无损检测方案Final中文版.docx
《无损检测方案Final中文版.docx》由会员分享,可在线阅读,更多相关《无损检测方案Final中文版.docx(40页珍藏版)》请在冰豆网上搜索。
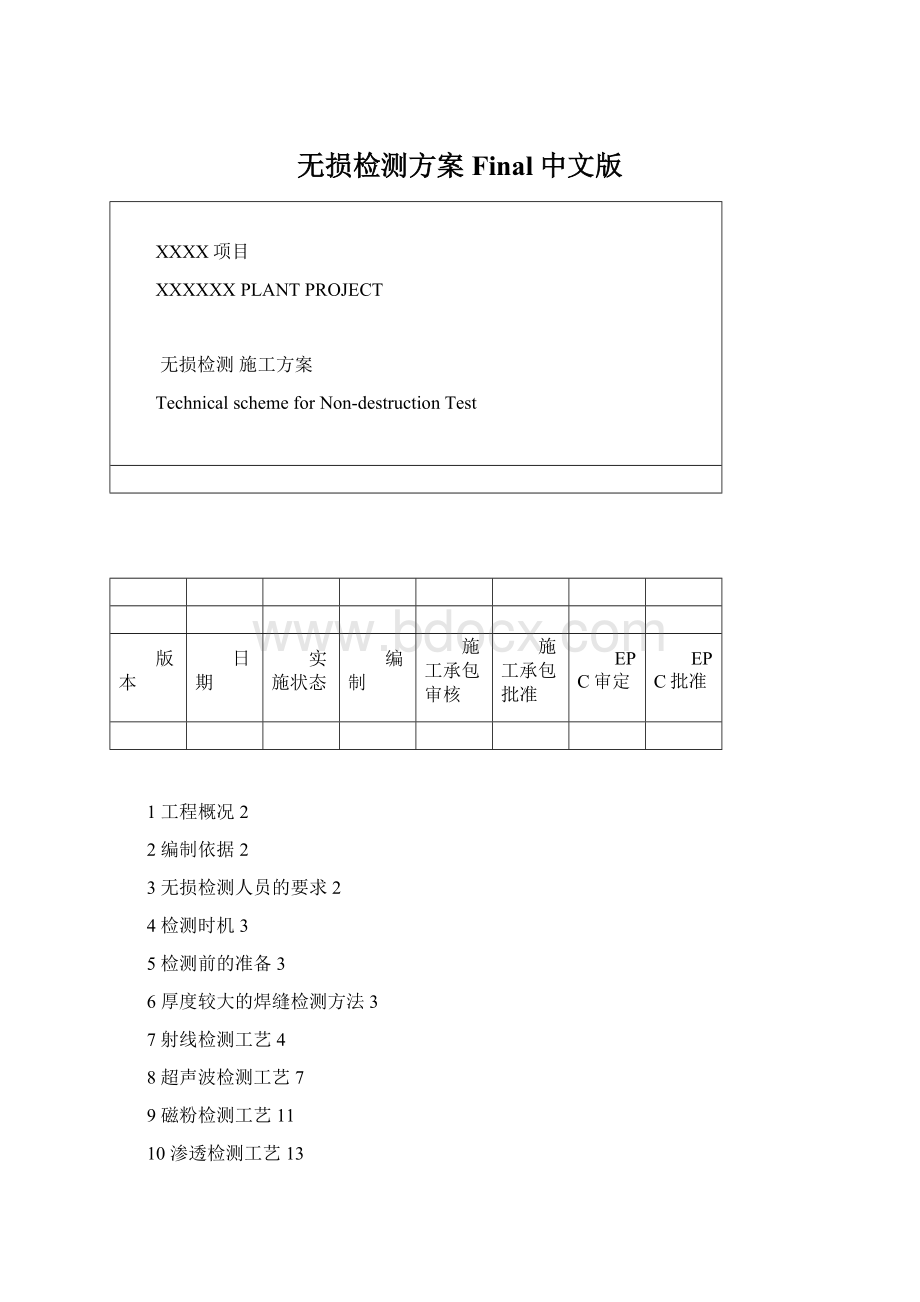
无损检测方案Final中文版
XXXX项目
XXXXXXPLANTPROJECT
无损检测施工方案
TechnicalschemeforNon-destructionTest
版本
日期
实施状态
编制
施工承包审核
施工承包批准
EPC审定
EPC批准
1工程概况2
2编制依据2
3无损检测人员的要求2
4检测时机3
5检测前的准备3
6厚度较大的焊缝检测方法3
7射线检测工艺4
8超声波检测工艺7
9磁粉检测工艺11
10渗透检测工艺13
11硬度检验工艺规程16
12光谱分析检验工艺规程17
13质量控制措施19
14HSE因素识别和评价及HSE措施26
15文明施工31
1工程概况
1.1工程简介
xxxx项目是以煤资源作为原料,新建一套氮肥联合装置,其生产规模为32万吨/年合成氨和56万吨/年尿素。
主要生产装置包括:
煤气化装置,能力为1,350吨/天;CO变换和硫回收装置、低温甲醇洗和液氮洗装置、氨合成装置,能力为1000吨/天;尿素装置,能力为1760吨/天等。
主要的公用工程包括:
空分,能力为35,000NM3/H;循环流化床锅炉及电站,能力为36MW;循环冷却水,能力为50,000M3/H;脱盐水,能力为210M3/H等。
同时还包括行政楼、成品库等一些辅助设施。
1.2工程特点
●项目雨季多,每年6月下旬至9月共约有3个多月的雨季;尤其晚上下雨时候较多,而无损检测工作主要是在夜晚工作,这给检测工作带来很大的难度和不便。
采取雨季施工措施费用较多,且安全风险加大。
●设备材料运输不便,办理相关跨国运输通(报)关手续,路途运输等方面时间较长。
●现场制造安装的装置众多,高空探伤作业量大。
2编制依据
●XX项目承包合同或协议。
●图纸设计要求。
●相关标准、规程、规范等。
●JB/T4730.1-4730.6-2005承压设备无损检测。
●GB11345-89钢焊缝手工超声波探伤方法和探伤结果分级。
●越南标准6153:
1996:
受压容器–设计,构造,制造安全技术的要求。
3无损检测人员的要求
3.1检测人员必须是经培训并由国家质量监督检验检疫总局颁发的Ⅰ、Ⅱ、Ⅲ级检验资格证,才能从事与所持资格证级别相应的无损检测工作。
取得Ⅱ级以上证书的人员方可填写和签发检验报告。
RT-Ⅱ、UT-Ⅱ、MT-Ⅱ、PT-Ⅱ级证以上(含Ⅱ级)均需两人以上持有。
3.2检测人员的矫正视力不得低于1.0,应按规定体检合格后才能上岗。
从事磁探、渗透检测工作的人员,不得有色盲、色弱。
3.3每个施工项目至少有两个II级或以上持证人员,负责初评、复评(审核)工作,带头并指导按规范要求进行检测工作。
4检测时机
射线检测应在质检员外观检查合格,表面达到检测要求,委托书下达后,按委托书要求的时间进行。
对于有延迟裂纹倾向的材料,检测必须在焊完24小时进行;对具有热裂纹倾向的材料应在热处理完成后进行。
5检测前的准备
5.1检件表面的要求
对焊缝及热影响区表面质量(包括焊缝余高高度)应经外观检查合格,表面不规则状态在底片上的影像应不掩盖焊缝中的缺陷或与之相混淆,否则应做适当处理。
检测面应经外观检查合格,所有影响检测的锈蚀、飞溅和污物都应予以清除,其表面粗糙度应符合检测要求。
5.2对检测委托的要求
焊缝外观检验合格后,由项目委托方有关人员填发检测委托书或委托通知单,一式两份,一份交检测作业组,另一份作为原始资料存档。
检测委托书内容包括容器编号(或锅炉号、加热炉号、裂解炉号、贮罐号、管线号等)或其他工件编号、焊口序号、焊工号、材质、规格、焊接方法、检测标准、检测比例、合格级别等,这些内容应符合所执行的相应施工验收规范及标准的要求,不符合要求的应要求委托方重新编制委托。
6厚度较大的焊缝检测方法
因为γ源在使用中存在众多的安全隐患,以及对线性危害性缺陷检出率有一定的局限性,本项目不采用γ射线检测方法。
对厚度T≥20mm的管道焊缝的内部缺陷检查,应在焊缝根部焊接完成后,先进行X射线检测确认焊缝根部合格后再进行填充盖面焊接,填充盖面焊接焊完后再进行100%超声波检测(A型脉冲反射法PE或衍射时差法TOFD)或全部焊接完成后直接采用100%超声波检测(PE或TOFD);对厚度T≥40mm的容器焊缝焊接完成后应采用100%超声波检测(PE或TOFD)。
7射线检测工艺
7.1适用范围
适用于压力管道、锅炉、压力容器、贮罐等承压设备焊接工程,采用射线检测方法的无损检测。
其它特种设备或金属结构焊接工程也可参照执行。
母材厚度大于或等于2mm的碳素钢、低合金钢、不锈钢、铝及铝合金、钛及钛合金对接焊缝的射线检测。
7.2射线检测设备、器材的选择及有关要求
7.2.1射线设备的选择及要求
选用便携式X射线探伤机。
7.2.2胶片的选择
在满足灵敏度要求的前提下,一般选用柯达、Agfa、日本富士等。
胶片的固有灰雾度D0≤0.3。
7.2.3像质计及对比试块(沟槽试块)的选择
各种焊缝均可选择R10系列通用线型像质计,对小径管焊缝也可选择专用(等径金属丝)像质计;对采用单面焊双面成型的焊缝(如管道焊缝)还应加装对比试块,小径管焊缝应装小径管I型(IA或IB)专用对比试块,其他管焊缝应装Ⅱ型一般对比试块。
7.2.4评片室
评片应在专用评片室内进行。
评片室内的光线应暗淡,但不全暗,周围环境光线不得在底片表面产生反射。
7.2.5黑度计
黑度计的测量范围应达到4.5以上,使用经国家标准计量局鉴定合格的标准密度片。
7.3检测程序及有关技术要求
7.3.1透照方法的选择
7.3.1.1外径大于100mm的钢管对接焊缝一般采用双壁单投影分段透照,大管焊缝可考虑中心透照或偏心法透照。
7.3.1.2外径≤φ100㎜的钢管对接焊缝当T≤8㎜,且g(焊缝宽度)≤D0/4采用双壁双投影透照;同时当T/D0≤0.12时透照两张片,两次透照方向相互垂直;当T/D0>0.12时,透照三张片,每张片相隔。
上下焊缝的影像在底片上呈椭圆形显示,焊缝投影间距在1倍焊缝宽度左右。
7.3.1.3不满足上述条件或焊缝椭圆成像有困难时,可垂直透照重叠成像,垂直透照重叠成像应相隔60°或120°透照3次,并应适当提高管电压。
7.3.2管道焊缝分段透照数量的确定
双壁透照时的有关参数一般按合同中附件-5表执行。
注:
实际应用时透照次数(拍片数量)应尽可能满足相应检测标准规定的K值(透照厚度比)要求,(包括因某些法兰口小径管2次透照无法满足相应检测标准规定的K值或者现场实际情况达不到2次透照条件的法兰口小径管);若在实际应用中出现合同中未列出管径规格时,应按照相关标准中的规定确定相应的拍片数和其他参数。
7.3.3像质指数
应按射线照相质量等级、透照方式、像质计放置方式、透照厚度W的不同选择像质指数。
7.3.4像质计选择、放置及有关要求
7.3.4.1塔器、容器焊缝及管径大于100㎜的对接焊缝,像质计采用JB/T4730.2-2005标准中规定的像质计,一般放在射线源侧的工件表面上被检焊缝区的1/4处,金属丝应横跨焊缝并与焊缝方向垂直,细丝置于外侧。
当管径小于等于100㎜时,可采用专用像质计或通用型像质计。
7.3.4.2管道焊缝还必须放置ⅠA或ⅠB型对比试块(管径小于等于100㎜时)或Ⅱ型对比试块(管径大于100㎜时)。
7.3.4.3多个小管焊缝透照在一张底片上时,可以只使用一个像质计,应放在最外侧的管子上。
7.3.5对比试块
为检测焊缝未焊透、内咬边或内凹的深度,管焊缝透照时采用I型或Ⅱ型对比试块,平行放置在距焊缝5mm处。
7.3.6透照厚度比
焊缝的透照厚度比即射线束斜向透照最大厚度与母材厚度的比值。
K=T,/T式中:
T——母材厚度,mm
T,——射线束斜向透照最大厚度,mm
AB级:
100mm<D0≤400mm环缝的透照厚度比K值不大于1.1,D0>400mm环缝的透照厚度比K值不大于1.2,纵缝的透照厚度比K值不大于1.03。
7.3.7射线检测标识
7.3.7.1对外径φ>100mm的焊口,采用双壁单投影透照,至少拍4张(具体片数,按有关标准要求确定),原则上使用字码带,可用0、1、2、3、4、5……按有效透照长度,分别按顺序帖在原带上,拍6张片时片位号分别用0-1、1-2、2-3、3-4、4-5、5-0表示,其它拍片数依此类推。
使用字码带可免放搭接标记,直接用数字表示,如0-1片中的0、1分别表示左、右搭接标记。
7.3.7.2对外径φ≤100mm的焊口,采用双壁双投影透照时,至少为两张底片,两次间隔90°,底片号为A、B,每张片放置中心标记并离焊缝边缘至少5mm。
7.3.8现场检测记录
现场检测人员必须用公司规定的记录表格做好射线检测原始记录,要求填写内容完整、规范、准确,并签名。
7.4暗室处理
胶片的暗室处理按公司暗室处理作业指导书执行。
7.5底片评定
7.5.1底片评定范围的黑度应为:
A级:
D=1.5~4.0,
AB级:
D=2.0~4.0,小径管φ≤100mm:
D=1.5~4.0。
7.5.2灵敏度合乎要求,能在底片均匀部位(邻近焊缝的母材金属区)观察到相应的像质指数。
7.5.3各种字码标记齐全。
7.5.4在评定表中圆形缺陷定量应标注为φxx×xx(个数),并写上总点数。
如φ2×1,φ1×3,共计5点。
条状缺陷标注:
长度L×条数,条状缺陷组还应标注总长度ΣL。
并在评定纸上标注缺陷的大概位置。
7.5.5级别的评定按执行的相应标准进行。
7.6返修与扩探
7.6.1当发现超标缺陷且委托方有返修要求时,由复评人员填写“焊缝超标缺陷通知单”,通知单一式两份,一份留底作为存档资料,一份交委托方。
7.6.2对返修部位进行射线检测时,应加“R”标记,一次返修时加“R1”,二次返修时加“R2”…
7.6.3局部射线检测的焊缝,如果出现超标缺陷,除对缺陷返修部位按原条件复检外,还应按有关规范的要求进行扩探,扩探部位应加“K1”、“K2”…的标记。
7.7检测报告及布片图
项目无损检测责任师组织编制检测报告和布片图,检测报告要填写齐全,书写工整规范,不得涂改,如一页报告中有空白,在空白第一栏标注“以下空白”字样;检测报告经项目无损检测责任师审核或RT无损检测专业检测责任工程师审核并签名后,由具备资格条件的被授权人员签发。
项目无损检测责任师审核的检测报告,同时还应将报告的电子版报RT无损检测专业检测责任工程师备案(复审)。
8超声波检测工艺
8.1超声检测设备、器材的选择及有关要求
8.1.1仪器选择
超声波探伤仪选用A型脉冲反射式超声波探伤仪(模拟式或数字式仪器),频率范围1~5MHz。
如汕头超声波检测仪CTS-23A、CTS-23B、CTS-26A、CTS-36、CTS-2000和武汉中科创新HS600C等,本项目采用数字式超声波探伤仪。
8.1.2探头选择
8.1.2.1晶片有效面积一般不应超过500mm2,且任意一边长不大于25mm。
8.1.2.2承压设备检测的探头选用可按相关标准的规定执行。
8.1.3试块的选择
8.1.3.1直探头用试块
钢板检测用试块:
采用CBI标准阶梯试块和CBIIΦ5平底孔标准试块(通常根据钢板厚度选用CBII-1或CBII-2)。
8.1.3.2斜探头用试块
a)焊缝检测用试块:
CSK-IA、CSK-ⅢA等。
b)管道环缝超声波检测试块:
GS-1、GS-2、GS-3、GS-4试块。
8.1.3.3当施工验收规范或设计文件另有规定时,也可以采用验收规范或设计文件要求的其他形式的标准试块和对比试块。
8.1.4耦合剂的选择
选用机油、浆糊、甘油和水等,透声性好且不损伤检测表面。
8.1.5制作距离—波幅曲线
根据检测标准的规定,制作距离—波幅曲线,数字式超声波探伤仪直接自动生成距离—波幅曲线。
8.1.6对检测的一般要求
8.1.6.1检测覆盖率
检测时,应尽量扫查到工件的整个被检区域,探头的每次扫查覆盖率应大于15%。
8.1.6.2探头的移动速度
探头的扫查速度不应超过150mm。
当采用自动报警装置扫查时,不受此限。
8.1.6.3扫查灵敏度
扫查灵敏度至少比基准灵敏度高6dB。
8.1.7检测记录
现场检测人员在检测过程中应使用公司规定的记录表格做好原始记录。
记录中的内容原则上不得涂改,若要更改仅能采用杠改方法并在每处改动处附近签上姓名和日期。
8.1.8检测报告
项目无损检测责任师组织编制检测报告和检测部位图,检测报告要填写齐全,书写工整规范,不得涂改;如一页报告中有空白,在空白第一栏标注“以下空白”字样;检测报告经项目无损检测责任师审核或无损检测专业责任工程师审核并签名后,由具备资格条件的被授权人员签发。
项目无损检测责任师审核的检测报告,还应将报告的电子版报无损检测专业责任工程师备案(复审)。
8.2超声波测厚
8.2.1适用范围
适用于用数字式超声波测厚仪或A型脉冲反射式超声波探伤仪对压力管道、锅炉、压力容器、储罐、钢结构、原材料及零部件材料等进行厚度测定。
8.2.2检测器材
8.2.2.1采用带延迟块的单晶直探头或双晶直探头。
8.2.2.2采用测厚仪自配带试块或与被测材料同材质标准试块。
8.2.3测厚操作
8.2.3.1测厚部位用细砂纸轻轻打磨,以除去氧化皮或油漆等,保证光洁。
8.2.3.2在测厚部位涂上少许耦合剂。
8.2.3.3将探头垂直于测厚表面并通过耦合剂与被测件紧密接触。
8.2.3.4从显示屏上读取所测厚度值。
8.2.3.5管壁测厚时,如使用单晶直探头,应使探头中心线与管轴中心线相垂直并通过管轴线;使用双晶直探头测厚时,探头分割线必须与管轴中心线垂直。
8.2.4记录与报告
8.2.4.1检测人员应详细记录测厚工件编号、测厚位置和所测数据。
8.2.4.2根据原始记录出具测厚报告,报告至少应包括工件名称、编号、材质、委托单位、编号、仪器型号、测厚部位和测定结果等。
8.3钢制承压设备焊缝(对接焊缝、管座角焊缝、T型焊缝)超声检测
8.3.1适用范围
适用于母材厚度为6~400mm全焊透熔化焊对接焊缝的超声检测。
不适用于铸钢焊缝和内径小于或等于200mm的管座角焊缝,也不适用于外径小于250mm或内外径之比小于80%的纵向焊缝检测。
8.3.2探头参数测试
8.3.2.1探头前沿距离
利用CSK-IA等试块的R100mm曲面测探头的前沿距离,测量三次取平均值。
8.3.2.2探头K值
利用CSK-IA或CSK-IIIA等试块测探头的K值,测量三次取平均值。
8.3.3距离—波幅曲线
本项目采用数字式超声波仪器,距离-波幅曲线自动生成。
8.3.4检测灵敏度
8.3.4.1斜探头扫查灵敏度不低于最大声程处的评定线灵敏度。
8.3.4.2检测横向缺陷时,应将灵敏度提高6dB。
8.3.4.3表面补偿
可根据检件粗糙度程度来定,一般补偿3~6dB。
8.3.4.4直探头扫查时,将无缺陷处第二次底波调节为荧光屏满刻度的100%,作为检测灵敏度。
8.3.5检测面
8.3.5.1当母材厚度小于或等于46mm时,一般采用单面双侧检测。
8.3.5.2当母材厚度大于46mm时,一般采用双面双侧检测或双面单侧两种K值探头检测。
8.3.5.3平板焊缝或大直径环向焊缝应进行横向缺陷检测。
8.3.6对接焊缝的检测方法
8.3.6.1对焊缝主要采用锯齿型扫查、平行和斜平行扫查。
8.3.6.2确定缺陷的位置、方向、和形状,区分真假缺陷信号主要采用的四种基本扫查方法:
前后、左右、转角和环绕。
8.3.6.3曲面工件焊缝的检测
a)尽量按平板对接焊缝的检测方法进行检测,对于受几何形状限制无法检测的部位应进行记录。
b)纵缝检测时,对比试块的曲率半径与检测面曲率半径之差应小于10%。
c)环缝检测时,对比试块的曲率半径应为检测面曲率半径的0.9~1.5倍。
d)测定缺陷位置与深度时,注意作适当修正。
8.3.7现场检测及记录
检测人员根据上述方法对被检件进行现场检测,现场检测人员在检测过程中应使用公司规定的记录表格做好原始记录。
8.3.8缺陷评定
按设计文件规定的相关标准进行评定。
8.3.9检测报告
根据原始记录编制检测报告。
9磁粉检测工艺
9.1检测仪器的选择及要求
焊缝检测时通常选用磁轭式检测仪或旋转磁场检测仪;若采用荧光磁粉检测时,还应配上黑光灯。
9.2磁粉的选择及磁悬液配制
9.2.1磁粉
按相关标准规定正确选用磁膏。
9.2.2磁悬液:
一般用水磁悬液,配制方法及浓度控制按磁膏生产厂家的推荐。
9.3灵敏度试片
选用A1型灵敏度试片,通常选用A1-30/100型试片。
9.4工艺参数
9.4.1磁化方法:
磁轭法,或交叉磁轭复合磁化法。
9.4.2磁化方向:
纵向磁化。
9.4.3磁化通电方式:
连续法
9.5系统灵敏度的校验
将A1-30/100试片贴在工件被检范围的一端,刻槽的一面朝向工件。
用与工件检测相同的磁化规范进行磁化,当试片人工刻槽磁痕清晰显示时,则认为系统灵敏度合格。
9.6工件的磁粉检测
9.6.1焊缝(及焊疤)的磁粉检测
使磁轭与工件接触良好。
同一部位至少磁化两次。
每一被检区进行两次独立的磁化检验,两次磁化检验的磁力线应大致相互垂直。
磁轭极间距应控制在75~200mm范围内,检测的有效区域为两极中心连线两侧各50mm的范围内,磁化区域每次应有15mm以上的重叠。
9.6.2施加磁悬液
用连续法进行检测,磁悬液必须在通电时间内施加完毕。
通电时间为1-3秒,间隔1秒。
在对工件磁化的同时,用喷壶对工件施加磁悬液。
停施磁悬液至少1秒后才能停止磁化。
9.6.3磁痕观察
在进行磁化的同时,对形成的磁痕进行观察,但磁化结束时应及时观察检测区内磁粉堆集情况。
观察时使用手电筒或手把灯照明,必要时使用3-5倍放大镜观察。
9.6.4检测记录
9.6.4.1发现磁痕后,应不少于2次反复磁化,但确认为相关显示后,用记号笔在工件上标出,用草图在检测记录上标注。
9.6.4.2现场检测人员在检测过程中应使用公司规定的记录表格做好原始记录。
记录中的内容不得涂改,若要更改仅能采用杠改方法并在每处改动处附近签上姓名和日期。
9.7缺陷评定
按设计文件规定的相关标准进行评定。
9.8检测报告
9.8.1检测结束后,应及时编制、签发检测报告。
报告内容应包括:
工程名称、工件名称、工件编号、焊缝编号、仪器型号、验收标准、缺陷情况、返修情况、检测结论等。
9.8.2检测报告
项目无损检测责任师组织编制检测报告和检测部位图,检测报告要填写齐全,书写工整规范,不得涂改;如一页报告中有空白,在空白第一栏标注“以下空白”字样;检测报告经项目无损检测责任师审核或无损检测专业责任工程师审核并签名后,由具备资格条件的被授权人员签发。
项目无损检测责任师审核的检测报告,还应将报告的电子版报无损检测专业责任工程师备案(复审)。
10渗透检测工艺
10.1检测器材
10.1.1渗透检测剂
渗透检测剂由渗透剂、清洗剂、显像剂组成,本工程选用苏州美柯达公司生成的大铜锣牌DPT-5型渗透检测剂。
10.1.2灵敏度试块:
镀铬试块、铝合金对比试块。
试块用后应清洗干净并妥善保存。
10.2检测工艺
10.2.1检测方法:
ⅡC-d(溶剂去除型着色渗透剂快干式显像法)。
10.2.2渗透剂施加方法
采用喷涂法,当渗透温度为10-50℃时,渗透时间至少为10分钟;当渗透温度小于10℃时,渗透时间应用铝合金对比试块试验确定,且至少为15分钟,具体参照所使用牌号着色剂的使用说明书。
10.2.3清洗方法:
擦洗,严禁过清洗。
10.2.4显像剂施加方法
采用喷涂法,当显像温度为10-50℃时,显像时间应不少于7分钟;当显像温度小于10℃时,显像时间应用铝合金对比试块试验确定,且一般不少于15分钟,具体参照所使用牌号着色剂的使用说明书。
10.3检测剂性能校验
将镀铬试块与工件一起进行检测操作,若试块上三处辐射状裂纹区都能清晰显示,则认为渗透检测剂系统灵敏度性能合格。
10.4验收标准
按设计文件的相关标准规定或国家标准执行。
10.5检测操作:
操作程序如下图
10.5.1预清洗
用清洗剂把被检部位表面的油污和污垢彻底清除,并让其自然干燥。
10.5.2施加渗透剂
用喷涂法施加渗透剂,喷嘴距工件表面20-30mm,渗透剂要覆盖整个被检部位。
并应在整个渗透时间内保持湿润状态。
10.5.3去除多余的渗透剂
渗透结束后,先用卫生纸将大部分多余的渗透剂擦除干净,再将清洗剂喷涂至卫生纸上进行擦洗。
直到将多余渗透剂擦洗干净,但不允许往复擦洗或将清洗剂直接喷涂在被检部位。
10.5.4施加显像剂
显像剂使用前要充分摇匀,薄而均匀的喷涂在被检表面。
喷嘴距工件表面300-400mm,喷嘴方向与被检表面的夹角为30°~40°。
10.5.5观察
显像时间结束后,对检测部位进行观察,光线较暗时可使用手把灯或手电筒照明,必要时用3-5倍放大镜进行观察。
10.6缺陷记录
发现缺陷后,用记号笔在工件上标出,并用草图在检测记录中标注。
现场检测人员在检测过程中应使用公司规定的记录表格做好原始记录;记录中的内容原则上不得涂改,若要更改仅能采用杠改方法并在每处改动处附近签上姓名和日期。
10.7缺陷评定
按设计文件的相关标准规定或国家标准进行评定。
10.8后处理
检测结束后,用干净的卫生纸清除检测部位的渗透剂和显像剂。
10.9检测报告
10.9.1检测结束后,应及时签发检测报告。
报告内容应包括:
工程名称、工件名称、工件编号、焊缝编号、检测剂型号、验收标准、缺陷情况、返修及复检情况、检测结论等。
10.9.2项目无损检测责任师组织编制渗透检测报告和检测部位图,检测报告要填写齐全,书写工整规范,不得涂改;如一页报告中有空白,在空白第一栏标注“以下空白”字样;检测报告经项目无损检测责任师审核或无损检测专业责任工程师审核并签名后,由具备资格条件的被授权人员签发。
项目无损检测责任师审核的检测报告,还应将报告的电子版报无损检测专业责任工程师备案(复审)。
11硬度检验工艺规程
11.1目的
为确保锅炉、压力容器、压力管道工程安装过程中硬度检验结果准确、可靠,满足工程设计文件、国家、行业标准及规范的要求,特制定本程序。
11.2适用范围
●公司承担的锅炉、压力容器、压力管道施工现场焊接工程,采用里氏硬度检验方法的理化检验。
●适用壁厚大于等于5mm的碳钢、合金钢管及其焊接接头经过热处理后的硬度检验。
●适用于合金钢螺栓的硬度检验。
11.3硬度检验人员资质要求
硬度检验人员应持有理化检验技术资格证书,并保证其在有效期内,才能从事硬度检验工作。
11.4硬度检验所需的设备、机具
里氏硬度计。
里氏硬度计要经计量部门检定合格,并在周检期内。
11.5检验程序及要求
11.5.1接受硬度检验根据检测委托书的要求,明确检测件材质、规格,以及焊接材料的材质,了解焊接方法、焊接接头的热处理工艺。
11.5.2根据检测委托书及管道单线图,确定硬度检测