圆锥齿轮夹具设计.docx
《圆锥齿轮夹具设计.docx》由会员分享,可在线阅读,更多相关《圆锥齿轮夹具设计.docx(17页珍藏版)》请在冰豆网上搜索。
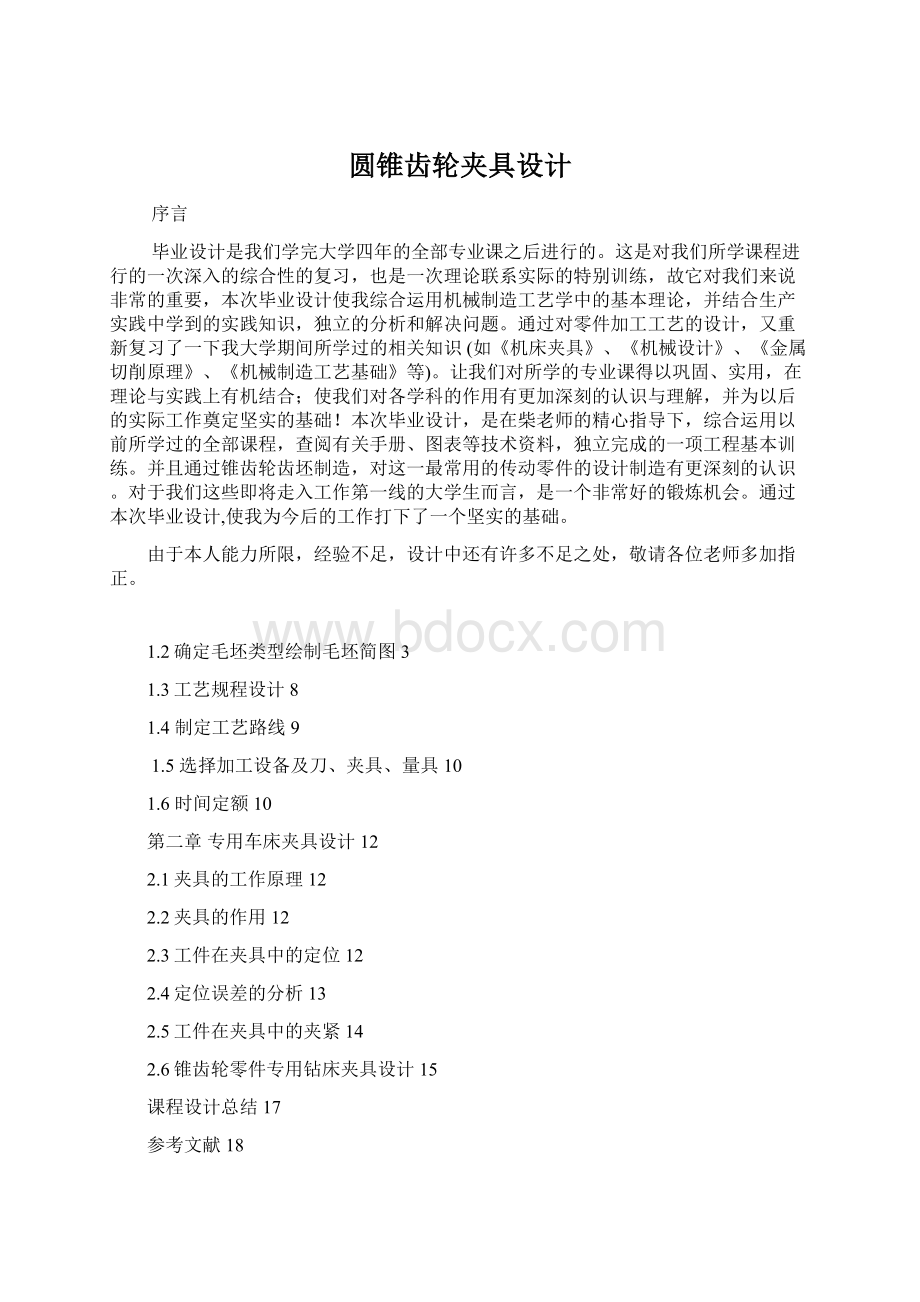
圆锥齿轮夹具设计
序言
毕业设计是我们学完大学四年的全部专业课之后进行的。
这是对我们所学课程进行的一次深入的综合性的复习,也是一次理论联系实际的特别训练,故它对我们来说非常的重要,本次毕业设计使我综合运用机械制造工艺学中的基本理论,并结合生产实践中学到的实践知识,独立的分析和解决问题。
通过对零件加工工艺的设计,又重新复习了一下我大学期间所学过的相关知识(如《机床夹具》、《机械设计》、《金属切削原理》、《机械制造工艺基础》等)。
让我们对所学的专业课得以巩固、实用,在理论与实践上有机结合;使我们对各学科的作用有更加深刻的认识与理解,并为以后的实际工作奠定坚实的基础!
本次毕业设计,是在柴老师的精心指导下,综合运用以前所学过的全部课程,查阅有关手册、图表等技术资料,独立完成的一项工程基本训练。
并且通过锥齿轮齿坯制造,对这一最常用的传动零件的设计制造有更深刻的认识。
对于我们这些即将走入工作第一线的大学生而言,是一个非常好的锻炼机会。
通过本次毕业设计,使我为今后的工作打下了一个坚实的基础。
由于本人能力所限,经验不足,设计中还有许多不足之处,敬请各位老师多加指正。
1.2确定毛坯类型绘制毛坯简图3
1.3工艺规程设计8
1.4制定工艺路线9
1.5选择加工设备及刀、夹具、量具10
1.6时间定额10
第二章专用车床夹具设计12
2.1夹具的工作原理12
2.2夹具的作用12
2.3工件在夹具中的定位12
2.4定位误差的分析13
2.5工件在夹具中的夹紧14
2.6锥齿轮零件专用钻床夹具设计15
课程设计总结17
参考文献18
第一章机械加工工艺规程设计
1.零件分析
1.1零件的作用
圆锥齿轮是用来传递两相交叉轴之间运动和动力的,轴交角可根据传动需要来任意选择,一般机械中多采用90度,圆锥齿轮的轮齿有直齿、斜齿和曲齿等多种形式,其中直齿圆锥齿轮机构由于设计制造和安装均较方便,故应用最为广泛,本次毕业设计设计的圆锥大齿轮则主要用于齿轮减速器中的运动和力的传动。
1.2零件的工艺分析
由零件图得知,其材料为45钢,锻造后调质处理具有较高的强度、韧性和表面耐磨性。
该零件的主要加工面为A面、B面、圆锥面C、圆锥面D和内孔Φ34+0.039及键槽6+0.021,内孔的精度直接影响到锥齿轮与轴的装配精度,从零件图(图1)上可以看出,其内孔的表面粗糙度等级要求最高,结合大批量生产的实际要求生产效率高,故采用先钻内孔,然后拉削内孔,即可达到表面1.6的粗糙度要求。
对于两端面,则表面为3.2的粗糙度,故采用带电磁吸盘工作台的立式铣床两次走刀即可满足加工等级要求,两锥面的粗糙度等级要求也为3.2,故可用CA6140车床来完成加工,然后在专用刨齿机上刨齿轮轮齿,最后去毛刺调质处理即可达到图纸的各项技术要求。
2.确定毛坯类型绘制毛坯简图
2.1选择毛坯
根据生产类型,零件的结构、形状、尺寸及材料等选择毛坯的制造方式和精度。
1.毛坯的类型选择
①零件的材料及力学性能
当零件的材料选定后,毛坯的类型就大致确定了。
例如,材料为铸铁,就选择铸造毛坯;材料是钢材且力学性能要求高时,可选锻件等。
锻造材料主要是各种碳钢与合金钢。
②零件的结构、形状、尺寸
形状复杂的毛坯常用铸造方法,如箱体、机架、底座等。
用于铸造的材料有灰铸铁、可锻铸铁、球墨铸铁、铸钢、有色金属合金等。
形状比较简单的零件毛坯,如轴类、套类、盘类、板类、长条类等零件,一般采用型材。
型材的种类主要有圆、方、六方棒料,板材,管材,角钢,工字钢等。
薄壁零件不可用砂型铸造;常见的一般用途的钢质阶梯轴零件,如各台阶的直径相差不大,可用棒料;如各台阶的直径相差较大,宜用锻件等。
2.毛坯的制造方法
①生产类型
大量生产时应选精度和生产率都比较高的毛坯制造方法,如金属型铸造、精密铸造、模锻、冷冲压、粉末冶金等,使毛坯的形状更接近于零件的形状。
在单件小批生产中,一般采用木模手工砂型铸造和自由锻造。
②生产条件
③充分考虑使用新工艺、新技术和新材料的可能性。
综合考虑为满足技术要求决定采用铸造成型制造毛坯,铸造成型后进行退火处理去除内应力。
2.2确定毛坯的外形尺寸、公差和机械加工余量
2.2.1毛坯外形尺寸的确定
零件工艺分析:
在车间领取的材料是圆钢型材,根据毛坯特点的可知,工艺顺序为:
车两端面——车轴端外圆——车轴端锥面——车齿端锥面。
因为零件最高表面粗糙度仅为3.2,故半精车就能达到粗糙度要求,
加工设备的选择:
根据学校金工车间车间现有的加工设备条件,选择CA6140车床作为加工机床,刀具选用45°弯头车刀、90°车刀、反向车刀
加工过程:
把圆钢装夹在CA6140车床的主轴三爪卡盘上,夹紧后开动机床,先粗车两端面,再精车两端面,装夹一端,车轴部使直径达到
58,长度为19mm,车轴端锥面,把反向车刀装夹在刀架上,调好角度,使切出来的锥面母线相对于轴线的角度为45°,然后掉头装夹,车削大端锥面,刀具可选用常用的90°车刀,转动刀架底盘,使切出来的大端锥面母线相对于轴线的角度为47°,完成后可去毛刺,然后用纱布打磨一下,
d.具体工序如下所示:
工序
内容
机床设备
刀具
量具
10
车两端面
CA6140
45°弯头车刀
游标卡尺
20
车轴端外圆
CA6140
90°车刀
游标卡尺
30
车轴端背锥面
CA6140
反向车刀
通用量角器
40
车齿锥面
CA6140
90°车刀
通用量角器
终上,毛坯效果图设计如下
2.2.2尺寸公差和机械加工余量确定
毛坯余量是指同一表面上毛坯尺寸与零件设计尺寸之差。
零件表面的加工总余量不仅与表面各工序加工余量有关,而且与毛坯的制造方法和精度有关。
(1)铸件毛坯的尺寸公差、加工余量
铸件尺寸公差由高到低分为CT1~CT16共16个等级(GB/T6414—1999),其公差带数值如下表2所示,铸件尺寸公差一般对称分布如95±4.5(CT13),非对称分布需要在基本尺寸后面标注偏差,如
(CT13)。
成批和大量生产的铸件,毛坯的公差等级按表3选取;单件和小批生产的铸件,毛坯的公差等级按表4选取。
要求的铸件机械加工余量分10个等级(GB/T6414—1999)如表5所示,由小到大分别为A、B、C、D、E、F、G、H、J和K级,用代号RMA表示。
铸件的机械加工余量等级主要与生产类型、铸造工艺方法、铸造公差等级和铸造材料有关。
推荐用于各种铸造合金和铸造方法的RMA等级按表6选取。
铸件的机械加工余量分单侧(单面)和双侧(双面),双侧加工余量与加工要求的关系
表2铸件的尺寸公差(带)数值(GB/T6414-1999)mm
表3成批和大量生产的毛坯铸件的公差等级mm
方法
公差等级CT
铸件材料
钢
灰铸铁
球墨铸铁
可锻铸铁
铜合金
锌合金
轻金属合金
镍基合金
钴合金
砂型铸造
手工造型
11~14
11~14
11~14
11~14
10~13
10~13
9~12
11~14
11~14
砂型铸造机器
造型和壳型
8~12
8~12
8~12
8~12
8~10
8~10
7~9
8~12
8~12
金属型铸造(重力铸造或低压铸造)
——
8~10
8~10
8~10
8~10
7~9
7~9
——
——
压力铸造
——
——
——
——
6~8
4~6
4~7
——
——
熔模铸造
水玻璃
7~9
7~9
7~9
——
5~8
——
5~8
7~9
7~9
硅溶胶
4~6
4~6
4~6
——
4~6
——
4~6
4~6
4~6
注:
1.表中所列出的公差等级是指在大批量生产下、且影响铸件尺寸精度的生产因素已得到充分改进时铸件通常能够达到的公差等级。
2.本标准还适用于本表未列出的由铸造厂和采购方之间协议商定的工艺和材料。
表4要求的铸件机械加工余量(RMA)mm
表5毛坯铸件典型的机械加工余量等级
毛坯尺寸图如下(毛坯尺寸,其余未标尺寸与设计尺寸相同)
3.工艺规程设计
定位基准的选择
3.1粗基准的选择原则:
a、重要加工表面余量均匀原则。
b、保证不加工面位置正确原则。
c、粗基准只能使用一次原则。
d、精基准平整光洁,定位可靠原则。
3.2精基准的选择原则:
a、应尽可能选用设计基准作为定位基准(基准重合原则)。
b、应尽可能选用统一的定位基准加工个表面以保证各面间的位置精度(基准统一原则)。
c、有时还要遵循互为基准、反复加工的原则。
d、有些加工工序要求加工余量小而均匀,以保证加工质量和提高生产率,这时就以加工面本身作为精基准(自为基准原则)。
由于圆锥大齿轮总体上为盘状零件,故在加工过程中先铣两端面,其中先选哪个面为粗基准都是一样的,则先选上端面为粗基准定三个自由度加工下端面,然后再以gh端面为精基准加工上端面即能保证加工尺寸精度等级。
4.制定工艺路线
根据各表面加工要求和各种加工方法能达到的经济精度,确定各表面的加工方法如下:
端面采用铣削加工,圆锥面采用车削加工,钻削Φ32孔,再把Φ32孔镗削到Φ34孔,然后用插齿机插削键槽,最后刨齿去毛刺清洗检验入库。
根据先面后孔原则、先粗后精原则,则初步拟定加工工艺路线如下:
工序号
工序内容
10
下料
30
锻造
30
调质处理
40
铣削上两端面
50
铣削AB端面
60
车削齿轮大端圆锥面C、车削圆锥面D
70
车削Φ56外圆
80
钻削Φ32内孔
90
镗削Φ32至Φ34
100
插键槽
110
滚齿
120
去毛刺、清洗
130
检验
140
入库
上述方案遵循了工艺路线拟定的一般原则,但某些工序有些问题,还值得进一步讨论,在第60工序时,因为在车床上加工,又因其尺寸较大,不易设计夹具也不易在车床上装夹,故为了方便加工可把第60工序放到第80、90工序后加工,这样在设计夹具时可用端面及内孔定位,用心轴加紧,对于90工序,因为工件为大批量生产,为提高生产效率可改用拉削加工,这样可以提高效率缩短工时,同样对于100工序也可以改用拉削方式加工。
综上分析,修改后的工艺路线如下:
工序号
工序内容
简要说明
10
下料
20
锻造
30
调质处理
增大表面硬度及耐磨性
40
铣削上端面
先加工基准面
50
铣削AB端面
60
钻Φ32内孔
留拉削余量
70
拉至Φ34内孔
80
车削Φ56外圆
90
车齿轮大端圆锥面C,车圆锥面D
100
拉键槽
110
滚齿
120
去毛刺、清洗
130
检验
140
入库
5.选择加工设备及刀、夹具、量具
由于生产类型为大批量生产,故加工设备宜以通用机床为主,辅以少量专用机床的流水生产线。
工件在机床上装卸及机床间的传送均有人工完成。
铣上下端面时,考虑到工件的定位夹紧方案及夹具结构设计等问题采用立铣,选择直径为Φ150mm的C类可转位面铣刀,专用夹具和游标卡尺。
钻Φ32孔,选用Z3070钻床,选择Φ32专用群钻及游标卡尺。
拉削Φ32内孔至Φ34,选用L6120拉床拉削,选用专用拉刀和游标卡尺。
车削圆锥面D、E,选用CA6140通用车床,刀具选用45°弯头车刀及专用量具。
拉削键槽选用L6120拉床,专用键槽拉刀和游标卡尺。
滚齿选用通用滚齿机及专用滚刀、专用量具。
6.时间定额
时间定额是在一定的技术组织条件下制订出来完成单件产品(如一个零件)或某项工作(如一个工序)所必需的时间,时间定额时安排生产计划、核算成本的重要依据之一,也是设计或扩建工厂(或车间)时设备和人员数量的重要资料。
时间定额中的基本时间可以根据切削用量和长度来计算的,其余组成部分时间,可取自根据经验而来的统计资料。
在制订时间定额时要防止两种偏向,一种是时间定额订得过紧,影响了工人的主动性和积极性;另一种是时间定额订得过松,反而失去了它应有的指导生产和促进生产的作用,因此制订的时间定额该具有平均先进水平,并且应随着生产水平的发展而及时修订。
完成一个零件一个工序的时间称为单件时间,它包括下列组成部分:
(1)、基本时间
——是指直接改变工件的尺寸形状,相对位置和表面质量所消耗的时间,对于切削加工来说,基本时间是切除金属所耗费的机动时间(包括刀具的切入和切出时间在内)
(2)、辅助时间
——指在各个工序中为保证完成基本工艺工作需要做的辅助动作所耗费的时间,所谓辅助动作包括:
装、卸工件,开动和停止机床,改变切削用量,测量工件,手动进刀和退刀等手动动作等。
基本时间和辅助时间的总和称为操作时间。
(3)、工作地点服务时间
,一般按操作时间的2%——7%来计算。
(4)休息和自然需要时间
,一般按操作时间的2%来计算。
因此单件时间是
=
+
+
+
对于工序10所需的单间时间如下,铣削机动时间的计算公式:
机动时间
=
式中
的有效长度:
其中
为铣刀直径,
为铣削宽度,
就本工步而言,有效切削长度为150
(铣削宽度
;铣刀直径
)
故有:
又因为铣削C面和铣削B面相同,则
;
则:
根据经验取
;
;
则:
其它工序具体时间见工序卡片。
第2章专用钻床夹具设计
机床夹具是机械加工工艺系统的重要组成部分,是机械制造中的一项重要工艺装备。
工件在机床上进行加工时,为保证加工精度和提高生产率必须使工件在机床上相对夹具占有正确的位置,完成这一功能的辅助装置称为机床夹具。
机床夹具在机械加工中起着重要的作用。
它直接影响想机械加工质量、生产效率和生产成本以及工人的劳动强度等。
因此机床夹具设计是机械加工工艺准备中的一项重要工作。
1.夹具的工作原理
1.1使工件在夹具中占有正确的加工位置,这是通过工件各定位面与夹具的相应定位元件的定位工作面(定位元件上起定位作用的表面)接触配合或对准来实现的。
1.2夹具对于机床应先保证定位元件的定位工作面对夹具与机床相连接的表面之间的相对准确位置。
这就保证了夹具定位工作面相对机床切削运动形成表面的准确几何位置,这就达到了工件工件加工面对定为基准的相互位置精度要求。
1.3使刀具相对有关的定位元件的定位工作面调整到准确位置。
这就保证了刀具在工件在加工中的表面对工件定位基准的位置尺寸。
2.夹具的作用
夹具是机械加工中不可缺少的一种工艺装备。
1).保证稳定可靠地达到各项加工精度要求。
2).缩短加工工时,提高劳动生产率。
3).降低生产成本。
4).减轻工人劳动强度。
5).可由较低技术等级的工人进行加工
6).能扩大机床工艺范围。
3.工件在夹具中的定位
定位的目的是使工件在夹具中相对于机床、刀具、占有确定的正确位置,并且应用夹具定位工件还能使同一批工件在夹具中的加工位置一致性好,在夹具设计中,定位方案不合理,工件的加工精度就无法保证,工件定位方案的确定是夹具设计中首先要解决的问题,用六个定位支承点与工件接触,并且保证合理分布,每个定位支承点限制工件的一个自由度,便可将工件六个自由度完全限制,工件再见在空间的位置也就被唯一地确定,因此,要是工件完全定位,就必须限制工件的六个自由度,即工件的六点定位原理,在应用工件“六点定位原理”进行定位问题分析时,应该注意以下几点:
1).定位就是限制自由度,通常用合理布置定位支承点的方法来限制工件的自由度。
2).定位支承点限制工件自由度的作用,应理解为定位支撑点与工件定位基准面始终保持紧贴接触,若二者脱离,则意味着失去定位作用。
3).一个定位支承点仅限制一个自由度,一个工件仅有六个自由度,所以设置的定位支承点数目原则上不应超过六个。
4).分析定位支承点的定位作用时,不考虑加力的影响,工件的某一个自由度限制是指工件在这一方向上有确定的位置,并非指工件在受到其脱离定位支承点的外力时,不能运动,欲使其在外力作用下不能运动,是夹紧的任务。
反之,工件在外力作用下不能运动,即被夹紧,也并非是说工件的所有自由度都被限制了,所以定位和夹紧是两个概念,绝对不能混淆。
5)定位支承点是由定位元件抽象而来的,在夹具中,定位支承点总是通过具体的定位元件体现,至于具体的定位元件应转化为几个支承点,需结合其结构进行分析。
需注意的是,一种定位元件转化的支承点的数目一定的,但具体限制的自由度与支承点的布置有关。
6).在夹具设计和定位分析中,经常遇见以下几个问题:
a.完全定位和不完全定位:
限制了工件全部六个自由度,称为工件的完全定位;工件的六个自由度没有被完全限制的定位称为不完全定位,
b.过定位和欠定位:
在加工中,如果工件的定位支承点数少于应限制的自由度数,必然导致达不到所要求的加工精度。
这种工件定位点不足的情况,称为“欠定位”欠定位在实际生产中,是绝对不允许的。
反之,若工件的某一个自由度同时被一个以上的定位支承点重复限制,则对这个自由度的限制会产生矛盾,这种情况被称为“过定位”,过定位在某些情况下是被允许的。
4.定位误差的分析
当夹具在机床上的定位精度达到要求时,如果工件在夹具中定位不准确,将会使设计基准在加工尺寸方向上产生偏移,往往导致加工后工件达不到要求。
产生定位误差的原因有,定位基准与设计基准不重合产生的定位误差,定位副制造不准确产生的基准位移误差。
从零件图和工艺过程可知,在铣削上下端面时,定位基准和设计基准相重合不存在定位误差,所以能达到很好的尺寸精度,在钻削内孔时因为需要留拉削余量,也不需要保证很高的精度要求,只要能保证内孔轴线与上下两端面的垂直度就可以达到要求,同样拉削内孔时必须保证轴线相对与两端面的垂直度,在60工序中,由于采用内孔和心轴定位,则因为设计基准和定位基准不重合,产生定位误差,根据零件图的技术要求和经验知,其定位误差在合理的范围内,故不必计算校核。
5.工件在夹具中的夹紧
设计合理的夹紧机构,必须首先合理的确定夹紧力的三要素:
大小、方向、作用点。
1).加紧力的确定原则:
a.夹紧力的作用方向应垂直主要定位基准面。
b.夹紧力作用方向应使所需夹紧力最小,这样可使机构轻便、紧凑,工件变形小,对手动夹紧可减轻工人劳动强度。
c.夹紧力作用方向应使工件变形尽可能小。
2).夹紧力作用点的确定
a.夹紧力的作用点应落在支承元件或几个支承元件形成的稳定受力区域内。
b.夹紧力作用点应该在工件刚性好的部分。
c.加紧力作用点应尽可能靠近加工面。
3).夹紧力的大小
夹紧力的大小可根据切削力、工件重力的大小、方向和相互位置关系具体计算,为安全起见,计算出的夹紧力应乘以安全系数K,故实际夹紧力一般比理论计算值大2到3倍。
6.锥齿轮零件专用钻床夹具设计
6.1夹具设计任务
为了提高劳动生产率,保证加工质量,降低劳动强度,需设计专用夹具。
为工序60钻扩孔设计钻床夹具,所用机床为立式钻床525钻床,成批生产规模。
6.2确定夹具的结构方案
(1)确定定位方案,设计定位装置
根据工序简图规定的定位基准,选用一面两套定位方案。
从基准的重合原则和定位的稳定性、可靠性出发,选择下端面为主要定位基准面,并选择轴外圆为另外的定位基准面。
定位元件采用V形块与工件轴外圆配合,限制4个自由度,夹具体与工件定位端面接触,限制一个自由度。
实现工件完全定位。
(2)确定夹紧机构
钢套的轴向刚度比径向刚度好,用两个V形块压紧。
(3)确定导向装置
Φ32孔要求进行钻、镗两个工步的加工,生产批量大,故选用快换钻套作为刀具的导向元件。
6.3画夹具装配图
夹具装配总图,在图上应将V形块、钻模板与夹具体的连接结构表达清楚。
其中钻套与夹具体采用过渡配合,用锁紧螺母固定。
钻模板与夹具体用两个销钉、两个螺钉连接。
夹具装配时,待钻模板的位置调整准确后再拧紧螺钉,然后配钻、铰销钉孔,打入销钉。
课程设计总结
此次设计是锥齿轮工艺和夹具设计,这是一项对知识要求非常广泛,同时对个人和集体组合能力要求非常高。
比如,在知识方面,它包括了我们在大学时所学的机械设计,机械加工工艺,材料,机械加工基础,机械制图,夹具设计,机械制造等。
通过本次毕业设计,我又重新温习以上知识,并且在柴老师的指导下,我又学到了许多新知识,在此非常感激。
纸上得来终觉浅,绝知此事枯躬行。
通过对这一周的机械制造装备实训的学习,我松了一口气,感觉自己以前专业知识学得不够扎实,好多已经忘了,这几天查了大二大三很多相关的专业书,使我对以往所学的理论基础、专业知识和基本技能进行了一次较为全面的训练,培养了我严谨的科学态度、独立分析和解决问题的能力以及敢于创新的精神。
在设计的过程中通过对零件图的研究和分析制定了一套合理的工艺,本工艺在理论上是可行的,并且对于图纸上要求的粗糙度,位置度,尺寸精度等都可以较好的满足。
还具有较好的经济性。
为了能更好的加工还对典型的工序进行了专用夹具的设计,在夹具的设计过程中,我们始终按照夹具的设计基本原则并结合实际情况,做到夹具结构局部优化与整体化于一体,在保证其功能前提下,尽量简化夹具的结构和增加夹具自动化的能力。
通过本次设计,我充分认识到学习先进软件的必要性,先进的软件能提高效率和减少设计者时间上的成本。
我的整个设计过程中遇到了很多我不易解决的问题,让我感到很是困惑!
但
最终通过查阅多方面的资料或指导教师的引导,这些问题都得到了解决。
我想通过
这样的一种亲身的磨砺,对我以后的工作与学习会大有裨益。
毕竟我学会了利用理
论知识来解决实际问题的能力!
每周柴老师都给我们安排了答疑,在答疑过程中,柴老师给了我很多指导和鼓舞,老师严谨治学和耐心的教导,使我收获很大,最终完成了这次实训。
参考文献
【1】:
李洪主编,机械加工工艺手册,北京出版社,1990年。
【2】:
孟少农主编,机械加工工艺手册,第一卷,机械工业出版社,1991年。
【3】:
张龙勋主编,机械制造工艺学课程设计指导书及习题,机械工业出版社,1999年。
【4】:
卢秉恒主编,机械制造技术基础,机械工业出版社,2008.6(重印)。
【5】:
申永胜主编,机械原理教程(第二版),清华大学出版社,2005年。
【6】:
王绍俊主编.《机械制造工艺设计手册》.哈尔滨:
哈尔滨工业大学出版社.1994
【7】:
赵志修主编机械制造工艺学北京:
机械工业出版社1984,2
【8】:
李益民主编.《机械制造工艺设计简明手册》.哈尔滨:
哈尔滨工业大学出版社.200
【9】:
陈红钧主编.《实用机械加工工艺手册》.北京:
机械设计出版社.2003