品管意识与AQL.docx
《品管意识与AQL.docx》由会员分享,可在线阅读,更多相关《品管意识与AQL.docx(17页珍藏版)》请在冰豆网上搜索。
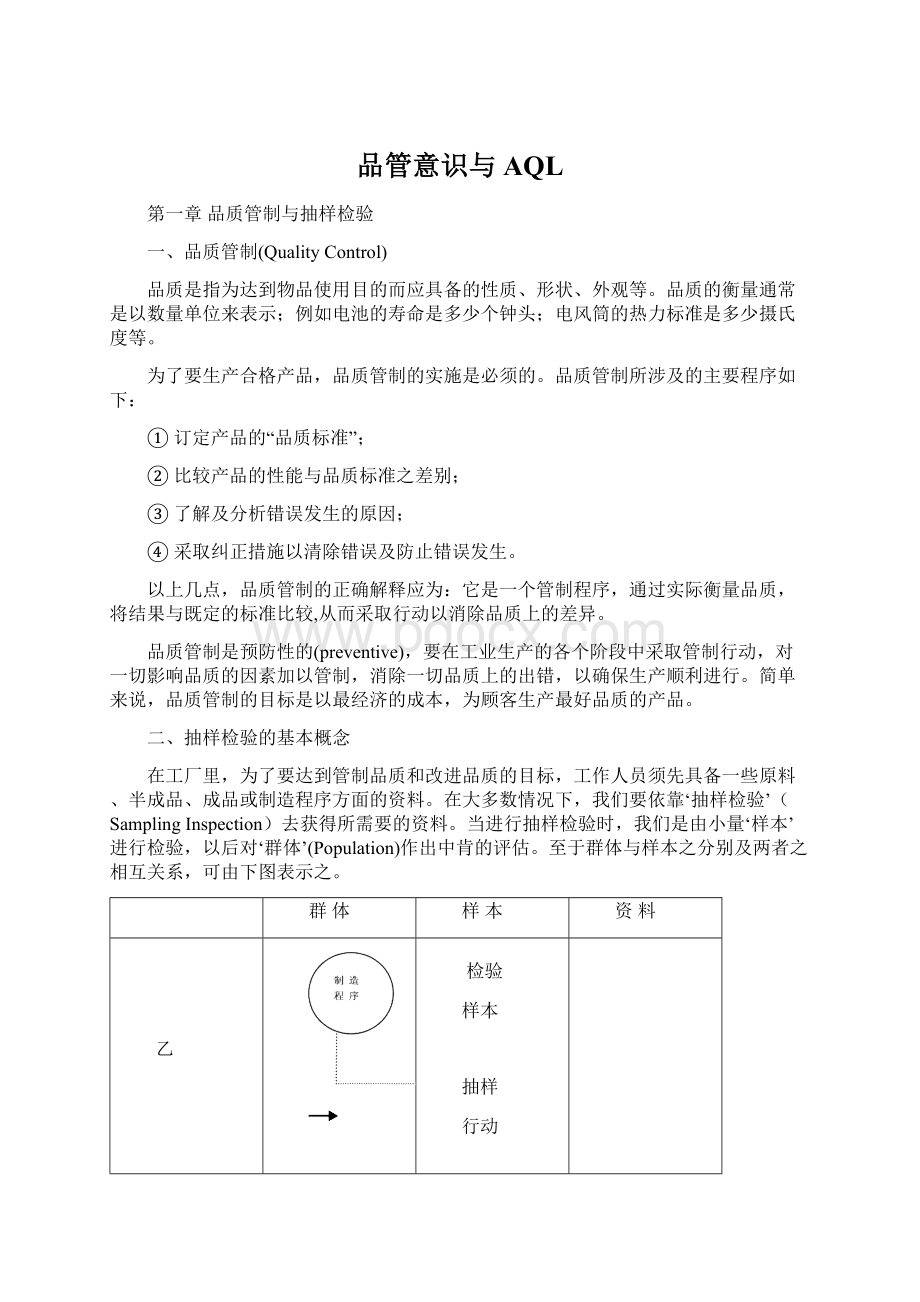
品管意识与AQL
第一章品质管制与抽样检验
一、品质管制(QualityControl)
品质是指为达到物品使用目的而应具备的性质、形状、外观等。
品质的衡量通常是以数量单位来表示;例如电池的寿命是多少个钟头;电风筒的热力标准是多少摄氏度等。
为了要生产合格产品,品质管制的实施是必须的。
品质管制所涉及的主要程序如下:
①订定产品的“品质标准”;
②比较产品的性能与品质标准之差别;
③了解及分析错误发生的原因;
④采取纠正措施以清除错误及防止错误发生。
以上几点,品质管制的正确解释应为:
它是一个管制程序,通过实际衡量品质,将结果与既定的标准比较,从而采取行动以消除品质上的差异。
品质管制是预防性的(preventive),要在工业生产的各个阶段中采取管制行动,对一切影响品质的因素加以管制,消除一切品质上的出错,以确保生产顺利进行。
简单来说,品质管制的目标是以最经济的成本,为顾客生产最好品质的产品。
二、抽样检验的基本概念
在工厂里,为了要达到管制品质和改进品质的目标,工作人员须先具备一些原料、半成品、成品或制造程序方面的资料。
在大多数情况下,我们要依靠‘抽样检验’(SamplingInspection)去获得所需要的资料。
当进行抽样检验时,我们是由小量‘样本’进行检验,以后对‘群体’(Population)作出中肯的评估。
至于群体与样本之分别及两者之相互关系,可由下图表示之。
群体
样本
资料
乙
检验
样本
抽样
行动
甲
检验
样本
抽样
行动
资料
图1群体,样本与资料间的相互关系
如图1甲所示,品管人员可从某‘批量’(LOT)中抽取一个样本去找出有关该批量的资料,其主要目的是评诂该批量的品质,而作出‘允收’(ACCEPTANCE)或‘拒收’(REJECTION)的决定。
如图1乙所示,品管人员亦可从某‘制造程序’(PROCESS)中抽取样本去得到有关该制造程序的资料,其主要目的是对程序作出评估,以决定是否需要调校。
与‘全数检验’比较,‘抽样检验’有以下优点:
1、检验的产品较少,符合经济原则;
2、在检验过程中,因搬运以致损坏的机会减少;
3、使用较少的检验员;
4、没有全数检验工作的单调;
5、适用于会因检验而受损坏的产品;
6、将全批产品拒收,强调产品品质需要不断改进。
虽然‘抽样检验’的优点很多,它亦有如下缺点:
1、有允收不良品或拒收良品的风险;
2、花费较多时间在策划及文件处理上。
比较之下,‘抽样检验’的优点远多于其缺点。
三、‘随机抽样’(RANDOMSAMPLING)及其他抽样方法
以上已论及‘抽样检验’的概念及其优缺点,然‘抽样’的方法有正确或不正确的分别。
正确的抽样方法有好几种,其中的‘随机抽样’最为重要。
随机抽样的意思是在执行随机抽样时,群体的每一份子(不论其所在位置)都有机会被抽中,而且每一份子都有相同抽中的机会。
严格说来,依据上述去进行随机抽样是很困难和不方便的,有时侯,真正的随机抽样是不可能的。
重要的是,品管人员应了解到‘随机抽样’与‘非随机抽样’的分别。
其实‘随机抽样’可以用下面简单图形表示。
批量样本
图2随机抽样
除了随机抽样外,比较重要的抽样方法有以下两种:
1、‘分层抽样’(STRATIFIEDSAMPLING)方法
有些时候,一个群体中可能存在若干个层面,如果品管人员预先认识到这点,然后对每一个层面都进行抽样,有如下图所示,这种抽样方法称为‘分层抽样’法。
批
量
样本
图3分层抽样
2、‘聚集抽样’(CLUSTERSAMPLING)方法
批
量样本
图4聚集抽样
在‘聚集抽样’中,品管人员集中抽取批量中某一部份作为样本,它的好处是简单及节省人力,缺点是当批量中组成份子分布不均匀时,会出现很大的误差。
四、抽样的误差(SAMPLINGERROR)
如果我们将抽样检验所得的资料和详细全数检验的结果作一比较,我们会发觉有某种程度的误差。
误差形成的原因有两种:
一种是无可避免的‘先天性’的误差,另外一种是人为的误差,然第二种误差是可以避免的。
如果我们应用‘随机抽样’和‘分层抽样’这些良好的抽样方法,误差会很小;否则,应用不良的抽样方法时误差会很大。
另一方面,‘抽样的误差’可以被分析为两类:
第一类误差被称为‘偏差’(BIAS);如图所示,甲乙两点间的距离便代表抽样结果的‘偏差’。
大偏差
样本之分布群体之分布
乙甲
甲=整体平均值
乙=样本平均值
小
乙甲
图五抽样结果的偏差(SAMPLINGBIAS)
第二类误差叫做‘离势’(DISPERSION)。
这个现象比较难于明白。
假设品管人员重复地向同一个‘群体’抽取很多个‘样本’;他会发现‘样本’之间有差异存在。
如果‘样本数’(SAMPLESIZE)大的话,差异会很小;否则,‘样本数’小的话,差异会较大。
对品管人员而言,明白以上的分别并不最重要;最重要的是需要理解到当抽样的工作做得好的话,抽样的结果便可靠(误差很小);如果抽样的工作做得不好,误差会很大,甚至引导管理人员作出错误的决定。
第二章逐批验收抽样检验(lot-to-lotacceptancesamplinginspection)
一、简介
‘逐批验收抽样’是最常见的抽样计划。
这类抽样是从每批产品抽出预定数目的样本,检验其品质性能。
如果不良品(defectives)的数目是少于所规定的,整批产品合格;反之,不良品高于某个预定的数目,整批产品会被拒收。
逐批验收抽样计划既可根据产品的不良品数目(numberofdefectives)而作出允收或拒收的决定;它亦可以根据产品的缺点数目(numberofdefects)作出有关的决定。
为了易于明白起见,本节将集中讨论找出不良品数目的抽样,但大家要认识到以下所讨论的同样适用于找出产品的缺点数的抽样。
二、验收抽样计划的种类
1、单次抽样检验(singlesamplinginspection)
单次抽样检验是从一批产品中抽出样本一次,根据检验结果来决定这批产品合格与否。
所有单次抽样计划可以用以下简单的‘流程图’(flowchart)表示。
其中N代表批量,n代表样本数,C代表允收数,d代表不良品数。
如d≤Cd>C
如
图6单次抽样计划流程图
2、二次抽样检验(Doublesamplinginspection)
二次抽样检验较为复杂。
先要进行首次抽样,从第一次抽样所得的资料,作出下面其中一项决定:
A允收整批产品
B拒收整批产品
C进行第二次抽样
如果需要进行第二次抽样,则以两次抽样加起来的数据才作出允收或拒收的决定。
所有二次抽样计划可以用以下的流程图表示。
在流程中:
N=批量n1=第一次样本数C1=首次允收数R1=首次拒收数
n2=第二次样本数C2=合共允收数R2=合共拒收数
d1≤C1d1≥R1
C1≤d1≤R1
d1+d2≤C2d1+d2>C2
3、多次抽样检验(multiplesamplinginspection)
‘多次抽样检验计划’是指那些要进行三次(或以上)的抽样才能作出允收决定的抽样计划。
在执行方面,它与二次抽样检验相拟,但更加复杂,一般在工厂中比较少应用,在此不进一步说明之。
三、批量的组成(formationoflots)
在品管中,批量通常是指检验批量(inspectiopnlot),它不一定等于制造批量(productionlot)或载运批量(shipmentlot)。
批量的组成会影响抽样计划的有效性。
批量的组成有两个重要的原则应注意到。
1、每批产品的来源应尽量是相同的;即是用相同的机器,相同的操作人员,及相同的物料生产的。
当产品的来源不同时,抽样计划的有效性会受影响;如果要采取纠正行动去消除不良品时,做起来比较困难。
2、由于‘样本数’的增加并非与批量的增加成比例,一般来说,批量愈大,抽样检验所需人力物力愈为经济。
四、样本的选择(selectionofsample)
抽样检验的样本须能代表整批产品。
理想的抽样计划都基于一个前提就是每件产品被抽取的机会都是相同的,亦即所谓随机抽样法,这在第一节里我们应该已有认识。
除非应用适当的抽样方法,否则抽样的误差是很大,例如某个检验人员知道最高一层的产品是最好的,而他又全部由这一层抽取样本检验,结果必然有偏差。
品管人员的责任是尽量使抽样的方法没有偏差。
五、生产者与顾客所胃之风险(producer`sandconsumer`srisk)
应用验收抽样计划时,在生产者方面来说,是希望所有良好的送验批量都被允收;实际上,小部份良好的批量可能被拒收,这种现象在品管中被称为‘生产者的风险’。
另一方面,在顾客来说,当然希望所有不良的送验批量都被拒收;实际上,小部份不良的批量可能被允收,这种现象则被称为‘顾客的风险’。
在执行验收抽样计划时,这两种现象都不能完全避免,只有良好的抽样计划才能使‘生产者’和‘顾客’的风险处于低水平。
第三章MIL-STD-105D之抽样步骤及图表
一、‘MIL-STD-105D’之简介
1942年贝尔电话实验室的一群工程师设计一个逐批检验产品的抽样标准,其后由美国政府采纳应用。
这套标准最初命名为JAN-STD-105。
其后经过四次修改,最后在1963年,由美国、英国及加拿大之委派人员修订成为‘MIL-STD-105D’。
MIL-STD-105D可应用于以下项目的抽样检验:
1、制成品
2、配件与原料
3、制造工序
4、半制成品
5、货仓的存货
6、其他
这标准中所载的抽样计划基本用于连续生产的每批产品,但独立的整批产品仍可采用,不过并不是所有内载的抽样计划都适合。
二、‘允许品质水平’(AQL)
‘允许品质水平’的定义是:
根据抽样检验的取决,某个制造程序可以被允许接纳的不良品出现的平均比率。
这个定义不易于完全明白,但在MIL-STD-105D中,允收品质水平(AcceptanceQualityLevel)是最重要的部份,因为在此标准中,允收品质水平是作为查出个别抽样计划的索引(index)。
一般来说,允收品质水平是由合约或规格书所订明,而不同级别的缺点会有不同的‘允收品质水平’去规限。
三、‘缺点’之分级
任何不符合‘要求’(requirements)的现象都可以被列为‘缺点’(defects)。
而‘缺点’又可按其性质或‘严重性’被分为以下几个级别:
1、‘严重缺点’(Criticaldefect):
可能影响产品的安全使用或主要功能的缺点。
2、‘主要缺点’(Majordefect):
可能导致产品失效或减低其效能的缺点。
3、‘次要缺点’(Minordefect):
任何不能符合既定要求又不严重影响产品的外观或性能的缺点。
四、‘检验水平’之选择
MIL-STD-105D提供有不同之‘检验水平’以供选择,共有Ⅰ、Ⅱ、Ⅲ、S1、S2、S3、S4等七个水平。
简单来说,它们之分别主要在于抽取样本数的多少(相对于同样的批量)。
在实际应用上,主要的选取原则是:
检验水平Ⅰ:
当检验所需成本甚高应考虑使用;
检验水平Ⅱ:
一般情况应用之;
检验水平Ⅲ:
当检验所需成本较低可选择使用;
S1至S4:
需要进行某些‘破坏性’测试时使用。
另一方面要考虑到的是,检验水平S1至S4所需的抽样数比较少,但抽样结果的偏差较大;检验水平Ⅲ需要的抽样数最多,但偏差最小。
五、正常、加强及减轻检验(Normal,TightenedandReducedinspection)
在一般情况下,品管人员最常使用是‘正常检验’的抽样计划(如表ⅡA所示);事实上,很多品管人员长时期不变去使用‘正常检验’。
不过,MIL-STD-105D提供了‘加强检验’及‘减轻检验’等计划作为特殊情况的对策。
1、由‘正常检验’转为‘加强检验’:
当连续五批产品送检时有两批被拒收,应马上转为‘加强检验’。
2、由‘正常检验’转变为‘减轻检验’:
当连续十批产品送检时全部被允收;此外,十批产品被发现的不良品数目少于某特定的数目,可以考虑转为‘减轻检验’。
其他有关‘加强’转‘正常’,‘减轻’转‘正常’的条件在MIL-STD-105D中都有明文规定,在此省略不提。
六、MIL-STD-105D之正确使用步骤
MIL-STD-105D中提供‘单次’,‘二次’,及‘多次’抽样计划选择。
不过,单次抽样计划是最常用的,它的正确使用步骤如下:
1、看先订明产品的收货标准;
2、决定‘允收品质水平’;
3、决定‘批量’;
4、选定所要采取之‘检验水平’,常用的是‘Ⅱ’;
5、从表Ⅰ中找出‘样本数’之代号;
6、决定使用‘正常’,‘加强’或‘减轻’检验,常用的是‘正常检验’;
7、从表Ⅱ中找出‘允收数’及‘拒收数’;
8、进行抽样检验,得出不良品数目,决定允收或拒收送检批量。
附表Ⅰ:
样本数索引
表ⅡA:
单次抽样计划之正常检验
表ⅡB:
单次抽样计划之加强检验
表ⅡC:
单次抽样计划之减轻检验
第四章资料的搜集(colletionofdata)
一、搜集资料之目的
在工厂里,有大量生产及其他的资料被搜集及储存。
遇到不同的生产项目与不同的生产程序,工作人员往往需要不同的资料去解决生产上的问题。
首先,让我们探讨一下搜集资料的目的。
大致上,搜集所得的资料都是作为‘行动’与‘决定’的依据。
分析起来,在工场里搜集资料有以下不同的目的:
1、协助明了实际情况
很多时候,工作人员需要搜集资料去了解工场的生产或品质状况,如造出来制品之尺寸分布,来料批量中之不良品百分率,或个别工序之报废率等。
根据所得资料,工作人员可以与既定规格或生产目标比较,看是否需要采取行动去改善。
2、分析生产问题的原因
要找出生产上问题或产品缺点原因,工作人员需要搜集和分析有关的资料,这些资料如果不能从过往记录中取得,就要安排一些试验去收集。
搜集所得的资料往往要应用各种‘统计方法’(Statisticalmethods)去分析,才能有效地解决问题。
3、制造程序管制
测量制成品或半制成品某些品质特性,然后应用‘管制图’去处理资料,工作人员可以评估制造程序是否处于‘稳定状况’,作为矫正制造程序之依据。
4、调校用的资料
在工厂里,机器的正常操作可能需要不断的调校。
例如工作人员需要不停调校电熔炉的炉温去达到操作要求,调校是根据仪器所得的温度的资料来进行的。
5、‘允收’或‘拒收’货品用的资料
这种资料是用来决定货品是允收或拒收,有两种方法去获得有关资料,即‘全数检验’和抽样检验。
二、正确的资料
以上提及过,搜集所得的资料都是作为‘行动‘的依据。
衡量过由资料反映出来的情况后,便可以采取适当行动。
因此,首先要确定所搜集得的资料是否代表典型情况。
我们可以提出两个问题。
1、所集得的资料是否代表事实?
2、资料是否经过整理和分析,使之反映实际情况?
第一个问题是关于抽样方法的问题;第二个问题是关于统计方法的问题。
抽样方法必须配合所需资料,对于为什么要搜集资料和选用何种抽样方法的问题,都必须详加考虑。
仅仅选用适当的抽样方法并不足够,还要考虑到所集得的资料是否代表事实,而所使用之统计方法是否有助于作出客观的判断。
三、资料的形式
现假定我们要判断几种布料的柔软度。
柔软度是一种难以量度的品质特性,它不像布料的长度或宽度可以有简单的方法量度。
但如果能够将布料按其柔软度加以排列,就已经获得有价值的资料。
一辆汽车行驶时的震动程度是另外一个很难量度的品质特性的例子,但如果我们被五个人分别驾驶该车辆,然后要求他们把视察所得作一报告,便可以获得一些有用的资料。
再重申一次,搜集资料,加以整理,目的是作为行动的依据。
资料可以有不同的形式。
一般来说,资料可以分为两大类:
1、量度资料:
例如长度、重量、时间等。
2、可点算资料:
例如不良品数目、缺点数目、生产故障次数等。
此外,亦有些资料不列入上述两大类;例如比值资料。
四、资料的组织
资料经过整理和分析后,便可以提供我们想要知道的事实。
为了方便整理和分析,我们要注意以下两点:
第一是清楚注明资料的性质。
工场内有很多资料可供搜集,但往往由于没有注明资料的性质,经过一段日子后,没有人再知道这些资料的由来而成为没有价值的资料。
因此,记录集得的资料时,应设法记下搜集的目的,所用仪器,负责人员以及所用方法等。
第二是记录的方式必须使资料易于使用。
如果能熟习资料表(datasheet)或查核单(checksheet)的技巧,就可以把资料组织得好。
五、搜集资料须紧记的几点
1、资料是行动的依据
必须时常记着:
资料是行动的依据。
养成根据资料来讨论问题的习惯,尊重资料所显示的事实。
2、了解搜集资料的作用
明白须根据资料来讨论问题外,接着要决定搜集哪种资料与搜集该种资料的作用。
集得资料后,必须加以审查,以确定它的用途。
3、将生产或品质上问题尽量化为统计资料
决定了要搜集什么资料后,不一定表示这种资料必然可以得到。
通常主要的困难是缺少仪器和人力。
解决的主要关健在于管理人员是否有足够的努力和能力。
一个良好的工厂管理人员通常会尽力设法搜集所需的资料。
品管训练课程之实验
(一)
主题:
随机抽样之操作特性
Ⅰ、实验内容:
假定在胶盒内之全部钢珠为一固定批量,而其中不同颜色之钢珠为不良件(某一个百分比),现在我们可以对此批量进行随机抽样。
⑴首先我们每次抽取样本数10粒,并记下不良件数目。
我们重复进行多次并用以下方式记录低抽样结果:
样品中不良件数目出现次数假定我们重复做100次
0(件)59
1(件)32
2(件)8
31
⑵此次我们将抽样数增加至20粒,并如前进行抽样及记低抽样结果。
⑶最后我们将抽样数增加至100粒,并如前进行抽样实验。
Ⅱ、结论:
⑴虽然每次均抽取同样(样本数),抽样结果并非每次一样(不良件数目),不良件数目会形成一个分布。
⑵当抽样数为10粒时,我们发觉不良件为0件之出现次数最多,然实际上批量中的确存在某个比例之不良件。
即是说,抽样结果并不太可靠。
⑶当S.S.增加至100粒时,不良件之分布开始呈(常态分布)而与实际情况越于接近。
品质管制的新理论
旧的观念——检查员找出坏品
新的观念——操作员预防出错
很多人认为改善产品品质意味着雇用更多检查员去检验和测试每一件制品,然后在出厂前设法改正有毛病的制品。
这是一种事后评价的品管制度,在这种制度下,一切有待货品造好后才依赖逐批检验去决定货品是否可以放行。
由于品管部全权负责出厂货品品质,一旦有任何重大的设诉品质事件,涉及的品管人员可能被撤职。
此种品管方式只能施加压力使检查员更努力去找寻坏品,但找出坏品并不能使公司减低已经造成的损失,处理坏品的方法不外两种,修改或报废,而两者都是无可奈何是事后补救行动。
反之,新的观念着重于设立预防制度,每一个人或操作工人都需要负责他工作份内的品质,工人需要知道什么是坏品,制造准则,有问题时该如何反映,和制品是否能符合顾客的要求。
为了达到上述的目标,管理阶层的承诺和支持是非常重要的。
通过管理阶层的影响和参与,新的品管观念和工作方法才能够在工场和其他岗位落实,工人都知道产品的质与量是同样重要,有关制品和制造程序的要求和规格都能够传达到每个生产工场,一旦制造上有所出错时,工人便能及时发现。
全员参与是达到上述目标的要素,提高产品品质不再是品管部的专利,它是所有员工的共同目标。
同样的原则可以引伸到和供应商的关系上,供应商的积极参与是更好地促进品质运作能够成功的要素。
在正式投产之前,你的员工必须获悉和清楚产品的要求和标准。
当你的操作人员发觉制品或生产程序偏离既定的规格,在继续生产之前,我们应该先调查出错的根本原因和采取纠正措施。
在调查制造出错的根本原因方面,我们建议你尝试分析以下六个基本因素(6M):
人员(Man)机器(Machine)方法(Method)
物料(Material)量度(Measurement)管理(Management)
旧的观念——检查关卡制度
新的观念——制造程序管制
旧的观念着重于设立关卡,逐批检验货品(例如来料检验),根据检验报告,货品的处理有以下三个可能性。
整批收货拣货和重做报废
后两种处置方面必然招致公司某种程度的损失。
制造程序管制能帮助我们即时发现问题,采取纠正行动,和减少不符合要求的代价。
目前香港**公司正设法加强制造程序管制以取代逐批检验的做法。
我们希望各供应商能够与我们一齐去实现制造程序管制,如果将来你们能够达到这个目标,公司可能推下一个供应商检定计划以取代目前的来料检验制度。
旧的观念——好品质意味的高成本
新的观念——促进品质能减低成本
优质是免费的!
如果我们能有效应用上面提及的品管制度去处理品质问题,操作人员又能避免次品的产生。
旧的观念认为重做、拣货、修改等支出是制造优质产品的必需成本。
为了与邻近地区竞争,我们需要降低制造成本,而最好的突破方法便是改变我们对品质的观念。
旧的观念——生产力与优质是相对的
新的观念——生产力与优质近乎同义词
生产力与优质两者是同样重要和不可或缺的。
只有优质而生产力低会令公司破产,只有高生产力而品质低劣同样会将公司带入困境。
因此,不要轻率地承接一些超乎本身制造程序能力的订单,如果你们认为可以达到公司的要求,先设法和公司的人员商讨去解决困难。
旧的观念——错误是难以避免的
新的观念——错误是可以完全避免的
在制造过程中,我们应该预期所有产品都是良好的而不是某个比例的不良品是难以避免的。
旧的观念——自动化是用来减低劳工成本的
新的观念——自动化亦可以用来改进产品品质
如果能配合适当的制造程序管制、设备维修和优良设计,自动化生产可以大量生产出一些符合规格的制品。
旧的观念——优质只是针对制造部门
新的观念——优质应该推及所有部门
工作的质素和第一次把它做对的概念不单适用于制造部门,事实上应该至公司每一个部门和每一件工作。
旧的观念——制造的损耗是促进优质的动力
新的观念——顾客的要求是促进优质的动力
我们需要倚赖预防制度才能改善品质和确保符合顾客的要求。
旧的观念——优质是一个任务
新的观念——优质是一个焦点
促进优质不单是某些部门(例如品管部)的任务,而应该是公司所有人员的共同目标。
优质是每一个工作所附带的态度
同样地这焦点适用于供应商与公司的关系,在互相尊重,互相信任和互相增益之条件下一齐去推行优质运动;你们和你们的全体员工参与是我们和各位供应商未来成功的要素。
珠海市鸿丰电子塑料玩具有限公司
QC入厂培训课程纲要
一、所有QC入厂工作时,均要接受培训,培训教程为——《品管员训练课程》
二、《品管员训练课程》主要内容如下:
第一章:
品质管制与抽样检验,在此章中将详述。
⑴品管管制的定义:
⑵‘抽样检验’的基本概念;
⑶‘随机抽样’及其它抽样方法;
⑷抽样的误差。
第二章:
逐批验收抽样检验,在此章中将详述。
⑴逐批验收抽样的定义;
⑵验收抽样计划的种类;
⑶批量的组成;
⑷样本的选择;
⑸生产者与顾客所冒之风险。