冷轧工艺知识问答精华版.docx
《冷轧工艺知识问答精华版.docx》由会员分享,可在线阅读,更多相关《冷轧工艺知识问答精华版.docx(36页珍藏版)》请在冰豆网上搜索。
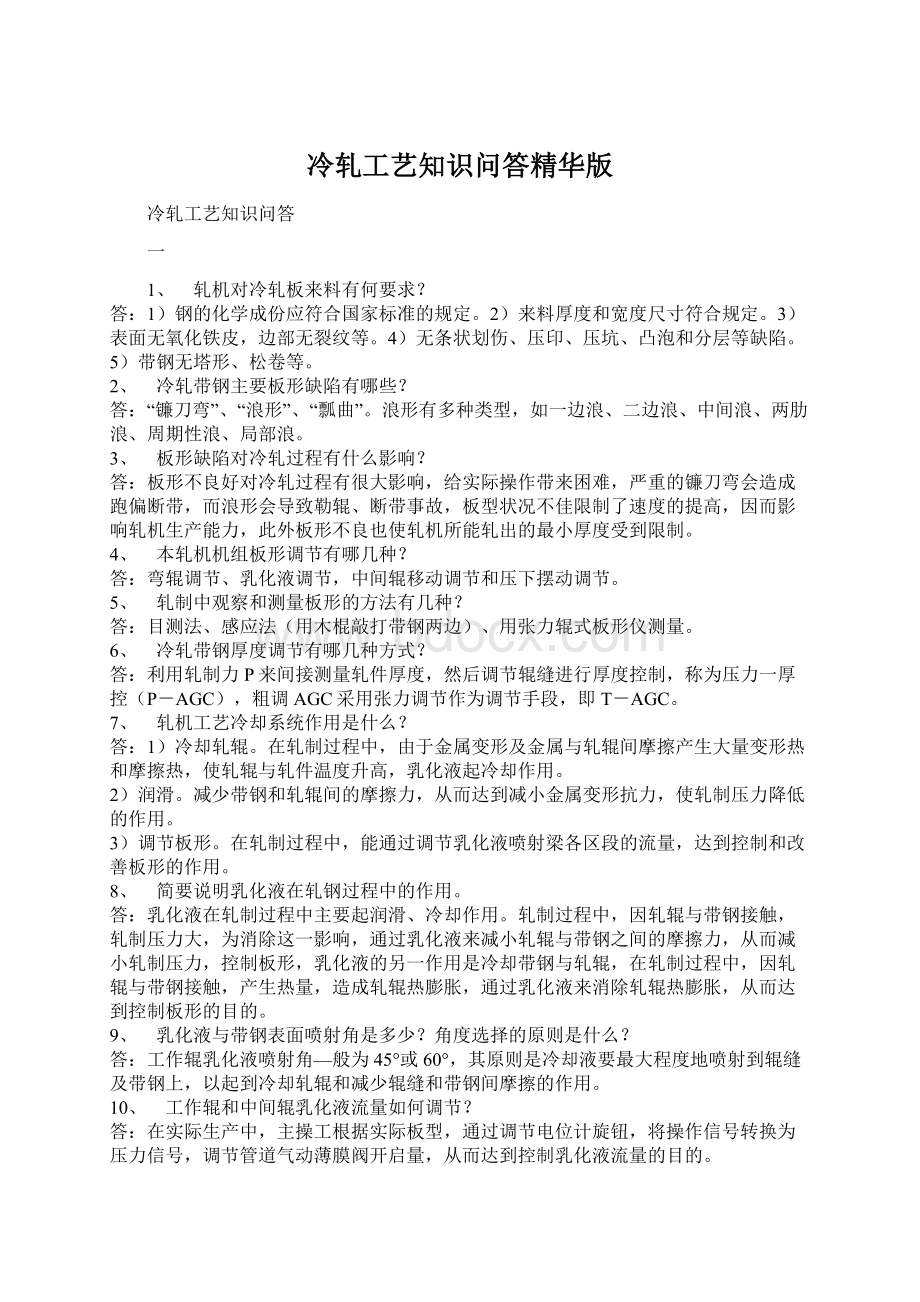
冷轧工艺知识问答精华版
冷轧工艺知识问答
一
1、 轧机对冷轧板来料有何要求?
答:
1)钢的化学成份应符合国家标准的规定。
2)来料厚度和宽度尺寸符合规定。
3)表面无氧化铁皮,边部无裂纹等。
4)无条状划伤、压印、压坑、凸泡和分层等缺陷。
5)带钢无塔形、松卷等。
2、 冷轧带钢主要板形缺陷有哪些?
答:
“镰刀弯”、“浪形”、“瓢曲”。
浪形有多种类型,如一边浪、二边浪、中间浪、两肋浪、周期性浪、局部浪。
3、 板形缺陷对冷轧过程有什么影响?
答:
板形不良好对冷轧过程有很大影响,给实际操作带来困难,严重的镰刀弯会造成跑偏断带,而浪形会导致勒辊、断带事故,板型状况不佳限制了速度的提高,因而影响轧机生产能力,此外板形不良也使轧机所能轧出的最小厚度受到限制。
4、 本轧机机组板形调节有哪几种?
答:
弯辊调节、乳化液调节,中间辊移动调节和压下摆动调节。
5、 轧制中观察和测量板形的方法有几种?
答:
目测法、感应法(用木棍敲打带钢两边)、用张力辊式板形仪测量。
6、 冷轧带钢厚度调节有哪几种方式?
答:
利用轧制力P来间接测量轧件厚度,然后调节辊缝进行厚度控制,称为压力一厚控(P-AGC),粗调AGC采用张力调节作为调节手段,即T-AGC。
7、 轧机工艺冷却系统作用是什么?
答:
1)冷却轧辊。
在轧制过程中,由于金属变形及金属与轧辊间摩擦产生大量变形热和摩擦热,使轧辊与轧件温度升高,乳化液起冷却作用。
2)润滑。
减少带钢和轧辊间的摩擦力,从而达到减小金属变形抗力,使轧制压力降低的作用。
3)调节板形。
在轧制过程中,能通过调节乳化液喷射梁各区段的流量,达到控制和改善板形的作用。
8、 简要说明乳化液在轧钢过程中的作用。
答:
乳化液在轧制过程中主要起润滑、冷却作用。
轧制过程中,因轧辊与带钢接触,轧制压力大,为消除这一影响,通过乳化液来减小轧辊与带钢之间的摩擦力,从而减小轧制压力,控制板形,乳化液的另一作用是冷却带钢与轧辊,在轧制过程中,因轧辊与带钢接触,产生热量,造成轧辊热膨胀,通过乳化液来消除轧辊热膨胀,从而达到控制板形的目的。
9、 乳化液与带钢表面喷射角是多少?
角度选择的原则是什么?
答:
工作辊乳化液喷射角—般为45°或60°,其原则是冷却液要最大程度地喷射到辊缝及带钢上,以起到冷却轧辊和减少辊缝和带钢间摩擦的作用。
10、 工作辊和中间辊乳化液流量如何调节?
答:
在实际生产中,主操工根据实际板型,通过调节电位计旋钮,将操作信号转换为压力信号,调节管道气动薄膜阀开启量,从而达到控制乳化液流量的目的。
11、 什么叫“镰刀弯”和“S弯”?
它们对冷轧生产有何影响?
答:
“镰刀弯”和“S弯"指在带钢中心线沿带钢长度方向出现的镰刀形和S形变化而言,在轧制过程中引起带钢跑偏,严重时造成断带,使带钢卷取也产生塔形,钢卷上、下两端松紧不均。
12、 冷轧带钢有哪些品种?
答:
冷轧带钢主要有深冲钢板、普碳板、自行车板、镀锌钢板、彩涂板和电镀锡板。
13、 冷轧工艺有哪些特点?
答:
1)带钢在轧制过程中产生不同程度的加工硬化,钢质愈硬,轧程愈多。
2)冷轧过程必须采用工艺冷却及润滑。
3)冷轧中采用张力轧制,张力轧制就是带钢在轧制中轧制变形是在一定前后张力作用下进行。
14、 冷轧中采用张力轧制的作用?
答:
防止带钢在轧制过程中跑偏(保证正确对中轧制);使所轧带钢保持平直(包括在轧制过程中保持板形平直和轧后板形良好);降低金属的变形抗力,有利于轧制更薄产品,起适当调节冷轧机主电机负荷的作用,由于张力的变化会引起前滑与轧辊速度的改变,故对冷轧过程有一定自动调节作用。
15、 什么叫冷轧?
冷轧带钢有哪些优点?
答:
金属或合金在低于再结晶温度下进行的轧制叫冷轧,通常指的冷轧是将轧材不经过任何温度处理进行加工,在轧钢过程中轧件随着变形增加,温度不断升高,为了防止轧件和轧辊温度的升高,轧钢过程需要不断采取降温措施来控制温度升高,一般冷轧的轧件最高出口温度为150℃。
冷轧生产可提供大量高精度和性能优越的钢板和带钢,其最主要的特点是加工温度低,同热轧相比,有以下优点:
1)冷轧带钢产品尺寸精确,厚度均匀;2)可获得热轧无法生产的极薄材(≤O.001mm);3)表面质量优越,不存在热轧带钢常出现的麻点、压入氧化铁皮等缺陷。
4)具有很好的机械及工艺性能;5)可实现高速轧制和全连续轧制,具有很高生产率。
16、 冷轧带钢厚度波动的原因有哪些?
答:
冷轧带钢厚度的波动主要原因在于轧制压力的波动,而影响轧制压力波动因素是多方面的。
1)带钢方面原因,带钢化学成分和组织结构不均匀,轧制速度的变化对带钢厚度的变化有很大影响,如带钢的焊缝等。
2)轧机方面的原因,轧辊的热膨胀、轧辊的磨损、轧辊的偏心运转等也会造成带钢厚度的波动。
3)轧制工艺方面的原因、冷轧轧制时带钢前、后张力的变化,轧制速度的变化,摩擦系数的波动等,也是造成厚度波动的原因。
17、 写出中间辊轴向移动量调节公式。
答:
S=(辊身长度一带钢宽度一校正值)/2
其中:
校正值为中间辊端部倒角弧长,单位:
mm
18、 乳化液系统长时间停车应采取哪些措施?
答:
1)将系统泵、循环泵、及粗分离器、磁棒过滤器、皮带刮油器传动停。
2)打开收集箱压缩空气喷吹阀,防止长时间停车造成油水分离。
19、 对轧钢工艺润滑的基本要求有哪些?
答:
1)适当的油性。
2)良好的冷却效果。
3)对轧辊和带钢表面有良好的冲洗和清洁作用。
4)良好的理化稳定性。
5)退火性能好。
6)防锈性能好。
7)对人体健康无害。
8)油源广泛,成本低。
20、 乳化液分哪些类型?
答:
乳化液分为水包油型(O/W)和油包水型(W/O)两种类型,前者含油量在10%以下,后者一般在30—40%以上。
21、 轧辊表面裂纹产生的原因是什么?
答:
1)由于轧辊本身质量问题,内部有缺陷。
2)由于操作原因造成裂纹,新辊换上后,预热时间太短,在轧制第一卷钢时轧制速度过快,轧辊温度急骤升高产生内应力,或由于轧制压力太大,使轧辊产生裂纹,发现有裂纹应及时换辊,否则会造成轧辊掉肉甚至爆裂。
22、 在轧制过程中会产生哪些轧辊缺陷?
这些缺陷对带钢表面质量有何影响?
答:
1)轧辊裂纹:
带钢表面会产生等距离大小、形状与裂纹相同的突出轧痕。
2)轧辊掉肉:
在裂纹的基础上若不及时换辊,继续高速,大轧制力轧制,会产生轧辊掉肉,若发现应立即停机,换辊,否则会发生断带。
3)勒辊:
由于升速或甩尾不当,带钢跑偏会造成勒辊,勒辊后带钢表面会产生勒印,其颜色与周围不同,手摸无感觉。
4)轧辊热划伤,由于高速轧制时,乳化液流量太小,产生变形热不能及时带走,使轧辊温度升高,带钢表面油膜破裂。
造成带钢表面条痕状划伤,另外轧辊打滑,带钢与轧辊产生相对摩擦,也会产生热划伤。
5)轧辊老化,辊身表面产生桔子皮纹。
6)轧辊划伤:
由于下工作辊护板间隙未调整好,在下工作辊表面产生一道道平行等距的划痕,其距离等护板筋间的距离。
7)粘辊:
由于断带造成碎带钢粘在辊身表面,轻微的粘辊可用油石打磨消除。
23、 轧辊爆裂产生的原因有哪些?
答:
1)轧辊内部存在裂纹,在高速大轧制力轧制时,会产生爆裂。
2)轧辊表面裂纹在磨削过程中未掏沟处理消除裂纹,在轧制过程中裂纹扩大,产生爆裂。
3)操作因素:
新换轧辊预热时间太短,第一卷钢升速太快,轧制压力突然增加,以及在轧制过程中发现裂纹未及时换辊,轧辊连续轧制产生疲劳,致使内裂纹扩大,容易产生轧辊爆裂。
24、 换辊后第一卷各道次为什么采用较大弯辊?
答:
由于轧辊必须以某一特定规程轧制若干卷后才形成稳定的热凸度,因此,换辊后第一卷的轧制相当于冷辊轧制,而冷辊的热凸度为零,所以,实际凸度曲线是水平线T,完好板形如图示,当以正常轧轧制力PA轧制时,产生完好板形的凸度应该是K’,但实际轧辊凸度是车削凸度K(本车间k=0),它远小于完好板形线所需凸度,因此带钢必然形成明显的边浪,为消除边浪而采用较大弯辊。
25、 在轧制过程中,带钢出现跑偏的原因是什么?
如何处理?
答:
在轧制过程中带钢出现跑偏一般在穿带或甩尾时发生,造成带钢跑偏的原因主要有以下几个方面:
1)来料原因。
来料板型不好,有严重的边浪,使带钢边缘控制装置不能准确及时地进行有效调节,造成第一道次带钢跑偏,采用措施是:
轧制速度不要太高,操作者留心注意观察,及时进行双摆调节,发现问题及时停车。
2)操作原因。
由于操作者双摆调节不例题,造成带钢跑偏。
3)电气原因。
由于在轧制过程卷取机张力突然减小或消失造成带钢跑偏、断带。
4)轧辊。
由于轧辊磨削后有严重的锥度,使得压下校不了,在轧制过程中给操作者双摆调节增加了难度,轻者会产生严重一边浪造成板形缺陷,重者造成带钢跑偏、断带。
5)带钢边缘控制装置故障、跑偏装置、灯管或镜表面污染或被其他物体遮住,使跑偏装置失效造成第一道次跑偏。
带钢轻微跑偏可以通过调节双摆及时消除,严重跑偏发现后应立即停车,将带钢剪断重新穿带,如轧辊损坏应及时换辊。
26、 造成带钢断带的原因有哪些?
断带后如何处理?
答:
在轧制过程中造成断带有以下几个方面原因:
1)来料原因。
来料有严重质量缺陷,如废边压入,严重溢出边及严重欠酸洗或过酸洗,厚度严重不均,板形边浪或中间浪会导致断带。
2)设备故障。
电气、控制系统故障或液压系统故障,常见的有张力波动、张力消失、液压系统停车等。
3)操作故障。
操作事故造成的断带是较常见的,如发现带钢跑偏,来料缺陷未及时降速或停车;道次计划选用不合理,道次变形量太大,造成轧制压力大,板形难控制,道次前、后张力太大,将带钢拉断;前道次带钢某处厚度波动(减薄或超厚),后道次未及时减速或将张力控制切断,造成断带等。
4)轧辊爆裂造成断带,断带后,应立即停车,将机架内带钢拉出,并将工作辊、中间辊拉出,检查工作辊、中间辊是否粘辊或损坏,轻微粘辊可用油石将表面磨平,严重损坏,应换支承辊。
另外必须将机架内断带碎片清扫干净,若轧机主传动轴安全环断应立即通知机械人员更换安全环,否则无法抽出工作辊。
必要时可将乳化液喷射打开,将残留在机架内碎小带钢冲洗干净。
更换轧辊后,开轧的第一卷钢速度不要太快,并且认真检查其表面质量。
27、 轧制过程中,轧机产生振动的原因是什么?
应如何处理?
答:
轧机振动一般发生在高速轧制极薄带钢时,由于振动,使带钢厚度波动,同时易产生断带,另外,厚度波动经过镀锡后产生“斑马纹”使镀锡板降组,甚至产生废品。
产生振动的原因很多,主要有以下几个方面:
1)轧制速度太高,成品规格薄。
2)道次轧制工艺参数不合理,如轧制压力低,变形量小,带钢前张力较大。
3)润滑条件不佳,如乳化液浓度太高或太低。
4)轧辊损坏,如中间辊或支承辊断带时损坏未及时更换。
5)轧辊轴承与轴承座之间存在间隙。
出现轧制过程中轧机产生振动,应分析判断产生的原因,并采取相应的措施进行处理。
若原因较复杂一时难以下结论,或者发现原因后一时难以处理,可适当降低轧制速,消除或降低振动程度,等到机组检修时再进行处理。
28、 轧制过程中,对带钢张力有何要求?
张力波动会产生哪些后果?
答:
在轧制过程中,如穿带,加减带以及稳定轧制各个阶段,要求带钢前、后张力保持恒定。
一般来说,要求轧机加减带时带钢张力波动≤±15%,卷取机与轧机间带钢张力波动≤±5%,稳速轧制时,带钢张力波动±5%。
在轧制过程中,如果带钢张力波动,将会使带钢表面产生二肋浪(俗称“起梗子"),给板型控制带来困难,不能正常升速,严重者造成勒辊,甚至断带。
29、 轧机对冷轧普碳钢坯料有哪些要求?
答:
带钢表面光洁,不得有裂缝、折叠、分层、气孔、非金属夹杂、粗毛刺和鳞片层,
30、 造成轧辊压痕有哪些原因?
答:
轧辊压痕主要是由于杂物进入轧机,使轧辊辊面被压出不同形状的坑。
一般产生的压痕的轧辊必须更换。
31、 造成粘辊有哪些原因?
答:
造成粘辊的原因是局部压下量过大,断带碎片、折叠带钢等进轧机所致。
一般轻微粘辊经人工用磨石磨削后可继续使用,带钢表面要求高时必须换辊。
二
1、 对冷轧轧辊的材质有哪些要求?
答:
冷轧过程中,轧辊表面承受很大的挤压和强烈的磨损。
高速轧制时卡钢、过烧等会造成辊面裂纹。
因此,冷轧工作辊应该具有极高而均匀的硬度,一定深度的硬化层以及良好的耐磨性与抗裂性。
轧辊具有良好的耐过烧、抗裂性是延长轧辊寿命的主要因素。
2、 轧辊硬度不够对轧制过程有哪些影响?
答:
轧辊硬度不够,轧制时弹性压扁大,轧辊与带钢表面接触面积增大,要获得同样厚度的产品,必须增大轧制压力,而轧制压力大对板形的调节不利。
3、 轧辊粗糙度过大对轧制过程有哪些影响?
答:
轧辊粗糙度大,轧制时轧辊与带钢表面摩擦系数增大,造成摩擦力增大,轧制压力增加。
4、 怎样用弯辊来消除“两边浪”和“中间浪”?
答:
当轧制过程中带钢出现两边浪时,说明带钢两边的轧制压力过大,这时应用正弯辊来消除两边浪,当出现中间浪时,说明轧辊原始凸度或热凸度太大,这时用负弯辊来消除。
5、 如何防止穿带时的跑偏?
答:
首先,在穿带前一定要校正好压下,给定好辊缝,看来料质量情况,是否有边浪,观察带钢运行情况。
发现跑偏及时调节压下,如跑偏太快调不过来迅速停车。
6、 在轧制过程中,带纲出现跑偏的原因和如何处理?
答:
在轧制过程中,带钢出现跑偏一般在穿带或甩尾时发生,造成带钢跑偏的主要原因有以下几个方面:
1)由于来料的原因来料板形不好,有严重的边浪,使带钢边缘控制装置不能准确及时地进行有效调节,造成第一道次带钢跑偏,采取措施是轧制速度不要太高,及时调节压下摆动调节或及时停车。
2)操作原因由于操作压下摆动调节不合理,造成带钢跑偏。
3)电气原因由于在轧制过程卷取机张力突然减小或消失造成带钢跑偏、断带。
4)轧辊由于轧辊磨削后有严重的锥度,使压下找不准,在轧制中给操作压下摆动增加了难度,轻者会产生严重一边浪造成板形缺陷,重者造成跑偏断带。
5)带钢边缘控制装置故障、跑偏装置、灯管或接受装置污染等,使跑偏装置失效造成第一道次跑偏。
7、 带钢平直度及表示方法是什么?
答:
带钢平直度指带钢沿宽度方向上各点延伸率相异程度或带钢横向应力分布的最大幅度,单位:
I相对延伸率幅度0.001%时为1“I”(即:
1米长度相对延伸1毫米)。
8、 轧辊磨削会出现哪些质量缺陷?
在轧制过程中会产生哪些不良后果?
答:
1)辊身有锥度:
造成压下不能校正,并容易造成一边浪,板形难以控制,要求辊身锥度小于O.1mm
2)磨削不圆:
辊身有椭圆度。
在轧制过程中产生振动,轧制压力波动,沿长度方向带钢厚度波浪形变化。
3)凸度:
在机组工艺上要求轧辊为平辊,若轧辊有凸度,在轧制过程中易产生带钢中间浪和二肋浪
4)轧辊表面粗糙度太大。
在轧制过程中轧制压力增加,板形难以控制,并且影响带钢表面质量。
5)轧辊辊身裂纹,由于未对裂纹进行掏沟、磨净。
未对轧辊进行探伤检测,在轧制过程中带钢表面产生与裂纹形状的突出轧痕。
9、 怎样防止轧辊磨损不均?
答:
首先,中间辊的辊肩部采用R=500~1500mm的圆角;其次,各轧辊采用不同的硬度,工作辊硬度HS为95以上,中间辊硬度HS为75~80。
支撑辊硬度为60~65,这样就有效的防止了磨损不均的问题。
10、 轧辊断辊产生原因
答:
1)轧辊制造原因:
辊颈部位本身就有缺陷,加之该部位承受扭距最大。
轧辊断辊一般发生在辊颈部位。
2)爆辊造成断辊:
大轧制力高速轧制时爆辊造成断辊。
断辊部位在爆裂部位。
3)操作原因造成断辊:
压下偏斜,轧辊一侧受力。
容易造成轧辊在辊颈部位断裂。
11、 引起轧制压力增大的因素是什么?
1)来料成分中C、Si含量高,当C>0.07%Si>O.02%轧制压力明显增加。
来料严重超厚,来料超厚>0.2mm以上,当轧制最后道次时,累计变形量达到90%,已产生加工硬化,变形抗力增加导致变形困难。
热轧工艺不合理,温度制度(开轧温度、终轧温度、卷取温度等)、变形制度不合理。
2)轧辊:
磨削质量不过关粗糙度>0.4um时,轧制压力明显升高。
工作辊硬度不够:
轧制过程中产生弹性压扁,使变形区接触弧面积增大,总轧制压力增加。
3)总变形量太大或道次计划变形分配不合理,致使变形量大的道次轧制压力大。
4)测厚仪测量值与实际不符,由于测厚仪不到位、未校正、系统故障或者外罩污染,会出现测量值误差。
正差时将造成轧制压力增加。
12、 轧制后带钢产生边裂的原因是什么?
答:
1)由于酸洗后切边剪的剪刃间隙未调整好或剪刀已坏未及时更换,剪边后边部毛刺,轧后容易产生边裂。
2)来料边部含碳量高,边部硬度高,轧后容易产生边裂。
3)总变形量太高或道次变形量分配不合理,最后道次压下量太大,有可能轧后产生边裂。
13、 简述常用乳化液设备。
答:
各种乳化液介质输送泵(系统泵、回流泵、循环泵等),管道阀门(截止阀、翻板阀、薄膜阀等)。
磁性过滤器、平板带式过滤器、反冲洗过滤器、双联过滤器、预过滤器等过滤设备。
搅拌器、刮油板、加热器、冷却器等辅助设备。
14、 如何正确配置乳化液?
答:
清洗机架、乳化液箱、收集槽及管道等涉及整个乳化液循环回路的相关部位。
加水打循环后排放,然后加水、加温至规定要求,加油量对应目标浓度按照容量法计算:
Lt=Qr×J
式中:
Lt——加油量(升)
Qr——乳化液总量(乳化液箱+管道容积)m3。
三
1、 常用加油方式有哪些?
答:
泵口加油、乳化液箱体加油、直喷式加油。
2、 简述乳化液温度调控的作用。
答:
对于不同的轧制油品均有相应的乳化液颗粒度控制,而颗粒度的变化将影响到轧制油的润滑性,因此现场乳化液温度控制应对应油品的温度一颗粒度控制曲线制订使用区间。
3、 简述乳化液浓度发生异常对轧制过程的影响。
答:
乳化液浓度大辐下降会造成乳化液的润滑性下降,轧制力上升,表面质量、板型难以控制。
乳化液浓度大辐上升会造成轧制打滑,若由于外来杂油泄漏造成的浓度上升,会降低乳化液皂化值,轧制力上升,表面质量、板型难以控制。
4、 乳化液浓度发生异常的原因分析。
答:
乳化液浓度发生异常应首先再次取样化验,确认浓度异常的可靠性。
造成浓度下降的原因有:
补充水质异常造成PH值下降;乳化液温度异常;乳化液箱体搅拌装置故障;乳化液过滤装置过度使用;加油管路泄漏;循环回路泄漏造成补充水量过大等。
造成浓度上升的原因有:
外来杂油泄漏;酸洗工序带钢预涂油过量;加油量过大等。
5、 简述皂化值的概念及其作用。
答:
中和一克酸所需氢氧化钾的毫克数称为皂化值。
皂化值是反映乳化液油脂含量的主要指标,一般而言,皂化值与杂油含量成反比;同时皂化值的大小也反映了轧制油的润滑性及对带钢表面的影响,皂化值愈高,润滑性愈好,但退火后表面清净性较差。
因此应根据不同的产品大纲要求,选用具有相应皂化值的轧制油。
6、 皂化值下降时的调控手段。
答:
造成皂化值突然下降的因素有:
外来杂油泄漏;酸洗工序带钢预涂油过量等。
调控手段:
检查处理外来杂油泄漏;停机、停止乳化液箱体搅拌,使外来杂油漂浮,刮除杂油后补充新的轧制油;
若由于酸洗工序带钢予涂油过量造成的皂化值下降,则可补充新的轧制油至规定范围。
7、 简述PH值的概念及作用。
答:
PH值是反映乳化液中的酸碱度,PH值7为中性,大于7为碱性,小于7为酸性。
PH值影响乳化液中的颗粒度,影响乳化液的稳定性。
一般来说,PH值偏碱性,乳化液会趋向稳定;PH值偏酸性,乳化液会趋向不稳定。
若乳化液PH值发生异常,一般应及时检验补充水质及酸洗带钢表面质量。
8、 简述电导率的概念。
答:
电导率是指乳化液电阻的大小,是检测乳化液中各种离子含量的指标,主要监测生产过程中补充水的质量和酸洗带钢表面氯离子的含量情况。
9、 轧制过程中润滑方式分为几种?
答:
边际润滑、液体润滑、极压润滑。
10、 轧制油的主要性能指标。
答:
润滑性,极压性,稳定性,清洁性,退火挥发性、防锈性。
11、 简述乳化液点检内容。
答:
乳化液设备运行状况;循环回路泄漏状况;系统压力,温度;乳化液外观;机架钢板表面质量。
12、 简述表面夹杂缺陷特征。
答:
钢板表面呈现点状、块状或线状的非金属夹杂物(如耐火材料、保护渣等),沿轧制方向间断或连续分布,其颜色为红棕色、深灰色或白色。
严重时,钢板出现孔洞、破裂、断带。
13、 简述分层缺陷特征。
答:
钢板内部或断面上出现分离层,有时在分层的缝隙中有肉眼可见的夹杂物,呈深灰色,分层不在钢板边缘时,板面出现无规则的小波纹或鼓包。
轧制后,凸出部分发亮,波纹不能消除。
剪切或冲压时,钢板分层。
14、 简述氧化铁皮压入缺陷特征。
答:
热轧时氧化铁皮被压入钢板表面,呈点状、条状或鱼鳞状的黑色斑迹,分布面积大小不等,压入的深浅不一,一般下表面多于上表面。
酸洗时无法洗掉,铁皮脱落时成为凹坑。
15、 简述粘结缺陷特征。
答:
退火钢卷层间互相粘合在一起称粘结,粘合的形式有点状、线状和大块面粘合,粘结较严重时,手摸有凸起感觉,多分布于带钢的边部或中间;严重的面粘结,开卷时被撕裂或出现孔洞,甚至无法开卷。
16、 简述锈蚀缺陷特征。
答:
钢板表面局部呈现不规则的点状、块状、条片状的锈斑,轻微者颜色浅黄;较重者颜色为黄褐色或红色;严重者为黑色,表面粗糙。
17、 简述划伤缺陷特征。
答:
钢板表面呈现直而细、深浅不一的沟槽。
平行于轧向,连续或断续,疏密不一,无一定规律,平整前划伤处较平滑,沟槽处颜色为灰黑色,平整后划伤,有毛刺,呈金属亮色。
18、 简述卷取擦伤缺陷特征。
答:
带钢表面呈现点状、短线状伤痕,沿轧制方向不规则分布,形如蝌蚪,擦伤处有金属亮色,精整擦伤有扎手感,平整擦伤较平滑,擦伤多发生在带钢头尾部。
19、 简述折皱缺陷特征。
答:
薄钢板表面呈现凹凸不平的皱折,多发生在小于0.8mm以下的薄板,皱纹边部成一定角度,严重折皱成压褶。
20、 简述塔形缺陷特征。
答:
钢卷外形缺陷,在钢卷的端面一圈比另一圈高(或低),连续不断,形如宝塔,多出现于钢卷的内(外)圈部分。
21、 简述溢出边缺陷特征。
答:
带钢卷取时,边缘形成的端面参差不齐,有时一圈比一圈突出,继而又一圈比一圈凹进,连续不断。
22、 简述扁卷(心型卷)缺陷特征。
答:
卧放的钢卷,内径变形尺寸不一现象,与地面平直,形状似心,液称心型卷,多发生在厚度≤0.5mm的钢卷中。
23、 简述粘结产生原因。
答:
冷轧时,卷取张力过大或张力波动,板形不佳,造成隆起,在层间压力较大部位产生粘结;带钢表面粗糙度太小;板形不良,产生边浪或中间浪,以及存在焊缝、塔形、溢出边,吊运夹紧时局部挤压以及堆垛时下层受压等,造成局部压紧粘结;炉温控制不当,温度过高;钢质太软,钢中碳、硅含量少,粘结倾向高;退火工艺制度不合理,退火时间太长或退火工艺曲线有误。
24、 简述锈蚀产生原因。
答:
钢板与周围介质(空气、水、汽)等接触,发生化学反应,形成铁的氧化物。
退火钢卷在中间库停留时间长(大于10天),表面可见局部点锈,相对湿度大,或厂房漏水,加速锈蚀。
钢板涂油不均,在未涂油处出现红、黄色锈。
防锈油水分多,质量差或钢板包装后,运输途中进水、湿度大,存放时间长。
25、 简述乳化液斑缺陷特征。
答:
经退火的钢板表面呈现不规则的或象小岛形状的黑色、褐色图形,常出现在带钢的头尾部