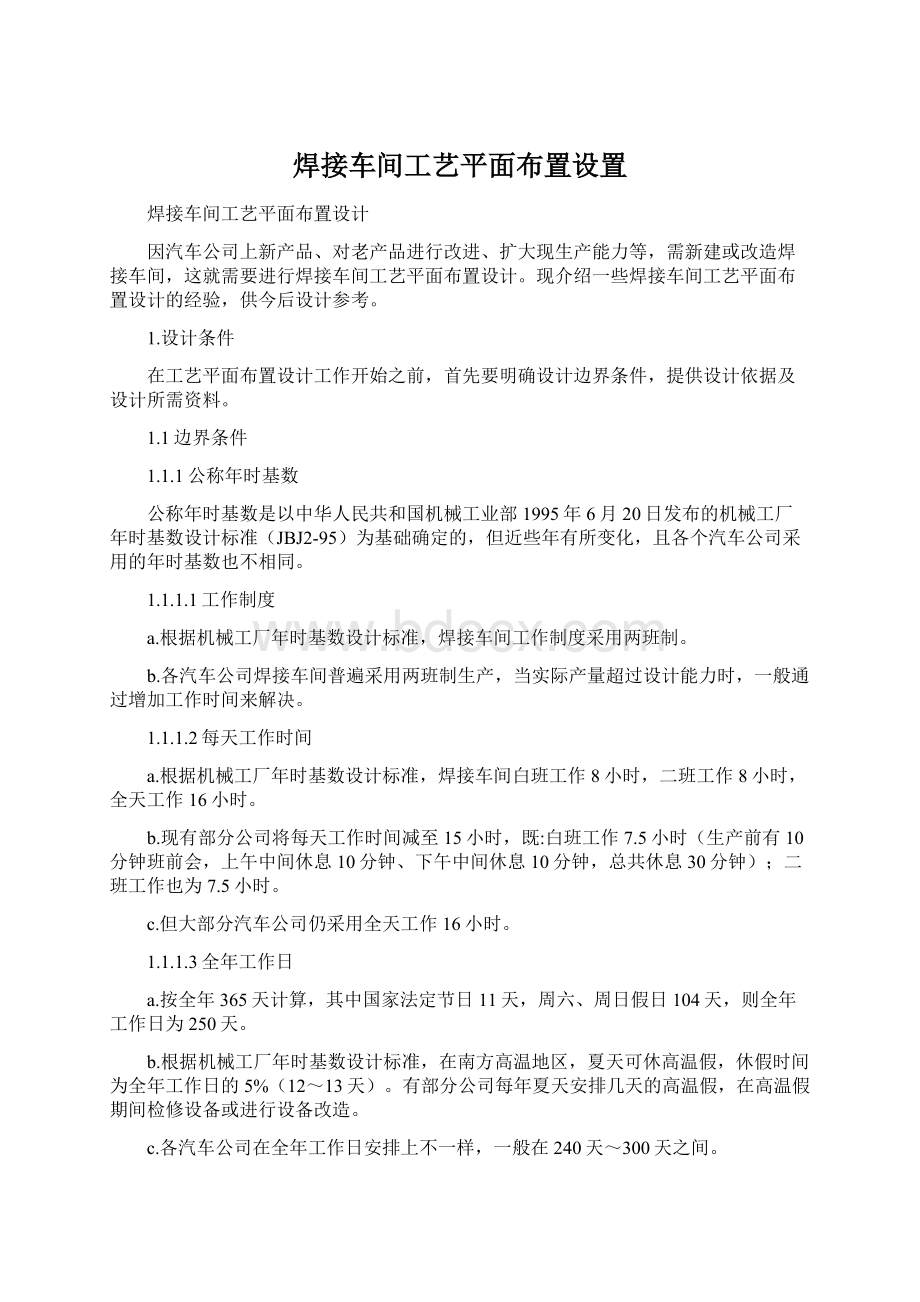
焊接车间工艺平面布置设置
焊接车间工艺平面布置设计
因汽车公司上新产品、对老产品进行改进、扩大现生产能力等,需新建或改造焊接车间,这就需要进行焊接车间工艺平面布置设计。
现介绍一些焊接车间工艺平面布置设计的经验,供今后设计参考。
1.设计条件
在工艺平面布置设计工作开始之前,首先要明确设计边界条件,提供设计依据及设计所需资料。
1.1边界条件
1.1.1公称年时基数
公称年时基数是以中华人民共和国机械工业部1995年6月20日发布的机械工厂年时基数设计标准(JBJ2-95)为基础确定的,但近些年有所变化,且各个汽车公司采用的年时基数也不相同。
1.1.1.1工作制度
a.根据机械工厂年时基数设计标准,焊接车间工作制度采用两班制。
b.各汽车公司焊接车间普遍采用两班制生产,当实际产量超过设计能力时,一般通过增加工作时间来解决。
1.1.1.2每天工作时间
a.根据机械工厂年时基数设计标准,焊接车间白班工作8小时,二班工作8小时,全天工作16小时。
b.现有部分公司将每天工作时间减至15小时,既:
白班工作7.5小时(生产前有10分钟班前会,上午中间休息10分钟、下午中间休息10分钟,总共休息30分钟);二班工作也为7.5小时。
c.但大部分汽车公司仍采用全天工作16小时。
1.1.1.3全年工作日
a.按全年365天计算,其中国家法定节日11天,周六、周日假日104天,则全年工作日为250天。
b.根据机械工厂年时基数设计标准,在南方高温地区,夏天可休高温假,休假时间为全年工作日的5%(12~13天)。
有部分公司每年夏天安排几天的高温假,在高温假期间检修设备或进行设备改造。
c.各汽车公司在全年工作日安排上不一样,一般在240天~300天之间。
1.1.1.4公称年时基数
a.在规定的工作制度下,工人和设备在一年内工作的小时数,称为公称年时基数。
b.由于工作制度、每天工作时间及全年工作日不同,公称年时基数也不同。
c.举例:
若按每天工作16小时,全年工作250天计算:
设备公称年时基数=全年工作日×每天工作时间
=250天×16小时
=4000小时
工人公称年时基数=全年工作日×每天工作时间
=250天×8小时
=2000小时
1.1.2设计年时基数
1.1.2.1设备设计年时基数
a.从设备公称年时基数中扣去公称年时基数损失,设备在一年内工作的小时数,称为设备设计年时基数。
b.设备开动率=设备设计年时基数/设备公称年时基数。
设备开动率(有的公司称为综合开动率)一般为80%~90%。
数值小的常用于焊装线等复杂设备,数值大的常用于分装阵地的简单设备。
c.举例:
若焊装线综合开动率按85%计算:
设备设计年时基数=4000小时×85%=3400小时。
1.1.2.2工人设计年时基数
a.从工人公称年时基数中扣去公称年时基数损失,工人在一年内工作的小时数,称为工人设计年时基数。
b.公称年时基数损失包括职工年休假、探亲假、婚假、丧假、产假、病事假等。
根据机械工厂年时基数设计标准,工人公称年时基数损失在10~15%。
c.举例:
若工人公称年时基数损失取11%时:
工人设计年时基数=2000小时×(1-11%)=1780小时。
1.2设计依据
1.2.1车型种类和生产规模
a.若为一次开发的车型,应提供全系列车型的种类(宽、窄、长、短、高、矮)和生产规模。
b.若为分期开发的车型,需提供后续开发车型的种类和生产规模。
c.若为老车间改造,需提供原有车型的种类和生产规模。
d.若为老车间改造,并保留部分车型,需提供保留车型的种类和生产规模。
1.2.2投产时间
a.明确新车型的投产时间,提供新车型的主日程计划。
b.在新车型的主日程计划中明确了产品研发、工艺设计、新车间建设、设备工装准备、现场安装调试、车身产品PT1、PT2及SOP等阶段的进度。
c.一个全新车型的生产准备周期一般要2年左右,一个成熟车型的生产准备周期一般1年左右。
生产准备周期与产品种类、生产规模、投资额度及技术水平等有很大关系。
1.2.3加工程度
a.根据焊接车间可利用生产面积,可利用面积经济性,工艺布置与物流合理性,产品收益性等来决定车身零合件的自制程度。
b.有一定规模的汽车公司,配套环境比较好的地区,车身产品的自制程度相对较低。
降低自制程度可以有效的降低生产面积与工艺投资。
c.车身的主要总成、主要的结构件,主要的外表面件一般为自制件,这样可以有效的控制产品质量。
1.3产品设计资料
a.在规划设计阶段要提供产品构想书,产品的详细结构、主要设计尺寸及零件材料、表面状态、料厚等资料。
此项工作多半由汽车公司自己完成。
b.在产品开发期间需组织制造部门的技术人员对产品的工艺性进行评审,并在此基础上对产品进行工艺性优化。
有些汽车公司将这部分工作交给制造商完成。
c.在工艺设计阶段要提供全系列车型车身产品数模、产品数据树及通用件明细表等。
d.在产品数模冻结前应将工艺定位孔标注在产品图中,工艺定位孔的位置与尺寸应得到制造部门的认可。
工艺定位孔对夹具设计与产品质量影响很大,我们要特别关注,并帮助汽车公司进行优化。
1.4工艺设计资料
a.若为新建车间,需提供厂房土建资料,提供电气、压缩空气、循环水接口资料及其它相关技术资料。
b.若为老车间改造,需提供原有车型工艺设计资料与工厂设计资料,提供保留的设备、工装等实物资料。
c.若为老车间改造,并保留部分原有车型,需提供原有车型种类和生产规模,提供原有车型工艺设计资料与工厂设计资料,提供保留实物的资料。
1.5明确质量目标
产量、质量、成本都是重要的设计目标,但与我们关系较大的是质量目标。
随着产品质量目标的提高,产品设计水平、工艺设计水平、夹具设计水平也需相应提高,工艺投资也会相应增加。
我们应对汽车车身产品的质量目标有一定的了解。
1.5.1外观质量
a.外观质量对油漆后的质量影响较大,同时它又容易受油漆和喷涂方法的影响,因此,决定外观质量要考虑其与喷涂方法的关系。
随着金属漆比例的增加,对白车身外观质量的要求会越来越高
b.白车身外观质量检查一般分为A、B、C三个区域。
左/右侧围、前顶盖、左/右车门、前围上盖板为A区,A区外观质量要求最高;后顶盖、侧围后部为B区,B区外观质量要求较高;中顶盖、后围为C区,C区外观质量要求较低。
1.5.2装配质量
a.装配质量是单个零件精度的集和,跟产品装配工艺性、冲压与焊接工艺保障能力、零合件精度、焊接夹具精度、驾驶室装配精度都有密切关系。
b.装配质量判定的主要项目有:
白车身骨骼精度、车门间隙与面差合格率、面罩间隙与面差合格率、CS-VES评价等。
c.在设计前要提出驾驶室的产品技术条件和驾驶室骨骼精度目标值,轿车及高端卡车车身的骨骼精度可达85%以上,微型车车身的骨骼精度要求较低,在70%左右即可满足使用要求。
1.5.3焊接质量
a.焊接质量跟产品的焊接工艺性、冲压件质量、焊接方法、夹具保障能力、焊接设备等都有密切关系。
b.焊接质量判定的主要项目是焊点合格率。
c.当对焊点焊接、表面质量及焊点间距要求较高时,考虑采用机器人焊接,或在夹具上增加一些必要的保障措施。
d.在设计前要明确焊接质量要求,见相关的焊接标准。
1.6明确质量保证措施
a.做好模具、夹具、检具定位基准统一,提高零件、总成及车身制造精度。
b.选用成熟、可靠、并具有一定先进水平的工艺与设备。
c.进一步完善零件、总成、白车身及工装检测手段、检测工具及检测阵地。
d.物流设备、工位器具配备齐全,保证零合件的储运质量。
e.在劳动强度大,产品质量要求高的工位采用机器人焊接。
f.点焊机配备质量好的恒流控制箱,确保焊接质量。
g.随着镀层钢板、高强度板等新材料应用,随着节能、环保水平提升,中频直流焊接、激光焊接、点焊机群控技术等将得到推广应用。
2.产品装焊工艺性优化
汽车车身有良好的装焊工艺性,是做好汽车车身装焊工艺设计工作的基础,它直接影响到车身的工艺设计质量、产品制造质量及产品收益性等,
因此,需认真作好要装焊工艺性审查与优化工作。
主要审查内容如下:
2.1产品设计优化
a.产品系列化设计
宽型、窄型、长型、短型、高顶、矮顶等所有品种的驾驶室全部设计完成后再投入生产准备,会大大降低工艺设计难度,提高生产准备质量,缩短生产准备时间,提高产品收益性。
b.产品通用化设计
提高同系列宽、窄、长、短、高、矮驾驶室的通用化设计水平,提高新、老驾驶室之间的零件及分总成通用性,尤其是地板定位基准的一致性,尽量减少专用零件与专用总成数量,降低焊装线设计(或改造)难度,可以有效的减少设备与夹具投资,提高产品收益性。
c.产品标准化设计
提高产品的标准化设计水平,有利于提高工艺设计与工装设计水平,有利于提高产品制造质量。
d.产品合理分块
对产品进行合理分块,可以最大限度的减少焊装线装配总成的数量,降低装配难度,减少线上焊接工作量,方便工人操作,提高产品质量,降低工艺投资。
2.2装配工艺性优化
装配工艺性审查包括装配方法、产品结构、装配方向及装配顺序等。
a.装配方法
根据生产纲领与产品结构合理确定装配方法,如:
夹具定位装配、样板定位装配、工件自定位装配等。
根据确定的装配方法,提出产品优化意见。
b.装配方便性产品结构要便于零件与总成的装配及定位,便于总成与驾驶室的吊挂及运输,在装配时不允许出现负角。
c.装配方向
主要总成要沿X、Y、Z方向垂直装配,有利于夹具定位;其余总成与零件也要尽量避免斜角度装配,以利于简化夹具,方便操作。
d.装件顺序
装件顺序要综合考虑零合件装配的方便性,工件定位的合理性,焊钳操作的接近性,装焊工作量的均衡性及生产节拍等
2.3焊接工艺性优化
焊接工艺性审查包括焊接方法、焊点接近性、焊点接头形式及焊件厚度等。
a.焊接方法
根据生产纲领与产品结构合理确定焊接方法,如:
机器人焊接、自动焊机焊接、悬挂点焊机焊接、固定点焊机焊接、二氧化碳焊机焊接等。
根据确定的焊接方法,提出产品优化意见。
b.焊点接近性
根据确定的焊接方法对焊点接近性进行审查。
采用机器人焊接时,可以选择尺寸大一些的焊钳;采用悬挂点焊机焊接时,需选择尺寸小一些的焊钳;采用固定点焊机焊接时,上下电极的负角不能太大。
c.焊点接头形式
常用的焊点接头形式有搭接接头和翻边接头两种形式。
搭接接头产品造型好看,焊点处贴合较好,但焊钳接近性差。
翻边接头产品造型不好看,焊点处贴合较差,但焊钳接近性好。
为了满足产品造型要求,产品外表件越来越多的采用搭接接头取代翻边接头。
d.焊件厚度
单层焊件厚度不宜超过2.5mm,两层焊件总厚度不宜超过5mm,三层焊件总厚度不宜超过4.5mm,避免四层料焊接。
当焊件较厚,且层数较多时,可以采用内部加强板开孔的方式,减少焊件总厚度。
2.4定位合理性
零合件的合理定位,可以有效的提高零件与总成制造精度。
a.定位方式
常用的定位方式有孔定位、形状定位、凸点定位、凸台定位、螺栓定位等。
要根据生产纲领、产品结构、精度要求等进行合理选择。
b.定位孔
根据工件的尺寸与姿态,根据夹具重复定位夹紧的次数与夹紧方式合理选择定位孔的位置与尺寸。
定位孔尺寸的确定要有利于保证装配尺寸,便于焊钳操作。
c.定位面
根据工件的尺寸、重量、姿态,根据夹具重复定位夹紧的次数,夹紧方式及重要度合理选择定位面的位置、形状与尺寸。
尽量消除零合件与夹具偏差对总成精度的影响。
d.定位基准统一
首先根据车身焊接需要提出总成工艺定位孔与工艺定位面的位置与尺寸,再经冲压、总装(或内饰)专业进行确认,最后标注在产品数模上。
这样可以有效的统一模具、零件检具、分装夹具、线上夹具、总成检具的定位基准,还可以统一自制零合件与外制零合件基准。
3.工艺设计
新车型工艺设计,新焊装线建设,是提高产品质量和工艺水平的良好机会,此时应充分利用国内外先进技术与设备,协调好产品质量、生产能力和制造成本的关系,生产高质量、低成本的产品。
良好的工艺设计是平面布置设计的基础,它影响到焊接车间平面布置设计、投资额度及项目实施效果。
3.1确定生产方式
车身产量、品种与工艺特点不同,生产方式也不同,在车身焊接生产中常用的生产方式有小批量生产、中批量生产、大批量生产、混流生产及柔性化生产等。
3.1.1小批量生产
a.当车身年产量小于3000台时,采用小批量生产方式。
b.这种生产方式装焊工艺水平很低,仅用于少量特殊车型。
3.1.2中批量生产
a.当车身年产量在3000台~30000台时,采用中批量生产方式。
b.此种生产方式装焊工艺水平较低,在卡车领域应用较多。
c.地板总成与车身总成一般采用多工位生产,采用电动葫芦、梁式天车、人工推送小车、人工推送滑撬或人工推送放置在托盘上的车身等非机械化方式完成总成输送。
d.前围总成、后围总成、左/右侧围总成及顶盖总成等一般采用1~2个工位生产,采用电动葫芦、助力装置及人工来完成总成的输送。
e.总成的装配与焊接主要采用人工,劳动强度大,生产率低。
3.1.3大批量生产
a.当车身年产量为30000~150000台时,采用大批量生产方式。
b.此种生产方式装焊工艺水平一般,应用较广。
c.地板总成、车身总成等一般采用机械化传送线,焊后总成采用自行葫芦输送。
左/右侧围总成及顶盖总成等主要分总成多采用自动上线装置装配,大部分焊点均采用机器人焊接。
d.主要分总成为多工位生产。
产量较低时采用简单的传送方式,以人工焊接为主;产量较高时采用机械化传送方式,采用少量机器人焊接。
e.实力很强的汽车公司、产量很高的焊装线,则大量采用机器人焊接。
3.1.4混流生产
a.混流生产是指在一条焊装线上可以容纳同一系列多种车型同时生产的能力。
可以混流生产宽、窄、长、短、高、矮等所有车型,也可生产其中部
分车型。
b.此种生产方式装焊工艺水平较高,在汽车车身的各个领域得到了广泛应用。
c.车型的变化主要通过夹具、吊具或传送机构上的运动部件来实现,常用的运动部件有平移机构、翻转机构、升降机构等。
d.地板总成、车身总成等都采用机械化传送线,在卡车车身焊接生产中以往复杆传送方式为主,在轿车车身焊接生产中以滑撬(或台车)传送方式为主。
e.地板总成、车身总成的焊点普遍采用机器人焊接。
公司实力很强、焊装线产量很高时,大量采用机器人焊接;公司实力较弱、焊装线产量较低时,只采用少量机器人焊接;公司实力很弱、仍采用人工焊接。
3.1.5柔性化生产
a.柔性化生产是指在一条焊装线上可以容纳不同系列多种车型同时生产的能力。
可以混流生产不同系列的不同车型。
b.此种生产方式装焊工艺水平最高,在国外汽车公司车身焊装线上已大量应用,在国内只有少量高水平的轿车车身装焊线上得已应用,
c.实现车身柔性化生产的关键是实现总装线总装工位的柔性化装焊,而柔性夹具与机器人的应用则是实现车身柔性化生产的基础。
d.总装工位可通过机器人抓取不同车型的夹具实现多种车型任意切换,也可通过在一套夹具上切换不同的定位模块来切换车型,而这些动作要通过机器人来实现。
e.柔性化生产可使新开发的车型在原有焊装线上混流生产,从而减少工艺投资,缩短生产准备时间,提高产品收益性。
3.2确定点焊方式
因产品结构、生产纲领、生产品种及投资额度不同,采用的点焊方式也不同,在汽车车身焊接生产中常用的点焊方式有固定点焊、悬挂点焊、多点焊、机器人点焊等。
3.2.1固定点焊
在通用固定点焊机上,采用不同的机臂和焊接辅具,可以进行多种中小零合件的焊接。
采用固定点焊机焊接占地面积小,工艺投资少,生产组织灵活,是首选焊接方式。
a.对装配尺寸要求较高的小总成采用样板定位,要求定位样板定位准确、装件方便、轻便灵活。
b.对装配尺寸要求不高的小总成可考虑采用凸点定位、缺口定位,凸焊螺栓定位等,凸点、缺口及凸焊螺栓孔的尺寸根据设计标准确定。
c.采用专用辅具,可以在固定点焊机上焊接凸焊螺母、凸焊螺栓等焊接标准件。
d.对体积较大的总成可考虑采用简易的助力装置降低劳动强度,如:
布置在空中的弹性吊挂装置,布置在固定点焊机上的弹性支撑装置及布置在工位边的辅助支撑装置等。
3.2.2悬挂点焊
采用不同形式的焊钳,对较大的合件或总成进行焊接。
采用悬挂点焊机焊接占地面积较大,工艺投资较多,生产组织不灵活,但目前仍是最主要的焊接方式。
a.对体积较大、装配尺寸要求较高的总成采用夹具定位焊接,要求夹具定位准确、工件装卸方便、焊钳操作灵活。
b.对体积较小、但装配尺寸要求较高,又难以用固定点焊机焊接的总成,也可考虑采用夹具定位焊接。
c.焊钳的合理选择、焊钳的接近性、焊钳的操作灵活性等非常重要,对焊接质量与生产效率会产生很大的影响。
d.悬挂点焊机分成分体式焊机与一体式焊机两种;而分体式焊机点焊控制箱又分成安装在变压器上与不安装在变压器上两种;而不安装在变压器上的控制箱又分成安装在空中钢平台上与安装在地面钢立柱旁两种。
e.悬挂点焊机目前仍以工频焊机为主,在特殊场合采用了体积小、重量轻、操作灵活的中频直流一体式悬挂点焊机。
3.2.3多点焊
多点焊机可以分组依次焊接数个、数十个、甚至更多的焊点,曾是电阻点焊实现机械化、自动化的重要方法之一。
由于工艺投资大,设备故障率高,产品柔性差等缺点,多点焊接已基本上被点焊机器人所取代。
a.现在多点焊机一般用于总装线总装工位的定位点焊,点焊左/右侧围总成与地板总成连接处。
有些公司还用于点焊左/右侧围总成与前围总成、后围总成及顶盖总成连接处。
b.现多点焊机焊接变压器仍以工频交流为主,少量有实力的公司已改用中频直流,改用中频直流焊接后可以减少变压器数量,提高焊点质量。
c.一些产量较小的焊装线,采用了傀儡焊钳,通过电缆线与导电板引致夹具外侧,采用普通悬挂点焊机焊接。
采用傀儡焊钳可以降低设备投资。
3.2.4机器人点焊
机器人的应用主要根据生产纲领、生产品种、柔性化要求、产品焊接工艺性等多种因素来综合考虑,是实现车身焊接自动化、柔性化生产的主要设备。
a.车身生产纲领越高,生产品种越多,柔性化需求越强,采用机器人焊接
的必要性就越大。
b.一般焊钳尺寸越大、人工装配与点焊越困难,采用机器人装配与点焊的必要性就越大。
c.一般对焊接质量要求越高,尤其是外表面件焊点,采用机器人焊接的必要性就越大。
3.3确定焊装线传送方式
由于生产纲领、生产品种、生产方式不同,焊装线传送方式也不同,常用的焊装线传送方式有机械化传送与非机械化传送两种。
车身年产量超过3万辆,焊装线一般采用机械化传送方式;车身年产量小于3万辆,焊装线一般采用非机械化传送方式。
机械化传送又分为往复杆传送、台车传送及滑撬传送等。
3.3.1往复杆传送
3.3.1.1传送方式
a.往复杆行走轨迹为上升、传送、下降、返回,每个动作都能实现慢-快-慢,停位准确。
往复杆输送线单个循环时间为20秒左右,往复送件的重复到位精度为±1毫米,往复杆输送升降行程一般不超过1000mm。
b.工件的水平输送是通过调频电机驱动齿轮齿条做往复运行实现的,有的调频电机安装在往复杆上,有的调频电机安装在焊装线旁的地面上。
c.往复杆的升降有气动、液压及电动驱动方式。
现在已很少采用液压驱动方式,气动驱动方式应用的也不多,电动驱动方式应用的最多,常用的电动驱动方式有摆臂式与齿轮齿条式两种。
d.摆臂驱动方式采用调频电机、双速电机或伺服电机带动曲柄旋转1800,从而实现输送线本体的顶升与落下,一般采用液氮平衡缸平衡输送线本体与工件的重量。
这种形式的焊装线结构简单,常用于升降行程较大的车身产品,如:
东风天龙、天锦车身焊装线。
e.齿轮齿条驱动方式采用调频电机带动贯通全线的齿条实现往复运动,通过齿轮带动各个工位夹具齿条实现输送线本体的顶升与落下,采用气动平衡缸平衡输送线本体与工件的重量。
这种形式的焊装线结构较复杂,常用于升降行程较小的车身产品,如:
奇瑞L11轻卡车身焊装线。
3.3.1.2国外应用情况
a.往复杆传送方式曾是汽车车身焊装线的主要传送方式之一,上个世纪八、九十年代曾在国外得到广泛应用。
b.此种传送方式柔性较差,不利于焊装线的换型改造,也无法实现焊装线的柔性化生产。
c.国外新建的车身焊装线,已很少采用此种传送方式。
3.3.1.3国内应用情况
a.往复杆传送方式仍是国内车身焊装线的主要传送方式之一,在国内仍在大量使用。
b.此种传送方式虽然存在柔性较差等问题,但因为往复杆传送方式运行平稳,可靠性高,维修方便,造价较低,仍是国内卡车车身焊装线的主要传送方式。
如:
一汽J6车身焊装线,重汽A7车身焊装线、柳汽M5车身焊装线等。
c.轿车车身焊装线已基本不再采用往复杆传送方式。
3.3.2轻便轨道+随行夹具式台车传送
3.3.2.1传送方式
a.采用随行夹具式台车具有独立的定位夹紧系统;有足够的强度和刚度,不易变形;通过轻便轨道输送,运行噪音低,稳定、可靠、移动精度高;可直接利用台车上的动力定位夹紧机构对车身进行定位夹紧。
b.定位装置可以实现自动转换,转换精度容易控制,适合多品种生产,柔性化强。
c.由于单车及系统的柔性化设计要求和制造成本都很高,在主要焊接工位上对台车的定位也有较高的要求,因此,在选择这种输送方式时首先要考虑生产批量和制造成本。
3.3.2.2国外应用情况
a.随行夹具式台车传送方式在上世纪九十年代与本世纪初,曾是轿车车身焊装线的最主要传送方式,常用在大批量生产的轿车焊装线上。
b.部分轿车车身焊装线采用双层传送方式,上层为台车传送的机器人自动焊接生产线,下层为空台车返回线,地面没有设备基础坑,如;德国奔驰汽车公司的轿车车身焊装线。
c.部分轿车焊装线采用单层传送方式,如:
韩国起亚汽车公司的轿车车身焊装线。
3.3.2.3国内应用情况
a.国内部分轿车生产企业的车身焊装线已与国外处在同一水平,焊装线的主要装备都由国外供应商直接提供,部分轿车车身焊装线采用了这种输送方式。
b.目前尚没有收到国内卡车车身焊装线采用台车传送方式的信息。
3.3.3动力滚床+滑撬传送
3.3.3.1传送方式
a.动力滚床采用皮带输送、变频调速同样可以获得较低的噪音。
滑撬本
身带有精确的定位机构,但不具备动力夹紧装置。
b.可以进行车身的一般性补焊工作。
在设计上也可以实现多车型滑撬的共享。
可通过设置90°~180°旋转机构进行分支,容易实现柔性化改造和产能提升改造。
c.采用动力滚床+滑撬式的输送方式制造成本相对较低,而且检测维护方便。
由于车身滑撬具有造价低、体积小、重量轻,便于维修、传送效率较高等特点,所以应用比较广泛。
d.滑撬也可作为线下运输的车身支具,用于车身的离线检查转运及车身存储等其它场合。
3.3.3.2国外应用情况
a.动力滚床+滑撬式传送方式是现在车身焊装线的主要传送方式之一,常用在大批量生产的轿车焊装线上。
b.采用滑撬传送方式,焊装线工位间距可变,可以根据工艺需要确定工位间的距离。
c.滑撬还可以实现地板线、总装线、调整线、白车身储存及运输通用,空滑撬空中返回至地板线一工位。
日本的许多汽车厂就采用了此种传送方式。
d.有的汽车公司滑撬实现了地板线、总装线、调整线及油漆车间前处理共用,法国雷诺卡车车身焊装线就采用了此种传送方式。
3.3.3.3国内应用情况
a.此类输送线在国内轿车生产中得到了大量应用,如:
襄樊天籁轿车车身焊装线。
b.在微型车生产中也有应用。
c.国内有的汽车公司也在着手考虑卡车车身焊装线采用动力滚床+滑撬式输送方式。
3.3.4非机械化传送
驾驶室年产量在3万辆以下,总装线一般都采用非机械化传送方式,常采用的非机械化传送方式有以下几种。
3.3.4.1人工推送台车方式
a.地板总成与车身总成采用台车输送,台车的升降通过装配工位的4个气缸完成,台车的前进