WorkFlow与EasyFlow合并教材MPS上课教材help.docx
《WorkFlow与EasyFlow合并教材MPS上课教材help.docx》由会员分享,可在线阅读,更多相关《WorkFlow与EasyFlow合并教材MPS上课教材help.docx(80页珍藏版)》请在冰豆网上搜索。
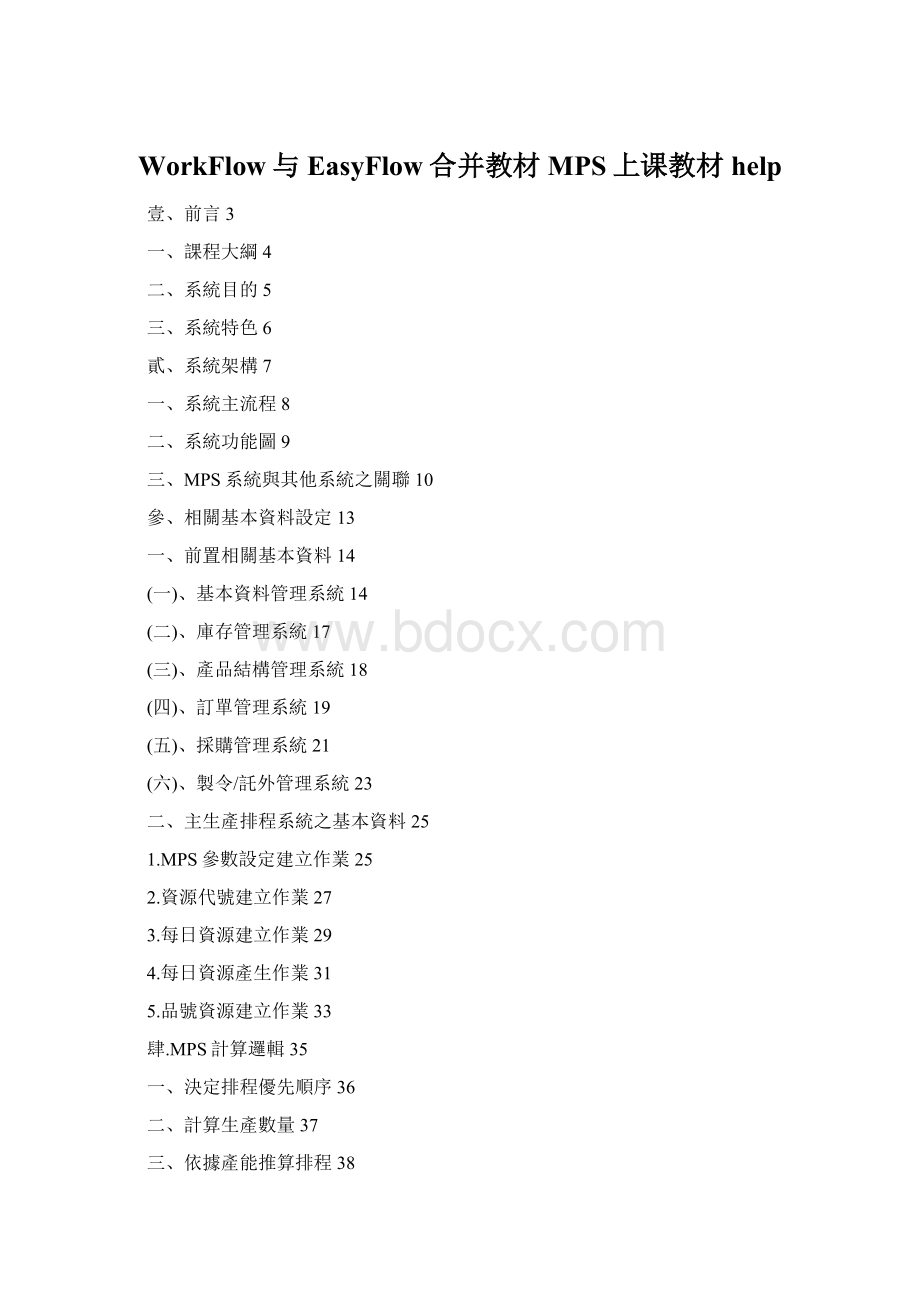
WorkFlow与EasyFlow合并教材MPS上课教材help
壹、前言3
一、課程大綱4
二、系統目的5
三、系統特色6
貳、系統架構7
一、系統主流程8
二、系統功能圖9
三、MPS系統與其他系統之關聯10
參、相關基本資料設定13
一、前置相關基本資料14
(一)、基本資料管理系統14
(二)、庫存管理系統17
(三)、產品結構管理系統18
(四)、訂單管理系統19
(五)、採購管理系統21
(六)、製令/託外管理系統23
二、主生產排程系統之基本資料25
1.MPS參數設定建立作業25
2.資源代號建立作業27
3.每日資源建立作業29
4.每日資源產生作業31
5.品號資源建立作業33
肆.MPS計算邏輯35
一、決定排程優先順序36
二、計算生產數量37
三、依據產能推算排程38
伍.批次作業及資料維護管理39
一、排程來源產生作業40
二、排程來源建立作業43
三、排程計劃產生作業47
四、排程計劃維護作業49
五、排程計劃鎖定作業54
六、排程計劃發放作業56
七、製令排程調整作業59
八、排程計劃清除作業64
陸、報表管理65
一、資源別生產排程表65
二、排程中產能負荷分析表69
三、資源別產能負荷分析表72
四、排程加班/外包建議表75
五、品號資源明細表78
六、排程計劃明細表80
柒、上機實習83
壹、前言
一、課程大綱
二、系統目的
三、系統特色
一、課程大綱
1.前言
2.主生產排程系統之系統架構
3.相關基本資料設定及欄位說明
4.MPS計算邏輯
5.批次作業及資料維護管理
6.報表管理
7.測驗及問卷
二、系統目的
對於整個製造業而言,最令人感到困擾且無助的問題便是生產排程計劃的即時性及可參考性。
生產排程的問題,通常整個製造業的生產環境因為有許多的不確定因素,如產能上的限制,不確定的訂單插單,訂單交期的變更及前後生產排序的選擇等都將導致生產排程計算上的困難,如果再依賴生管人員以人工的經驗法則臨時派工,常常導致生管人員疲於奔命的調整生產排程,而假如生管人員一時的錯誤判斷將導致工作分派紊亂,生產現場無法有效的進行製造生產的問題產生。
想要以有限的產能及應付訂單接單的不確定性來滿足客戶訂單,就必須執行即時而有效的多廠生產排程,模擬及工令的發放程序及生產現場的跟催。
『WorkflowERP』提供廣泛的計劃性模擬功能,從銷售預測,實際接單,產能計劃,主生產排程及發放生產計劃皆能有效且迅速協助製造業編製產品的主生產排程計劃,並對生產排程計劃進行模擬及分析,以評估其生產製造的可行性,大幅提昇生產排程的有效性及控制性,增加製成品的週轉率與生產線產能的稼動率及積極性。
三、系統特色
●依不同生產型態可定義排程優先順序的設定,透過不同的優先順序,進而模擬找出最佳排程方法。
●可以針對訂單與銷售計劃排定須要生產的項目,並可以追溯原訂單,並且比較是否滿足訂單的交期。
●可以自動依照瓶頸資源自動產生每日瓶頸資源產能資料。
●可針對每日的瓶頸資源產能事前排定產能計劃,便於滿足客戶交期的需求。
●排程資料可依使用者的需求自行調整生產優先順序,生產數量與預定生產的日期,以滿足特別的需求。
●調整後的排程計劃可再與產能計劃比較,並建議排定加班或外包計劃。
●可提供排程反覆運算,以便於產能計劃修正後的調整。
●排程前自動計算每張訂單所需要的淨需求數量,便於安排生產數量,大幅減少製成品存貨。
●依據產品對於產能的負荷,自動依照每日瓶頸資源產能排定生產時程(有限產能)。
●確定的排程計劃可自動發放成製造命令。
●系統可提供獨立的多批次模擬生產計劃,以便於生產排程的比較與建議調整。
●系統提供即時的生產計劃排程甘特圖示,以利於計劃人員作計劃調整的參考。
貳、系統架構
一、系統主流程
二、系統功能圖
三、MPS系統與其他系統之關聯
一、系統主流程
二、系統功能圖
三、MPS系統與其他系統之關聯
⏹基本資料管理系統
A.廠別資料建立作業:
系統可分為多廠分廠執行其主生產排程計劃,所 以有多廠的區分,需於此建立廠別的代號。
B.庫別資料建立作業(納入可用量計算):
系統可分分庫的執行需求計劃,因此有多庫的區分需於於此建立廠別的代號,其中亦要特別注意的是此庫的存量是否為計劃執行中供給量之一必須於「納入可用量計算」的參數打勾。
C.行事曆建立作業:
必須有工廠行事曆的資料以判斷模擬推算前置生產或採購的時間日程。
⏹庫存管理系統
在擬具各項產品及料件之補充計劃時,將自『庫存管理系統』讀取其庫存量資料。
因此務必使庫存系統中各料件之庫存正確率達95%以上。
而在即時性方面則應將資料延緩時間縮至0.5天以內,必須要檢視的資料有:
A.品號基本資料:
主要庫別、生產線別、品號屬性、主供應商、固定前置天數、
變動前置天數、批量、檢驗天數
⏹產品結構管理系統
生產計劃去推算相依需求時,必須依據此系統中之產品用料資料,因此,產品用料資料之正確性十分重要。
另外,一項主件在生產時所慣用之「製令別」必須註明正確,以做為自動發放製令時之依據。
於產品結構中的「用量資料」,「損耗率」,「材料型態」,「生效日期」,「失效日期」及「選配預設」都必須確定其正確性。
另外材料的取替代資料的檢視亦須要的。
只要產品結構有作任何的異動,都應執行『低階碼計算更新作業』,以確保模擬資料的正確性。
⏹訂單管理系統
在執行生產計劃產生作業時,將以『訂單管理系統』中之客戶訂單獨立需求資料做為計劃之源頭.因此,此資料必須能夠儘量反映事實。
特別注意交期已過卻還未出貨的訂單需重新檢查是否依然視為未交之訂單。
A.銷售預測:
單頭:
納入生產計劃、廠別。
單身:
日期、預測數量、已受訂量。
B.客戶訂單:
單頭:
出貨廠別、確認碼。
單身:
訂單數量、贈品數量、已交數量、贈品已交量、
預交日、結案碼。
⏹採購管理系統
A.採購單資料:
單頭:
廠別代號、確認碼。
單身:
採購數量、已交數量、預交日、結案碼。
B.請購單資料:
單頭:
廠別代號、確認碼。
單身:
請購數量、需求日期、採購碼、結案碼。
⏹製令/託外管理系統
製令/託外管理系統』中之製令預計生產資料及製令預計用料資料,是擬具生產及採購計劃時十分重要的兩項資料。
因此,必須令其能夠反映正確且即時的狀況。
特別注意已超出預計完工日期的製令單多時卻還未入庫製令單需重新檢查是否依然視為未結之製令單。
A.製造命令:
單頭:
生產廠別、入庫庫別、預計產量、已生產量、
報廢數量、預計開工、預計完工、狀態碼、確認碼。
單身:
需領用量、已領用量、庫別。
B.加工計價資料:
加工廠商、加工單價。
⏹LRP/MRP系統
A.LRP批次需求計劃產生作業,若選擇計劃依據為「依MPS計劃」,
則需指定計劃批號,可將排程計劃依BOM展料,產生採購計劃資料。
B.MRP物料需求計劃產生作業,若勾選計劃依據為「依MPS計劃產
生」,需指定計劃批號,可將排程計劃依BOM展料,批次產生採購計劃資料。
參、相關基本資料設定
一、前置相關基本資料
二、主生產排程系統之基本資料
一、前置相關基本資料
(一)、基本資料管理系統
1.廠別資料建立作業
⏹程式代號:
CMSI02
⏹作業目的:
1.廠別資料為庫存或商品異動相關報表資料的篩選條件,在
產生相關報表時,均可用廠別來篩選條件。
當然將來在執
行MRP/LRP(物料需求計劃--生產計劃系統)時廠別亦是一
個重要資料區隔或篩選條件。
2.為配合全球ERP的管理,如果你只有單一製造廠管理,亦請您設定一個廠別代號來標示,在本系統的異動單據(領(退)料單、生產入庫單、託外進(退)貨單…等)輸入時必須指定廠別。
⏹作業畫面:
因主生產排程是分廠計算需求,故須先設定相關廠別。
2.庫別資料建立作業
⏹程式代號:
CMSI03
⏹作業目的:
商品存貨儲存的倉庫,期初上線時請將庫別資料先行建立,
再進行庫存系統的「品號資料建立」。
⏹作業畫面:
⏹庫別性質:
分存貨倉及非存貨倉二種,非存貨倉之料件不計入成本。
⏹納入可用量計算:
此倉庫的數量是否可納入可用量來累加。
主生產排程只計劃需納入可用量計算之庫別的料件數量。
⏹存檔時庫存量不足准許出庫、確認時庫存量不足准許出庫:
庫存數量為0時,可否執行出庫相關單據的存檔、確認。
3.行事曆建立作業
⏹程式代號:
CMSI08
⏹作業目的:
依工廠休假方式設定工廠的行事曆,將來系統在推算開
工日、完工日、預計領料日及採購日期時,遇到休假日
時,會調整相關日期資料,而行事曆一年產生一次即可,
公司已確定之休假計劃應進行登錄。
⏹作業畫面:
行事曆為主生產排程產能與日期推算之依據,故須先設定各年度之『工廠行事曆』。
(二)、庫存管理系統
1.品號資料建立作業
⏹程式代號:
INVI02
⏹作業目的:
建立公司各品號資料。
⏹作業畫面:
⏹品號屬性:
MPS只計劃品號屬性為M.自製件及S.託外加工件之料件。
⏹固定前置天數、變動前置天數、批量:
總前置天數=(需求數量/批量)*變動前置天數+固定前置天數。
⏹檢驗天數:
品管檢驗所需天數。
⏹安全存量:
MPS計算需求數量的考慮因子。
(三)、產品結構管理系統
1.BOM用量資料建立作業
⏹程式代號:
BOMI02
⏹作業目的:
建立產品的組成、用量等資訊。
⏹作業畫面:
⏹單頭重要欄位
a.標準批量:
料件於生產時之標準生產批量。
b.製令單別:
生產此一料件之常用製造命令單別。
⏹單身重要欄位
a.組成用量:
生產『標準批量』之主件所需使用之元件數量。
b.底數:
用來計算組成用量之分母。
c.損耗率:
在生產製造過程中之標準損耗率。
d.生效日及失效日:
此元件於此BOM中之有效期限。
e.投料時距:
MPS推算日期的因子,製令開工日與這個元件投入生
產的時間差距,為推算領料日期之依據。
(四)、訂單管理系統
1.銷售預測建立作業
⏹程式代號:
COPI04
⏹作業目的:
預測各品號未來可能之銷售資料。
⏹作業畫面:
⏹單頭重要欄位
a.納入生產計劃:
銷售預測資料是否為MRP/LRP/MPS的需求來源。
b.廠別:
預測廠別。
⏹單身重要欄位
a.日期:
預測日期,會成為排程資料的預交日期。
b.預測數量-已受訂量=排程資料的需求數量
(同時也是九大量的計劃銷售量)。
2.客戶訂單建立作業
⏹程式代號:
COPI06
⏹作業目的:
建立客戶訂單資料。
⏹作業畫面:
⏹單頭重要欄位
a.出貨廠別:
訂單預計出貨的廠別。
b.確認碼:
經過核准確認的單據才生效。
⏹單身重要欄位
a.預交日:
會成為排程資料的預交日期。
b.訂單數量+贈品數量-已交數量-贈品已交量=排程資料的需求數量(同時會是九大量的預計銷售量)。
c.結案碼:
主生產排程系統不考慮結案碼為Y.已完工y.指定完工的項目。
若訂單剩餘未交量已不出貨,請將該品項指定結案。
(五)、採購管理系統
1.採購單建立作業
⏹程式代號:
PURI07
⏹作業目的:
建立採購單資料。
⏹作業畫面:
⏹單頭重要欄位
a.廠別代號:
採購單預計進貨的廠別。
b.確認碼:
經過核准確認的單據才生效。
⏹單身重要欄位
a.採購數量-已交數量=九大量的計劃採購量。
b.預交日:
供給日期。
c.結案碼:
主生產排程系統不考慮結案碼為Y.已完工y.指定完工的項目。
若採購單剩餘未交量已不進貨,請將該品項指定結案。
2.請購單建立作業
⏹程式代號:
PURI05
⏹作業目的:
建立請購資料。
⏹作業畫面:
⏹單頭重要欄位
a.廠別:
請購需求的廠別。
b.確認碼:
經過核准確認的單據才生效。
⏹單身重要欄位
a.需求日期:
為排程資料的供給日期。
b.請購數量=九大量的預計請購量。
c.結案碼:
主生產排程系統不考慮結案碼為Y.已完工y.指定完工的項目。
若請購單不抛轉採購單,請將該品項指定結案。
(六)、製令/託外管理系統
1.製造命令建立作業
⏹程式代號:
MOCI02
⏹作業目的:
建立製造命令資料。
⏹作業畫面:
⏹單頭重要欄位
a.生產廠別:
製令預計生產的廠別。
b.預計產量:
來源為主生產排程系統發放之生產數量。
c.預計產量-已生產量-報廢數量=九大量的預計生產量。
d.預計開工:
來源為主生產排程系統發放之預計開工日。
e.預計完工:
來源為主生產排程系統發放之預計完工日。
f.狀態碼:
主生產排程系統不考慮狀態碼為Y.已完工或y.指定完工的製令。
若製令單剩餘未生產量已不生產,請將該工單指定結案。
g.確認碼:
經過核准確認的單據才生效。
⏹單身重要欄位
a.需領用量-已領用量=九大量的預計領用量。
2.加工計價資料建立作業
⏹程式代號:
MOCI09
⏹作業目的:
建立廠商加工計價資料。
⏹作業畫面:
⏹主生產排程系統發放託外製令時,會依品號符合生、失效日,產生加工廠商及加工單價。
二、主生產排程系統之基本資料
1.MPS參數設定建立作業
⏹程式代號:
MPSI01
⏹程式名稱:
MPS參數設定建立作業
⏹作業目的:
須先設定MPS計算數量及推算日期之依據,以方便日後作為計算數量及產能推算的依據。
⏹輸入畫面:
⏹欄位說明:
1.需求計算方式(MA002):
*1.淨需求、2.毛需求,選擇以何種方式計算需求數量。
*當需求計算方式=淨需求時,自動預設顯示[計算庫存可用量]
=Y求數量。
2.計算庫存可用量(MA003):
針對毛需求時是否於「排程計劃維護作業」中顯示出十大量(各項預計數量與計劃數量)之資料。
3.排程優先順序(MA004):
將所有選擇納入排程之訂單或銷售預測資料,依照一定之原則排列使用資源的優先順序,排列的方式有下列:
(1).依預交日:
依據訂單上之預交日期,預交日較早的訂單,先佔用資源,以滿足客戶需求。
(2).依生產天數:
(總需求數/批量)*變動前置天數+固定前置天數(品號基本資料之設定)。
生產天數較短之訂單,優先佔用資源,以滿足批量達成率。
(3).依最晚開工日:
預交日-1-檢驗天數-生產天數(考慮行事曆的休假日)。
最遲須在何日開工,計算出來最晚開工日較早的訂單,優先佔用資源。
4.生產件開單日延遲999天(含)以上者視為急單處理(MA005):
當製造命令的開單日期(排程發放日期)>製造命令的預計開工日999天(含)時,即將製造命令建立作業中之急料碼打勾。
5.產能推算方式(MA006):
可選擇1.有限產能或2.無限產能。
若為有限產能:
於「品號資源建立作業」中僅能指定一項瓶頸資源。
若為無限產能:
於「品號資源建立作業」中不需指定瓶頸資源。
6.無限產能產能落點(MA007):
可選擇1.最後一天或2.批量分攤。
批量分攤:
將生產數量依品號基本資料檔的批量及變動前置天數分攤於每日排程。
⏹作業重點:
1.若產能推算為「1.有限產能」,但品號無瓶頸資源時,則依無限產能推算排程。
2.資源代號建立作業
⏹程式代號:
MPSI05
⏹程式名稱:
資源代號建立作業
⏹作業目的:
建立多項資源的產能資料。
⏹輸入畫面:
⏹欄位說明:
1.資源代號(MB001)
*資源的代號,不可空白。
2.資源名稱(MB002)
*資源的名稱。
3.廠別(MB003)
*輸入時自動預設「廠別資料檔」的第一筆廠別資料,亦可修改。
*可點選
(icon)或[F2]廠別資料查詢,其資料須存在於「廠別資料檔」中,並自動顯示廠別名稱,但不允許空白。
*新增時可修改廠別資料,但修改狀態時此欄位不可輸入。
4.每日最大產能(MB004)
*每日最大產能為理想值。
*此欄位必須大於等於零。
5.每日產能(MB005)
*MPS之推算是以每日產能之設定為依據。
*此欄位必須大於等於零。
6.產能單位(MB006)
*一般設定為時間單位,此單位亦為固定耗用與變動耗用之單位。
7.備註(MB007)
*可點選
(icon)或[F2]片語資料查詢。
3.每日資源建立作業
⏹程式代號:
MPSI06
⏹程式名稱:
每日資源建立作業
⏹作業目的:
執行「每日資源產生作業」後,至此作業檢視及修正每日資源資料及已耗產能之資料。
⏹輸入畫面:
⏹欄位說明:
單頭(資源代號建立作業中之資料,不能修改)
1.資源代號(MB001)
*按查詢確認後自動顯示資源代號。
2.資源名稱(MB002)
*此欄位僅作顯示。
3.廠別(MB003)
*此欄位僅作顯示。
4.每日最大產能(MB004)
*此欄位僅作顯示。
5.每日產能(MB005)
*此欄位僅作顯示。
6.產能單位(MB006)
*此欄位僅作顯示,查詢時自動預設為「人時」。
7.備註(MB007)
*此欄位僅作顯示。
單身
1.日期(MD002)預設為行事曆中所設定之非休假日,可視實際狀況新增、刪除。
例如:
假日加班則應增加加班日期。
2.當日產能(MD003):
資源代號建立」所設定之每日產能,若行事曆中設定當天只工作半天,則產能會自動減半。
此處可視實際需求而修正產能大小,例如:
員工加班則當天產能就應增加。
3.瓶頸耗用(MD004):
由「製令排程調整作業」中,製令子單身之各項資源的瓶頸耗用所回寫。
4.非瓶頸耗用(MD005):
由「製令排程調整作業」中,製令子單身之各項資源的非瓶頸耗用所回寫。
⏹作業重點:
1.執行「每日資源產生作業」依據「資源代號建立」及「行事曆建
立」之資料,產生每日資源資料,可以修改,無法手動新增。
4.每日資源產生作業
⏹程式代號:
MPSB06
⏹作業名稱:
每日資源產生作業
⏹作業目的:
批次產生每日可用資源資料(批次作業)。
⏹輸入畫面:
⏹欄位說明:
基本選項
1.選擇廠別
*可點選
(icon)或[F2]廠別資料查詢,其廠別資料須存在於「廠別資料檔」中,但不允許空白。
2.選擇資源代號
*可點選
(icon)或[F2]瓶頸資源單頭檔查詢,若空白表全部。
3.輸入日期
*預設系統年月的月初~月底。
(EX.系統年月:
95/05=>預設為95/05/01~95/05/31)。
*可點選
(icon)或[F2]日期快手查詢需產生之每日資源日期起迄區間.但不允許空白。
*休假日之產能預設為0,僅須工作半天之產能會自動減半(如星期六)。
4.已存在者重新產生:
若產生完每日產能資料後又更動資源代號之產能資料,則須重新產生每日資源資料,此時即需勾選此一選項。
⏹作業說明:
1.系統將已建立之資源代號資料加上行事曆的工作日期,產生所輸入期間之每日資源產能於「每日資源建立作業」中。
2.若行事曆為工作半天,則產能會自動減半。
(如星期六)
3.當日產能=每日產能*天數比率
5.品號資源建立作業
⏹程式代號:
MPSI07
⏹作業名稱:
品號資源建立作業
⏹作業目的:
建立每個品號生產時所需耗用的資源明細。
⏹輸入畫面:
⏹欄位說明:
單頭(品號資料建立作業中之資料,不能修改)
1.產品品號(MB001)
*按「查詢」確認後自動顯示產品品號。
2.產品品名(MB002)
*此欄位僅作顯示。
3.產品規格(MB003)
*此欄位僅作顯示。
4.單位(MB004)
*此欄位僅作顯示。
5.生產線別(MB068)
*此欄位僅作顯示。
6.主供應商(MB032)
*此欄位僅作顯示。
單身(資源代號建立作業中之資料)
5.資源代號(MC001)
*[F2]資源代號查詢,其資源資料須存在於「資源代號檔」中。
6.資源名稱(MB002)
*此欄位僅作顯示。
7.廠別(MB003)
*此欄位僅作顯示。
8.每日標準產能(MB005)
*此欄位僅作顯示。
9.每日最大產能(MB004)
*此欄位僅作顯示。
10.產能單位(MB006)
*此欄位僅作顯示。
11.瓶頸資源(MC009)
*若參數設定中【產能推算方式】設定為『有限產能』,方可勾選【瓶頸資源】。
*一個品號僅可勾選一筆資源代號。
12.固定耗用(MC003)
*使用此資源固定耗用的時間。
13.變動耗用(MC004)
*使用此資源耗用批量所需時間。
14.耗用批量(MC005)
*收集變動耗用之批量。
⏹作業重點:
1.此作業不可新增,當庫存系統「品號資料建立」後,若品號屬性為「M.自製件」或「S.託外加工件」,則系統會自動新增一筆品號資料於單頭。
2.根據此產品品號於資源代號中的產能狀況,輸入各項資源的固定耗用、變動耗用及耗用批號等資料。
3.固定耗用,變動耗用、耗用批量:
A.將來計算品號資源之總耗用量。
B.品號使用此資源之總耗用量=(需求數量/耗用批量)*變動耗用+固定
耗用。
肆.MPS計算邏輯
一、決定排程優先順序
二、計算生產數量
三、依據產能推算排程
一、決定排程優先順序
將所有選擇納入排程之訂單或銷售預測資料,依照設定之排程優先順序,產生產品品號使用資源的優先順序。
排列的方式有下列三種:
1.依據預交日:
依據訂單上之預交日期,預交日較早的訂單,先佔用資源,以滿足客戶需求。
2.依據生產天數:
A.生產天數=(總需求數/批量)*變動前置天數+固定前置天數。
B.其中批量、固定前置天數及變動前置天數皆為品號基本資料中之設定。
C.生產天數較短之訂單,優先佔用資源,以滿足批量達成率。
3.依據最晚開工日:
最晚開工日=預交日—1—檢驗天數—生產天數(考慮行事曆之休假日),亦即最遲須在何日開工。
計算出來最晚開工日較早的訂單,優先佔用資源。
二、計算生產數量
依照「MPS參數設定作業」需求計算方式的設定,依照毛需求或淨需求的條件,計算各計劃來源之生產數量及生產天數。
1.毛需求:
毛需求數量=訂單之(訂單數量+贈品數量)—(已交貨量+已交贈品量)
或銷售分析中之預測數量—已受訂量。
2.淨需求:
淨需求=毛需求數量—預計結餘量。
A.考慮安全存量
預計結餘量=庫存量+(預計生產+預計進貨+預計請購+計劃生產+計劃採購+請拋採未確認)—(安全存量+預計銷售+預計領用+計劃銷售+計劃領用)。
B.不考慮安全存量
預計結餘量=庫存量+(預計生產+預計進貨+預計請購+計劃生產+計劃採購+請拋採未確認)—(預計銷售+預計領用+計劃銷售+計劃領用)。
其中,十大量之資料來源如下:
.計劃銷售量=未達成之銷售預測量(預測數量-已受訂量)。
.計劃生產量=LRP生產計劃內之生產數量。
.計劃採購量=LRP採購計劃內之採購數量。
.計劃領料量=LRP生產計劃內之領料數量。
(相依需求量,LRP上階主件的元件需求量)