普通轿车车身涂装车间设计.docx
《普通轿车车身涂装车间设计.docx》由会员分享,可在线阅读,更多相关《普通轿车车身涂装车间设计.docx(13页珍藏版)》请在冰豆网上搜索。
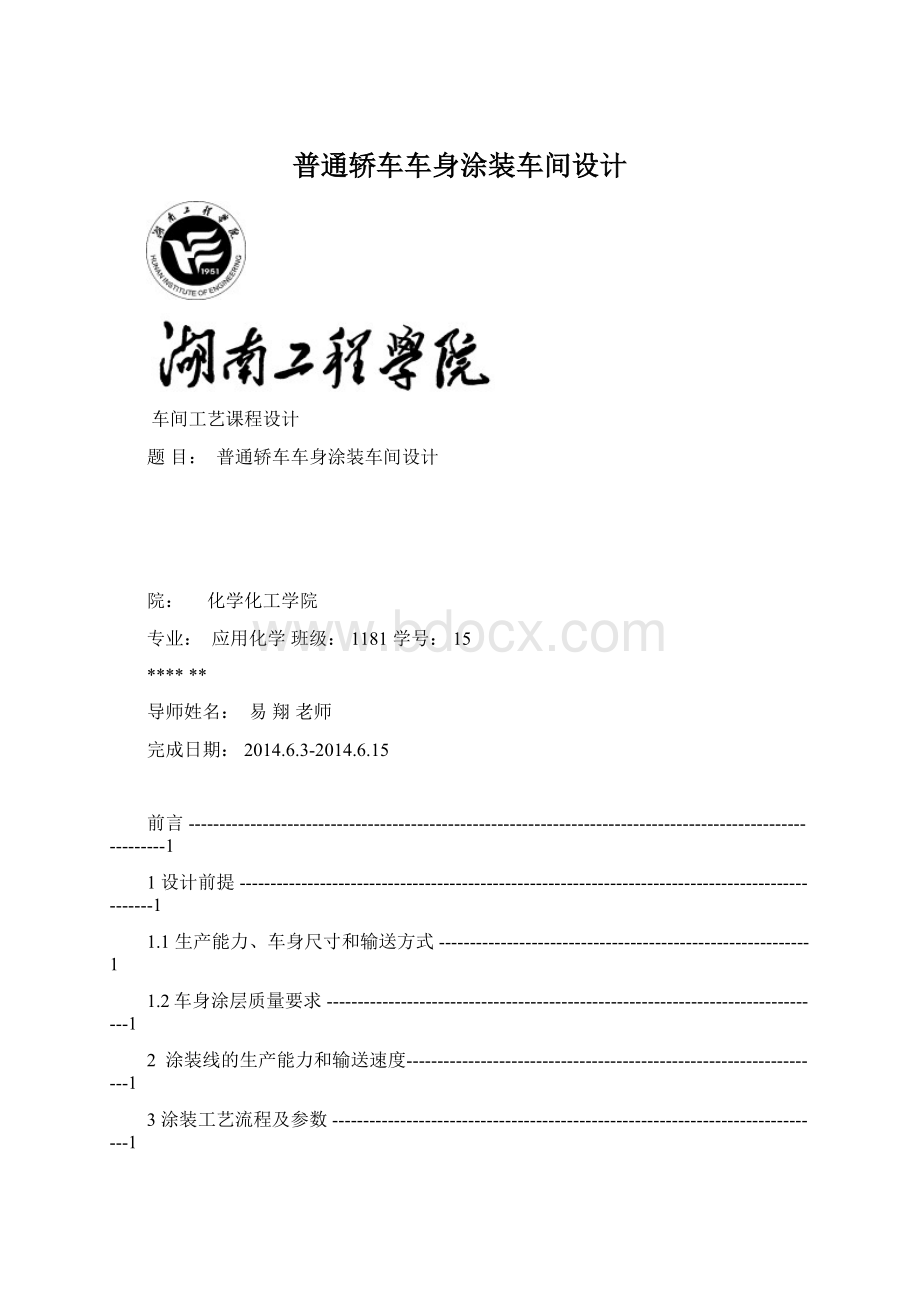
普通轿车车身涂装车间设计
车间工艺课程设计
题目:
普通轿车车身涂装车间设计
院:
化学化工学院
专业:
应用化学班级:
1181学号:
15
******
导师姓名:
易翔老师
完成日期:
2014.6.3-2014.6.15
前言-------------------------------------------------------------------------------------------------------------1
1设计前提---------------------------------------------------------------------------------------------------1
1.1生产能力、车身尺寸和输送方式------------------------------------------------------------1
1.2车身涂层质量要求---------------------------------------------------------------------------------1
2涂装线的生产能力和输送速度--------------------------------------------------------------------1
3涂装工艺流程及参数--------------------------------------------------------------------------------1
4涂装设备的设计---------------------------------------------------------------------------------------1
4.1前处理设备-------------------------------------------------------------------------------------------1
4.2电泳线--------------------------------------------------------------------------------------------------1
4.3烘干设备-----------------------------------------------------------------------------------------------1
4.4水性底色漆闪干室---------------------------------------------------------------------------------1
4.5车底喷涂线-------------------------------------------------------------------------------------------1
4.6喷漆线及配套设备---------------------------------------------------------------------------------1
5涂装主要设备的计算--------------------------------------------------------------------------------1
5.1电泳槽-----------------------------------------------------------------------------------------------------1
5.2喷漆室-----------------------------------------------------------------------------------------------------1
6涂装三废处理----------------------------------------------------------------------------------------------1
6.1大气污染---------------------------------------------------------------------------------------------------1
6.2水质污染---------------------------------------------------------------------------------------------------1
7总结--------------------------------------------------------------------------------------------------------1
参考文献-------------------------------------------------------------------------------------------------------1
普通轿车车身涂装车间设计
0前言
随着汽车涂装技术的发展和环保要求的逐步提高,国内汽车涂装线已越来越重视环保节能型涂装新材料、新工艺的应用。
设计汽车涂装线时,涂装设备的工作原理和参数必须与之相匹配;同时,为了追求涂装线的高精益化和高柔性化,设备选型应尽可能多地采用国产设备,通过加强设备维护来提高整个生产线的开动率,从而降低生产线的建设费用;还要充分了解和预测新车型的开发,新涂装线应能满足多品种共线生产,使后续车型投产时对生产线的停产改造时间尽可能短。
现在,根据设计任务的要求,设计一个年产10万辆普通轿车的车身涂装车间,选用典型的3C3B涂装工艺。
工艺选定后,根据所采用的工艺及年生产纲领的要求,进行工艺的设计及计算。
工艺的设计包括工艺流程的确定、各工序采用的工艺规范等。
选择和计算各工序所采用的前处理槽的尺寸及数量,选择车间所需的主要设备等。
设备选型与计算完毕后,设计车间平面布置图、阴极电泳槽图、以及喷漆室的设计图。
最后对所设计的内容进行评述。
1设计前提
1.1生产能力、车身尺寸和输送方式
被涂物尺寸(长×宽×高):
4.8m×1.7m×1.4m
生产纲领:
10万台/年
净生产能力:
300台/d,工作时间:
23h/d。
输送方式:
前处理、电泳线采用摆杆输送机;车底喷涂采用反向滑橇;中涂、面漆喷涂线及其他部分采用滑橇输送系统。
1.2车身涂层质量要求
满足中、高级轿车的涂层质量要求。
电泳底漆、中涂漆和面漆的涂膜厚度的要求不一样,电泳漆:
外表面≥18μm,内部空腔≥1lμm;中涂:
外表面30~40μm,内表而15~20μm;面漆:
金属底色漆12~20μm或素色漆20—25μm,清漆35~50μm。
2涂装线的生产能力和输送速度
根据设计前提的要求,综合考虑各线设备利用率、返工率和交换件生产需求,确定涂装线的产能和输送速度,见表1。
每年计算时间:
335天(扣除一个月检修期)
生产方式为流水线生产。
生产节奏为T=t•k/M
式中:
t—工时基数,min;
M—生产纲领;
k—设备有效利用率
工人总数=
输送链速度:
v=L/T
式中:
v—链速,m/min;
L—挂距,m;
T—生产节奏,min/辆;
表1
序号
生产线
线数
(条)
设备利用率
(%)
挂距
(m)
生产节奏
(min/辆)
输送速度
(m/min)
返修5%
(台/日)
1
2
3
4
5
6
7
8
9
1011
前处理
电泳
电泳烘干
电泳打磨
车底喷涂
中涂
中涂烘干
中涂打磨
面漆喷涂
面漆烘干
检查
1
1
1
1
1
1
1
1
1
1
1
90
90
90
95
95
90
90
90
90
90
95
6.0
6.0
5.0
6.0
6.0
6.2
5.0
6.0
6.2
5.0
6.0
4.15
4.15
4.15
4.37
4.37
4.15
4.15
3.94
3.94
3.94
4.16
1.45
1.45
1.20
1.37
1.37
1.49
1.20
1.52
1.57
1.27
1.44
—
—
—
—
—
—
—
15
15
15
15
3涂装工艺流程及参数
根据所用涂装材料和工艺的要求,确定的涂装工艺流程及参数见表2。
表2
序号
工序名称
处理方式
工艺参数
区段长度/m
备注
时间/min
温度/℃
1
2
2.1
2.2
2.3
2.4
2.5
2.6
2.7
2.8
2.9
2.10
2.11
2.12
2.13
3
4
4.1
4.2
4.3
4.4
4.5
4.6
5
6
7
8
9
10
11
12
13
14
14.1
14.2
14.3
14.4
14.5
14.6
14.7
15
16
17
滑橇锁紧/检查+预清理挂转至前处理输送链
前处理
热水洗
预脱脂
脱脂
水洗
水洗(浸入即出)
表调(浸入即出)
磷化
水洗
水洗(浸入即出)
钝化
水洗
循环纯水洗
洁净纯水洗
沥干
电泳涂装
阴极电泳(含0次UF液洗)
用循环UF液洗
用循环UF液洗
洁净UF液洗
循环DI水洗
洁净DI水洗
沥干
电泳烘干,强制冷却
所有缝隙处涂密封
车底喷涂
去遮蔽,擦净车身外表面
电泳打磨
喷中涂
中涂烘干,强制冷却
中涂打磨
喷面漆
手工喷涂底色漆
自动喷涂底色漆
检查补喷底色漆
晾干
手工喷涂罩光清漆
自动喷涂罩光清漆
检查补喷罩光清漆
晾干
面漆烘干,强冷
检查,报交
自动+手动
喷
喷
浸
喷
浸
浸
浸
喷
浸
浸
喷
浸
喷
自动
浸
喷
浸
喷
浸
喷
热风对流
压涂或喷涂
高压无气喷涂
手工
手工
手工或自动
热风对流
手工
手工
自动
手工
手工
自动
手工
热风对流
手工
约12
0.5
0.5~1.0
3
0.5
10s
10s
3
0.5
10s
10s
0.5
10s
0.25
3.0~4.0
0.5
10s
0.1~0.2
10s
0.1~0.2
30
30
3
3
30
RT
50±5
50±5
50±5
RT
RT
RT
40±5
RT
RT
RT
RT
RT
RT
28±1
RT
RT
RT
RT
RT
175±5
RT
RT
RT
RT
20~25
140
RT
≥20
≥20
≥20
≥20
≥20
≥20
≥20
140
≥20
约17.4
约8.7
43.2
43.2
45.7
推杆悬连一般不带滑橇
如采用旋转送机,设备长度可缩短约20%
可溢流至2.9工序
纯水电导≤10μS
如采用旋转送机,设备长度可缩短约20%
补加4.3工序的槽液
布置在4.3工序的出口
布置在4.5工序的出口
20min为车身保温时间
20min为车身保温时间
4涂装设备的设计
涂装设备的设计,包括工区的布置、处理方式、工艺时间和温度等。
均要符合表2的要求。
4.1前处理设备
采用以摆杆输送机为输送设备的连续通过式结构,前处理分为脱脂、水洗、磷化、水洗等部分,全部采用喷浸结合式。
喷淋压力l~1.5Pa,脱脂采用碱性脱脂剂,温度60~80℃,时间3min,用电热管加热,磷化采用锌系磷化剂,温度45~55℃,时间2min,用电热管加热水,然后通过热交换器来加热磷化剂。
在该设备的两端装有风幕,防止热量向外扩散,磷化剂配方中的各种原料通过气动泵按所消耗掉的数量从原料筒中源源不断地进行补充,再通过现场化验来进行调整。
两道水洗工序系用室温的通过净化处理自来水,时间各为1min。
4.1.1室体
室体内的非喷淋工区设置单侧过道,喷淋工位不设过道。
在脱脂工区以后的室体内,有防止车身表面因停线而变十的喷湿装置。
需要加热的工区室体有保温层,保温层厚度50mm。
在前处理线出入口、脱脂工区设置送排风,防止蒸汽、水雾等聚集、外溢,磷化上区设置送排风,防止酸雾聚集。
4.1.2工艺槽
所有浸槽的液面到槽沿的距离为250mm,车顶到液面距离为300mm。
槽体材质为不锈钢,所有加热槽隔热层厚度50mm。
每个槽子上有RO水和自来水的快速加水口,要求将单个空槽子灌满的最长时问为30min,每个槽子排空的时间也为30min。
4.1.3加热、除油、除铁屑和除渣等系统
系统的循环采用不锈钢离心泵,为了维修,设置泵的移出轨道,电葫芦。
加热系统采用不锈钢板式换热器,脱脂液采用一级加热,磷化液采用二级加热,磷化液与加热介质的温差≤l0℃,槽液加热到工艺温度所需时间最长为4h。
在热水洗、预脱脂和脱脂系统设置除油和除铁屑装置,除油装置采用二级油水分离,一级加热破乳,二级采用油水分离器,使槽液含油量低于2g/L。
除铁屑装置首先采用旋液分离器除去槽液中大颗粒铁屑,再用磁性分离器除去小颗粒铁屑,经纸带式过滤机对浓缩液处理后,清液返回脱脂槽。
对磷化槽液配置了全量过滤除渣系统,将含高浓度磷化渣的磷化液从磷化槽底部锥斗中泵入到除渣系统的压滤室,经过压滤、吹干、刮渣处理后,使磷化槽中渣含量≤120×10-6。
4.2电泳线
4.2.1室体
电泳工区设置双侧过道,UF水洗II工区设置单侧过道。
在电泳工区和电泳后通道内有送排风系统,其中电泳工区送排风口沿电泳槽侧均布,以降低电泳室体内的有机溶剂浓度。
4.2.2工艺槽
电泳槽体用6.5mm厚碳钢制作,6mm厚的环氧玻璃钢做衬里,用20000V的高,蓝试验衬里的瞬间放电性,保证衬里的绝缘性能。
其他工艺槽的槽体材质为4㎜厚的SUS304不锈钢。
4.2.3超滤装置、直流电源和阳极
超滤装置采用进口卷式膜管,车身电泳后清洗需要的新鲜超滤液量为2×10-3m3/(m2·min),具有对单根膜管反冲洗功能。
电泳直流电源采用国产设备,参数为l500A/450V,输出电压连续可调,共3套。
阳极采用3段电压,车身入槽后通电。
阳极采用管式阳极,阳极(含底部阳极)与阴极面积比为1:
4。
4.3烘干设备
烘干设备包括电泳、中涂、面漆烘干室,采用π型结构。
烘干室保温层厚度为150㎜,内皮材料为渗铝钢板,外皮材料为镀锌波纹板。
保温材料采用密度为120kg/m3的矿物棉。
4.3.1加热系统
加热系统采用独立区域加热器,加热器包括燃烧器、换热器、嵌入式防爆离心风机、过滤器、电气控制等部件。
辐射升温区采用燃烧产生的高温烟气直接加热辐射板。
对流升温区和保温区采用间接加热,进入烘干室的热空气要经过两次过滤,即在加热器内经过换热器后进行第1次过滤,在烘房的内部风管出风口进行第2次过滤,过滤等级为EU8。
烘干室从冷态达到工作温度的升温时间为lh,并有紧急情况下降温能力,即在2h内可冷却到45℃。
烘干室进出口升降机上方均布置热顶,以防止烘房出入口的油烟冷凝。
4.3.2废气焚烧系统
3个烘干室共用1套RTO废气焚烧系统,废气处理量为40000m3/h,该系统由3个蓄热室、一个氧化室和1个过滤室组成。
3个蓄热室轮流进行蓄热、放热并执行反吹清扣功能,
氧化室氧化分解废气,过滤室对进入蓄热室的废气进行过滤。
4.3.3强冷室
采用致冷后的冷空气进行强冷,在强冷室的致冷箱内,空气经过EU4过滤、表冷段致冷、EU8过滤后进入强冷室。
4.4水性底色漆闪干室
采用直通式烘干室结构。
闪干室在0.5h内可从冷态达到丁艺温度。
在升温区加热箱内,新鲜空气经EU4过滤器→表冷段→加热段→Eu8过滤,然后由风机送入升温区室内风管,经送风口EU8过滤器后进入闪干室内,送风温度为70℃,含湿量≤0.015kg/kg干空气。
在保温区加热箱内,循环空气进入加热箱经过换热器、EU8过滤器后,由风机送入保温区室
内风管,经送风口EU8过滤器后进入闪干室内,送风温度为90℃。
闪干后的强冷室使用经致冷后的冷空气使车身温度≤35℃。
4.5车底喷涂线
采用以反向滑橇输送机为输送设备的间歇通过式结构。
沿整个室体布置送排风,送风由上位空气供应装置供应。
4.6喷漆线及配套设备
喷漆线包括中涂、底色漆和清漆等3条生产线。
4.6.1空气供应装置
该装置由进风段、初效过滤段、表冷段、加热段、加湿段、风机段、均流段、消声段、中效过滤段、亚高效过滤段和出风段等组成,负责向喷漆窒提供经调温、调湿后的李气。
在夏季,高温高湿的室外空气在表冷段经过冷却除湿后,再在加热段进行等湿升温,使空气温、湿度满足喷漆的要求。
在冬季,低温低湿的室外空气在加热段经过等湿升温后,再在加湿段进行等焓加湿,使夺气温、湿度满足喷漆的要求。
为了节能,将打磨室和喷漆线的擦净室的供风进行回用,将其送风量的65%过滤后返回到对应的空气供应装置进风口。
4.6.2动、静压室和喷漆室
来自夸气供应装置的窄气经动、静,K室后形成均匀的层流进入喷漆室内,静压室底部过滤层的过滤等级为EU5。
喷漆窜体壁板为1.2mm的5US304-4<锈钢板和6mm的夹胶玻璃,室体两侧外壁f:
装有荧光灯箱,通过玻璃窗照射到室体内部,在人工喷涂和检查补漆工区布置有喷漆枪站。
4.6.3文丘里漆雾捕捉系统
进入喷涂区的气流环绕车身,将喷漆时产牛的漆雾向下带入漆雾捕捉系统。
该系统通过文氏口效应将水流充分雾化,水雾与气流中的漆雾通过碰撞、混合,漆雾被水雾捕捉凝聚成含漆雾的水滴,然后通过降低风速和用挡水板使风向多次转变,水滴从气流中分离出来落入水槽中,捕捉漆雾的效率达98%以上,被净化后的空气由排风机送入70m高的烟囱排放。
5涂装主要设备的计算
5.1电泳槽
电泳槽是电泳涂装作业的浸槽,形状有船型和矩形两种。
船型电泳槽适用于大量流水连续式生产。
其两端的斜坡长度取决于被涂物出入槽的角度,平段的长度根据链速和泳涂时间确定。
根据输送被涂物的轨迹,求取必要的最小限度的主槽形状。
为保证槽液较好的搅拌状态和最佳的极间距,电泳槽容纳被涂物要留有间距。
平段长度:
L=1.45×3=4.35m
电泳槽的液面到槽沿的距离为250mm,车顶到液面距离为300mm。
车底到槽底的距离为500mm,底座的高度为250mm,车身距槽壁的距离为500mm。
所以电泳槽本体:
2700mm×2450mm×(4000~10000)mm。
5.2喷漆室
喷涂室的大小首先取决于喷涂作业间的大小。
再根据选用的喷漆室的类型和供、排风系统的布置方式来确定其外形尺寸。
喷涂作业间的大小与被涂物外形和大小、生产方式、喷涂工位的布置等因素有关。
喷涂室的喷涂作业间内尺寸:
宽度(W)=被涂物宽度+作业区宽度(0.8~1.5m)×2
所以,W=4.7m
高度(H)=被涂物高度+工件离格栅板距离(0.3~0.5m)+工件离顶棚的高度(1.5~2.0m)
所以,H=3.4m
长度(L)=单件喷涂工时(min)×输送链速度(m/min)+工件距出入口距离(0.6~1.0m)×2
所以,L=5.71
喷涂室断面的决定:
(1)被涂物的高度:
1400㎜。
(2)被涂物的宽度:
旋转时的最大宽度:
5100㎜
(3)被涂物顶离输送链轨顶高度:
1500㎜
(4)被涂物下端至水槽间距:
300㎜
(5)水槽高度:
400㎜
(6)喷涂作业区宽度:
1000㎜
(7)工件至水幕间距:
400㎜
(8)净化室:
600㎜
(9)供风室:
450㎜
6.涂装三废处理
涂装车间产生的“三废”——废水,废气,废渣主要危害会对环境造成大气污染和水质污染。
6.1大气污染
造成大气污染的主要物质是烟尘、粉尘和有害气体等。
涂装车间废气主要由喷漆室、流平室、烘干室处产生,主要有挥发性溶剂、涂料粉尘、热分解产物、燃烧废气等。
废气处理方法:
直接燃烧法、触媒氧化分解法、活性炭等吸附剂的吸附法、水洗。
6.2水质污染
废水有:
前处理废水;电泳废水;喷漆室废水;湿打磨废水等。
废水处理方法:
凝集沉淀法、上浮分离法、离子交换法、膜分离法生化处理法等。
7总结
汽车现在已经普及,设计一个好的汽车涂装方案(既可以降低成本又可以提高),有着很大的必要。
质量和成本是增强产品竞争力的两大支柱。
制造业获得竞争力优势的奥秘是用同等数量的原材料和能源,加工出更多更好的产品,从而创造出更高的产值。
在当前的环境下,涂装工艺设计必须改变观念,依靠技术进步,创新设计模式,在确保涂装质量的基础上,重视涂装线的环保性和经济性,尽最大努力实现涂装车间的生产经济规模化。
这样我国汽车才有别国竞争的实力。
通过两周的课程设计,我进行了独立思考,使我的工艺基础得到了复习和提高,结合自己的知识和课程设计在找资料的过程中丰富了我的知识面。
在遇到困难的时候不是知难而退而是迎难而上,对我的学习有很大帮助。
这次设计与我们的生活紧密相关的东西,提高了我的学习兴趣,也为以后的毕业论文设计打下了基础。
参考文献
[1]王民信,王丽君.汽车涂料.北京:
化学工业出版社,2005.
[2]伍泽涌,卢鸿琏,肖泽星.新型涂装前处理应用手册[M].成都:
四川科学技术出版社,1998.
[3]王锡春.最新汽车涂装技术[M].北京:
机械工业出版社,1997.
[4]王锡春.涂装车间设计手册.北京:
化学工业出版社,2008.
[5]吴涛编.汽车涂装车间工艺设计基础.吉林:
吉林工业大学出版社,1993.
[6]叶扬祥,潘肇基.涂装技术使用手册.机械工业,2003.
[7]王民信,王丽君.汽车涂料.北京:
化学工业出版社,2005.