TV外观通用检验规范.docx
《TV外观通用检验规范.docx》由会员分享,可在线阅读,更多相关《TV外观通用检验规范.docx(22页珍藏版)》请在冰豆网上搜索。
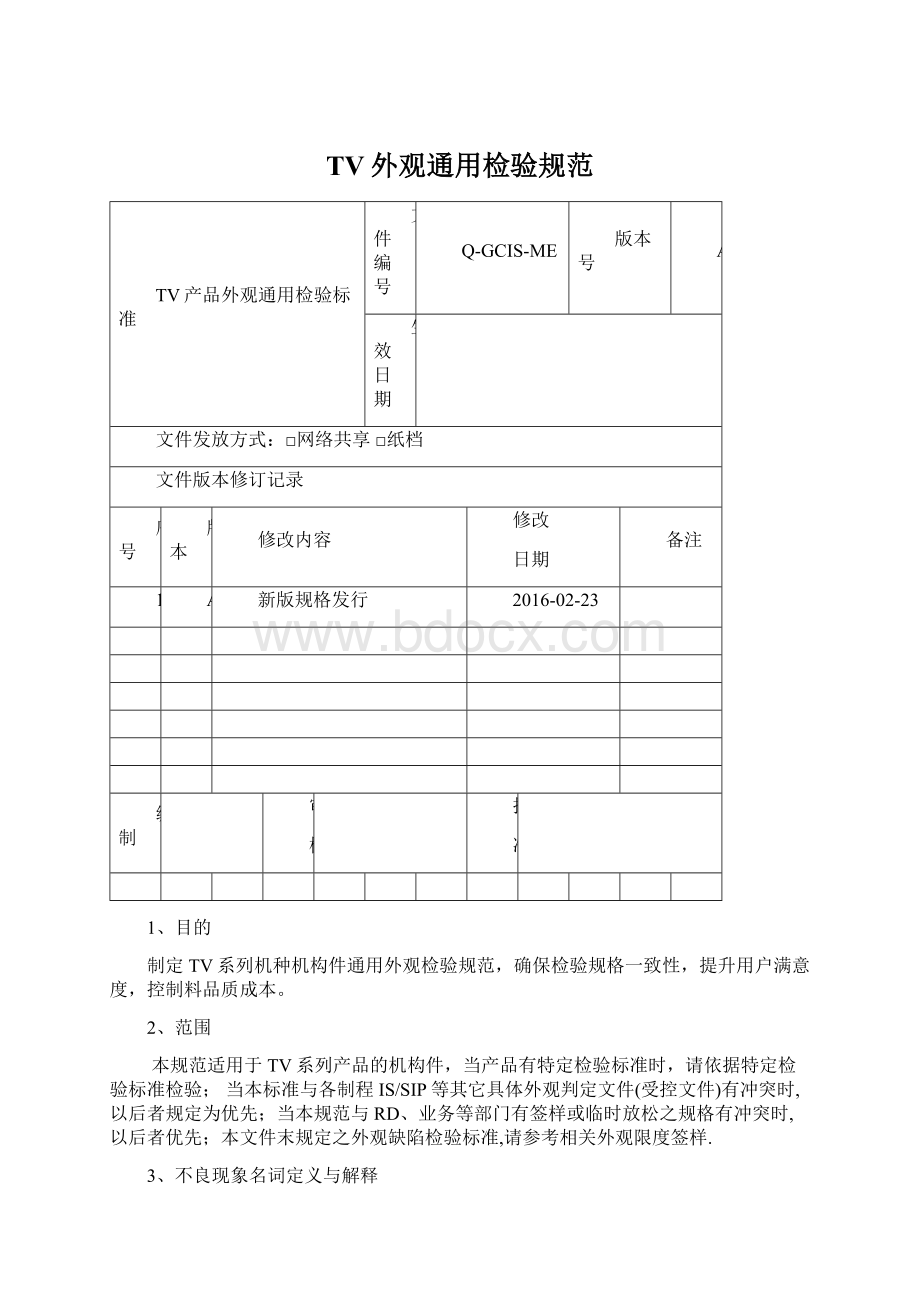
TV外观通用检验规范
TV产品外观通用检验标准
文件编号
Q-GCIS-ME
版本号
A
生效日期
文件发放方式:
□网络共享□纸档
文件版本修订记录
序号
版本
修改内容
修改
日期
备注
1
A
新版规格发行
2016-02-23
编制
审
核
批
准
1、目的
制定TV系列机种机构件通用外观检验规范,确保检验规格一致性,提升用户满意度,控制料品质成本。
2、范围
本规范适用于TV系列产品的机构件,当产品有特定检验标准时,请依据特定检验标准检验;当本标准与各制程IS/SIP等其它具体外观判定文件(受控文件)有冲突时,以后者规定为优先;当本规范与RD、业务等部门有签样或临时放松之规格有冲突时,以后者优先;本文件末规定之外观缺陷检验标准,请参考相关外观限度签样.
3、不良现象名词定义与解释
3.1通用不良名词定义与解释
项次
名词
名词解释
1
缺陷
不完美或瑕疵.
2
纹理不均
材料表面局部纹路不均匀,不整齐
3
利边
在产品外露边面处有锋利尖角或锐边﹐导致在正常使用或维护接触时,产生人体伤害之缺陷.
4
脏污
各环节中操作不整洁,附着在产品表面的脏点或油污(通常可擦除).
5
手指印
于材料来料或制程贮运过程中,因人手直接接触工件表面所残留之印记.
6
变形
在加工、运输及装配等过程中,产品受本身内应力作用或外力作用使形状改变.
7
针孔
产品表面或贯穿到产品内部或基体金属之微小孔道.
8
异物镶嵌
金属物或非金属物在加工、运输及装配等过程中,被压入工件表面.
9
裂痕/缝
延伸至产品表面之下或穿透产品之缝隙.
10
凹陷/压伤/碰伤
在加工、运输及装配等过程中,产品受异物挤压或碰撞产生的表面下陷或变形.
11
刮痕
在加工﹑运输﹑装配等过程中,产品受异物划过等引起的线状痕迹.
12
模痕
模具在使用过程中造成产品表面均匀的类似刮痕或挤料的痕迹.
13
色差
工件与工件之间或工件与标准色板之间表面颜色不一致.
14
阴阳色
同一工件表面局部亮度不一或色泽不均匀.
15
手感
指甲感和指腹感的统称.
16
指甲感
用指甲(或尖,硬,细木棒—仅适用于用手指难以实现时)垂直于产品表面滑动,有停顿或阻滞感觉,主要用于检测宽度较小的缺陷(如刮伤﹑划伤等).
17
指腹感
用指腹垂直于产品表面滑动,有停顿或阻滞感,主要用于检测宽度或面积较大的缺陷(如压坑或凹陷等).
18
油污
在制程清洁不良,附着在产品表面的油污.
3.2塑料成型不良定义
19
异色
表面色泽的改变,常由咬花深度和突起的突然改变造成,常在浇口,熔接线和壁厚突然改变的部位
20
黑点(线)
塑料在成型过程中,因排气不良,树脂被烧焦而形成的黑色物质.
21
杂质
夹杂在塑料中的外来变色异物.
22
毛边
从产品表面溢出的胶料,通常位于入子的周围.
23
气孔
由于过度收缩或有空气无法逸出而形成的真空.
24
气泡
由被缚气体形成的球形空间.
25
烧焦痕
由塑料热降解造成的颜色改变,一般呈棕黑色斑点或条纹.
26
脱模拉伤
产品在顶出过程中因摩察而产生的损伤,常由拔模斜度不适当或成型压力过大造成
27
分模线毛边
从模具分模线表面溢出的胶料.
28
不饱模
因模腔末完成充满造成的某些特征不完整缺失.
29
缩水
因塑件冷却不均匀造成的局部表面凹陷,不连续或皱折.
30
咬花纹
由模具咬花形成的产品表面纹理.
31
结合线
塑料成型时形成的线,通常表现为横过产品面的明显的线.
32
顶白
模具开模或顶出产品时因拉力而引起的塑件变形.
33
流痕
因料流不一致造成的条纹或颜色改变.
3.3金属零件素材/冲压不良定义
34
条纹
材料表面顺轧制方向的直线状纹路性缺陷.
35
轧(模)痕
在轧制过程中或成形时不均衡轧制,引起的垂直轧制方向的痕迹.
36
摩擦痕
板材之间或板与轧辊之间,产生的摩擦痕迹,一般呈分散状或扫帚状,阳极/电镀后产生异色;
37
毛边
冲裁时因材料撕裂而在冲切边缘所产生之尖锐凸起.
38
压毛边不良
压毛边过大时造成毛边处材料流向侧边,形成新的毛边.
39
氧化物
金属件因底材与氧气发生化学反应生成之变色化合物.
40
废料压痕
金属废料夹在模具表面与产品间造成的产品表面凹坑.
41
断面接刀痕
冲裁切边时,因分制程多次冲裁切造成接口处不齐整.
42
冲压塌角
指冲压落料时因材料受力而产生之材料塌陷现象.
43
折(模)痕
产品折弯时,因材料流动不均或模具摩擦,于边部或折弯处产生的压折磨损痕迹.
44
铆合印痕
铆合时在外观面形成的印痕.
45
桔皮(拉料凹陷)
折弯时或成形时因材料受应力不均,造成内、外表面的晶粒变化不一致,在产品成形部位表面产生桔子皮状的缺陷,严重时产生下陷裂纹.
3.4表面电镀处理不良定义
46
麻点
在电镀过程中镀层表面形成的小坑.
47
起皮
镀层呈片状脱落于基体之现象.
48
起泡
在电镀过程中镀层与基体失去结合力形成凸起状镀层.
49
剥落
因不均匀之热膨胀或收缩引起的镀层表面的破裂或脱落.
50
黄斑
电镀过程中沉淀不良﹐或后处理﹑水洗时不干净有残留物所致.
51
斑点
镀层表面色斑,暗斑等缺陷.系因电镀过程中沉淀不良,异物粘附或钝化液清洗不干净所致.
52
烧焦
在过高电流的情况下形成的黑暗色,多出现在产品边角部位.
53
电弧痕
由于镀件相互碰﹐或镀件碰到镀槽﹑电极﹐等留下的痕迹.
54
彩虹(五彩)色
电镀过程中沉淀不良﹐或使用添加剂作表面处理后﹐在产品表面呈现的彩虹状变色.
55
条纹
电镀过程中产生的类似材料纹理的条状缺陷﹐严重时有手感.
56
雾状
在光亮镀层表面,存在不同程度的雾状覆盖物.
57
粗糙面
电镀过程中沉淀不良﹐产生的工件表面粗糙缺陷﹐严重时有手感.
58
树枝状结晶
在镀件边缘和其它高电流区形成的粗糙/松散的树枝状或不规则凸起的沉淀物.
59
海棉状镀层
与基体金属结合不牢固的疏松多孔的沉积物.
60
水渍
水洗不干净和/或干燥镀层表面时悬挂方法不当﹐工件表面有污染状附着物﹐而致产品表面变色.
3.5表面烤漆处理不良定义
61
起泡
漆膜干结后,局部与被涂物面失掉附着力,成直径不同的球状小泡向上膨胀隆起,内部包藏液体或气体,或隆起局部发生破裂的状态
62
细裂/开裂
在漆膜表面呈现轻微的裂痕称为细裂;如从裂痕处可开裂见到下层表面称为开裂.
63
剥落与脱皮
由于涂层和物体表面失去附着力,在涂层表面形成小片或鳞片状脱离的现象称为剥落;若整个涂膜脱落称为脱皮.
64
针孔
在漆膜表面出现一种凹陷的透底的针尖大小般的细微孔.
65
桔皮
涂料喷涂施工后,因流平性差,干燥后漆膜表面形成起伏不平的凹陷现象.
66
流挂
涂料施工于垂直物体表面上,未干前涂层有下流现象,造成干后漆膜厚薄不均,并有流痕.
67
变脆
漆膜经过一定时间后丧失柔韧性,在弯曲或冲击等外力作用下会发生开裂或成为碎片.
68
咬底
喷涂面漆后,面漆把底层漆膜熔融而带起的现象.
69
失光
漆膜干后,表面无光泽或光泽不足的现象.
70
发白
硝基漆或其它挥发干燥型涂料,施工或干燥后,漆膜光泽减退,如果是清漆则表面发白,透明度降低的现象,通常发生在潮湿环境中施工.
3.6表面印刷(丝印/移印)处理不良定义
71
线细
印刷文字或图案线条局部未印刷充满而宽度变小.
72
肥边
印刷文字或图案线条局部印刷过于充满而宽度变大.
73
轮廓不清晰
由于印刷文字或图案线条局部印刷颜色偏淡/深﹐或未印刷到等﹐导致整个印刷图案/文字轮廓不完整﹑不清晰.
74
欠缺
印刷文字或图案线条局部未印刷上而出现残缺.
75
重影
印刷文字或图案线条局部印刷迭重.
76
渗透(拖墨)
印刷文字或图案线条出现凸出或边缘呈锯齿状.
77
油墨飞溅
在印刷时油墨飞溅到丝印表面而形成的斑点
78
异物
空气中的灰尘,印刷机污物等夹杂物
4、外观等级面定义﹑划分﹑检视方法
4.1表面等级面定义:
(按重要顺序排列,A级面为最重要)
A级面:
指使用者最经常直接看到的面,如显示框外壳的正面;
B级面:
指用户可能经常看到的面,如显示框外壳的顶面﹑左右侧面﹑后面及支架表面;
C级面:
指使用者通常看不到的面,如显示框外壳的下表面;
D级面:
用户必须翻转或拆开产品后才可见到的面,如支架的下表面和所有内部表面.;
Lens:
若在蓝图上没有特殊要求,则所有lens都是A级面;
Logo:
无论其位于成品的哪一级面,均以A级面管控。
单独出货的部件,外观等级面升一级,如支架,则升级为A/B级别。
4.2外观面等级划分图标
所有未定义面为D级面.
4.3外观目视检视条件和方法
4.3.1检视灯光:
800LUX±150之冷白荧光照明.
4.3.2检视角度﹑检视距离﹑检视方法及检视时间,如下图所示
零件表面
零件表面
1.零件被检验表面中心距离光源1.0M.
2.检视面中心距离眼睛60cm.
3.零件与水平面成45度角,零件沿垂直和水平方向各旋转20度.
4.检视时间:
每个面不超过10s,且同一点不能停留超过6s.
5.检验员视力要求(含矫正)0.8以上。
圖1:
A級面檢視位置示意圖
1.零件被检验表面中心距离光源1.0M.
2.检视面中心距离眼睛60cm.
3.将零件与水平面成90度角,零件不旋转.
4.检视时间:
每个面不超过7s,且同一点不能停留超过6s.
5.检验员视力要求(矫正后)0.8以上。
圖2:
B﹑C﹑D級面檢視位置示意圖
4.4外观判定一般原则
4.4.1对于规则缺陷,需参考相关级面规定并用TV-ME-001外观缺陷比对片比照判定允收或拒收﹔对于不规则成品缺陷先用25%之灰度比对片覆盖(除非另有特殊规定),若看不到,则允收,若看到,则用TV-ME-001外观缺陷比对片比照判定允收或拒收.
4.4.2小于0.05mm2的任何缺陷均视为不见,但当此类小缺陷位明显群聚于A级面时拒收.
对于A级面,任意Φ50区域内只允收3个小于0.10mm2的缺陷,
对于B,C级面,任意Φ50区域内只允收5个小于0.10mm2的缺陷;
4.4.3对于A,B,C级面,任意两个大于0.10mm2的缺陷之间的距离不小于50mm;
对于D级面,任意两个缺陷之间的距离不限制;
对于相邻表面﹐无论其外观等级面是否相同﹐任意两个缺陷之间的距离不小于25mm.
4.4.4细长浅(不露底材)刮伤:
对于A级面,长度≤10mm,宽≤0.10mm,同一平面内不允许超过1个;
对于B级面,长度≤30mm,宽≤0.10mm,同一平面内不允许超过2个
对于C级面,长度≤60mm,宽≤0.20mm,同一平面内不允许超过3个;
对于D级面,长度≤100mm,宽≤0.25mm,同一平面内不允许超过5个
4.4.5当缺陷大小处于TV-ME-001外观缺陷比对片临界状态时,按缺陷偏小一级判定(放宽).
4.4.6对于D级面,原则上只要不影响装配和功能的外观缺陷都可允收.除非另有规定.
4.4.7任何零件表面应无灰尘,污垢,润滑油,机油或其它表面沾染物,如有,则用软棉布或WINDER擦,擦除后则允收.
4.4.8缩水﹑不饱模﹑烧焦痕﹑裂痕﹑表面氧化物﹑生锈﹑露底材﹑起气泡﹑起皮﹐不允收.有签样则依签样。
4.4.9棱边﹑去/压毛边:
目视均匀;将手指贴在棱边上,沿周边滑动检视感觉光滑,用母指斜向触摸无刮手感;具体程度比对签样,前框外观面不允许有飞边。
4.4.10未经过特别处理的飞边或毛边高度不超过0.13mm.
4.4.11单件出货的零件﹐外观等级加严一级﹕原为C﹑D级面加严为B﹑C级面.
4.4.12当本规范与各制程IS/SIP等其它具体外观判定文件(受控文件)有冲突时,以后者规定为优先.
当本规范与RD、业务等部门签样或临时放松之规格有冲突时,以后者优先.
4.4.13本文末规定之外观缺陷检验标准,请参考相关外观限度签样.
4.5表面烤漆处理外观判定一般原则和质量管理项目
4.5.1最终成品外观判定:
a.按附图等级面和TV-ME-001外观缺陷比对片.
b.折弯成形模痕缺陷依签样判定.
c.附着不良(细裂﹑开裂﹑剥落与脱皮等现象)以致露出底材者不接受.
d.变脆﹑咬底﹑发白等缺陷不接受.
e.起泡:
面积≤0.50mm2的按TV-ME-001外观缺陷比对片判定,面积>0.50mm2的不接受.
f.针孔:
大小TV-ME-001外观缺陷比对片判定.
4.5.2.素材(烤漆前)外观判定:
a.对于液体烤漆零件:
有很轻微手感的缺陷(深度约小于0.02mm,参照限度签样)全部允收;
对于粉体烤漆零件:
有很轻微手感的缺陷(深度约小于0.06mm,参照限度签样)全部允收;
b.对于手感较明显的缺陷,大小与允收数量按LCD-001外观缺陷比对片判定,OK则允收;
NG则需重工处理(可用砂纸打磨等).
c.折弯成形等模痕缺陷依签样判定.
4.6表面印刷处理产品外观判定一般原则和质量管理项目
4.6.1.按附图等级面和TV-ME-001外观缺陷比对片.
4.6.2.印刷字体或图案完整﹑正确﹑位置符合蓝图标注或签样.
4.6.3.印刷字体或图案必须颜色均匀,没有明暗﹑白点,条纹不一致.
4.6.4.印刷边缘轮廓线清晰均匀,不得有油墨堆积﹑模糊不清﹑重影﹑不得有凸起和凹陷感等缺陷.
4.6.5.印刷字体或图案不许有目视可见之纤维﹑毛发.
4.7表面电镀处理外观判定一般原则和质量管理项目
4.7.1最终成品外观判定:
(表面电镀后的零组件)
a.按附图等级面和TV-ME-001外观缺陷比对片.
b.折弯成形模痕缺陷依签样判定.
c.附着不良以致露出底材者不接受;起气泡﹑起皮不接受.
4.7.2.素材(电镀前)判定:
有非常轻微手感(深度约小于0.01mm,参照限度签样)的缺陷大小与允收数量按TV-ME-001外观缺陷比对片判定.
5、整机补充外观判定原则
5.1塑件验收标准
Defect
缺陷
AZONE
A面
BZONE
B面
CZONE
C面
DZONE
D面
Swollen
肿胀
区域面积≦0.3mm2
N≦1
区域面积≦0.5mm2
N≦2
区域面积≦0.5mm2
N≦3
Dent
凹陷
区域面积≦0.3mm2
N≦1
区域面积≦0.5mm2
N≦2
区域面积≦0.5mm2
N≦3
Weld
熔接线
长度≦10mm
长度≦20mm
长度≦30mm
-----------------
Stain
污迹
区域面积≦0.3mm2
N≦1
区域面积≦0.5mm2
N≦2
区域面积≦0.5mm2
N≦3
区域面积≦0.5mm2
N≦3
Burr
毛边
没有
没有
没有
没有
Shallowdamage
表面损伤
(Abrasiondamage)
(刮伤)
长度≦10mmN≦1
长度≦20mm
N≦2
长度≦30mm
N≦3
区域面积
≦0.5mm2
N≦3
Greasiness
油污
Nothing
没有
Nothing
没有
Nothing
没有
Nothing
没有
Inclusions
包容物
Nothing
没有
Nothing
没有
Nothing
没有
Nothing
没有
Knitlines
结合线
看不见的结合线是可以接受的
具体情况见样品
具体情况见样品
具体情况见样品
5.2丝印的标准
Defect
缺陷
AZONE
A区
BZONE
B区
CZONE
C区
DZONE
D区
Artworkmiss
丝印错误
Nothing
没有
Nothing
没有
Nothing
没有
Nothing
没有
Colordiscordant
颜色不一致
Nothing
没有
Nothing
没有
Nothing
没有
OK
Sawtooth
锯齿
Nothing
没有
Nothing
没有
Nothing
没有
Nothing
没有
允许丝印高度变化范围
<=0.1mm
<=0.2mm
<=0.2mm
<=0.2mm
Artworktilted
丝印倾斜
Square0.3mm
直角方向偏移0.3mm
Square0.4mm
直角方向偏移0.4mm
Square0.4mm
直角方向偏移0.4mm
Square0.4mm
直角方向偏移0.4mm
Stain
污迹
区域面积≦0.25mm2
N≦1
区域面积≦0.5mm2
N≦2
区域面积≦0.5mm2
N≦2
区域面积≦0.5mm2
N≦2
PinHole
小洞
区域面积≦0.1mm2
N≦2
标牌处没有
区域面积≦0.2mm2
N≦2
区域面积≦0.5mm2
N≦2
区域面积≦0.5mm2
N≦2
5.3铁件验收标准
Defect
缺陷
AZONE
A区
BZONE
B区
CZONE
C区
DZONE
D区
Scratchdamage
刮伤损害
长度<=10mm
宽度<=0.3mm
N≦1
长度<=15mm
宽度<=0.3mm
N≦3
Greasiness
油污
Nothing
没有
Nothing
没有
Nothing
没有
Nothing
没有
Swollen
肿胀
直径≦0.5mm
N≦2
直径≦0.5mm
N≦3
直径≦0.5mm
N≦4
装配OK皆可
Dent
凹陷
直径≦0.5mm
N≦2
直径≦0.5mm
N≦3
直径≦0.5mm
N≦4
装配OK皆可
6、颜色匹配
这个段落主要定义了产品制造过程中,对于不同材料混合使用在塑件、油印件和印刷件中,如何使用正确颜色认证方法来确保我们一致的颜色匹配。
这些指导将和供货商物料的PSCS规范一起,在制造地点做首件检查、采购、来料检验、组装和最后的认证。
最终目标是所有制造地点提供的零件和组装件达到所要求的最高质量的颜色匹配。
6.1检验流程
对于颜色匹配要求的精密程度取决于产品或系统相关联系中的美学应用。
视觉上对于颜色匹配的评价和分光亮度计CIE长*寛*高上不同的颜色数据联系在一起。
当一个异常出现,视觉上的匹配将代替仪器数据起决定作用。
工业设计部门(或者他们的代理商)和供货商们应该用合适的存储和周期性的检查来确保产品颜色标准没有被仪器数据所偏离。
供货商有责任在颜色匹配标准已经不适用时提出新的替代标准请求。
6.2照明要求
在一个配备了发光源CIECWF(F2)4400K,CIEA2854K和CIED6500K的明亮小隔间里操作
小隔间应该配置于满足ASTMD1729标准
颜色的规划和颜色匹配评估的认证应该在CIECWF(冷白荧光)光源下执行。
在CIEA光源和CIED6500K光源下,条件等色的评价应该在观看匹配样品和标准的同时进行评估。
颜色匹配方面的美学观感应该保持一贯的水平,不能出现任何不同。
条件等色也是颜色认证失败的一个重要原因。
6.3观察角度的要求
需要匹配的样品和颜色标识(色标)应该在不同的观察角度下进行评估。
在对比时需要匹配的样品应该彼此靠近且在一个平面内。
当有不同的反射光时这显得很重要。
黑色的对比应该使用B案例。
这个角度会降低反射光的光泽差异,会干涉影响L值(亮些或暗些)匹配对比。
这些测量参数如果用于评估颜色匹配应该是唯一的,对于制订颜色匹配的规定也同样如此。
6.4颜色测量的参数
当颜色匹配产品颜色时,供货商应使用下面的颜色测量参数
CIEdeltaL*a*b*
CIE三参数L*a*b*
CIECWFIlluminant(4400K)
CIE冷白荧光源(4400K)
CIE10Observer
CIE10观察
SpecularComponentIncluded
也同时包括一些反射的内容
在评估颜色匹配的质量时增加另外3个参数:
在样品和颜色标准之间的条件等色指数
需匹配的样品和颜色标准之间的光谱能量分布(SED)曲线
视觉直观的颜色评价,
供货商将会提供匹配样品和颜色标准之间的CIE参数L*a*b*和E*
6.5颜色认证的允许误差
我们不提供认证匹配中CIE参数L*a*b*的颜色允许误差
对于不同颜色允许的差会不一样且相对独立,这主要取决于对于产品来说颜色之于美学观感的重要性。
一旦颜色匹配获得通过,然后一批批的颜色允许误差,使用的颜色标准作为底线,应该得到应用。
6.6匹配样品认证报告
工业设计部门(或者他们的代理商)将会在视觉上和应用测量来评估颜色匹配样品是否合格。
当颜色认证标准(除颜料比例外)、填充料或模具混合物/涂料化学等发生改变时供货商必须重新认证材料。
7、缺陷比对片
注意:
下图不是1:
1比对片,使用时须使用1:
1透明塑料比对片
Whaley产品外观机构件缺陷比对片TV-ME-001
缺陷大小
(mm2)
缺陷类型:
外形与尺寸范例
外观等级面
(任意Φ50区域内允收数量)
A
B
C
D
0.05
OK
OK
OK
任何不影响机械性能之缺陷允收
0.08
OK
OK
OK
0.1
3
5
5
0.2
3
OK
OK
0.3
2
4
OK
0.5
2
(Φ100)
4
(Φ100)
4
0.7
2
4
1
不允收
3
1.5
2
2
2.5
3
说明:
1
对于A/B/C级面,任何缺陷之间距应>=50mm;可使用下图比对判定距离;
2
其他未明确缺陷,磨损、阴影、暗色、异色、表面纹理变化、脏污、细小刮花、变亮等,用右下侧标准灰度比对板覆盖其上,若缺陷仍可见,则判定“不良”;
3
灰尘允收数量和大小按照A级面判定;
4
丝印区域针孔允收数量和大小按A级面判定。
缺陷距离比对圈(50mm)标准灰度比对板25%(仅用于成品)