管道及阀门检修工艺规程.docx
《管道及阀门检修工艺规程.docx》由会员分享,可在线阅读,更多相关《管道及阀门检修工艺规程.docx(25页珍藏版)》请在冰豆网上搜索。
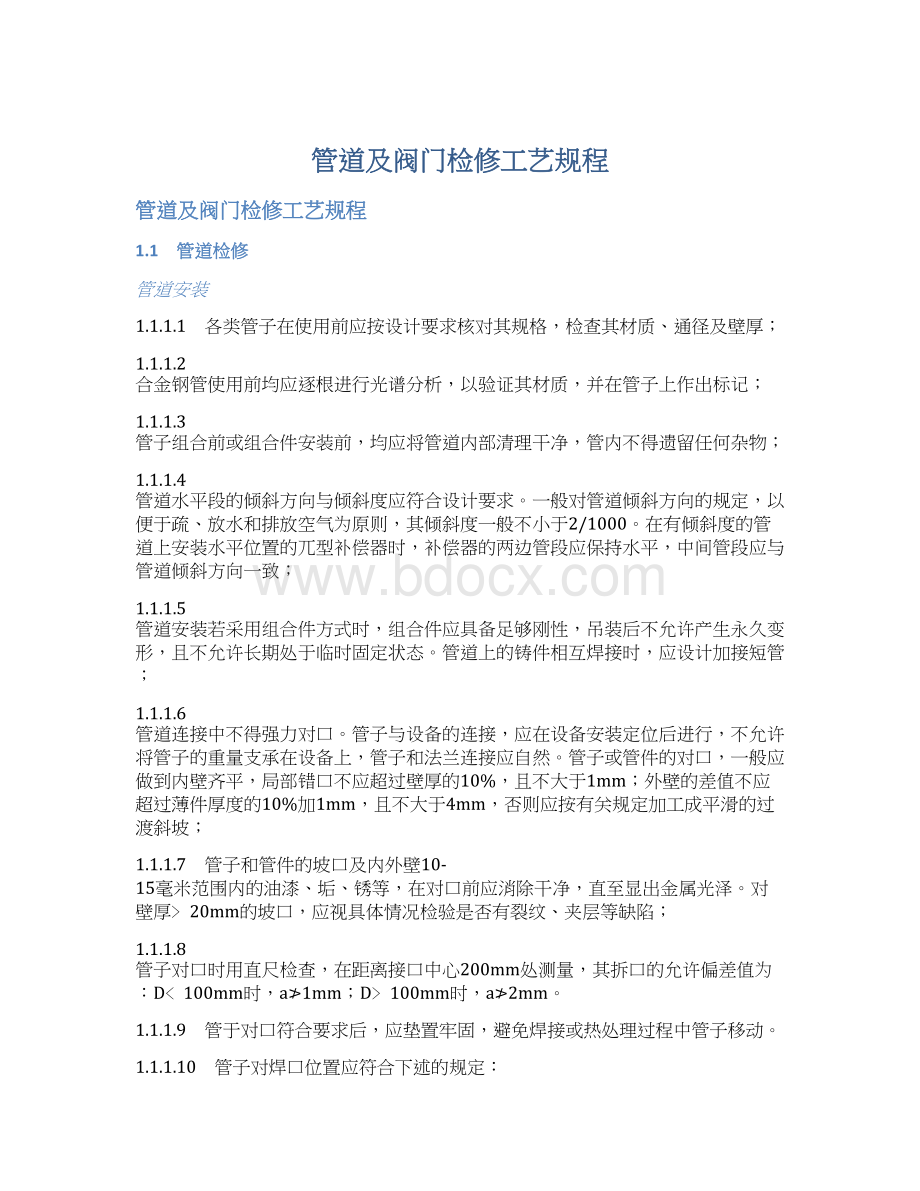
管道及阀门检修工艺规程
管道及阀门检修工艺规程
1.1 管道检修
管道安装
1.1.1.1 各类管子在使用前应按设计要求核对其规格,检查其材质、通径及壁厚;
1.1.1.2 合金钢管使用前均应逐根进行光谱分析,以验证其材质,并在管子上作出标记;
1.1.1.3 管子组合前或组合件安装前,均应将管道内部清理干净,管内不得遗留任何杂物;
1.1.1.4 管道水平段的倾斜方向与倾斜度应符合设计要求。
一般对管道倾斜方向的规定,以便于疏、放水和排放空气为原则,其倾斜度一般不小于2/1000。
在有倾斜度的管道上安装水平位置的兀型补偿器时,补偿器的两边管段应保持水平,中间管段应与管道倾斜方向一致;
1.1.1.5 管道安装若采用组合件方式时,组合件应具备足够刚性,吊装后不允许产生永久变形,且不允许长期处于临时固定状态。
管道上的铸件相互焊接时,应设计加接短管;
1.1.1.6 管道连接中不得强力对口。
管子与设备的连接,应在设备安装定位后进行,不允许将管子的重量支承在设备上,管子和法兰连接应自然。
管子或管件的对口,一般应做到内壁齐平,局部错口不应超过壁厚的10%,且不大于1mm;外壁的差值不应超过薄件厚度的10%加1mm,且不大于4mm,否则应按有关规定加工成平滑的过渡斜坡;
1.1.1.7 管子和管件的坡口及内外壁10-15毫米范围内的油漆、垢、锈等,在对口前应消除干净,直至显出金属光泽。
对壁厚﹥20mm的坡口,应视具体情况检验是否有裂纹、夹层等缺陷;
1.1.1.8 管子对口时用直尺检查,在距离接口中心200mm处测量,其拆口的允许偏差值为:
D﹤100mm时,a≯1mm;D﹥100mm时,a≯2mm。
1.1.1.9 管于对口符合要求后,应垫置牢固,避免焊接或热处理过程中管子移动。
1.1.1.10 管子对焊口位置应符合下述的规定:
a)管子接口距离弯管的弯曲起点不得小于管子外径,且不少于100mm;
b)两对接焊缝中心线间距离不得小于管子的外径,且不少于150mm;
c)管子接口应布置支吊架,接口距离支吊架边缘不得少于50mm。
对于焊后需作热处理的接口,该距离不得小于焊缝宽度的5倍,且不少于100mm;
d)管道焊口应避开疏放水及仪表管等开孔位置,一般距开孔的边缘不得少于50mm,且不得小于孔径。
管道穿过墙壁、楼板时,位于隔板内的管段不得有焊口。
见图76
图1 管子对中图
1.1.1.11 热力管道冷拉必须符合设计规定,更换管道应保持原设计值,进行冷拉前应检查:
e)冷拉区域各固定端安装牢固,各固定支架间所有焊口(冷拉器除外)焊接完毕并经检验合格,应作热处理的焊口亦作过热处理;
f)所有支吊架已装设完毕,冷拉器附近吊架的吊杆应预留足够的调整裕量,支吊架弹簧应按设计值预压缩并临时固定,不便弹簧承担管子载荷;
g)管道倾斜方向及倾斜度均符合设计要求;
h)法兰与阀门的联接螺栓已拧紧,管道冷拉后,焊口须经检验合格,应作热处理的焊口须作过热处理,方可拆除拉具。
1.1.1.12 管道敷设应整齐美观;
1.1.1.13 波形补偿器应按规定进行拉伸或压缩,与设备相连的补偿器,应在设备最终固定后方可连接,以减小应力。
管道附件
1.1.1.14 管道附件包括:
阀门、法兰及连接件、三通、弯头、大小头、波形补偿器、π型补偿器、流量孔板、流量喷嘴、节流孔板等。
1.1.1.15 各类管道附件使用前一般均应查明其规格、材质(或型号),公称通径和公称压力应符合设计规定。
当工作压力大于2.5MPa或工作温度大于300℃的管道施工前,对所使用的管道附件须核对出厂证件,并确认下列项目均符合国家或部颁的技术标准:
i)直接与管子焊接的附件化学成份;
j)压力大于或等于6.4MPa的承压附件(包括铸、锻、焊制件)热处理后的机械性能;
k)合金钢附件(包括铸、锻、焊制件)的金相分析结果(亦可用热处理状态说明代替),工作温度≥500℃且直径≥30mm的合金螺栓的硬度检查结果。
1.1.1.16 所有合金钢附件(阀门内部合金钢部件除外),不论有无制造厂出厂技术证件,安装前均应进行光谱复查,并由检修人员在附件上作出标志;
1.1.1.17 各异形制件(包括铸、锻、焊制件)及阀门应作外观检查,表面不应有粘砂、裂纹缩孔、折迭、夹渣、漏焊等除低强度和严密性的缺陷;
1.1.1.18 对法兰的要求:
l)法兰密封表面应光洁,不得有径向沟槽,且不得有气孔、裂纹、毛刺或其它降低强度和连接可靠性的缺陷;
m)带有凹凸面或凹凸环的法兰应能自然嵌合。
凸面的高度不得小于凹槽的深度;
n)法兰端面上联接螺栓的支承部位应与法兰接合面平行,以保证法兰连接时端面受力均匀;
1.1.1.19 螺栓与螺母的螺纹应完整、无伤痕、毛刺或断丝等缺陷。
螺栓与螺母应配合良好,无松动或卡涩现象;
1.1.1.20 对垫片要求:
o)法兰的垫片材料应符合设计要求;
p)石棉橡胶质垫片要求质地柔韧,无老化变质现象,表面不应有折损、皱纹等缺陷;
q)金属质垫片(平垫片及齿形垫片)的表面用平尺检查应接触。
垫片无裂纹、毛刺凹槽及粗糙加工缺陷,其硬度以低于法兰硬度为宜。
1.1.1.21 对阀门的要求:
r)各类阀门使用前应检查填料用料是否符合设计要求,填装方法是否正确,填料密封处的阀杆有无锈蚀,阀门开闭是否灵活,指示是否正确;
s)使用前必须进行严密性试验,检查阀座与阀芯、阀盖及填料室各结合面的严密性;
1.1.1.22 阀门使用前一般应解体,下列阀门使用前必须解体,检查检修合格后方可使用:
t)用于工作温度<450℃的阀门;
u)安全门和节流门(除制造厂有特殊规定者外);
v)严密性试验不合格的阀门。
1.1.1.23 管道上装有流量孔板、流量喷嘴或节流孔板者,应在管道冲洗后再行安装,安装时应配合热工人员进行检查,其孔径、几何尺寸和方向均应正确,孔板或喷嘴不得有碰伤等缺陷。
弯管
1.1.1.24 弯管前,应先做好样板,注意核实管子材质、规格,一般应选取管壁厚带有正公差的无缝钢管。
弯管前管道内应灌海砂或河砂,砂中应不含泥土和可燃性杂物,灌砂前砂要烘干,砂的粒度应根据管径选用,灌砂时必须充填捣实,再用木楔楔紧;
1.1.1.25 弯管时,对小管径的管子应在牢固的平台上进行,大管径应在弯管场进行。
弯曲半径应符合图纸要求,无明确规定时,弯曲半径必须大于管外径的3.5倍。
热弯弯头的加热温度不得超过1050℃,其最底温度:
碳钢为700℃,合金钢为800℃,且满足下列要求:
w)升温应均匀,使管壁、砂子升温一致;
x)加热长度L=πRα/180。
式中:
R—弯曲半径,π—圆周率,α—弯曲角度
y)热弯管道加热后,动作必须迅速、平衡地一次弯成,一个弯头的加热次数不允许超过三次(合金钢要求一次弯成)。
加热部分不允许锤击,弯好的弯头应保温,使其缓慢冷却,弯制过程严禁浇水冷却。
1.1.1.26 弯制好的弯头应圆滑,无分层、过烧、凹痕、裂纹等缺陷且满足如下要求:
zz)弯头弯曲部分的椭圆度:
β=(α1-α2)/α
β≤6%(对公称压力≥9.8MPa管道)
β≤7%(对公称压力≥9.8MPa管道)
式中:
α1—截面上测得最大外径
α2—同一截面上测得最小外径
α0—公称外径
aa)弯管外弧部分实测壁厚不得小于设计值壁厚。
1.1.1.27 最后,用压缩空气吹净弯头内的砂子及杂质。
对合金钢的弯头应根据材质进行热处理,处理后进行探伤及硬度检查。
管子支吊架
1.1.1.28 支吊架的种类包括:
bb)固定支架:
该种支架不仅承担管道的重量,而且还承担管道因受温度、压力变化所产生的附加力。
因此,在固定支架时,一定要保证托架和管箍跟管紧密接触,并且把管子卡紧,以防止管子转动、窜动,使之成为管道膨胀的死点。
不得在没有补偿装置的直管段上安两个固定支架;
cc)导向支架:
各零件应完整、牢固,导向槽内应清洁,在热态下能沿纵向自由移动。
导向支架和滑动支架的滑动面应不裸露并清理干净,滑动件与支承件接触良好,保证管道能自由膨胀,膨胀指示器应按规定正确装设,指示灵活准确,不得在管子和支座间塞垫块;
dd)弹簧支架。
支架下的支承结构应重直于作用力的方向。
调整弹簧压紧螺杆时,应保持管道水平。
按设计调整弹簧的压缩值,并作记录。
弹簧应完整不歪斜,无裂纹、变形等缺陷,弹簧弹性应良好。
运行中弹簧压缩量不应超过最大允许值90%;
ee)吊架。
吊架应焊接牢固,吊杆与管道应垂直。
弹簧及吊、拉杆应能承受管道的全部重量,并能消除或减少因介质流动而产生的管道振动。
1.1.1.29 支吊架的更换或安装步骤:
ff)支吊架安装前检查材质、规格、组装尺寸应符合设计要求;
gg)在混凝土柱上装设支架时,应将混凝土抹面层凿去后固定;
hh)管道支架应牢固完整,吊杆受力均布;
ii)安装管道支架的活动零件和吊架时应考虑管道的热位移,一般应向膨胀方向偏移一定的距离,其偏移位置应处于全部热位移的一半;
jj)导向架和滑动支架的滑动面应不裸露并清理干净;
kk)固定支吊架应按设计施工,不得在装有补装置的支管段上安装两个固定支架。
管道系统的严密性试验
1.1.1.30 各类管道安装完毕后应进行系统严密性试验,以检查各连接部位(焊缝、法兰接口)的严密性。
管道系统进行严密性水压试验前应做到:
ll)结束支吊架安装工作;
a)结束焊接和热处理工作,并已检验合格;
b)试验用压力表计经校验正确;
c)有严密性试验的技术、安全和组织措施。
1.1.1.31 管道严密性试验一般采用水压,其水质应洁净,灌水应保证能将系统内空气排尽。
试验压力应按设计图纸的规定,一般试验压力为工作压力的1.25倍,但不得小于0.2MPa。
对埋入地下的压力钢管,不得小于0.4MPa。
对主给水管道,以给水泵出口所能达到的最大压力的1.25倍作为试验压力。
1.1.1.32 管道系统在严密性试验时,对焊缝及其它应作检查的部位不能保温。
管道系统进行严密性试验时,应与运行中的管道隔绝,一般应装堵板。
如果以阀门隔绝时,阀门两侧温差不允许超过100℃。
若环境温度低于5℃。
的情况下进行水压试验时,必须根据具体情况,当压力达到试验压力后应保持5分钟,然后降至工作压力进行全面检查,无渗漏现象,即认为试验合格。
1.1.1.33 在管道进行严密性试验过程中,如发现泄漏,应降压消除缺陷后再进行试验。
结束试压后,应立即排尽系统内的全部存水。
管道的保温
1.1.1.34 管道的表面保温,不仅可减少热损失,减小管道内外壁温差,而且可防止其高温对电气设备仪表的影响和干扰;同时还可改善运行环境,防止人身烫伤事故。
1.1.1.35 管道保温注意事项:
d)保温前应对焊口、吊架、托架、伸缩节等部位仔细检查,承压管道新焊口处的保温工作必须在水压试验后进行;
e)管道上的温度计、插座、热工取样点分线盒、丝堵及铭牌等,保温时应留在外面。
在蠕胀测点、温度测点等处应采用活动保温结构,在活动支架与固定设备接触处应留出20mm-30mm间隙,以便于检修和拆换。
主蒸气、主给水管道焊口处保温应作出标记,便于检查焊口时,能准确地拆除保温层;
f)对500℃以上的管道,每隔3-4米留出10mm-15mm的伸缩缝,弯管的中心处留出20mm-30mm伸缩缝,伸缩缝内嵌入石棉绳,然后再涂上一层薄灰并压紧抹光;
g)对垂直布置的管道,每隔三米高度装设分段承重托架来支持保温层荷重,托架的宽度比保温层厚度小10mm—15mm;
h)位于油箱、油管、法兰附近的高温管道除保温完好外,一般要在外层包0.3mm—0.5mm厚的镀锌铁皮作保护层。
1.1.1.36 管道保温的工艺要求:
i)保温前应清除管道表面的锈垢,以保证保温层与管壁贴合良好;
j)高温大直径管道应采用两层保温砖,内层采用两半圆砖,外层采用120