乳化沥青层施工.docx
《乳化沥青层施工.docx》由会员分享,可在线阅读,更多相关《乳化沥青层施工.docx(8页珍藏版)》请在冰豆网上搜索。
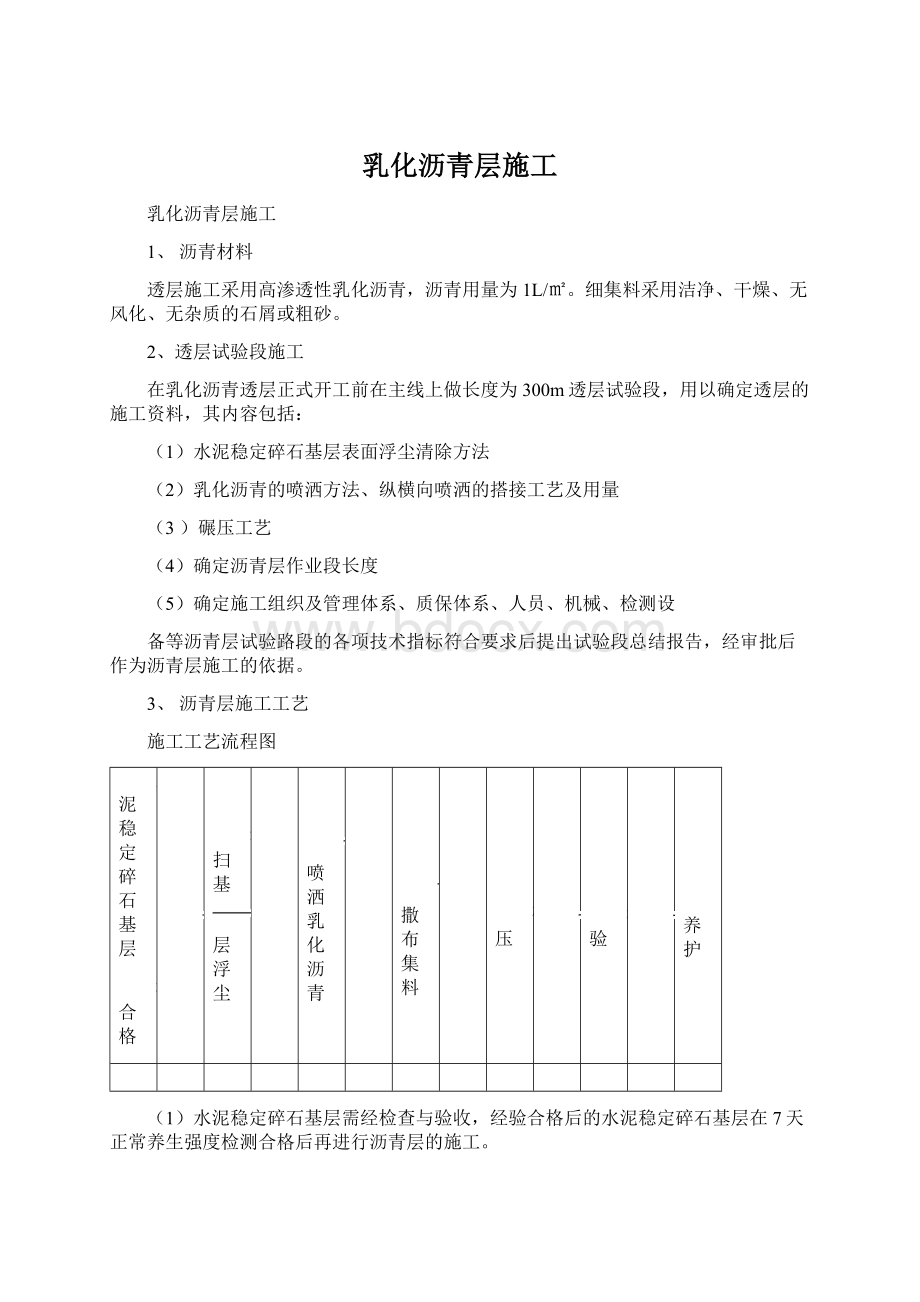
乳化沥青层施工
乳化沥青层施工
1、沥青材料
透层施工采用高渗透性乳化沥青,沥青用量为1L/㎡。
细集料采用洁净、干燥、无风化、无杂质的石屑或粗砂。
2、透层试验段施工
在乳化沥青透层正式开工前在主线上做长度为300m透层试验段,用以确定透层的施工资料,其内容包括:
(1)水泥稳定碎石基层表面浮尘清除方法
(2)乳化沥青的喷洒方法、纵横向喷洒的搭接工艺及用量
(3)碾压工艺
(4)确定沥青层作业段长度
(5)确定施工组织及管理体系、质保体系、人员、机械、检测设
备等沥青层试验路段的各项技术指标符合要求后提出试验段总结报告,经审批后作为沥青层施工的依据。
3、沥青层施工工艺
施工工艺流程图
水泥稳定碎石基层
检合格
清扫基
层浮尘
喷洒乳化沥青
撒布集料
碾压
检验
养护
(1)水泥稳定碎石基层需经检查与验收,经验合格后的水泥稳定碎石基层在7天正常养生强度检测合格后再进行沥青层的施工。
(2)消除水泥稳定碎石基层表面浮灰,先用人工用竹扫帚将水泥稳定碎石基层表面进行全面清扫,再用2-3台森林灭火鼓风机沿纵向排成斜线将浮灰吹净,若不能达到“除净”的要求,则用水冲洗,清除水泥稳定碎石基层表面浮灰,尽量使水泥稳定碎石基层顶面集料颗粒表面能部分外露。
(3)如果水泥稳定碎石基层表面已经干燥,则在喷洒乳化沥青之前一小时用洒水车快速喷洒少量水,以湿润水泥稳定碎石基层表面。
(4)等基层表面的水分稍干后浇洒乳化沥青,洒布透层沥青渗入基层一定的深度,不在表面形成油膜或流淌。
施工透层采用沥青洒布车一次洒布进行作业,并预先通过试洒,确定洒布车的行进速度、阀门开度和单位面积沥青用量。
(5)洒布沥青若有遗漏处,用人工补洒;如有积聚,刮除多余部分。
(6)在破乳后水份蒸发前,禁止车辆、行人上路。
4、质量检验
施工阶段检测包括:
乳化沥青喷洒、渗水试验、用量等。
(八)沥青混凝土面层施工
面层结构设计:
面层采用两层结构,上面层采用25㎜厚AC-10(A级70号道路石油沥青)细粒式沥青混凝土;下面层采用50㎜厚AC-16(A级70号道路石油沥青)中粒式沥青混凝土。
上面层采用细粒式沥青混凝土,要求平整、稳定、耐磨,矿料级配采用AC-10F,关键性筛孔2.36通过率需大于45%。
下面层采用中粒式沥青混凝土,矿料级配采用AC-16,关键性筛孔2.36通过率需大于38%。
l、施工准备
(1)机械配备
①摊铺设备为进口ABG423摊铺机,两台前后梯形摊铺,一台备用。
②沥青路面施工专用CC722型双钢轮振动压路机3台负责碾压成形。
⑤采用载重15吨的T815型和SDC3280自卸汽车共40辆,负责沥青混合料的运输。
④配备精度符合要求的质量检仪器,并在进场后安装调试到最佳状态。
并配备足够的易损部件。
(2)材料准备
①沥青混合料拌合设备为日本产RAP-2000LZ型型沥青拌和站一套,工作能力为200t/h。
上、下面层沥青混凝土均采用AH-70石油沥青,技术标准如下表:
针入度25℃,100g,5s
0.1㎜
60-80
延度15℃,5㎝/min
不小于(㎝)
100
软化点(环球法)
(℃)
44-54
闪点(℃)(COC)
不小于(℃)
230
含蜡量(蒸馏量)
不小于(%)
3
溶解度(三氯乙烯)
不小于(%)
99
薄膜加热试验163℃5h
质量损失
不小于(%)
0.8
针入度比25℃(%)
不小于(%)
55
延度(15℃)
(㎝)
50
②上面层细集料石质坚硬、清洁,不含风化颗粒,近似立方,公称最大粒径13.2mm,关键性筛孔2.36通过率需大于45%。
对进场料的粘附性不低于4级,否则掺加沥青抗剥落剂。
对进场细集料每500m3检验一次,不合格料决不进场。
考虑到与沥青的粘结力,在选择时需要进行混合料的水稳定性检验。
下面层集料采用石质坚硬、清洁、不含风化颗粒、近立方体颗粒的碎石,压碎值不大于28%,公称最大粒径16mm,下面层关键性筛孔2.36通过率需大于38%,。
对进场料的粘附性不低于4级,否则掺加沥青抗剥落剂。
下面层采用细粒式沥青混合料,矿料级配采用AC-16,其级配范围及技术指标见下
上面层采用细粒式沥青混合料,矿料级配采用AC-10F,其级配范围及技术指标见下表:
AC-10F矿料级配范围
筛孔尺寸(㎜)
13.2
9.5
4.75
2.36
1.18
0.6
0.3
0.15
0.075
通过百分率(%)
100
90-100
45-75
30-58
20-44
13-32
9-23
6-16
4-8
下面层采用中粒式沥青混合料,矿料级配采用AC-16,其级配范围及技术指标见下表:
AC-16矿料级配范围
筛孔尺寸(㎜)
19
16
13.2
9.5
4.75
2.36
1.18
0.6
0.3
0.15
0.075
通过百分率(%)
100
90-100
76-92
60-80
34-62
20-48
13-36
9-26
7-18
5-14
4-8
1.3填料
采用石灰岩、岩浆岩中的强基性岩磨细得到的矿粉。
矿粉必须干燥、清洁,每50吨检验一次。
拌和机回收的粉料全部弃掉,以确保沥青上面层的质量。
2、配合比设计
2.1热拌沥青混凝土的技术指标
指标名称
击实次数(次)
稳定度(KN)
流值(mm)
空隙率(%)
沥青饱和度(%)
浸水马歇尔试验(48小时)残留稳定度(%)
冻融劈裂试验残留强度(%)
AC-10
两面各50次
>5
2-4.5
3-6
70-85
≥80
AC-16
两面各50次
>4
2-4.5
3-6
70-85
≥80
2.2热拌沥青混合料配合比设计进行马歇尔试验、浸水马歇尔试验残留稳定度检验及车辙试验抗车辙能力检验三部分。
3、沥青混合料的拌和
3.1拌制沥青混合料时,严格掌握沥青和混合料的加热温度以及混合料的出厂温度。
如果温度不够,混合料不可能拌合均匀,摊铺无法平整,碾压不可能达到压实度,施工质量就根本无法保证。
施工温度范围见下表:
沥青加热温度
193-197℃
集料加热温度
180-190℃
混合料出厂温度
170-190℃
摊铺温度
不低于160℃
初碾压开始温度
不低于150℃
碾压终了温度
90℃
3.2为了保证施工温度,应该注意以下各个环节:
3.2.1沥青混合料拌和机在拌合时,集料的烘干温度要提高到170℃以上,拌和好的混合料贮存时间不得超过24小时。
拌合料贮存温度降低不超过10℃。
3.3根据试验室配合比结果进行试拌,通过试拌及相应的抽样试验确定拌和机每盘热料仓配合比。
3.4拌和时间不少于45s,由试拌确定,所有集料颗粒必须全部均匀裹复沥青结合料,并拌和均匀,无粗细分离及花白、结块现象。
3.5拌和机每天上午下午各取一组混合料试样做马歇尔试验及抽提筛分试验,检验油石比、矿料级配和沥青混凝土的物理力学性质。
4、沥青混合料的运输
4.1沥青混合料的运输采用大吨位的自卸翻斗车。
每辆车在使用前后必须清扫干净,为防止沥青与车厢板粘结在车厢侧板与底板涂一薄层油水混合液(柴油与水的比例为1:
3),并且不得有余液积聚在车厢底部。
4.2采用数字显示插入式热电偶温度计检测沥青混合料的出厂温度和运到现场温度。
插入深度大于150mm。
在运料车侧面中部设计专用检测孔,孔口距车厢底面约300m。
检测温度不低于160℃。
4.3拌和机向运料车卸料时,应多次挪动汽车位置,平衡装料,以减少混合料的离析现象。
4.4为防止混合料温度散失和不被污染,在运输车辆上备有覆盖设施。
5、沥青混合料的摊铺
5.1沥青混合料摊铺时采用两台摊铺机梯队作业方式,前后错开20-30m,采用悬浮式平衡梁自动找平方式,以保证上面层的平整度。
铺筑上面层前,对下面层的表面进行彻底的清扫,对于局部污染路段清除纹槽内泥土杂物,风干后均匀喷洒粘层乳化沥青,喷洒数量按沥青含量0.3kg/m2折算。
粘层乳化沥青喷洒后进行交通管制,禁止任何车辆通行和人员踩踏,乳化沥青破乳后,不粘车轮时进行摊铺上面层施工作业。
5.2摊铺机熨平板进行预热,预热温度达到100℃以上。
5.3运料车在摊铺机前10-30cm处停住,不得撞击摊铺机,更不允许偏撞。
卸料过程中运料车挂空挡,靠摊铺机推动前进。
5.4摊铺机缓慢、均匀、连续不间断地摊铺沥青混合料,摊铺过程中不随意变换速度或中途停顿,以提高平整度、减少混合料的离析,摊铺速度一般为2-4m/min。
为保持摊铺机在摊铺过程中不停顿,在摊铺前至少要求5台以上的运料车等候。
5.5在摊铺过程中,摊铺机螺旋送料器应相应于摊铺速度调整到保持一个稳定的速度均衡地转动,两侧保持有不少于送料高度2/3的混合料,以减少在摊铺过程中混合料的离析。
熨平板按所需厚度固定后,不随意调整。
6、沥青混合料的碾压
碾压设备组合:
双轮振动压路机2台,压实工艺本着“高温压实,高频低幅,跟踪碾压”的原则进行。
初压:
振动压路机开振动碾压4遍,控制速度在2-3km/h,振动频率35HZ-50HZ。
复压:
振动压路机静压2遍,最终消除轮迹,控制速度为3-5Km/h;终压采用胶压路机碾压2遍进行。
碾压时应注意:
A由于沥青混合料的性质决定碾压必须紧跟摊铺机进行,并不得产生推移、发裂,故采用列式梯队的方式进行碾压。
B压路机由低侧向高侧碾压,相邻碾压带若开振碾压时压路机轮迹的重叠宽度不超过20cm,压路机碾压起动、停止须减速缓慢进行。
C初压检查平整度,必须要时予以适当修整。
D复压时振动压路机先行走再开振,倒停车时先关振再倒车或停车,避免混合料形成鼓包。
E复压时应将驱动轮面向摊铺机,碾压路线及碾压方向不应突然改变导致混合料产生推移。
F碾压时,严禁压路机在已完成或正在碾压的路段上“调头”、急刹车及急转弯现象。
G压路机每次由两端折回的位置应呈阶梯形,随摊铺机向前推进,使折回处不在同一横断面上;碾压过程中只要压路机能错开车后压路机立即跟上碾压。
H为了防止混合料与压路机轮粘结,压路机的洒水装置要保持良好状态。
I压路机终压温度不小于90℃,最终消除轮迹。
路面温度冷却到50℃以前不得开放交通。
在当天碾压的尚未冷却的沥青混合料层面上,不得停放任何机械设备或车辆,不得散落矿料、油料等杂物。
碾压时,根据现场检测结果及时调整碾压遍数,最终使各项指标达到规范要求。
7、接缝处理
在接缝施工及构造物两端连接处必须仔细操作,保证衔接紧密、平顺。
7.1接缝施工要求
7.1.1施工缝必须保证紧密、平顺;构造物处应一次性连续摊铺。
7.1.2沥青混合料的摊铺应使纵、横向两种接缝都保持在最小数量。
7.1.3纵向接缝:
采用两台摊铺机摊铺,应先后梯队交错排列,摊铺机之间的距离宜保持在10-30m左右,以此保证纵向接缝湿热接缝。
7.1.4横向接缝:
由于工作中断使摊铺材料的末端已经冷却或者第二天才恢复工作时,应做成一道垂直横缝。
在下次行程进行摊铺前,应在上次行程的末端清理干净后涂刷适量粘层沥青或其它粘结材料,并注意调置整平板的高度,为碾压留出充分的预留量。
相邻两幅及上下层的横向接缝均应错位1m以上。
7.2纵向缝施工
7.2.1采用两台摊铺机梯队式作业的纵缝采用热接缝,将前一台摊铺机已铺一部分,留下10-20cm宽暂不碾压,作为后续部分的基准面,然后跨缝碾压,以消除缝迹。
7.2.2在摊铺过程中,上下面层的纵缝错开15cm以上。
7.3横向缝施工
7.3.1在施工结束时,摊铺机在接近端部前约1m处,将熨平板稍稍抬起驶离现场,用人工将端部混合料铲齐后再予以碾压,相邻两幅及上下层的横向接缝错位1m以上。
然后用3m直尺检查平整度,确保平整度符合要求,趁尚未冷却透时垂直铲除端部层厚不足的部分,在下次施工时成直角连接。
7.3.2在需要设置平接缝的位置直接切割成缝,清除接缝位置以外的集料,接续施工前对接缝面时行清洗、干燥及涂粘层沥青等处理。
7.3.3横向接缝处重新摊铺混合料时,为使接缝处的路面厚度和密度都能满足要求,需要在整平板上放置适当厚度的垫板,其厚度根据沥青混合料松铺系数确定。
7.3.4横向碾压时压路机应位于已压实的混合料层上,伸入新铺层的宽度为15cm,然后每压一遍向新铺混合料移动15-20cm,直至全部在新铺上为止,后改为纵向碾压。
8、施工阶段的质量管理
8.1沥青施工质量管理满足现行JTGF40-2004《公路沥青路面施工技术规范》的要求。
8.2沥青混合料质量控制
沥青混合料制造过程中的质量控制有以下几方面:
8.2.1拌和温度:
沥青的原材料和成品温度、集料烘干加热温度、混合料拌和温度及混合料的出厂温度,应该严格按照施工规范或技术要求的规定,随时随地进行检验。
8.2.2矿料级配:
逐盘采集打印各个热料仓的材料质量、矿料质量及一盘混合料的总质量,随机计算出矿料级配,与标准配合比进行对照。
8.2.3石油比:
与普通沥青混合料一样,检测矿料级配和油石比是质量检测的重点,每天每一台拌和机取样抽提筛分不少于二次。
油石比误差不超过±0.3%。