油泵调节垫片冲孔落料连续模具设计毕业设计论文.docx
《油泵调节垫片冲孔落料连续模具设计毕业设计论文.docx》由会员分享,可在线阅读,更多相关《油泵调节垫片冲孔落料连续模具设计毕业设计论文.docx(20页珍藏版)》请在冰豆网上搜索。
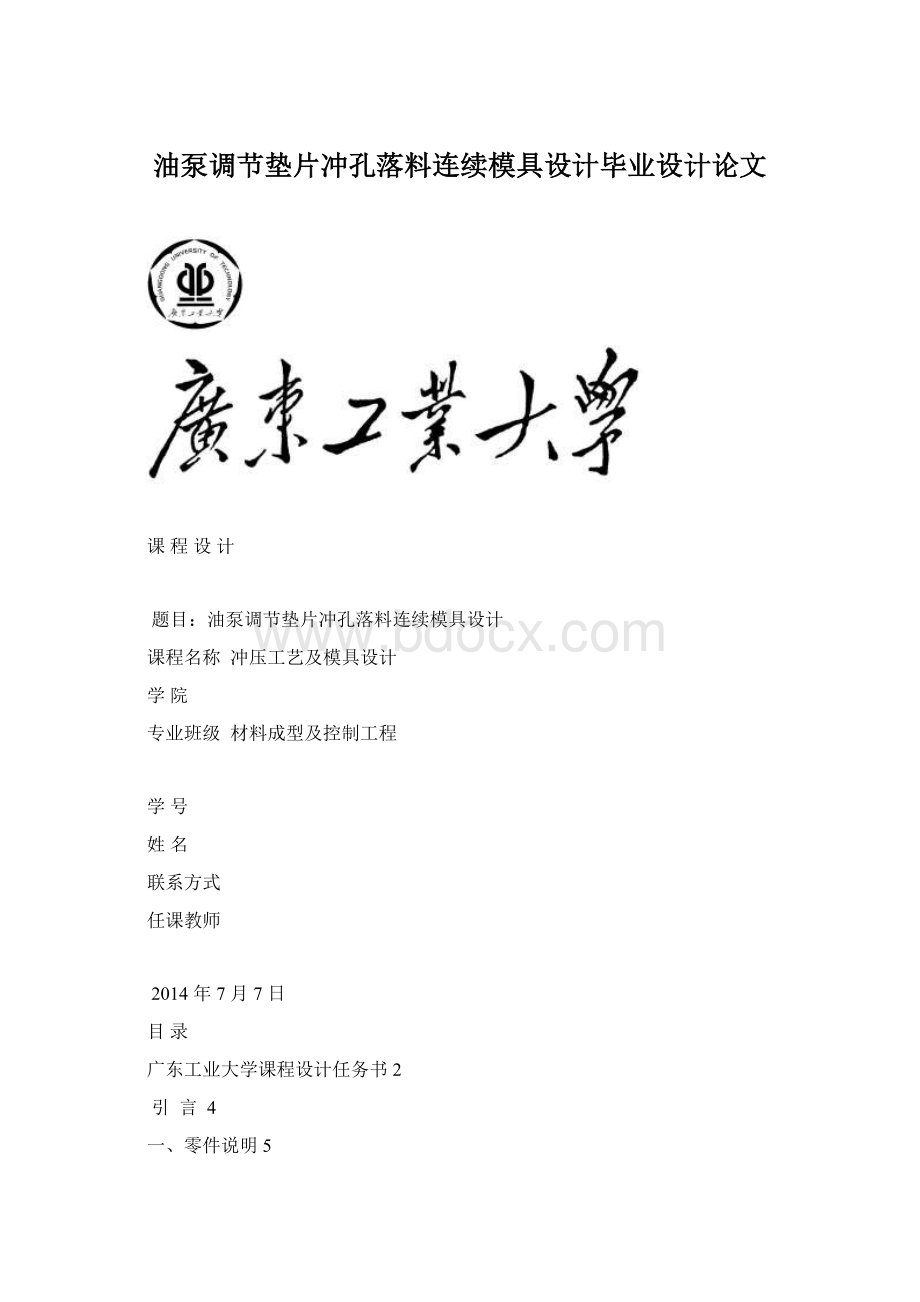
油泵调节垫片冲孔落料连续模具设计毕业设计论文
课程设计
题目:
油泵调节垫片冲孔落料连续模具设计
课程名称冲压工艺及模具设计
学院
专业班级材料成型及控制工程
学号
姓名
联系方式
任课教师
2014年7月7日
目录
广东工业大学课程设计任务书2
引 言 4
一、零件说明5
二、冲压件工艺分析6
三、模具设计计算7
1.排样、计算条料宽度及确定步距8
2.计算冲压力8
3.确定压力中心10
4.冲模刃口尺寸及公差的计算10
5.确定各主要零件结构尺寸12
1)凹模外形尺寸的确定12
2)凸模长度13
四、设计并绘制总图、选取标准件13
上模座14
下模座14
导柱15
导套16
垫板16
凸模固定板17
凹模17
落料凸模18
广东工业大学课程设计任务书
题目名称
油泵调节垫片冲压工艺及模具设计
学生学院
材料与能源学院
专业班级
材料成型及控制工程专业材料加工
姓名
学号
一、课程设计的内容
根据给定的冲压零件图进行产品的冲压工艺分析和比较,制定合理的冲压工艺方案,进行有关工艺计算,确定冲压模具的类型和结构,选择冲压设备,绘制模具的装配图及零件图,编制冲压工艺卡,并撰写设计说明书。
二、课程设计的要求与数据
1.课程设计时间共1.5周,按时独立完成课程设计任务,符合学校对课程设计的规范化要求;
2.绘制所设计模具的装配图和非标件零件图:
图纸整洁,布局合理,图样和标注符合国家标准;
3.编制冲压工艺卡,撰写设计计算说明书(约20页):
要求公式使用准确,计算正确,语言流畅,书写工整,插图清晰整齐;
4.设计说明书与图纸按学校规定装订成册。
三、课程设计应完成的工作
1.冲压工艺设计:
包括分析零件的冲压工艺性,拟订冲压件的工艺方案,确定合理的排样形式、裁板方法,并计算材料的利用率;确定模具结构及尺寸等;
2.根据总冲压力及考虑模具的结构尺寸选择成形设备的型号;
3.模具结构及其零部件设计:
设计一道工序的冲模,绘制冲模总装配图及主要零件图;
4.冲压工艺过程卡片;
5.设计计算说明书。
四、课程设计进程安排
序号
设计各阶段内容
地点
起止日期
1
布置题目,工艺分析与工艺计算
教3-111
6.30-7.1
2
工艺方案比较与模具结构草图
教3-111
7.2
3
绘制模具总装配图
教3-111
7.3~7.4
4
绘制零件图,编冲压工艺卡
教3-111
7.5~7.7
5
编写设计说明书
教3-111
7.8
6
答辩,提交所有资料
教3-111
7.9
五、应收集的资料及主要参考文献
[1]自编.冲模设计课程设计指导书[M].广东工业大学,2011.
[2]自编.冲模图册[M].广东工业大学,2011.
[3]姜奎华主编.冲压工艺与模具设计[M].北京:
机械工业出版社,1999.
[4]李志刚主编.中国模具设计大典[M].南昌:
江西科学技术出版社,2003.
[5]罗益旋主编.最新冲压新工艺新技术及模具设计实用手册[M].长春:
吉林出版发行集团,2004.
[6]肖景容,姜奎华主编.冲压工艺学[M].北京:
机械工业出版社,2000.
[7]郝滨海编著.冲压模具简明设计手册(第二版)[M].北京:
化工工业出版社,2009.
发出任务书日期:
2014年6月29日指导教师签名:
计划完成日期:
2014年7月8日基层教学单位责任人签章:
主管院长签章:
引 言
模具是现代化工业生产的重要工艺装备。
在国民经济的各个生产部门都越来越多地依靠模具来进行生产加工。
在产品生产的各个阶段,无论是大量生产,批量生产,还是产品试制阶段,也都越来越地依赖于模具。
因此模具工业已是国民经济的基础工业。
现代工业产品的品种发展和生产效益的提高,在很大程度上取决于模具的发展和技术经济水平。
目前,模具已成为衡量一个国家,一个地区,一家企业制造水平的重要标志之一。
我国模具制造技术是随着现代工业建设而发展的。
在50年代以前,当国内需要少数模具,只有少数企事业可以仿制,主要依靠模具钳工凭着个人技艺制造一些间单的模具,如电话机听筒之类的模具。
50年代以后,随着国民经济建设高潮的到来,随着国际经济技术合作交流的发展,国外的模具技术书刊,模具设计手册,模具制造资料等逐渐介绍到我国,对指导和促进模具技术的发展起了重要的作用。
自1959年起,电火花成型加工机床开始应用于模具生产,采用成形磨削方法加工凸模和电极,用电火花成型加工凹模,卸料板型孔,使模具制造水平又有一个较大的提高。
随后,由于模具制造技术的不断改进,模具技术的研究,模具标准化工作的开展和模具新材料的开发也得到进一步的发展。
这时我国的模具工业开始形成,出现了一些模具专业厂。
近年来,改革开放和国民经济的高速发展,推动了模具技术和模具工业的新发展,模具的品种。
精度和数量有了很大的发展,模具对工业产品的影响也越来越大,模具也更加引起人们的关注,很多科研院所和高等院校在模具技术的基本理论,模具的设计与结构,模具制造加工技术,模具材料以及模具加工设备等方面都取得了可喜的实用性成果。
这个时期是模具技术发展最快最迅速的时期。
模具标准化工作是代表模具工业和模具技术发展的重要标志。
特种加工工艺设备的改进和提高,使模具加工的自动化程度和效率都大大提高。
模具新材料的应用,以及热处理技术和表面处理技术的开发和应用,使模具寿命大幅度地提高。
我国模具制造技术水平,从过去只能制造简单模具发展到可以制造大型,精密,复杂,长寿命模具。
而模具领域最重要的组成部分就是冷冲压模具,约占模具总比例的40%。
冷冲压是利用安装在压力机上上的冲模对材料施加压力,使其产生分离或塑性变形,从而获得所需要零件的一种加工方法。
冷冲压不但可以加工金属材料,而且还可以加工非金属材料和复合材料。
冲压模具是将材料加工成所需冲件的一种工艺装备,冲压模具在冷冲压中至关重要,一般来说,不具备符合要求的冲压模具冷冲压就无法进行;先进的冲压工艺也必须依靠相应的冲模来实现。
1、零件说明
2、冲压件工艺分析
3、模具设计计算
制件如下图所示:
零件名称:
油泵调节垫片
材料:
H62
料厚:
0.2mm
生产批量:
大批量
要求设计此零件的冲裁模
该零件形状简单、对称,是由圆弧和直线组成的,冲裁件内外所能达到的经济精度为IT14,孔中心与边缘距离尺寸公差为±0.2mm。
将以上精度与零件简图中所标注的尺寸公差相比较,可认为该零件的精度要求能够在冲裁加工中得到保证。
其他尺寸标注、生产批量等情况,也均符合冲裁的工艺要求,故决定采用挡料销进行定位、弹性卸料装置、自然漏料方式的冲孔落料模进行加工。
方案一采用复合模进行加工。
复合模的特点是生产率高,冲裁件的内孔与外缘的相对位置精度高,板料的定位精度要求比级进模低,冲模的轮廓尺寸较小。
但复合模结构复杂,制造精度要求高,成本高。
复合模主要用于生产批量大、精度要求高的冲裁件。
方案二采用级进模加工。
级进模比单工序模生产率高,减少了模具和设备的数量,工件精度较高,便于操作和实现生产自动化。
对于特别复杂或孔边距较小的冲压件,用简单模或复合模冲制有困难时,可用级进模逐步冲出。
但级进模轮廓尺寸较大,制造较复杂,成本较高,一般适用于大批量生产小型冲压件。
比较方案一与方案二,复合模冲裁零件的几何形状与尺寸受到模具结构与强度方面的限制,且制件被顶到模具工作面上必须用手工或机械排除,生产效率稍低。
级进模可以自动送料生产效率高,且冲裁简单形状零件比复合模成本低。
所以根据零件性质故采用级进模加工。
1.排样、计算条料宽度及确定步距
2.计算冲压力
3.确定压力中心
4.冲模刃口尺寸及公差的计算
5.确定各主要零件结构尺寸
1)凹模外形尺寸的确定
2)凸模长度
4、设计并绘制总图、选取标准件
5、绘制非标准零件图
采用单排方案,如下图:
由表3-3
确定搭边值,根据零件形状两式件间按矩形取搭边值a1=1.5mm,侧搭边a=1.5mm,则进距:
s=60+1.5=61.5mm
条料宽度:
B0-△=(D+2a)0-△=980-0.5mm
该模具采用弹性卸料和下出料方式
1)落料力
查表3-20
得到黄铜(硬态)H62的抗剪强度τ=420MPa
F落=KLtτ
=1.3×264×0.2×420=28828N
2)冲孔力
中间大孔
F大孔=KLtτ=1.3×(46π-8+π×?
×8+2×2×0.2×420=16716N
三个小孔F小孔=KLtτ=1.3×9π×3×0.2×420=9262N
3)推料力
F推落=nK推F=4×0.063×28828=6916N
F推大孔=nK推F大孔=4×0.063×16716=4212N
F推小孔=nK推F小孔=4×0.063×9262=2334N
F总=F落+F大孔+3×F小孔+F推大孔+3×F推小孔
=28828+16716+3×9262+6916+4212+2334=86792N
模具压力中心是指冲压时各个冲压部分冲压力合力的作用点。
为了确保压力机和模具正常工作,应使冲模的压力中心与压力机滑块的中心相重合。
对于带有模柄的冲压模,压力中心应通过模柄的轴心线。
否则会使冲模和压力机滑块产生偏心载荷,使滑块和导轨之间产生过大的磨损,模具导向零件加速磨损,降低模具和压力机的使用寿命。
冲模的压力中心,可按下述原则来确定:
(1)对称形状的单个冲裁件,冲模的压力中心就是冲裁件的几何中心。
冲裁直线段时,其压力中心位于直线段的中点。
(2)工件形状相同且分布位置对称时,冲模的压力中心与零件的对称中心相重合。
(3)冲裁形状复杂的零件或多凸模的零件时,其压力中心可以通过解析计算法求出。
中心如下
落料时,选凹模作为基准,首先设计凹模刃口尺寸,间隙通过减少凸模刃口尺寸得到。
当以凹模为基准件时,磨损后刃口部分尺寸都增大,属于A类尺寸,采用配合加工方法。
零件图中未标注公差的尺寸由下图所示
该零件凸模刃口各部分尺寸按上述凹模的相应部分尺寸配制,保证双面间隙值
C=(5.0~8.0)%tCmin=0.01mmCmax=0.016mm
由于所冲形状接近于长方形,因此其凹模外形选择矩形,如图所示
根据工件的最大外形尺寸b=95mm和材料的厚度0.2mm,查表3-29
得:
K=0.2
可计算凹模的各尺寸如下:
厚度H=Kb=0.2×95=19mm
C=(1.5~2)H=28.5~38取c=30mm
则L=30×2+59.57+1.5+59.57=180.64mm
B=30×2+94.57=154.57mm
取L×B×h=200×160×20
由于该凸模尺寸较大,采用螺钉固定的方式,凸模长度为56mm
先用冲床的公称压力应大于计算出的总压力F总=86792N;最大闭合高度应大于冲模闭合高度+5mm;工作台台面尺寸应能满足模具的正确安装。
按上述要求,结合工厂实际,可用J23-10开式双柱可倾压力机。
并需在工作台面上配备垫块,垫块实际尺寸可配制。
该压力机参数如下:
公称压力/KN:
100
发生公称压力时滑块距下死点距离/mm:
4
滑块行程/mm:
60
行程次数/次·min-1:
135
最大封闭高度/mm:
180
封闭高度调节量/mm:
50
滑块中心到床身距离/mm:
130
工作台尺寸左右/mm:
360前后/mm:
240
工作台孔尺寸左右/mm:
180前后/mm:
90直径/mm:
130
立柱间距离/mm:
180
模柄孔尺寸(直径×深度)/mm:
30×50
工作台板厚度/mm:
50
垫板厚度/mm:
35
倾斜角(可倾式工作台压力机):
30°
按已确定的模具形式及参数,从冷冲模标准中选取标准模架。
绘制总图。
按模具标准,选取所需的标准件,查清标准件代号及标记,写在总图明细表内,并将各零件标出统一代号。
部分零件尺寸:
上模座
GB/T2855.1-2008L×B×H=200mm×160mm×40mm
下模座
GB/T2855.2-2008L×B×H=200mm×160mm×45mm
导柱
GB/T2861.1-2008d=28/32mmL=170/170mm
导套
GB/T2861.3-2008
D=28/32mmL=100/100mmH=38/43mm
垫板
JB/T7643.3-2008L×B×H=200mm×160mm×8mm
凸模固定板
JB/T7643.2-2008L×B×H=200mm×160mm×16mm
凹模
JB/T7643.1-2008L×B×H=200mm×160mm×20mm
落料凸模
卸料板
B0-△=980-0.5mm
F落=28828N
F大孔=16716N
F小孔=9262N
F推落=6916N
F推大孔=4212N
F推小孔=2334N
F总=86792N