连接盘铸造工艺设计汇编.docx
《连接盘铸造工艺设计汇编.docx》由会员分享,可在线阅读,更多相关《连接盘铸造工艺设计汇编.docx(21页珍藏版)》请在冰豆网上搜索。
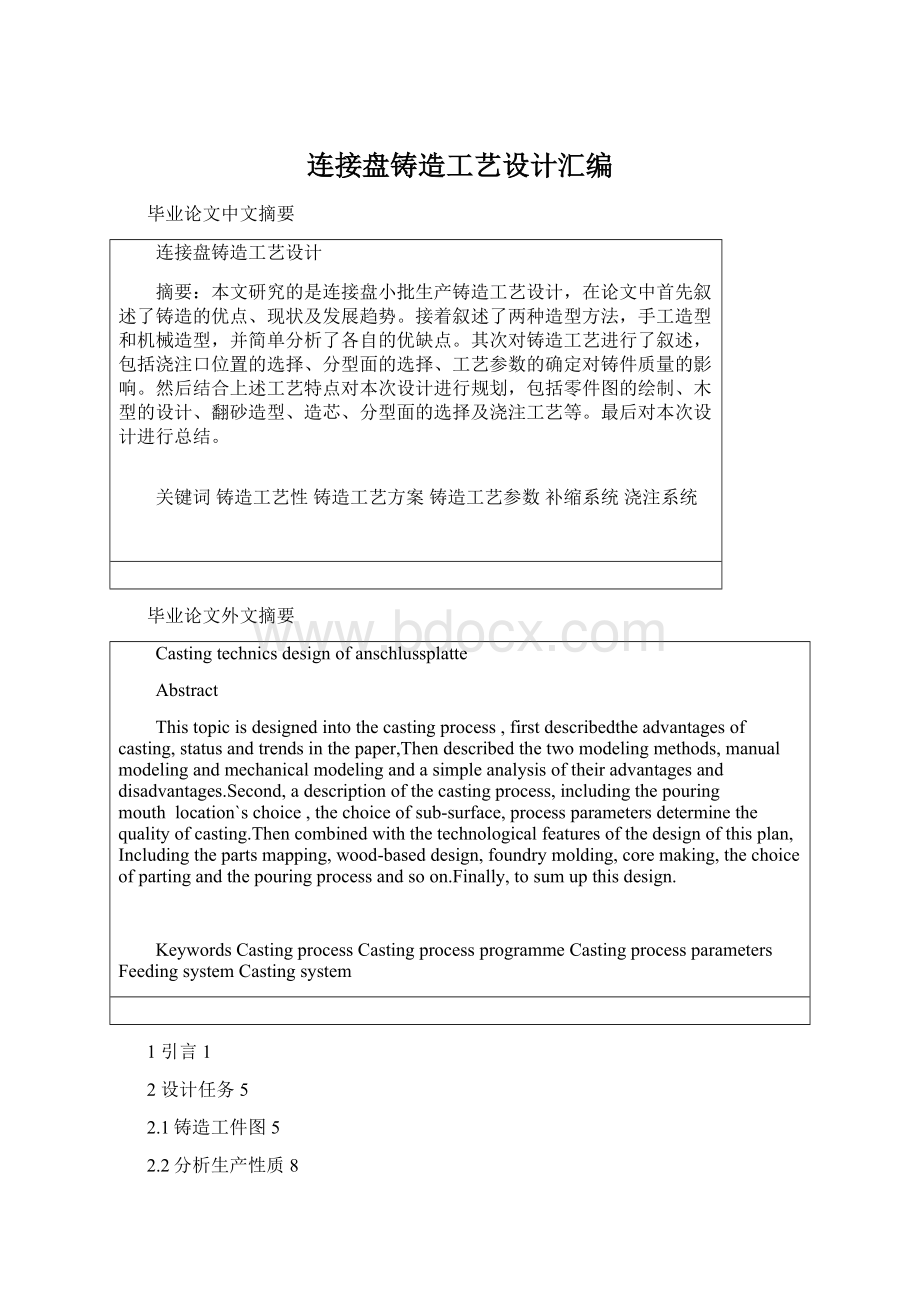
连接盘铸造工艺设计汇编
毕业论文中文摘要
连接盘铸造工艺设计
摘要:
本文研究的是连接盘小批生产铸造工艺设计,在论文中首先叙述了铸造的优点、现状及发展趋势。
接着叙述了两种造型方法,手工造型和机械造型,并简单分析了各自的优缺点。
其次对铸造工艺进行了叙述,包括浇注口位置的选择、分型面的选择、工艺参数的确定对铸件质量的影响。
然后结合上述工艺特点对本次设计进行规划,包括零件图的绘制、木型的设计、翻砂造型、造芯、分型面的选择及浇注工艺等。
最后对本次设计进行总结。
关键词铸造工艺性铸造工艺方案铸造工艺参数补缩系统浇注系统
毕业论文外文摘要
Castingtechnicsdesignofanschlussplatte
Abstract
Thistopicisdesignedintothecastingprocess,firstdescribedtheadvantagesofcasting,statusandtrendsinthepaper,Thendescribedthetwomodelingmethods,manualmodelingandmechanicalmodelingandasimpleanalysisoftheiradvantagesanddisadvantages.Second,adescriptionofthecastingprocess,includingthepouringmouth location`schoice,thechoiceofsub-surface,processparametersdeterminethequalityofcasting.Thencombinedwiththetechnologicalfeaturesofthedesignofthisplan,Includingthepartsmapping,wood-baseddesign,foundrymolding,coremaking,thechoiceofpartingandthepouringprocessandsoon.Finally,tosumupthisdesign.
KeywordsCastingprocessCastingprocessprogrammeCastingprocessparametersFeedingsystemCastingsystem
1引言1
2设计任务5
2.1铸造工件图5
2.2分析生产性质8
3工艺分析8
3.1铸造工艺图8
3.2浇注位置9
3.3分型面10
3.4工艺参数的选定11
3.4.1机械加工余量和公差11
3.4.2起模斜度12
3.4.3收缩率14
3.4.4铸造圆角14
3.4.5芯头15
3.5浇注系统19
4装备设计21
4.1造型21
4.2模样22
4.3芯盒24
4.4砂箱24
4.5型砂的成分和比例24
5总结25
参考文献27
致谢28
连接盘铸造工艺设计
1引言
铸造是人类掌握比较早的一种金属热加工工艺,已有约6000年的历史。
中国约在公元前1700~前1000年之间已进入青铜铸件的全盛期,工艺上已达到相当高的水平。
铸造是指将室温中为液态但不久后将固化的物质倒入特定形状的铸模待其凝固成形的加工方式。
被铸物质多为原为固态但加热至液态的金属(例:
铜、铁、铝、锡、铅等),而铸模的材料可以是沙、金属甚至陶瓷。
因应不同要求,使用的方法也会有所不同.
铸造-熔炼金属,制造铸型,并将熔融金属浇入铸型,凝固后获得具有一定形状、尺寸和性能金属零件毛坯的成型方法
铸造是将金属熔炼成符合一定要求的液体并浇进铸型里,经冷却凝固、清整处理后得到有预定形状、尺寸和性能的铸件的工艺过程。
铸造毛坯因近乎成形,而达到免机械加工或少量加工的目的降低了成本并在一定程度上减少了制作时间.铸造是现代装置制造工业的基础工艺之一。
铸造可按金属液的浇注工艺分为重力铸造和压力铸造。
重力铸造是指金属液在地球重力作用下注入铸型的工艺,也称浇铸。
广意的的重力铸造包括砂型浇铸、金属型浇铸、熔模铸造,泥模铸造等;窄义的重力铸造专指金属型浇铸。
压力铸造是指金属液在其他外力(不含重力)作用下注入铸型的工艺。
广义的压力铸造包括压铸机的压力铸造和真空铸造、低压铸造、离心铸造等;窄义的压力铸造专指压铸机的金属型压力铸造,简称压铸。
这几种铸造工艺是目前有色金属铸造中最常用的、也是相对价格最低的。
砂型铸造是一种以砂作为主要造型材料,制作铸型的传统铸造工艺。
砂型一般采用重力铸造,有特殊要求时也可采用低压铸造、离心铸造等工艺。
砂型铸造的适应性很广,小件、大件,简单件、复杂件,单件、大批量都可采用。
砂型铸造用的模具,以前多用木材制作,通称木模。
旭东精密铸件厂为改变木模易变形、易损坏等弊病,除单件生产的砂型铸件外,全部改为尺寸精度较高,并且使用寿命较长的铝合金模具或树脂模具。
虽然价格有所提高,但仍比金属型铸造用的模具便宜得多,在小批量及大件生产中,价格优势尤为突出。
此外,砂型比金属型耐火度更高,因而如铜合金和黑色金属等熔点较高的材料也多采用这种工艺。
但是,砂型铸造也有一些不足之处:
因为每个砂质铸型只能浇注一次,获得铸件后铸型即损坏,必须重新造型,所以砂型铸造的生产效率较低;又因为砂的整体性质软而多孔,所以砂型铸造的铸件尺寸精度较低,表面也较粗糙。
不过,旭东精密铸件厂集多年的技术积累,已大大改善了砂型铸件的表面状况,其抛丸后的效果可与金属型铸件媲美。
此次毕业设计目的是通过在铸造工艺分析的过程中梳理大学四年中学到的专业知识,学会发现问题并运用所学的知识来解决实际问题。
通过毕业设计巩固和拓展自己的专业知识,熟悉铸造工艺设计的流程,领略铸造工艺设计的要领,体验铸造工艺设计工作的内涵,为即将步入社会,走向工作岗位做最后的准备。
课题背景
铸造是金属成形的一种最主要方法,它是热加工的基础。
铸造的历史与华夏文明的历史一样悠久,我们的祖先在4000多年前就铸造出了“三星堆”那样精美的青铜器,其技术水平令人叹为观止,然而到了现代,作为全球铸件产量第一大国,中国的铸造水平却落后于发达国家。
早期
中国商朝的重875公斤的司母戊方鼎,战国时期的曾侯乙尊盘,西汉的透光镜,都是古代铸造的代表产品。
早期的铸件大多是农业生产、宗教、生活等方面的工具或用具,艺术色彩浓厚。
那时的铸造工艺是与制陶工艺并行发展的,受陶器的影响很大。
发展
中国在公元前513年,铸出了世界上最早见于文字记载的铸铁件-晋国铸型鼎,重约270公斤。
欧洲在公元八世纪前后也开始生产铸铁件。
铸铁件的出现,扩大了铸件的应用范围。
例如在15~17世纪,德、法等国先后敷设了不少向居民供饮用水的铸铁管道。
18世纪的工业革命以后,蒸汽机、纺织机和铁路等工业兴起,铸件进入为大工业服务的新时期,铸造技术开始有了大的发展。
近代
进入20世纪,铸造的发展速度很快,其重要因素之一是产品技术的进步,要求铸件各种机械物理性能更好,同时仍具有良好的机械加工性能;另一个原因是机械工业本身和其他工业如化工、仪表等的发展,给铸造业创造了有利的物质条件。
如检测手段的发展,保证了铸件质量的提高和稳定,并给铸造理论的发展提供了条件;电子显微镜等的发明,帮助人们深入到金属的微观世界,探查金属结晶的奥秘,研究金属凝固的理论,指导铸造生产。
我国铸造业的概况
我国铸件产量从2000年起超越美国已连续6年位居世界第一,其中2004年为2242万吨,2005年估计为2600万吨,铸件年产值超过2500亿元,铸件产量占世界总产量的1/4之多,已成为世界铸造生产基地。
根据全球主要铸件生产国2004年的产量统计可以看出,十大铸件生产国可分为两类。
一类是发展中国家,虽然产量大,但铸件附加值低,小企业多,从业人员队伍庞大,黑色金属比重大。
另一类是发达国家,如日本、美国及欧洲等,他们采用高新技术主要生产高附加值铸件。
发达国家总体上铸造技术先进、产品质量好、生产效率高、环境污染小、原辅材料已形成系列化。
欧洲已建立跨国服务系统,生产实现机械化、自动化、智能化。
生产过程从严执行技术标准,铸件废品率约为2%—5%。
重视用信息化提升铸造工艺设计水平,普遍应用软件进行充型凝固过程模拟和工艺优化设计。
从批量和劳动生产率看,欧、美、日的优势很大,日本的劳动生产率是人均年产铸件140吨,我国估计约为20吨,相差7倍。
我国人工成本低于1美元/小时,与发达国家相差几十倍,因而出口铸件具有优势。
但近年来材料价格猛涨,使我国出口铸件在材料成本方面的优势消失殆尽。
在产品质量和档次方面,我们远落后于发达国家。
近年我国铸件出口虽有所增长,但出口只占我国总产量的97%,占世界铸件市场流通量不到8%,总体增速缓慢,表现为质量较差、价格低。
长期以来,出口的铸件以中低档产品为主,各类管件、散热器、厨具及浴具占到36%。
一些出口铸件虽可达到国际标准,但要达到欧美客户标准还有距离。
在国内,铸造业是关系国计民生的重要行业,是汽车、石化、钢铁、电力、造船、纺织、装备制造等支柱产业的基础,是制造业的重要组成部份。
在机械装备中,铸件占整机重量的比例很高,内燃机占80%、拖拉机占50%—80%、液压件、泵类机械占50%—60%。
汽车中的关键部件几乎全部铸造而成;冶金、矿山、电站等重大设备都依赖于大型铸锻件,铸件的质量直接影响着整机的质量和性能。
我国铸造生产企业主要分布在东部,西部产量较少。
目前全国铸造企业约有24000家、从业人员约120多万。
从产业结构看,既有从属于主机生产厂的铸造分厂或车间,也有专业铸造厂,还有大量的乡镇铸造厂。
就规模和水平而言,既有工艺先进、机械化程度高、年产数万吨铸件的大型铸造厂,如重型行业、汽车行业、航空工业的一些先进的铸造厂;也有工艺落后、设备简陋、手工操作,年产铸件百余吨的小型铸造厂。
发达国家铸造技术发展现状
发达国家总体上铸造技术先进、产品质量好、生产效率高、环境污染少、原辅材料已形成商品化系列化供应,如在欧洲已建立跨国服务系统。
生产普遍实现机械化、自动化、智能化(计算机控制、机器人操作)。
铸铁熔炼使用大型、高效、除尘、微机测控、外热送风无炉衬水冷连续作业冲天炉,普遍使用铸造焦,冲天炉或电炉与冲天炉双联熔炼,采用氮气连续脱硫或摇包脱硫使铁液中硫含量达0.01%以下;熔炼合金钢精炼多用AOD、VOD等设备,使钢液中H、O、N达到几个或几十个10-6的水平。
在重要铸件生产中,对材质要求高,如球墨铸铁要求P≯0.04%、S≯0.02%,铸钢要求P、S均≯0.025%,采用热分析技术及时准确控制C、Si含量,用直读光谱仪2~3分钟分析出十几个元素含量且精度高,C、S分析与调控可使超低碳不锈钢的C、S含量得以准确控制,采用先进的无损检测技术有效控制铸件质量。
普遍采用液态金属过滤技术,过滤器可适应高温诸如钴基、镍基合金及不锈钢液的过滤。
过滤后的钢铸件射线探伤A级合格率提高13个百分点,铝镁合金经过滤,抗拉强度提高50%、伸长率提高100%以上。
广泛应用合金包芯线处理技术,使球铁、蠕铁和孕育铸铁工艺稳定、合金元素收得率高、处理过程无污染,实现了微机自动化控制。
铝基复合材料以其优越性能被广泛重视并日益转向工业规模应用,如汽车驱动杆、缸体、缸套、活塞、连杆等各种重要部件都可用铝基复合材料制作,并已在高级赛车上应用;在汽车向轻量化发展的进程中,用镁合金材料制作各种重要汽车部件的量已仅次于铝合金。
采用热风冲天炉、两排大间距冲天炉和富氧送风,电炉采用炉料预热、降低熔化温度、提高炉子运转率、减少炉盖开启时间,加强保温和实行微机控制优化熔炼工艺。
在球墨铸铁件生产中广泛采用小冒口和无冒口铸造。
铸钢件采用保温冒口、保温补贴,工艺出品率由60%提高到80%。
考虑人工成本高和生产条件差等因素而大量使用机器人。
由于环保法制严格(电炉排尘有9国规定100-250mg/m3、冲天炉排尘,11国规定100-1000mg/m3,或0.25-1.5kg/t铁液;砂处理排尘,8国规定100-250mg/m3。
),铸造厂都重视环保技术。
在大批量中小铸件的生产中,大多采用微机控制的高密度静压、射压或气冲造型机械化、自动化高效流水线湿型砂造型工艺。
砂处理采用高效连续混砂机、人工智能型砂在线控制专家系统,制芯工艺普遍采用树脂砂热、温芯盒法和冷芯盒法。
熔模铸造普遍用硅溶胶和硅酸乙酯做粘结剂的制壳工艺。
用自动化压铸机生产铸铝缸体、缸盖;已经建成多条铁基合金低压铸造生产线。
用差压铸造生产特种铸钢件。
所生产的各种口径的离心球墨铸铁管占铸铁管总量95%以上,球铁管占球铁年产量30%-50%。
成功地采用EPC技术大批量生产汽车4缸缸体、缸盖等复杂铸件,生产率达180型/小时。
在工艺设计、模具加工中,采用CAD/CAM/RPM技术;在铸造机械的专业化、成套化制备中,开始采用CIMS技术。
铸造生产全过程主动、从严执行技术标准,铸件废品率仅2%-5%;标准更新快(标龄4-5年);普遍进行ISO9000、ISO14000等认证。
重视开发使用互联网技术,纷纷建立自己的主页、站点。
铸造业的电子商务、远程设计与制造、虚拟铸造工厂等飞速发展。
2设计任务
2.1铸造工件图
铸件的cad三维图如下:
图2.1a铸造工件主视图
图2.1b零件三维图
图2.1c零件三维图
连接盘材料为HT200,采用砂型铸造,年生产量200件
2.2分析生产性质
(1)该零件属小批生产,零件上φ60mm的孔要铸出,需用一个型芯。
(2)四个φ12mm的小孔可不铸出,铸后再用机械加工出该孔,铸造工艺图上的不铸出孔用红线打叉
3工艺分析
3.1铸造工艺图
图3.1铸造工艺图
铸造工艺图是铸造行业所特有的一种图纸,它规定了铸件的形状和尺寸,也规定了铸件的基本生产方法和工艺过程。
单件,小批量的生产情况下,用规定画法,以便模具制造,造型,检验和技术存档。
铸造生产时,首先要根据铸件的结构特征、技术要求、生产批量、生产条件等因素,确定铸造工艺方案。
其主要内容包括浇注位置、分型面、铸造工艺参数(机械加工余量、起模斜度、铸造圆角、收缩率、芯头等)的确定,然后用规定的工艺符号或文字绘制成铸造工艺图。
铸造工艺图是生产过程的指导性文件,它为设计和指导铸造工艺设备提供了基本依据。
3.2浇注位置
此处省略 NNNNNNNNNNNN字。
如需要完整说明书和设计图纸等.请联系 扣扣:
九七一九二零八零零另提供全套机械毕业设计下载!
该论文已经通过答辩
(2)铸件的大平面朝下或倾斜浇注。
由于浇注时炽热的金属液对铸型的上部有强烈的热辐射,引起顶面型砂膨胀拱起甚至开裂,使大平面出现夹砂、砂眼等缺陷。
大平面朝下或采用倾斜浇注的方法可避免大平面产生铸造缺陷。
下图为平板铸件的浇注位置。
(3)铸件的薄壁朝下、侧立或倾斜。
为防止铸件的薄壁部位产生冷隔、浇不到缺陷,应将面积较大的薄壁置于铸件的下部,或使其处于侧壁或倾斜位置.
(4)铸件的厚大部分应放在顶部或在分型面的侧面。
主要目的是便于在厚处安放冒口进行补缩
图3.2浇注系统
3.3分型面
分型面:
是铸型组元间的接合面。
为便于起模,一般分型面选择在铸件的最大截面处。
分型面的选定应保证起模方便、简化铸造工艺、保证铸件的质量。
确定分型面应遵循如下原则。
(1)分型面应选择在模样最大截面处,以便于起模。
(2)尽量减少分型面。
(3)尽量使分型面平直。
(4)尽量使铸件的全部或大部分位于同一砂箱中。
(5)尽量使型芯位于下箱,并注意减低砂箱的高度。
依据分型面应选择在模样最大截面处,以便于起模。
尽量减少分型面尽量使分型面平直。
尽量使铸件的全部或大部分位于同一砂箱中。
尽量使型芯位于下箱,并注意减低砂箱的高度几点铸件的分型面如下图
图3.3分型面
3.4工艺参数的选定
3.4.1机械加工余量和公差
机械加工余量:
是指铸件加工面上预留的、准备切除的金属层厚度。
加工余量取决于铸件的精度等级,与铸件材料、铸造方法、生产批量、铸件尺寸、浇注位置等因素有关。
铸件的尺寸公差CT,其精度等级从高到低有1、2、3......16共16个等级;加工余量等级MA,从精到粗可分为A、B、C、D、E、F、G、H、J共9个级别。
下表为砂型铸造常用铸造合金单件和小批生产时公差等级及与之配套的加工余量等级。
铸件的公差等级和加工余量等级确定后,加工余量数值可根据GB/T11350-1989选取;公差的数值可按GB6414—86选取
铸件最大尺寸
浇注时位置
加工面与基准面之间的距离
<50
50-120
120-260
260-500
500-800
800-1250
<120
顶面底,侧面
3.5-4.52.5-3.5
4.0-4.53.0-3.5
120-260
顶面底侧面
4.0-5.03.0-4.0
4.5-5.03.5-4.0
5.0-5.54.0-4.5
260-500
顶面底侧面
4.5-6.03.5-4.5
5.0-6.04.0-4.5
6.0-7.04.5-5.0
6.5-7.05.0-6.0
500-800
顶面底侧面
5.0-7.04.0-5.0
6.0-7.04.5-5.0
6.5-7.04.5-5.5
7.0-8.05.0-6.0
7.5-9.06.5-7.0
800-1250
顶面底侧面
6.0-7.04.0-5.5
6.5-7.55.0-5.5
7.0-8.05.0-6.0
7.5-8.05.5-6.0
8.0-9.05.5-7.0
8.5-106.5-7.5
表3.4.1铸件加工余量
3.4.2起模斜度
起模斜度:
为使模样(或型芯)易从铸型(或芯盒)中取出,在模样(或芯盒)上与起模方向平行的壁的斜度称为起模斜度,可用角度α或宽度a表示,提倡使用宽度a。
模样的起模斜度可采用增加壁厚、加减壁厚、减小壁厚三种取法。
图3.4.2工件的起模斜度与加工余量
起模斜度需要增减的数值可按有关标准选取,采用粘土砂造型时的起模斜度可按JB/T5105—1991确定。
一般木模的斜度α=0.3°~3°,a=0.6~3.0mm;金属模的斜度α=0.2°~2°,a=0.4~2.4mm。
模样越高,斜度越小。
当铸件上的孔高度与直径之比小于1(H/D<1)时,可用自带芯子的方法铸孔,用自带芯子的起模斜度一般应大于外壁斜度。
见下表
测量面高度(毫米)
金属模
木模
a(毫米)
α°
a(毫米)
α°
<20
0.5-1.0
1°30′-3°
0.5-1.0
1°30′-3°
20-50
0.5-1.2
0°45′-2°
1.0-2.0
1°30′-2°30′
50-100
1.0-1.5
0°45′-1°
1.5-2.0
1°-1°30′
100-200
1.5-2.0
0°30′-0°45′
2.0-2.5
0°45′-1°
表3.4.2砂芯铸造用起模斜度
3.4.3收缩率
收缩率:
为补偿铸件在冷却过程中产生的收缩,使冷却后的铸件符合图样的要求,需要放大模样的尺寸,放大量取决于铸件的尺寸和该合金的线收缩率。
一般中小型灰铸铁件的线收缩率约取1%;非铁金属的铸造收缩率约取1.5%;铸钢件的铸造收缩率约取2%。
3.4.4铸造圆角
铸造圆角:
模样壁与壁的连接和转角处要做成圆弧过渡,称为铸造圆角。
铸造圆角可减少或避免砂型尖角损坏,防止产生粘砂、缩孔、裂纹。
但铸件分型面的转角处不能有圆角。
铸造内圆角的大小可按相邻两壁平均壁厚的1/3~1/5选取,外圆角的半径取内圆角的一半。
3.4.5芯头
芯头:
是指砂芯的外伸部分,用来定位和支承砂芯。
芯头有垂直和水平芯头两种。
芯座是指铸型中专为放置芯头的空腔。
芯头和芯座尺寸主要有芯头长度L(高度H)、芯头斜度α、芯头与芯座装配隙s等,其数值与型芯的长度(高度)和直径有关
图4.4.5A垂直芯头高度h和h1
L
当D或(A+B)/2为下列数值时的高度h
≤30
31-60
61-100
101-150
≤30
15
15-20
—
—
31-50
20-25
20-25
20-25
—
51-100
25-30
25-30
25-30
20-25
101-150
30-35
30-35
30-35
25-30
表3.4.5A垂直芯头高度h和h1
由h查h1
下芯头高度h
15
20
25
30
35
40
45
50
55
60
上芯头高度h1
15
15
15
20
20
25
25
30
30
35
表3.4.5B由h查h1
图3.4.5B垂直芯头的斜度α
芯头高度h
15
20
25
30
35
40
50
60
70
用α/h表示斜度时
用角度α表示时
上芯头
2
3
4
5
6
7
9
11
12
1/5
10°
下芯头
1
1.5
2
2.5
3
3.5
4
5
6
1/10
5°
表3.4.5C垂直芯头的斜度α
铸型种类
D或(A+B)/2
≤50
51-100
101-150
151-200
201-300
301-400
401-500
501-700
湿型
0.5
0.5
1.0
1.0
1.5
1.5
2.0
2.0
干型
0.5
1.0
1.5
1.5
2.0
2.5
3.0
3.5
表3.4.5D垂直芯头与芯座之间的间隙s
由连接盘的铸件图以及查上表可知型芯直径为L=38mm长度为120mm上芯头高度为h1=15MM下芯头为h=25MM,s=0.5.上芯头斜度7.5°下芯头斜度为4.5°,如图:
图3.4.5C芯头尺寸
3.5浇注系统
浇注系统是砂型中引导液态合金流入型腔的通道。
生产衬套中常常因浇注系统设计安排不当,造成砂眼、夹砂、粘砂、夹渣、气孔、铁豆、抬箱、缩孔、松孔、缩松、冷隔、浇不足、变形、裂纹、偏折等铸造缺陷。
此外,浇注系统的好坏影响造型和清理工作的繁简,砂型的体积大小和型砂的耗用运输量,非产生性消耗的液态合金用量等等。
所以,浇注系统与获得优质铸件,提高生产效率和降低铸件成本的关系是密切相联的。
因此对浇注系统的设计必须慎重认真。
常用的浇注系统大多由浇口杯(外浇口)、直浇道、横浇道、内浇道等部分组成。
正确的浇注应该:
1)使液态铸铁平稳充满砂型,不冲击型壁和砂芯,不产生激溅和涡流,不卷入气体,并顺利的让型腔内的空气和其他气体排出型外,以防止金属过渡氧化及产生砂眼、铁豆、气孔等缺陷。
2)阻挡夹杂物进入型腔,以免在铸件上形成渣孔。
3)调节砂型及铸件上各部分温差,控制铸件的凝固顺序,不阻碍铸件的收缩,减